There are so many types of rubbers available on the market that it can be confusing to find the right one. So here is a simple article discussing the 15 most commonly used rubbers, their properties, and their applications.
Properties of Rubber
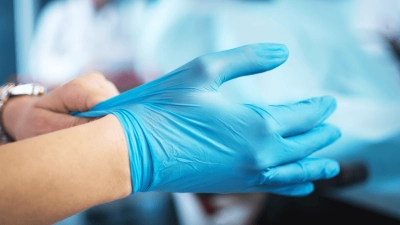
Rubber is a unique material for several reasons. It can be soft or hard, solid or liquid, flexible or rigid, and much more.
Only a handful of materials can match the versatility of rubber; even then, some applications cannot function without rubber.
Following is a small list of various types of rubber properties and their importance.
1. Elasticity
Elasticity is the property of a material to return to its original state after experiencing a compressive or tensile force. Higher elasticity means the material can deform and return to its original shape.
In short, elasticity is a measure of the stretchiness of a material. This property can be seen in several materials, including elastomers (rubber), metals, and plastics.
However, rubber is by far the most elastic of all the materials. Elasticity is necessary for the industrial space; many products like pipes, gaskets, and seals require elastic materials like rubber.
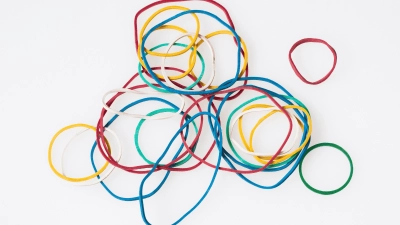
Good elasticity is why rubber materials are predominantly used in pipes, gaskets, and seals. Rubber gets its elasticity from its distinct molecular makeup.
It is made up of long polymer chains entangled with one another. These chains can be pulled and pushed but eventually return to their original state.
2. Vulcanization
Vulcanization is a chemical process used to strengthen rubber materials. Rubber is put into a kiln alongside sulfur and heated to approximately 280°F to 320°F.
Adding heat results in sulfur atoms embedding themselves between the molecular rubber chains.
Vulcanized rubber has better hardness and tensile strength, increasing elasticity, good abrasion resistance, and excellent weathering resistance.
3. Thermal Contraction
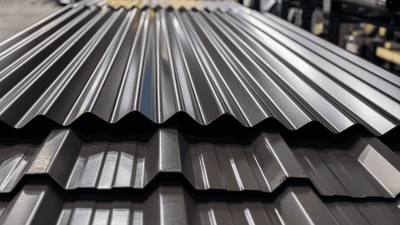
Thermal contraction is the decrease in material volume due to a temperature change. Materials react differently to temperature changes; metals contract with the decrease in temperature, but rubber contracts with the increase in temperature.
The long molecular chains curl up and shrink when heat is applied to a rubber material.
Thermal contraction is not ideal, but it is preferable to thermal expansion. An increase in volume can cause interference with neighboring components in a product.
A decrease in volume can result in minor stresses, which are easier to deal with.
4. Insulation
Insulation is the property of a material to prevent the flow of heat or electric current through it. Natural and synthetic rubber is an insulator of electric current in all its forms.
However, the heat resistance of rubber can vary from a complete insulator to a weak conductor.
Sound insulation properties make rubber a desirable material for electronic components.
5. Compression Set
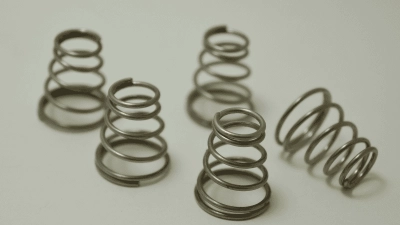
A compression set measures material deformation after long-term exposure to compressive stress.
In rubber products, a compression set is used to measure the amount of material that does not revert to its original shape.
Rubber is commonly used in gaskets, seals, and o-rings, so a poor compression set can affect long-term device operation.
6. Water & Air Resistance
Natural rubber and all synthetic rubbers have a non-porous structure, resulting in excellent impermeability. Water and air resistance allow natural and synthetic rubbers to be used in various hydraulic and pneumatic applications.
Airtight synthetic rubbers like food-grade silicone are often used in the food industry for packaging. While natural rubber is often used in plumbing seals and gaskets.
7. Durability
Rubber is a resilient material that can withstand high levels of stress. However, with proper vulcanization and chemical formulations, rubber can be modified to withstand even harsher environments.
Rubber has good abrasion resistance, low-temperature resistance, flame resistance, and moderate tear resistance.
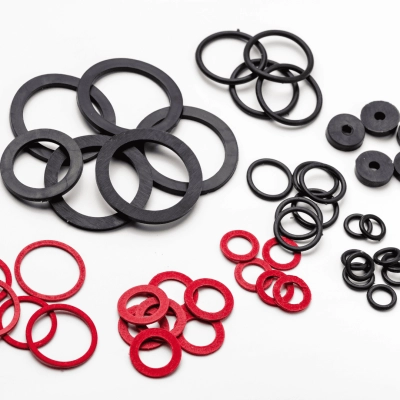
Send Your Inquiry Now!
Quality Meets Affordability. Inquire Now for High-Quality Products at Low Volumes.
Common Types of Rubber Materials
Two primary categories of rubber material are available on the market: natural rubber and synthetic rubber.
Natural rubber is processed tree sap that comes from rubber trees. Synthetic rubber is a whole category full of different types of rubber materials.
In total, there are around 40 types of natural and synthetic rubber, and here is a list of the most common types of rubbers you need to know about.
Natural Rubber (NR)
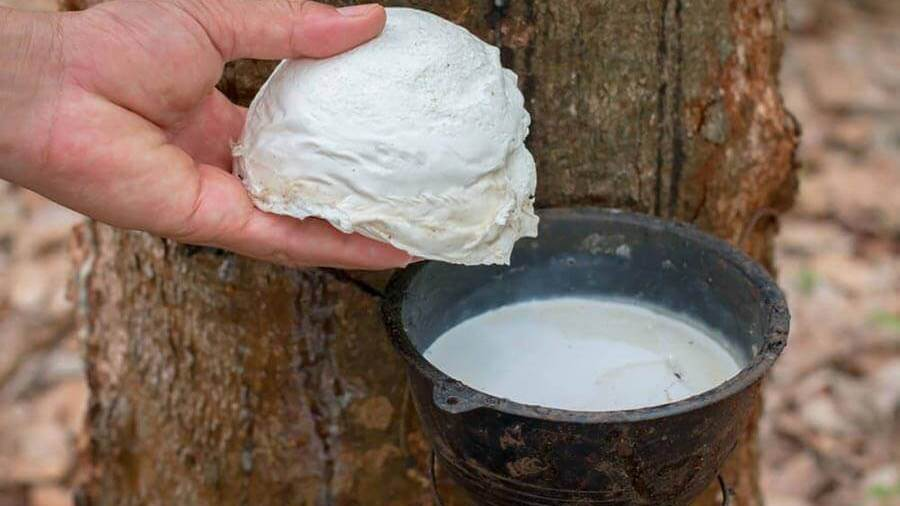
Natural rubber is known by many names, including latex, Indian rubber, gum rubber, or Amazonian rubber, but the essential attributes are the same. Organic sap is collected from rubber trees and processed into useable natural rubber.
The natural rubber has excellent resistance to stress and fatigue, in addition to its decent compression set and tear resistance.
Natural rubbers have good mechanical and thermal properties but are particularly weak to most chemicals.
Oils, fuel, acids, alkalines, and amines should not come directly with a natural rubber material. Hence, natural rubber is often mixed with other compounds for added strength.
It is often used for room-temperature applications like rubber bands, tires, vibration dampers, gaskets, and seals. With the addition of some fortifying compounds, it can be used for roofing, flooring, and adhesive applications.
Styrene-Butadiene Rubber (SBR)
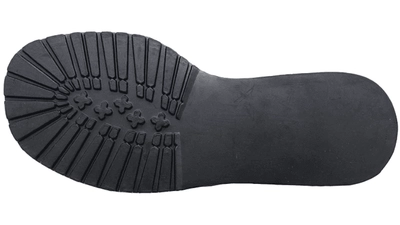
Styrene-butadiene rubber is a family of rubber compounds created from a combination of styrene and butadiene. Styrene-butadiene rubber is the most complex and most durable synthetic rubber out of all others.
Developed in 1929 by a chemist in Germany, it was predominantly used throughout WW2 for automobile tires and various other rubber products.
Styrene-butadiene rubber (SBR) shares several material properties with natural rubber. It displays better durability but is one of the types of rubber that is weak to chemical and environmental damage.
Today, nearly half of all car tires in the world are made of Styrene-butadiene rubber. Additionally, you can find this material in your shoe soles, rubber cutting boards, and roofing.
Silicone Rubber (VMQ)
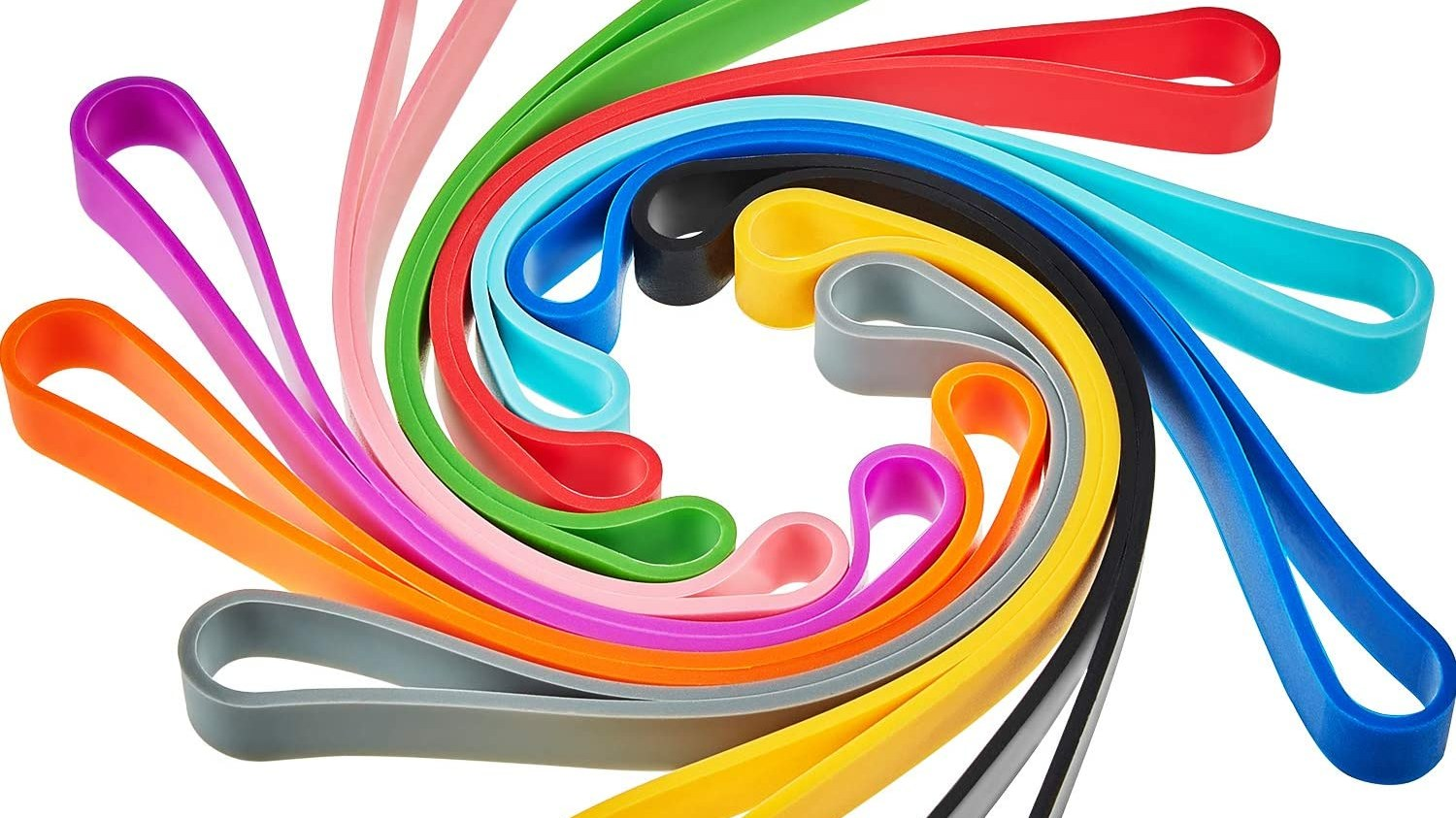
Natural silicone (Si) is processed with carbon (C), oxygen (O), and hydrogen (H) to create a synthetic elastomer called silicone rubber.
Uncured silicone rubber exists as a liquid and requires vulcanization, curing, and sometimes catalyzation to convert to a solid. Silicone has the most diverse set of material properties of any other rubber.
It has good flame resistance, excellent resistance to chemicals and low temperatures, and significant environmental performance. Fuel and chemical solvents are a big threat to silicone rubbers.
Natural rubber is used in several industries, from medical to automotive. It is used for biocompatible medical products and hypoallergenic food products.
Additionally, you can find silicone rubbers in synthetic lubricants and adhesives.
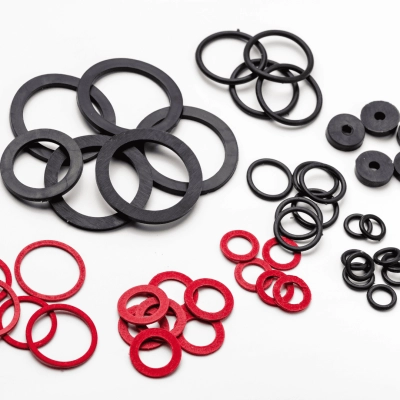
Send Your Inquiry Now!
Quality Meets Affordability. Inquire Now for High-Quality Products at Low Volumes.
Fluorosilicone Rubber (FVMQ)
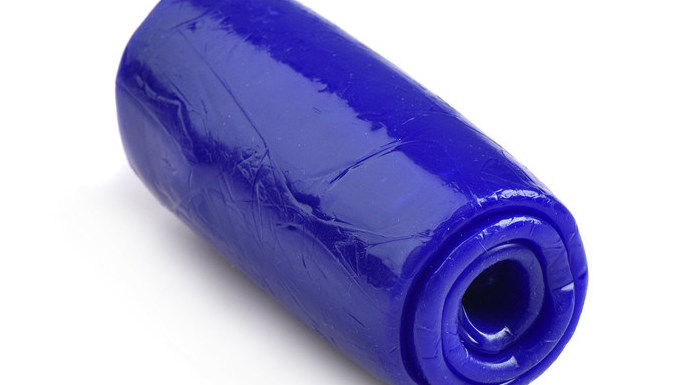
Fluorosilicone is a modified form of silicone rubber designed to be long-lasting and stable at extreme temperatures. It is one of the more expensive types of rubber and is sparingly used for general-purpose products.
FVMQ improves on all regular silicone’s poor physical properties and abrasion resistance. Its only shortcoming is medium-low gas permeability and ketone.
Because of its high cost, FVMQ is unusable for simple items like rubber bands and shoe soles. Instead, it is often used for gaskets and seals in some engineer parts and hydraulic brake fluid setups.
Nitrile Rubber (NBR)
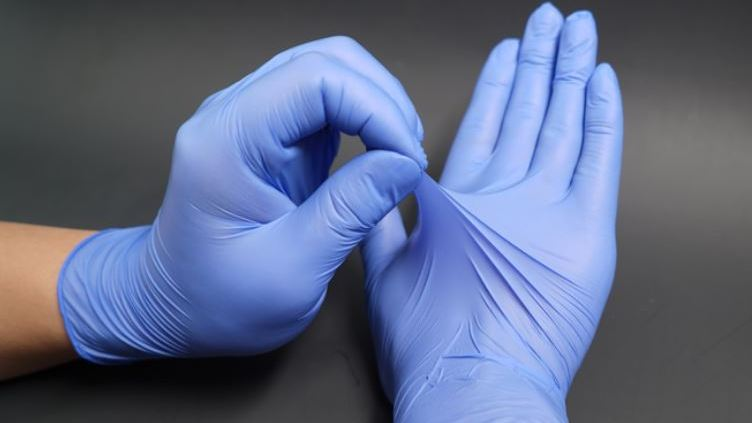
Nitrile rubber is a synthetic elastomer with increased chemical resistance. It is also called nitrile butadiene rubber, acrylonitrile-butadiene rubber, NBR, and Buna-N and is commercially trademarked under Perbunan, Nipol, Krynac, and European.
Nitrile rubber was developed in the 1940s as one of the first oil-resistant elastomers.
NBR has relatively poor resistance to thermal changes for a synthetic rubber compound. Depending upon the configuration, it will also have poor flame resistance.
But all of NBR’s shortcomings are offset by its ozone, fuel, and oil resistance. Additionally, nitrile can be mixed with PVC for added aging, gasoline, ozone, and flame resistance.
Hence, it is widely used in the automotive and oil and gas industries. Nitrile rubber inner tubes, seals, and gaskets are commonly used in gasoline tanks for vehicles. For medical applications, nitrile is the premier option for surgical gloves.
Hydrogenated Nitrile Rubber (HNBR)
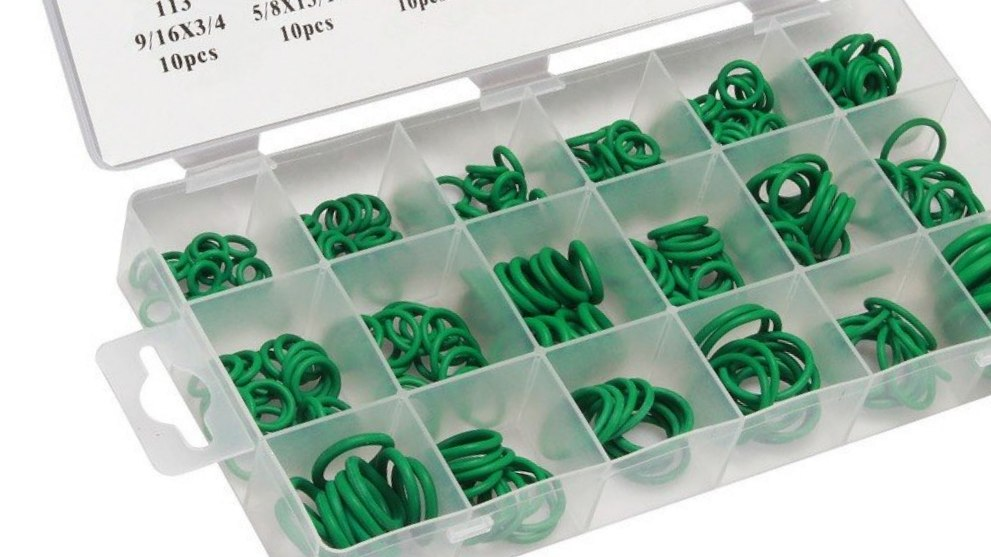
Hydrogenation is the addition of hydrogen molecules to a compound. HNBR is a product of the hydrogenation of butadiene in Nitrile rubber. Hydrogenation results in higher resistance to oils and chemicals but, more importantly, higher operating temperatures.
HNBR material has the same moderate physical properties, abrasion resistance, and resistance to petroleum oils as NBR.
Hydrogenated nitrile rubber is also used for high-performance applications like oil drilling equipment and motors.
Polychloroprene Rubber (CR/Neoprene®)
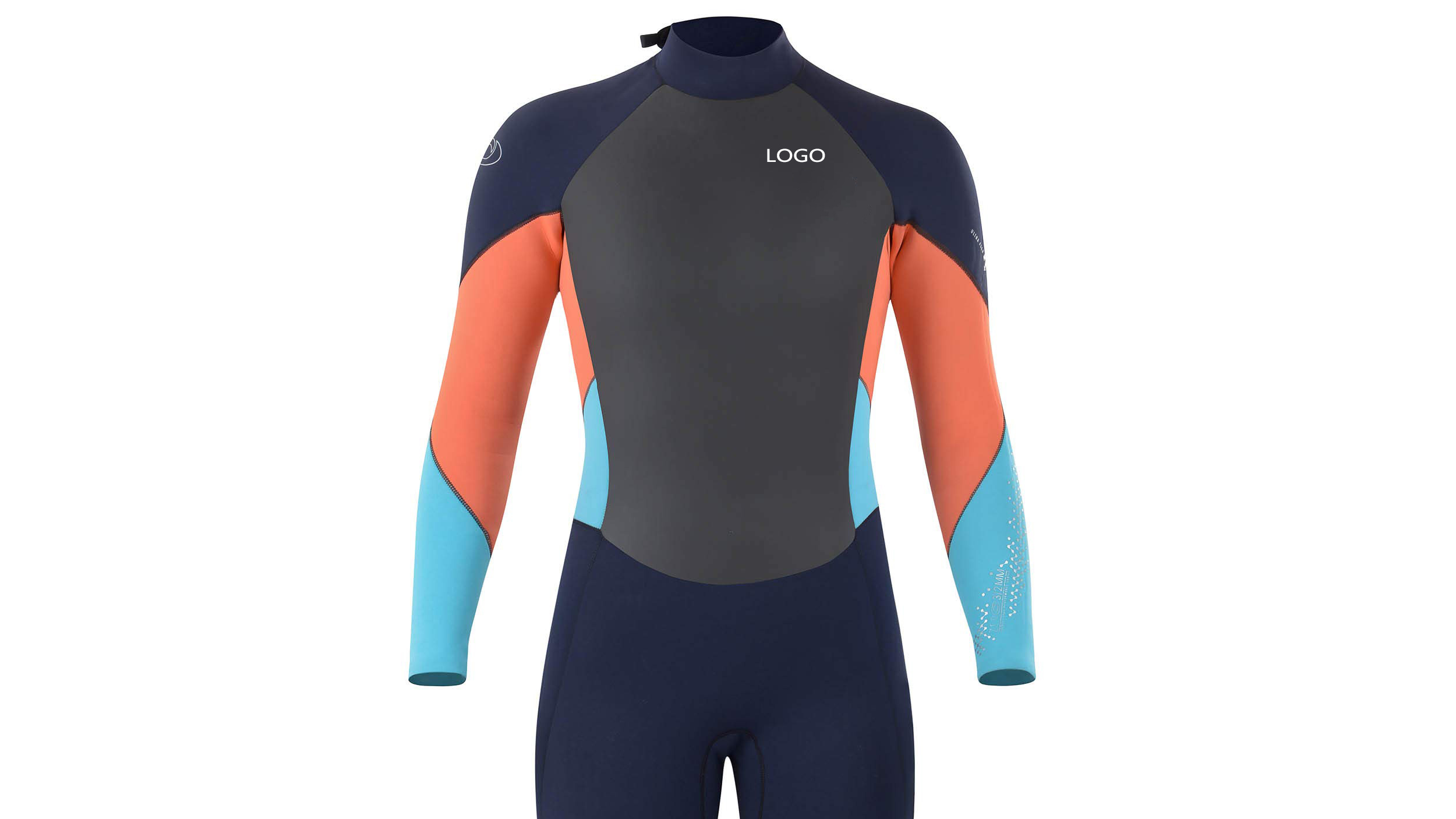
Neoprene rubber is made of a volatile and colorless liquid called chloroprene. Chloroprene is one of the oldest rubber material types, designed in the 1930s.
The DuPont company trademarked Neoprene for its rubber compound, which has become synonymous with polychloroprene rubber.
Neoprene rubber has decent oil and chemical resistance and less susceptibility to degradation and corrosion. It is weak to concentrated acids, alkalies, and a few chemical solvents.
Neoprene rubber is used in high-pressure gaskets, hoses, adhesives, weather striping, commercial and industrial safety masks, and water sports clothing.
Swimwear and diving suits are commonly made from neoprene for their excellent waterproofing.
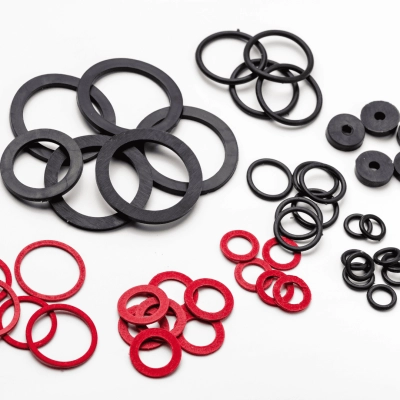
Send Your Inquiry Now!
Quality Meets Affordability. Inquire Now for High-Quality Products at Low Volumes.
Butyl Rubber (IIR)
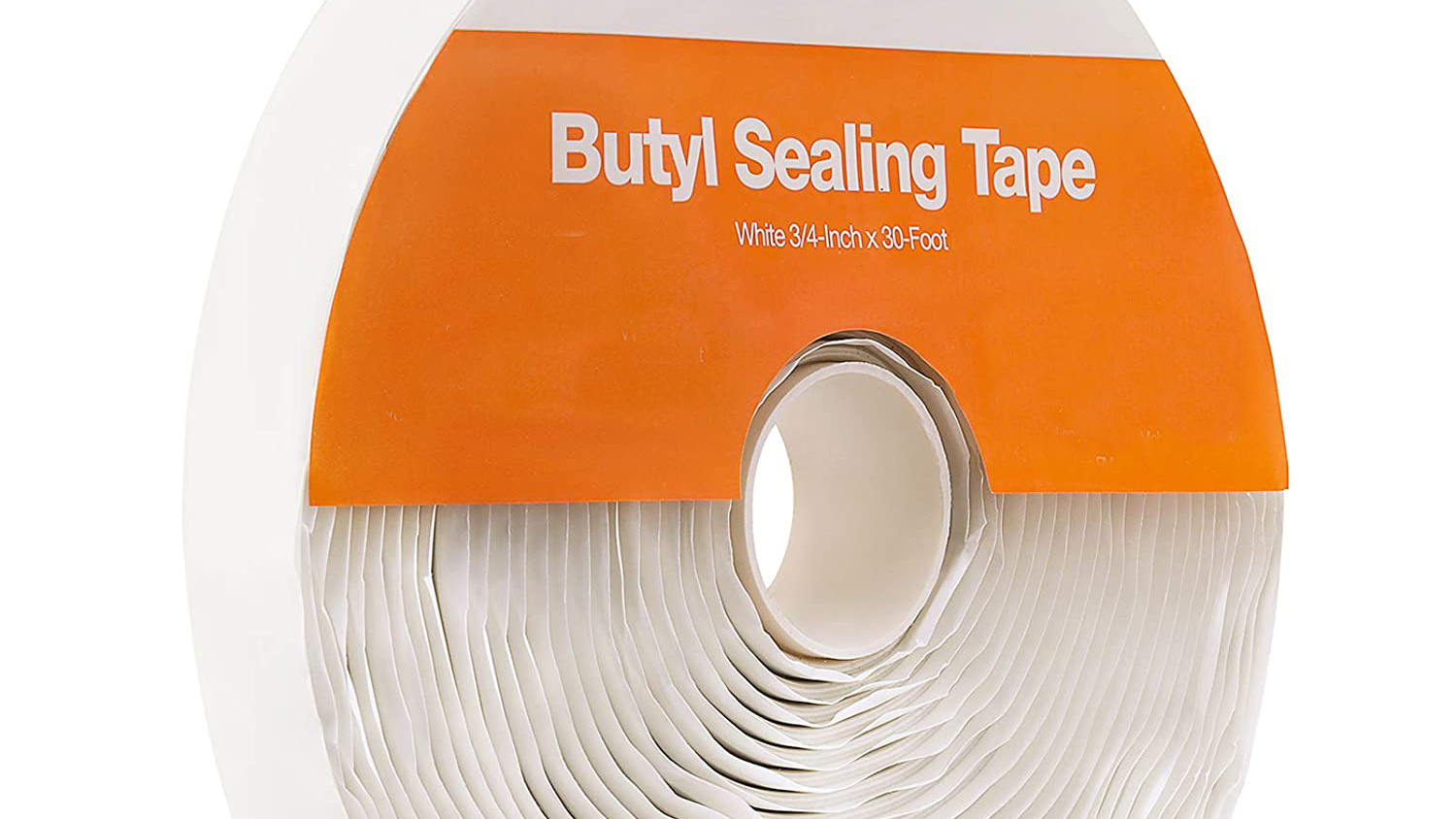
Butyl rubber (or Butyl Isobutylene Isoprene Rubber) is a synthetic elastomer with an exceptionally low gas permeability out of all the different types of rubber.
Butyl rubber has excellent chemical resistance; it can withstand concentrated acids, alkalines, and alcohol. Additionally, butyl rubber has excellent low-temperature properties and ozone resistance.
Butyl rubber is used in several applications but is heavily preferred for sealants and airtight gaskets.
You can also find butyl rubber in shoe soles, car tires, inner tubes, and bubble gum.
Ethylene Propylene Rubber (EPDM)
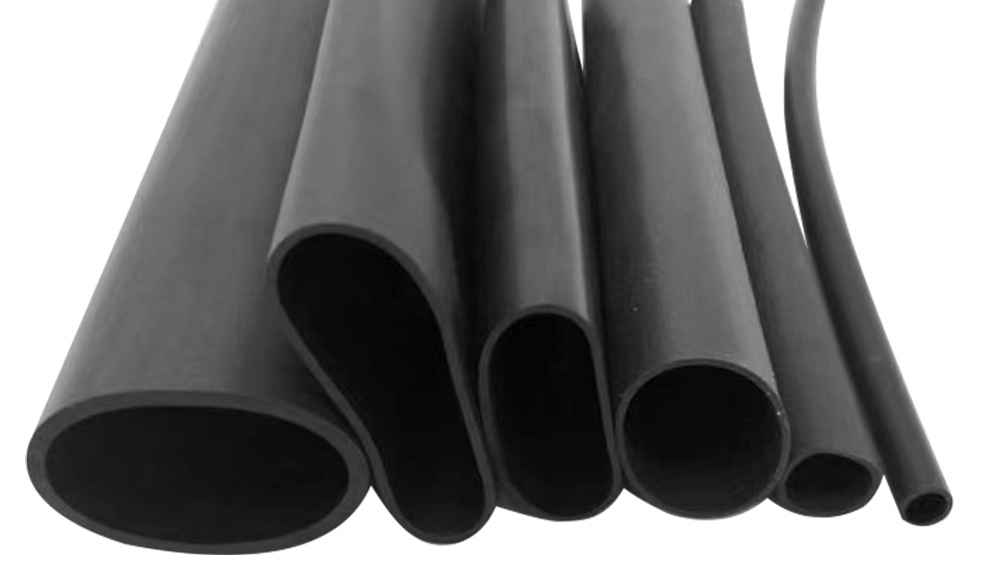
EPDM rubber is one of the most challenging and resilient synthetic rubbers. It is commonly used as a rubber foam for additional cushioning and insulation benefits.
It has good abrasion resistance, thermal and physical properties, waterproofing, and insulation capabilities. EPDM Rubber is particularly weak to fuels, solvents, and petroleum-based oils.
EPDM rubber is mainly used for outdoor applications like garden hoses, garage door seals, and door mats. It is often desired for its insulation and noise-damping properties in the automotive industry.
Polyurethane Rubber (PU)
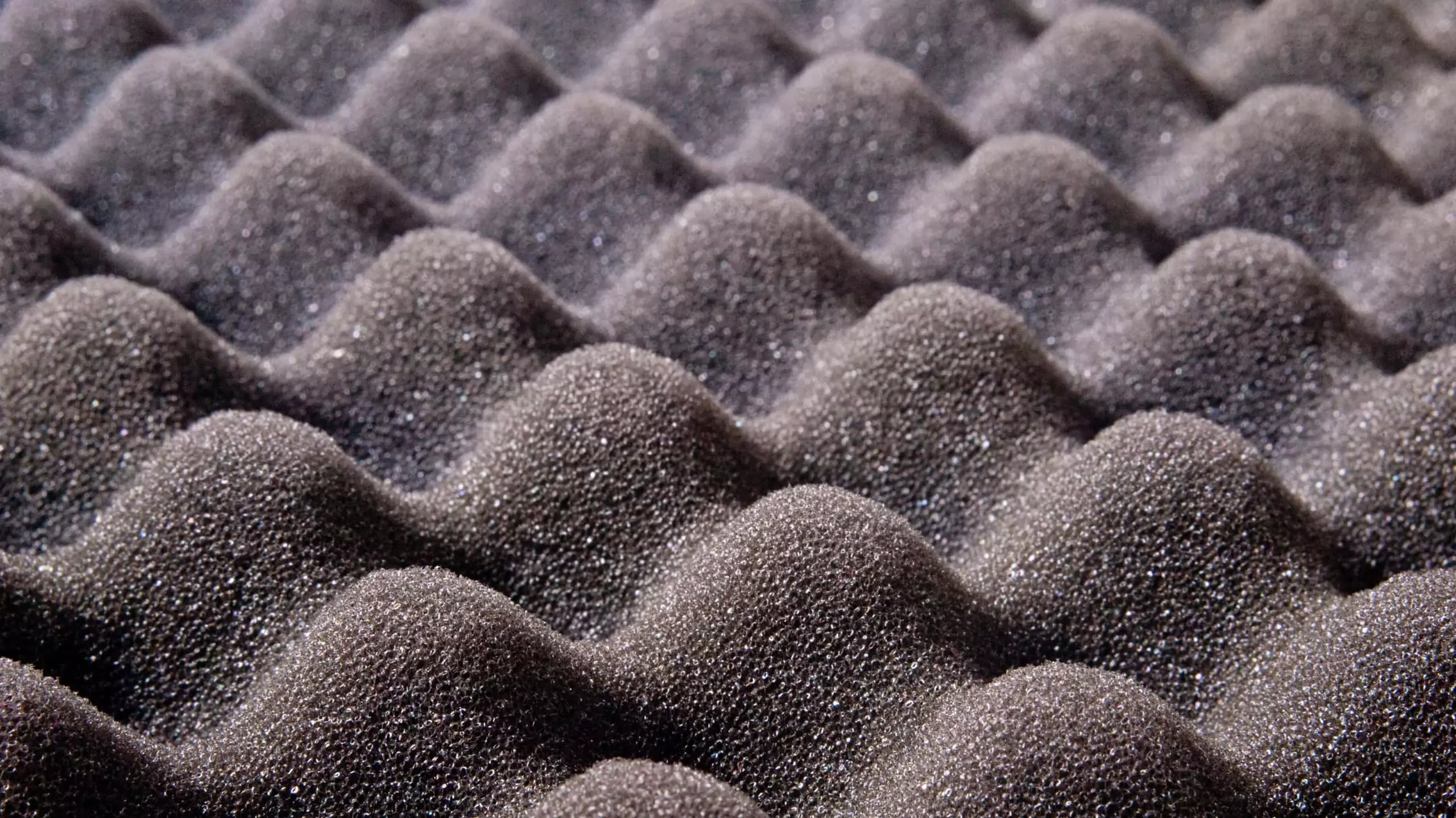
Polyurethane is a group of polymers containing organic compounds stitched together by carbon links. It is a highly flammable compound and is often mixed with other elements.
PU rubber properties are mostly shape and form-dependent. It generally has good corrosion and abrasion resistance but is susceptible to petroleum-based oils.
Most polyurethane rubber is made from rubber foams and covered with a different material. Furniture is the most common use for polyurethane foams, as it covers a wide range of products.
Cushions, pillows, seats, clothing, shoes, and carpets are all polyurethane.
The two most common types of rubbers made from polyurethane are polyether (EU) and polyester (AU).
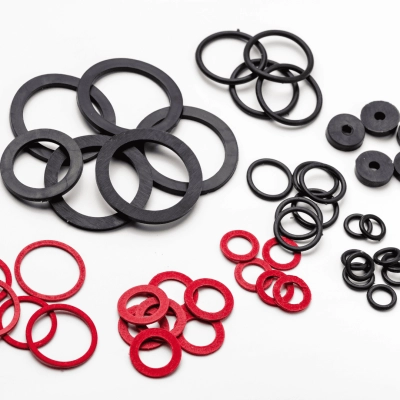
Send Your Inquiry Now!
Quality Meets Affordability. Inquire Now for High-Quality Products at Low Volumes.
Fluoroelastomer (FKM/Viton®)
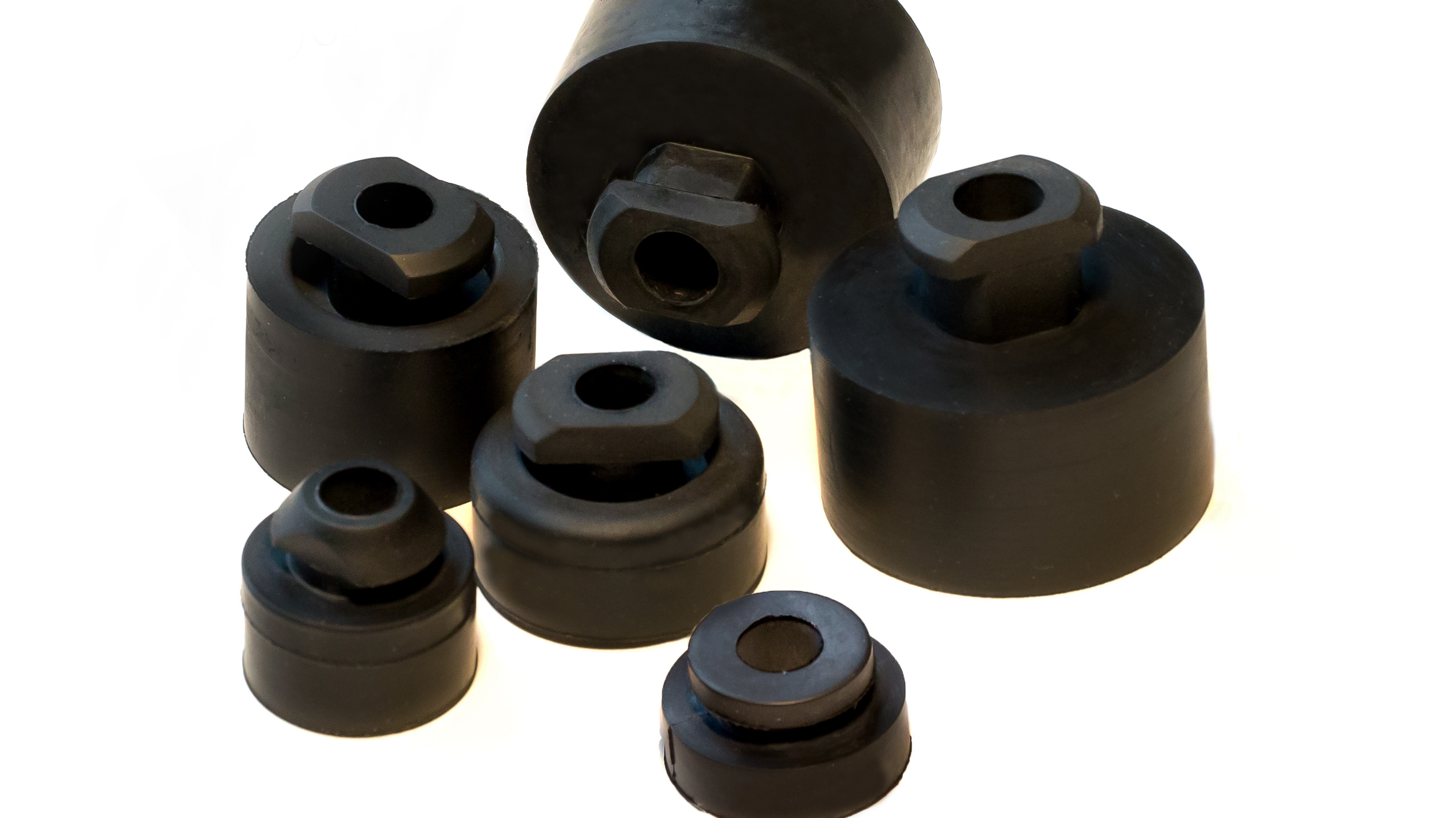
FKM is known by a few names, such as fluorocarbon rubber, fluoroelastomer, or Viton. It is an incredibly dense material with a greenish-brown hue. FKM is a rare material and rarely seen outside of industrial applications.
It is resistant to fuels, mineral oils, acids, alcohols, and solvents. Additionally, FKM has one of the highest operating temperature specifications. It is the most robust rubber material, only susceptible to certain chemicals.
FKM is primarily used in high-performance machines, like vehicles and industrial equipment. Automotive O-rings, gaskets, hoses, and industrial protective gloves are often made from FKM.
Polyacrylic Rubber (ACM)
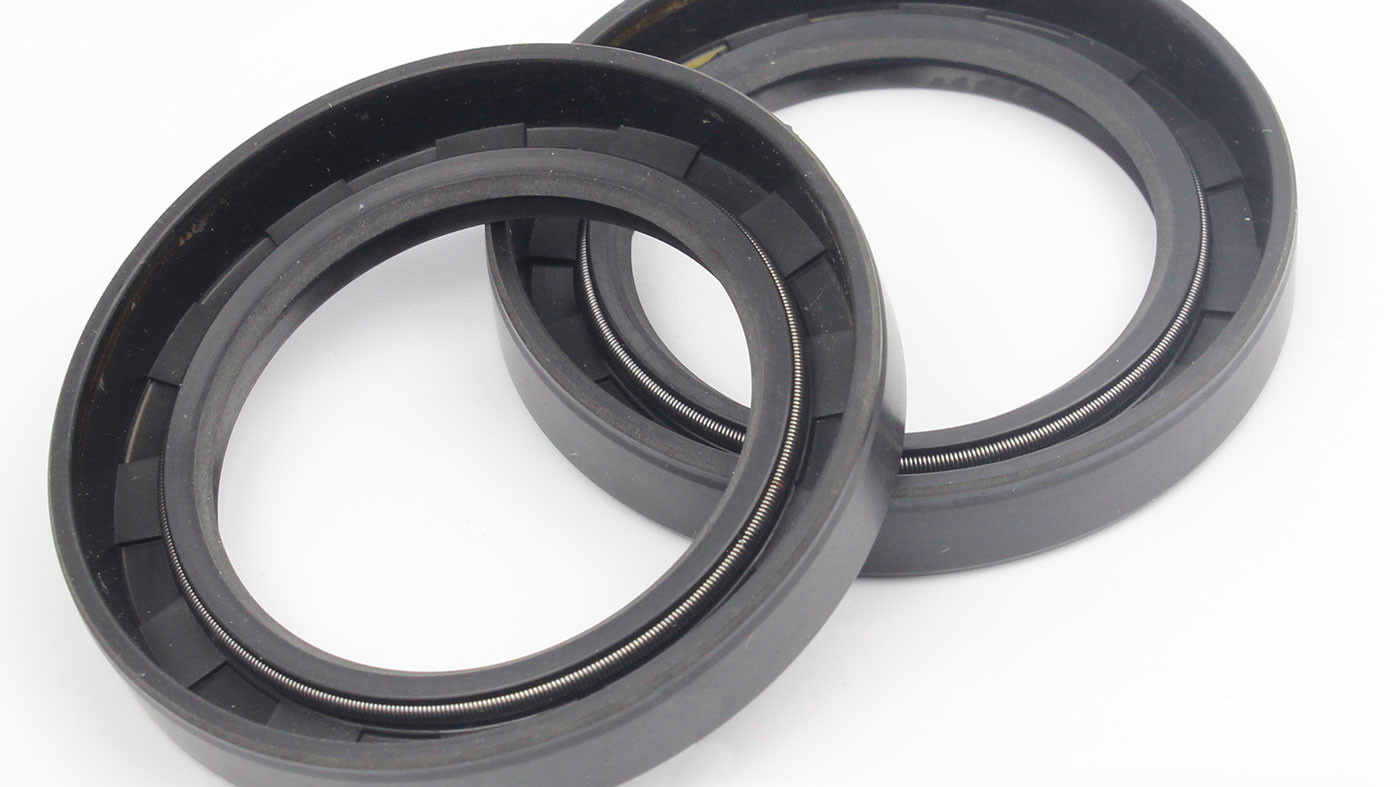
ACM is a specialized elastomer designed to have great fuel and oil resistance. As it is a specialized material, it is uncommon in general applications.
It has excellent ozone, heat, and oil resistance, making it ideal for use in engine blocks.
ACM seals, o-rings, belts, and gaskets are found in most high-temperature sections of a car engine. It can also be used as an ingredient for industrial-grade sealants and protective coatings.
Ethylene Acrylic Rubber (EA/Vamac®)
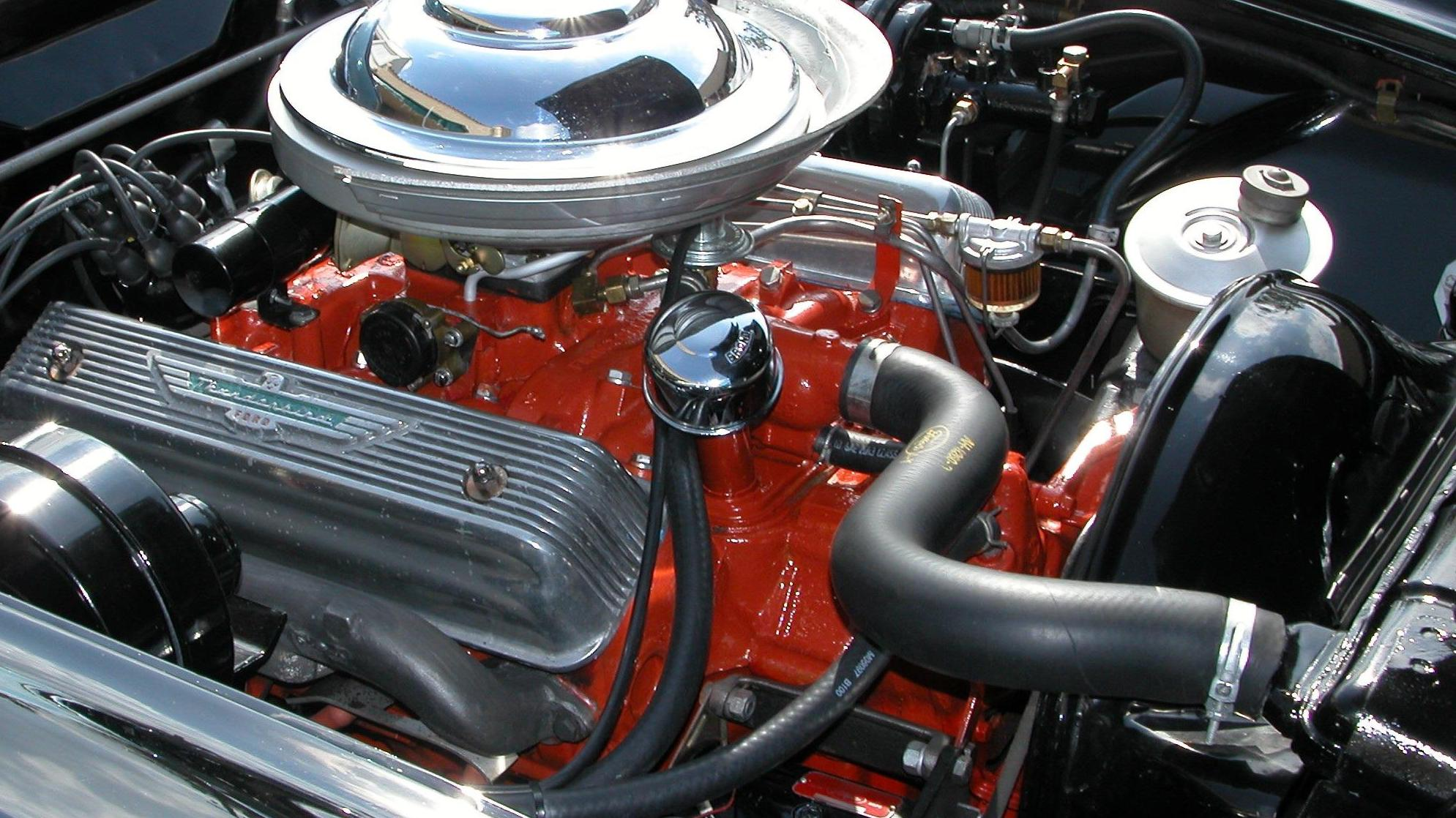
EA rubber is a common automotive material, often known by its trademarked name Vamac.
Of all the different types of rubber, EA stands out for its resistance to extreme temperatures and environmental effects.
Ethylene acrylic rubber has poor fuel resistance and is susceptible to various chemicals. It is commonly used in automotive seals, gaskets, o-rings, cables, and high-voltage connector insulation.
Epichlorohydrin (ECO/Hydrin®)
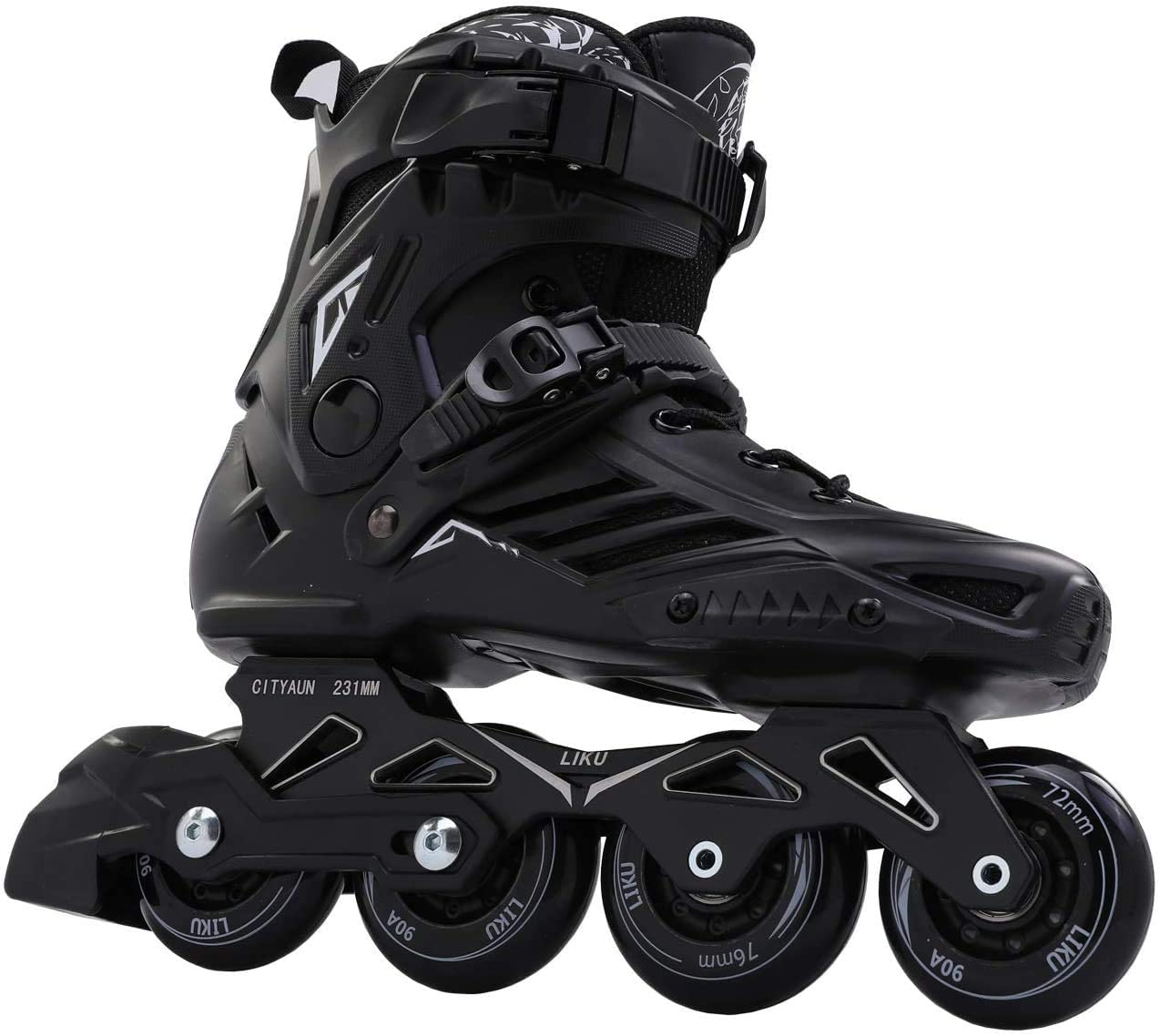
ECO stands out for its excellent weathering resistance among the many different types of rubber. It is similar to nitrile but offers key improvements in chemical resistance and operating temperatures.
Epichlorohydrin has decent material properties but has notably better fuel, oil, and solvent resistance. It is used in the automotive industry for o-rings, seals, and gaskets. Commercially, you can find ECO rubber in the roller blades of the tires.
Foam Rubber
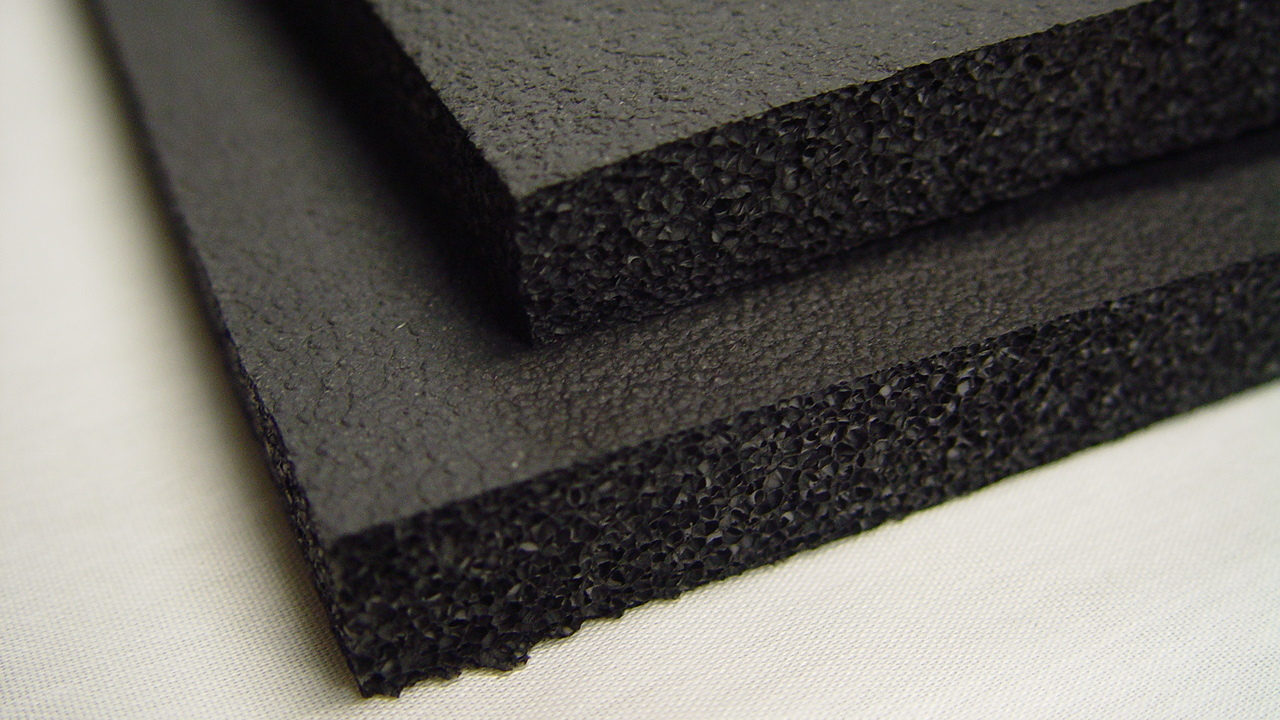
Foam rubber is not a type of rubber material but a form factor for natural rubber and synthetic rubbers.
It combines a rubber material with a foaming agent to create a matrix structure with tiny air bubbles propagating through it.
Foam rubber’s physical properties depend on the base rubber used in manufacturing. It is commonly used for in-wall insulation and stuffing for mattresses, chairs, cushions, and sofas.
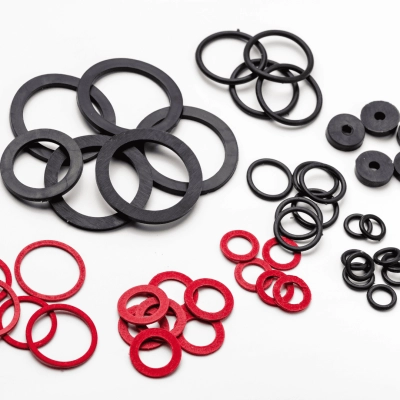
Send Your Inquiry Now!
Quality Meets Affordability. Inquire Now for High-Quality Products at Low Volumes.
Natural vs. Synthetic Rubber
Natural rubber is generally fine for most applications. But as you go towards high-performance equipment, natural rubber, the flaws of natural rubbers become evident.
Many modern-day vehicles, instruments, and equipment require more robust, durable, and resilient materials. Following is a comparison of naturally occurring rubber compounds with lab-made synthetic rubber.
Material | Elasticity | Durability | Compression Set | Abrasion Resistance | Tear Resistance |
---|
As far as physical properties are concerned, naturally occurring rubber is still the king. However, some synthetics come close to or exceed the performance of natural rubbers. Hence we still see many manufacturers and suppliers opt for the natural option.
Material | Acids | Alkalies | Fuels | Oils | Solvents |
---|
Chemical resistance comparison paints a very different picture. Almost all rubbers, natural and synthetic, struggle with most chemicals. While it may seem like an even match-up between natural and synthetic rubbers, it is slightly favored towards one side.
Synthetic rubbers also struggle with chemicals but offer a much more comprehensive range of material choices than one realistic option. Additionally, some synthetic options are far superior in certain situations.
Material | Cold | Heat | Flame | Gas Permeability | Ozone | Water |
---|
Finally, we see an apparent defeat for natural rubber. Despite showing average resistance to most environmental effects, synthetics left it in the dust. With a few exceptions, almost every synthetic rubber outperformed its natural counterpart.
Other than water resistance, natural rubbers could not compete with synthetic options. Temperature and ozone resistance are desirable properties for all outdoor rubber applications, and the synthetic options offer an overall better choice.
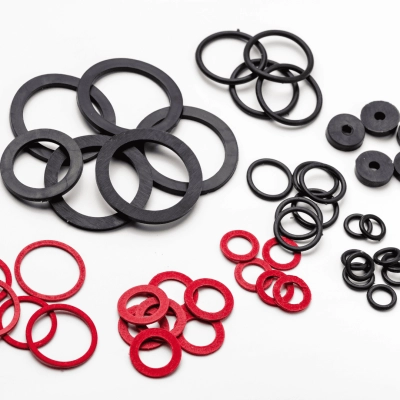
Send Your Inquiry Now!
Quality Meets Affordability. Inquire Now for High-Quality Products at Low Volumes.
Conclusion
Rubbers are very diverse in nature and physical properties. While natural rubbers generally offer excellent properties, they are outmatched by synthetic rubbers in most situations.
Each type of rubber has further subtypes and formulations that strengthen individual attributes.
When selecting a material for your projects, pay close attention to individual properties. Then ask the manufacturer to fine-tune the materials to meet your tolerances.
Why go to Hongju for your Rubber Manufacturing needs?
Hongju is one of China’s leading manufacturers and wholesale suppliers of rubber products. We offer several OEM and ODM services, including Compression Molding, Injection Molding, and Die-Cutting.
Additionally, we have flexible minimum order quantities and quick turnaround times. Come and contact us quickly!