In this article, we delve into the world of EPDM rubber and its performance under the influence of extreme temperatures. Discover how this resilient material thrives in both the heat of industrial operations and the chill of outdoor settings. Whether it’s automotive components, industrial machinery, or outdoor applications, EPDM rubber showcases its capability to handle temperature extremes with unwavering competence.
What is EPDM Rubber?
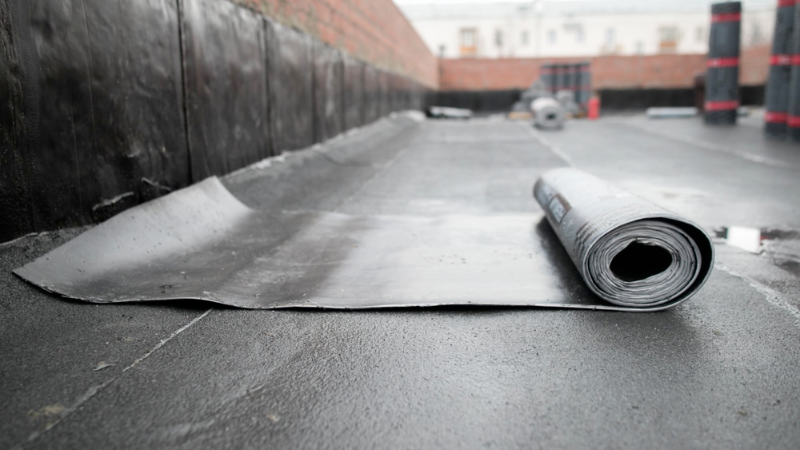
EPDM(ethylene propylene diene monomer) is a synthetic rubber known for its exceptional durability and resistance to various environmental factors. It is widely used in a range of industries due to its versatile properties, including excellent weather resistance, tear resistance, abrasion resistance, electrical insulation, and chemical resistance.
EPDM rubber is created through the polymerization of ethylene, propylene, and a diene monomer, resulting in a flexible and resilient material that can thrive in diverse conditions. This high-temperature-resistant rubber material provides the possibility to produce high-reliability seals at temperatures beyond the range of traditional rubber materials.
EPDM rubber is characterized by its ability to maintain its integrity even when exposed to extreme temperatures, making it a popular choice for applications that require long-term performance in both hot and cold environments.
Does EPDM Rubber Have Good Heat Resistant Properties?
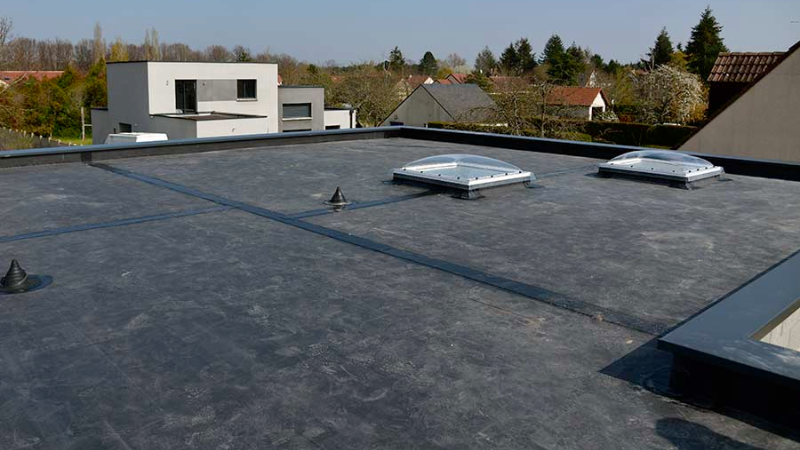
EPDM synthetic rubber, short for Ethylene Propylene Diene Monomer, stands as one of the front-runners in the domain of rubber materials known for temperature endurance. Its makeup differentiates it from natural rubber and places it in the cadre of high-performing synthetic rubbers when it comes to heat resistance.
- Temperature Spectrum: EPDM, often hailed as an extreme temperature rubber, can consistently withstand temperatures from as low as -40°C (-40°F) to highs around 150°C (302°F) for short intervals. This spectrum positions it well above many other rubber materials in terms of heat tolerance.
- Comparison with Alternatives: When juxtaposed with EDPM and silicone rubber, both these materials are recognized for their high-temperature stability. However, EPDM’s unique molecular structure offers excellent resistance not just to heat but also to UV radiation, ozone, and several chemical agents. It’s worth noting, however, that EPDM has a relatively poor fuel resistance, especially when compared to conventional nitrile rubber.
- Applications: EPDM’s status as a particular extreme temperature rubber has led to its widespread adoption in industries that demand high-temperature resistant rubber. From automotive seals, that encounter engine heat, to roofing materials that must bear the brunt of the sun, EPDM’s heat resistance is a key factor in its selection.
Inquire About Our Silicone and Plastic Products!
How Can You Test the Heat Resistance of EPDM Rubber?
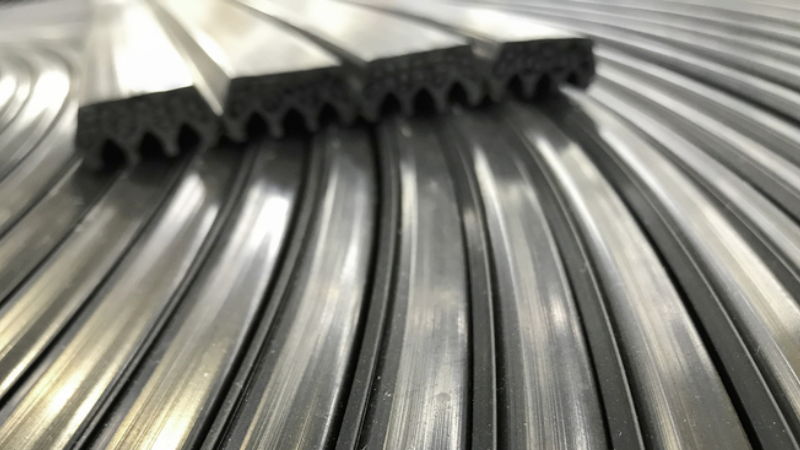
Evaluating the heat resistance of EPDM rubber is crucial to ensure its suitability for specific applications. Various testing methods are employed to assess how well EPDM rubber performs under elevated temperatures. Some common techniques include:
- Heat Aging Test: In this test, EPDM rubber samples are exposed to elevated temperatures for an extended period, simulating real-world conditions. The samples are then assessed for changes in physical properties, such as hardness, tensile strength, elongation, and color. Any significant alterations in these properties can indicate the material’s performance under heat stress.
- Oven Aging Test: EPDM rubber samples are placed in an oven at a specified temperature for a predetermined time. After exposure, the samples are examined for changes in their physical and mechanical properties. This test helps to determine the material’s resistance to heat-induced degradation.
- Dynamic Mechanical Analysis (DMA): DMA involves subjecting EPDM rubber samples to varying temperatures and frequencies while measuring their mechanical responses. This test provides information about the rubber’s viscoelastic behavior under different thermal conditions.
- Thermogravimetric Analysis (TGA): TGA is used to analyze the weight loss of EPDM rubber as it is heated. It helps identify the temperature at which significant degradation or decomposition occurs.
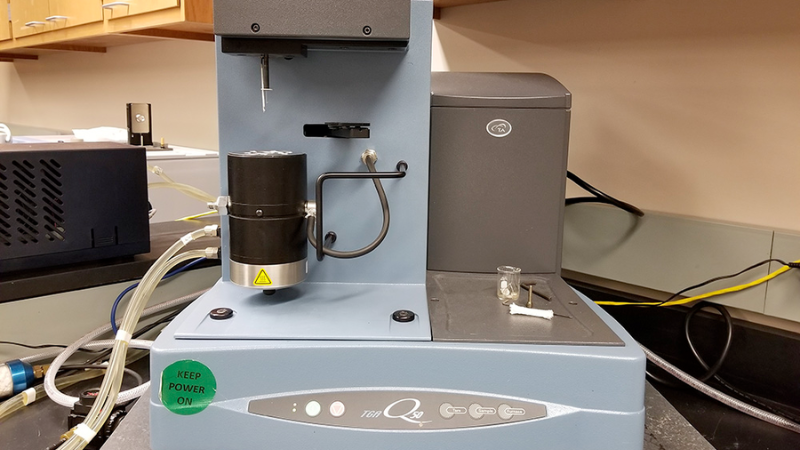
These tests collectively provide a comprehensive understanding of EPDM rubber’s excellent resistance to heat, enabling engineers and manufacturers to select the appropriate rubber formulation for specific temperature-sensitive applications. Proper testing ensures that EPDM rubber maintains its integrity and performance even in extreme heat environments.
Moreover, testing laboratories often conduct additional evaluations such as Fourier Transform Infrared Spectroscopy(FTIR) and Differential Scanning Calorimetry (DSC). FTIR helps identify any chemical changes that may occur due to heat exposure, while DSC measures the thermal behavior of the EPDM rubber.
Inquire About Our Silicone and Plastic Products!
What Factors Affect the Heat Resistance of EPDM Rubber Products?
EPDM rubber is known for its excellent resistance to heat, making it a popular choice in various industries. However, several factors influence how well EPDM rubber can handle extreme temperatures. Let’s delve into these key factors to gain a better understanding of EPDM’s high-temperature stability.
Composition and Formulation
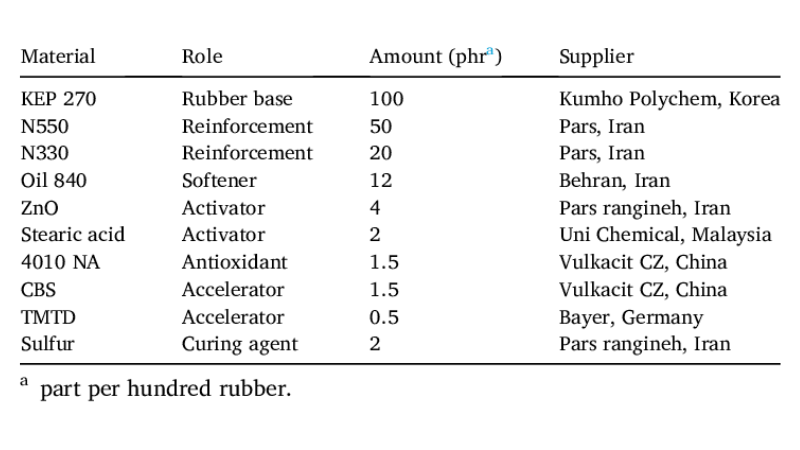
The composition and formulation of the EPDM compound have a significant impact on excellent resistance to heat. Different manufacturers may use varying recipes, resulting in different levels of thermal stability. The type and quality of raw materials used, such as ethylene, propylene, and diene monomers, affect the overall performance of the EPDM rubber.
Fillers, Additives, and Curing Agents
Fillers, additives, and curing agents also play crucial roles in influencing the thermal stability of EPDM rubber products. Various fillers like carbon black or silica are commonly added to improve mechanical properties but can influence thermal conductivity differently. Similarly, additives like antioxidants or UV stabilizers can enhance heat resistance by preventing degradation caused by high temperatures.
Curing agents are responsible for crosslinking the polymer chains in EPDM rubber during vulcanization. The choice of curing agent affects not only the physical properties but also the heat resistance of the final product. For instance, peroxides are commonly used as curing agents for high-temperature applications due to their ability to form strong crosslinks.
Crosslink Density
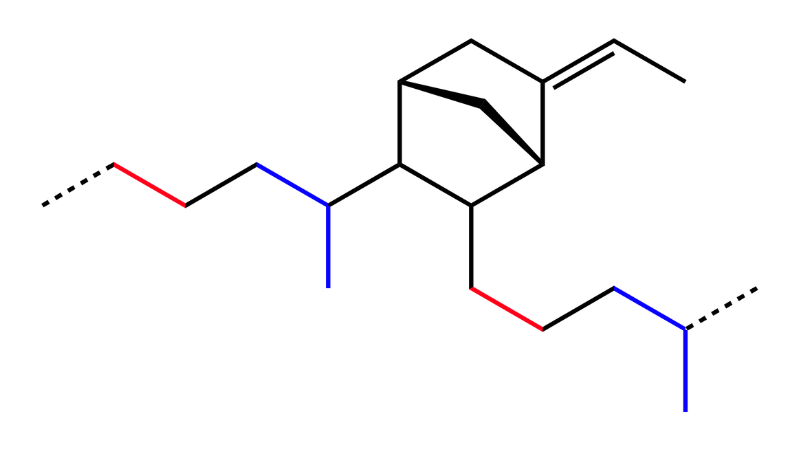
Crosslink density is a critical factor that determines the maximum operating temperature range for EPDM rubber products. It refers to the number of chemical bonds between polymer chains within the material structure. Higher crosslink density results in improved heat resistance as it enhances stability at elevated temperatures.
Reinforcing Fibers
The presence or absence of reinforcing fibers can significantly impact the heat resistance of EPDM rubber products. Reinforcements like aramid or glass fibers provide additional strength and rigidity to the rubber, but they can also affect its thermal properties. The fibers act as conductive paths for heat transfer and may alter the overall thermal behavior of the EPDM compound.
Inquire About Our Silicone and Plastic Products!
Evaluating EPDM Rubber’s Heat Resistance Properties
EPDM rubber is known for its exceptional heat resistance, making it a popular choice for various applications that involve extreme temperatures. When considering the suitability of EPDM rubber for such conditions, it is crucial to evaluate its heat aging characteristics, mechanical properties, and thermal stability.
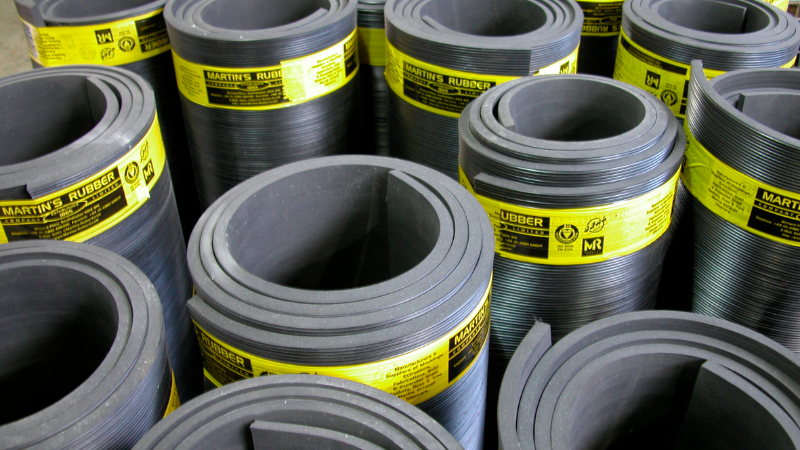
Understanding Mechanical Properties
Mechanical properties play a vital role in determining EPDM rubber’s ability to withstand extreme temperatures. Tensile strength and tear resistance are among the critical aspects evaluated during testing. These properties help assess how well the material can maintain its structural integrity when exposed to high temperatures.
EPDM rubber typically exhibits excellent tensile strength even at elevated temperatures. This characteristic ensures that it can resist deformation or failure when subjected to significant stress or strain caused by thermal expansion or contraction.
Furthermore, tear resistance is essential as it determines the material’s ability to resist tearing or cracking under mechanical stress at high temperatures. EPDM’s inherent tear resistance makes it highly suitable for applications where extreme temperature fluctuations occur.
Assessing Thermal Stability
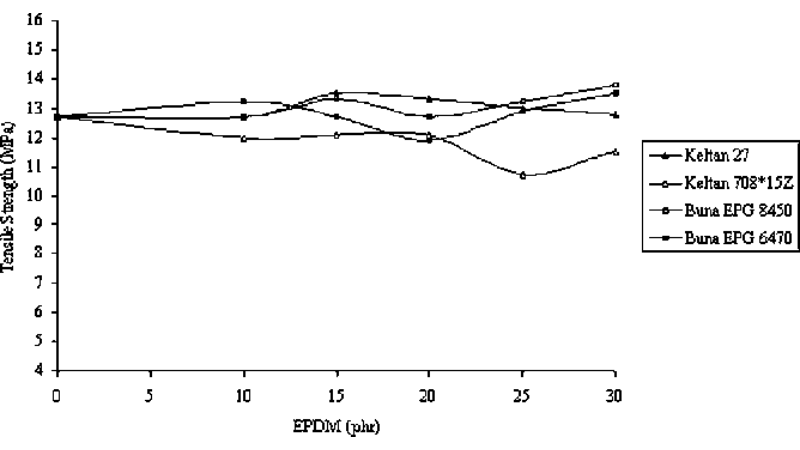
Thermal stability is another crucial factor when evaluating EPDM rubber’s performance in extreme temperature environments. Weight loss measurements and changes in other material properties provide insights into its ability to withstand prolonged exposure to high temperatures.
By subjecting samples of EPDM rubber to controlled heating over time, any weight loss can be measured accurately. This indicates how well the material retains its mass and structure under elevated temperatures. Changes in electrical properties can also indicate thermal degradation.
Understanding these factors helps determine whether EPDM rubber is suitable for applications involving extreme temperatures. The ability to maintain its physical properties, mechanical strength, and thermal stability under such conditions makes it a reliable choice.
Inquire About Our Silicone and Plastic Products!
Applications Requiring High Heat Resistance with EPDM Rubber
EPDM rubber is a high-temperature-resistant rubber that can handle extreme temperatures, making it ideal for various applications. From automotive engine components to HVAC systems and roofing membranes, EPDM rubber offers excellent heat resistance in outdoor environments.
Automotive Engine Components
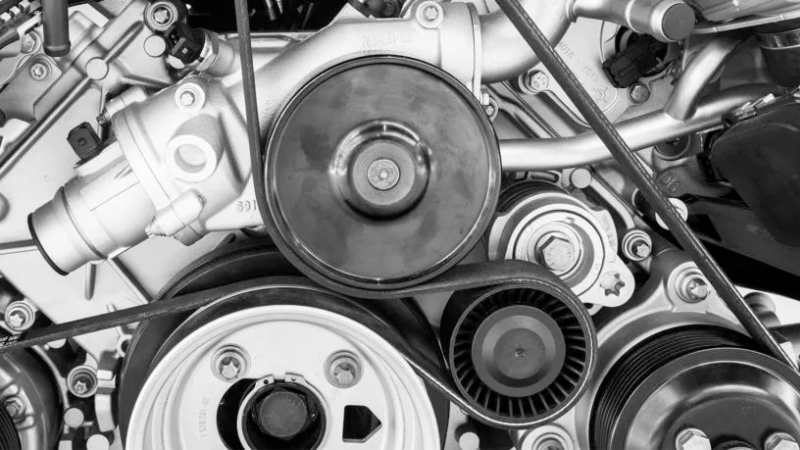
One of the primary uses of EPDM rubber is in automotive engine components that are exposed to high temperatures. The material’s exceptional heat resistance allows it to withstand the intense heat generated within engines without degrading or losing its functionality. EPDM rubber seals, gaskets, and hoses ensure that the engine operates efficiently even under extreme conditions.
HVAC Systems
EPDM rubber plays a crucial role in heating, ventilation, and air conditioning (HVAC) systems. These systems often encounter hot air and coolant fluids, which can be detrimental to standard materials. However, EPDM’s excellent heat resistance makes it an ideal choice for HVAC applications. Whether it’s sealing ducts or insulating pipes, EPDM ensures optimal performance by withstanding the high temperatures encountered in these systems.
Roofing Membranes for Commercial Buildings
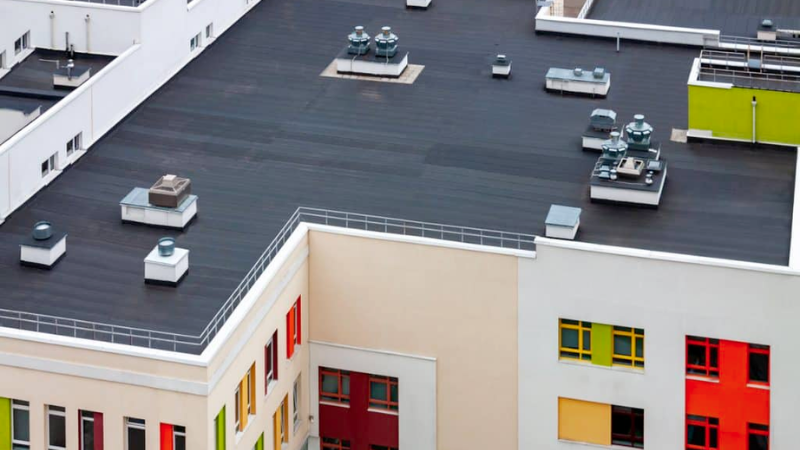
Commercial buildings require roofing materials that can endure harsh weather conditions while providing effective insulation. This is where EPDM roofing membranes excel. These membranes are made from EPDM rubber and offer outstanding heat resistance properties, making them perfect for commercial roofs exposed to direct sunlight and temperature fluctuations. With their ability to withstand UV radiation and resist thermal degradation, EPDM roofing membranes provide long-lasting protection against extreme temperatures.
Electrical Insulation Products
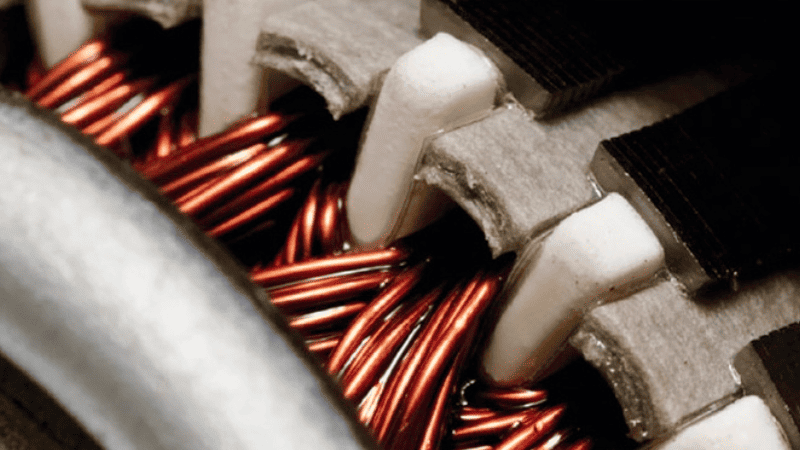
EPDM rubber finds extensive use in electrical insulation products due to its excellent thermal stability. It is an effective insulator even at high temperatures, ensuring safety and reliability in electrical applications. EPDM-based electrical insulation products offer superior performance when exposed to extreme temperatures, from cable jackets to connectors and insulating tapes.
In addition to its remarkable heat resistance capabilities, EPDM also exhibits other desirable properties. It boasts excellent resistance to corrosive chemicals, making it suitable for applications where exposure to aggressive substances is a concern. EPDM rubber also demonstrates low flammability, ensuring enhanced safety in environments with fire hazards.
Inquire About Our Silicone and Plastic Products!
Conclusion
EPDM rubber excels in extreme temperatures, making it a go-to material for industries facing harsh conditions. Its UV, ozone, and chemical resistances further enhance its versatility, benefiting both silicone producers and their B2B clients.
Experience the Hongju Advantage with EPDM Rubber
Are you a silicone producer looking for natural or synthetic rubber materials that stand the test of temperature extremes? Dive deeper into the benefits of EPDM rubber with Hongju Silicone. Contact us today to explore how EPDM can elevate the quality and durability of your products.