In this guide, we will cover everything you need to know about EPDM rubber. But what are the benefits of EPDM rubber, and how is it different from other types of rubber? In this guide to EPDM rubber, you will understand everything from its components to its manufacturing, advantages, and uses.
What is EPDM Rubber?
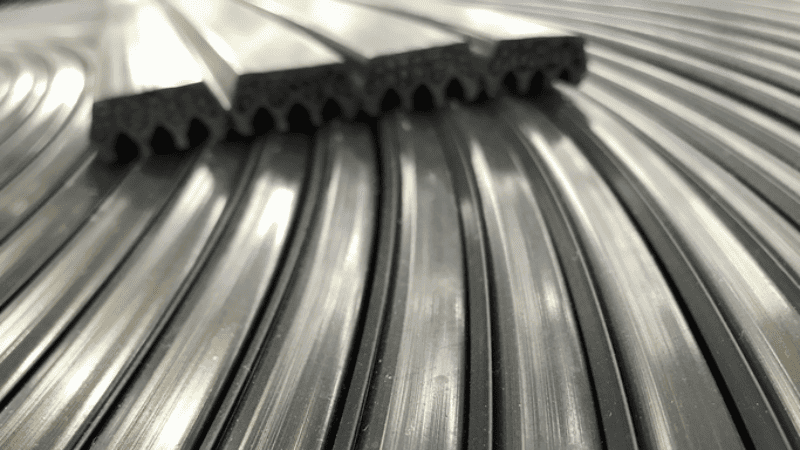
EPDM is a synthetic rubber made from ethylene, propylene, and a diene monomer. It was first developed in the 1960s by researchers at the Exxon Corporation. EPDM rubber is classified as an M-Class elastomer according to the ASTM D-1418 standard. This category is primarily defined by a polymer backbone with saturated polyethylene chains, often called “polymethylene.”
Expertly recognized for its superior performance in exterior applications, EPDM stands out for its exceptional resistance to environmental wear-and-tear factors, including ozone exposure, ultraviolet (UV) rays, and oxidation process. As a high-density synthetic rubber, it is especially valued for its ability to create dependable seals, even in environments subject to extreme cold, making it a top choice for low-temperature applications.
Chemistry of EPDM Rubber
As mentioned earlier, EPDM comprises ethylene, propylene, and diene monomers. This unique combination is what makes the material undergo cross-linking with sulfur. Cross-linking is an important process for enhancing its durability and elasticity. When examining the mechanical properties of EPDM, it is evident that it possesses a lower density than Thermoplastic Polyurethane (TPU), which results in a lighter material. It also shows lesser tensile strength, meaning it is not as rigid or prone to stretching under tension.
Furthermore, EPDM exhibits a reduced tensile modulus, indicating it is more flexible and softer than TPU. And then EPDM’s hardness is lower. This means it is less resistant to surface indentation and abrasion, yet this contributes to its high flexibility and resilience in various applications.
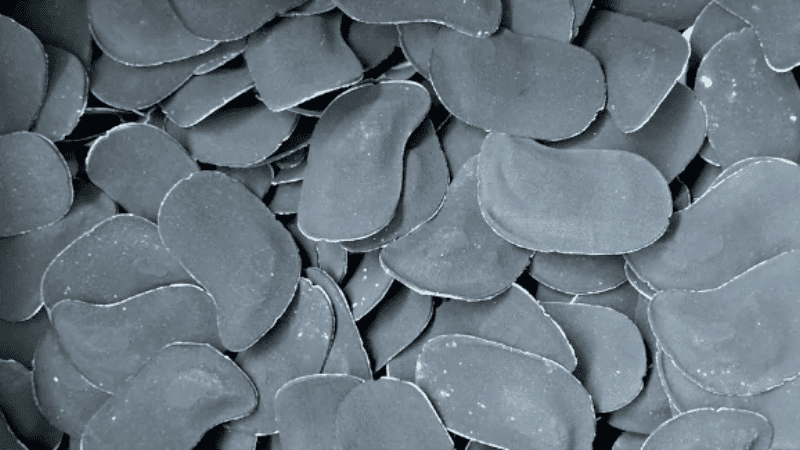
So, how does cross-linking take place, and why is it important? Well, Cross-linking in EPDM rubber is achieved through accelerated sulfur vulcanization. To enhance the thermal stability and lower the compression set, a co-agent-assisted peroxide cure is often utilized. Sulfur vulcanization transforms polymers like natural rubber into more durable materials by heating them with sulfur or sulfur-based compounds.
During this chemical process, sulfur creates cross-linking bridges between polymer chains, significantly altering the material’s mechanical and elastic characteristics. This cross-linking is crucial for EPDM, as it contributes to its desired properties, such as high flexibility and longevity under various environmental conditions. You see EPDM rubber roofing as one of the most durable options.
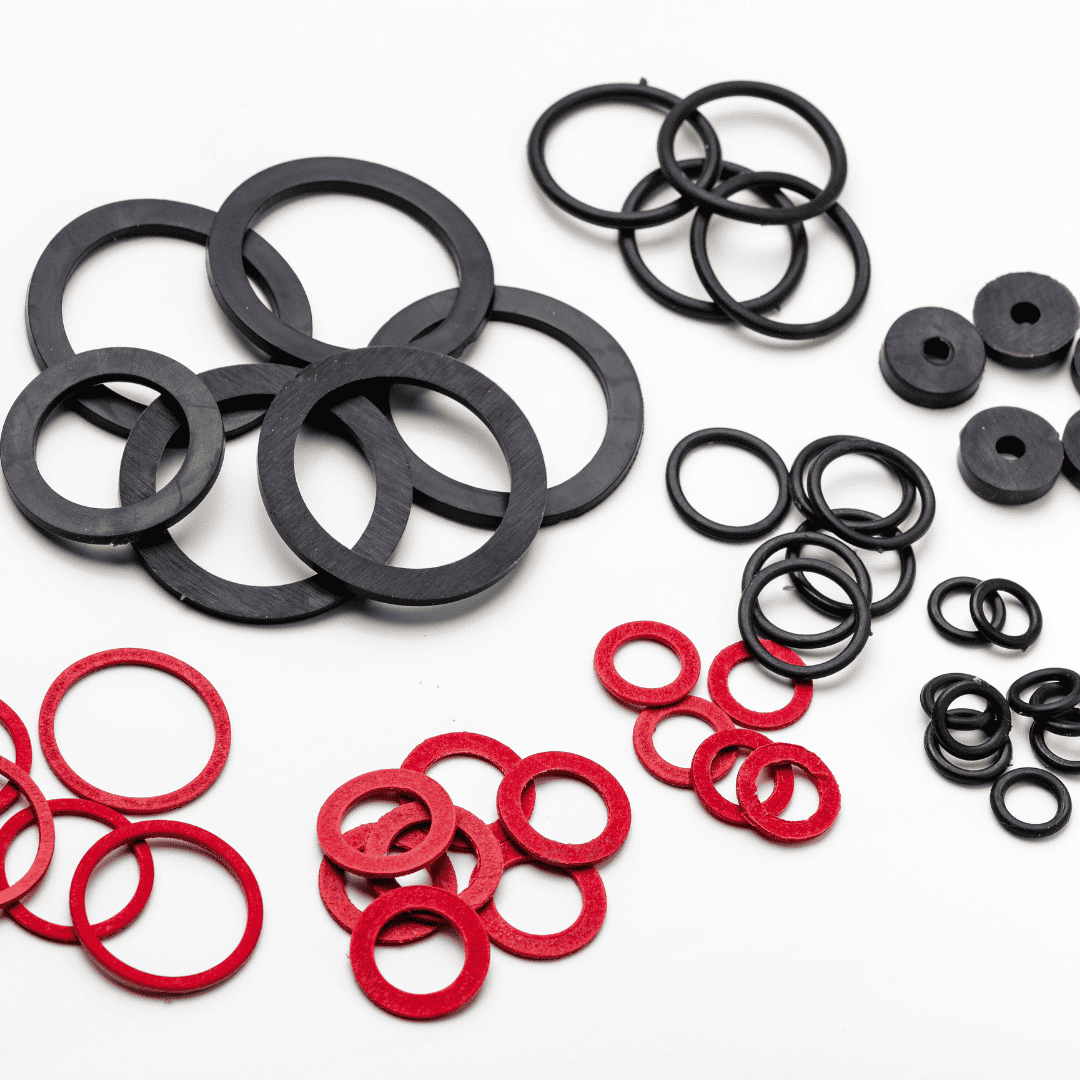
Send Your Inquiry Now!
Quality Meets Affordability. Inquire Now for High-Quality Products at Low Volumes.
Advantages of EPDM Rubber
EPDM rubber has vast applications, which means they are not limited to EPDM roofs or EPDM roofing systems only. This vast usage of EPDM rubbers is their countless advantages. Here are just some of the many advantages of EPDM rubber:
1. Lasting Resistance
One of the standout advantages of EPDM rubber is its exceptional durability. This material is stronger than many natural and synthetic rubbers regarding withstanding wear and tear. It resists tearing and abrasion, meaning it will not get damaged easily. This makes EPDM ideal for surfaces and products exposed to harsh conditions.
2. Thermal Efficiency
Energy efficiency is another key benefit of EPDM, particularly when used in roofing. Its naturally black color helps soak up the sun’s warmth. In cooler climates, this type of EPDM roofing system helps buildings stay warm by retaining heat, which can lower heating costs and increase the roof life as well.
3. Ozone and Chemical Resistance
EPDM stands out for its ability to fight off damage from ozone and chemicals. It has a top-notch ozone-resistant rating, protecting against the sun’s harmful effects. Being ozone-resistant ensures that the material does not crack or degrade when exposed to the high levels of ozone found in urban environments.
4. Fire Retardant Properties
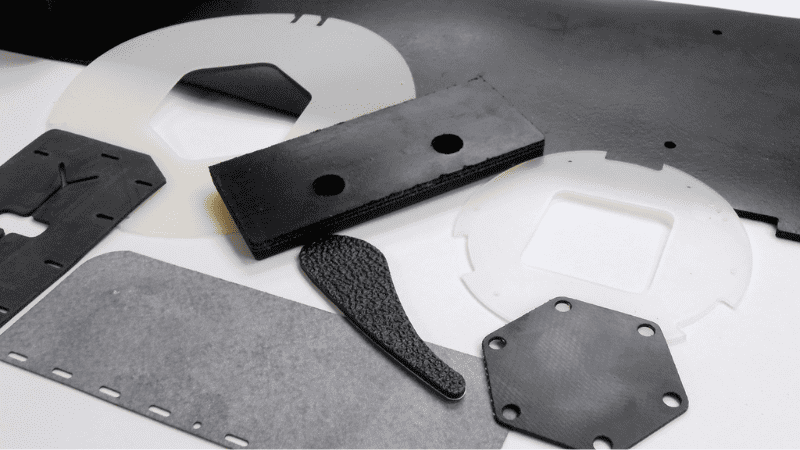
In the face of fire, EPDM can help by being fire-resistant. Not only does it resist catching flame, but it can also slow down the spread of fires. This attribute makes it a safer option for numerous applications, particularly in building construction.
5. Exceptional Water Resistance
Regarding water resistance, EPDM outperforms many other rubbers. This makes it the go-to choice for outdoor and wet applications. Whether it is an EPDM roof surface or a sealant, EPDM material ensures that water doesn’t penetrate, protecting structures and components from moisture damage.
Applications of EPDM Rubber
The following are three of the major areas where EPDM rubber is used:
Industries
In the industrial world, EPDM rubber plays an important role and has several uses and applications. Gasket seals and O-rings benefit from their impermeability to water, while grommets, vital for cable management, capitalize on their insulating properties. In the world of the HVAC industry, EDPM rubber is known for forming essential components like tubing, seals, and insulation. Its consistent performance under variable weather conditions and different temperature ranges makes it indispensable for ensuring the efficiency and safety of HVAC systems.
Construction
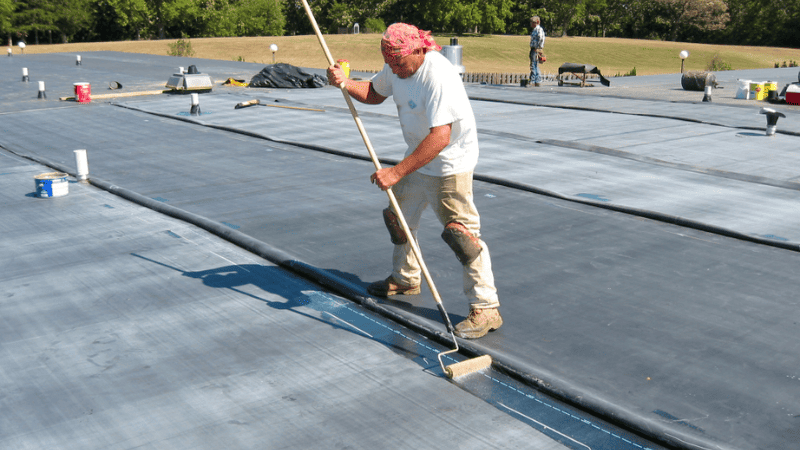
EPDM’s water-resistant traits are perfect for creating watertight EPDM membranes and versatile sealants. But it is not limited to this only! Its resilience also makes for dependable garage door seals and pool liners that can withstand fluctuating temperatures and exposure to sunlight. Builders trust EPDM’s ability to provide long-term protection against the elements. That’s why you see an EPDM rubber roof ranks among the most trusted roofing options available for even commercial buildings.
Automotive
The automotive industry is one of the fastest-growing industries in the world. And that’s where the use of EPDM roofing material has increased. And that’s not something to be shocked by. EPDM rubber proves vital in the automotive industry, with applications ranging from weatherproofing seals around doors and windows to durable brake system components and even the elastic tubing and hoses that underpin a vehicle’s fluid transport system. Additionally, windshield wipers rely on EPDM for its flexible yet sturdy nature, ensuring clear visibility in harsh conditions.
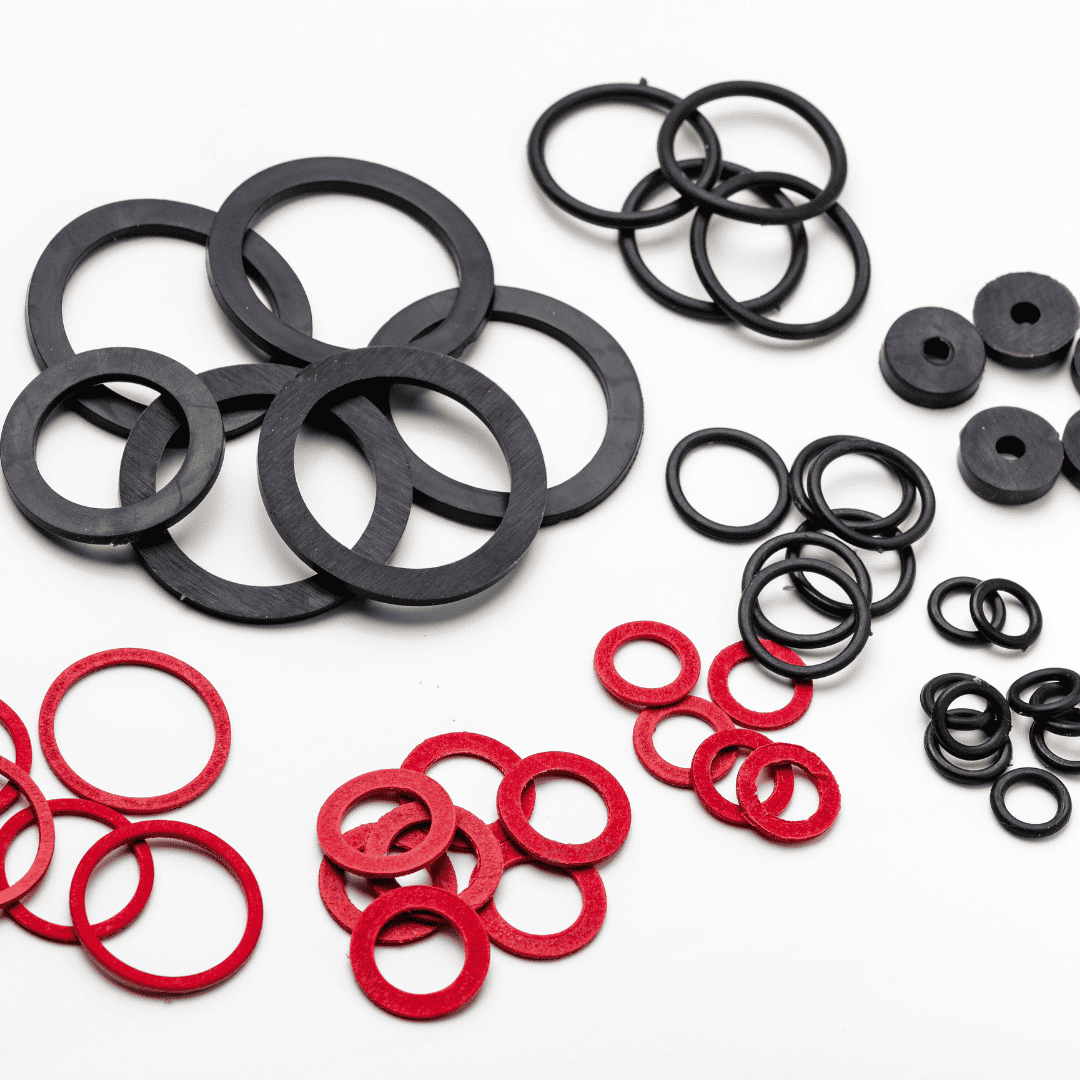
Send Your Inquiry Now!
Quality Meets Affordability. Inquire Now for High-Quality Products at Low Volumes.
Manufacturing and Processing of EPDM Rubber
EPDM rubber is not in a ready-to-use form. It has to go with a proper manufacturing and processing stage from where you get an EDMP rubber that can be used for different applications.
The manufacturing process of EDPM rubber goes through four main processes/steps. The first one is:
1. Polymerization
In this first process, various monomers are prepared and combined. Here, the mixing process starts in a reactor that mixes the material while controlling the temperature. To kick off the reaction, a catalyst solution is added. This all happens mainly in liquid form with extra propylene, which acts not only as an ingredient but also as a diluent to keep everything consistent.
During the entire process, there is a constant eye on the speed of the polymerization process. The speed depends on how much catalyst is introduced, and the temperature is easily maintained by evaporating some of the propylene. As the EPDM forms, it drops out of the mix as a solid. Here, the goal is to chemically join propylene and ethylene in a solution to create the rubber’s polymer chains.
2. Purification
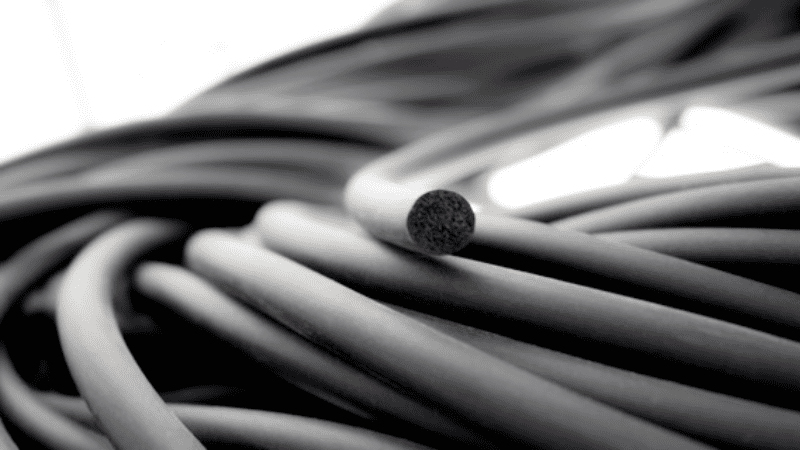
In purification, the mixture created in the polymerization stage is moved to another vessel. This is where the polymerization gets stopped, and the mix is treated with toluene and water. The toluene’s job is to ensure the water can pull out any leftover catalyst from the polymer. Then, steam strippers go to work. They remove monomers and solvents that didn’t react, clean up the polymer slurry from the catalyst, and get everything ready to be recycled back into the reactor for more polymerization.
3. Vulcanization
When this phase is over, a vulcanization phase happens, which is important in making the rubber. Sulfur is commonly used to create strong cross-links between the EPDM polymer chains, making the rubber tougher and more elastic. Occasionally, when a sulfur-less product is needed, peroxides are used as the vulcanizing agent.
4. Finishing
After the purification stage, the material is in small, wet pieces. In the finishing stage, these small, wet pieces are mixed with a few additives that help the pieces stay separate and stop them from clumping together. After mixing with these additives, the mixture is filled with excess water and sent to a rotary screen to remove that extra water. From there, the damp EPDM goes through an extruder that pushes out any remaining water. The now dry EPDM crumb, with very little moisture left, is cooled off, pressed into bales, and packaged for shipping.
After all these processes, the resulting EPDM can be shaped into many forms, including pellets, cement, or sheets of different thicknesses, tailored to the requirements of different uses and industries.
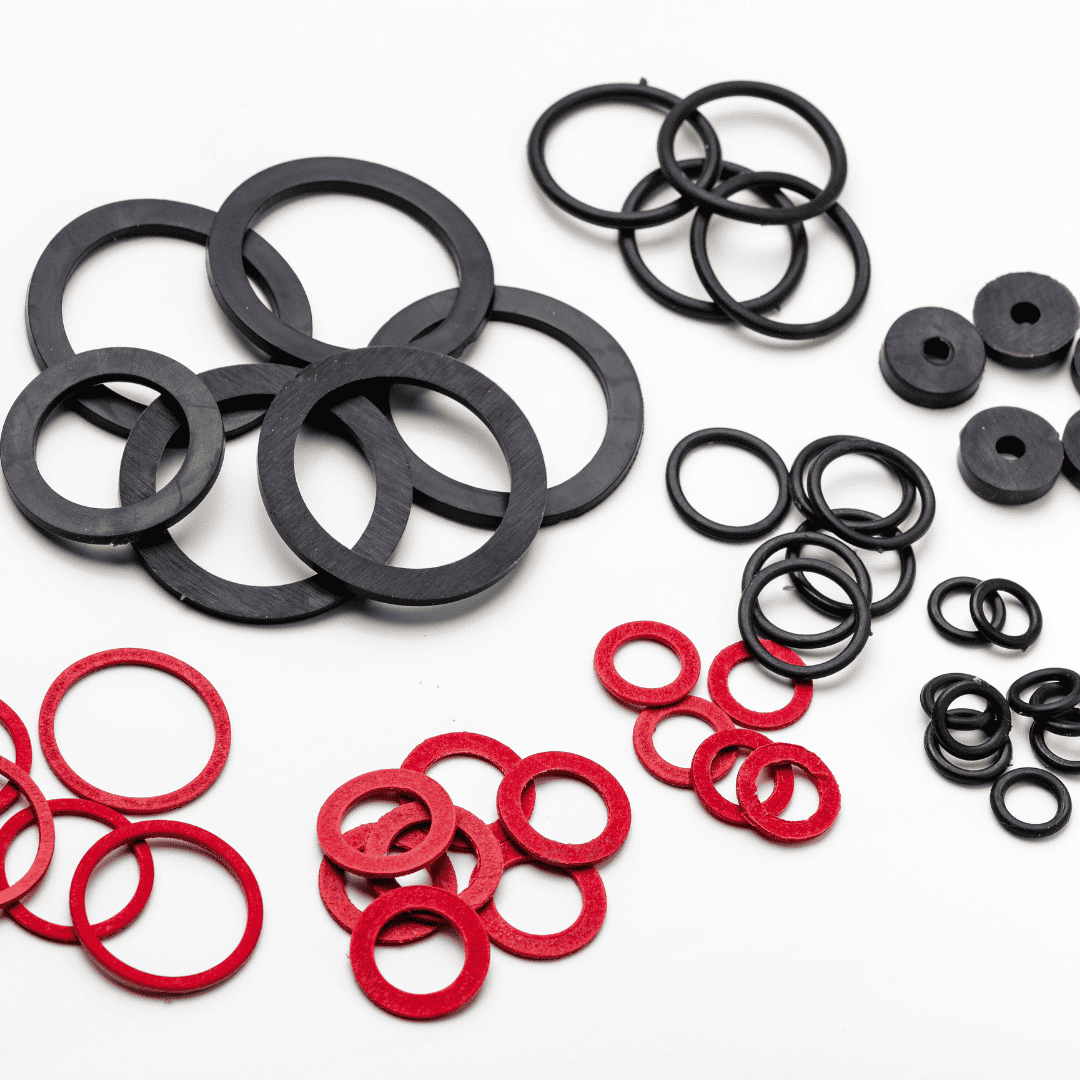
Send Your Inquiry Now!
Quality Meets Affordability. Inquire Now for High-Quality Products at Low Volumes.
How to Choose the Right EPDM Rubber
EPDM rubber is one of the best options available for roofing substrates. However, all this can happen only if you have the right EPDM rubber. Here is a complete guide to EPDM roofing you need:
1. Understand Application Requirements
The selection of the right EPDM rubber starts with a clear understanding of your project’s specific needs. Every application has a different set of requirements that the material must meet. Some common areas include elasticity, temperature resistance, or exposure to certain chemicals. If you define the application requirements upfront, you can ensure that the chosen EPDM rubber will align with the intended use, providing optimal performance.
2. Considering Longevity and Durability
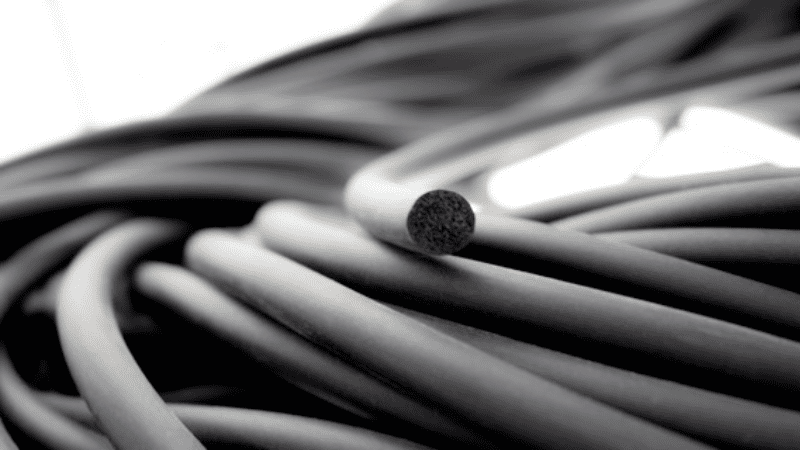
Longevity and durability are important factors when selecting EPDM rubber. You have to understand how long you need the rubber to last and under what conditions it will operate. If your application involves harsh conditions, choosing a higher grade of EPDM that can resist wear and tear is a wise investment to prevent future breakdowns and reduce the need for frequent replacements.
3. Researching Supplier Reputation
The history and credibility of your EPDM rubber supplier should guide your decision. A supplier with a solid reputation will likely offer high-quality materials that meet your specifications. Researching and choosing a trusted supplier is important as it can offer peace of mind that the EPDM rubber you receive is consistent and suitable for your application’s long-term requirements. Sourcing EPDM rubber from reputable manufacturers is very important to ensure that the end product meets the highest standards of quality and consistency. Established manufacturers, like Hongju, typically have rigorous testing and quality control processes, which means that their EPDM rubber is more likely to meet or exceed industry standards and performance benchmarks.
Maintenance and Care of EPDM Products
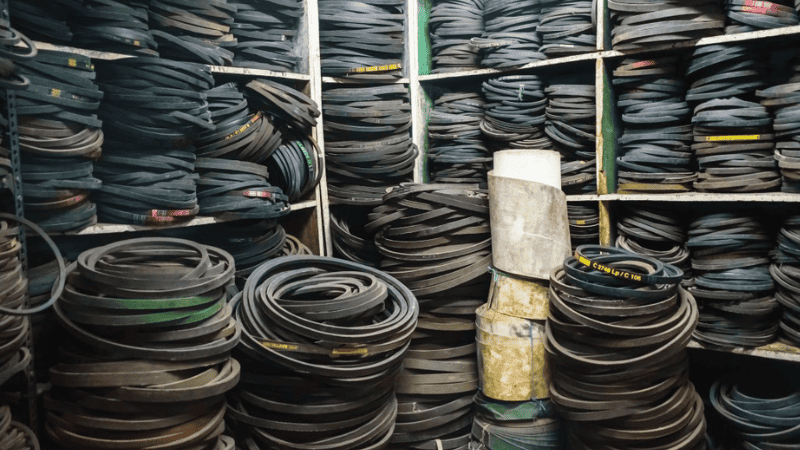
Properly maintaining EPDM rubber is essential to extend its service life and maintain its efficacy. Below are some guidelines to ensure that your EPDM products remain in the best condition:
- Routine Cleaning: Regularly clean EPDM surfaces with mild, soapy water to remove dirt and debris, which can cause abrasions and degrade the rubber over time.
- Avoid Harsh Chemicals: Do not use petroleum-based cleaners or solvents as these can significantly deteriorate the quality of the EPDM. Always check the chemical compatibility of cleaning agents with EPDM.
- Inspect Regularly: Conduct frequent visual inspections for signs of wear, cracking, or other damages. Early detection of issues can prevent more serious problems and potentially costly repairs.
- Minimize UV Exposure: While EPDM has excellent UV resistance, prolonged exposure to sunlight can still affect its lifespan. Where possible, limit the exposure to direct sunlight.
- Check for Water Pooling: Ensure good drainage around EPDM installations, especially on flat roofs, to prevent water from pooling, which can cause damage over time.
- Proper Installation: Ensure that EPDM rubber is installed correctly according to the manufacturer’s guidelines, as poor installation can lead to premature wear or failure.
- Follow Manufacturer’s Recommendations: Stick to the maintenance and care instructions provided by your EPDM manufacturer, as different grades and applications might require specific care.
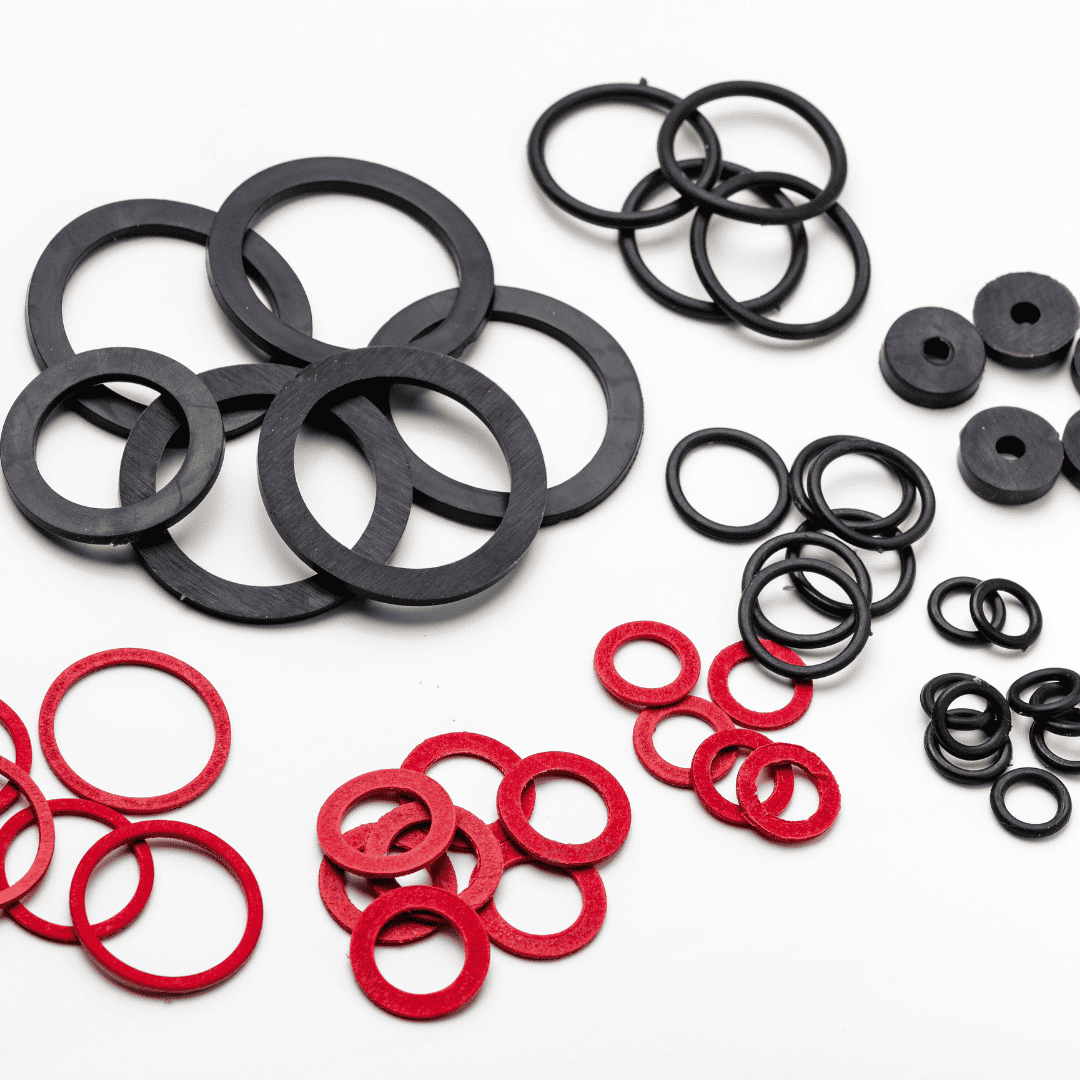
Send Your Inquiry Now!
Quality Meets Affordability. Inquire Now for High-Quality Products at Low Volumes.
Conclusion
So, this was a detailed guide about the EPDM rubber. We have discussed its composition, properties, applications, and factors to consider when choosing the right grade for your needs. We hope you now understand everything regarding EPDM rubber. If you are after EPDM products, make sure to get them from a well-reputed brand.
Take the Next Step Towards Durability and Efficiency
Ensure the durability and performance of your equipment with the right EPDM rubber by Hongju. Take the first step to optimize your operations and guard against the unexpected by choosing a material that stands the test of time. Don’t compromise on quality; get in touch with the experts who can guide you to the perfect EPDM solution tailored to your specific needs.