When it comes to silicone rubber vs. other materials, the competition is quite fierce. Silicone rubber is the prince of the pack — well known for its durability, longevity, and resistance to harsh environments.
However, as compared to natural rubber, silicone elastomers, ethylene propylene diene, and others, it is certainly costly.
The million-dollar question is — Is silicone rubber worth the higher price tag? This is where we come in.
In this article, we will take a closer look at the key factors that influence the choice of the right material in the manufacturing and construction industry so that you can make the best decision for your project.
Are you prepared? Let’s delve into it!
What is Silicone Rubber
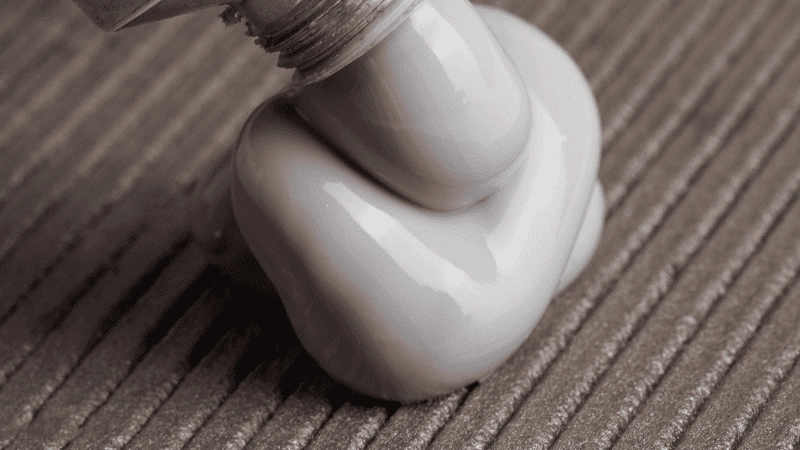
Silicone rubber is a synthetic rubber made from a combination of carbon and silicone. It can adapt to a wide range of environments.
With a unique combination of strength flexibility and resistance to cold, heat, and UV radiation, this polymer can withstand harsh conditions easily.
Properties of Silicone Rubber
Its chemical structure — silicon atoms linked with oxygen — sets it apart from other polymers. You get a material that is both reactive and stable. According to the application, you can formulate it to be pliable and soft or rigid and hard.
The polymer is versatile in terms of appearance, texture, and color. It can be opaque or transparent, matte or shiny. You can mold it into intricate designs and shapes with ease. Silicone rubber is certainly the polymer that can go the distance!
Industrial Use of Silicone Rubber
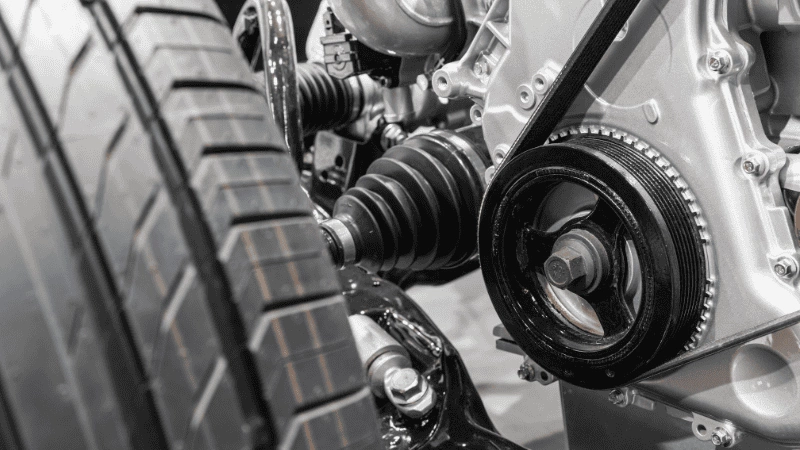
The amazing properties of silicone rubber make it a popular choice in all industries, from aerospace to automotive. In the construction industry, silicone rubber is used as weatherproofing material.
Whether it is your doors, windows, or roofs, you can easily use the polymer to protect them against harsh weather conditions.
You can also use it as a sealant for seams and joints in buildings that prevent air infiltration and water leaks.
Since it is non-toxic in nature, silicone rubber is popular in the food and beverage industry. Similarly, creating prosthetics and implants is a top choice in the medical industry.
Here’s a table showcasing the pros and cons of silicone rubber. Let’s take a look!
Pros of Silicone Rubber | Cons of Silicone Rubber |
---|---|
Excellent resistance to high and low temperatures | Limited Abrasion Resistance |
Highly flexible | Low Tear Strength |
Good shock-absorbing properties | High Cost |
Low Toxicity | Limited Adhesion Properties |
Low Gas Permeability | Low Density and Hardness |
Send your inquiry for prompt quotations!
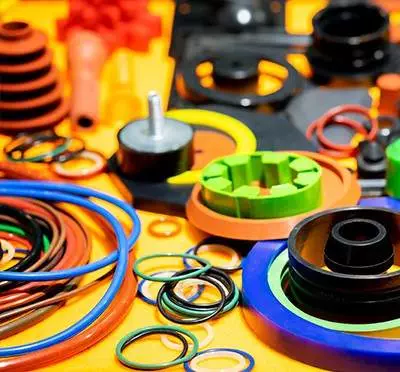
Silicone Rubber vs. Other Materials
When it comes to choosing the perfect material, the choices are endless. The options can seem overwhelming, from natural rubber and synthetic rubber to silicone elastomers and styrene butadiene rubber.
Each material has its own unique perks and pitfalls, particularly when it comes to balancing cost and quality.
Let’s look at the properties of these materials one by one and then compare them with silicone rubber to help you make an informed decision.
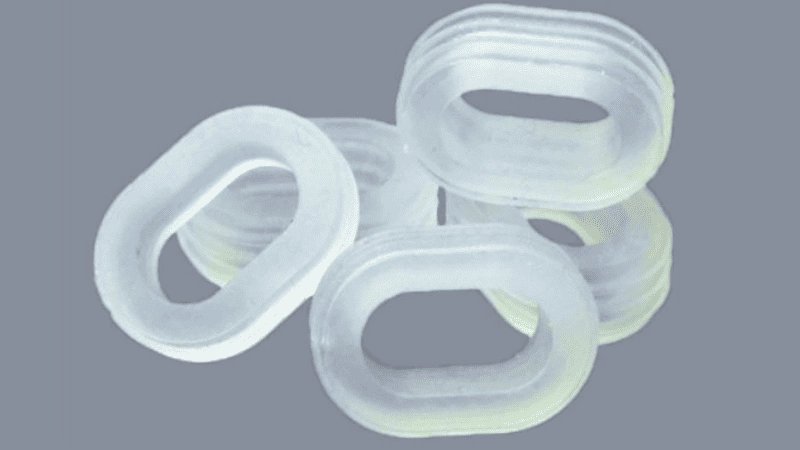
When choosing a material for a specific application, cost is always a major consideration. Several options are available in the world of rubber, including silicone rubber, natural rubber, synthetic rubber, styrene-butadiene rubber, silicone elastomers, and ethylene propylene diene (EPDM).
Each of these materials has its own advantages and disadvantages in terms of cost and quality.
Natural Rubber
Starting with natural rubber is a renewable resource derived from the sap of rubber trees. It is highly elastic and tear-resistant, idealizing projects requiring high tensile strength.
However, it degrades when exposed to harsh natural elements such as heat, light, and chemicals.
This impacts its longevity and durability. The cost of natural rubber depends on its quality but is affordable compared to other types of rubber. It is ideal for products such as tires and conveyor belts due to its flexibility.
However, as it is not resistant to extreme conditions, you can’t use natural rubber for applications or projects that require temperature or chemical resistance.
Pros
- Renewable Resource
- Good Tensile Strength
- Tear Resistant
Cons
- Poor Heat Resistance
- Starts to Degrade Upon Chemical Exposure
- Not Durable
Synthetic Rubber
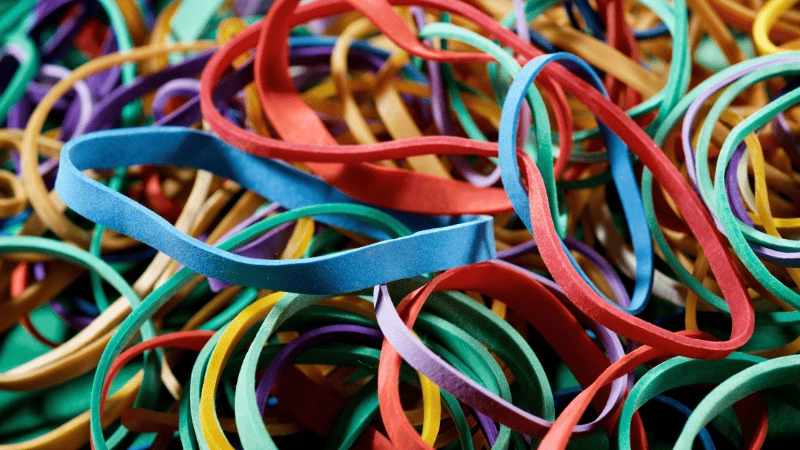
Synthetic rubber is made from petroleum-based chemicals. It is less expensive than natural rubber. Moreover, it has improved abrasion and weathering. However, it is not very elastic and becomes brittle over time.
It is used in the automotive industry to make engine components such as seals and gaskets as it is heat resistant.
Even though synthetic rubber is resistant to temperatures and chemicals, it falls short of the mark when compared with silicone rubber.
Pros
- Abrasion Resistance
- Slight Protection against Weather Conditions
Cons
- Not Very Elastic
- Cracks over time
Styrene-Butadiene Rubber
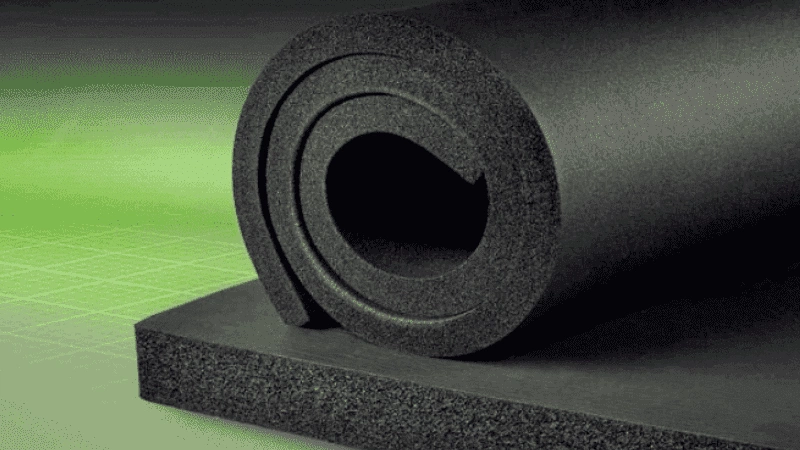
SBR — Styrene-butadiene rubber — is a type of synthetic rubber. It is highly resistant to abrasion. Moreover, the impact strength of SBR is good as well. However, it is not elastic and is more prone to splitting and cracking.
Styrene-butadiene rubber is also used in the automotive industry to make seals and gaskets. However, it is not as chemical resistant as silicone rubber is.
Pros
- Better Abrasion Resistance than Natural Rubber
- Good Impact Strength
Cons
- Poor Elastic Strength
- Cracks and Splits Easily
Silicone Elastomers
Silicone elastomers, including silicone rubber, are popular due to their excellent resistance to temperature changes, chemicals, and UV radiation.
They are highly flexible and have great insulators. However, they are expensive compared to natural and synthetic rubbers, which makes them less common.
Silicone elastomers are often used in the aerospace and medical industries.
Pros
- Highly Flexible
- Excellent Resistance to Temperature Changes
- Protects against Weather
Cons
- Very Expensive
Ethylene Propylene Diene
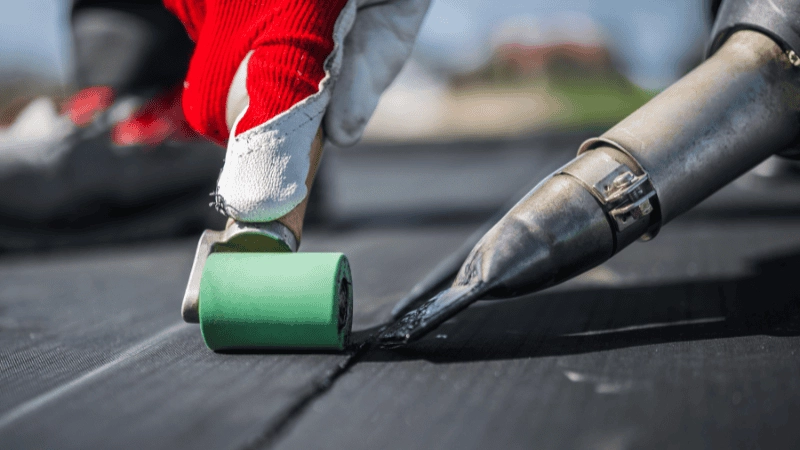
EPDM is also a synthetic rubber that is mostly used in roofing applications. It has excellent weather resistance and durability. Moreover, it is also resistant to UV radiation. However, it is expensive and heavy on the pocket.
EPDM rubber is used in roofing and automotive applications. While it is not as heat-resistant as silicone rubber, it is more affordable.
Pros
- Weather Resistant
- Durable
- Long Lasting
Cons
- Not effective against extreme temperature changes
Send your inquiry for prompt quotations!
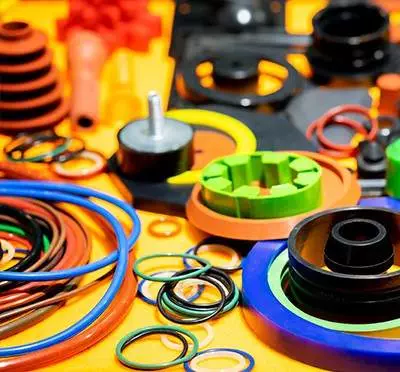
4 Essential Factors to Select Rubber Material
When evaluating the cost and benefits of various rubber materials, there are key factors you must consider. Let’s take a look at them.
1. Material Properties
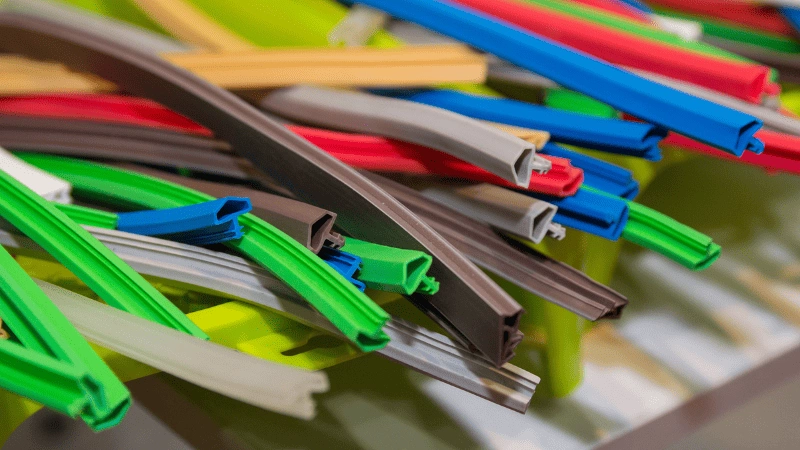
You have to keep an eye on each material’s unique physical and chemical properties. Remember how these properties will impact the finished product’s performance. Compare the material’s strength, durability, and resistance to wear and tear.
Mechanical Properties | Silicone Rubber | Natural Rubber | Synthetic Rubber | Styrene-Butadiene Rubber | Ethylene Propylene Diene |
---|---|---|---|---|---|
Tensile Strength | 700-1500 psi | 2000-5000 psi | 1500-3000 psi | 500-3000 psi | 1000-2000 psi |
Elongation | 100-1000% | 600-1000% | 200-800% | 200-800% | 200-700% |
Compression | 30-70% | 40-70% | 40-80% | 20-50% | 30-70% |
It is important to understand that the values above vary as per each material’s specific grade and formula. Moreover, the kind of project, as well as the environmental factors, also affect the performance of each material.
2. Production Costs
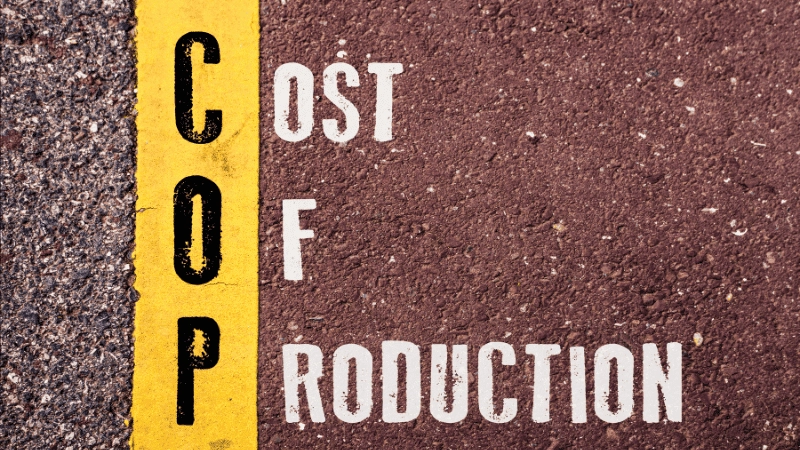
Another important consideration is how much it costs to manufacture the material.
The complexity of the production process along with the raw materials needed affects the production costs. If any specialized processes or equipment are required for manufacturing, it drives the costs up.
Sr | Natural & Synthetic Rubber | Silicone Rubber, SBR, & EPD |
---|---|---|
1 | Affordable | Expensive |
2 | Well-Established production process | Require Specialized Equipment/Production Processes |
When evaluating the production costs of various rubber materials, you have to keep an eye on the long-term benefits and savings.
For example, even though silicone rubber is expensive to produce, it has better durability, leading to cost savings in the long run by reducing replacement and maintenance costs.
3. Availability and Lead Time
The next factor you should consider is the availability. This can affect the cost and the timeline of your project.
Moreover, it also impacts the overall feasibility of using a certain material. Natural and synthetic rubber are widely available and have been used for a long time.
However, natural rubber is produced in countries such as Indonesia and Thailand, which can impact lead time and costs.
Even though silicone rubber is not widely available since it is used in specialized applications, it is certainly worth the lead time.
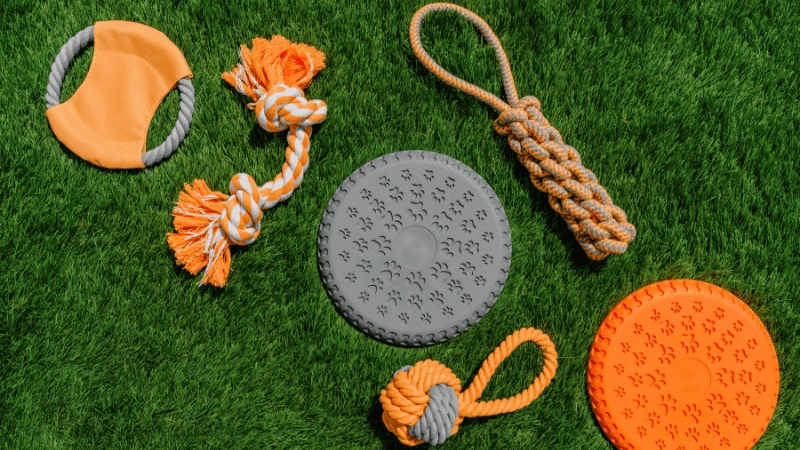
4. Environmental Impact
It would be best to consider each material’s environmental footprint. If there are any sustainability or regulatory considerations, take them into account.
Natural rubber is biodegradable and comes from a natural source, so it is thought of as the most eco-friendly. However, this varies on land use, greenhouse gas emissions, and water consumption.
Synthetic rubber is made from petroleum-based products and has the most significant environmental impact.
Silicone rubber is a great option since it is durable and long-lasting, so you don’t have to replace it often. Moreover, it is recyclable, which reduces its environmental impact even more.
Send your inquiry for prompt quotations!
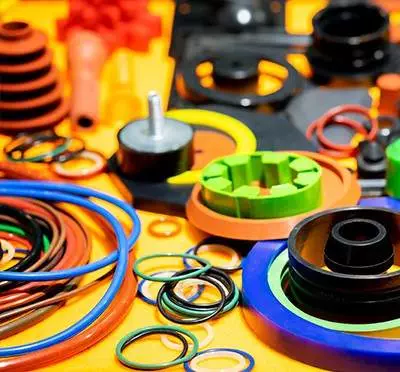
Unlock Savings and Sustainability
When thinking about the cost versus quality trade-off, it is essential to consider the project’s specific needs. You have to choose the material that will give you the best performance and durability while being easy on the pocket.
Some materials — such as silicone rubber — are expensive upfront. However, when you consider their resistance to degradation and durability, you will see that they are more cost-effective in the long run.
You have to consider the total cost of ownership. If a material is more durable and resistant, it means less frequent replacements and, thus, a reduction in the overall costs.
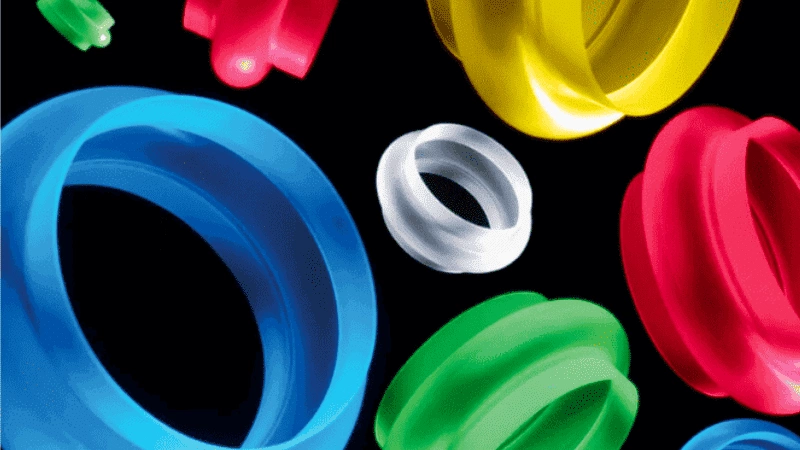
With careful consideration, you can make a conscious choice that aligns with your values and meets your project requirements.
Don’t let short-term costs overshadow the long-term impact. So, what are you waiting for? Choose wisely and make a difference!
Conclusion
Ultimately, the best choice depends on the specific needs of your project. By considering factors such as material properties, production costs, availability, and environmental impact, you can make an informed decision that maximizes both efficiency and sustainability.
Find the Perfect Rubber Material for Your Project
As you decide which rubber material to choose for your project, keep in mind that Hongju to help you. Our team of experts is ready to assist you in making the best choice based on your specific needs and requirements.
If you are still unsure which rubber material you should get, contact us today to schedule a consultation or to request a quote. Let us help you create a product that meets and exceeds your expectations!