Its unique properties, such as temperature resistance, electrical insulation, and chemical stability, make it the go-to material for various applications. In this guide, you will learn everything about silicone rubber, including its chemistry, advantages, uses, and much more!
What is Silicone Rubber?
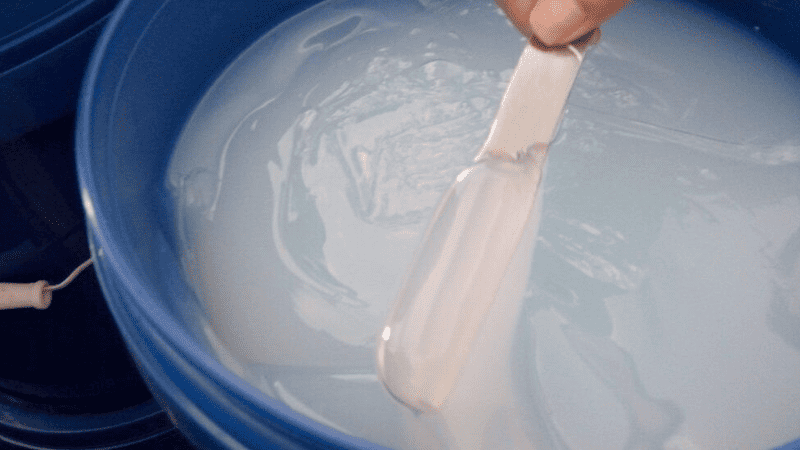
Silicone rubber is an elastomer, a type of polymer with rubber-like flexibility and resilience. This polymer contains a blend of silicon, carbon, hydrogen, and oxygen elements. It comes in various forms, commonly as either a one-part or two-part system, which refers to the method of curing or hardening the material (we will explain these later). In most cases, manufacturers add fillers to the silicone material to enhance its thermal conductivity or tensile strength, etc. The versatility and adaptability of silicone rubber make it one of the most used materials in the industries.
Chemistry of Silicone Rubber
Let’s break it down into composition and curing or vulcanization processes with the types of vulcanization.
Composition
As mentioned earlier, silicone rubber is composed of a polymer called elastomer. So, we can say that silicone rubber is composed of silicon, carbon, hydrogen, and oxygen elements. Here, silicon acts as the main ingredient of the material. It is known for providing thermal stability and chemical inertia to the material. Next up, we have carbon and hydrogen, which are responsible for providing the organic structure, which offers flexibility. And then, there is oxygen, an element that acts as a bridge between silicon atoms, facilitating the material’s rubber-like elasticity.
Curing/Vulcanization Processes
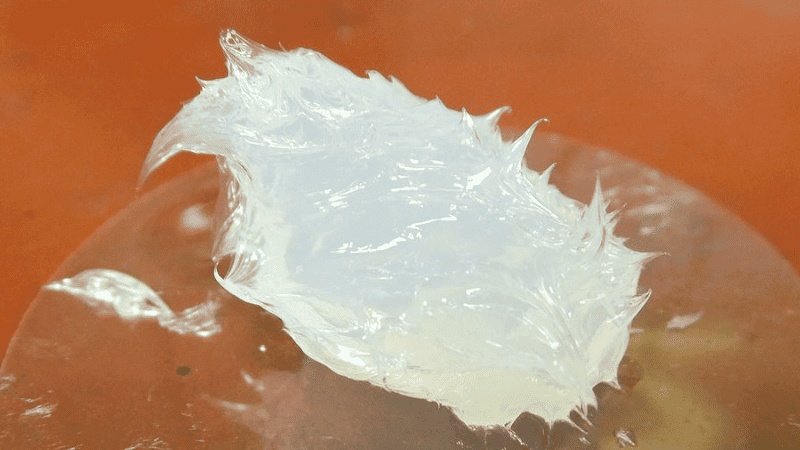
Curing or vulcanization is important to have a useable silicone rubber material with all the characteristics. Before this process, the silicone we have is present as a highly adhesive gel or liquid. To convert it into solid silicone rubber and attain a durable state, it must go through the process of curing. Vulcanization or curing is a two-stage process where the substance is first molded into the desired form during manufacture and then subjected to a prolonged post-cure process to complete the solidification. This ensures the material’s integrity and performance stability.
Here are some common types of vulcanization or curing processes used for silicone rubber:
- Platinum Cure: In platinum-based cure, there is a need for a catalyst to create strong bonds between silicone molecules without creating any byproducts. This process is pretty quick for different types of silicone rubber, but you have to be careful because certain elements like sulfur and tin can inhibit the cure.
- Peroxide Cure: Peroxide cure is by far the most common curing process used for the production of silicone rubbers. In this process, a reaction takes place that creates byproducts. Later, these can be removed through post-curing, resulting in a clean product suitable for food contact, medical, and other useful purposes. However, peroxide curing is a slower process than platinum, but it is worth the time it consumes.
- Condensation Cure: The condensation cure process is based on either one-part or two-part systems. In the case of one-part systems, they interact with humidity to cure. On the other hand, two-part systems require mixing to initiate curing. This is a versatile process and not easily inhibited. However, it produces sealants ideal for construction and can be tailored to be acidic, neutral, or alkaline.
Take the First Step:
Requst for an Inquire
Quality Meets Affordability. Inquire Now for High-Quality Products at Low Volumes.
Advantages of Silicone Rubber
Silicone rubber is known for many advantages, such as its exceptional thermal stability and electrical insulation, making it an important component in sectors ranging from consumer electronics to aerospace engineering.
Here’s a detailed look at the advantages of silicone rubber:
1. Extreme Temperature Resilience
One of silicone rubber’s most notable physical properties is its ability to endure extreme temperatures without losing performance. Capable of operating continuously from -100°F to 300°F and able to handle even more severe temperatures in short bursts, silicone rubber maintains its properties across a broad temperature range, making it ideal for high-stress environments.
2. Electrical and Mechanical Reliability
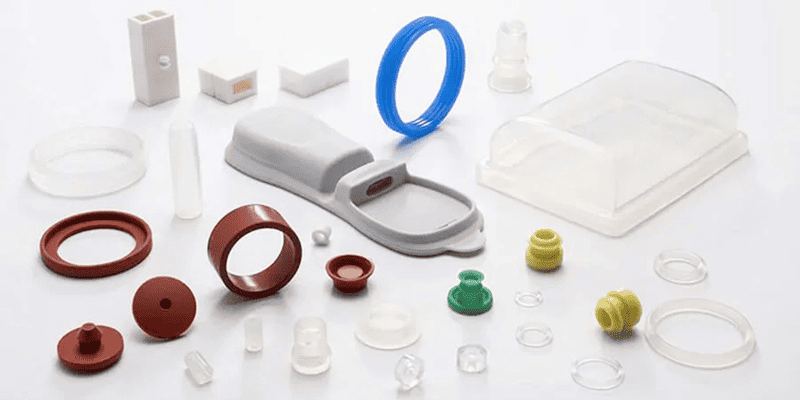
Conductive silicone rubbers, which contain electrically conductive materials, serve various functions, such as keypad contacts and cable shielding. This material has unparalleled adaptability as it offers a resistance spectrum suitable for various uses.
3. Safety
There is no alternative to safety. The safety features offered by silicone rubbers are crucial for use in enclosed spaces like aircraft and subways. The silicone rubber is inherently flame-retardant, meeting UL94 HB standards and minimizing the emission of toxic gases and black smoke when exposed to fire. So, you can’t doubt its safety.
4. Weather and Chemical Resistance
Due to its durability against weather elements, silicone rubber does not degrade with exposure to ozone. Unfortunately, this is not the case with organic rubbers. Additionally, silicone rubbers can withstand over a decade of contact with wind, rain, and sunlight. Even when submerged, its resistance to water, oils, solvents, and other chemicals secures its position as a superior material for sealing and insulation applications.
5. Versatility and Bio-compatibility
Last but not least is the versatility and bio-compatibility of silicone rubber. Silicone rubber’s chemical and physiological inertness means it will not react adversely with other materials, and it aligns with FDA standards, allowing safe usage in different products, particularly medical devices and baby care products. You can understand its versatility by looking at its various applications and customizations available. Silicone rubber can achieve specific coloration, durability, and resistance properties.
Applications of Silicone Rubber
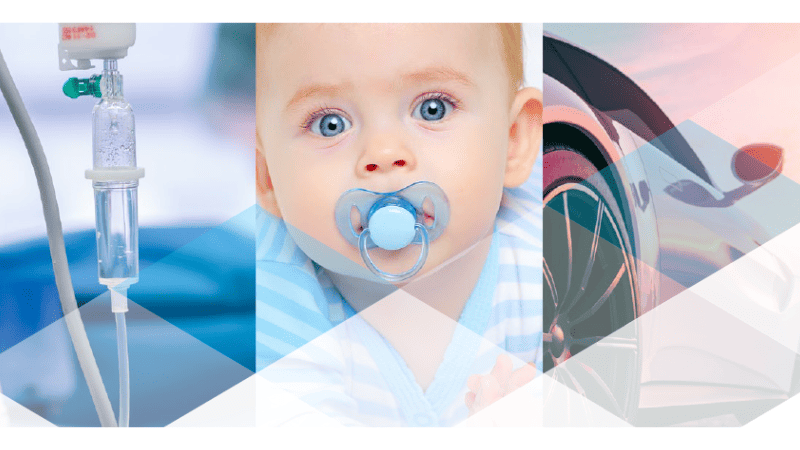
Silicone rubber is known for its versatile applications. Here are just some of the many applications of silicone rubber material:
- Automotive: In the automotive sector, silicone rubber is crucial for creating reliable gaskets, seals, hoses, and various under-hood components that can withstand high temperatures and harsh conditions.
- Caulks: Utilized in both residential and industrial settings, silicone caulks are prominent for providing an enduring, flexible, and waterproof seal.
- Construction: In construction, silicone caulk is used to seal joints and gaps and provide a water-resistant barrier, demonstrating remarkable durability and flexibility over time.
- Consumer Products: Everyday consumer products such as kitchen utensils, bakeware, and protective cases for electronics often employ silicone rubber for its safety and resilience.
- Electronics: Its use in electronics is extensive due to its electrical insulation properties, making silicone rubber an excellent choice for coatings, sealants, and insulators in delicate electronic devices.
- Healthcare: Silicone rubber’s bio-compatibility makes it a preferred material in the healthcare industry, especially for prosthetics, tubing, and numerous other medical applications.
- Industrial: In the industrial world, silicone rubber is used for insulation, vibration damping, and protective sheathing due to its durability.
- Insulation: Its thermal stability makes it an ideal insulator in many applications, ranging from energy-efficient windows to electrical wire coatings.
Take the First Step:
Requst for an Inquire
Quality Meets Affordability. Inquire Now for High-Quality Products at Low Volumes.
Types of Silicone Rubber
The diversity in silicone rubber types allows for a range of products with distinct properties. Some common types include:
Liquid Silicone Rubber (LSR)
Liquid Silicone Rubber (LSR) is a distinctive type of silicone that is used for a range of flexible and durable products. LSR is a mix of two components; the first part includes long chains of polysiloxane, which are the main building blocks of silicone materials, and these are combined with a special kind of silica that strengthens the rubber. These form a vital basis for the silicone’s characteristics.
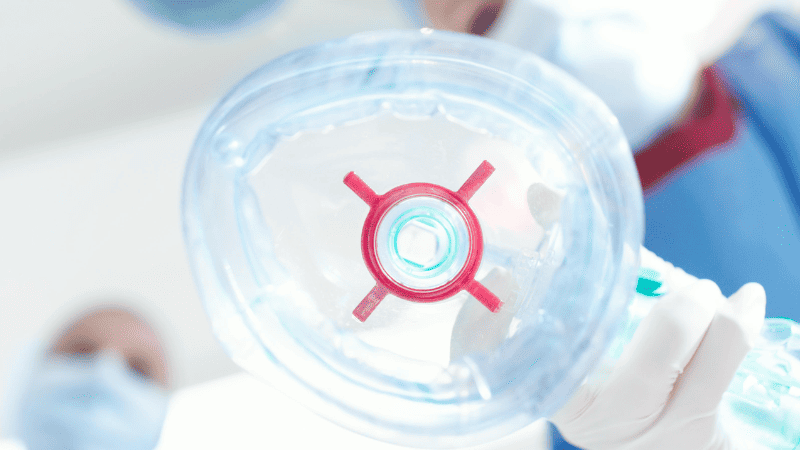
The second part of this system incorporates Components A and B. Component A holds a platinum catalyst that initiates the curing or vulcanization process. On the other side, Component B contains a compound known as “methyl hydrogen siloxane,” which is a cross-linker. This cross-linker binds the silicone chains together more firmly, which is crucial in setting its shape and form. Additionally, an alcohol inhibitor in Component B prevents the cure from happening too quickly or at the wrong time. Working together, these elements produce a rubber that is strong yet flexible and highly reliable for various applications
High Consistency Rubber (HCR)
High Consistency Rubber (HCR) is another form of silicone rubber known for its solid nature. It starts as a high-molecular-weight polymer with substantial polymer chains, similar in texture to chewing gum. This form of silicone rubber needs heat to cure, and it often uses catalysts such as peroxide or platinum to start the curing process. The curing transforms the HCR from its original gummy state to a material that is stretchy and strong at the same time. The heat causes the polymer chains to link together tightly, creating the elastic and durable qualities that make HCR a valuable resource in various industries, especially where parts need to maintain their structure under stress or pressure.
Room Temperature Vulcanizing (RTV) Silicone
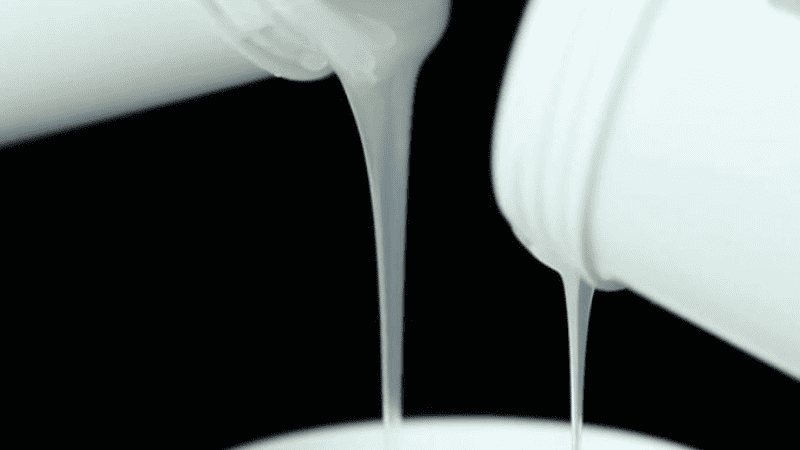
As the name speaks for itself, Room Temperature Vulcanizing (RTV) Silicone becomes solid under normal room conditions. This means it doesn’t need heat to cure. It does this with help from a special ingredient – a catalyst often made of platinum or a tin-based substance like dibutyltin dilaurate. You can get RTV silicone in just one container, or sometimes you need to mix it from two different parts. These two different parts are the base stuff that makes up the silicone and the curative, which is the chemical that makes the silicone harden. RTV silicone can handle heat well and will not get damaged in temperatures up to 356°F. People like to use RTV silicone because it is not hard to work with, and you can use it for lots of different projects.
Fluorosilicone Rubber (FSR)
Fluorosilicone Rubber (FSR) stands out for its exceptional fuel, oil, and solvent exposure resistance, making it the material of choice in the aerospace and automotive industries. Its unique composition ensures it retains silicone’s beneficial properties while providing superior chemical resistance. The role of Fluorosilicone Rubber is significant in general-purpose molded, extruded, and calendered parts. Some examples of these silicone rubber products include diaphragms, gaskets, O-rings, oil seals, and the list goes on.
Manufacturing and Processing of Silicone Rubber
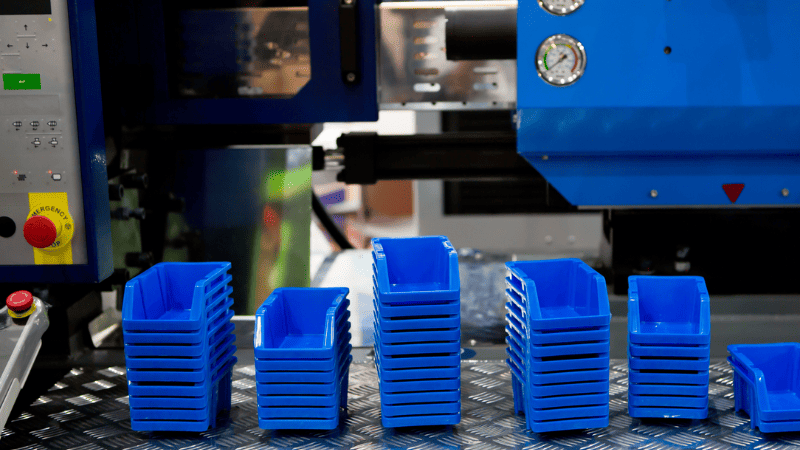
Let’s divide this section into two main processes:
- Extrusion
- Molding
Extrusion
This process involves pushing silicone rubber compound through a die. The die is a stainless steel disc with a specific pattern. The purpose of this process is to create various silicone forms. Silicone extrusion is a highly specialized process in which silicone rubber is shaped into profiles with complex cross-sections that are impossible to create through more conventional manufacturing methods. Here is how this process goes:
- The silicone compound is fed into the “extruder.” It is a machine known to convert the silicone into unique shapes.
- In the next step, the materials are then put into the feed hopper. It serves as the entry point through which the silicone begins its transformative journey.
- Inside the extruder, the rubber compound is then forwarded into different flutes of the revolving screw. This component applies rotational and forward forces, and as a result, it plays a key role in progressing the silicone through the machine.
- During the entire process, the silicone is consequently forced through the extrusion die (having a sophisticated design), emerging on the other side as a continuous profile of the desired shape.
- The final steps of the process take place inside an oven. Here, radiant heat properly cures silicone rubber, setting its shape and setting its renowned resilience and durability. The result is a product ready for use in various industrial or consumer applications.
Molding
Molding is a technique that involves shaping silicone rubber using a mold. There are two types of molding processes:
Compression Molding
The process starts by heating the silicone, which we press into the mold in a big chunk. The heat from pressing the material then transforms it. The entire process feels like pressing down on a sponge and having it soak up heat, which changes the sponge, making it take on a new, permanent shape after it has been heated and formed.
Injection Molding
With injection molding, the process is a little different. Here, the silicone is heated until it is malleable. After this, it is pressurized to squirt through a nozzle into a mold. When the hot silicone fills the nooks and crannies of the mold, it copies the mold’s exact shape. After cooling down, the rubber hardens into the designated form, ready to be popped out like ice cubes.
Take the First Step:
Requst for an Inquire
Quality Meets Affordability. Inquire Now for High-Quality Products at Low Volumes.
How to Choose the Right Silicone Rubber
Not all silicone rubbers are the best. Those that have been manufactured and processed with a proper process are made differently. So, a silicone rubber highly resistant elastomer is of no use if it doesn’t meet your requirements. Here are a few tips to help you choose the right silicone rubber for you.
1. Flexibility
One of the main properties of silicone rubber is its flexibility and excellent resistance. Silicone rubber is very flexible, which means it can be twisted, stretched, and bent repeatedly without losing its original shape. This makes it ideal for products that require frequent manipulation. So, a more flexible silicone rubber will be a great choice than a silicone rubber with average flexibility.
2. Temperature Resistance
Unlike organic rubber, silicone rubbers made with a highly durable elastomer are highly temperature resistant. This makes them a perfect option to use against different kinds of temperatures. So, check if your selected product has high-temperature resistance or not before selecting silicone rubber for yourself.
3. Tear Strength
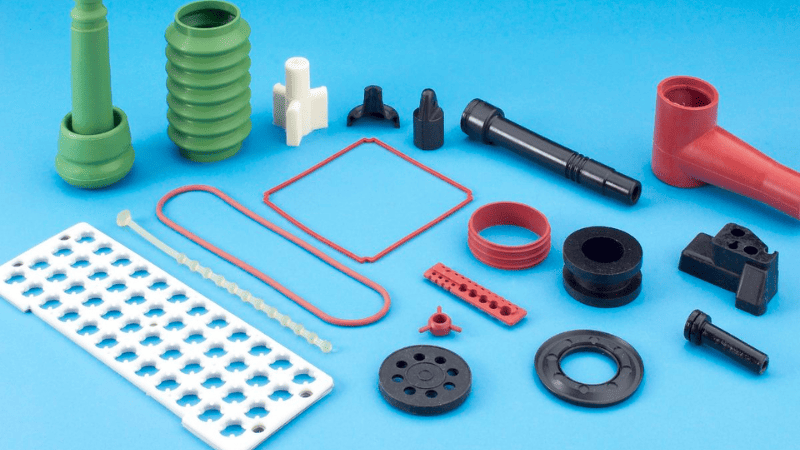
Silicone rubber can withstand tearing. This is vital for products that will undergo harsh mechanical conditions or those that are expected to have high durability. If you are looking for products that will face harsh mechanical conditions, you need to keep tear strength as the top priority.
4. Budget
Sometimes, the budget can be a problem because different brands offer different rates for silicone rubbers. Despite its benefits, silicone rubber can be more expensive than other materials, so it must align with your financial constraints. That’s where you always need to find a reliable manufacturer like Hongju. We have been in the market since 1999. As a leading manufacturer and wholesale supplier, we specialize in developing sustainable and durable silicone solutions tailored to your needs. With us, you can never go wrong with the quality and price of the silicone rubbers.
Take the First Step:
Requst for an Inquire
Quality Meets Affordability. Inquire Now for High-Quality Products at Low Volumes.
Conclusion
So, is there any doubt about the resilience and adaptability of silicone rubber? From its unparalleled temperature resistance to its exceptional tear strength, silicone rubber is a superior choice in many applications, outperforming many natural and synthetic alternatives. However, all this is possible if you opt for a reliable manufacturing brand that has a name in the world.
We hope now you understand everything about silicone rubbers, their uses, their advantages, and how to select the right silicone rubber for you. So, make the right decision in your first attempt, and don’t have any regrets later on!
Make the Sustainable Choice with Hongju – Contact Us Today!
At Hongju, we have been at the forefront of innovation since 1999. Our commitment to the environment goes hand in hand with our dedication to quality, ensuring that our silicone rubber products meet and exceed the most rigorous safety standards. Don’t wait because your journey towards eco-friendly excellence is just a click away. Contact Us Today and be a part of the change you wish to see. Want an expert design guide? Click Here!