This guide will help you to understand how you can assess your gasket needs, achieve the right compression percentage for your application, the factors that affect compression, and even how you can avoid permanent deformation of your gaskets in some applications. Read on as we uncover the secrets of silicone gasket compression percentage.
What is the Silicone Gasket Compression Percentage?
The silicone gasket compression percentage is the difference between the original thickness of the gasket and the thickness of the compressed silicone gasket, divided by the gasket’s original thickness, i.e., before compression, expressed as a percentage. It is a simple measure of how much a silicone gasket is compressed when in use.
The silicone rubber gasket compression percentage can serve as a good guide that ensures you don’t apply too little compression when installing your rubber gasket. Perhaps more significantly, it can also serve as a guide that ensures you don’t apply too much compression on your seal.
The common assumption is that the tighter you can get your rubber gasket the better but this common mistake negatively affects the gasket’s mechanical properties and can cause poor long-term performance of a seal in some applications.
What are Silicone Gaskets?
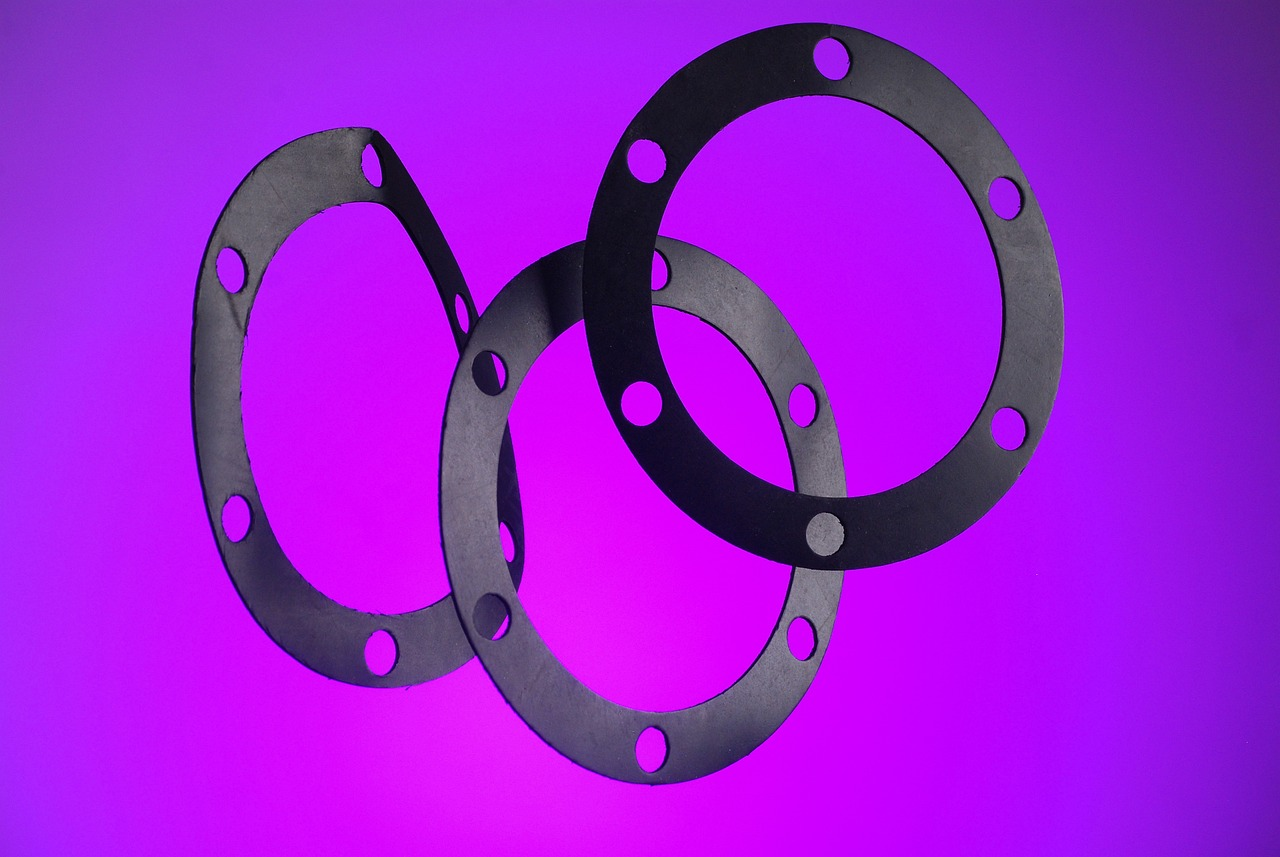
Silicone gaskets are flexible seals that are installed and compressed between mating surfaces to keep substances from leaking into or out of the sealed space. They are also used to maintain pressure levels inside sealed spaces.
When compressed, a silicone gasket adapts to the unevenness of the mating surfaces, filling grooves and scratches. This creates a mechanical barrier that keeps substances from moving from one side of the mating surfaces to another.
Traditionally, gaskets were made using asbestos and natural rubber, but silicone gaskets have become increasingly popular because of properties such as:
- Low toxicity
- Low flammability
- Good insulation properties
- Safe for food and medical applications
- Good resistance to ozone, ultraviolet light, and many chemicals
- Excellent high and low-temperature performance compared to natural rubber gaskets
There are different types of silicone gaskets possessing a range of properties that make them suitable for different applications. Some types of silicone gaskets include:
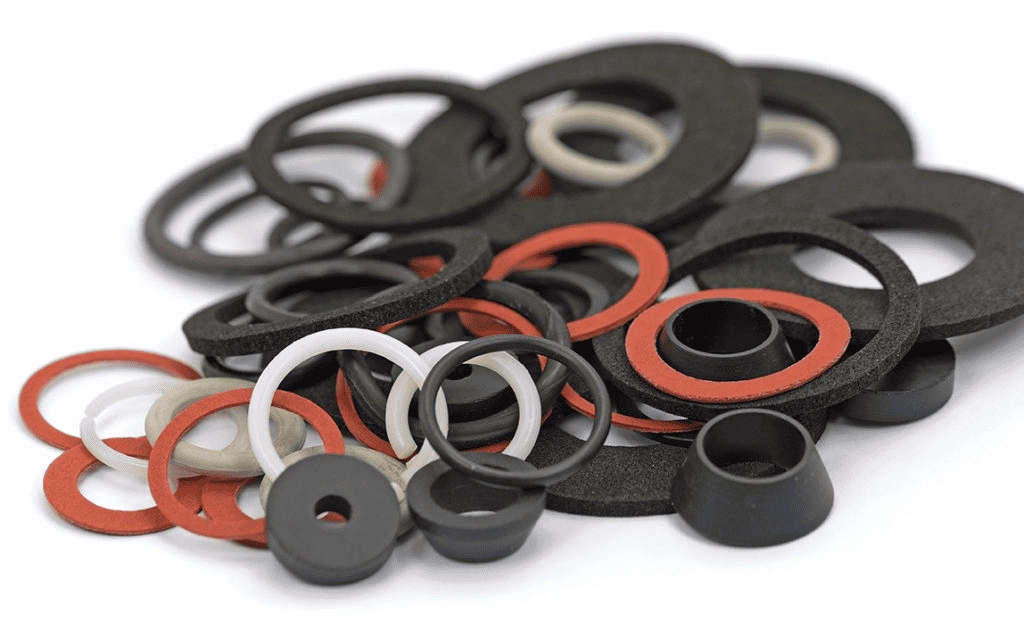
- Die-cut gaskets: Die-cut silicone gaskets are produced using a die and a press, resulting in precise cuts and consistency from one gasket to the next.
- Fluorosilicone gaskets: These gaskets offer superior resistance to petroleum-based products such as oils, fuels, and coolants compared to other silicone gaskets. These can provide a reliable seal in an automotive or aerospace application.
- Silicone foam gaskets: These gaskets are lightweight and possess good compression set properties. They are softer than sponge gaskets and can be used for sealing, insulation, and cushioning.
- Silicone sponge gaskets: Silicone sponge is considered waterproof and can withstand high temperatures. Its tear resistance and tensile strength exceed that of silicon foam and you can also use this gasket type for cushioning and sealing in the outdoors.
- Solid silicone gaskets: These gaskets are not as soft as their foam or sponge counterparts. They form a good seal at lower compression rates and have varieties with both low and mid-range durometers.
- Conductive rubber gasket: Electrically conductive rubber gaskets contain conductive particles. You can use these where you need a reliable seal along with shielding from electromagnetic interference (EMI) and radio frequency interference (RFI).
- FDA-approved food-grade gaskets: These silicone gaskets are made from materials that are considered food-safe. They can withstand heat and aren’t degraded by cleaning products. These will be vital to you if you are a beverage or food manufacturer.
Send your inquiry for prompt quotations!
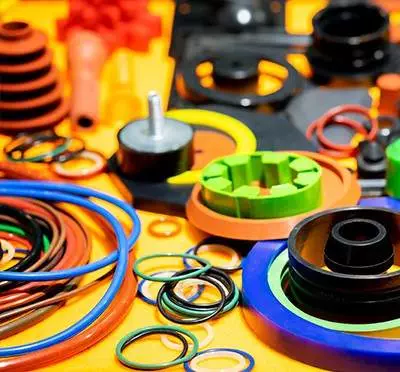
Compression in Gasket Design
How much a gasket can be compressed along its thickness is a factor that must be considered when a gasket is being designed. Leakages are more likely to occur if a gasket compresses too little or too much.
Role of Compression in Sealing
A certain amount of compression is necessary for a gasket to form a good seal between mating surfaces. When you compress a gasket, it undergoes some elastic and plastic deformation, forcing it to fill the irregularities that would permit the escape of a gas, liquid, or powder.
If the compression is too little, the gasket will not fill enough of the irregularities to completely prevent a leak. However, too much compression can also cause more permanent deformation, making it less likely that the gasket will rebound enough to form an adequate seal the next time you compress it.
Factors Influencing Gasket Compression
Several factors affect how much a gasket can be compressed. These include:
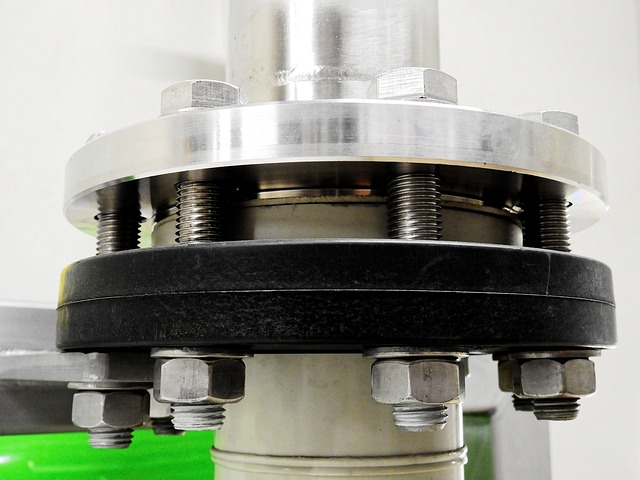
- How tightly the bolts are torqued
- The properties of the material used to form the gasket
- The design of the mating surfaces
To form good seals, the bolts of your flanges should neither be too tight nor too loose. If the bolts are not torqued enough, the gaskets are not deformed enough to form good seals between mating surfaces. However, the gaskets will undergo permanent deformation if the fasteners are over-torqued.
A softer silicone gasket can form a better seal since it requires less compressive force to conform to the imperfections on the mating surfaces. However, such soft materials would also struggle to maintain the seal under higher pressures.
Some flanges offer a large surface area for the gasket while others have less space available to them. Flanges with more surface area allow the use of wider gaskets which can be compressed more. These offer better sealing but they take up more space and don’t suit low-pressure applications.
Gaskets with smaller widths can be used where there’s less space but they don’t offer the best seals.
Send your inquiry for prompt quotations!
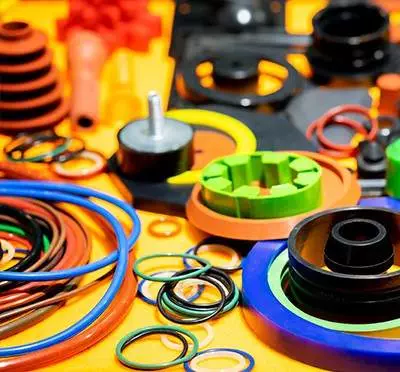
Silicone Gasket Compression Percentage: The Science
Silicone gasket compression percentage, commonly referred to as silicone gasket compression, is one of several guides you can use to avoid leaky joints. What is this metric and how is it calculated when tightening flanges?
Definition and Importance
Silicone gasket compression percentage is the percentage of the initial thickness of the silicone gasket that it has been reduced by when compressed.
For example, if a 2 mm silicone gasket has an ideal compression percentage of 30, its ideal thickness under compression will be 1.4mm. Its compression percentage at any time can be calculated using the formula below:

If the 2mm silicone gasket above was compressed to a thickness of 1.6 mm, its compression percentage can be calculated as follows:

The importance of knowing the silicone gasket compression percentage is that it can help you determine if you have applied enough compression to form an effective seal.
When torquing nuts or screws, it is also easy to assume that the tighter you can get it the better the seal formed, but this can damage the gasket.
With the silicone gasket compression percentage to guide you, you can periodically measure the thickness of the gasket and use the formula above to determine when adequate compression has been achieved.
Material Behaviour
Isomers such as silicone rubber and natural rubber are some of the best materials for gaskets. Their ability to stretch or compress several times their size is useful, but they have a few other characteristics you should be aware of when they are used as gasket materials.
Viscoelasticity in Silicone Rubber Gaskets
One of silicone rubber‘s mechanical properties is called viscoelasticity. This property can help to create a better seal but can also compromise the durability of the gasket material.
Viscoelasticity describes the ability of a material to exhibit both viscous and elastic behavior at the same time when subjected to a force. This means that under deformation, these materials exhibit both solid-like and liquid-like behavior.
When silicone rubber is made to be viscoelastic, when subjected to a sudden force, e.g., when struck with a hammer, the material will exhibit a great degree of stiffness. The hammer can be bounced off the material without leaving a mark!
On the other hand, when a force is applied to the same material over a certain period, the material gradually deforms to take up the shape that is dictated by the force. The same material that will bounce off a hammer strike can be deformed by a finger pressing down on it for some time.
When the deforming force is removed, the material slowly rebounds until it regains its original shape.
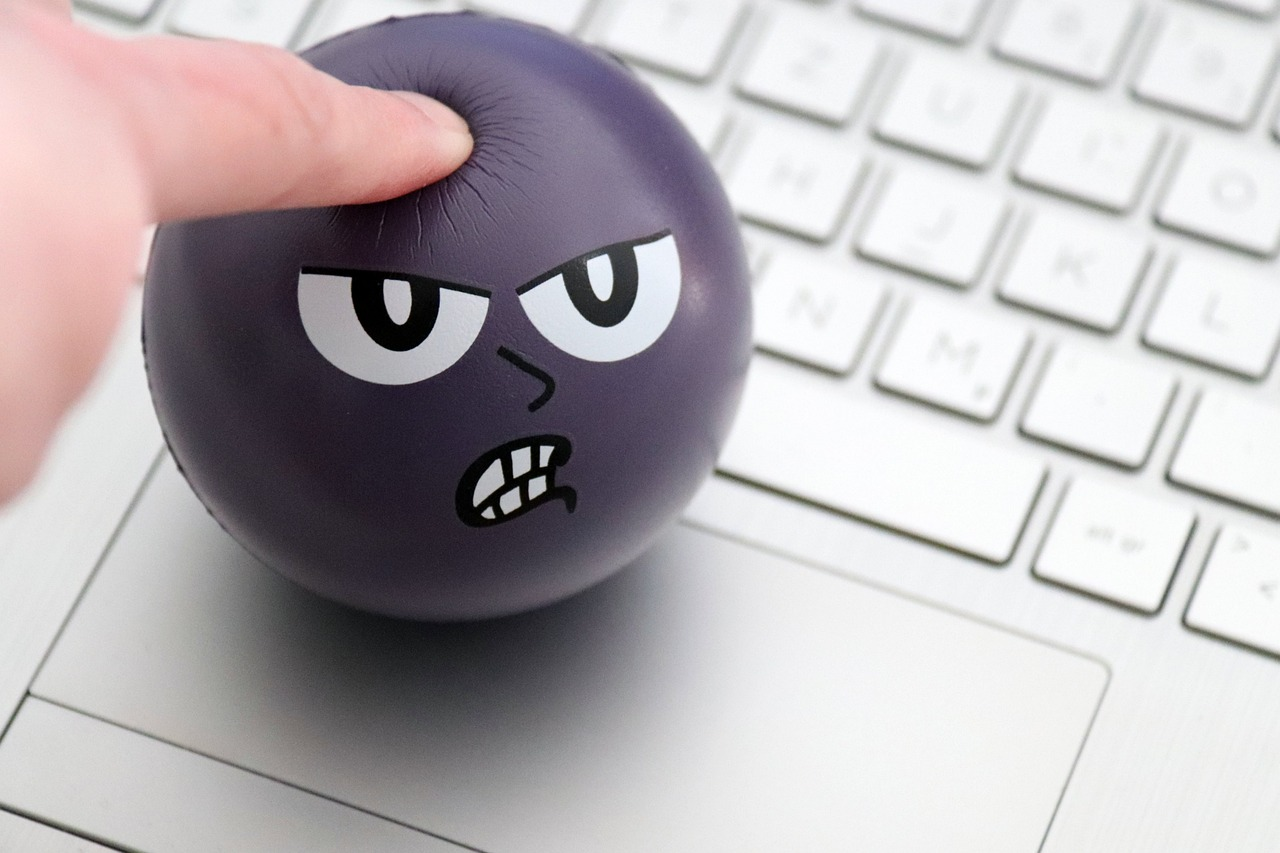
This ability to deform gradually can result in a silicone gasket forming a better seal as it gradually ‘flows’ to fill the imperfections.
On the other hand, in the context of silicone gasket compression percentage, this same viscoelastic property can be a problem. When installing the gasket, you may apply enough compression to achieve the desired compression percentage.
However, with time, the gasket material may deform further resulting in differences in measurement. The gasket may return to its original dimensions when the compression is removed, but the dimensional differences that show up hours after fitting may create other challenges.
Stress-strain Characteristics of Silicone Rubber Under Compression
The stress-strain characteristics of silicone rubbers under compression are not linear, especially when enough time passes. The amount of strain or deformation exhibited by silicone rubber may change even under constant stress.
One way that this can be observed is when a silicone rubber gasket is initially bolted into place. Initially, it will resist the compression more, causing it to push deeper into the small gaps and imperfections on the flange surfaces.
However, one hour later, the degree of this ‘pushback’ will have reduced by some percentage. This can lead to a less-than-perfect seal and leakage.
These stress-strain characteristics of silicone rubber are affected by several factors including:
- Composition of the silicone rubber used
- Strain rate i.e., the period over which the stress acts
- Environmental conditions e.g., temperature and humidity
- Exposure to certain chemicals
These factors can result in the silicone rubber becoming softer and undergoing more strain even when the stress is constant. In one case, in conditions with 0% relative humidity, the silicone rubber became stiffer and needed more compressive stress to achieve the same strain levels.
This complex stress-strain behavior can impact silicone gasket compression percentage especially if conditions during installation are vastly different from conditions during operation.
Optimal Compression Ranges
How much compression you should apply to your gasket is not a singular answer. The ideal amount of compression will depend on the specifics of your application. Even so, it is commonly agreed that the sweet spot for compression is between 35% and 40% for both sponge and solid silicone rubbers.
This sweet spot is something we aim for, but it’s not guaranteed that you’ll get the results you want within this range. In any case, it is recommended that you never go above 50% compression. The lower limit is more variable and can be 10%, 15%, or even 25%.
Compression percentage does not only affect the quality of the seal your gasket provides, it also determines how long your gasket can serve you. When your compression percentage is on the higher side of the optimal values, there is a higher possibility that your gasket will fail early.
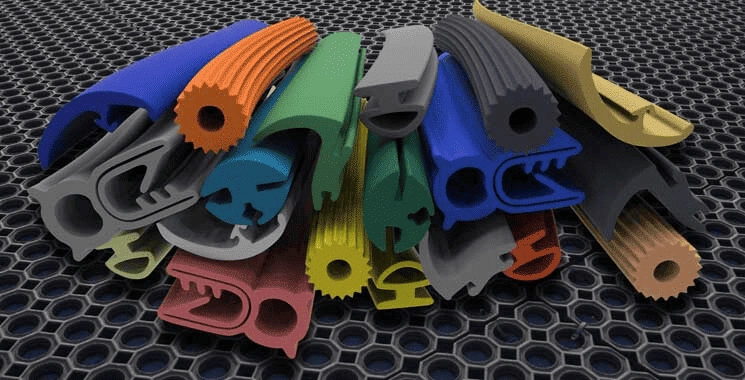
When silicone gaskets are subjected to compression they undergo both elastic and plastic deformation. The higher the compression percentage the more plastic deformation takes place.
The portion of deformation that is due to the material’s elasticity will recover when the compressive load is removed. However, the plastic deformation is permanent and this is why your gasket will only recover a percentage of its initial thickness but not all of it.
Too much plastic deformation can result in a poor seal in applications where stress is periodic rather than constant. This is because such dynamic applications require the material to recover some of its initial thickness from time to time to maintain the seal.
A higher compression percentage can also cause the gasket material to tear or rip, quickly rendering it ineffective.
Send your inquiry for prompt quotations!
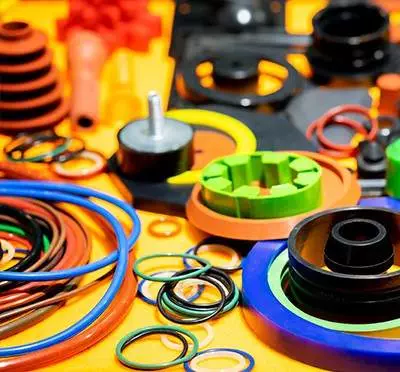
The Role of Compression Set
Compression set is a key factor when deciding whether a material will serve as a good gasket material. Compression set tests are ordinarily used as a measure of the sealing performance of O-ring compounds.
It can be used to quickly compare the expected durability of different materials when an application features cyclic compressive loads.
What is a Compression Set?
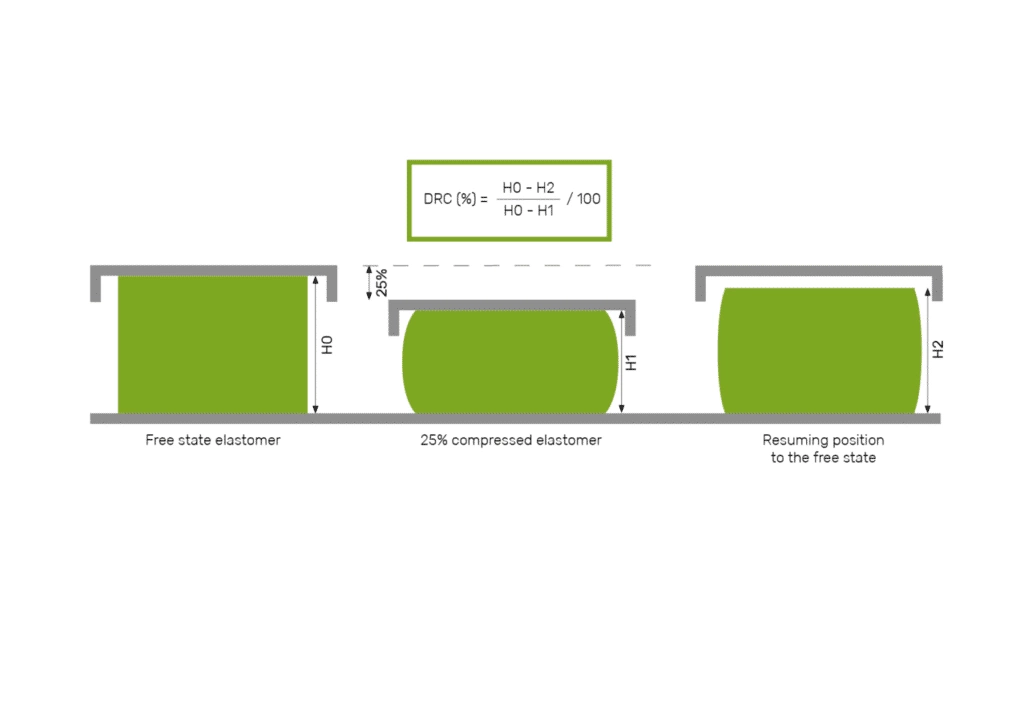
Broadly speaking, a compression set is a parameter that quantifies how good a material is at regaining its original shape after being compressed. In the case of a silicone gasket, compression sets can be used to express how much of its thickness has been permanently lost after being subjected to a compressive force.
The compression set of a material is important because it can tell you if it is resilient enough to be used reliably for a specific application. A lower compression set is preferred because it implies the material recovers more and will have greater durability in applications with cyclical compressive loads.
Compression Set VS. Silicone Gasket Compression Percentage
Compression sets A and B measure how much a gasket material can recover after it has been subjected to a compressive force and allowed to recover. Compression set A involves subjecting the material to a constant force while compression set B involves compressing the material to 75% of its initial thickness.
Gasket compression percentage is the percentage of the difference in thickness between the original gasket and the compressed gasket.
To calculate compression set B, the silicone gasket compression percentage is set to 25% by default. This means you can work backward using the compression percentage formula to identify the thickness under compression.
For example, suppose I had a 1.5mm thick piece of silicone rubber. In that case, I can use the compression percentage formula above to identify the thickness under compression needed for the test as shown below.

The result of the above operation, 1.125, is 75% of 1.5mm.
What Does a High Compression Set Mean in Practice?
Materials with a high compression set are less likely to regain a significant portion of their original dimensions after the compressive force is removed. This indicates poor resilience and such materials may develop gaps and leaks sooner if used as seals.
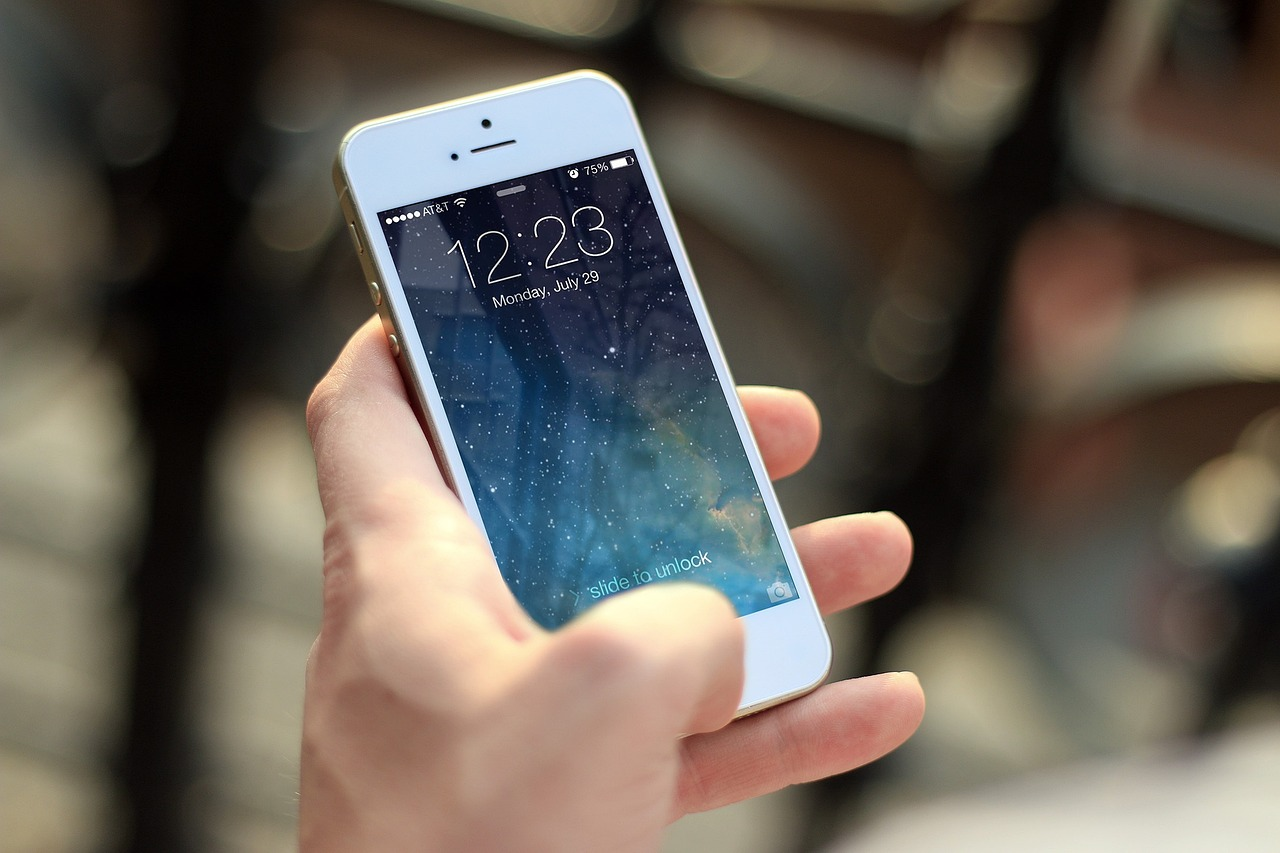
In applications that involve cyclic loading, a gasket will be subjected to different compressive stresses at different times. A lower compression set material will be compressed when compressive stress is high and regain most of its original thickness when the compressive stress lessens. It is less likely that a gap will be left between the mating surface and the gasket.
However, a higher compression set material will be compressed but will recover less of its original thickness when the compressive stress reduces. This means that when loading is cyclic, gaps may form faster between the mating surface and the gasket.
This does not mean that high-compression set gaskets have no use. They are well-suited for use in electronic equipment and other applications with permanent compression.
Send your inquiry for prompt quotations!
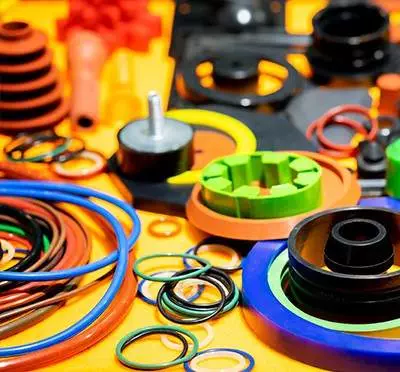
Factors Affecting Compression Percentage
It’s not enough to know a material’s ideal compression percentage. Several factors can limit how much compression you can apply including the thickness of the gasket, the surfaces of the metal parts being mated, and the joint’s operating environment.
Gasket Thickness
It is generally recommended that you use a thinner gasket if possible. Thinner gaskets are less likely to leak, less likely to suffer a blowout, cost less, and experience less creep relaxation. However, a gasket compression percentage of 20% in a thicker gasket can seal more imperfections than the same compression percentage in a thinner gasket.
Therefore, a thinner gasket may need a greater compression percentage to provide an adequate seal, and in some cases, even this isn’t enough. Deciding the best gasket thickness is guided by many factors that revolve around the specific application. These include:
- Flange thickness
- Flange diameter
- Internal pressure on the gasket during operation
- Presence of damage to the flange
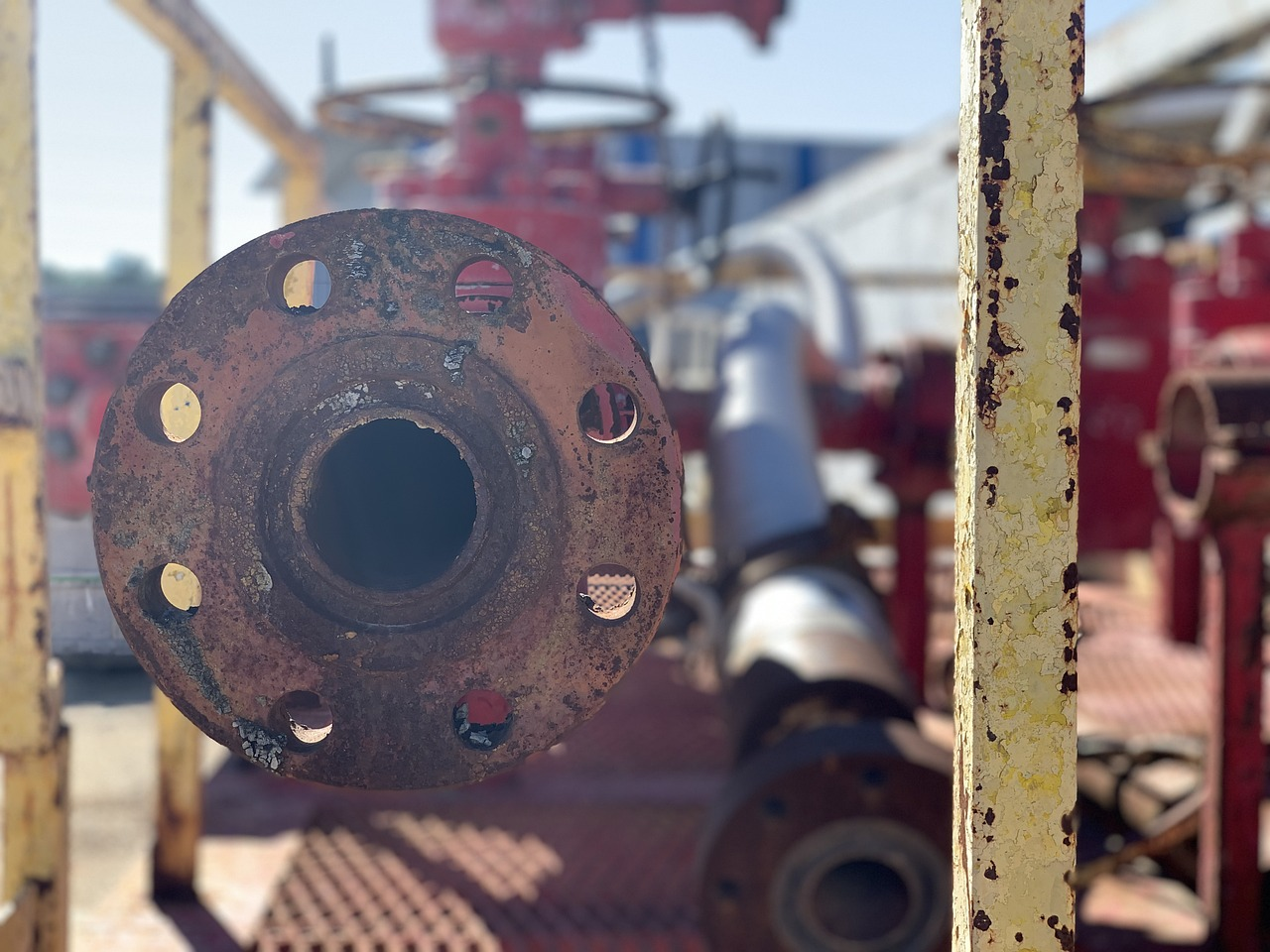
In some applications, tight spacing may require a specific final thickness. This means that the gasket would have to be a specific size when compressed. The chosen gasket thickness would have to factor in the compression percentage to avoid exceeding the maximum compressive stresses.
Flange Surface Finish
Flange surfaces commonly feature a smooth or serrated finish. The type of finish affects both the type of gasket material and the gasket compression percentage that is needed to get a good seal.
Compared to a smooth finish, a serrated finish offers better resistance to the gasket material. This friction between the gasket material and the flange surfaces makes it harder for the gasket to become dislocated and cause a leak even when the compression percentage is lower.
It is common practice to use serrated sealing surfaces in applications that feature high temperatures and high pressures. These types of finishes should be paired with soft gaskets such as silicone which can deform more easily and enter the grooves for superior sealing.
You can also pair a soft silicone gasket with a flange with a smooth finish in low-pressure, low-temperature applications. However, mating surfaces with a smooth finish are usually paired with hard or metallic gaskets.
Operational Temperatures
When silicone rubber is heated to a temperature of around 300°F (150°C) there may not be any significant difference in its compressive behavior. However, at around 392°F(200°C), silicon rubber will start to harden. A gasket may also swell and its shape may change.
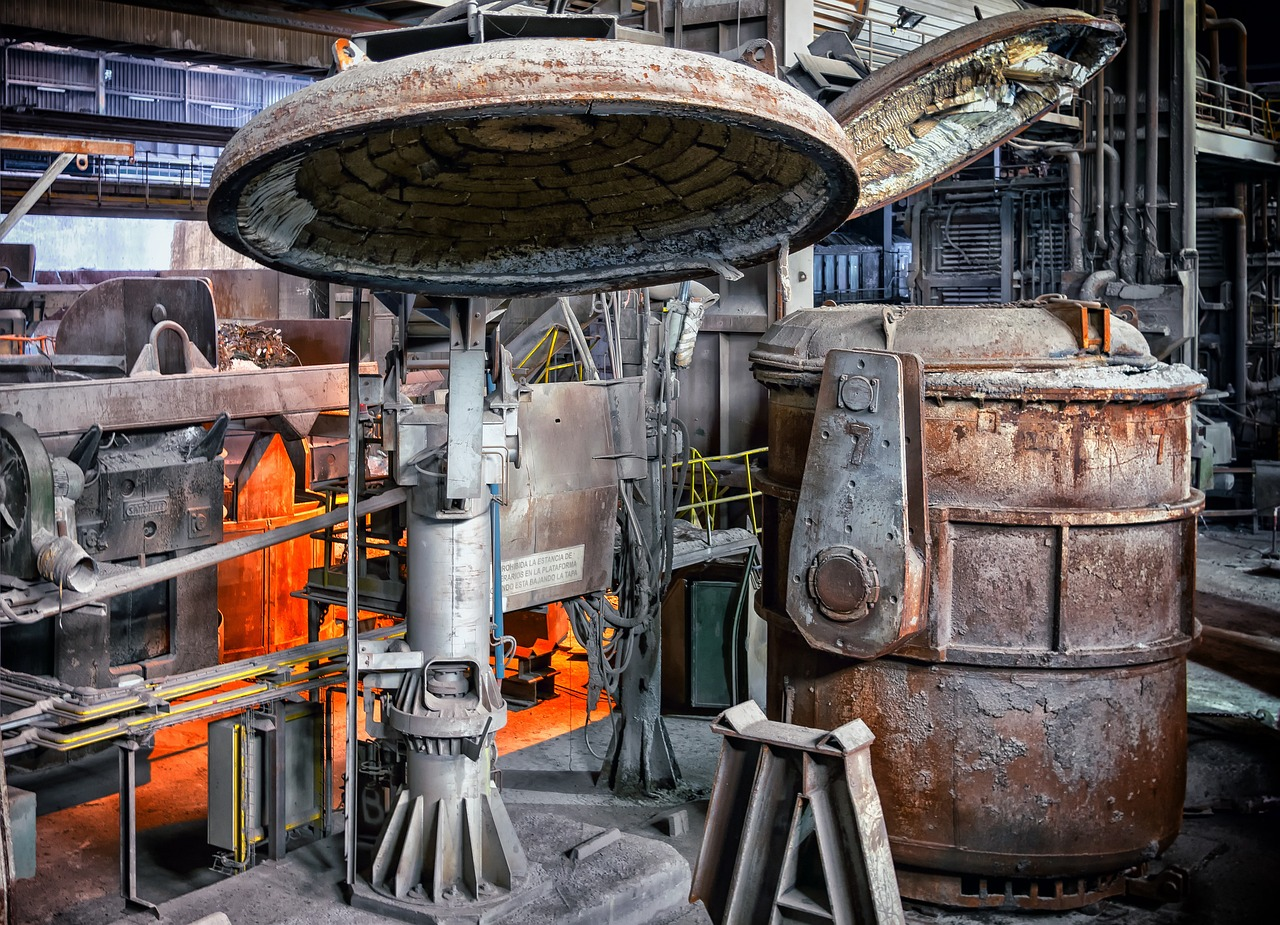
This increased deformation at higher temperatures may be combined with poorer recovery. This means the material would have higher compression sets.
Very low temperatures can also result in lower compressibility of the silicone rubber. These changes in the compressibility of silicone rubber at certain temperatures may make the gasket less effective.
To ensure that sealing is not significantly affected by temperature variations, you can take steps such as:
- Knowing the temperatures your gasket will be exposed to during operation.
- Choosing the right gasket material, especially for high-temperature and low-temperature applications.
- Ensuring proper installation of the gasket including choosing the right compression percentage to accommodate temperature-induced expansion and contraction of metal parts.
Send your inquiry for prompt quotations!
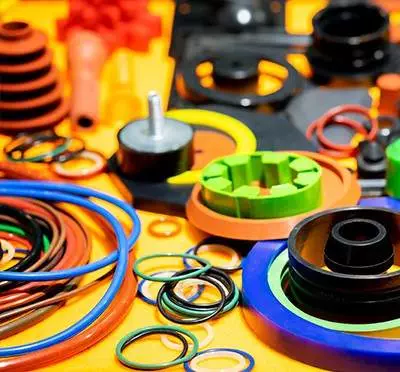
Conclusion
When you install a new silicone gasket, one of the questions you are likely to ask is how much compression you need to form a tight seal. This is a question that can be partially answered using the silicone gasket compression percentage.
Although there is an ideal range of compression percentage values, there are other factors that dictate how much compression you should use to get a seal that withstands the test of time. These properties include the gasket material, the smoothness of the mating surfaces, operating temperatures, and more.
This guide is a great place to start but it certainly helps to talk to an expert to discuss your specific gasket needs so you can make a better choice when you need a silicone gasket.
Find Out Your Gasket’s Ideal Compression Percentage From Hongju
Are you struggling to get a good seal when using silicone gaskets? You could be using the wrong compression percentage or you may need a different type of silicone gasket for your application. The experts at Hongju can help you understand your gasket needs so you can start getting seals that last.