In this article, we will take an in-depth look at what reaction injection molding is, the different types of this manufacturing technology, the materials used, and its advantages and disadvantages. Let’s dive into the ins and outs of reaction injection molding.
What is Reaction Injection Molding?
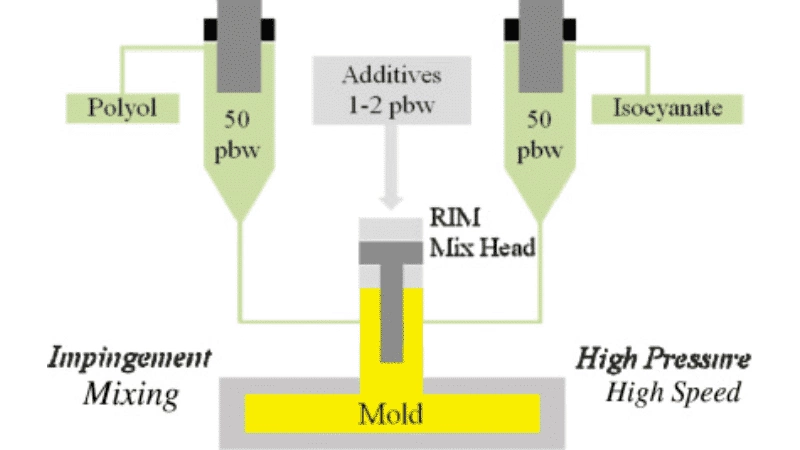
Reaction injection molding is a production process where thermosetting polymers with low viscosities are mixed and pumped into a mold and allowed to cure, taking the forms dictated by the inside of the mold. Unlike regular injection molding where molded parts only need to cool to maintain their shape, RIM parts need time to cure for their forms to set.
When the RIM process starts, two liquid components are thoroughly mixed at high pressure before being injected into the mold cavity at low pressure. This low injection pressure is important to this process because it allows for the use of less expensive tooling compared to regular injection molding.
In plastic injection molding, the plastic material simply cools inside the mold. However, in RIM, a chemical reaction takes place between the different components in the mold to form the final part. This reaction takes place quickly, and cycle times for reaction injection molding can be less than 60 seconds.
2 Types of Reaction Injection Molding
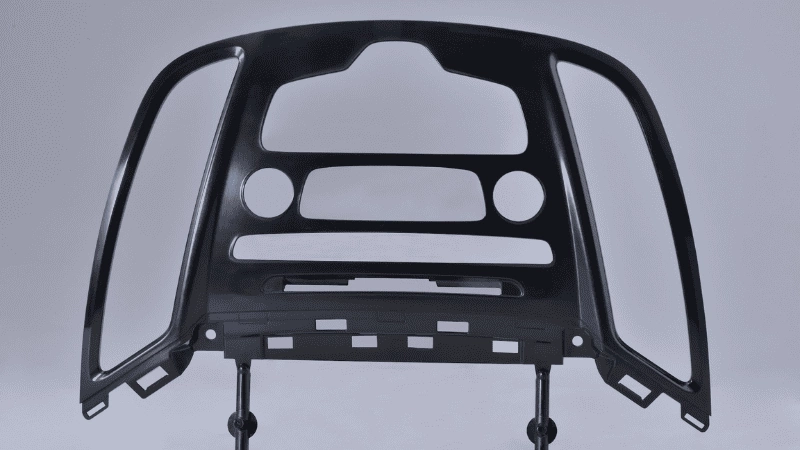
One regularly cited benefit of the reaction injection molding process is the level of design flexibility it allows you to achieve. Part properties such as flexibility and strength, can be controlled to a significant degree.
One factor that makes this possible is the availability of different types of RIM processes.
Structural Reaction Injection Molding (SRIM)
Structural reaction injection molding is a type of RIM used to manufacture parts with higher levels of stiffness. This is achieved by reinforcing the parts with various fibers. Unlike other types of RIM, the fibers used in SRIM are in the form of:
- Mats
- Meshes
- Preforms
The reinforcements are placed inside the molds before the liquid polymer is injected. Parts made using structural reaction injection molding are used in different industries, including the medical, automotive, and aerospace industries.
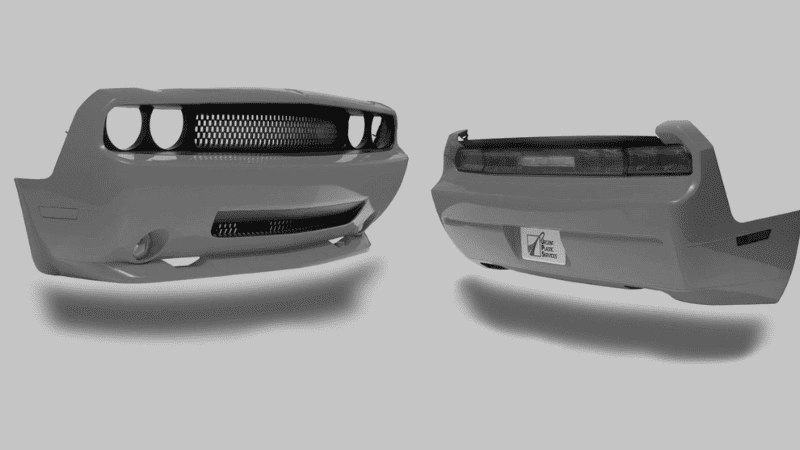
Parts made using this technology include shelves, panels, and doors, where stiffness is an important feature.
For the best results, the mesh or mats used in SRIM have to be completely saturated. Therefore, very low-viscosity liquid polymers are preferred in this process since they can flow better inside the mold.
Reinforced Reaction Injection Molding (RRIM)
Reinforced reaction injection molding is a variation of RIM used to manufacture much larger parts. It is gaining popularity in the transportation industry thanks to its ability to produce long-lasting parts that weigh less.
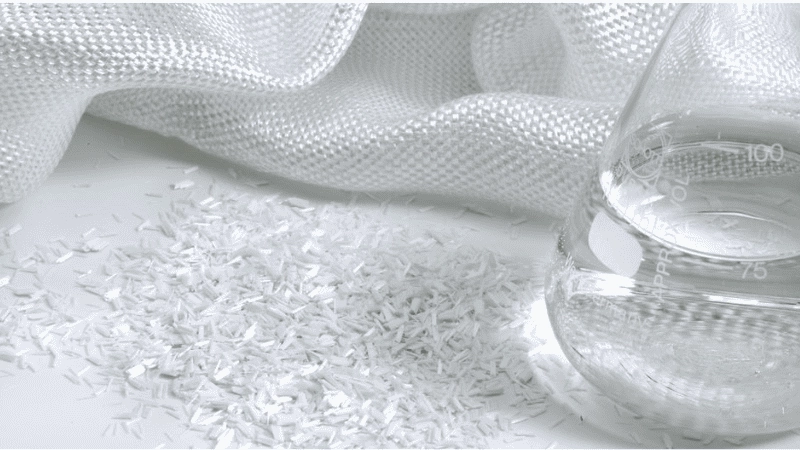
Similar to SRIM, RRIM involves the addition of reinforcing fibers to the molded part. However, there are some notable differences, including:
- The fibers used in the RRIM process are short-strand fibers. The fibers are chopped or milled beforehand.
- The fibers and the liquid polymer are mixed before being injected into the mold
Glass fibers are the conventional reinforcing agents, but the use of carbon fibers is starting to become common.
Parts made using RRIM are much stronger and have higher impact resistance compared to parts made using the regular RIM process. This makes it a good process to manufacture parts such as body panels that are resistant to deformation and wear.
Compared to processes such as compression molding, RRIM parts don’t shrink as much when removed from their molds. The parts also undergo less thermal expansion at extreme temperatures.
Send your inquiry for prompt quotations!
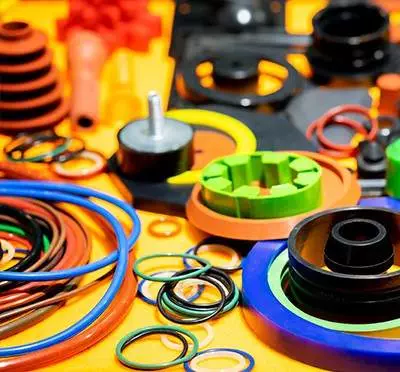
Components and Materials Used in RIM
Reaction injection molding can be used to achieve parts with a wide range of properties. This is thanks to the different types of raw materials and additives that are compatible with this process.
Polyurethane is the material that is most commonly associated with RIM, but parts made using polyureas, polyamides, silicone, and other materials can also be processed using the RIM process.
Types of Materials Associated With RIM
Depending on the formulation of the liquid thermosetting polymer, the reaction injection molding process can yield parts made of the following materials:
- Structural Foams: Structural polyurethane foams are lightweight, stiff, and long-lasting. These materials have a cellular structure that is achieved using blowing agents. Structural foams can be molded into a wide range of shapes and are even used in place of some injection molded parts. These foams are used for rigid housings to protect medical and electronic devices.
- Elastomeric Polyurethanes: This class of polyurethanes is very flexible in addition to having superior impact, abrasion, and corrosion resistance. These materials are popular for military applications, among others, and can also be painted or pigmented.
- Flexible Foams: These elastomeric foams are significantly denser, yet remain flexible. Depending on the inputs, the material surface may have a skin-like finish or not. The skin-like finish makes the parts easier to clean and more durable. These materials are used for medical devices, products for babies, etc.
- Rigid Foams: These styrofoam-like materials can achieve a wider range of densities compared to structural foams and are more resistant to chemicals. Applications that employ rigid foams include buoyancy aids.
- Dicyclopentadiene: Also known as DCPD, this material is made using gas oils that have been heated. They have very high impact resistance and are used to make protective shields used in military and defense and heavy machinery.
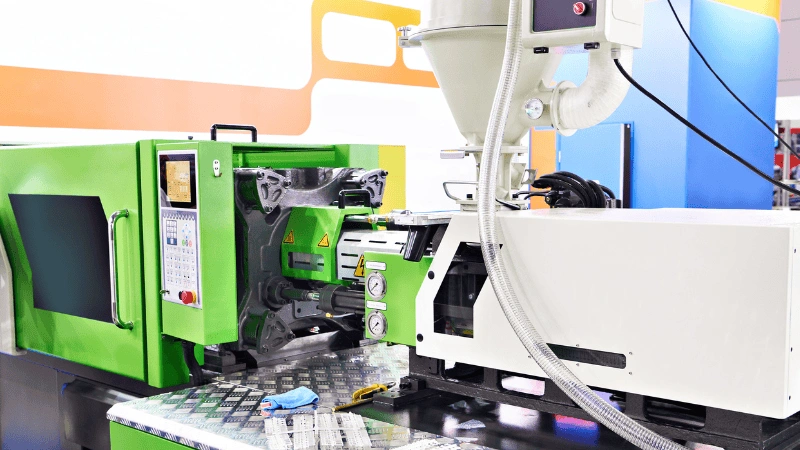
Additives and Catalysts Used in RIM
The reaction injection molding process would not be as successful as it currently is without the use of various additives. These additives include:
- Catalysts: Catalysts are substances that are added to chemical reactions to speed them up, or lower the pressure and temperature needed for the reactions to take place. Amines, tin, zinc, bismuth, and even zirconium have been used as catalysts in the manufacture of polyurethanes.
- Surfactants: These compounds reduce the surface tension between liquid, gas, and solid components. In RIM, they help the polyurethane foam to stabilize and set by keeping the foam from collapsing. They also help to control the size of cells and limit post-curing shrinkage.
- Blowing agents: These substances produce gases that, in turn, form the cells inside the RIM parts. A blowing agent can be either chemical or physical. Commonly used blowing agents include water and liquid carbon dioxide.
- Antioxidants and UV stabilizers: These are added to limit the rate of degradation of the final part.
- Pigments: These are added to give the product a specific color.
- Plasticizers: Plasticizers can be added to make the final part more flexible.
Send your inquiry for prompt quotations!
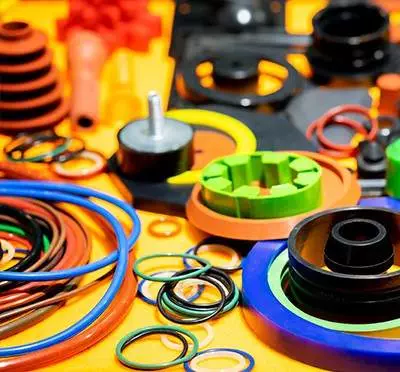
Process of RIM
The basic reaction injection molding process starts with two liquids stored in two separate tanks. These liquids are kept separate and may be at two different temperatures during storage. When it’s time to start the RIM process, the steps below are followed.
Step 1: Measuring or Metering Components
Precise amounts of the liquids are drawn from the storage tanks to be mixed. The amount of the different components used must be tightly controlled because this will affect the properties of the final product. Metering units are used for this purpose.
Step 2: Mixing
The two well-measured liquids are mixed at high pressure with the aid of an impinging mixer. This thoroughly mixes all the liquid components, including any necessary additives.
Step 3: Dispensing Mixture Into Mold
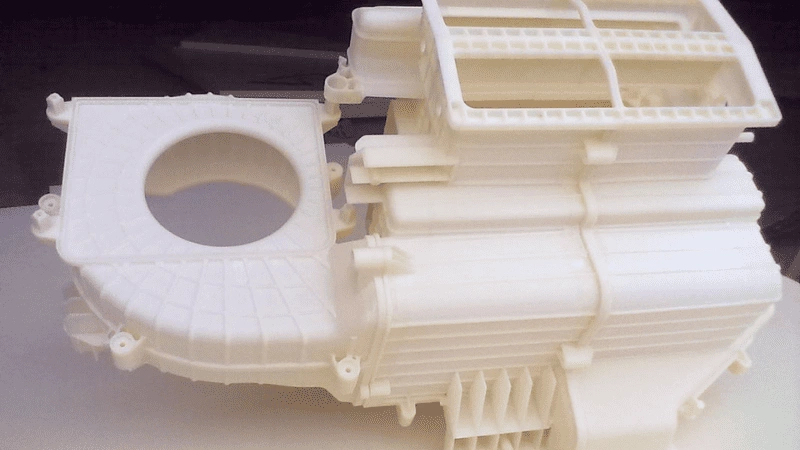
The dispensing of the liquid mixture into the mold cavity takes place soon after mixing because the chemical reactions between the components start when they are mixed.
The liquid is dispensed into the heated mold by the after-mixer which keeps the liquid well mixed while lowering its pressure. The temperature of the mix is also lower compared to traditional injection molding at this stage (140 – 248℉).
When the liquid mixture is in the mold, the components undergo an exothermic reaction. The material is held in the mold long enough for the expansion and curing process to take place. This allows the formed solid to take and retain the shape of the mold.
Step 4: Cooling
The exothermic reaction can result in temperatures within the heated mold reaching as high as 350℉. For the part to be removed by hand, these temperatures must be lowered. This is achieved with the aid of waterlines within the mold.
Step 5: Demolding
Once the part has sufficiently cured and cooled, it is released from the mold. This process must be handled carefully to avoid damaging the fresh part.
Step 6: Post-Processing
This can involve the removal of excess material or applying a treatment or coating to the surface of the finished part if desired by the customer.
Send your inquiry for prompt quotations!
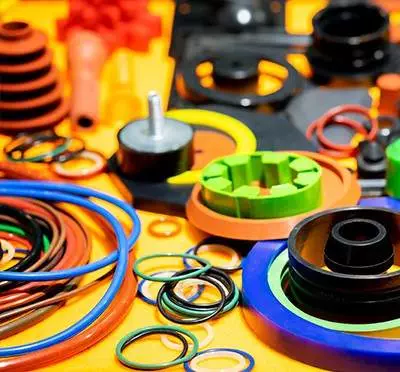
Advantages and Limitations of RIM
Reaction injection molding has a long list of advantages compared to traditional injection molding and other manufacturing processes. These advantages include:
- Superior part properties: The parts made using the RIM process can be stronger, lighter, and more flexible than parts made using other manufacturing methods. This has allowed it to replace even plastic injection molding in some applications.
- Larger and thinner parts: Compared to injection molding, the mixture that is dispensed into the mold in RIM has a much lower viscosity. This mixture can flow more easily, allowing manufacturers to make parts that are larger or those with thinner walls.
- Use of Inserts: Another benefit of the low viscosity of the mixtures used in RIM is that many inserts can be successfully used inside the mold. This allows more complex forms to be achieved in the part.
- Low tooling costs: Setting up plastic injection molding is expensive because the tooling used must be able to withstand high temperatures and pressures. On the other hand, RIM uses lower temperatures and pressures and requires lower clamping forces. This enables the use of less expensive mold materials that are easier to machine including aluminum.
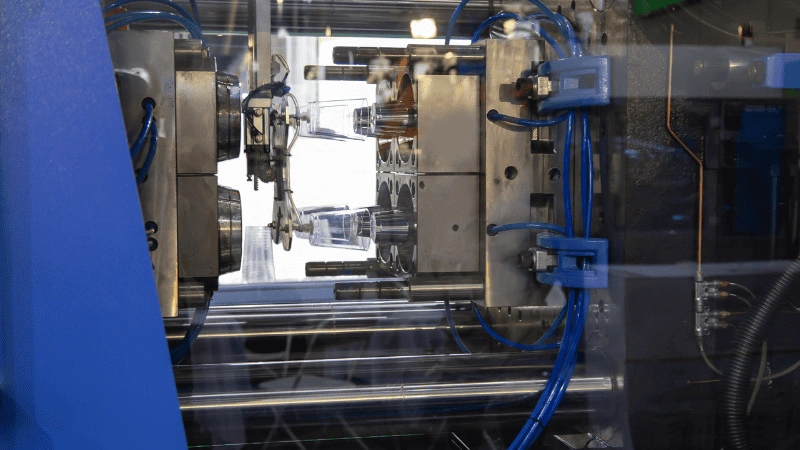
Unfortunately, RIM is not a perfect process and has a few challenges. These include:
- Longer cycle times: Compared to injection molding, reaction injection molding has a much longer cycle time. Injection-molded parts can be produced in seconds, while the cycle times for RIM-manufactured parts are usually several minutes.
- Limited Material Options: Polyurethane may be one of the most commonly used materials, but the RIM process doesn’t currently work with thermoplastic polymers and many other materials.
- Pollutants: Some of the materials used for reaction injection molding produce volatile organic compounds.
- Low-strength tools: The tooling used for RIM can be made from less expensive materials. However, this also makes them easier to damage and less suitable for mass production.
Applications of RIM
RIM-manufactured parts are found in many industries and the list continues to grow. This method of manufacturing is better suited for lower-volume products compared to plastic injection molding.
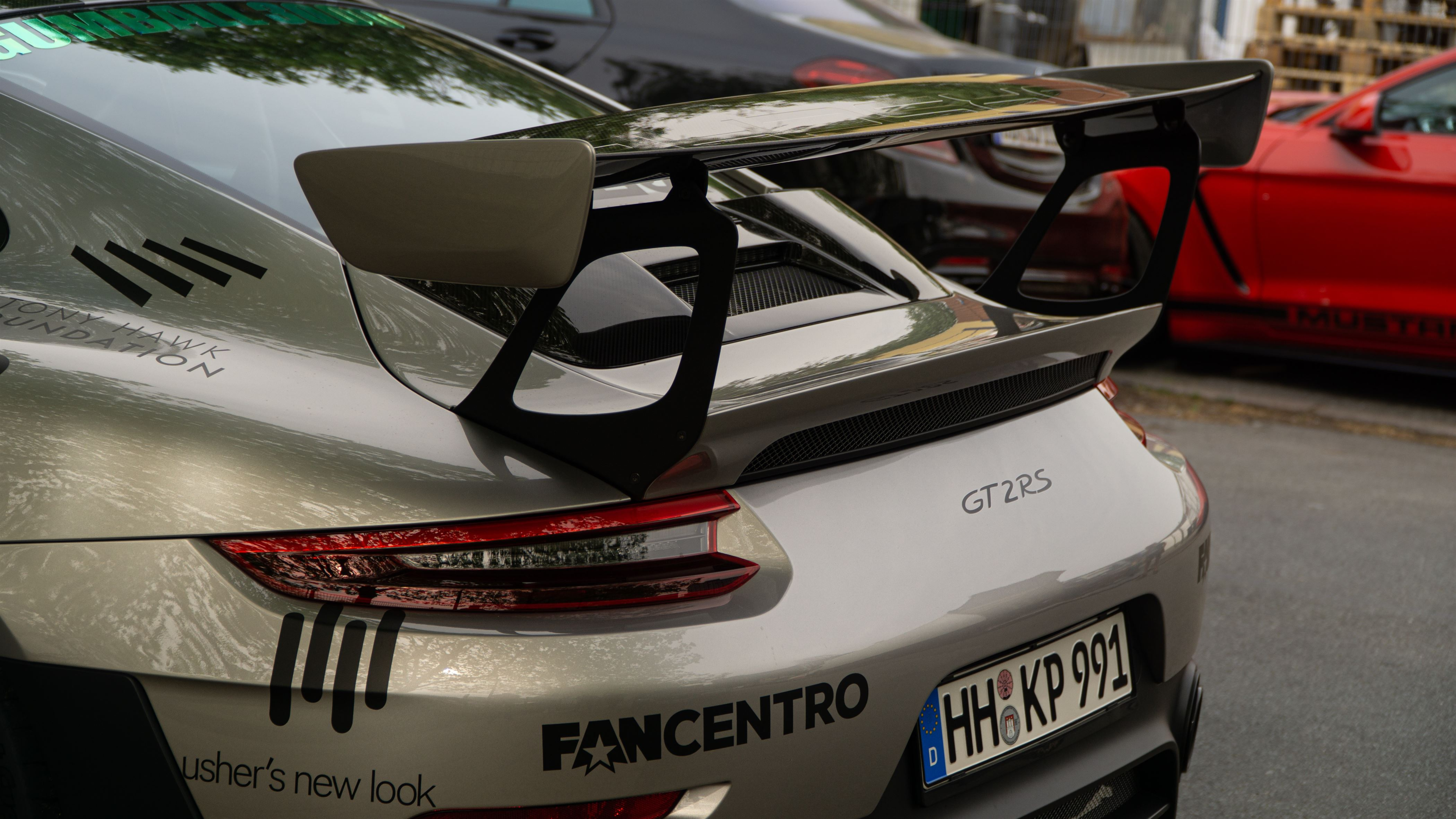
Some notable examples of how RIM products are used include:
- Housings and enclosures for electronics
- Panels and ducts for the aerospace industry
- Engine housings in the marine industry
- Doors, windows, and access panels in the construction industry
- Flexible and elastic products for the sports and recreation industry.
- Automotive bumpers, door panels, armrests, and spoilers in the transport industry
- Enclosures for equipment in the medical industry, such as CT scanners and MRIs.
Send your inquiry for prompt quotations!
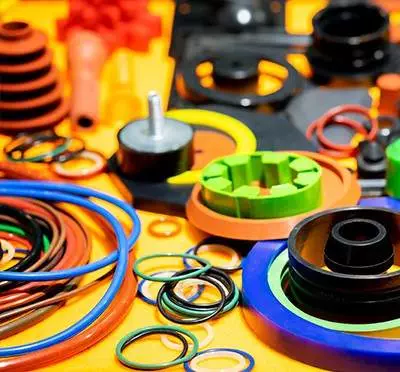
Conclusion
Reaction injection molding is a manufacturing process that produces parts using thermosetting polymers. This gives it several advantages over traditional injection molding, including a lower tooling cost thanks to the lower process temperature and pressure.
RIM-manufactured parts can be reinforced to make them stronger or stiffer. The list of compatible materials is still short, but it is growing. RIM already has a long list of applications in key industries, including the medical, automotive, and aerospace industries.
Let Hongju Answer Your RIM Manufacturing Questions
Are you considering using reaction injection molding for your next product? Working with the right team, Hongju, is just as important as working with the right process.
Reach out to the experts at Hongju today and get their input. You can get to know more about the RIM manufacturing process and what it can do to take your business to the next level.