In this definitive guide, we strive to expand your comprehension of various aspects related to injection molding surface finishes. We will highlight their importance in designing products and their impact on the product’s functionality and aesthetics.
What’s more, we will walk you through the most common surface finish standards and also explain the various post-molding processes to enhance the finish. By the end of this article, both designers and manufacturers will be able to make informed decisions regarding the surface finishes of their specific products. So read on.
What Are Injection Molding Surface Finishes?
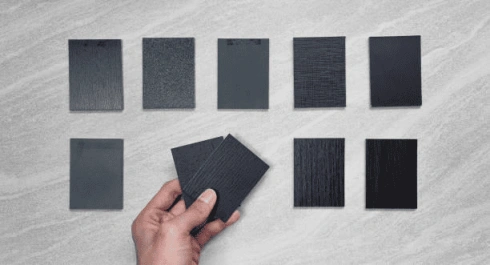
Surface finishes hold significant importance in the world of plastic injection molding, as they play a vital role in shaping the visual appeal and functionality of engineered items. Opting for the appropriate surface finish can substantially elevate a product’s perceived value and overall appearance.
Since the aesthetic appeal of an engineered product is determined by its appearance and how it feels in your hands, the mold surface finish plays a crucial role in it.
For instance, designers can use different textured plastic finishes to improve the appearance of a product. They can opt for a matte or glossy finish to attain the ideal surface quality that appeals more to the customers and increases the product’s perceived value.
Importance of Surface Finishes in Injection Molding
The surface finish of engineered products is one of its most important aspects. In addition to increasing its value, it also plays a crucial role in the product’s functionality and usability.
What’s more, the selected surface finish also affects the molding process as it helps designers and engineers determine the tools, manufacturing process, and raw materials used.
Here’s how surface finish impacts a product:
Increases the Product’s Aesthetics
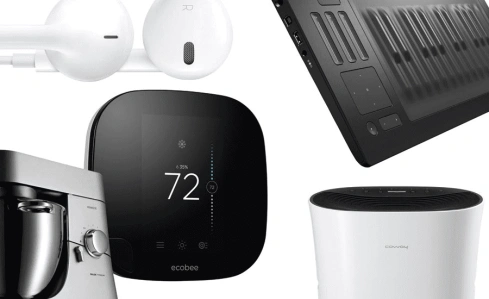
Designers rely on the product’s texture for a variety of reasons. For starters, products that have an excellent surface finish have a positive appeal to customers.
But in addition to giving products a polished look with a matte or smooth texture, the surface finish also hides imperfections that are generated during the product. For instance, you will notice fewer weld lines, tool marks, and sink marks on the injection molded part.
For instance, the surface texture of a product can diminish weld line visibility, tool machining marks, shadow marking, and flow lines on a product.
Improves the Product’s Functionality
In addition to the aesthetic aspect, the surface finish of injection molding plastics also plays an important role in its functionality. For instance, a product design may require it to have a strong grip so the consumers can hold it firmly.
For instance, slip-resistant products such as swimming caps necessitate a texture that offers a firm grip. This also increases the safety and usefulness of such products.
Some other molded products with a paint job may need more surface roughness so that the paint sticks to the surface. A smooth SPI surface finish won’t be suitable for such products.
Additionally, you can opt for a textured surface finish for products with undercuts to get a strong pull.
Inquire Now for Fast Quotations!
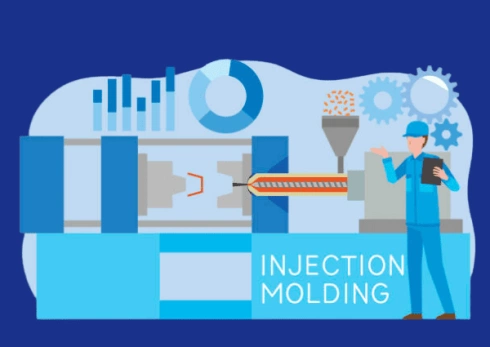
Injection Molding Surface Finish Options
When it comes to injection molding surface finishes, there are three internationally recognized injection molding surface finish standards. These include the PIA (SPI), VDI, and Mold-tech standards. Out of these three, the SPI grades are the most popular standards.
PIA (or SPI) Standards
The Plastics Industry Association (PIA), previously known as the Society of Plastic Industry (SPI), is an independent trade organization based in the U.S. It has established some standard injection molding surface finishes.
There are over 12 plastic surface finish types, which are categorized into 4 categories. These are determined by the aesthetic qualities of each surface finish option. They range from glossy to textured finishes.
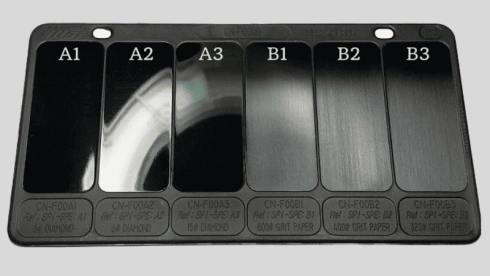
These include:
- Diamond Finish/Gloss Finish – Grade A
Grade A finishes are the most expensive surface finishes that offer an extremely smooth and glossy appearance. They necessitate the use of hardened tool steel molds, which are meticulously buffed through a specialized process employing various grades of diamond buffing.
This unique finishing technique involves a directional rotary polishing method and utilizes a highly refined buffing paste. As a result, it scatters light rays and imparts a texture that isn’t entirely clear. As a result, you get a very glossy and smoother SPI surface finish, also known as the “Diamond” or “buff” finish.
PIA gloss grade finish is ideal for products that require an extremely smooth finish, such as visors or lenses.
This grade is further categorized into 3 SPI standards, namely A-1, A-2, and A-3. The A-2 diamond finish is the most commonly used option. It offers a high gloss finish that gives your products a very aesthetically pleasing surface.
surface finish | SPI standard | Finishing method | Surface Roughness – Ra um (mil) | Cost of surface finish |
---|---|---|---|---|
Super High Glossy finish | A-1 | Grade #3, 6000 Grit Diamond Buff | 0.012 – 0.025 (0.5 – 1) | Very High |
High Glossy finish | A-2 | Grade #6, 3000 Grit Diamond Buff | 0.025 – 0.05 (1 – 2) | High |
Normal Glossy finish | A-3 | Grade #15, 1200 Grit Diamond Buff | 0.05 – 0.1 (2 – 4) | Moderate |
- Semi-Gloss Finish – Grade B
The grade B semi-gloss finishes are achieved by applying various sandpaper grades in a linear motion. This gives the surface a linear pattern and is ideal for getting rid of tooling, molding, and machining parts.
The semi-gloss surface finish gives products a nice appearance while getting rid of any marks that occur while using the machine or tools. This finish is ideal for products that don’t require much of an aesthetic appeal and aren’t for show.
Finish | SPI standard | Finishing Method | Cost |
---|---|---|---|
Fine Semi-glossy finish | B-1 | 600 Grit sandpaper paper | Very High |
Medium Semi-glossy finish | B-2 | 400 Grit sandpaper paper | High |
Normal Semi-glossy finish | B-3 | 320 Grit sandpaper paper | Moderate |
- Matte Finish – Grade C
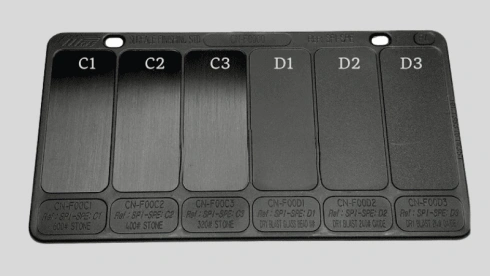
The grade C surface finish, also known as stone finish, is one of the most popular and affordable surface finishes that is achieved by using fine stone powder. This finish helps cover any machining marks and also offers a quick and easy release.
Finish | SPI standard | Finishing Method | Cost |
---|---|---|---|
Fine Matte finish | C-1 | 600 Grit sanding stones | Very High |
Medium Matte finish | C-2 | 400 Grit sanding stones | High |
Normal Matte finish | C-3 | 320 Grit sanding stones | Moderate |
- Textured Finish – Grade D
The grade D textured finish is most commonly used in consumer goods and industrial parts. It offers a great aesthetic appearance to the products but is also ideal for engineered products that don’t require an appealing appearance.
At first, the surface of the product is first buffed using a fine stone powder. Later on, the product is dry blasted using glass beads or aluminum oxide. This process allows you to attain a non-directional and smooth surface finish.
As a result, you get a textured surface on the product that gives you a firm grip, covers any marks, and hides fingerprint smudges.
Finish | SPI standard | Medium | Cost |
---|---|---|---|
Satin Textured finish | D-1 | Dry Blast Glass Bead #11 pressure blasting | High |
Dull Textured finish | D-2 | Dry Blast #240 Oxide pressure blasting | Moderate |
Rough Textured finish | D-3 | Dry Blast #24 Oxide pressure blasting | Low |
Typically, the Grade D textured finish is used in consumer goods featuring handles, such as smartphones, injection-molded parts that require a subdued or satin finish, or thermoset industrial parts.
VDI Standards
Established by Verein Deutscher Ingenieure (VDI), VDI surface finish is the second most popular surface finish standard. It is used by engineers and designers from Europe, North America, and Asia.
An Electrical Discharge Machining (EDM) is part of the machining process to achieve this finish option. However, standard texturing techniques such as stone, sandpaper, and grit can also be used to get this finish.
VDI Value | Description | Applications | Surface roughness (Ra) |
---|
Mold-Tech Standards
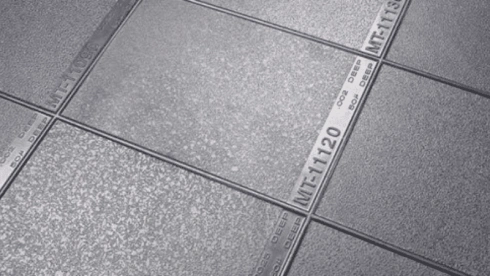
As you can tell from its name, the Mold-Tech standard is based on the Mold-Tech specifications. Like Grade A Diamond finish, Mold-Tech surface finish is classified into four series, namely A, B, C, and D.
The Series A finishes include fine-to-textured matte finishes that don’t require any texturing procedures such as laser or masked chemical etching. They are mostly used on consumer products.
For instance, one of these has a smooth concrete finish, while another one has a sand-like texture.
Mold-Tech surface finishes are achieved by alteration or laser etching of the mold cavity. Each one of them is marked according to the texture depth and the serial number and is indicated by an “MT-” and a five-digit code.
However, these surface finishes are coarser than SPI finishes. Therefore, you will need to use a deviant draught angle of 1.5° for every 0.001″ of the texture depth.
Inquire Now for Fast Quotations!
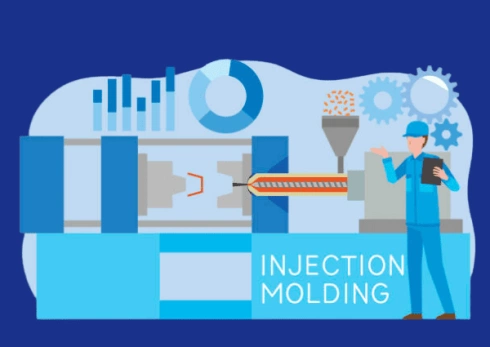
Post-Molding Processes to Enhance Finish
Several post-molding processes can help you achieve the desired finish for molded products.
Whether you want better durability, increased functionality, or improved aesthetics, selecting the right post-molding process according to the industry requirements can help you achieve it.
Some of these processes include:
Painting and Coatings
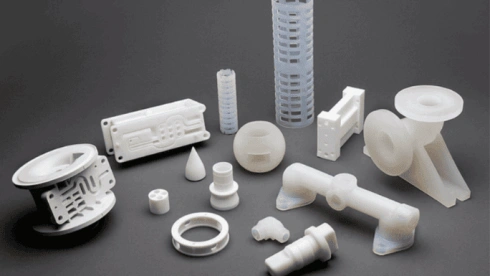
When it comes to enhancing the surface finish of your products, a good paint and coating can prove to be the best element to achieve that. In addition to improving the aesthetics of the product, a high-quality paint and coating also add a protective layer to it.
There are various types of paints and coatings, including liquid paints and powdered coatings. You can customize them to achieve a matte or glossy surface finish. What’s more, you can also protect the molded product from UV rays, abrasion, or moisture with an extra layer of protective coating.
Physical Vapor Deposition (PVD)
Physical Vapor Deposition (PVD) is a highly advanced process that enhances the surface finish of your molded products. It covers the product’s layers with thin layers of materials to obtain a good visual appearance and durable finish.
With PVD, you can get enhanced corrosion protection, better hardness, and higher wear resistance. You can also use this technique to get decorative finishes for your product, including a chrome finish.
PVD is an ideal post-molding process for products from the electronics, aerospace, and automotive industries. It is preferred by many designers and engineers due to its aesthetics and functional benefits.
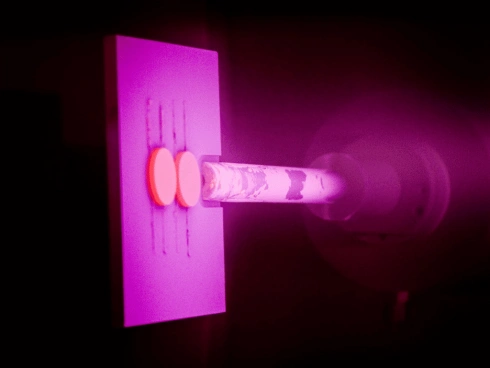
Laser Surface Texturing
Laser surface texturing allows you to enhance both the appearance and the functionality of your products. It is a high-precision technique that involves creating intricate patterns and textures on the product’s surface to get visually pleasing designs.
You can use this technique to improve the grip of your products, get rid of friction, or get a better aesthetic appeal. It’s a highly precise and flexible process that can help you achieve a specific finish on the molded products.
Laser surface texturing can be applied to products from various industries due to its versatility, such as electronics, medical products, and automotive.
Post-Process Polishing
Post-process polishing is a traditional technique used to enhance the surface of molded products. It involves polishing the surface to get rid of any imperfections and spots that are left behind after manufacturing.
With post-process polishing, you can get a smooth and flawless surface. You can also customize this process to get the desired level of gloss and smoothness. Therefore, it can be used for a variety of applications.
Post-process polishing can have significant results on the overall appearance and feel of your product. It is an affordable way to achieve the desired finish without having to opt for expensive techniques.
Inquire Now for Fast Quotations!
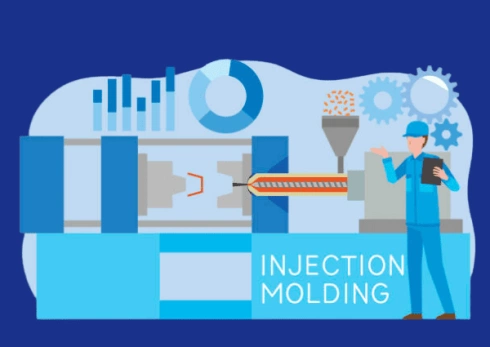
Cost Implications of Mold Finishes
When it comes to the overall functionality and appearance of injection molded parts, mold finishes play a crucial role. However, they can also impact the production cost heavily.
It is important to understand the cost implications of mold finishes before making any decisions. Below are some of the key factors that affect the overall cost of mold finishes:
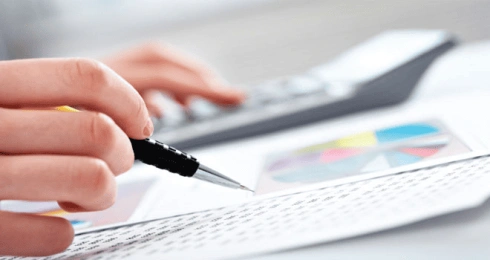
1. Tooling Expenses
Tooling expenses can have major cost implications on mold finishes. Injection molding heavily relies on molds to produce high-quality parts. These molds come in various metals, including steel and aluminum. The choice of metal for these molds has a significant impact on the surface finish of the products.
What’s more, molds are designed to specifically match the precise specifications of the intended product. Molds also have several features that are critical to their functionality, such as cooling channels, runner systems, and precise surface geometries.
Additionally, the Plastics Industry Association (PIA) has established standards to guide engineers in choosing the best mold material for their specific application.
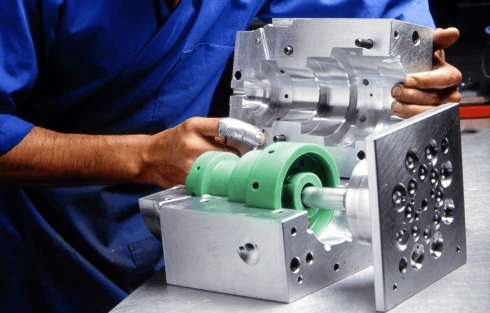
All of these factors play a crucial role in the cost management of the product. Bigger molds with more cavities use extra production and machining efforts, leading to higher costs. A mold with more cavities costs more and has a higher risk of quality issues.
To make sure you don’t have to bear any costly issues, it is important to consider the efficiency gains as compared to increased tooling costs.
You should aim for the right material to manage the tooling expenses effectively. You should aim to find the right balance between staying within the budget and getting the desired finish on the molded products.
2. Production Speed and Costs
The production speed and cost of mold finishes also have serious cost implications. The injection speed in the injection molding process seriously impacts how soon the mold will wear down and require maintenance.
If the production speed is high, it can lead to more frequent repairs, increasing the overall cost of the procedure in the long term. Lower production speed, on the other hand, reduces the overall cost.
3. Type of Post-Molding Process
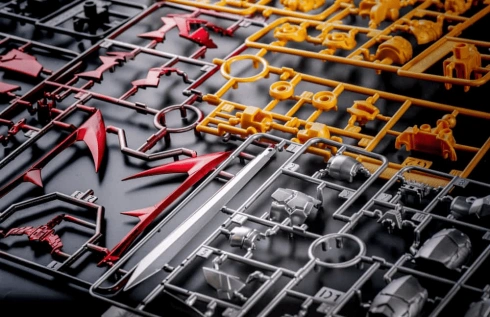
There are various types of post-molding processes with varying costs. The process you choose can significantly impact the cost of the mold finish. Some basic processes, like polishing, are more affordable.
While advanced techniques like Physical Vapor Deposition (PVD) have higher material and equipment costs. Therefore, it is important to choose the right process that offers a tradeoff between the desired finish quality and budget considerations.
4. Production Volume and Batch Size
The production volume and batch size can also seriously impact the cost dynamics of mold finishes. For one-off projects or smaller batch sizes, it is not wise to invest in costly finishes.
On the other hand, for large production volumes, it makes sense to use higher quality and expensive finishes as economies of scale can make the process more cost-effective in the end.
5. Maintenance and Lifespan
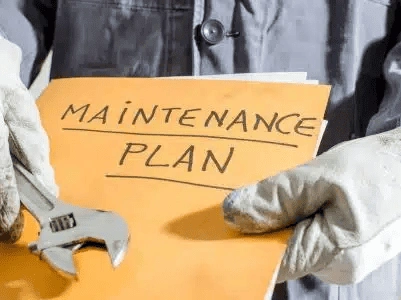
Regular maintenance plays an important role in the lifespan of molds. The cost of maintenance, including the injection molding machine, material, and labor costs, can have a huge impact on the cost of the mold finishes. Neglecting regular maintenance can cause premature wear in the molds and increase the overall costs.
Even though a steep initial investment in high-quality mold finishes may seem costly at first, it can lead to reduced maintenance costs, longer-lasting molds, and lower overall costs over time. So, make sure to consider maintenance during the process so you can extend the lifespan of your mold.
What’s more, if you are producing a high-value product, it’s worth opting for an expensive finish that enhances its functionality and aesthetics. But if you are producing a budget product or mass-producing products, it is better to opt for a more affordable mold finish.
It’s important to find the right balance between production speed and production costs.
Inquire Now for Fast Quotations!
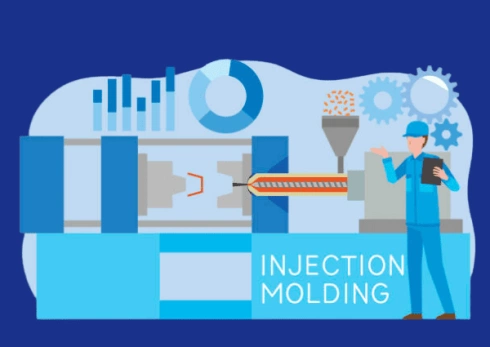
Selecting the Right Surface Finish
Selecting the right surface finish for engineered products is important to achieve the desired functionality and aesthetic appeal.
Below, we outline a structured approach to finding the right surface finish for plastic injection molded parts in the form of a step-by-step guide:
1. Outline Your Specifications
The first step when selecting the right surface finish involves clearly defining your product’s requirements. Outline all the specifications by considering the intended use of the product, its aesthetic requirements, the desired gloss and texture requirements, as well as its functionality.
2. Consider the Choice of Material
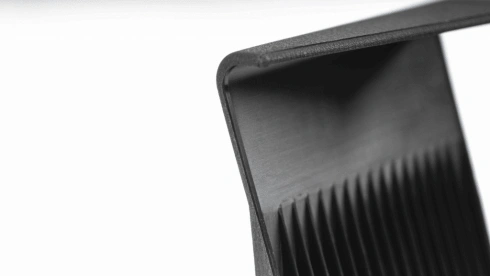
The next step involves taking into account the choice of material for the product. Materials significantly impact the surface finish of a product. While some provide a naturally smoother finish, others necessitate using special finishing procedures.
Make sure to select a material that aligns with your product goals. If you can’t afford a supplementary surface finishing process, make sure to choose a material that offers a naturally smooth surface finish.
3. Learn About the Industry Standards
In the next step, familiarize yourself with the industry guidelines and standards. Organizations like the Plastics Industry Association (PIA) have valuable information regarding mold finishes and materials.
Make sure to learn about these guidelines as they have set standards for injection molding surface finish options.
4. Determine the Need for Post-Molding Processes
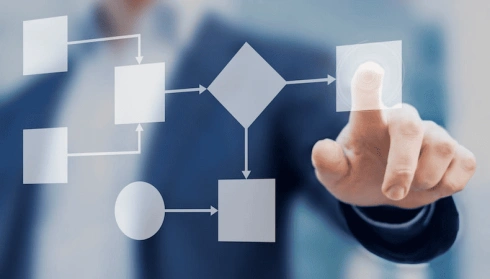
Once you have a good grasp of the industry standards, the next step involves determining whether you will need post-molding processes to attain the desired surface finish. Many post-molding processes enhance the finish of the product.
These include paintings and coatings, laser surface texturing, polishing, etc. Make sure to consider the cost of these processes when determining the need.
5. Select the Mold Material
Many things affect the surface finish of your product. This also includes the mold material you select. Even though aluminum molds are more affordable, they don’t offer a smooth surface finish. Therefore, you will need additional post-processing to get the desired finish.
On the other hand, hardened steel molds offer a smoother surface finish. So make sure to evaluate the mold material according to the required finish.
6. Consider the Product’s Applications
When selecting the product’s surface finish, it is important to consider its intended use. Some products have more of a functional use. So they focus on aspects like relevance for specific tasks and durability. These can include aerospace and industrial machinery components.
On the other hand, for consumer products such as electronics, automobiles, or smartphones, surface finish is an incredibly essential part of a product’s desirability, from a business standpoint. It affects your brand image.
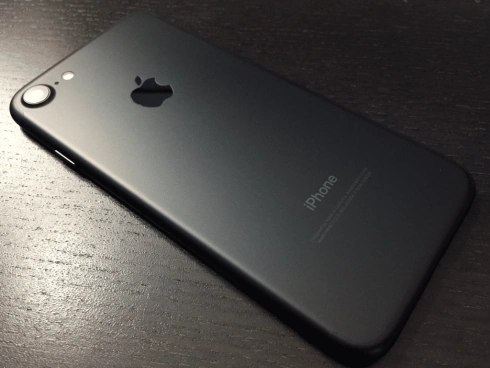
Therefore, it is important to strike the right balance between the aesthetics and functionality of the product, while considering its intended use, industry, and end user.
7. Create Prototypes
Once you have considered the intended use of the product, it is time to carry out practical testing and evaluation. Create test parts and prototypes in several mold finishes to help you evaluate how they affect the product’s feel, performance, and appearance.
By having a real prototype that you can use in real situations, you can get key insights about which surface finish suits your requirements and complements the product’s design. It is a great way to reveal subtle nuances that are not apparent in a theoretical analysis.
8. Do a Cost-Benefit Analysis
For the next step, you evaluate the financial aspects of various surface finish options by doing an analysis of the costs and how they balance against the benefits they provide.
While opting for the perfect surface finish can greatly enhance your product’s visual and market appeal, it is important to consider its cost implications on your budget. This includes both immediate expenses and long-term production costs.
Evaluate how the selected surface finish will affect the maintenance, repair, and replacement needs of the mold over time. It will help you make a cost-effective choice that also aligns with your product goals.
9. Consult With an Expert
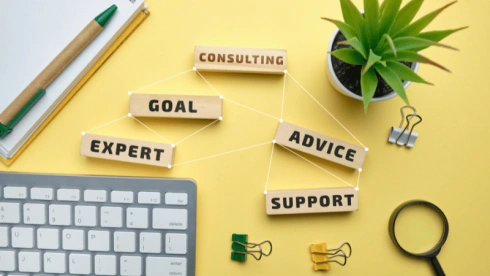
If you are unsure about the most suitable surface finish for your product, reach out to mold design engineers or industry experts. These professionals can provide specific insights and recommendations according to your product and customer base.
With the help of their expertise, you can make the right decision that aligns with the industry standards as well as your product’s requirements.
10. Quality Control
Last but not least, it is important to maintain the desired level of surface finish quality by establishing a quality control process. This can be done by implementing systematic inspections and testing procedures that ensure the selected finish consistently meets your defined standards.
Conducting period quality control assessments can help you identify any issues and make timely corrections to maintain product quality. So it’s important to consistently monitor and validate the surface finish.
Inquire Now for Fast Quotations!
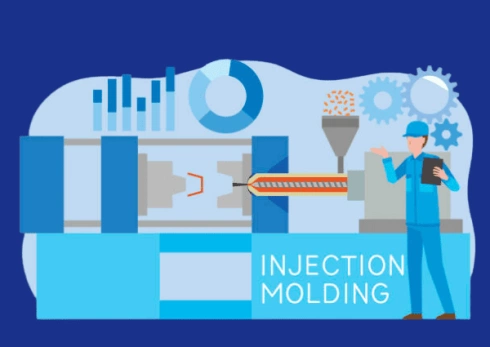
Conclusion
In conclusion, designers and product engineers need to understand the intricacies of injection molding surface finish. This definitive design guide explains everything you need to know about surface finishes and their role in the product’s functionality and aesthetics.
After reading through this article, both designers and engineers are equipped with the knowledge required to make informed decisions regarding the surface finishes of any product. Your journey to achieving the ideal surface finish starts here.
Why Choose Hongju for Injection Molded Products?
When it comes to selecting a partner for your injection molded products, it is painstakingly crucial to make the right choice. Hongju is not just a manufacturer of injection molded parts. We are your innovation partners!
Our customer base includes businesses from diverse industries, including consumer electronics, household appliances, and automotive electromechanics. So, no matter which industry you are from, allow our engineers to help you develop the ideal injection-molded plastic parts with our injection molding capabilities.