According to some experts, 5.9 million tons of plastic products will be injection molded in 2024. By 2029, this value is expected to reach 7.24 million. Given the immense popularity of plastic injection-molded products today, this should come as no surprise.
In this article, we examine plastic injection molding in detail including the steps that form the process, the components of the machines, the materials used, and more. We’ll also examine how injection molding compares to the increasingly popular 3D printing process.
What is Plastic Injection Molding?
Plastic Injection molding is a forming process where a plastic material is transformed into a molten state and injected into a tightly sealed mold. The molten material is held inside the mold until it sets and assumes the shape of the mold, forming the plastic part.

Injection molding can be used to manufacture products using different polymers including thermosets and elastomers. However, this process is mainly associated with thermoplastics.
Companies that use or sell plastic products can choose from a wide range of manufacturing processes including compression molding, blow molding, extrusion, and rotational molding. However, injection molding is more widely used because of benefits such as:
- Design complexity: Injection molding can be used to manufacture parts with a high degree of detail and complexity. This is thanks to the nature of the process, plus advances made in mold design and machining.
- Consistency: Injection molding allows for tighter control of process parameters. A single mold can be used to produce millions of parts with little variation between them.
- Low unit cost: Injection molding has a very low unit cost when used for mass production. This is because the cost of a single mold, the most expensive component, can be spread out over millions of individual parts.
- Quality: The tighter control over the process and a high degree of automation means injection molding can achieve products of higher quality than other plastic forming processes.
- Energy and material efficiency: When used for mass production, injection molding uses very little energy to produce each part. The closed molds also result in very little material wastage.
Manufacturing Process of Plastic Injection Molding
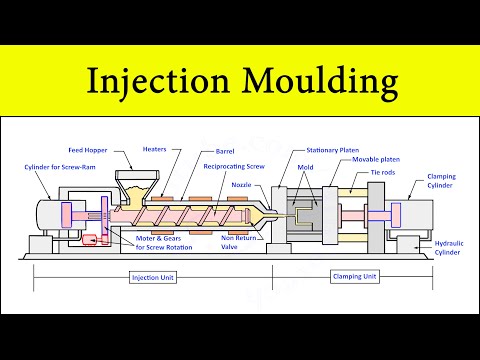
The plastic injection molding process can be summarized into the five steps below. Due to the cyclic nature of production, some of the steps occur concurrently. This quickens the process and keeps production times low.
#1: Material Feeding
The plastic raw material is fed into the barrel of the machine via a hopper. The material is usually in the form of pellets and can be virgin, recycled, or a mix of the two.
Inside the barrel, the plastic pellets are melted by a combination of the pressure from the screw and heat from heating elements outside the barrel. The temperature of the molten material must be carefully controlled to ensure the part can be injected and formed efficiently.
#2: Clamping Of the Mold
The different parts of the mold are clamped together under great pressure. The cavity inside the clamped mold will dictate the shape of the final product. The mold must be clamped at high pressure to prevent the molten material from leaking outside the cavity.
#3: Injection into Mold
When the molten plastic reaches the end of the barrel, the gate used for injection opens and the molten material at the front of the barrel is forced into the mold cavity at high pressure. This is achieved by the forward motion of the reciprocating screw.
The clamping and injection pressure must be balanced to limit flash (material overflow).
#4: Holding and Cooling
During the holding phase, the screw remains in place after the correct pressure has been achieved, this has three notable benefits, i.e.:
- It ensures the mold cavity is fully packed with material
- It prevents the backflow of the material into the barrel
- It reduces the shrinking of the molded part
After holding, the part is held inside the mold a little longer to give it enough time to cool, solidify, and retain the correct shape before being ejected.
#5: Ejection and Post-Processing
Once the part has cooled sufficiently, the mold halves are separated and the formed part either falls out or is ejected using ejector plates or pins.
Depending on the part, some post-processing may be needed before the part is packaged and shipped. This could be the removal of flash, laser etching, etc. Post-processing can be automated or manual.
Send your inquiry for prompt quotations!
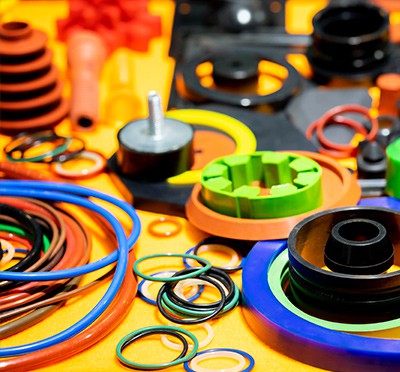
Injection Molding Machine Components
The parts of plastic injection molding machines can be divided into three. These are the injection unit, mold, and clamping unit components.
Injection Unit
The injection unit consists of the hopper, barrel, reciprocating screw, and heating bands. These serve the following roles:
- Hopper: This is the opening through which the plastic pellets are fed into the barrel.
- Barrel: This is the housing for the reciprocating screw. It holds the polymer pellets in one end and the molten material in the gated end.
- Reciprocating screw: The rotating and reciprocating motion of the screw pushes the material from one end of the barrel to the other. The screw also applies the pressure needed for injecting the molten material into the mold.
- Heating bands: These are placed outside the barrel to heat it, helping to melt the plastic material and maintain it at a specific temperature before injection.
Mold
The mold is the part that shapes the molten plastic into the desired shape. It consists of two or more separate parts that are clamped together to form the cavity in the shape of the final product.
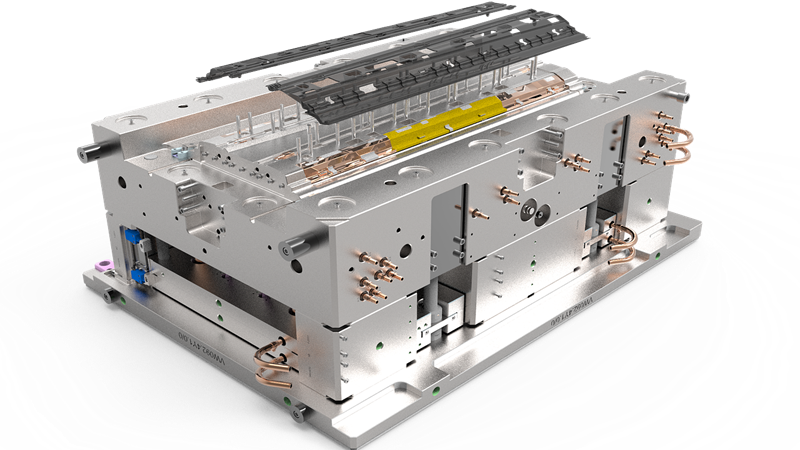
Typical mold parts are:
- Cavity: This part is fixed and creates the space into which the plastic material is injected.
- Core: The core is the movable part of the mold and it fits into the cavity to create the shape of the final part.
- Side action: These are inserts used to achieve undercuts in the mold designs.
- Ejector pins/ ejector plates: These help to remove the cooled part from the mold.
- Cooling channels: These allow a cooling medium to run through the mold to cool the part faster.
In any manufacturing project, the mold is usually the most expensive component. The other parts of the plastic injection molding machine can be reused when making different products. The mold must be replaced for each new product. Even a small change in part design may require machining a new mold.
For long production runs, high-strength steel is used. Machining such materials is expensive and can be made more expensive if the final part is very complex and requires a high degree of accuracy. To lower these costs, prototyping can be done using cheaper materials.
Clamping Unit
The clamping unit applies the pressure that holds the two mold halves in place. It consists of a movable platen that is connected to the mold core. Movement is achieved using a hydraulic system, a toggle mechanism, or a magnetic module.
Send your inquiry for prompt quotations!
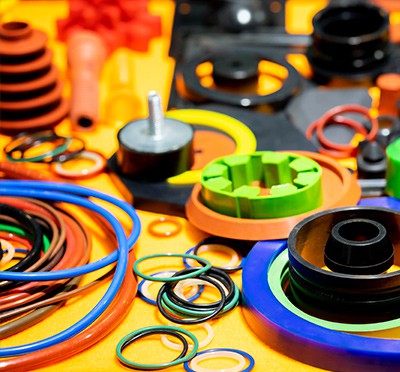
Types of Plastic Injection Molding
There are different forms of injection molding for different types of materials such as thermoset injection molding and liquid silicone rubber injection molding. However, even regular thermoplastics can be molded in more than one way.
Conventional Injection Molding
This is the injection molding process described above. A suitable thermoplastic material is melted and injected into a mold and allowed to cool. The molten material solidifies in the shape created by the two mold halves.
Conventional injection molding is one of the most commonly used processes. Its simplicity makes it easy to manufacture millions of products using a single mold. This is the process used in the manufacture of products such as bottle caps.
Multi-Shot Injection Molding
This is a form of multi-material injection molding that uses two or more injection units. These injection units contain different materials that are injected sequentially creating a layering effect.
Multi-shot injection molding can be achieved by rotating the mold from one injection unit to another or by designing the mold with two gates.
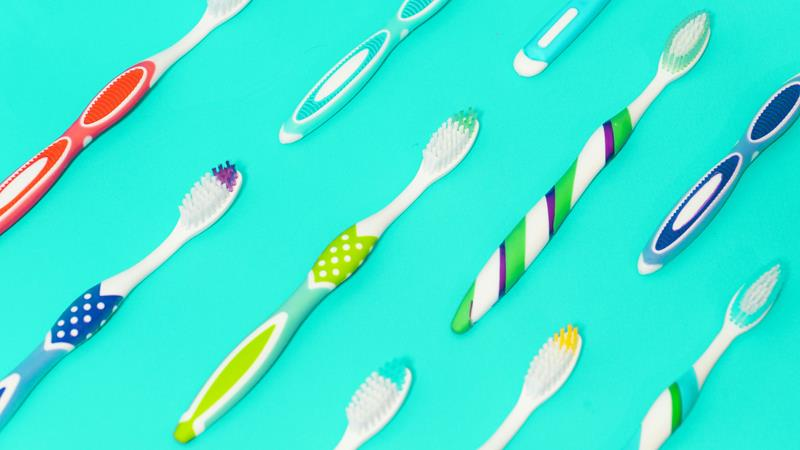
Multi-shot injection molding is used to achieve different effects including manufacturing multi-material parts or creating a soft touch surface on a part. Products made using this method include toothbrushes, plastic cups, power-tool housings, etc.
Micro-Injection Molding
This is injection molding of parts that weigh between 0.1 and 1 gram. The parts should also have tolerances between 10 and 100 microns.
The basic process of conventional injection molding still applies to micro-injection molding but injection molding at this scale requires special considerations. These include:
- Micro molds: The molds used for this process are small in every aspect. Machining the molds requires the use of special tools and techniques including precision CNC and EDM.
- Shot size: The amount of material injected into the mold can be fractions of a gram. This requires injection units that can attain a very high feed resolution.
- Precision: The sizes and applications of the parts made using this method mean they have smaller tolerances than parts made using other injection molding processes.
Micro-injection molding is used for manufacturing plastic parts for many applications including smartphone components, drug delivery systems, hearing aid components, motor parts, etc.
Insert Molding
Insert molding is a form of injection molding where the material is injected over an existing plastic or metal part. For instance, the material can be injected over metallic screw threads to create a plastic part with stronger threads.
The molten plastic cools around the insert, creating a permanent bond between the two. This results in strong yet lightweight parts.
In this process, the insert is placed inside the mold before injection. This can be done by hand or it can be automated to achieve greater quality and consistency, and lower cycle times. Examples of parts made using insert molding include electrical plugs, screw fasteners, pins with plastic heads, etc.
Send your inquiry for prompt quotations!
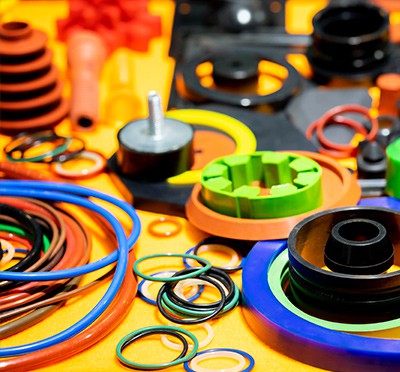
How Do You Choose Plastic Material for Injection Molding?
Material selection is a critical point in the injection molding process. The material chosen will affect process parameters, production times, and mold materials. More importantly, the material will also affect the suitability of the finished part for the application.
Semicrystalline Vs Amorphous Thermoplastics
Plastics used for injection molding are typically either semicrystalline or amorphous. In amorphous plastics, the polymer chains that form the molecular structure are randomly entangled. In semi-crystalline polymers, the polymer chains are structured in some way.
This difference in molecular structure affects certain qualities of thermoplastics including their response to heat, transparency, chemical resistance, and fatigue resistance. Common qualities of semi-crystalline thermoplastics include:
- Sharp melting points
- High opacity
- Good chemical resistance
- High fatigue strength
- Aren’t easily bonded using solvents and adhesives
Common examples of semi-crystalline thermoplastics are polypropylene, polyethylene terephthalate (PET), and HDPE.
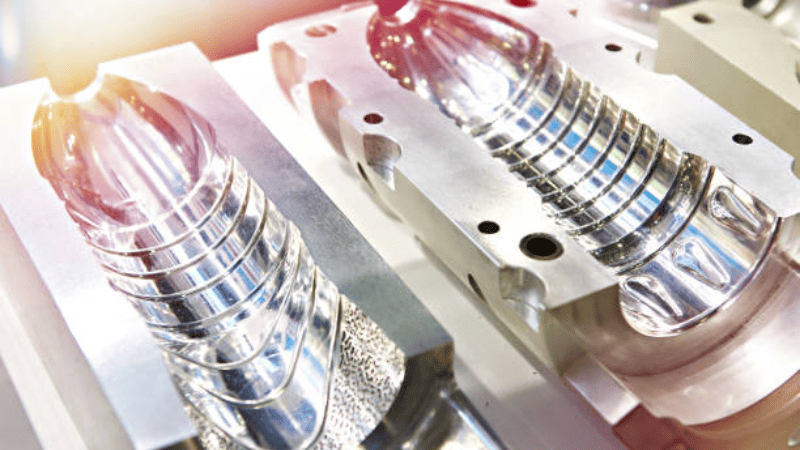
On the other hand, amorphous thermoplastics have qualities such as:
- Ease of molding
- High transparency
- Low chemical resistance
- Can be bonded using solvents and adhesives
- Soften across a wider temperature range
Examples of amorphous thermoplastics are polycarbonate, polystyrene, ABS, and acrylic.
The choice of amorphous or semi-crystalline thermoplastic will depend on the specifics of the application. Semi-crystalline plastics are good for applications where a high degree of wear is expected while amorphous thermoplastics are best restricted to structural applications. However, there are other important considerations to keep in mind as well.
Considerations When Choosing Injection Molding Materials
The selection of a specific thermoplastic for an injection molding project is dictated by the application of the final part.
1. Operating temperature
The performance of plastics changes at very cold or high temperatures. The temperature extremes of the application should be considered when choosing the material since different plastics respond differently to these extremes.
Acrylic and ABS are both amorphous, but acrylic has better temperature resistance. This means it can operate at higher temperatures than ABS.
2. Exposure to the Elements
Certain plastics should only be considered for injection molding if the application will be indoors.
In the outdoors, plastic parts can be exposed to high and low temperatures, extreme temperature swings, UV, and moisture.

These factors can contribute to the faster degradation of plastics such as PLA. Materials such as polypropylene fare better when used outdoors.
3. Strength
If a plastic part will be subjected to a load, it must have the strength to sustain the load. A few examples of plastic parts being subjected to loads include:
- Pipe fittings being exposed to high internal pressures from liquids or gases
- Plastic gears being used to transfer motion
- Plastic hangers being used to hold parts, etc
Different types of strengths should be considered as well. Some materials have excellent tensile strength but poor compressive or flexural strength. This means you must consider the specific way the part will be loaded.
4. Chemical Exposure
Plastics respond differently to chemicals. For example, ABS reacts with acetone and should not be used in an environment where acetone is heavily used or stored. Look up how any plastic you’re considering using behaves when exposed to different chemicals to avoid premature failure.
5. Safety
If an injection molded part will be in contact with human skin or used for eating, it must be certified safe for that application.
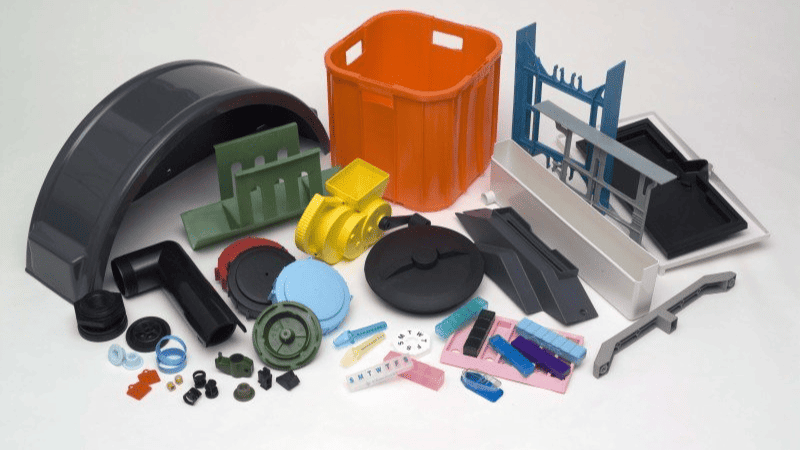
Many everyday plastics are not food-safe and can cause different reactions if they come into contact with human skin. This is especially important where there will be repeated or prolonged exposure.
6. Cost
Plastics are generally considered inexpensive but there are different types of plastics and some are more expensive than others.
Some plastics have been in mass use for longer and have established supply chains and predictable demands. They may also be easier to manufacture and will, therefore, be cheap. Others are on the opposite end of the spectrum and therefore cost more.
The unit cost of choosing one plastic over another may seem minimal but when manufacturing millions of parts, the impact of the more expensive material will be significant.
Send your inquiry for prompt quotations!
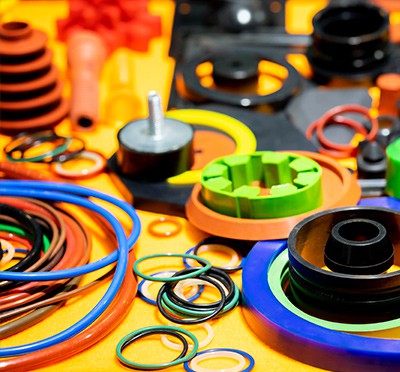
3D Printing Vs Injection Molding
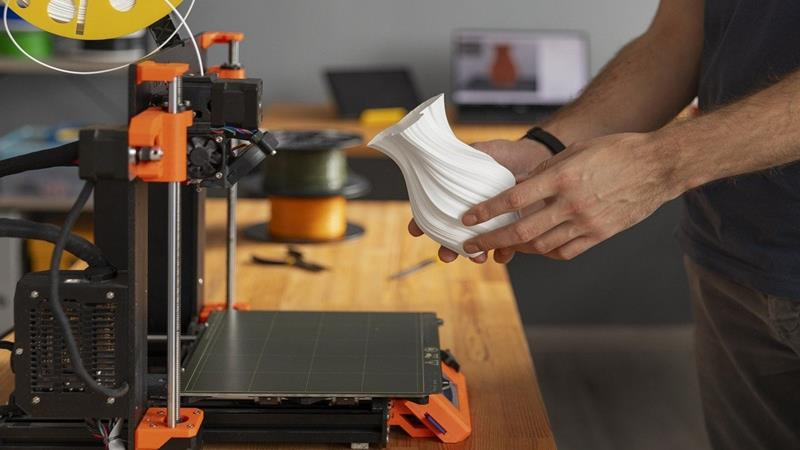
The rise of 3D printing has led to comparisons between these two manufacturing technologies. However, there are many important differences between injection-molded and 3D-printed products. The table below summarizes how these two technologies compare.
Property | Injection Molding | 3D Printing |
---|---|---|
Cost | High setup costs, low part cost | Low setup cost, high part cost. |
Capacity | Thousands or tens of thousands of parts per day | <100 parts per day depending on size |
Lead times | Long lead times due to time needed to design and machine mold. | Short lead times |
Part size | Can be very small, very large, and anything in between. | The largest commercial 3D printers are typically restricted to 1m3. |
Design Flexibility | Design changes can’t be easily implemented. | Design changes are easy to implement. |
Surface finish | No layer lines | Some 3D printing technologies have visible layer lines. |
Despite many people’s perception, injection molding and 3D printing are not competing technologies for the most part. Each technology has specific advantages that make it an ideal choice for certain applications.
Plastic injection molding is the standard option for mass production. The high cost-per-part associated with 3D printing and the low speed of manufacturing each part make it a less-than-ideal choice. Injection molding is also the better choice where specific surface finishes are desired or if a part requires different materials or inserts.
On the other hand, 3D printing is unbeatable when the lead times for production are extremely short or where low manufacturing volumes make mold production too expensive. It’s also the ideal choice for prototyping when different iterations of the same product must be tested.
Challenges and Considerations In Plastic Injection Molding
There are certain challenges you have to plan for when considering injection molding. If not properly addressed, these challenges can undermine the success of the project.
Design Considerations
Injection molding molds must be designed with injection molding in mind. Apart from accuracy and consistency, the mold design should facilitate quick and easy part ejection. It must also have features such as vent holes, sprues, gates, and cooling channels at the right locations.
Poorly designed molds can result in defects and long injection molding cycle times.
Tooling Costs
Injection molding comes with a high initial cost. This is mainly due to the cost of the mold. The use of less expensive mold materials e.g., aluminum, should be considered if the production volume will be low.
Quality Control
Quality control can make or break the injection molding project. You can end up with defective parts due to poor mold design, poor process control, low-quality materials, mold defects, etc.
Quality control measures must be implemented at all stages of the plastic injection molding process to detect these issues early and limit their impact on the overall project.
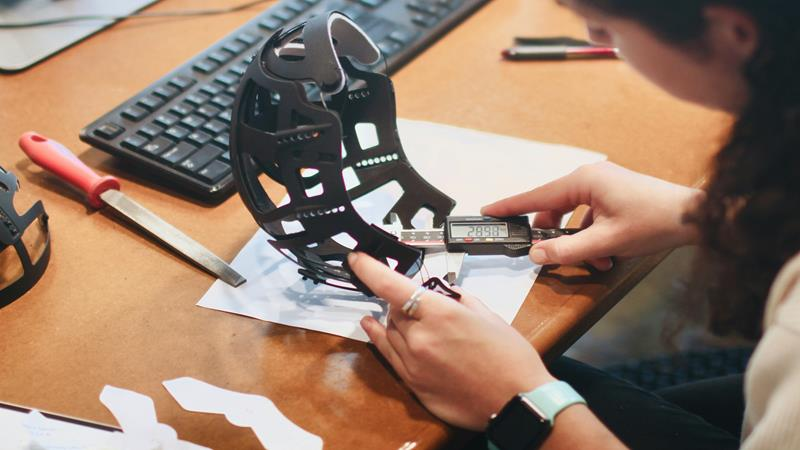
There are automated measures that can be deployed on the production line and physical measures that require operators on the production floor and a good communication system.
Send your inquiry for prompt quotations!
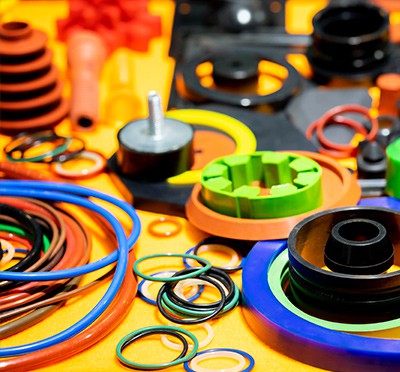
Conclusion
Plastic injection molding remains one of the most important manufacturing processes in the world today. Despite its high setup cost, no other process is as cost-effective for mass production.
There are different types of plastic injection molding processes today and the list of compatible materials is long. If you choose to use plastic injection molding, remember to work with experts who can help you get the best out of this process.
Why Hongju Silicone Is the Plastic Injection Molder You Need
If you need plastic injection molding services for your next big project, Hongju Silicone is the right partner. We have 23 years of design and manufacturing excellence and our plastic and silicone rubber parts are used all over the world. We have partnered with other companies to manufacture OEM and ODM parts and you too can benefit from our low MOQs and rapid deliveries. Visit our website to find out more about our services.