In this concise exploration, we spotlight the seven essential post-processing acts that elevate a simple mold to a masterpiece. Embark with us on this less-trodden path where precision-engineered parts receive their final polish, ensuring they don’t just leave the factory, but make their mark upon arrival.
Importance of Post Processing for Injection Molded Parts
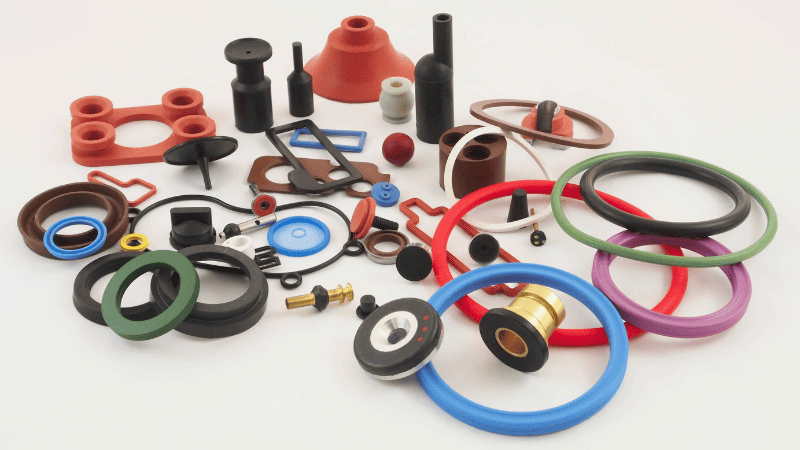
Post-processing is a critical phase in the injection molding process, ensuring that each part not only fits its purpose but also exceeds expectations. It is where precision meets durability, and aesthetics blend with functionality.
Post-finishing treatments, such as trimming and deburring, eradicate any imperfections that could compromise product integrity or impede performance. Advanced surface finishes enhance resistance to environmental stressors and can be tailored to meet specific tactile or visual requirements.
This stage is integral for achieving a level of sophistication that resonates with quality-focused markets and is crucial for products that aim to lead rather than follow. It’s an investment in the product’s lifecycle, contributing to a reduced need for replacements and affirming the brand’s commitment to excellence.
Precision Trimming and Flawless Finish
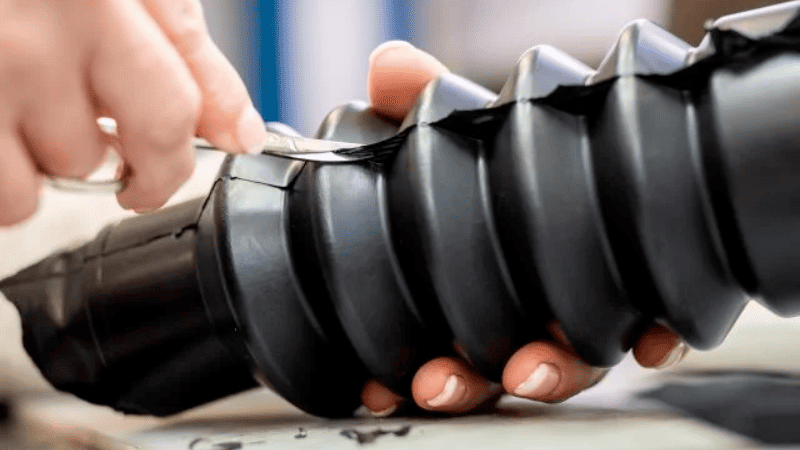
- Removing Excess Material with Expertise
In the meticulous process of plastic injection molding, precision trimming is critical. At Hongju Silicone, we excel in efficiently removing sprues, runners, and any excess flash, a necessary step to meet the high standards of injection molded parts. Our skilled technicians use specialized equipment to cut away these imperfections, ensuring each plastic component is immaculate and conforms to exacting specifications.
- Achieving Smooth, Seamless Edges
Deburring is an essential post-processing step that Hongju Silicone perfects for every injected molded part. This process involves smoothing edges to remove burrs, resulting in a clean finish that complements the part’s design. We utilize a blend of manual and automated deburring techniques, designed to accommodate a variety of plastic surfaces and part geometries. These methods not only improve the tactile quality but also prevent any potential issues during assembly or end-use.
Inquire Now for Fast Quotations!
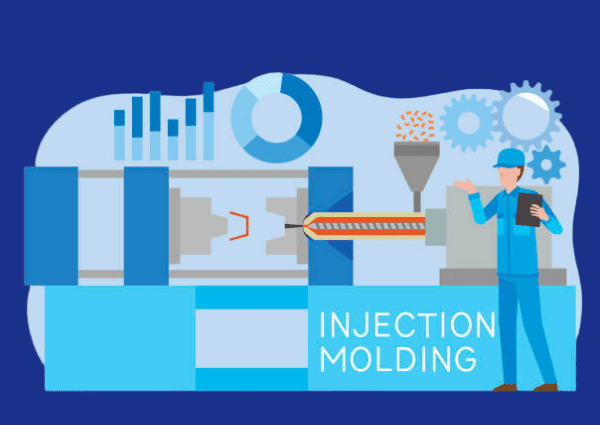
Surface Finishing: Enhancing Aesthetic and Functionality
After the initial post-molding steps, surface finishing is paramount to enhance both the aesthetic appeal and functional characteristics of the plastic injection molded parts. Hongju Silicone takes pride in its comprehensive range of finishing techniques that not only improve the appearance but also enhance the performance of the products.
A Spectrum of Finishing Techniques
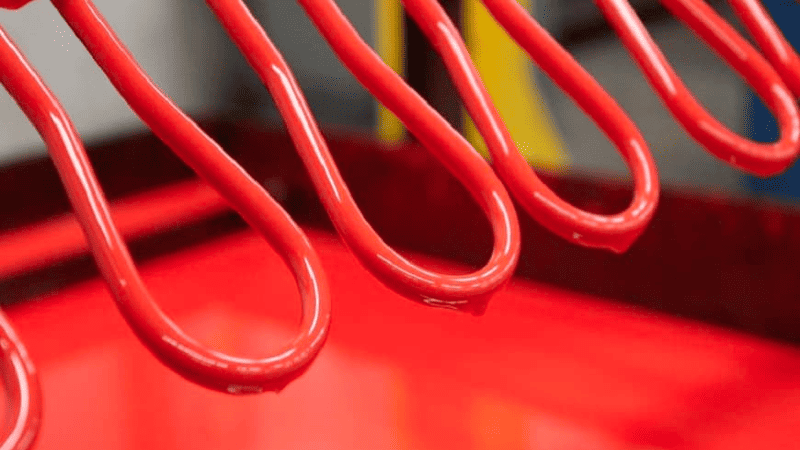
Our repertoire of surface finishes includes a variety of textures and polishes that can be customized to the needs of the plastic component. Whether it’s achieving a matte look or a high-gloss shine, our finishing processes are designed to meet diverse industry standards. We consider factors such as the type of plastic resin used and the intended use of the product to select the most appropriate finishing method.
Functional Finishes for Optimal Performance
In the realm of injection molding, where molten plastic is transformed into precise components, the post-processing step of surface finishing is crucial. Hongju Silicone doesn’t just improve the appearance; we ensure that each plastic injection molded part functions at its best.
Our post-processing techniques are designed to enhance the properties of the plastic, increasing resistance to environmental factors, chemical treatments, and mechanical stress. For example, parts requiring low friction surfaces benefit from our specialized coatings, while others might need to resist chlorinated solvents or higher temperatures, particularly in high injection scenarios.
We also cater to niche requirements such as injection molded parts for medical devices, which demand finishes that inhibit bacterial growth. By employing finishes that are both cleanable and resilient, we create surfaces on plastic housings that meet the stringent hygiene standards of healthcare environments.
Heat Treatment: Enhancing Material Properties
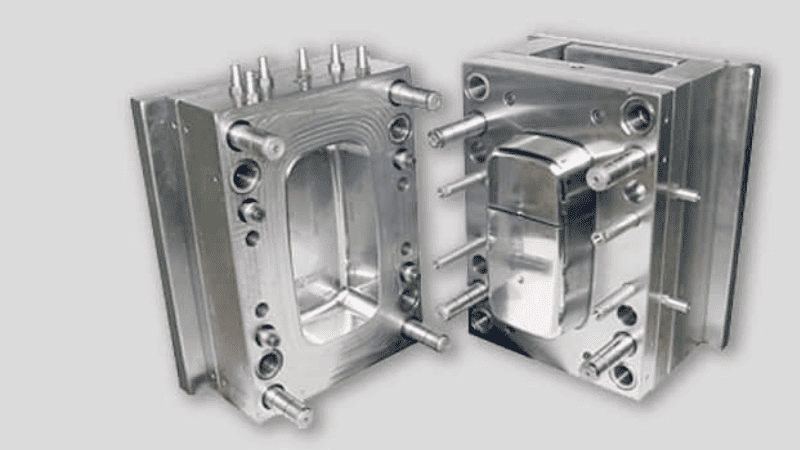
Heat treatment plays a pivotal role in the post-processing of injection molded parts, serving as a method to improve mechanical properties and relieve residual stresses. At Hongju, we utilize controlled heat treatment processes to optimize the performance of plastic components, ensuring they can withstand higher temperatures and stress conditions.
- Stress Relieving: After the injection molding cycle, parts may contain internal stresses due to high injection pressures and cooling rates. A carefully managed heat treatment can alleviate these stresses, enhancing the tensile strength and impact resistance of the plastic parts.
- Enhancing Performance: By tailoring heat treatment parameters to the specific type of plastic, Hongju maximizes the properties of the plastic. This can result in improved high-temperature performance and longevity, making each part a good candidate for demanding applications.
- Precision in Process: Using state-of-the-art equipment, we ensure that heat treatment is applied uniformly across the part. This attention to detail prevents deformation and maintains the integrity of the plastic surface — critical for parts that require high precision, such as those used in CNC machined assemblies.
Hongju’s commitment to excellence extends to our heat treatment processes, where we apply our expertise to enhance the properties of plastic in the production of plastic parts. By doing so, we ensure that the parts not only meet but exceed the rigorous demands of their applications.
Inquire Now for Fast Quotations!
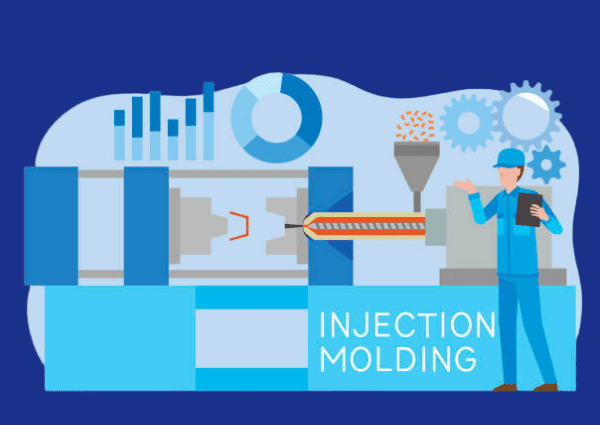
Plating and Metalizing: Achieving Superior Aesthetics and Functionality
Plating and metalizing are transformative processes in the world of injection molded parts, where plastic surfaces are coated with metal to provide a unique finish and additional properties.
- Aesthetic Appeal: Through plating, parts can exhibit a metallic sheen, giving the appearance of solid metal at a fraction of the cost and weight. This process is crucial for components in the consumer electronics industry where visual appeal is paramount.
- Enhanced Durability: Metalizing plastic parts not only improves their appearance but also increases their wear resistance and electrical conductivity. This is particularly beneficial for plastic components that require a robust finish to extend their lifecycle.
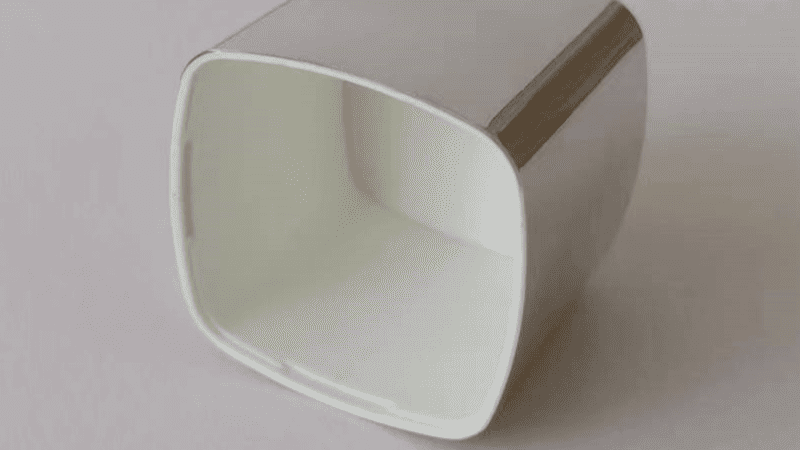
Incorporating plating and metalizing into the post-processing of plastic injection molded parts adds significant value, transforming ordinary plastic housings into premium-grade components. With Hongju’s commitment to quality, these processes are meticulously monitored to ensure the highest level of performance and aesthetics.
Chemical Treatments: Enhancing Properties and Performance
Chemical treatments play a pivotal role in the post-processing of plastic injection molded parts. These processes are employed to enhance the performance characteristics of plastic surfaces, ensuring they meet specific functional requirements.
- Surface Activation: Chemical treatments can be used to alter the surface energy of plastic parts, which is crucial for adhesion in painting or bonding applications. Surface activation processes prepare plastic surfaces to bond securely with coatings or other materials.
- Stress Relieving: Some injection molded parts may undergo stress-relieving treatments to remove residual stresses caused by the molding cycle. This can prevent warping or deformation, maintaining the dimensional integrity of complex parts.
- Enhancing Resistance: Treatments can impart good chemical resistance to plastics, making them suitable for harsh environments. By selecting the appropriate chemical treatment, plastic components can resist degradation from exposure to chlorinated solvents or other aggressive chemicals.
Inquire Now for Fast Quotations!
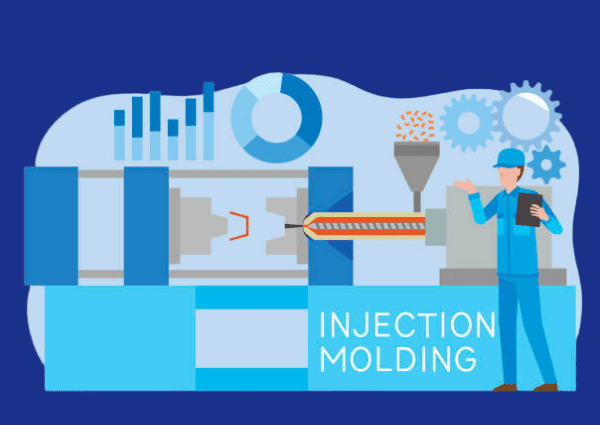
Quality Control and Inspection: Ensuring Excellence in Every Part
Quality control and inspection are critical stages in the injection molding post-processing sequence where each plastic injection molded part is meticulously evaluated to ensure it meets the established standards and specifications.
- Dimensional Accuracy: Using advanced measuring tools and equipment, technicians verify the dimensions of plastic parts to confirm they adhere to precise design requirements. This step is vital to prevent issues in the assembly or function of the part in its final application.
- Surface Inspection: The plastic surface is scrutinized for flaws that could affect the appearance or performance of the part. Defects such as sink marks, weld lines, or short shots are identified and addressed.
- Functional Testing: Parts may undergo various functional tests to simulate their performance under actual working conditions. This could include stress testing, impact resistance checks, and fatigue testing, ensuring the plastic component will perform as intended.
Hongju’s Commitment
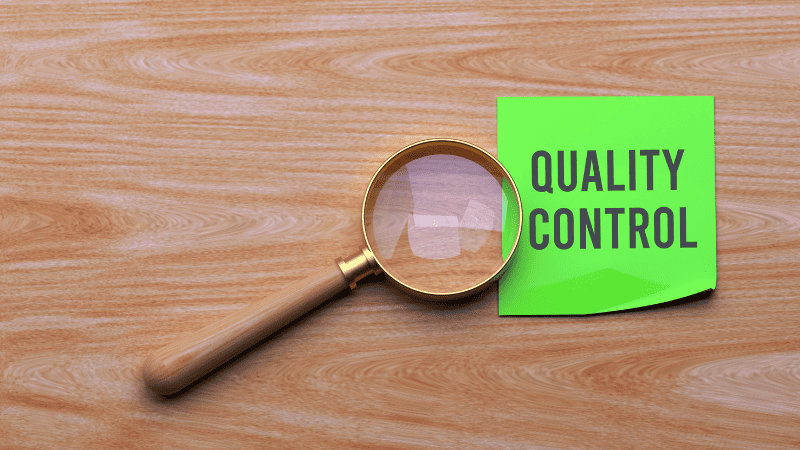
At Hongju, we incorporate state-of-the-art quality control protocols and inspection methods to guarantee that every component not only looks flawless but also functions optimally. With a keen eye for detail, our quality experts are integral to our promise of delivering excellence.
Each part is a testament to our commitment to quality, reflecting the care and precision that goes into our manufacturing process. From the design process to the final quality inspection, Hongju Silicone ensures that every part aligns with our client’s expectations and our stringent quality benchmarks.
Packaging and Shipping: The Final Touch in Injection Molding Post-Processing
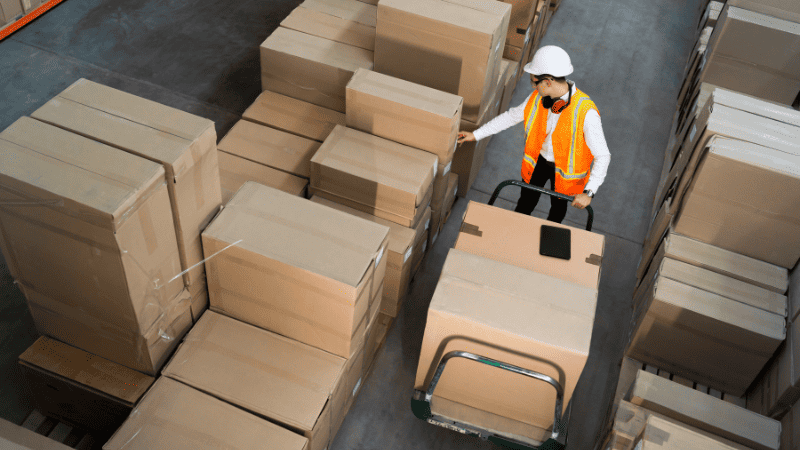
The final step in the journey of an injection molded part is packaging and shipping, where the emphasis is on protecting the part’s integrity until it reaches the customer.
- Secure Packaging: The plastic injection molded parts are carefully packed to prevent damage during transit. Materials used for packaging are chosen based on the properties of the plastic and the part’s design to ensure maximum protection.
- Tailored Solutions: At Hongju, we understand that each part might require unique packaging solutions. Whether it’s bulk packaging for plastic housings or individual wraps for complex components, our packaging is designed to protect and preserve.
- Shipping Logistics: Our logistics expertise means we can deliver parts anywhere in the world efficiently and on time. We manage everything from the size of the injection molding package to the shipping method, ensuring that your parts arrive in perfect condition.
- Eco-Friendly Options: We are committed to sustainability, and our packaging materials reflect this commitment. Whenever possible, we use recyclable or biodegradable materials to minimize environmental impact.
Hongju’s meticulous approach to packaging and shipping is an integral part of our end-to-end service offering, ensuring that the quality crafted within the walls of our facility is maintained all the way to your doorstep.
Inquire Now for Fast Quotations!
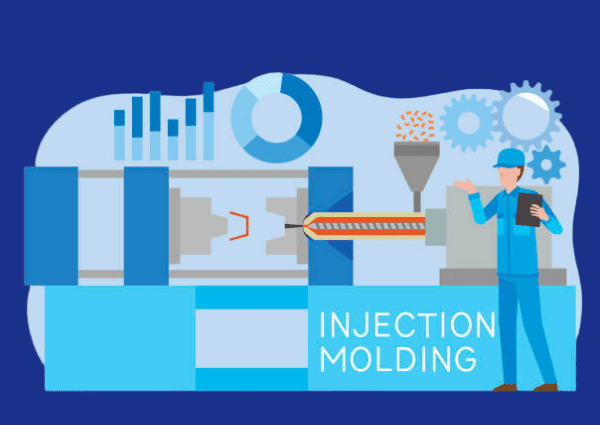
Conclusion
In wrapping up our exploration of the 7 post-processing steps in injection molding, it’s clear that each stage is crucial in transforming a molten plastic concept into a market-ready product. From the initial trimming and deburring to the delicate surface finishing, followed by heat treatment, plating and metalizing, and chemical treatments, every step is performed with precision. Quality control and inspection ensure that no defect goes unnoticed, maintaining the high standards set forth by Hongju.
Choose Hongju for Superior Injection Molding Services
Discover the difference Hongju Silicone can make with our advanced injection molding services. For precision, quality, and care that set industry standards, contact us! Elevate your products with Hongju’s commitment to excellence.