Mastering the understanding of this pressure and its influence on the molding process is crucial for ensuring the production of high-quality plastic parts. In this article, we’ll delve deep into the world of injection pressure, its types, and the factors that affect it.
What is Injection Pressure?
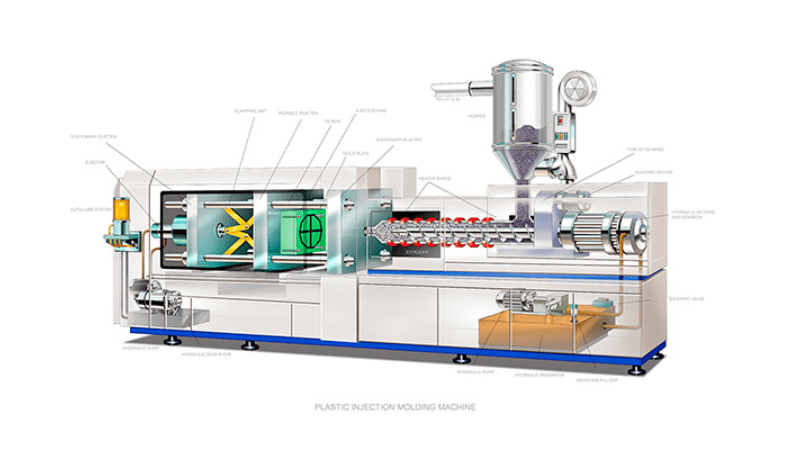
Injection pressure is a pivotal parameter in the plastic injection molding process. It determines the force with which the molten plastic material is introduced into the injection mold. Measured in pounds per square inch (psi), it’s exerted by the machine’s hydraulic system to push the molten plastic through the nozzle into the mold cavity.
How does injection pressure affect mold filling?
Proper injection pressure is essential for achieving a complete fill of the mold cavity. When the molten plastic is injected, it must have enough force to overcome any resistance met during flow. This is paramount because insufficient injection pressure can lead to incomplete filling, and spawning defects like short shots or voids.
How does injection pressure affect material flow rate?
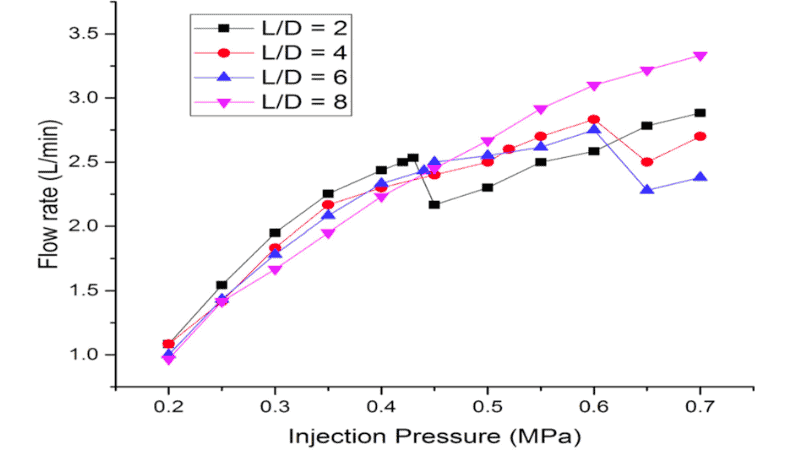
The direct relationship between injection pressure and material flow rate is vital. Higher pressures translate to faster flow rates, facilitating the quick filling of complex geometries and thin-walled sections. Conversely, lower pressures might cause a slower flow, potentially leading to issues such as flow hesitation or premature solidification of the material.
Aptly setting the injection pressure holds benefits:
- Filling the mold: Ensuring the entire mold cavity is filled lets the molten material reach every mold feature.
- Compensating for material viscosity: Different plastics vary in viscosity, and adjusting the injection pressure ensures a consistent material flow.
- Achieving desired polymer flow rate: The polymer flow rate must be optimal. Injecting too fast can cause defects, while too slow might not fill the mold.
- Minimizing defects: An ideal injection pressure can curb common defects like sink marks. However, excessive pressure may give rise to problems like flashing, where excess material squeezes out.
In essence, managing the correct injection pressure is pivotal. It should be adequate to fill the mold but not so excessive as to compromise the final product’s integrity.
Take the First Step:
Requst for an Inquire
Quality Meets Affordability. Inquire Now for High-Quality Products at Low Volumes.
Types of Injection Pressure
In the realm of plastic injection molding, understanding the nuances of various pressures is pivotal to ensuring optimal product quality. The key pressures in this manufacturing process include injection pressure, holding pressure, and backpressure. Each plays a unique role and has distinct implications for the molding process.
Injection Pressure
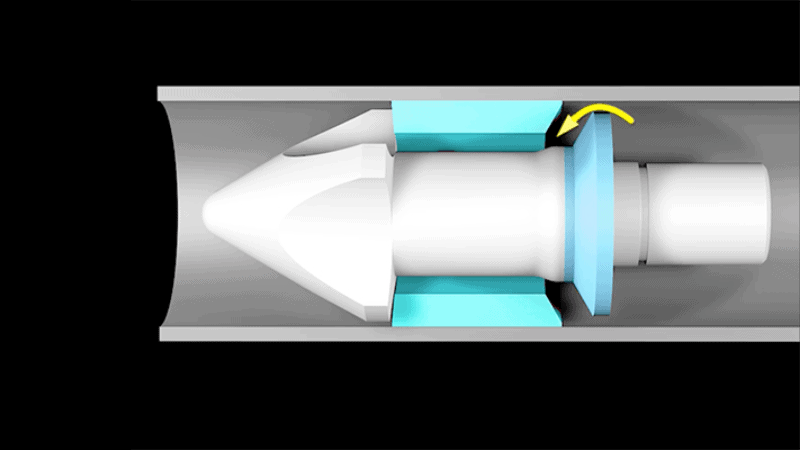
- Definition: This is the force exerted by the hydraulic system of the injection molding machine to push the molten plastic material through the nozzle into the injection mold.
- Purpose: Its primary role is to ensure the mold is filled completely.
- Implication: Properly calibrated injection pressure ensures consistent material flow rate and complete filling of mold cavities. It aids in compensating for the natural resistance encountered by the flowing plastic, especially in intricate mold designs or thinner sections. Insufficient injection pressure can cause defects like short shots, whereas excessive pressure might lead to flash.
Holding Pressure
- Definition: Once the mold is filled with molten plastic material, holding pressure is applied to pack the material into the cavity and maintain it under pressure during the cooling and solidification phase.
- Purpose: Its main purpose is to ensure the plastic fills any shrinking areas as it cools and solidifies, thereby reducing the risk of voids or sink marks.
- Implication: A well-maintained holding pressure results in high-quality parts with consistent dimensions. Incorrectly set holding pressures might not compensate for the material’s natural shrinkage, leading to deformities in the final product.
Backpressure
- Definition: This pressure is exerted against the reciprocating screw in the injection molding machine during the plasticizing phase when the screw retracts to accumulate a new shot of molten plastic.
- Purpose: It aids in ensuring proper melting and mixing of the raw material, controls the polymer flow rate, and assists in removing any entrapped air from the molten plastic.
- Implication: A controlled backpressure ensures homogeneous melting of plastic granules and reduces issues like material degradation. If too high, it can lead to excessive shear heat, potentially degrading the material. Conversely, too low of a backpressure might result in inadequate mixing and possible material variations in the final part.
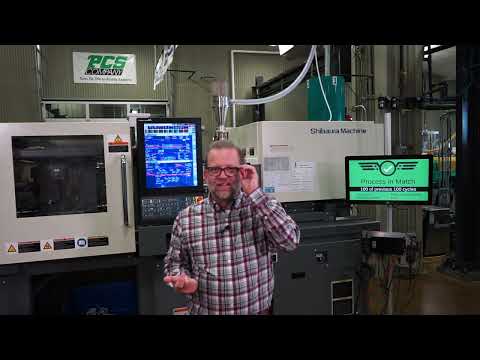
Each of these pressures holds significant importance in the molding process. They must be meticulously managed to guarantee the production of high-quality parts while minimizing potential defects. Proper calibration and understanding of these pressures can significantly elevate the quality and consistency of plastic injection molded parts.
Impact of Pressure on Plastic Injection Molded Parts
The pressure applied during the plastic injection molding process isn’t merely a matter of arbitrary force; it’s a critical variable that profoundly affects the quality, appearance, and structural integrity of the molded parts. Let’s explore the various ways in which pressure can impact plastic injection molded parts:
Part Fill and Dimensions:
- Properly calibrated injection pressure ensures that the molten plastic material fills the entire injection mold cavity, reaching even the finest and most intricate details. This ensures the final part reflects the desired dimensions and intricate details of the mold design.
- Insufficient pressure might result in incomplete filling, leading to defects such as short shots or weld lines.
- Excessive pressure can cause overpacking, potentially distorting the part’s dimensions or causing flash.
Surface Quality:
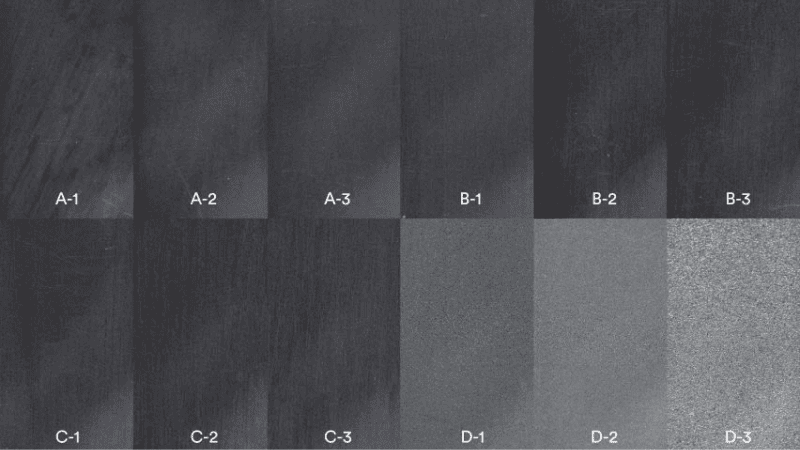
- The pressure applied, especially during the holding phase, affects the surface finish of the final part. Inadequate holding pressure can lead to sink marks on the part’s surface, particularly in thicker areas where the material shrinks upon cooling.
- Conversely, overly high injection pressures might lead to jetting, which appears as snake-like lines on the surface due to rapid material entry into the mold.
Structural Integrity:
- Consistent pressure ensures that the molten plastic flows uniformly throughout the mold, resulting in a part with even wall thickness and uniform strength.
- Varying or incorrect pressures can introduce internal stresses within the part, making it prone to warping or even cracking during its lifespan.
Material Distribution:
- Pressure plays a direct role in determining the flow rate of the molten plastic. Proper pressure ensures uniform flow and even distribution of material throughout the part.
- Issues like flow hesitation or freezing fronts can arise from lower pressures, leading to potential weak points or material buildup in specific sections.
In essence, the pressures exerted during the molding process have a direct relationship with the part quality. Optimizing and precisely controlling these pressures is an important factor in producing high-quality parts with minimal defects. Proper pressure management is pivotal in striking the balance between speed, efficiency, and quality in plastic injection molding.
Take the First Step:
Requst for an Inquire
Quality Meets Affordability. Inquire Now for High-Quality Products at Low Volumes.
Influence of Material Viscosity on Pressure
Material viscosity is a fundamental property in the plastic injection molding process. Essentially, viscosity is a measure of a material’s resistance to flow. For molten plastic materials, viscosity is influenced by factors like temperature, shear rate, and the specific polymer composition. The relationship between material viscosity and the requisite pressure in the injection molding process is both direct and multifaceted. Here’s a detailed examination of their interplay:
1. Basics of Viscosity and Pressure
Higher viscosity materials, being thicker, necessitate greater injection pressure to move the material through the injection mold and fill the cavity. Conversely, lower-viscosity materials, being more fluid-like, generally require less pressure.
2. Temperature Dependence
The viscosity of molten plastic material decreases with increasing temperature. Thus, if a material is heated beyond its ideal processing temperature, it will flow more easily, potentially reducing the need for high pressures. However, overheating can lead to material degradation and other issues.
3. Shear Thinning Nature
Many thermoplastic polymers exhibit shear thinning behavior, meaning their viscosity decreases under high shear rates. As the injection speed and pressure increase, the material experiences higher shear, reducing its effective viscosity and aiding the flow. This characteristic is beneficial, especially when molding intricate or thin-walled parts.
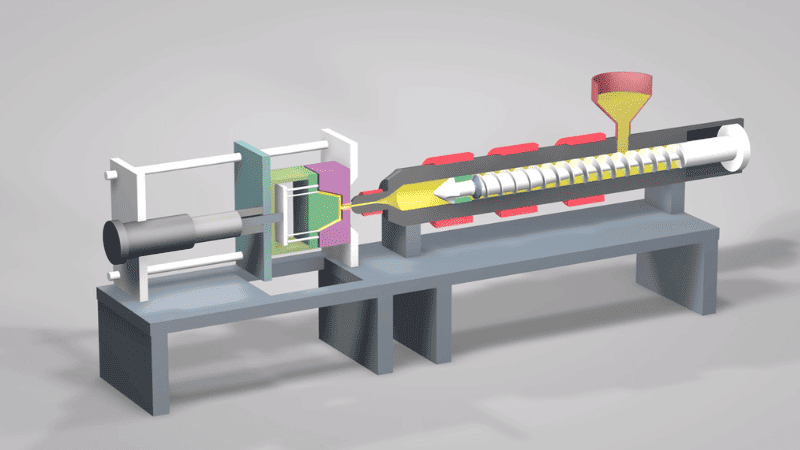
4. Material Flow Paths and Resistance
Viscous materials encounter more resistance as they travel through narrow sections, gates, and intricate features of a mold. This resistance requires compensatory increases in injection pressure to ensure complete and uniform filling.
5. Impact on Packing and Holding Pressure
The viscosity of the molten material influences not only the initial injection pressure but also the subsequent holding or pack pressure. High-viscosity materials might need higher pack pressures to compensate for material shrinkage and ensure dense, void-free parts.
Factors Affecting Injection Pressure in Injection Molding
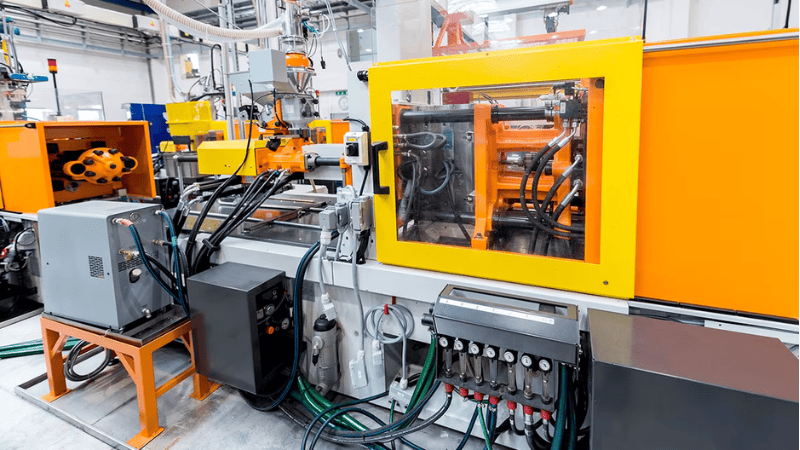
In the intricate world of plastic injection molding, the application of the correct injection pressure is pivotal for manufacturing precise and high-quality parts. Various factors influence the optimum injection pressure. Here, we delve into these determining elements:
- Material Viscosity: Different plastic materials have varying viscosities. Highly viscous materials often require a higher injection pressure to facilitate material flow through the mold channels.
- Mold Design and Complexity: The design intricacies of the injection mold, such as narrow channels, intricate features, or thin walls, can necessitate higher pressures. This ensures the molten plastic material adequately reaches all areas of the mold.
- Mold Temperature: As the mold temperature rises, most plastic materials become less viscous. Consequently, a hotter mold might require a lower injection pressure. Conversely, a colder mold may require an increase in pressure to compensate for increased material viscosity.
- Gate Size and Location: Smaller gates can resist the flow of the molten plastic, demanding a higher injection pressure. Additionally, the location of the gate can influence how easily the material fills the mold cavity.
- Molding Machine Type: The design and capability of the molding machine itself can impact the achievable injection pressures. Some machines might offer a more consistent and higher pressure range than others.
- Use of Runner Systems: Runner systems can influence the temperature and flow of the molten plastic, potentially reducing the required injection pressure compared to cold runner systems.
In conclusion, optimizing injection pressure in the plastic injection molding process is a complex task that requires considering numerous variables. Proper calibration ensures not only the production of high-quality parts but also the longevity of the molding equipment and efficiency in the manufacturing process.
Take the First Step:
Requst for an Inquire
Quality Meets Affordability. Inquire Now for High-Quality Products at Low Volumes.
Conclusion
The injection molding process is a complex dance of precision, materials, and machinery, with injection pressure standing at its core. By understanding the multifaceted interplay between different pressures, the properties of molten plastic material, and the intricacies of the mold, manufacturers can effectively optimize their processes. Achieving the right balance ensures the consistent production of high-quality parts, minimizes defects, and boosts overall efficiency.
Discover the Perfect Solution for Your Business with Hongju
Hongju stands at the forefront of plastic injection molding excellence. We harness advanced machinery and deep expertise to master injection pressure and material flow rate, ensuring peak quality in every product. Our commitment to innovation and precision minimizes common molding defects. With Hongju, quality, and reliability are molded into every piece. Choose us for unmatched manufacturing prowess.