What makes injection molding remarkable is its ability to produce numerous items efficiently and cost-effectively. It’s a scientific process that blends heat and pressure to craft practical items. After injection molding, the various molded products cool down.
Understanding the Injection Manufacturing Process
To truly appreciate the role of runner systems in injection molding, we must first grasp the foundation of this transformative manufacturing process. The injection process and molding process is not just an injection molding process or a method; it’s an engineering marvel that has reshaped industries and brought countless products into existence.
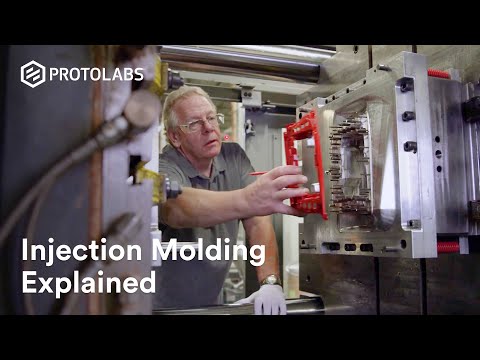
The Craft of Injection Molding Process
At its core, the injection molding process involves heat, pressure, and materials. It starts with a granular or powdered material, often in the form of plastic or rubber, which is fed into the hopper of the injection molding machine. The material is then under injection pressure and heated until it reaches a molten state, ready for its transformation.
- The Mold
The heart of injection molding is the mold cavity itself. This meticulously crafted, hollowed-out piece of steel or aluminum is no ordinary vessel; it’s the blueprint for the product to be molded and born. The mold is split into two halves, with mold cavities and even multiple mold halves with holes, being a complex system of runners, gates, and gaps that define the product’s shape.
- The Injection
As the molten material reaches the right consistency, it’s injected, under high pressure, into the mold cavity. This is where the magic happens. The material quickly fills every nook and cranny, taking on the desired shape of injection molded parts and parts within the mold cavity. It’s here that the product’s destiny is determined, whether it’s a small plastic toy, a medical device component, or an intricate automotive part.
- Cooling and Solidification
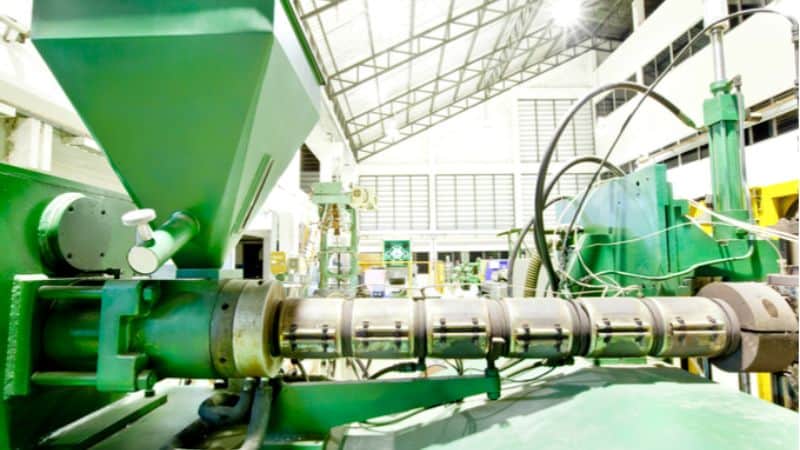
But the process doesn’t end there. The mold, now filled with hot, molten material, needs time to cool and solidify. Cooling channels, strategically embedded in the mold surface, facilitate rapid cooling during this crucial phase of mold assembly. The precise control of a mold’s cooling channels and times is a science in itself, as it influences the product’s quality and structural integrity.
- Ejection
Once the pressure on the molded product or mold’s surface has solidified, the mold’s halves are separated, and the product is ejected through ejector pins or mechanisms. This might seem simple, but it’s a carefully orchestrated act. Ejector pins ensure that the pressure on the product is released without damage.
The Versatility of Injection Molding
The true significance of injection molding technology lies in its remarkable versatility. It’s the method behind the creation of everyday items like plastic bottles, lids, and toothbrushes. But it doesn’t stop there. Injection molding technology gives life to vital components in industries such as aerospace, healthcare, and automotive manufacturing. From the smallest intricate, molded parts to large, complex structures, injection molding delivers precision and reliability.
A Vital Part of the Manufacturing Process
In essence, injection molding is not just a process; it’s an art that shapes the modern world. Its significance in manufacturing is undeniable, enabling the creation of a vast array of products that enhance our lives. Understanding this foundational process sets the stage for comprehending the crucial role that runner injection molding parts and systems play in making it all happen.
What Are Runner Systems of Injection Molding Machines?
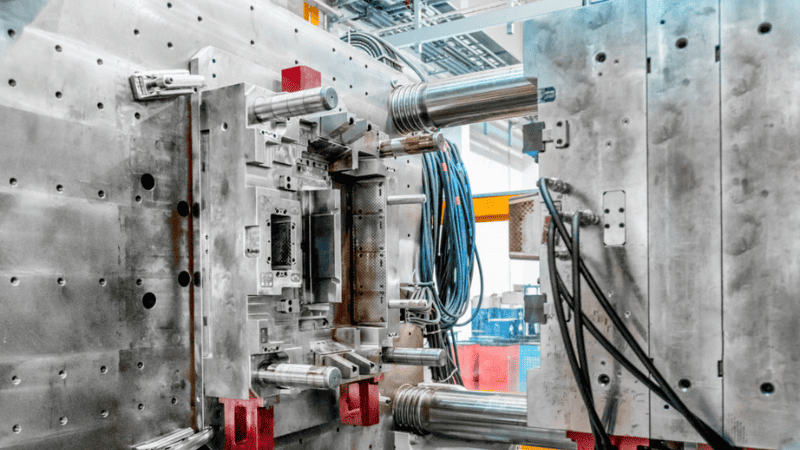
In the world of injection molding, think of runner systems as the traffic managers. They’re like the hidden heroes, making sure things run smoothly. These systems are a bunch of particular pathways, like little rivers, that help hot, gooey material get from the machine nozzle to where it needs to be inside the whole plastic injection molding part itself.
Why Are They So Important?
Without runner systems, it would be like trying to drive without roads or guide lanes. Chaos would rule, and the things we make wouldn’t turn out right. So, they’re a bit like the conductors of an orchestra, making sure all the instruments play together in harmony.
- Keeping Things Just Right
These runner systems are also like thermostat controls, making sure the temperature and flow of the gooey stuff are just right. This whole process control is super important because it helps make certain every molded part that comes out is perfect, just the molded part the way it’s supposed to be molded.
- Less Waste, More Savings
Runner systems are also eco-friendly. They make sure we use as little plastic material as possible, which is not only good for the environment but also for saving money in production.
It’s not random; designing these runner systems is like a schematic diagram or creating a blueprint. Engineers carefully plan the size, shape, and flow path of these pathways to make everything work perfectly.
Key Components of Runner Systems
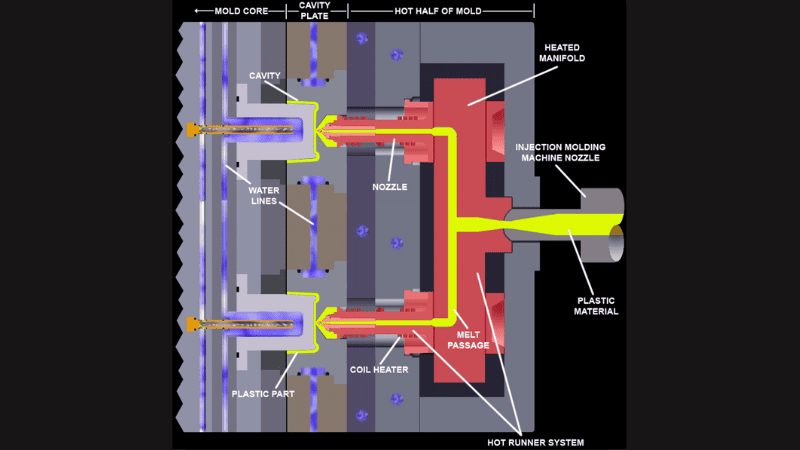
Runner systems might sound complicated, but they’re made up of some basic building blocks that work together like a well-practiced team. Let’s break down these critical components in a simple way.
- Meet the Players
Imagine a highway system for molten material. It has to be carefully designed to get things where they need to go. In our story, two main characters stand out: the sprue and gates.
- The Sprue
Please think of the sprue as the main entrance to our highway system. It’s like the grand gateway where the molten material first enters the runner system. It’s a big deal because it sets the stage for everything that follows.
- The Gates
Now, imagine the gates as checkpoints along the highway. They’re like little doors that control the flow of molten plastic material from the sprue into the plastic injection molding mold cavity. These gates have to be just right in size and shape like Goldilocks finding the perfect chair in the Three Bears’ house.
The Art of Design
But here’s the secret sauce: the design of these components is super important. It’s like having a skilled chef create a recipe. The size and shape of molded parts of the sprue and gates can make or break the flow and quality of the final product.
So, in a nutshell, runner systems are like well-organized highways, with components involved: the sprue as the main entrance and the gates as traffic cops, ensuring everything goes smoothly. Designing these components carefully is like crafting the perfect recipe for a delicious meal – it’s crucial for making top-notch products in injection molding.
Types of Runner Systems
Runner systems, like superheroes, have different versions, each with its special powers. There are two main types: hot runner systems and cold runner systems. Let’s explore what makes them unique.
Hot Runner Systems
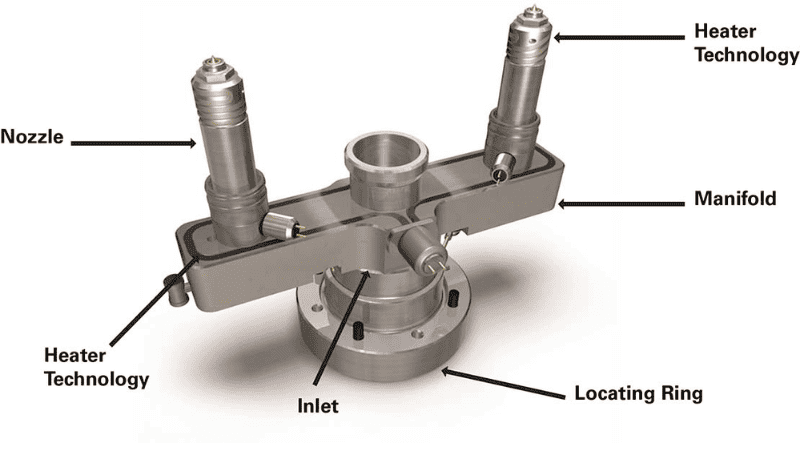
Imagine a system that keeps the already molten plastic material hot and flowing smoothly through the channels. That’s precisely what hot runner systems do. They make sure there’s a continuous flow of material, which means less waste and more production efficiency. These systems are like the champions of high-volume production and crafting complex shapes. They’re like the speedsters of the injection molding world, ensuring things keep moving.
Cold Runner Systems
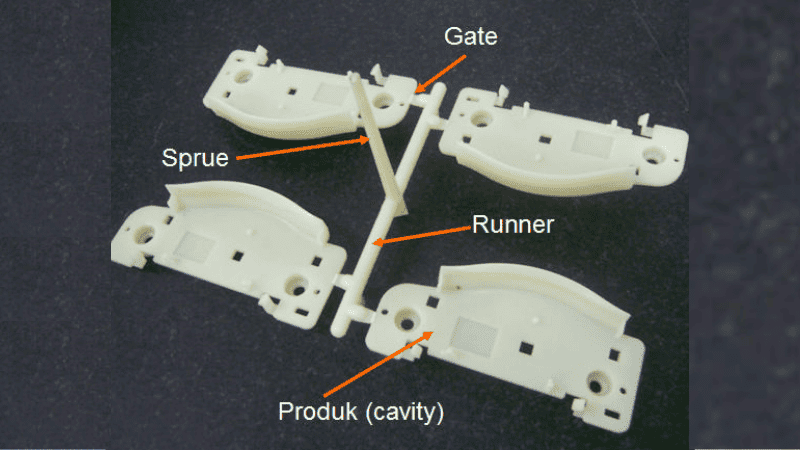
Now, picture a system that lets the molten plastic or parts of the molten material fantastic and solidify after each cycle. This cooled material is called runner and can be reused or recycled. Cold runner systems are like the budget-friendly option, especially for making medium to low quantities of products. They’re like the thrifty heroes, making the most of every bit of material.
Materials Compatibility
In the realm of injection molding, we encounter an array of materials, each with its distinct attributes. These materials encompass plastics, rubber, metal alloys, and more. They possess varying mechanical properties, too, including melting points and flow characteristics, akin to dancers with unique styles.
Hot Runners
Consider hot runner systems as the instructors who thrive in higher temperatures. They are best suited for materials that exhibit low viscosity and excellent flow properties. This partnership ensures smooth and efficient material movement, akin to a well-choreographed dance.
Cold Runners
In contrast, cold runner systems excel in their temperature sensors, maintaining a cooler atmosphere. They are the ideal choice for materials requiring extended cooling and solidification times. These materials demand a more measured approach, akin to a slower-paced dance routine.
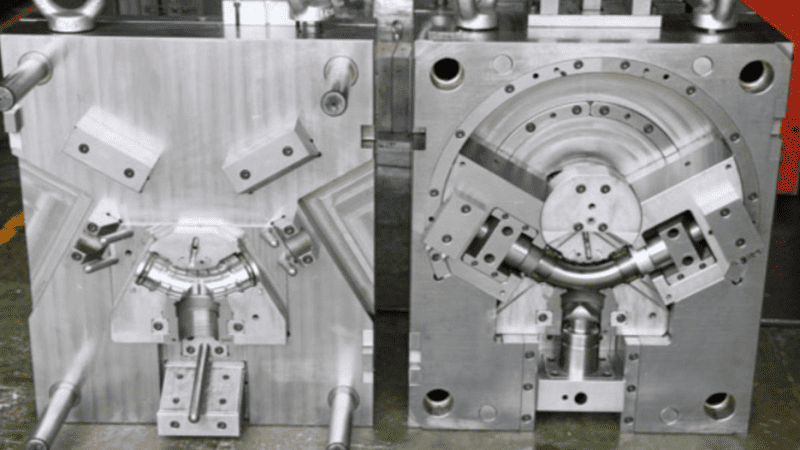
The Significance of Compatibility
The art of selecting the right runner system for a specific material lies at the heart of the injection molding process. It resembles the process of matching dance partners based on their dance style. A mismatch between the material and the runner system can result in suboptimal performance.
Advantages & Disadvantages of Each System
When it comes to injection molding, one critical decision is choosing between hot runner and cold runner systems. Each has its own set of advantages and drawbacks that can impact factors. Here’s a concise look at the pros and cons of each system.
Hot Runner Systems
Advantages
- Reduced Material Wastage: Hot runners excel in efficiency by the heat transfer, keeping the material in a molten state. This technology eliminates the need to discard cooled runners after each cycle, significantly down cycle time and reducing material wastage.
- Faster Cycle Times: The continuous flow of molten material in hot runners leads to shorter cycle times. This is particularly advantageous for high-volume production, where speed matters.
Disadvantages
- Higher Initial Costs: Hot runner systems come with a higher upfront investment. The specialized components required for heating and maintaining the material in a molten state contribute to this cost.
- Maintenance Demands: Maintaining precise temperature control in hot runner systems is crucial. This necessitates regular upkeep, which can translate into ongoing maintenance expenses.
Cold Runner Systems
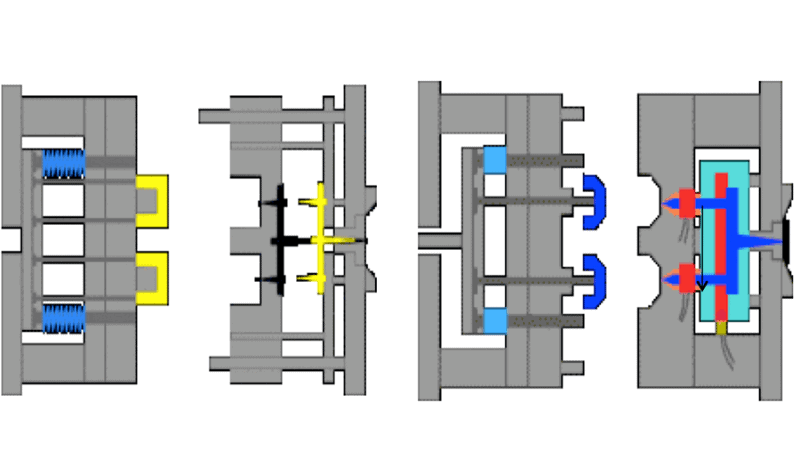
Advantages
- Cost-Effectiveness: Cold runner systems are budget-friendly. They do not require the extensive heating and insulation components of hot runners, making them a cost-effective choice.
- Simplicity: These systems are straightforward in design and operation. They are easy to set up and maintain, making them suitable for various applications.
Disadvantages
- Increased Material Wastage: Cold runner systems generate solidified plastic material, known as runners, after each cycle. These runners are typically discarded or recycled, leading to higher material wastage compared to hot runners.
- Longer Cycle Times: The cooling and solidification process in cold runners can extend cycle times, which may not be suitable for high-speed production scenarios.
Factors Influencing the Choice of Runner System
When it comes to choosing the ideal runner system for your injection molding endeavor, several crucial factors come into play. These factors are akin to puzzle pieces, each contributing to the complete picture of the decision-making process. Let’s delve into these influential elements.
Material Properties
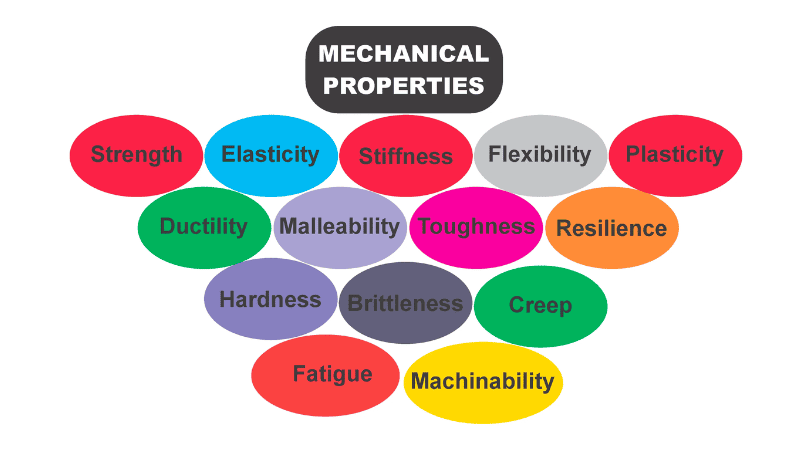
Imagine the material you’re working with as the foundation of your project. Materials have unique characteristics, such as their melting points, flow behaviors, and costs. These properties can greatly affect the choice of the runner system.
- Melting Point: Some materials melt at lower temperatures, while others require higher heat. This guides you towards either hot or cold runner systems, depending on compatibility mold temperature.
- Flow Behavior: Materials differ in how rapidly and easily they flow when molten. This impacts the efficiency of various parameters of material distribution, directing you toward a runner system that suits the material’s flow characteristics.
Complexity of Part Design
Think of the design of your product as a complex puzzle. Some parts are straightforward, while others are intricate and delicate. The complexity of your part design plays a pivotal role in the runner system choice.
- Complex Parts: Intricate surface designs often benefit from hot runner systems, which provide precise control over material flow. This is like having a skilled artist use a fine brush for intricate details.
- Simple Parts: For straightforward designs, cold runner systems might suffice. They offer simplicity and cost-effectiveness, akin to using a basic tool for a straightforward task.
Production Volume
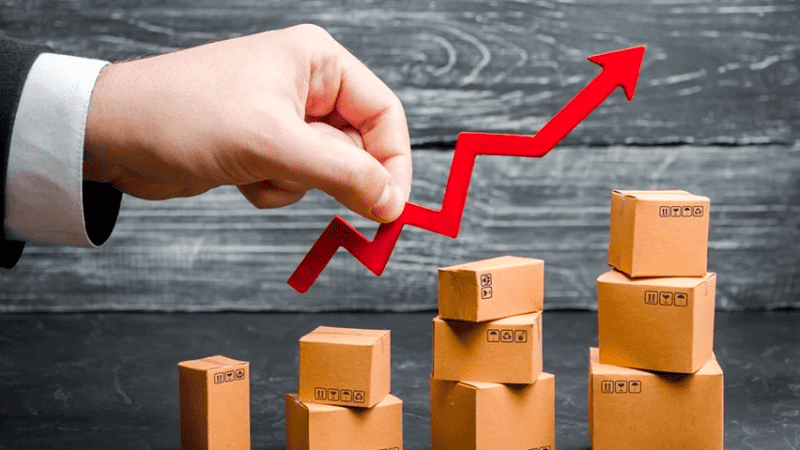
Production volume is like the heartbeat of your project. It determines the pace of injection speed and scale of your manufacturing process.
- High Volume: In scenarios where you need to produce a large number of parts quickly, hot runner systems shine. Their efficiency and reduced cycle times are akin to a well-oiled machine for high-speed mass production.
- Low to Medium Volume: Cold runner systems are more budget-friendly for lower production volumes. While they might result in longer cycle times, they can be cost-effective for smaller-scale operations.
Budget Constraints
Picture your budget as the frame that holds your project together. It sets the boundaries and determines how you allocate resources.
- Generous Budget: If your budget allows for higher initial investment and ongoing maintenance costs, hot runner systems might be a feasible choice, given their efficiency benefits.
- Tight Budget: Cold runner systems are budget-friendly, making them a suitable option when financial constraints are a primary consideration.
Operational Considerations of Each System
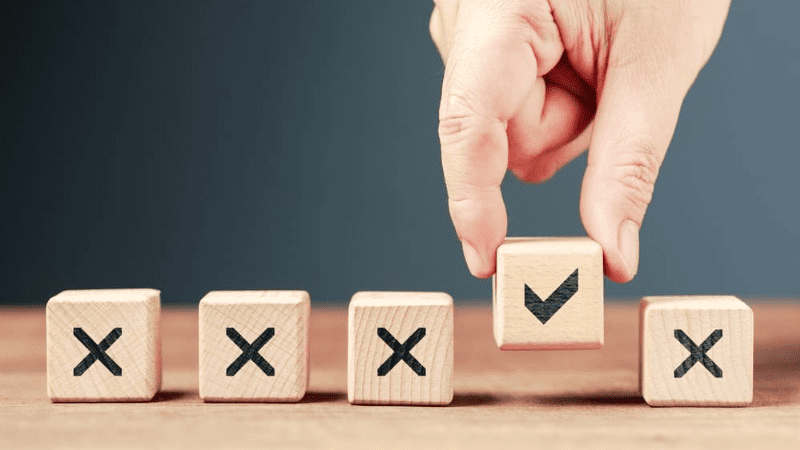
Let’s explore the operational aspects of both hot and cold runner systems, focusing on the critical factors that ensure efficiency and success.
Hot Runner Systems
Operating hot runner systems requires meticulous attention to detail and precision. Think of it as piloting a high-performance sports car; you need to keep everything finely tuned.
- Regular Maintenance: Just like a sports car needs routine maintenance, hot runners demand regular upkeep. This includes checking and maintaining heaters and nozzles to ensure they function at their best. Any malfunction here can disrupt the flow of molten material.
- Precise Temperature Control: Temperature control is the heartbeat of hot runner systems. Maintaining precise temperatures throughout the system is crucial for consistent product quality. Think of it as tuning a musical instrument; even a slight deviation can result in a discordant note
- Adequate Insulation: Proper insulation is like providing a warm coat to protect against the cold. It ensures that the heat generated in the hot runner cooling system itself is contained, reducing energy consumption and promoting efficiency.
Cold Runner Systems
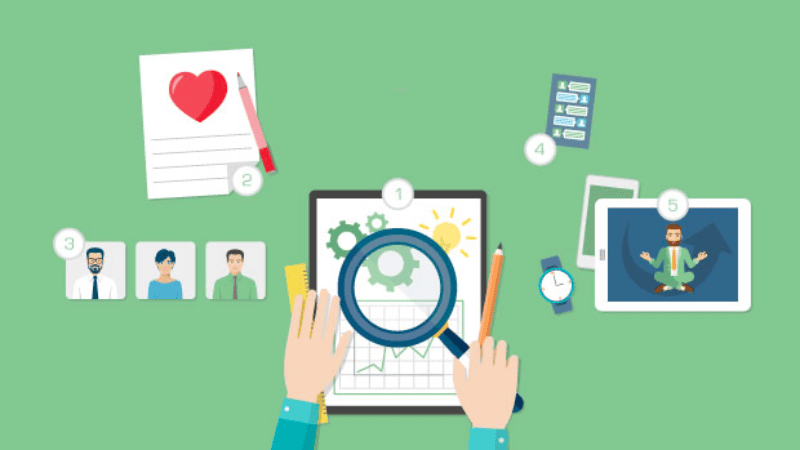
Operating cold runner systems involves a different set of considerations, emphasizing simplicity and efficiency.
- Optimizing Runner Design: The design of the runner channels is critical for minimizing material wastage. Imagine it as designing a plumbing system where you want to ensure minimal water loss. Well-designed runners reduce waste and keep costs in check.
- Managing Cooling Times: Cold runner systems require patience. It would be best if you managed the cooling times effectively to ensure that the material solidifies as desired. This is akin to patiently waiting for a cake to cool before adding frosting.
- Implementing Recycling Practices: Sustainability is essential in modern manufacturing. Implementing recycling practices for the solidified material (runners) can reduce waste and promote eco-friendliness. It’s like recycling glass, plastic products, or paper to reduce environmental impact.
Conclusion
As we conclude our journey through the world of runner systems in injection molding, it’s essential to emphasize their indispensable role in achieving quality, efficiency, and cost-effectiveness in the manufacturing process. Whether you opt for the precision of hot runner systems or the cost-efficiency of cold runner systems, understanding their intricacies is the key to unlocking success in the injection molding process.
Discover the Perfect Solution for Your Business with Hongju!
As a trailblazer in innovative technologies and services, Hongju offers tailor-made solutions designed to streamline operations, boost productivity, and drive growth. Whether you’re a budding startup or a well-established enterprise, explore our offerings and get in touch today.
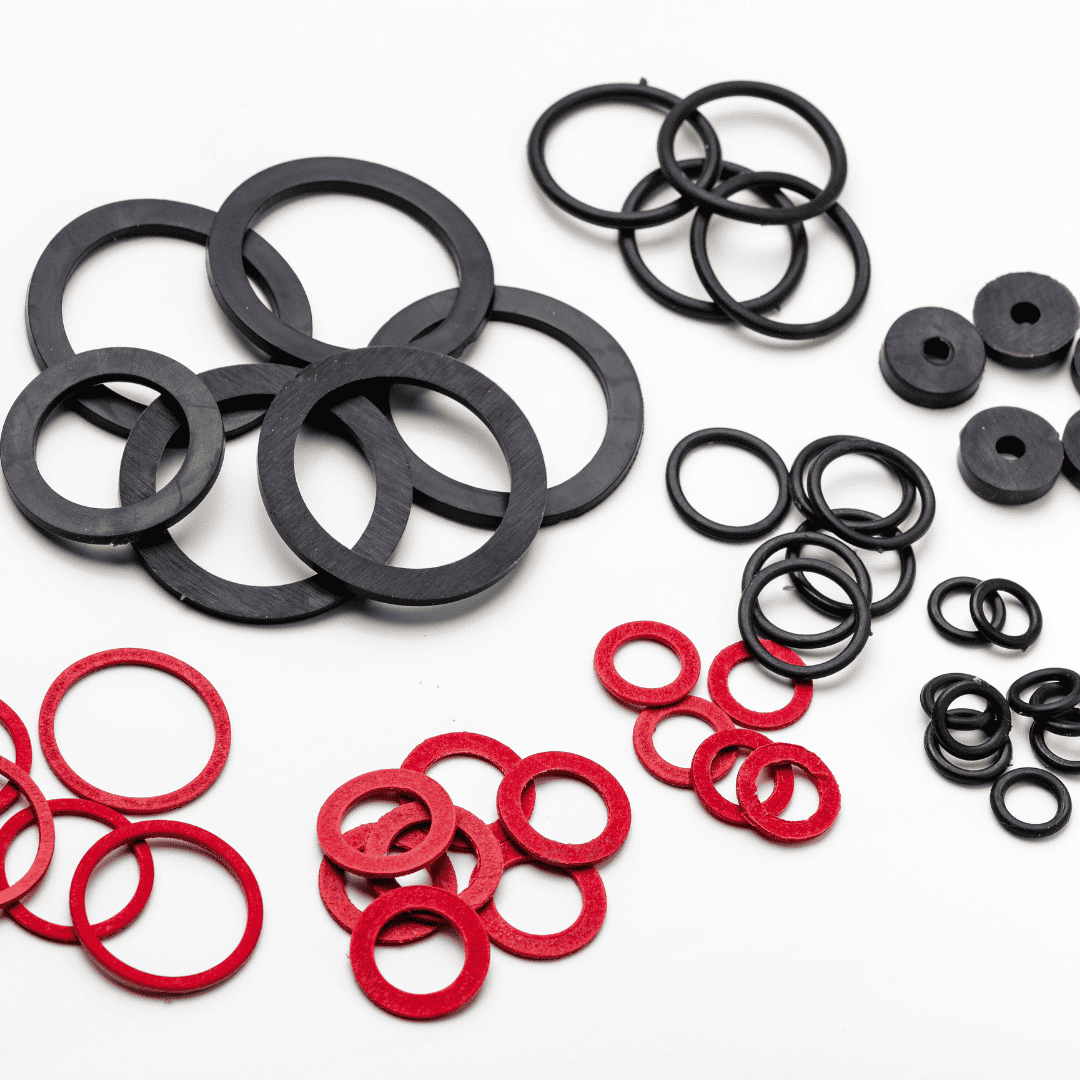
Send Your Inquiry Now!
Quality Meets Affordability. Inquire Now for High-Quality Products at Low Volumes.