It lets you begin with the most common plastic injection molding technique and then delve into the latest micro-injection molding method with narrow dimensional tolerances. You will be able to understand 7 different types of injection molding, their main advantages, common material, and real-world applications.
So, are you ready to unwrap a guide that is your ticket to get a complete understanding of injection molding? If yes, then let’s start unraveling the method behind the molding machine and groundbreaking products below:
Thermoplastic Injection molding
It is a reversible injection molding process during which thermoplastic materials are turned into a liquid state and then injected into a mold cavity in an injection molding machine. When melted plastic material is inside the mold cavity in the injection molding process machine, the material cools down so that it takes the desired shape.
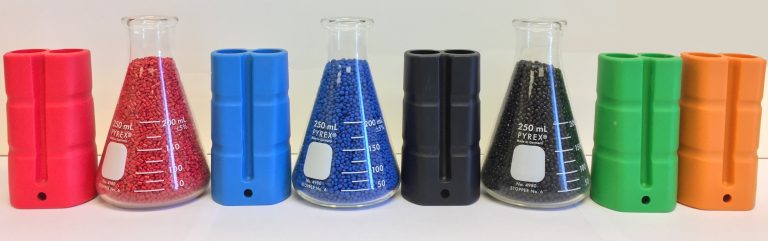
This popular plastic injection molding process is highly used to create fully functional parts. This method is used to create anything that requires top-level surface finish and accuracy. It offers high tolerance and accuracy for molded parts.
When you compare it with other plastic manufacturing processes, you realize it is a cost-effective and efficient molding technology due to its high production output rate. This fast processing method is helpful in manufacturing plastic parts, which are identical.
Thermoplastic injection molding is used to create a wide variety of consumer products such as toys, electronic casings, and storage containers. It has good use in automotive components such as bumpers, dashboard parts, and interior trim.
When you look into the medical industry, you find out that the thermoplastic injection molding technique has a good use in this industry as well. It is employed to create different medical devices and equipment such as IV components, syringes, and surgical tools. These components are highly bio-compatible and are quite easy to sterilize.
The most common use of thermoplastic resin can be seen in packaging industries, where this technique is helpful in producing lightweight and recyclable food containers, bottles, and caps.
Since this procedure produces molded parts with high chemical resistance, it is quite useful in manufacturing construction materials such as pipes and fittings.
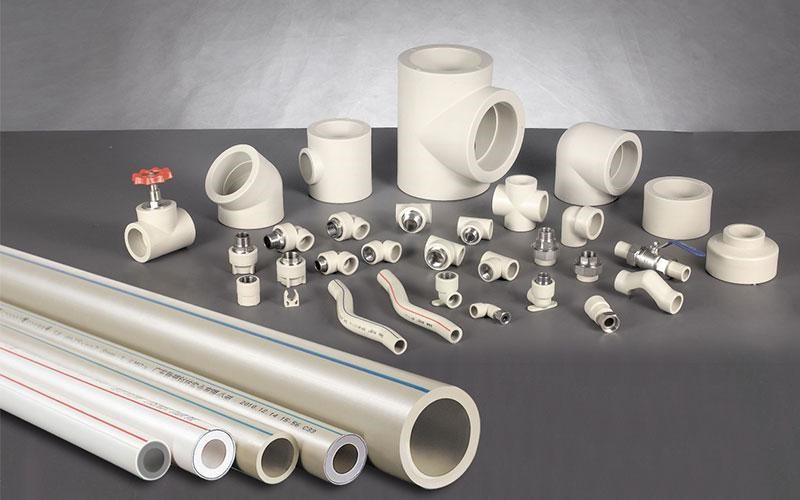
Both thermoset and thermoplastic injection molding offer unique advantages and are chosen based on the material properties and application needs. Thermosets offer heat resistance and chemical stability, while thermoplastics provide versatility and recyclability.
Advantages
Let’s explore 5 benefits you can get from thermoplastic injection molding:
- Precision and Consistency: When your project involves the creation of complex and intricate parts at high volumes, accuracy, and consistency levels, you can achieve desirable results with the thermoplastic injection molding method. Since it makes it easy to achieve tight tolerance and high-quality finish. That means you can produce identical molded parts with exact specifications in every batch of production.
- Cost Savings: Every industry wants to achieve the goal of cost-effectiveness. And thankfully, you can go with mass production with this plastic injection molding technique. It allows you to produce large quantities quickly. Its initial tooling cost is offset quickly with high-volume production and then you get low per unit cost.
- Wide Material Selection: You can select a wide variety of materials with this technique. It allows you to pick a material as per your application specification. Whether you are looking for flexibility, strength, or too much shear heat resistance properties, everything such property is covered well with this technique.
- Customization: You can get it with this method when you need top-notch injection molding design flexibility. It lets you integrate different features into molded parts during the molding process. There won’t be any need to go with a secondary operation when the first operation can do it all. During the injection mold and design process, designers can incorporate textures, threads, and inserts into the thin wall injection molding part. In other words, it’s easy to produce complex designs with thermoplastic injection molding
- Reduced Material Waste: Everyone tries his best to reduce waste during the manufacturing process. Fortunately, the thermoplastic method helps you achieve sustainability goals. If there is any excess material after the molding is done, then this material can be reused and recycled to reduce overall environmental impact.
Material Selection
Here’s a list of commonly used thermoplastic materials for plastic injection molding:
- Polystyrene (PS)
- Polyvinyl chloride (PVC)
- Polyvinylidene fluoride
- Nylon Polyethylene (PE)
- Polypropylene (PP)
- Polyethylene terephthalate
- Polyurethane (PU)
- Acrylonitrile-butadiene-styrene (ABS)
- Polycarbonate (PC)
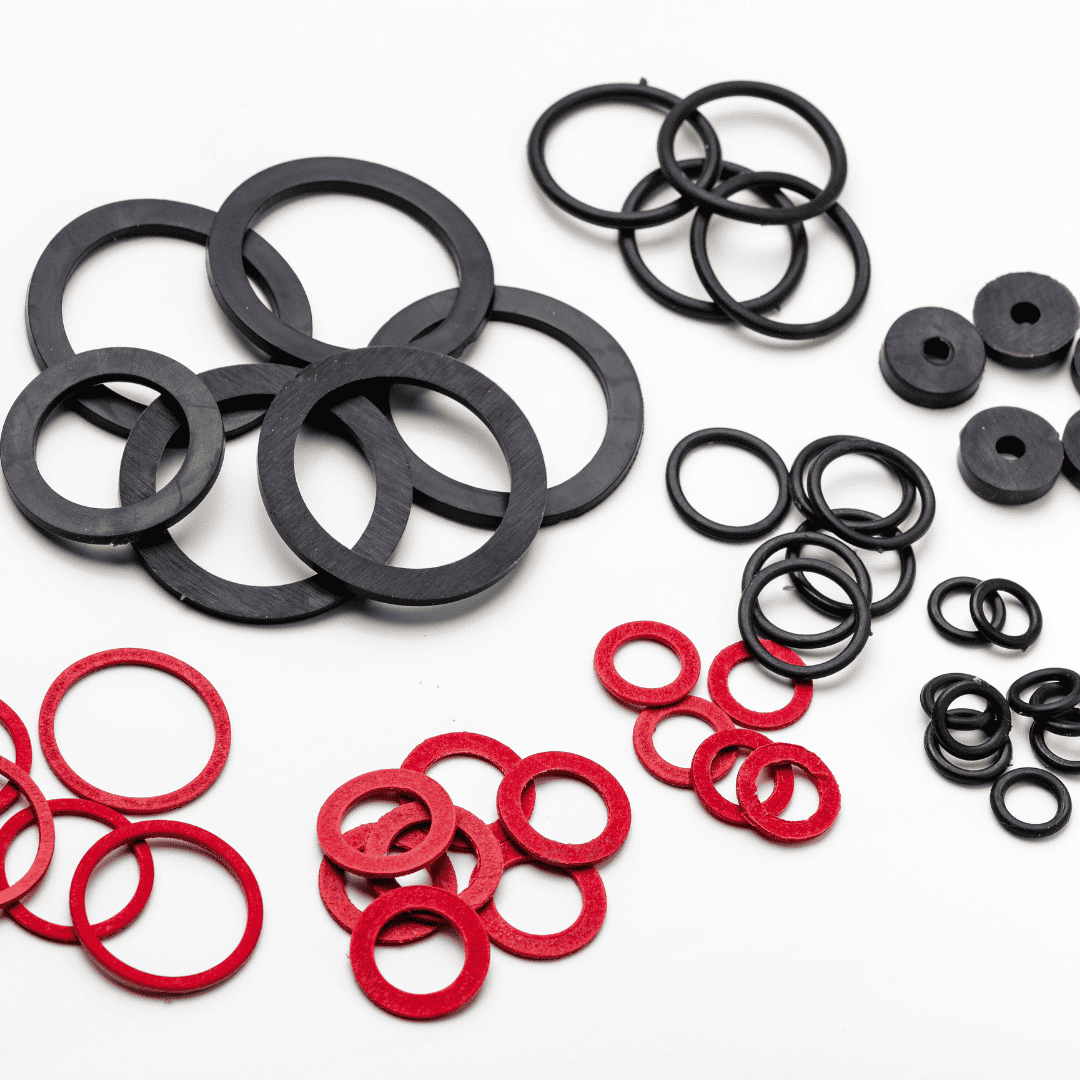
Send Your Inquiry Now!
Quality Meets Affordability. Inquire Now for High-Quality Products at Low Volumes.
Thermoset injection molding
It is an irreversible manufacturing process during which cold material is injected into a hot mold of an injection molding machine to create a final part. This injection cooling process also cures the part that can never be melted again.
This process is commonly used to create parts that can withstand high temperatures. The best example is medical parts. For example, dental tools with metal parts must withstand the claving process and sanitization, so they can be used over and over again.
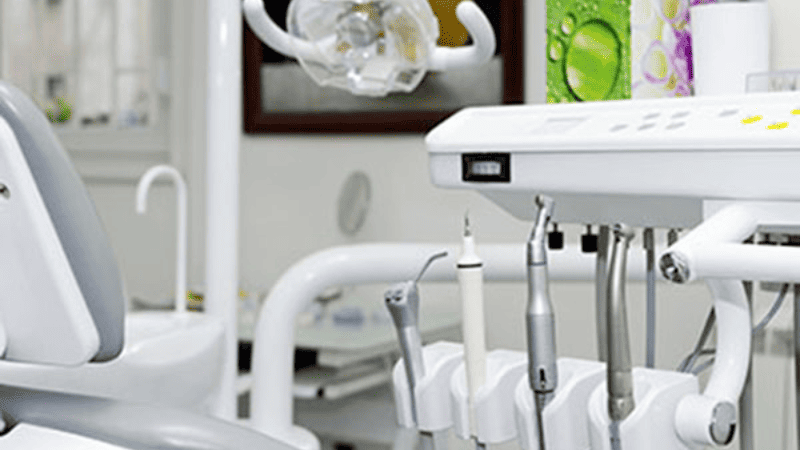
Thermoset materials are stronger than thermoplastic materials. Parts made of thermoplastic injection molding can be melted, but thermoset parts can’t be re-melted.
This technique of plastic injection molding is quite suitable for those industries that require strong and durable plastic parts. Since thermoset material undergoes a chemical reaction to create a strong bond, thermoset molded parts are highly resistant to chemicals, electrical conductivity, and temperature.
Thermoset materials are used for manufacturing connectors, housing, and electrical insulators. The best example of this technique in the automotive industry is the creation of brake parts, distributor caps, and ignition components.
The best example of this technique is found in our kitchen where you can see cookware handles and knobs. Thermoset plastics are used to produce heat-resistant handles and knobs, which don’t melt or deform if temperatures go high.
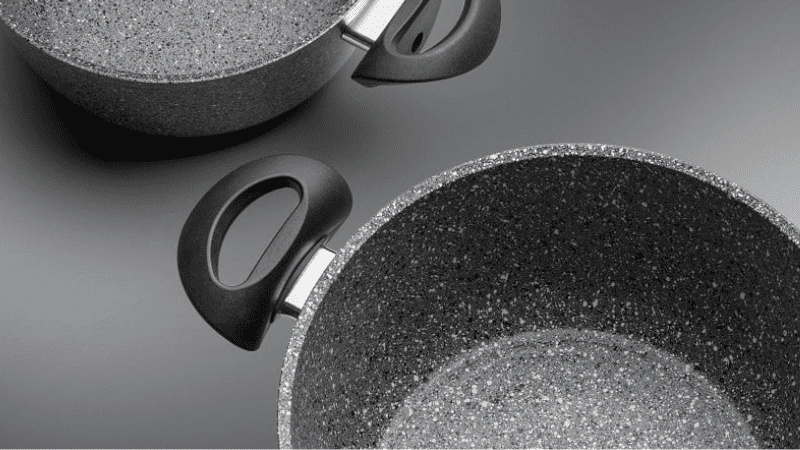
This technique is also applied in the Aerospace industry where thermoset materials are used to produce engine parts and electrical connectors. These components are highly durable and show great resistance against temperature.
Advantages
Here are the key benefits of employing thermoset injection molding :
- Withstand Heat: The best thing about thermoset molded parts is that they won’t soften or deform regardless of how high a temperature level is. They are quite ideal for an object that needs to be used in extreme heat conditions such as electrical insulators, under-the-hood automotive parts, etc.
- High Chemical Resistance: Another plus of thermoset molded parts is they can withstand a wide range of chemicals. Therefore, they are quite suitable for application in industries where chemical exposure is constant. For example, when you need to create parts for chemical processing like oil and gas, thermoset parts seem like a good option.
- Precision: There are certain industries where you must have to create parts with top-notch dimensional stability. The best example is electrical connectors, which are usually created with this method.
- Electrical Insulation: Thermoset molded parts usually remain electrically non-conductive. So, they are designed to work under extreme conditions.
- Strength: Thermoset injection molding parts can withstand mechanical stress and loadbearing. These specifications make them the most suitable structural components.
Material Selection
Here is a list of commonly used materials for thermoset injection molding:
- BMC (Bulk Molding Compound)
- Phenolic Resin
- Epoxy Resin
- DAP (Diallyl Phthalate )
- Silicone Resin
- SMC (Sheet Molding Compound)
- Polyester Resin
- Urea Formaldehyde Resin
- Bakelite
- Melamine Formaldehyde Resin
- Epoxy Phenolic Resin
Liquid Silicone Rubber (LSR) injection molding
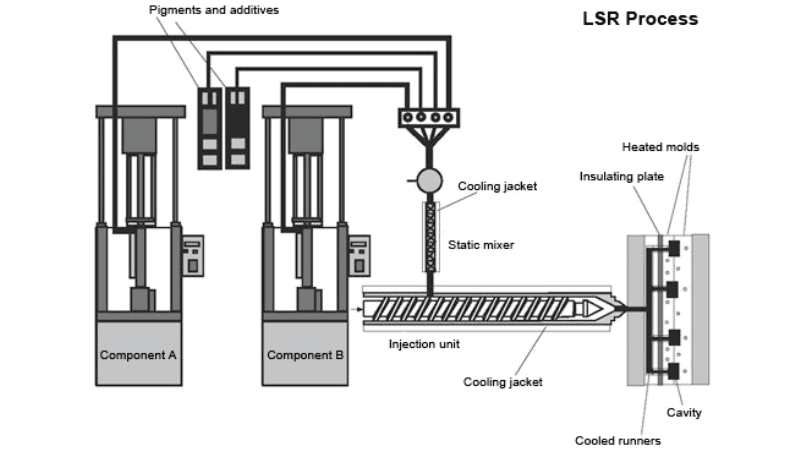
The producers of rubber-based products make the most of LSR Injection molding because this technique allows them to enjoy a high level of automation and almost 24/7 production run.
During (LSR) injection molding method, a two-part platinum-cured silicon compound is mixed and injected into the mold in the injection molding machine. Once this material is inside the mold, it cures into a flexible and solid rubber part.
The liquid Injection mold technique has revolutionized rubber industries because this method allows producers to create versatile products while maintaining a high level of precision. They can create highly detailed and intricate rubber components via this method.
The common application of LSR injection molding is in medical industries. This technique is quite effective in the creation of medical-grade silicone parts such as tubes, seals, and gaskets.
Since silicone rubber is quite safe and durable, this technique is effective in manufacturing baby bottle nipples and pacifiers.
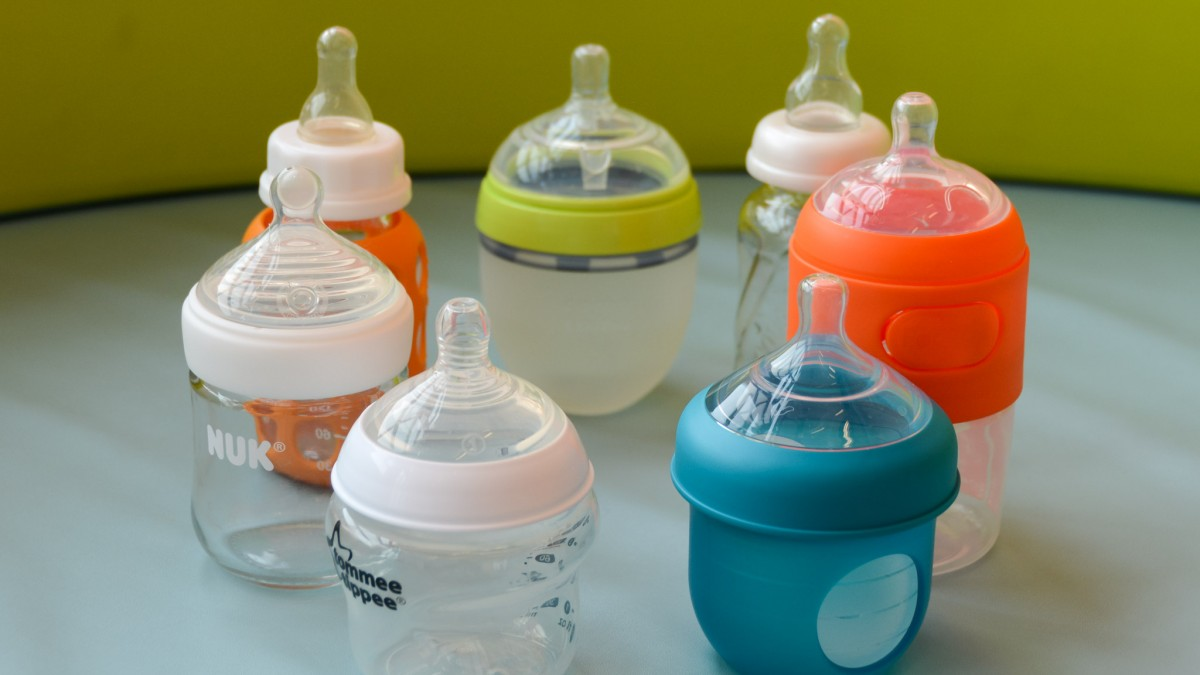
The role of LSR injection molding is big in the automotive Industry. This plastic injection molding method is used to produce automotive gaskets and seals. These components are highly resistant to shear heat burning and chemicals.
Advantages
Here are some benefits that you can only achieve with Rubber injection molding:
- Fast Production: The biggest advantage manufacturers can achieve with this technique is quick production. It is made possible with the short cycle of this process. It is cured after the cooling process and then you get the molded part more quickly with LSR as compared to other traditional methods.
- Biocompatibility: The LSR injection mold process is biocompatible. Thereby manufacturers can produce medical and health care products through this method. This technique is safe for the production of medical devices, components, and implants that come in contact with the human body.
- High Precision: Industries where products must have high precision and accuracy can make the most of this technique. It helps them produce highly detailed parts with tight tolerances.
- Withstand Temperature: The injection molded parts from this technique can withstand high levels of temperature from too cold to too hot. That means the part won’t lose its physical properties regardless of how extreme the temperature will be. So, you can use this technique for applications in extreme temperature conditions.
- Flexible and Durable: The injection Molded parts from LSR injection molding are highly durable and flexible. So, they are quite an ideal choice for applications that need to level performance and resilience such as gaskets and seals.
Material Selection
Here is some commonly used material for this molding process.
- General-Purpose LSR (GP-LSR)
- Fluorosilicone LSR (F-LSR)
- Transparent LSR
- LSR for Electronics
- LSR for Seals and Gaskets
- High-Temperature LSR (HTV-LSR)
- Medical-Grade LSR
- Electrically Conductive LSR
- Self-Lubricating LSR
- Food-Grade LSR
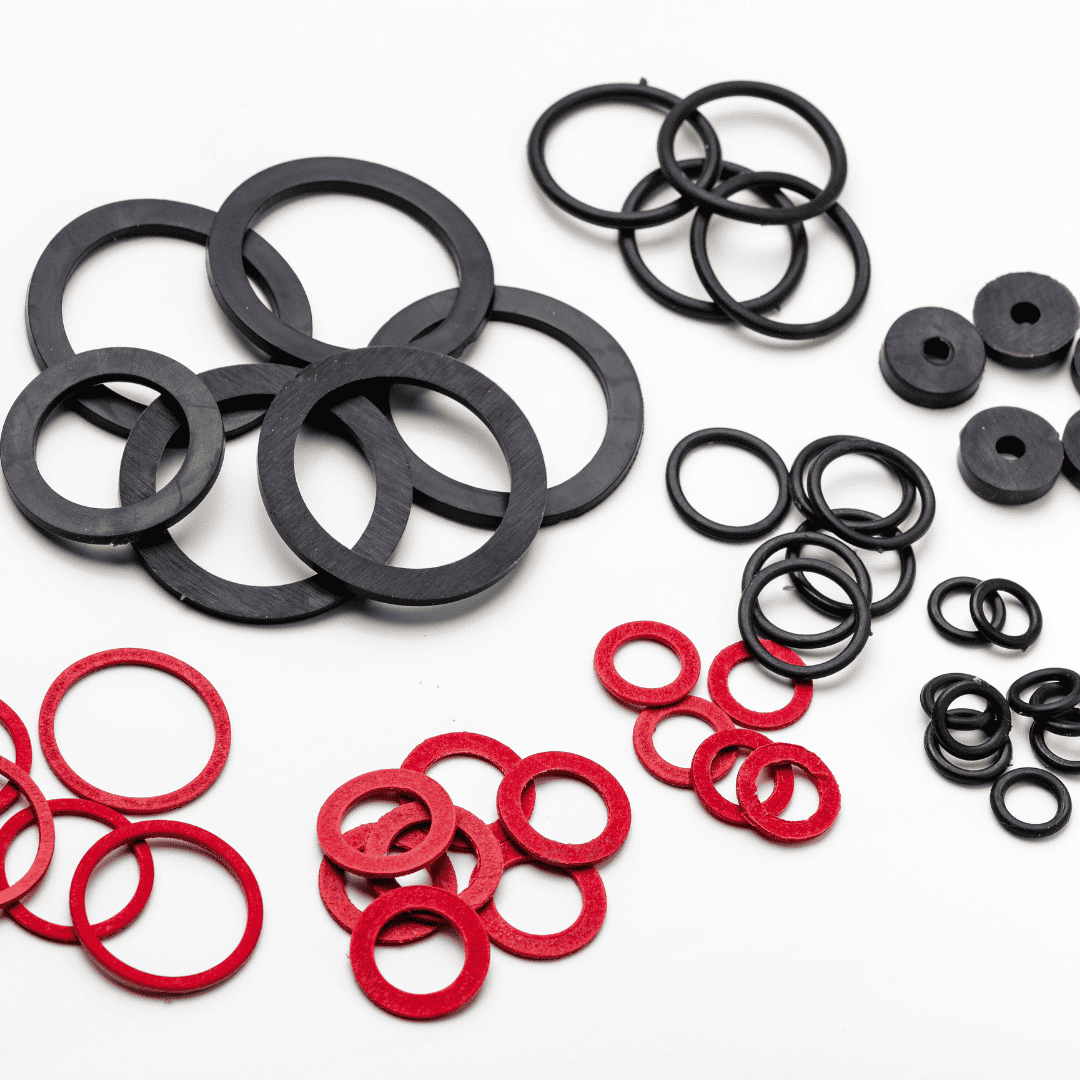
Send Your Inquiry Now!
Quality Meets Affordability. Inquire Now for High-Quality Products at Low Volumes.
Micro Injection Molding
This process is widely used for the production of incredibly small and complex plastic parts with as much accuracy and precision as possible. This technique takes miniaturization to the next level because it allows manufacturers to produce plastic with a weight of around 1 to 0.1 grams with tolerance levels of 1 to 100 microns
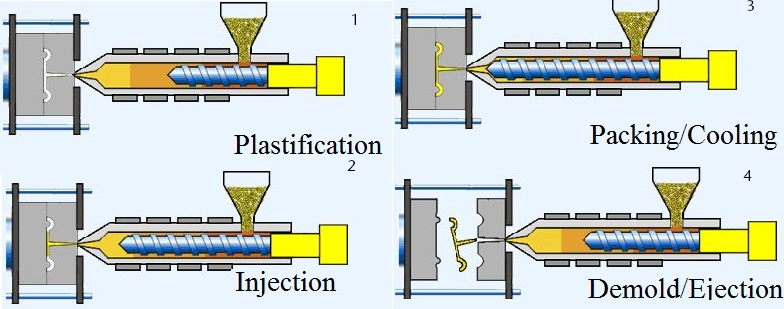
As far as applications of micro injection molding are concerned, you will be surprised to know this technique is widely used for the production of parts and components in the automotive, electronics, medical, and pharmaceutical industries.
The best example of micro-injected molded parts is tiny gear created for delicate watches or microfluidic devices for advanced medical diagnostics.
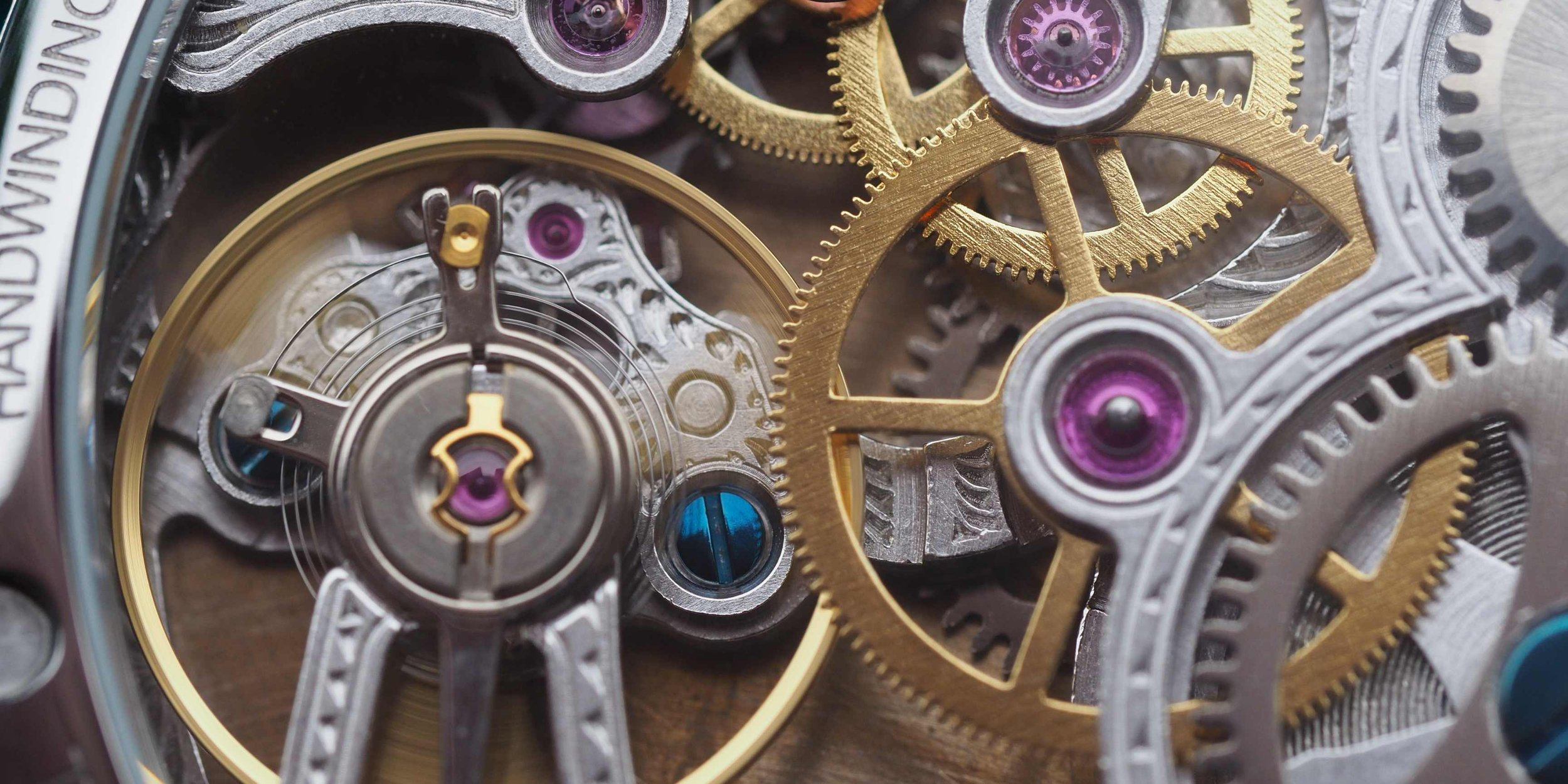
Manufacturers can expect outstanding precision with micron-level tolerances through this technique. This method is quite suitable for low-volume manufacturing and prototyping. When it comes to material choice, you can have diverse options from thermoplastic to bioresorbable polymers.
Advantages
Here are 5 main advantages of Micro injection molding
- Complex Geometrics: This versatile technique offers endless injection molding design possibilities to manufacturers. It allows you to create miniature marvels so basically it combines innovation with accuracy in various industries. It is a go-to solution for creating tinies yet intricate parts with unparalleled precision. So, when you want to create tiny parts with complex geometry, this technique is the best one you can pick.
- Precision: Industries such as medical devices and microelectronics where precision is a must in micro-objects can make the most of the microplastic injection molding process.
- Sustainability: This process produces less waste and thereby reduces environmental impact by utilizing molten plastic. You can achieve the goal of sustainable manufacturing through it.
- Consistency: There are many industries where you always need to create consistent parts repeatedly and if you deviate from the main shape or size, it’s a big problem. The micro injection molding process is certainly the best technique for such industries because it offers exceptional consistency without causing any impact on product performance. The product will pass a quality control test.
- Wide Material Option: Engineers can select the most suitable material for their application while using this technique. It’s because this method works for diverse materials.
Material Selection
Here is a list of materials commonly used for micro-injection molding:
- Bioresorbable Polymers
- Micro-Metal Alloys
- Thermoplastic
- High-Performance Engineering Plastics
Multi-component injection molding
Do you want to create eye-catching multi-colored or multi-material plastic components? What could be a better option than multi-component injection molding? It is also known as the multi-material molding (MMM) technique, during which two or more resins are injected to form a multi-material part.
This process combines different colors and materials to create high-quality plastic parts through molten plastic. The best example of MMM is a colorful and super soft smartphone case, which offers a comfortable grip. Since you can combine various materials and colors into one product, it allows you to create aesthetically pleasing functional products.
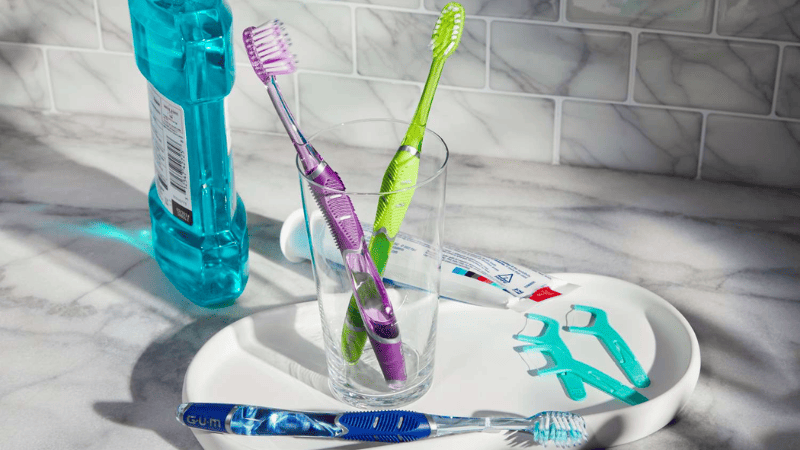
When it comes to its application in consumer products the best example is toothbrushes with rubber grips. It is an ideal technique for the creation of electronic enclosures, especially the ones that are usually integrated with gaskets.
Multi-component injection molding has great use in the medical industry. It allows manufacturers to create medical-grade equipment with different materials. It’s easy to combine material with varied flexibility, strength, and biocompatibility.
Advantages
Here are 5 advantages you can avail yourself with the Multi-component injection Molding technique.
- Cost Savings: This process allows molders to create a product in one go. There is no need for additional processing that reduces cycle time and material waste. You can produce products quickly and without wasting material.
- High-Quality Parts: Just like other injection molding techniques, multi-component processes also deliver high-quality parts with utmost precision and accuracy. It ensures that every component is positioned and bonded precisely. So, you can expect the production process of well-structured parts through it.
- Creative Design: Since it allows you to play with diverse colors textures and plastic materials, it facilitates you to create innovative designs with utmost flexibility. You are free to combine soft and hard plastic into one visually appealing product.
- Eco-Friendly: There is no need to have a secondary assembly step, so it reduces material waste. This eco-friendly manufacturing process reduces environmental impact.
- Manufacturing Efficiency: This process allows you to create a strong and reliable bond between multiple materials and components. This molding happens in a single operation. There won’t be any secondary step, as a result, cycle time is reduced and you can achieve high volumes and manufacturing efficiency.
Material Selection
Here is some common plastic material used for Multi-Component Injection Molding:
- Liquid Silicone Rubber (LSR)
- Thermoplastic Polyurethane (TPU)
- Polyolefins
- Polyesters
- Polyvinyl Chloride (PVC)
- Thermoplastics
- Thermoplastic Elastomers (TPE)
- Engineering Plastics
- Styrenic Polymers
- Acrylics
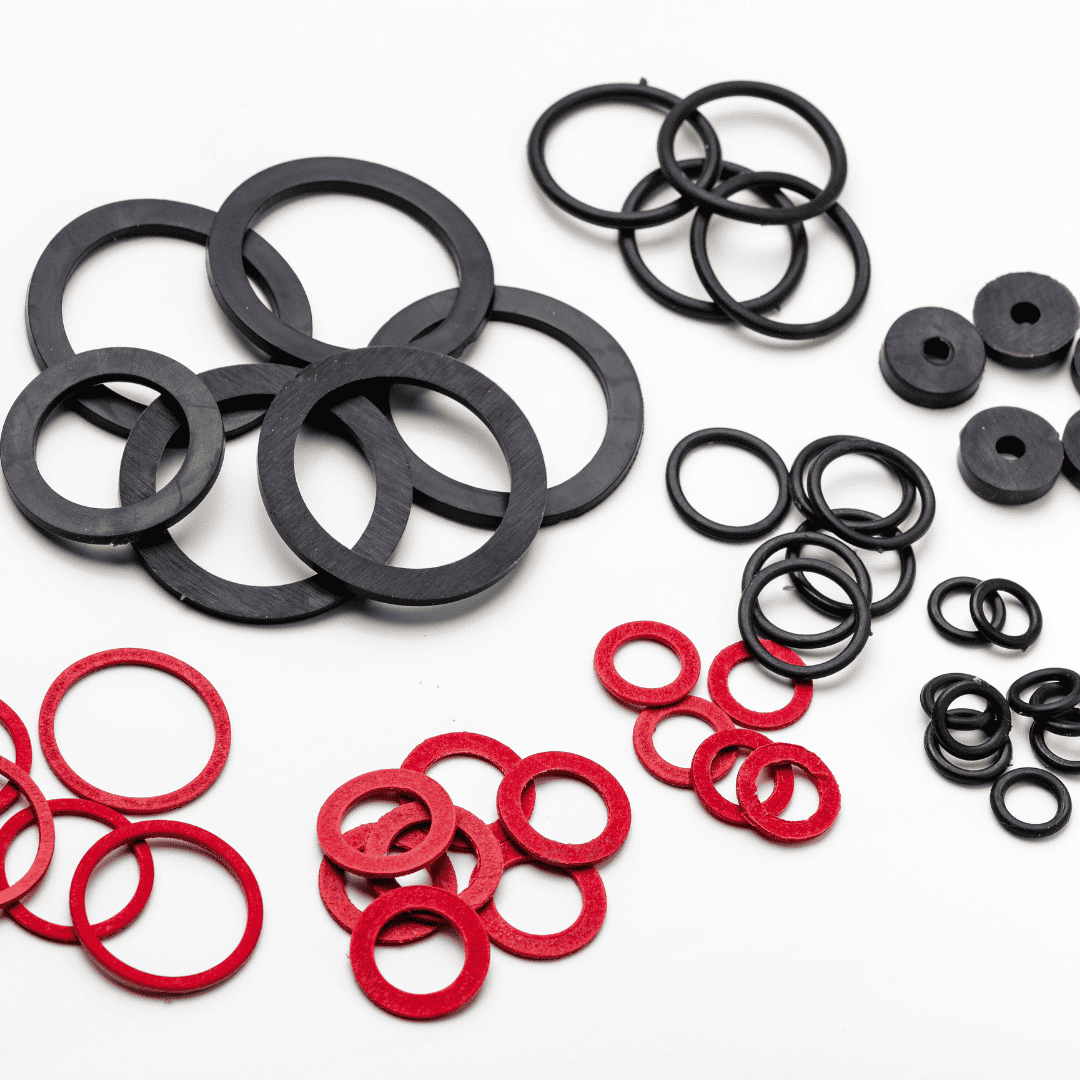
Send Your Inquiry Now!
Quality Meets Affordability. Inquire Now for High-Quality Products at Low Volumes.
Two-shot Injection Molding
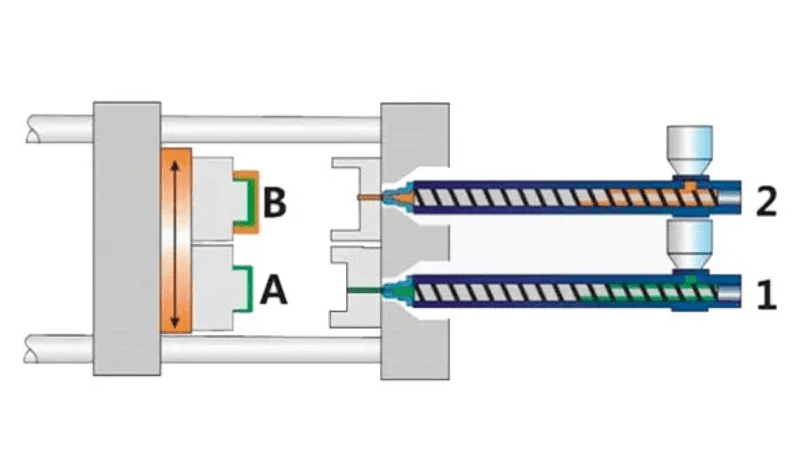
It is another common type of injection molding technique in which two different materials or colors are combined into a single process. When you want to create a two-in-one tool with multiple functions then you should opt for this process. It allows manufacturers to produce components with striking contrasts.
During two-shot injection molding, two different molten plastic materials with contrasting colors and properties are fused together to create a single part. This technique is quite effective in creating multi-functional parts in one piece.
The best example of this technique is in the automotive industry where manufacturers create dual-material dashboards. As far as its use in medical devices is concerned, it is effective in making syringe plungers; which usually requires a combination of rigid and flexible material in a single product.
Advantages
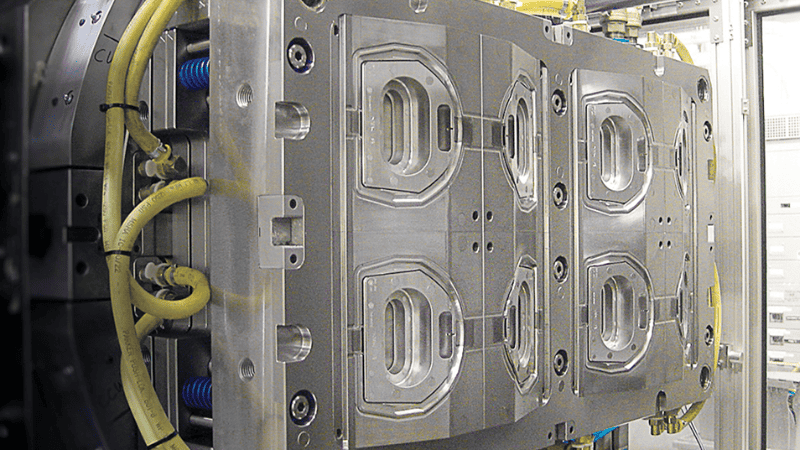
Here are five main advantages you can get from Two-Shot injection molding:
- Time and Cost Savings: There is no need for a secondary process when you can create an amazing product with only one step. There is no secondary assembly process that reduces material waste and your cost. You save time by producing a dual-shot product in one step.
- Innovative Design: You can integrate different materials, textures, and colors into one product. Therefore, creating a product that is highly functional and aesthetically pleasing is not a goal. Designers are free to use their creative skills to make some really amazing designs.
- High-Quality Parts: You can produce high-quality parts through this technique. It lets you combine soft and hard plastic in one product, thus creating a highly useful item. Manufacturers can bond complex materials through this process. With dual-shot, you can craft a visually appealing product with dual texture, color, or material.
- Efficient Production: You can achieve manufacturing efficiency via dual-shot injection molding. The production cycle time is reduced because there is no need to run a secondary assembly process.
- Reduced Environmental Impact: By minimizing material waste and eliminating the need for additional assembly steps, two-shot injection molding aligns with sustainable manufacturing practices, promoting eco-friendliness in production processes.
Material Selection
Here are some common materials used in the two-shot injection molding process.
- Thermoplastics
- Thermoplastic Elastomers (TPE)
- Liquid Silicone Rubber (LSR)
- Thermoplastic Polyurethane (TPU)
- Engineering Plastics
- Polyolefins
- Styrenic Polymers
- Acrylics
- Polyesters
- Overmolded Metals
Insert Molding
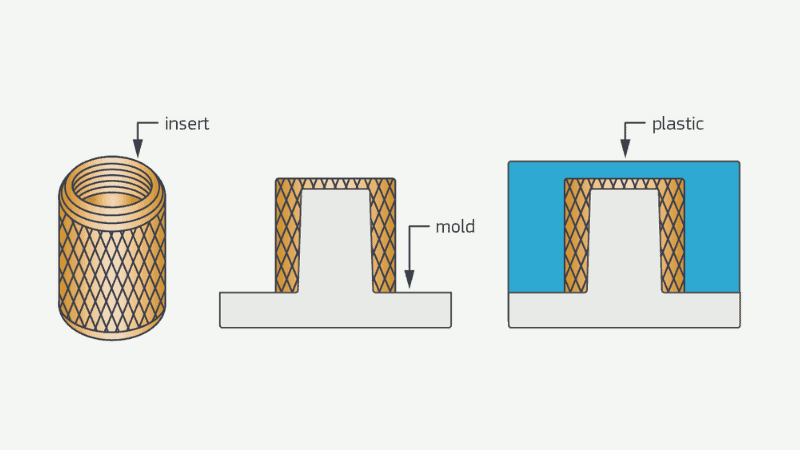
It is another technique of injection molding during which an insert is introduced in the process. This technique is useful in combining metal or non-metal inserts with plastic material.
This process is quite similar to traditional injection molding but with an additional step where an insert is added to a mold filled with melted plastic.
You always use a screwdriver that has a plastic handle. Well, it is the best example of a product created through insert molding, which is a process of making plastic components around other non-plastic parts or inserts.
The best example of this technique is catheters. In this medical device, soft tips are usually molded onto rigid bodies. Another good use of this technique is metal pins and connectors within plastic housing.
Advantages
Here are the main advantages you can get from this process.
- Complex Design: When your project involves complex assemblies into a single molded part, you can make the most of insert injection molding. It allows you to enhance overall design and create a product with precision.
- Versatile Applications: It is quite an innovative technique. Thereby, it has diverse applications in various industries such as consumer goods, medical devices, automotive, and electronics. Normally, when a project requires a nice combination of precision and durability, this technique seems like a great deal.
- Strong Bond: This method creates a secure and durable bond between the plastic and non-plastic parts. So, when an industry requires durable products then this technique is quite useful for them.
- Design freedom: It allows designers to combine plastic with other materials such as ceramics, metals, etc. This unique combination unlocks endless design possibilities for aesthetics and functionality.
- Reduces Size and Weight: It is an effective technique for creating lightweight small components. There is no need to use connectors and fasters to create a bond because metal inserts and resins make a strong bond during molding.
Material Selection
Here’s a list of commonly used materials for this molding process:
- Thermoplastics
- Thermosetting Plastics
- Metals (e.g., steel, brass, aluminum)
- Ceramics
- Glass
- Electronics Components (e.g., PCBs)
- Rubber and Elastomers
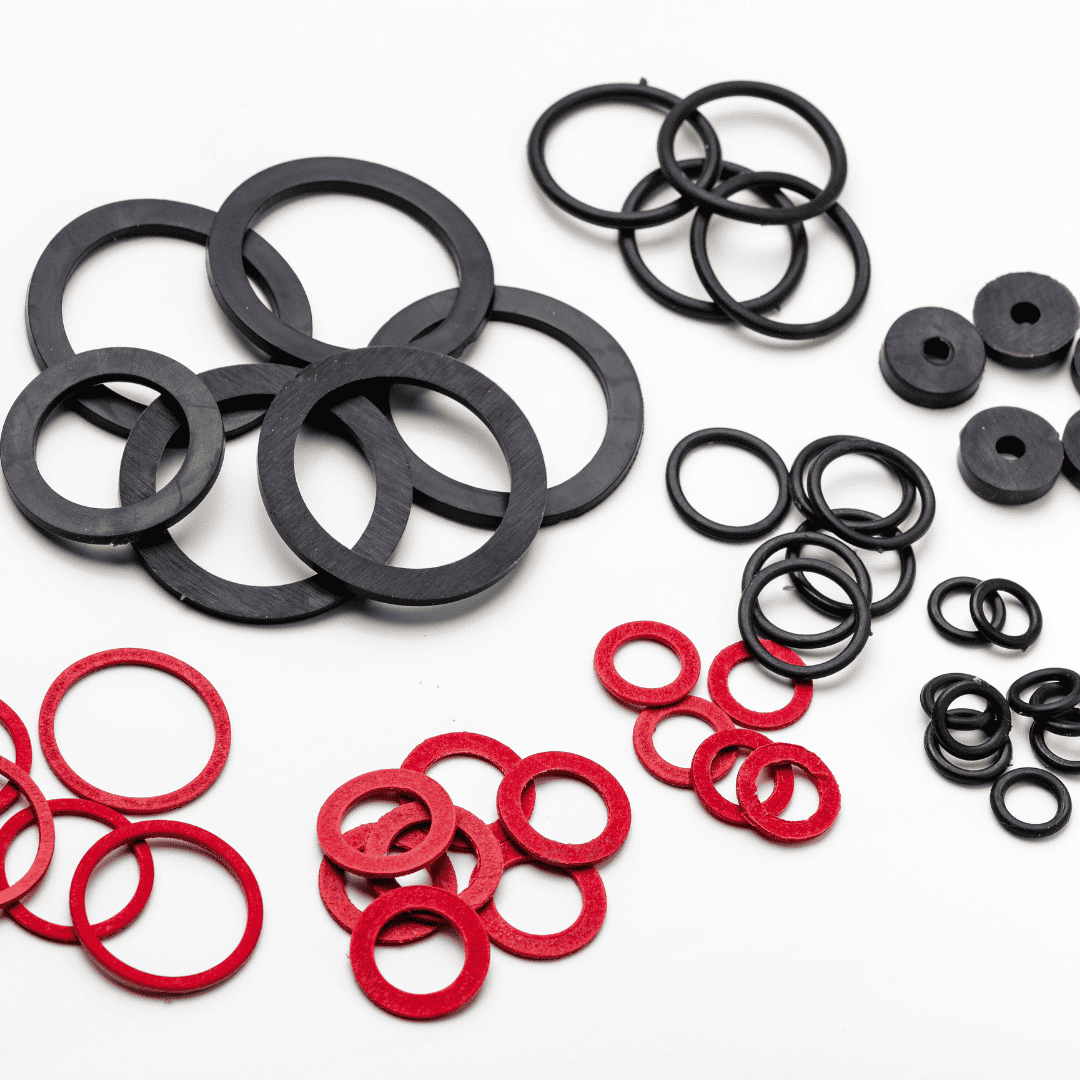
Send Your Inquiry Now!
Quality Meets Affordability. Inquire Now for High-Quality Products at Low Volumes.
Conclusion
Finally, you have explored five key types of injection molding techniques. Every technique is unique and has some benefits that are hard to achieve otherwise. Micro-injection molding is useful for creating miniature marvels where multi-component and two-shot injection molding makes it easy for you to create aesthetically pleasing products. Liquid Silicone Rubber (LSR) Injection Molding has revolutionized the rubber industry by creating the versatile design of rubber products, which are otherwise challenging to make.
No matter what technique you go for, it has shaped the products that enhance our daily lives, these injection molding techniques are the ultimate building blocks of the modern world.
Whether you are a professional designer, molder, or manufacturer, this guide has offered you every bit of detail about 7 key techniques of injection molding. You will be convinced that these techniques offer endless design possibilities.
Why Hire Experts in Injection Molding Techniques at Hongju?
Hongju has experts in injection molding techniques. We are well-versed in the art and science of every technique. With years of experience, knowledge, and insight, we are capable of guiding you through the journey of exploring and employing these key types of injection molding. If you want to make your business successful with any of these techniques of injection molding, you need experts at your side.
Click this link to connect with experts who are ready to go above and beyond to assist you in your injection molding project. Don’t miss this opportunity to gain experience and knowledge for the ultimate growth of your business.