Today, I’m going to tell you what are injection molding tolerances, the factors impacting tolerances, and the best process control to achieve tight tolerance in injection molding. From design and material selection to process control and quality assurance, everything is explained below. So, continue reading and uncover every aspect.
What Are Injection Molding Tolerances?
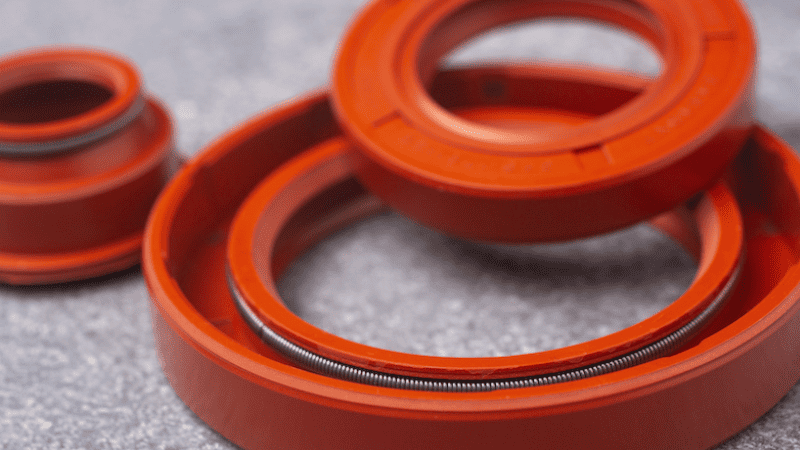
Injection molding tolerances refer to the acceptable limits within which the dimensions of a molded part can change while keeping its functionality and fit intact.
Typical toleration in injection molding ranges from ±0.1 mm to ±0.5 mm for general-purpose materials like ABS or polyethylene. But this tolerance can be looser or tighter based on the part specification and material.
Tolerances are quite important in the injection molding process because minor deviations can lead to functional issues, assembly problems or cosmetic defects. For example, if two parts are designed to fit together, but one part has an inaccurate hole, then it will cause assembly errors.
It is quite challenging to maintain a very tight tolerance as various factors affect tolerance.
Importance of Tolerance in Injection Molding Parts

Tolerance in injecting molding is quite an important element because it has a direct impact on the fit, function and overall quality of a product. Manufacturers give importance to tolerance during the process for to following reasons.
- Quality: Tolerance is a measure of quality. Parts produced based on specified tolerance are regarded as of high quality.
- Consistency across Batches: Product designers define consistency for a product to achieve consistency throughout different production runs. As a result, parts produced today will fit parts that are produced a month or year after.
- Functional Requirement: Performance requirements of some compliments depend on precise dimensions. Tolerance makes sure that all performance requirements are met properly.
- Perfect Fit: Many parts usually have to fit together with other components. Now if a part is too loose or too tight, it will adversely affect overall assembly. Process.
- Reduce Waste: The purpose of defining the acceptable range of variation for parts reduce waste. Because when parts will fit together properly they won’t be rejected. On the other hand, when parts don’t meet tolerance requirements, they will be rejected. As a result, the manufacturer needs to produce them again, and it will increase the associated cost.
Factors Affecting Injection Molding Tolerances
During the injection molding process, many variables can influence the tolerance. It’s vital for manufacturers and designers to understand all the factors. The following are the factors that affect injection molding Tolerances:
Material Properties
Every material has specific properties that can impact the acceptable level of variation in a part. Let’s find out what these properties are:
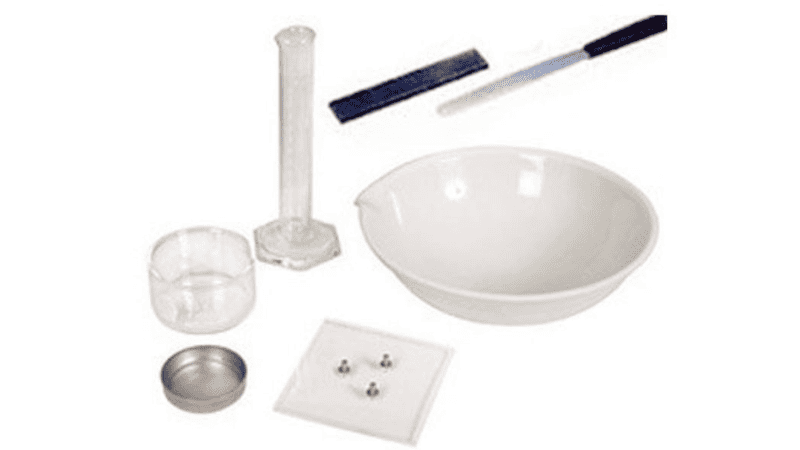
- Material Shrinkage: Shrinkage rates vary from one material to another. This rate changes the final Dimensions of the part.
- Thermal Stability: Different materials respond differently to thermal fluctuations. If a material is more vulnerable to temperature change then it causes more variability in part dimensions
- Viscosity: The material viscosity affects how well the material fills the mold. So, this material flow characteristic can impact the dimensional stability of parts.
Mold Design
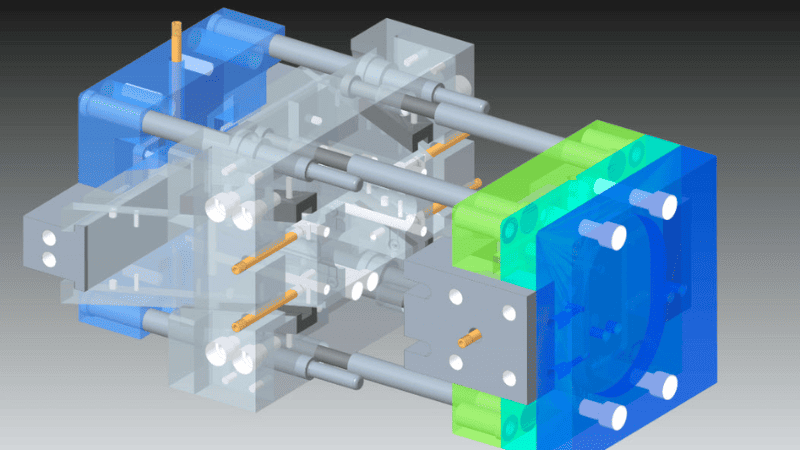
Another factor influencing injection molding is the mold design.
- Complexity: A complex mold with tight toleration is more challenging to make than a simple mold design.
- Tooling Material thing changing the standard injection molding tolerances is the type and quality of material used for mold manufacturing.
- Draft Angle: It is an angle at which a part is ejected. Draft angle is quite an important part of injection molding design because it impacts the easy removal of the part from its mold. It is vital to define right draft angles to minimize wear and tear.
Machine Parameters
Machine parameters also make or break the dimensions of a mold. Here are some parameters to consider.
- Injection Speed and Pressure: The manufacturer has to control the speed and pressure of injection because it can cause a deep impact on the final dimension.
- Cycle Time: How long a material is left to cool can change the shrinkage rates and overall dimensions of the part. Pay attention to the cooling process time.
- Clamping Pressure: When clamping pressure is incorrect, it will lead to uneven material distribution. As a result, you won’t be able to create mold as per the precise injection molding tolerance level.
Process Optimization Control
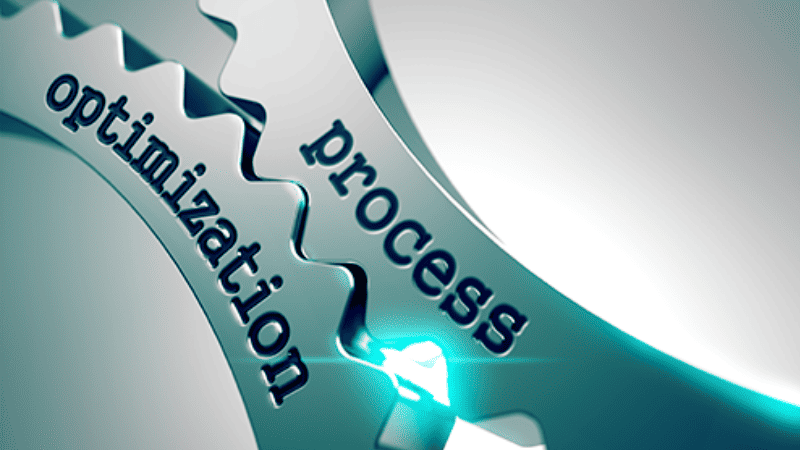
How you control the overall injecting modeling process also impacts tolerance. Here are some important factors to keep in mind during processing.
- When material and mold temperature are Inconsistent, then you will get parts with varied sizes.
- It is important to keep full tabs on the moisture level during processing because high moisture content often causes dimension instability and warping
- When your raw material is impure, it will introduce inconsistencies in size and shape.
Selecting the Ideal Material for Tight Tolerances
Do you want to maintain tighter tolerance? If yes, then you need to select an ideal material. Here is how you can do that:
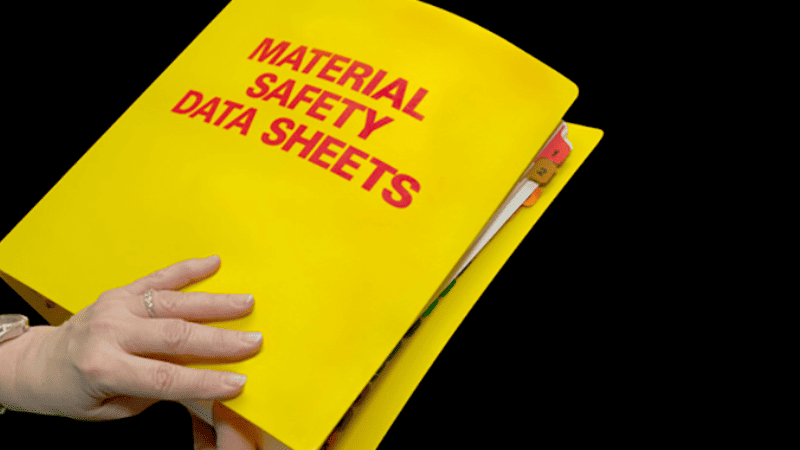
When you are looking for an ideal material, ensure that it has the following properties:
Choose a material with a low and consistent shrinkage rate. Thereby, you can control the final dimensions easily.
- Pick a material that remains stable at different temperature levels.
- Opt for a material that has high tensile strength and rigidity because it makes the process of maintaining shape and dimension less challenging for you.
- Always study material data sheets to get a clear picture of its shrinkage rate, thermal stability, and mechanical properties.
Processing Conditions and Their Impact
Here is how temperature, pressure, and cycle time have a big impact on the tolerances of injection-molded parts:
Temperature
Variations in mold and melt temperature impact the dimensions of the part. For example, when a material is too hot or too cold, it won’t fill the mold uniformly. What will be the impact then? Well, it will lead to inconsistent warping, filling, and dimensional instability.
Mold temperature affects how quality material cools down. When mold temperature is high, it will reduce internal stress but it may increase cycle chance. As a result, the chances of material warping increase to a great extent.
Pressure
Pressure is an important factor in overall mold processing. You need to be careful about holding and injecting pressure to get some ideal results.
- When injection pressure is too much, extra material will spill out of the mold. On the flip side, very little pressure results in incomplete mold filling.
- Manufacturer needs to maintain adequate holding pressure as well because
- Inadequate holding pressure adversely impacts dimensional accuracy.
Time
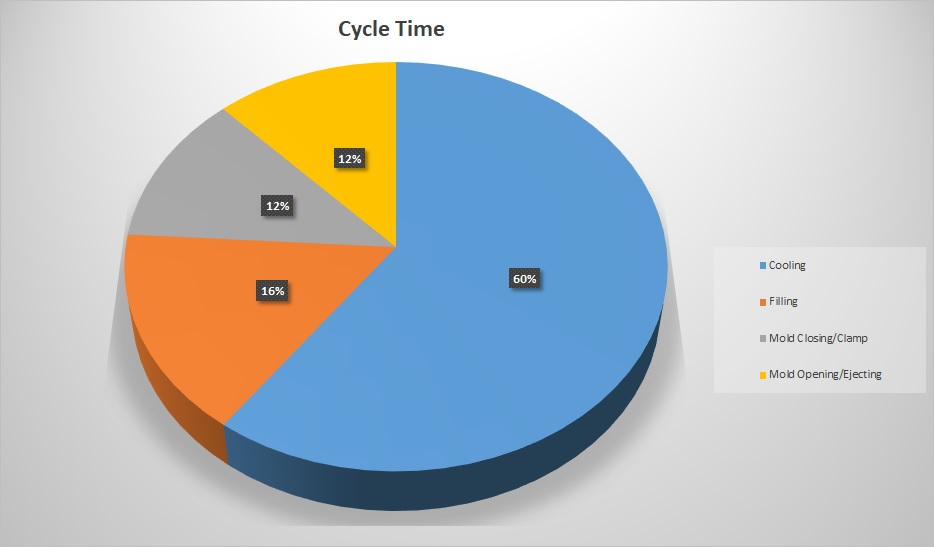
You need to adjust the appropriate time for filling, cooling, and ejection.
- Filling Time: It refers to the speed at which the mold is filled. Faster filling causes a void while slow filling leads to premature cooling. So, it’s important to pick the right filling time.
- Cooling Time: It is the length of time the material is allowed to cool in the mold. Excessive cooling boosts your time and cost while insufficient one causes warping. So, it’s always a good idea to choose the right cooling time.
- Ejection Time: It is the time required to eject the part from the mold. If you eject the part quickly, it may cause bending. However, late ejection increases cycle time. So, it is important to choose the right ejection time to prevent deformation.
Achieving Dimensional Tolerances in Injection Molding
Every manufacturer wants to achieve dimensional injection molding tolerances in injection molding. Here is how to do that.
Design Phase
You should rely on Computer-Aided Design (CAD) models because they will help you define dimensions and tolerances clearly.
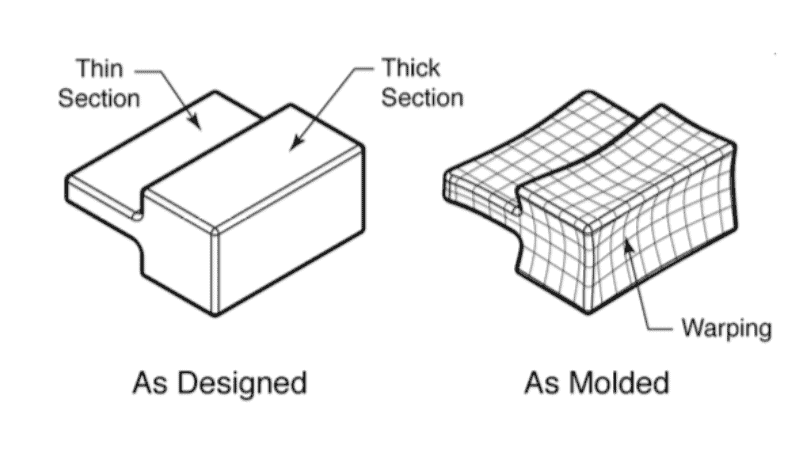
On the other hand, simulation software lets your team predict how the material will behave in the mold. This behavior info makes it easy for you to identify issues early on and find their solution.
Material Selection
Always spend time on material selection because when you have an ideal material at your side, it will drop the project cost. Try to choose the correct material with a consistent and low shrinkage rate. Don’t forget to conduct trials as material helps you get an insight into the material’s behavior under different conditions.
Tooling
Always pick high-quality mols as they let you maintain accuracy. Besides, premium tools are durable. You would be able to reap high ROI from them for years to come. It’s vital to keep your existing mold tools in good condition. Regular tool maintenance helps you avoid any deviations over time.
Process Parameters
Do you want to achieve dimensional tolerance during the injection molding process? If yes, then control the process parameters such as pressure, temperature, and cycle. Here is how
- Use temperature sensors to monitor and control the melt and mold temperature.
- Invest in pressure sensors so that you can maintain consistent injection and holding pressure.
- Try to find the optimal settings by experimenting with varied cycle times.
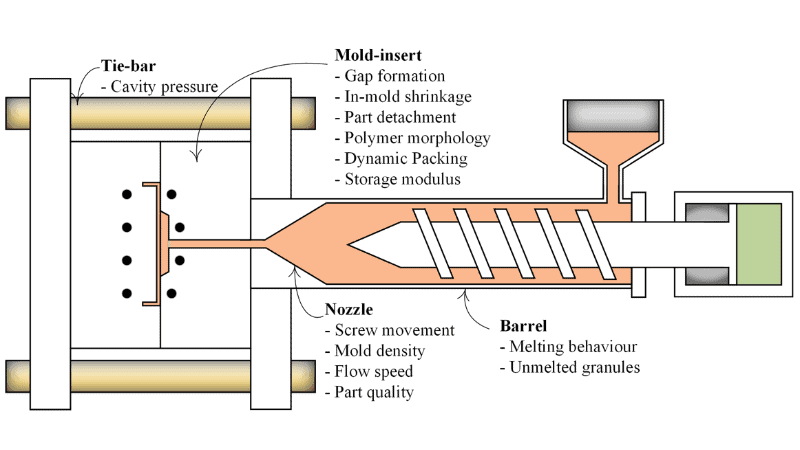
Implement Repeatable Process Controls
Process controls are some methods that help manufacturers calibrate variables affecting the part quality during the injection molding process. Every part manufacturing method and process has some variables. It’s vital to calibrate them to reduce the deviation. Common variables are temperature, holding time, and pressure. Here are six common process control methods:
- Develop SOPs
Standard Operating Procedures (SOPs) They will step-by-step guide to every injection molding process. Your staff can check SOPs for reference as and when they need.
- Sensor Integration
You need to integrate sensors into your overall process because they help you monitor key parameters such as pressure, temperature, and cycling time. You will be able to get real-time feedback and make adjustments accordingly.
- Automation and Process Control Software
If you want to maintain consistency, then you need to employ process control software, which will adjust parameters based on sensor data.
- Quality Checkpoints
You need to establish automated and manual checkpoints at every stage of the injection molding process These checkpoints help you keep the process cost-efficient
Introduce automated and manual quality checkpoints at critical stages. Use technologies like optical inspection or Coordinate Measuring Machines (CMM) for high-precision measurements.
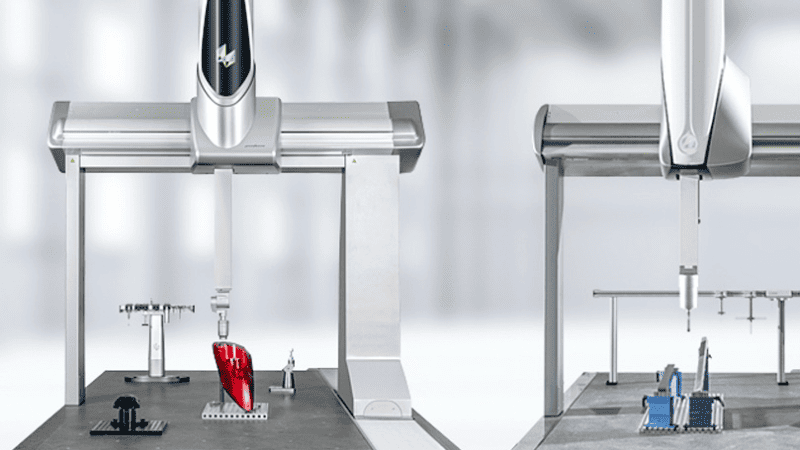
Conclusion
Nothing is as rewarding as mastering the art of precision in injection modeling. Don’t you think? So, if you want to enjoy this reward you need to pay meticulous attention to design, material selection, process parameters, and repeatable process controls.
On one side, you will optimize standard injection molding tolerance, and on the other side, you can meet or even exceed industry standards. If you become successful in optimization, you can deliver high-quality and reliable products, which in turn lets you boost your revenue and customer base through the competitive edge.
Discover the Perfect Solution for Your Business with Hongju
Adopt best practices for quality in injection molding and make precision a standard, not an exception. At Hongju, we can assure you of the highest quality silicone products and expertise to help you find the most suitable solution for your specific needs. Act now and elevate your entire business!
Take the First Step:
Requst for an Inquire
Quality Meets Affordability. Inquire Now for High-Quality Products at Low Volumes.