We’ll also discuss how Low-pressure molding simplifies the process of creating robust, moisture-resistant, and durable enclosures for sensitive components, making it an invaluable tool in today’s manufacturing landscape.
In this complete guide, you will know the basic information about the low-pressure system and the process in detail, and how to choose the perfect way for your needs. If you are interested in them, let us dive into it now.
Basics of Low-Pressure Molding
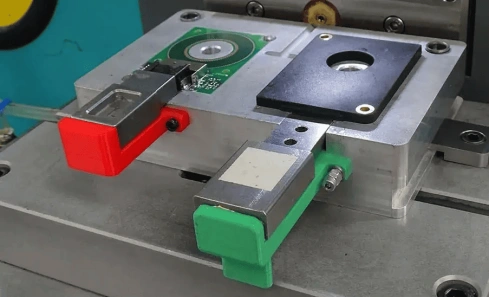
Low-pressure molding is a manufacturing technique for sealing and protecting sensitive electronics and components. It’s used in various industries to create a snug, protective layer around these mold parts.
The basic idea is to melt special, low-temperature plastic materials and gently mold them around the component. Low-pressure molding is unique because it doesn’t involve high temperatures or pressures, which can harm delicate electronics. Instead, it operates at low pressures and temperatures.
The process is quick and efficient, ensuring the encapsulated components in the plastics industry are safe from moisture, dust, and other environmental factors. Low-pressure molding is especially valuable when sealing intricate shapes and small spaces. This technology simplifies manufacturing time and is essential in today’s production world.
Process of Low-Pressure Molding
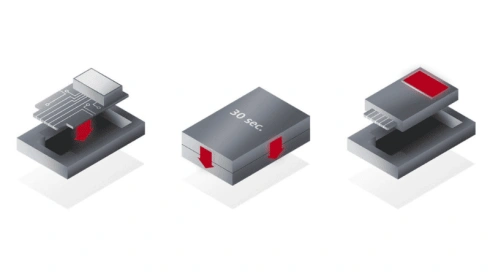
Low-pressure molding is a streamlined way of creating protective coverings for several components. Unlike the traditional potting process, which involves a more complex seven or eight-step process, the Low-Pressure Molding process requires only three simple steps.
Step 1: Melting the Molding Material
Initiating the process involves heating adhesive thermoplastic polyamide materials, often called “hot melts.” These materials, derived from natural fatty acids, prevent harmful emissions. They are heated in a sizeable hopper, preparing for the molding phase.
The low-pressure molding process in the Polyamides market exhibits robust growth, with a CAGR of -0.4%, currently valued at USD 572.6 million globally and projected to reach USD 557.4 million by 2027.
Step 2: Injecting the Mold Set
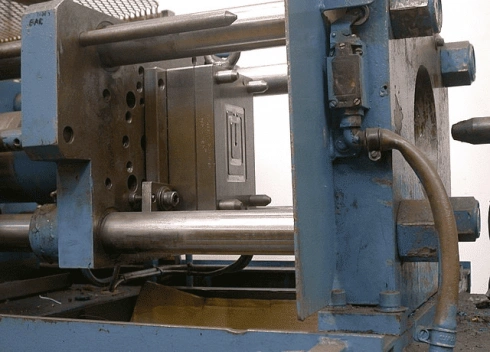
Now, the component to be protected, like wires or electrical parts, is placed into one half of the mold. The other half of the mold is closed, creating a space around the mold components. An injection molding machine gently pumps the liquified thermoplastic into the mold cavity until it’s filled.
Although the low-pressure injection molding process is slower than the high-pressure compression molding process, it’s still pretty quick, usually taking around 30 seconds, depending on the part’s size.
Step 3: Cooling Down
After injecting the molding material, the mold set is opened to allow the over-molded part to cool. Here’s where Low-Pressure Molding shines.
Unlike the traditional potting process, which needs a lengthy curing, Low-Pressure Molding cools rapidly at room temperature. That means you can remove the molded part from the mold and test it shortly after the injection.
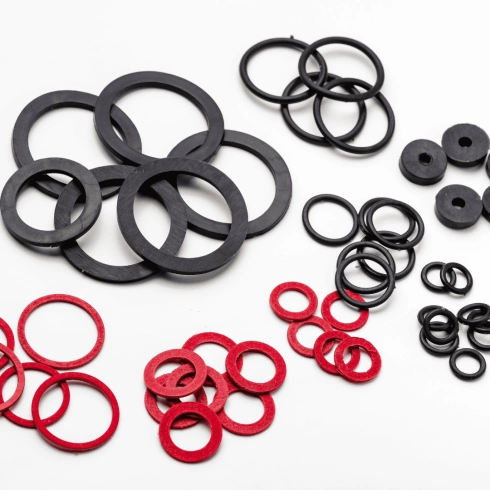
Send Your Inquiry Now!
Quality Meets Affordability. Inquire Now for High-Quality Products at Low Volumes.
6 Benefits of Low-Pressure Molding
Low-pressure molding is a revolutionary manufacturing technique that brings many advantages. Let’s delve into these key benefits in more detail, highlighting how this technology simplifies production and enhances the quality of end products.
Simplicity and Efficiency
One of the most compelling aspects of Low-Pressure Molding is its simplicity and efficiency. The process is designed to be straightforward, making it easy to understand and execute.
This user-friendly approach means quicker mass production without compromising on quality. You don’t need to be a manufacturing expert to appreciate the streamlined nature of this method.
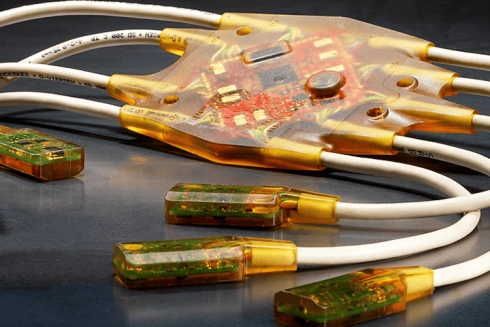
Speed and Flexibility
Low-pressure molding process isn’t just a set of manufacturing steps or techniques; it’s a lightning-fast process. The process ensures that your products are ready in no time. It excels in efficiency, easily adapting to various component sizes and shapes.
Low-pressure molding can handle everything, whether dealing with intricate or large components. This flexibility is a significant asset in a world where customization is increasingly important.
Environmentally Friendly
One standout feature of Low-Pressure Molding is its environmental friendliness. During the molding process, no harmful gases are generated. Moreover, the various materials used are derived from natural sources, which is a win for sustainability. This means you can easily recycle excess materials and scraps, minimizing waste and environmental footprint.
Low-Cost and Economical
Low-pressure molding is not only efficient but also budget-friendly. It requires fewer resources and less energy than traditional methods, making it a cost-effective choice. The best part is that you don’t need expensive molds – even aluminum molds work exceptionally well while maintaining durability. This reduces your overhead costs significantly.
Customizability
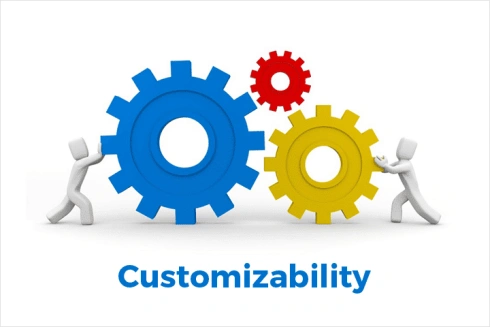
Low-pressure molding empowers you to customize your products to meet specific needs. It’s adaptable, ensuring a perfect fit every time. This customization ability is invaluable in a world where consumers and industries demand tailored solutions.
Lightweight and Resistant
The final products are incredibly lightweight, making them easy to handle and transfer molding. They’re also waterproof, heat-resistant, and capable of withstanding harsh conditions, including shock and external factors. This resilience ensures that your products remain reliable even in demanding environments.
Enhanced Aesthetics
Beyond functionality, Low-Pressure Molding enhances the overall appearance of your products. Its flexibility means there’s no need for additional insulation, resulting in sleek and polished final products. This aesthetic improvement can set your products apart in a competitive market.
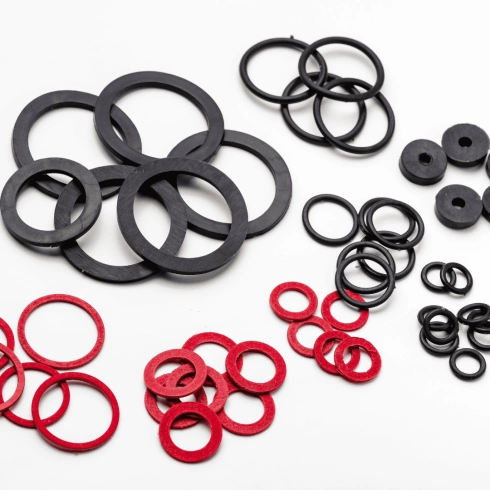
Send Your Inquiry Now!
Quality Meets Affordability. Inquire Now for High-Quality Products at Low Volumes.
Common Applications of Low-Pressure Molding
Low-pressure molding finds a wide range of applications across various industries thanks to its unique qualities and advantages compared to other molding techniques. Let’s explore some of the key areas where Low-Pressure Molding excels.
Electronics and Wiring Protection
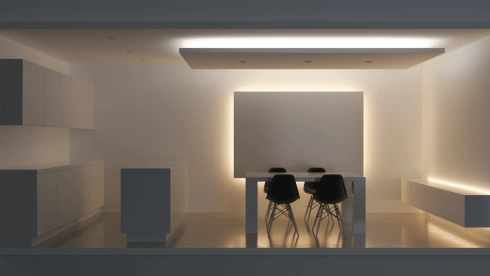
In electronics, Low-Pressure Molding is a game-changer. It’s used to protect delicate components and wiring from harsh environments. This includes safeguarding:
- Printed circuit boards (PCBs)
- Sensors
- Cable assemblies
- Connectors
- LED lighting systems
Low-pressure molding is the linchpin that offers a protective layer that is not just waterproof but also shock-resistant and reliable, ensuring the longevity of electronic devices in challenging conditions.
Automotive
The automotive industry relies on Low-Pressure Molding for sealing and safeguarding sensitive electronic components. It is extensively applied to protect:
- Airbag control modules
- Engine control units (ECUs)
- Engine Components.
- Wiring harnesses
- Sensors
Low-pressure molding technology guarantees that these components can endure the rigorous demands of the automotive sector, where temperature fluctuations and vibrations are commonplace.
Medical Devices
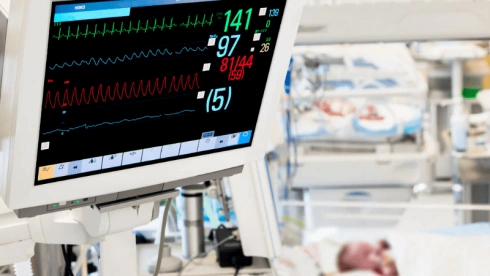
In the medical field, Low-Pressure Molding is used to encapsulate and protect electronics within medical devices, such as:
- Patient monitors
- Defibrillators
- Infusion pumps
- Ultrasound equipment
This application is paramount in guaranteeing the reliability and safety of these life-saving devices, where precision and consistency are of utmost importance.
Aerospace
The aerospace industry relies on Low-Pressure Molding to protect electronic components used in aircraft. This technology is applied to secure:
- Avionics systems
- GPS modules
- Flight control systems
- Communication equipment
With the ability to withstand high temperatures and challenging conditions, Low-Pressure Molding ensures the integrity of these components in the aerospace environment.
Consumer Goods
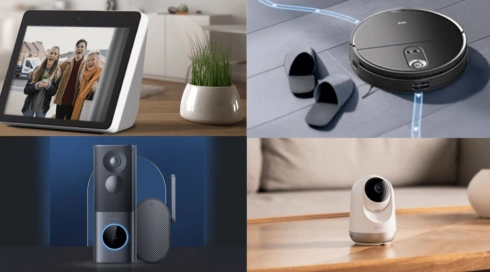
Low-pressure molding extends to the consumer goods sector, which creates products with enhanced durability and functionality. This includes:
- Remote controls
- Wearable devices
- Smart home products
- Electronic toys
The technology protects these devices and enhances their aesthetic appeal, making them more appealing to consumers.
Industrial Equipment
In the industrial sector, Low-Pressure Molding is employed to safeguard and enhance the performance of various equipment, including:
- Motor drives
- Control systems
- Industrial sensors
- Automated machinery
This application is critical to ensure the reliability and longevity of industrial equipment, where downtime can be costly.
Renewable Energy
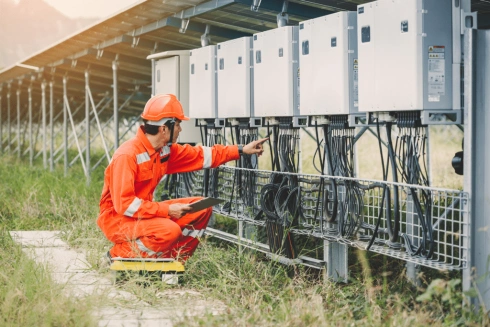
In the renewable energy sector, Low-Pressure Molding plays a crucial role in protecting electronic components used in:
- Solar inverters
- Wind turbine controls
- Battery management systems
Low-pressure molding is instrumental in contributing to the reliability of renewable energy systems, where the robustness of electronic components is paramount for consistent energy production.
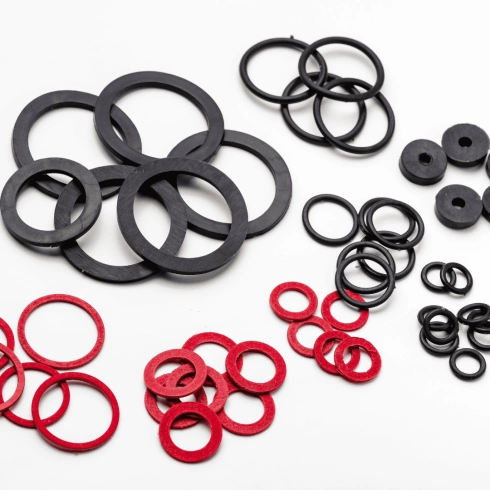
Send Your Inquiry Now!
Quality Meets Affordability. Inquire Now for High-Quality Products at Low Volumes.
Comparative Analysis: Low-pressure vs. High-pressure Molding
Two predominant techniques have emerged in injection molding: Low-Pressure Molding and High-Pressure Injection Molding.
Each of these methods offers distinct advantages and is suited to different applications. Let’s compare and contrast the two to understand their key differences and when to employ them.
Feature | Low-Pressure Molding | High-Pressure Molding |
---|---|---|
Pressure Applied | Typically up to 100 psi | Thousands to 20,000 psi or more |
Materials Used | Thermosets, polyamides | Thermoplastics, some thermosets |
Tooling Cost | Generally lower | Higher |
Cycle Time | Usually longer | Shorter |
Mold Wear | Reduced due to lower pressure | Faster due to higher pressure |
Part Complexity | Suitable for less complex parts | Can handle more complex geometries |
Part Quality | Good for encapsulating parts | Often higher precision and finish |
Part Strength | Generally adequate | Typically stronger |
Waste | Less waste due to overflows | Can have more waste due to sprue and runners |
Setup Time | Often quicker | Can be longer due to precise controls |
Applications | Electronics encapsulation, gaskets | Automotive parts, consumer goods, medical devices |
Equipment Cost | Generally lower | Higher due to advanced machinery |
Material Efficiency | Can be more efficient for certain applications | Often maximizes material usage, but with some waste |
Low-pressure molding is environmentally friendly as it limits harmful gas emissions. Besides, it consumes natural resources and recycles waste, thus minimizing our carbon footprint.
Apart from that, it ensures maximum efficiency and flexibility as it handles all sizes and shapes of components without compromising on quality.
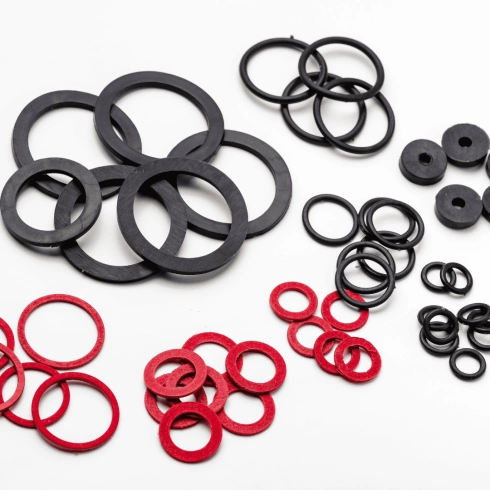
Send Your Inquiry Now!
Quality Meets Affordability. Inquire Now for High-Quality Products at Low Volumes.
Custom Material Options in Low-Pressure
Low-pressure molding offers a wide array of custom material options, allowing manufacturers to tailor the protective covering precisely to the needs of their components and applications. This flexibility is a key advantage of Low-Pressure Molding, as it ensures that the final product meets the specific requirements of each project.
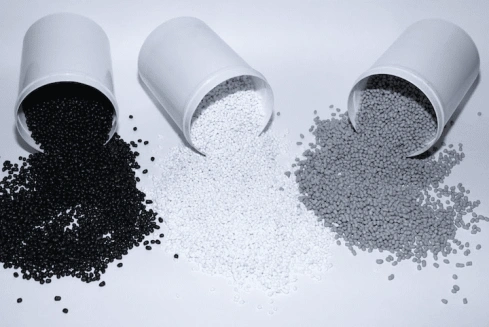
Here’s a closer look at the custom material options available in Low-Pressure Molding:
- Thermoplastic Polyamides (Hot Melts): These materials are often the go-to for Low-Pressure Molding due to their versatility. They are derived from natural sources and do not emit harmful gases during molding. Hot melts can be customized to meet specific temperature, strength, and flexibility requirements.
- Polyolefins: Polyolefin-based materials are known for their excellent resistance to moisture and chemicals. They can be customized to provide different levels of protection, making them suitable for a range of applications.
- Thermoplastic Elastomers (TPE): Thermoplastic Elastomers (TPE) are known for their flexibility and durability. They are often used for the overmolding process to provide a soft and comfortable grip on various products.
- Flame-Retardant Materials: For applications that require excellent protection against fire or high heat, custom materials with flame-retardant properties can be used to ensure safety.
- Conductive Materials: Custom materials with conductive properties can enhance electrical connections in electronics and automotive applications.
- UV-Resistant Materials: When the application is exposed to sunlight and UV radiation, UV-resistant materials can be customized to prevent degradation and maintain the integrity of the protective covering.
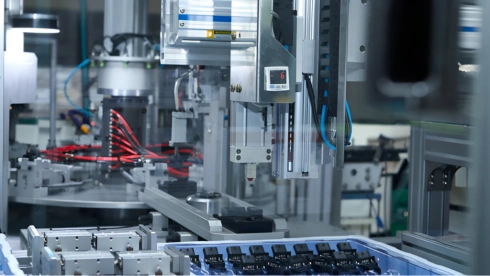
Why Choose Low-pressure Molding for Your Needs?
Due to its unique benefits, low-pressure molding is an attractive choice for various applications. Here’s why you should consider it for your specific needs:
- Delicate Component Protection: When you need to produce parts with delicate electronic components, sensors, or intricate wiring, Low-Pressure Molding offers a gentle yet robust solution. It safeguards these fragile components, ensuring their integrity even in harsh environments.
- Customization: Low-pressure molding allows the material to be customized to meet your precise requirements. You can tailor factors like hardness, rigidity, and color, ensuring the final product aligns perfectly with your needs.
- Speed and Efficiency: In a fast-paced manufacturing world, efficiency matters. Low-pressure molding is known for its speed, making it an excellent choice for high-volume production. With quicker cycle times, it keeps your production lines humming.
- Environmental Responsibility: Low-pressure molding is eco-friendly. It doesn’t emit harmful gases during the process and is often made from natural materials, promoting sustainability. Choosing Low-Pressure Molding aligns with environmental responsibility.
- Cost-Effective: Low-Pressure Molding is budget-friendly. It requires fewer resources, less energy, and doesn’t necessitate expensive molds. It’s an economically sound choice without compromising on quality.
- Versatility: Whether you’re in electronics, automotive, medical devices, aerospace, or consumer goods, Low-Pressure Molding adapts to diverse industries. Its versatility, particularly in insert molding applications, makes it a reliable option for many applications.
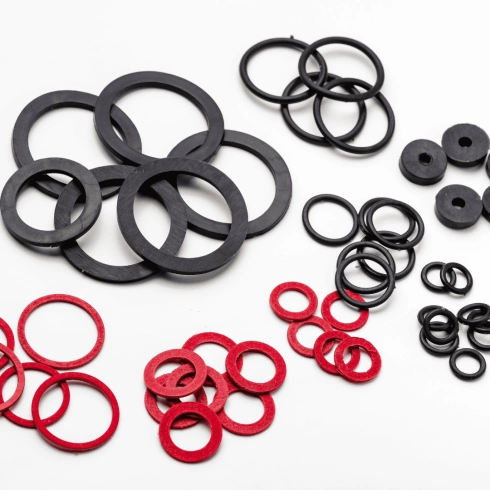
Send Your Inquiry Now!
Quality Meets Affordability. Inquire Now for High-Quality Products at Low Volumes.
Conclusion
Low-pressure molding is a revolutionary manufacturing method that offers protection, customization, efficiency, eco-friendliness, and cost-effectiveness. It is used in various industries like electronics, automotive, medical devices, aerospace, consumer goods, industrial equipment, and renewable energy.
It provides a reliable solution for safeguarding delicate components and enhancing product performance through injection molding plastics. Its advantages include speed, eco-friendliness, cost-efficiency, and versatility.
Make the Most of Low-Pressure Molding with Hongju
If you’re ready to explore the possibilities and harness the benefits of Low-Pressure Molding for your unique needs, Hongju invites you to take the next step.
Contact Hongju‘s experts today to discuss how this innovative technology can transform your manufacturing process and elevate the quality of your products and improve your business.