Whether you’re new to the injection molding process or an experienced manufacturer, understanding the intricacies of rubber overmolding is crucial for achieving optimal results. This comprehensive guide aims to explore this specialized molding process in depth, offering valuable insights for manufacturers across industries.
What is Rubber Overmolding?
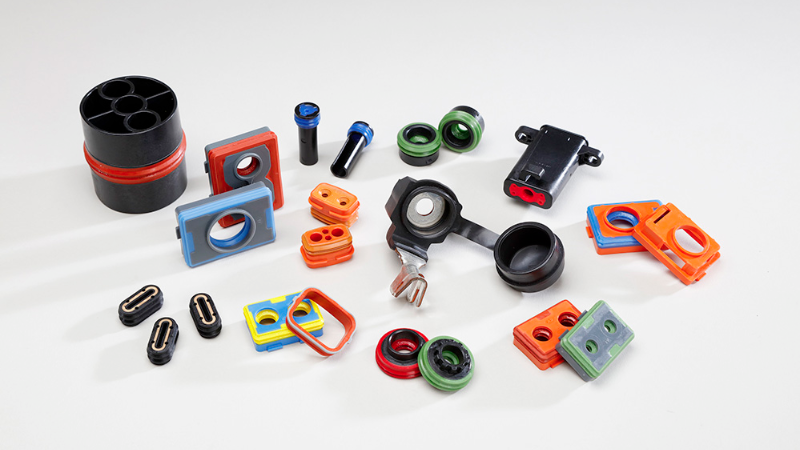
Rubber overmolding is an advanced manufacturing process that involves applying a second layer of elastomer material, typically rubber, onto a pre-existing substrate material or plastic component. The technique begins with the application of molten rubber to the desired area on the substrate. As it cools and solidifies, it forms a durable material layer that offers protective and functional features.
This process creates a strong mechanical bonding or chemical bonding between the rubber and the substrate, achieving seamless integration and enhanced mechanical properties. Different methods like injection molding and compression molding are utilized to achieve this bond. The final product benefits from improved shock absorption, flexural modulus, and a consistent wall thickness.
By using rubber overmolding, manufacturers can create molded components with superior performance characteristics, making it a go-to choice for various applications including medical equipment and consumer goods. The end result is a high-quality product with increased durability, resilience, and a broad range of potential functionalities.
Types of Rubber Used in Overmolding
The choice of rubber type plays a critical role in the overmolding process. Different types of rubber have varying mechanical properties, flexural modulus, and the material’s ability to withstand environmental factors. Here are some commonly used types of rubber in overmolding:
Thermoplastic Polyurethane (TPU)
Thermoplastic Polyurethane is renowned for its high abrasion resistance and is often used in applications requiring a durable material. It offers good mechanical bonding and is suitable for injection molding projects.
Silicone Rubber
Known for its wide temperature range and resistance to extreme conditions, silicone rubber is used for medical equipment and other sensitive applications. It provides excellent chemical resistance and shock absorption.
Nitrile Rubber (NBR)
This rubber type is widely used for its excellent oil and fuel resistance. It’s a suitable choice for overmolding tpe materials and other applications involving contact with oils and chemicals.
Ethylene Propylene Diene Monomer(EPDM)
EPDM is particularly useful in outdoor applications due to its excellent resistance to weather and ozone. It offers good shock absorption and is easy to mold, making it a cost-effective option for various overmolding projects.
Natural Rubber
Natural rubber offers excellent tensile strength and elongation properties. However, it has limited resistance to chemical attack and extreme temperatures.
Choosing the right type of rubber for your overmolding project depends on several factors including the substrate and overmold compatibility, application requirements, and cost considerations. Each rubber type offers its own set of advantages and potential drawbacks, making it crucial to carefully evaluate your needs before proceeding with the manufacturing process.
Benefits of Rubber Overmolding
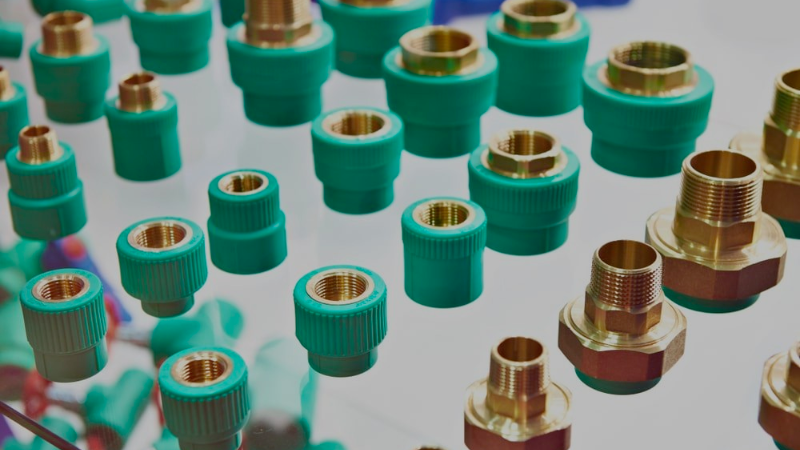
Rubber overmolding offers numerous advantages that make it a highly sought-after technique in various industries. Here’s a look at why manufacturers often prefer this manufacturing process:
- Enhanced Durability: Overmolding enhances the durable material qualities of the final product, increasing its lifespan. This is especially true when using rubber types with high mechanical properties and flexural modulus.
- Improved Functionality: Overmolding can add functional features like grips, seals, or cushioning. This is a plus point for applications requiring good shock absorption and mechanical features.
- Strong Bonding: The overmolding process creates a seamless integration between the substrate material and the overmold material. This strong bond can be either mechanical bonding or chemical bonding, depending on the materials used.
- Aesthetic Appeal: The molding process allows for the incorporation of multiple colors and textures, adding aesthetic value to the plastic component or product.
- Cost-Effectiveness: Rubber overmolding often results in a cost-effective manufacturing process. By eliminating the need for secondary processes like gluing or fastening, it reduces labor costs and production time.
- Enhanced Chemical Resistance: Certain types of rubber used in overmolding offer outstanding chemical resistance, making them ideal for medical equipment or industrial applications where chemical exposure is a concern.
Key Considerations in Rubber Overmolding
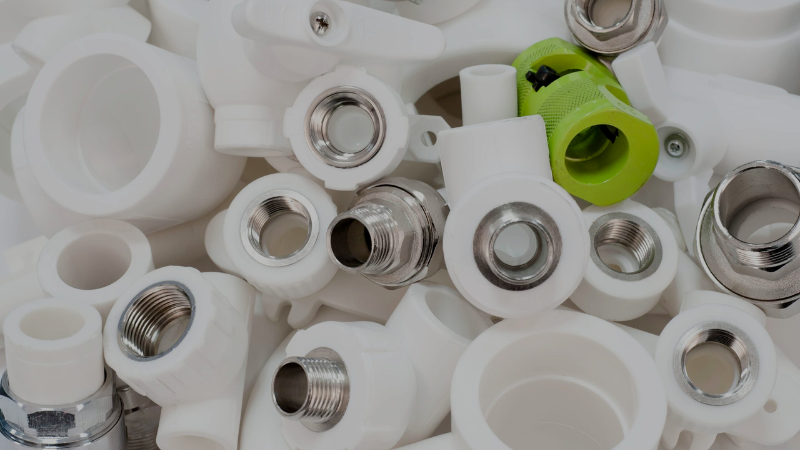
When planning an overmolding project, several critical factors should be considered to ensure successful outcomes. Below are some of the key aspects that manufacturers must keep in mind:
Material Compatibility for Optimal Adhesion
Achieving optimal adhesion in rubber overmolding requires careful consideration of the material compatibility between the rubber compound and the substrate. The choice of rubber compound should be compatible with the substrate material to ensure a strong bond. For example, if the substrate is made of plastic, selecting a rubber compound that adheres well to plastics is essential.
Different types of rubber compounds exhibit varying levels of adhesion to different substrates. Conducting thorough testing and analysis can help determine which combination of materials will provide the best results. This involves assessing factors such as chemical compatibility, surface energy, and mechanical properties.
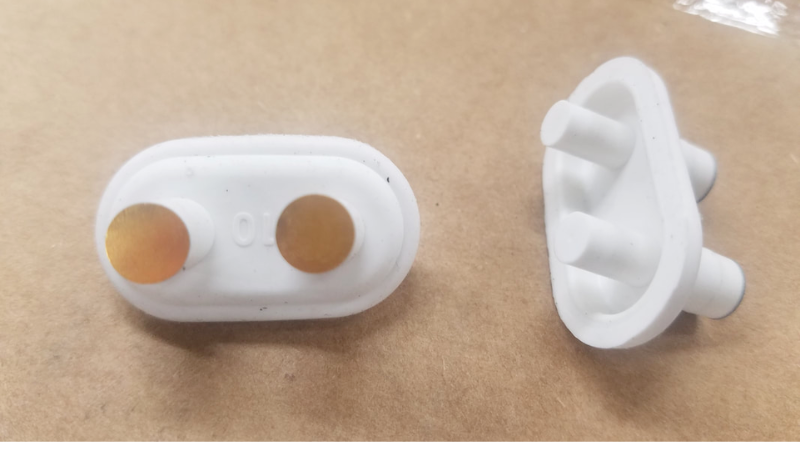
To ensure successful adhesion, it is crucial to consider factors such as:
- Chemical compatibility: The rubber compound and substrate should be chemically compatible to prevent any adverse reactions that may compromise bonding strength.
- Surface energy: The surface energy of both the rubber compound and substrate should be compatible for effective wetting and bonding.
- Mechanical properties: The mechanical properties of the rubber compound should match those required for proper bonding with the substrate.
By carefully matching materials based on these considerations, manufacturers can enhance adhesion strength and overall product performance in rubber overmolding applications.
Proper Mold Design for Uniform Distribution
In rubber overmolding, proper mold design plays a vital role in achieving uniform distribution of the rubber material during the molding process. A well-designed mold ensures that there are no air pockets or voids between the rubber and substrate, leading to improved adhesion and product quality.
Some key aspects to consider when designing molds for rubber overmolding include:
- Venting: Adequate venting allows trapped air or gases to escape during injection, preventing defects like bubbles or incomplete filling.
- Gate placement: Proper gate placement ensures even flow distribution throughout the mold cavity, minimizing any variations in thickness.
- Runner system design: An optimized runner system helps maintain consistent flow and pressure during the injection process, promoting uniform distribution of the rubber material.
Design Principles for Rubber Overmolding
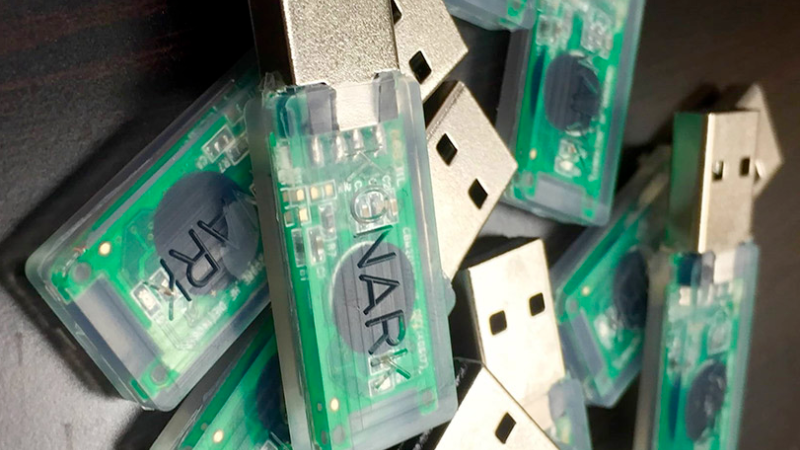
Design considerations play a crucial role in the success of rubber overmolding projects. By focusing on design for manufacturability, engineers can create parts that can be efficiently produced using overmolding techniques.
Wall Thickness Uniformity
One essential aspect of rubber overmolding design is maintaining wall thickness uniformity. This factor helps prevent defects such as air entrapment or incomplete filling during the molding process. When designing parts for overmolding, it is vital to ensure that the walls are consistent in thickness throughout the component. Variations in wall thickness can lead to issues like flow imbalances and inadequate material distribution, resulting in compromised part quality.
To achieve wall thickness uniformity, designers should consider the following strategies:
- Conducting a thorough analysis of the part geometry to identify potential areas where variations may occur.
- Utilizing computer-aided engineering (CAE) software to simulate and optimize mold filling patterns.
- Employing proper gate placement techniques to facilitate even material flow.
By paying attention to wall thickness uniformity, designers can minimize defects and enhance overall product performance.
Incorporating Draft Angles
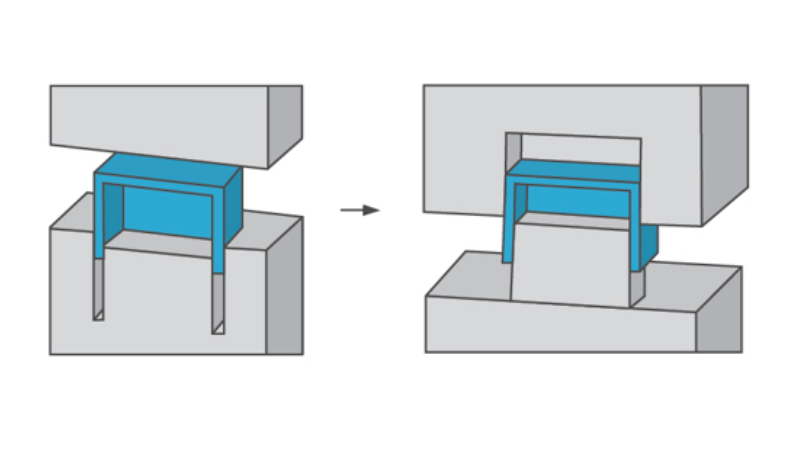
In addition to wall thickness uniformity, incorporating draft angles into the design is another critical consideration for successful rubber overmolding. Draft angles refer to the slight taper given to vertical surfaces of a part that allows for easy ejection from molds while maintaining dimensional accuracy.
When implementing draft angles in rubber overmolding designs, several benefits arise:
- Facilitates smooth release: The tapered surface reduces friction between the part and mold cavity, ensuring smooth ejection without damage.
- Prevents undercuts: Draft angles help avoid undercuts or features that would otherwise hinder part removal from the mold.
- Enhances mold fill: Proper draft angles aid material flow during the overmolding process, minimizing the risk of incomplete filling or air entrapment.
The Overmolding Process
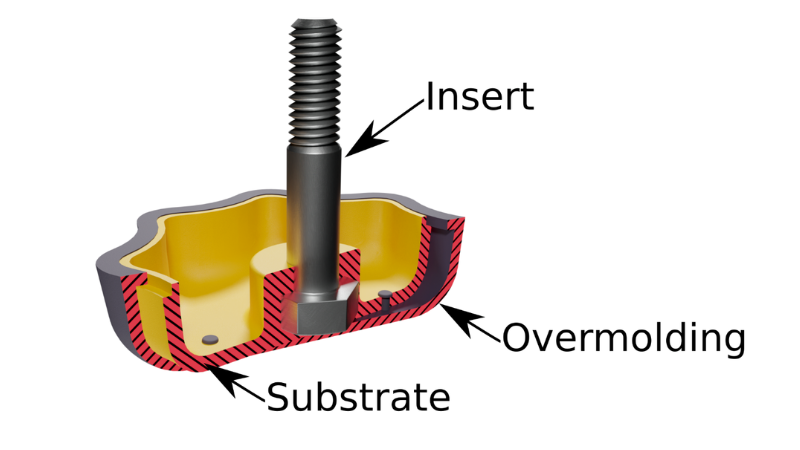
The overmolding process is a specialized manufacturing process that offers a myriad of benefits, including enhanced durability, functionality, and aesthetics. Let’s dig deeper into the intricacies of this fascinating technique, including the vital steps from preparation to post-production.
Prepping the Substrate
One cannot simply jump into the overmolding process without proper preparation. The substrate, often made of different materials such as metal or plastic, must be cleaned and primed for optimal adhesion. This ensures that the overmold material bonds correctly with the substrate, making for a durable material union.
Placing in a Mold and Injecting Molten Rubber
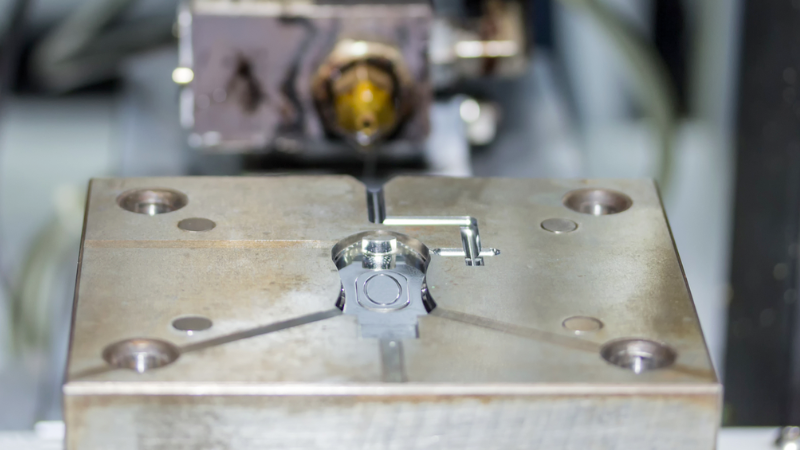
The cleaned and primed substrate is then secured in a specially designed mold suitable for injection molding. These molds are crafted with precise mechanical features, considering factors like consistent wall thickness. Specialized injection molding machines are used, which exert the appropriate clamping force and offer precise temperature control. Molten rubber, or other elastomer materials, are then injected into the mold cavity.
Injection Molding Nuances
During this injection molding process, molten rubber fills the mold under high pressure, ensuring that even intricate details are captured with high precision. Advanced injection molding techniques allow for greater design complexity, making it possible to achieve multiple layers, undercuts, and even specialized mechanical properties.
Post-Molding Operations
Once the molten rubber solidifies within the mold, it moves to the post-molding phase. This involves material thickness trimming, often carried out using specialized equipment. Excess overmold material is removed to meet design specifications.
Quality Control
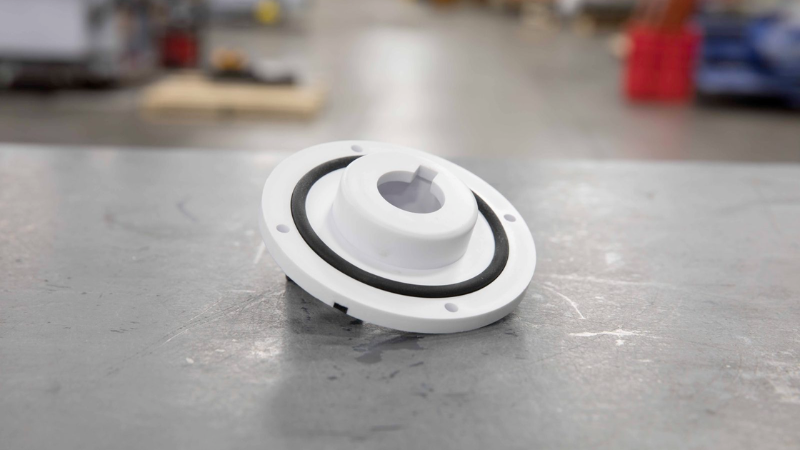
No overmolding project is complete without rigorous quality assurance. Post-molding operations include detailed inspections to search for any production defects or imperfections. These inspections ensure that each component, whether it’s for medical equipment or other applications, meets the necessary quality standards.
Liquid Silicone Rubber Overmolding: Benefits and Applications
Liquid silicone rubber (LSR) overmolding is a versatile manufacturing method that offers numerous benefits across various industries. With its ability to provide high precision, tight tolerances, and excellent part-to-part consistency, LSR overmolding has become a popular choice for producing complex components with intricate designs.
High Precision, Tight Tolerances, and Lower Production Costs
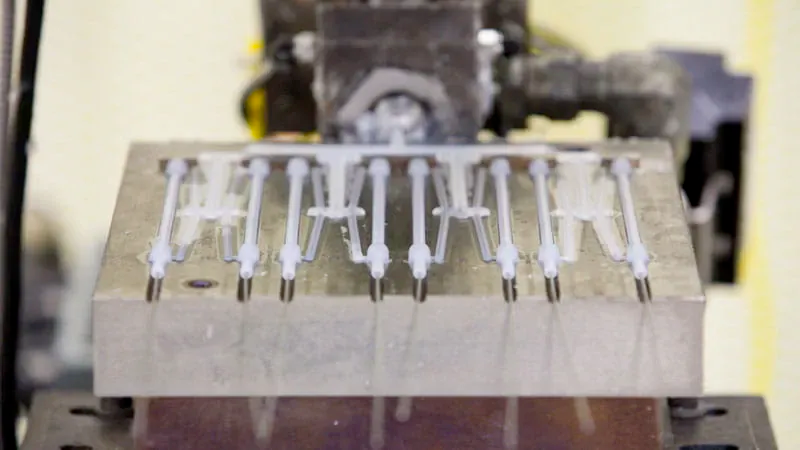
One of the key advantages of LSR overmolding is its exceptional precision. This manufacturing method allows for the injection of the liquid silicone material into intricate molds with great accuracy, enabling the creation of highly detailed electrical components. This level of precision ensures consistent product performance and meets the required specifications.
Additionally, LSR overmolding enables manufacturers to achieve tight tolerances and lower production costs. The finished products adhere closely to the intended dimensions, creating a strong chemical bond between the two materials and resulting in a seamless fit when combined with other parts or materials.
Wide Range of Applications with Material Selection and Vibration Dampening
LSR overmolded parts have found their place in a diverse range of industries due to their unique properties and thoughtful material selection. In the medical field, liquid silicone rubber is widely used for producing biocompatible components such as seals, gaskets, and valves. Its resistance to chemicals and UV light makes it an ideal material for devices that come into contact with bodily fluids or pharmaceuticals.
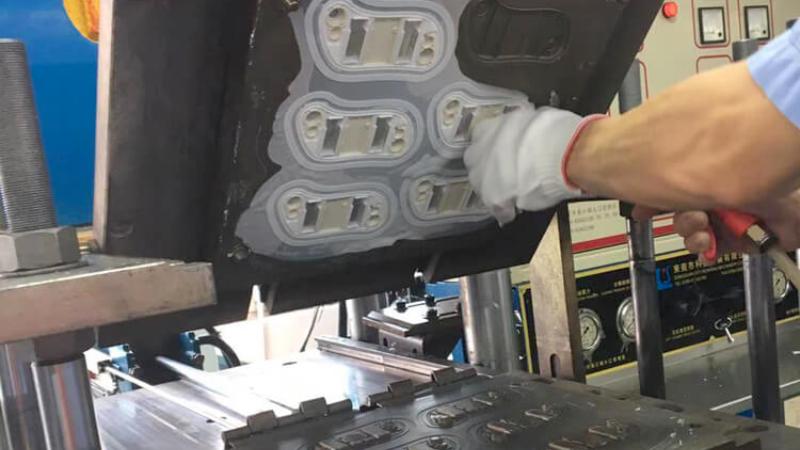
In consumer electronics and power tools, LSR overmolding provides durability along with enhanced functionality like vibration absorption. It can be employed in a two-shot or transfer molding process to create protective covers for sensitive electronic components like circuit boards or connectors. The flexibility and resilience of liquid silicone rubber offer optimal performance and vibration dampening, even under challenging conditions.
Automotive and Product Performance
Automotive manufacturers utilize LSR overmolding techniques to produce weather-resistant seals and gaskets. These components, often created using a two-shot process, are crucial for maintaining the integrity of various systems, such as engines, transmissions, and electrical connections, thereby enhancing overall product performance. Its ability to create a strong chemical bond also eliminates issues like shrink marks, contributing to the component’s durability.
By combining the benefits of lower production costs, material selection, and specialized manufacturing techniques like two-shot or transfer molding, LSR overmolding has become an invaluable tool for a plethora of applications.
Applications of Rubber Overmolding
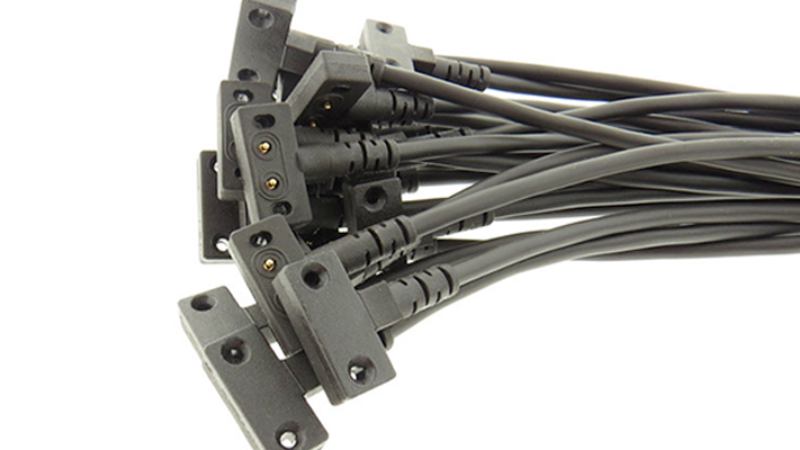
Rubber overmolding has become increasingly popular across various industries due to its versatility and ability to enhance product performance. From the automotive sector to electronics and medical devices, rubber overmolding offers a wide range of applications that cater to different needs and requirements.
Automotive Industry Applications
In the automotive industry, rubber overmolding is extensively used for enhancing grip, sealing components, and reducing vibrations. The applications are diverse and include:
- Grips on Steering Wheels: Rubber overmolding provides a comfortable and secure grip on steering wheels, improving driver control and reducing fatigue during long drives.
- Seals for Windows or Doors: Rubber overmolded seals help create a watertight barrier between windows/doors and their frames, preventing leaks and reducing noise transmission.
- Anti-Vibration Mounts: By incorporating rubber materials with excellent vibration-damping properties, manufacturers can reduce unwanted vibrations in various vehicle components such as engines or suspension systems.
These applications not only improve the overall driving experience but also contribute to safety by ensuring better control and reduced noise levels within vehicles.
Electronics Benefits from Rubber Overmolding
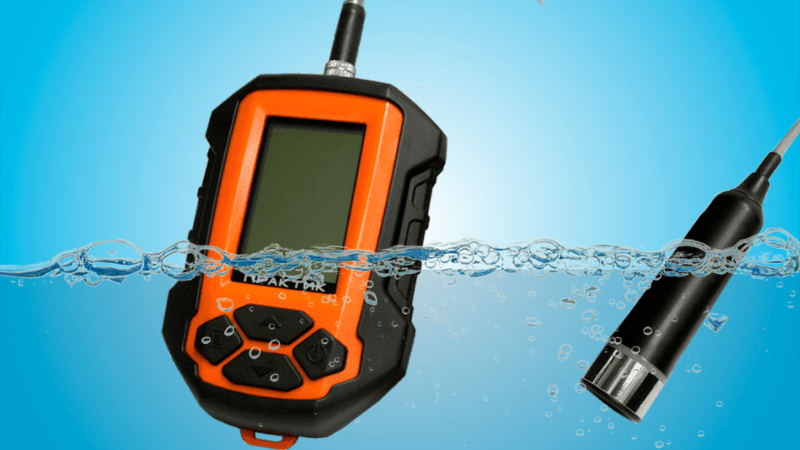
The electronics industry greatly benefits from rubber overmolding as it offers enhanced protection, durability, and functionality. Some common applications include:
- Connectors: Rubber overmolded connectors provide superior insulation against moisture, dust, and other environmental factors while ensuring reliable electrical connections.
- Keypads: Incorporating rubber overlays onto keypads enhances tactile feedback, making them more responsive for users in various electronic devices like remote controls or industrial equipment.
- Protective Cases: Rubber overmolding adds an extra layer of shock resistance to protective cases for smartphones or tablets, safeguarding them from accidental drops or impacts.
- Strain Relief Components: Cables often require strain relief to prevent damage at connection points. Rubber overmolded strain relief components offer flexibility and protection against bending or pulling forces.
Quality Control Challenges in Rubber Overmolding
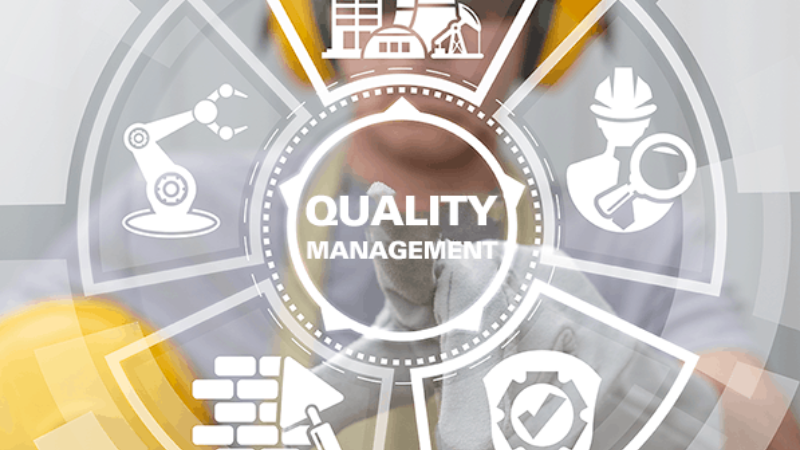
The overmolding process is a precise technique that combines multiple materials into a single, functional component. While it offers many benefits in terms of mechanical features and aesthetics, the process is not without its challenges, especially in the realm of quality control. Here are some of the key challenges manufacturers face:
Consistent Wall Thickness
Achieving a consistent wall thickness throughout the overmolded part can be challenging, especially with complex geometries. Variability in wall thickness can lead to imbalanced cooling rates, which in turn could result in warping or internal stresses in the final part.
Material Compatibility
Selecting the right overmold material to pair with the substrate material is crucial. Incorrect pairings can lead to weak mechanical or chemical bonding, causing premature seal failure or delamination in the finished part.
Injection Molding Project Planning
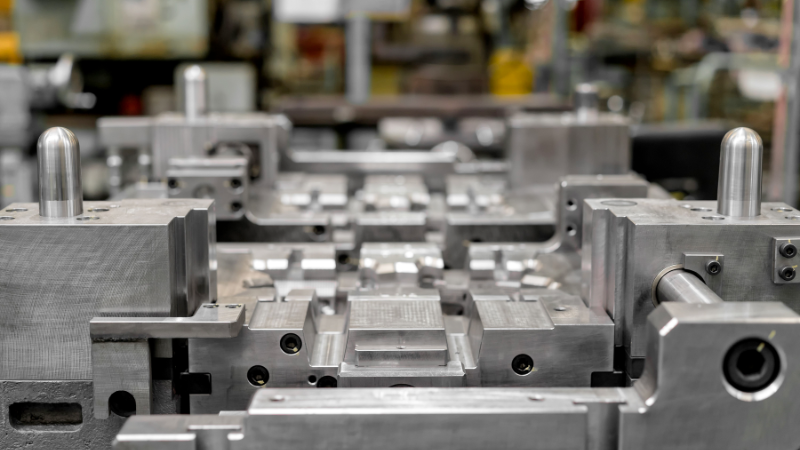
Proper planning and simulation for your injection molding project are critical to identify and solve any potential issues before they occur. Issues like air traps, weld lines, and insufficient filling can all be predicted and corrected in the planning stage.
Adherence to Industry Standards
Especially in industries like medical equipment and aerospace, where failure is not an option, adhering to industry-specific quality standards is challenging but essential. Compliance with these regulations assures the mechanical properties and chemical resistance of the overmolded part meet or exceed requirements.
Post-Molding Quality Assurance
After the molding process, rigorous quality assurance is vital. Each molded component must be inspected for any defects like air bubbles, uneven coloring, or structural weaknesses, which could compromise the part’s functionality or safety.
Navigating these challenges requires a deep understanding of the overmolding process and meticulous attention to detail. Manufacturers must employ rigorous testing methods and quality assurance protocols to ensure that the final product not only meets but exceeds expectations.
Tips for Rubber Overmolding Manufacturers
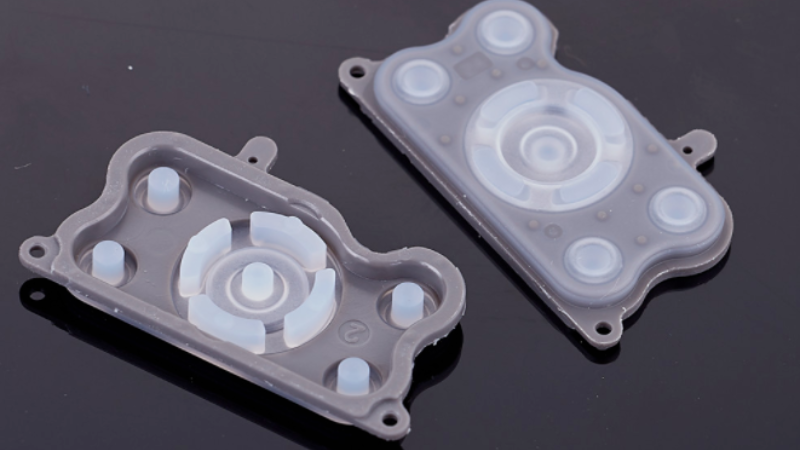
In the complex landscape of rubber overmolding, manufacturers can adopt several strategies to ensure the final product meets quality standards while remaining cost-effective. Here are some practical tips to consider:
- Process Optimization: Streamlining the manufacturing process through simulation and prototyping can save both time and resources. Utilize injection molding project planning tools to simulate the plastic flow, wall thickness, and other parameters before the actual production.
- Quality Checks: Incorporate quality checks at different stages of the overmolding process. Real-time monitoring of parameters like temperature, pressure, and material flow can help in identifying issues before they become significant problems.
- Flexural Modulus: Understanding the flexural modulus and other mechanical features of your materials can offer insights into the material’s ability to withstand various stresses and strains. This is critical for applications that will be subject to external forces.
- Training and Expertise: Training your team in specialized injection molding and overmolding techniques can go a long way in ensuring the quality and efficiency of your manufacturing process. Make sure everyone involved understands the importance of consistent wall thickness, material properties, and quality control.
By adhering to these tips and maintaining a focus on quality control, manufacturers can navigate the complexities of rubber overmolding effectively.
Conclusion
Navigating the complexities of rubber overmolding requires a keen understanding of material properties, process optimization, and quality control measures. By adopting the right strategies, from material selection to post-molding operations, manufacturers can create durable, high-quality molded components suitable for a range of applications.
Partner with Hongju for Your Next Overmolding Project
Hongju has the expertise and advanced technology you need. Let us guide you through your next overmolding project, ensuring high-quality and durable products tailored to your specific needs. Don’t leave your project to chance; click the link below to consult with Hongju’s overmolding specialists today!
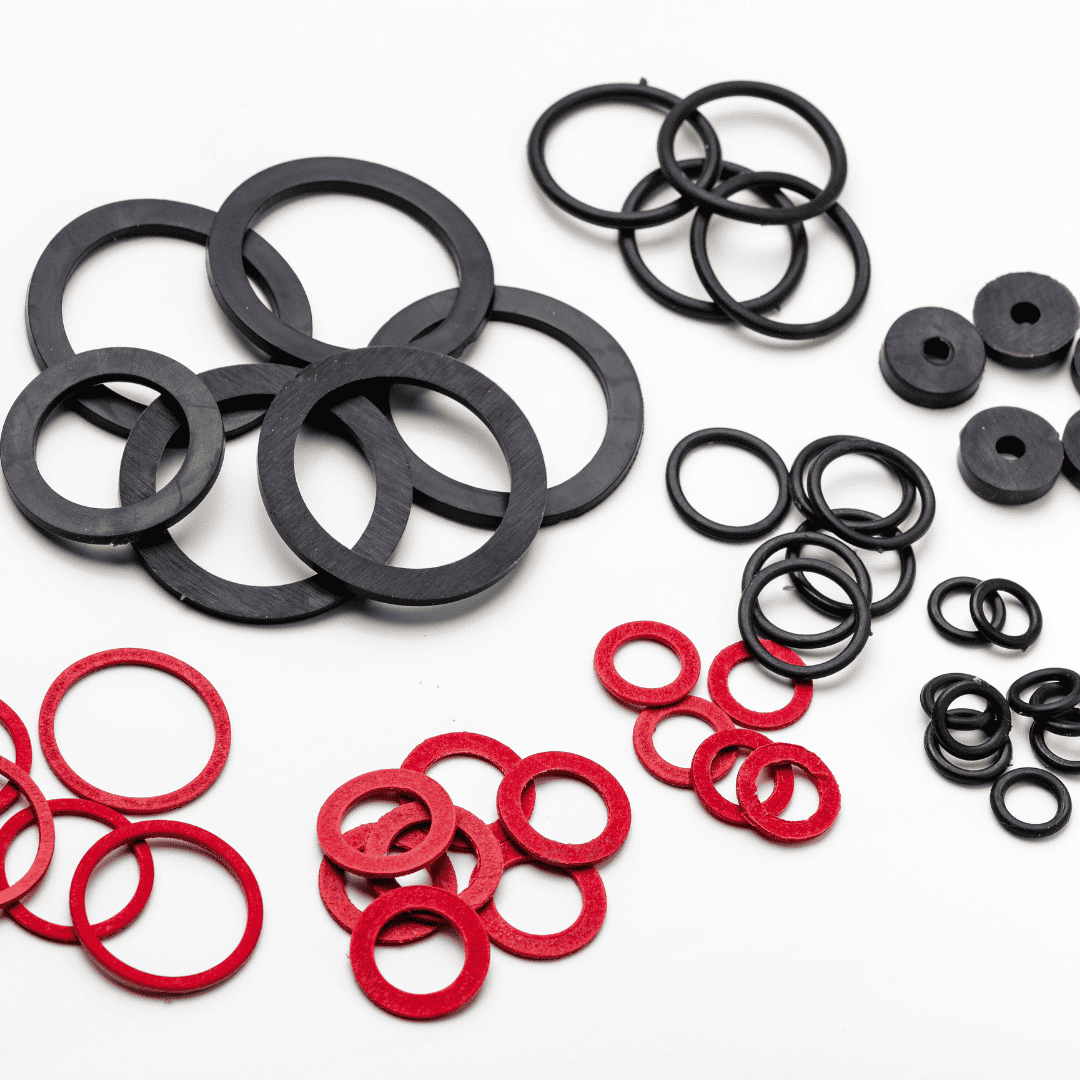
Send Your Inquiry Now!
Quality Meets Affordability. Inquire Now for High-Quality Products at Low Volumes.