Silicone is everywhere—it is used in healthcare, electronic devices, and even kitchen tools. Its flexibility and resistance to extreme conditions make it essential in many fields. However, different types of silicone have different physical properties. This article will explain seven types, their features, and how they are used.
1. High-Temperature Silicone Rubber
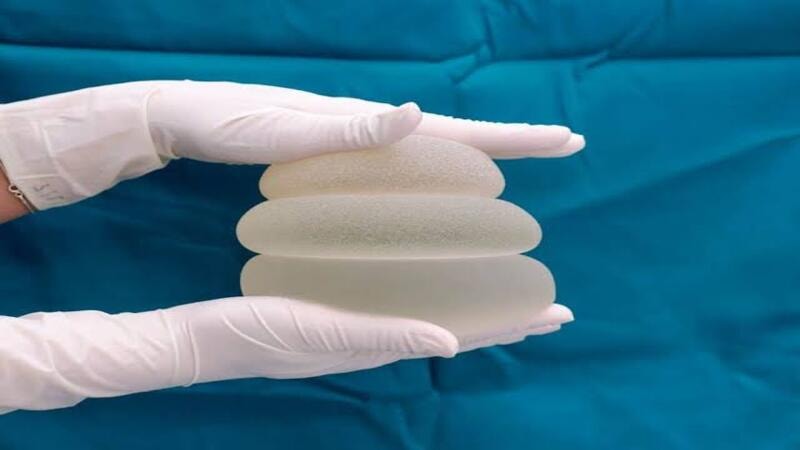
High-temperature silicone rubber is a synthetic material known for its resistance to heat. It remains flexible and strong even in extreme environments. Unlike regular rubber, it does not break down under continuous heat or chemical exposure. It performs well in temperatures from -60°C to +300°C. This rubber holds unmatchable properties.
Key Features
High-temperature silicone rubber offers outstanding heat resistance. Elasticity remains unchanged even at high temperatures. Strength and durability ensure long-term performance.
Applications
The automotive industry uses it for engine components. Gaskets and seals benefit from their thermal stability. Cooking appliances rely on it for safe operation at ambient temperatures. Industrial machinery depends on it for high-heat applications.
Best Use Cases
High-temperature silicone rubber is used for applications where materials must retain flexibility and strength under extreme heat. It is commonly used in aerospace, automotive, and industrial machinery for sealing, insulation, and gaskets.
Why It’s Important
Industries working with high heat rely on this silicone because it resists temperatures up to 300°C (572°F) without breaking down. Unlike other chemicals and regular rubber, it doesn’t harden, crack, or lose elasticity.
2. Fluorosilicone Rubber (FVMQ)
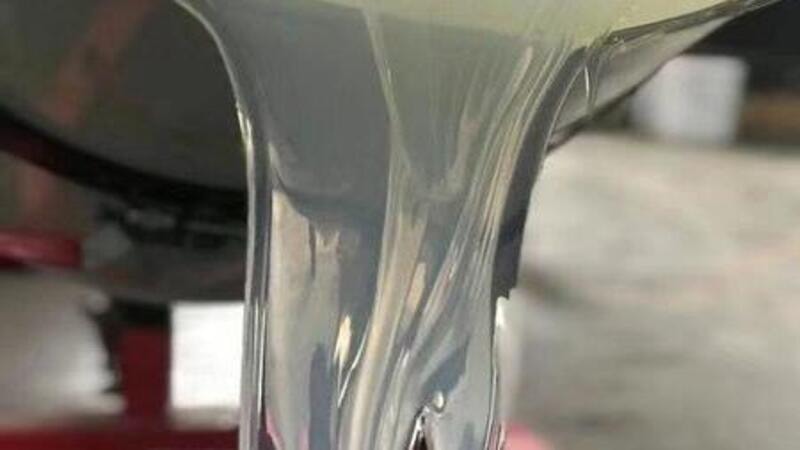
Fluorosilicone rubber offers the flexibility of silicone with superior chemical resistance. Fluorine components in the material structure create resistance to oils solvents and strong corrosive chemicals. The material provides better performance than standard silicone rubber.
Key Features
The material demonstrates outstanding performance against chemicals and oils. The material operates successfully at temperatures ranging from 200°C and above while keeping its stable condition. The substance has extended durability because of its chemical structure and its robust molecular patterns combined with extensive polymer chain length.
Applications
The aerospace and automotive sectors rely on this material to produce gaskets and seals that resist oil. The chemical resistance properties of this material make it suitable for industrial sealing applications. Modern technology implements it for protective device coatings and automotive applications.
Best Use Cases
Fluorosilicone rubber stands out for its ability to handle environments containing extreme temperatures, harsh chemicals, and fuel-based substances. Engineers choose fluorosilicone rubber extensively for critical material applications in the automotive and aerospace industries.
Why It’s Important
The multi-purpose polymer provides extraordinary protection to both intense heat conditions and corrosive agents which creates dependable service along with prolonged service life in severe operating environments. Engineers choose FVMQ because it has established itself through demanding tests and extended service durations.
3. Liquid Silicone Rubber (LSR)
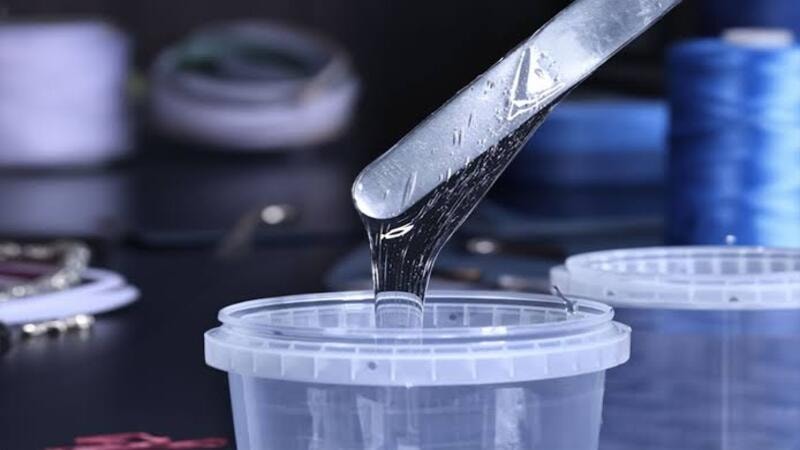
The high-purity thermoset elastomer Liquid Silicone Rubber (LSR) contains distinct chemical properties. The process of liquid injection molding makes it possible to achieve easy processing. It serves many applications because of its suitability. The operating range of LSR extends from -60°C to +300°C. LSR’s specific material properties are a result of its unique chemical structure.
Key Features
The material stability of LSR extends to both hot and cold environmental conditions. Liquid silicone rubber has both flexibility and strength. The material possesses insulation characteristics that enable its use in electronic applications. This material shows strong resistance to both chemical substances and water making it suitable for demanding conditions. The material’s biocompatible properties enable safe medical usage.
Applications
The medical industry uses LSR because it maintains safety standards and allows for sterilization processes. The material endures high heat within automotive systems therefore it serves as an ideal material for gaskets and hoses. The consumer market uses flexible LSR to create both bracelets and kitchenware products. The electronic industry employs LSR to protect sensitive components by using it as a wire insulation and sealing material.
Best Use Cases
The engineering community chooses this material because it enables precise molding operations during the production of small to medium-sized product batches.
Why It’s Important
The experts depend on its high precision along with its biocompatibility and flexible molding capabilities for their critical applications. Liquid silicone rubber’s unique properties and broad industrial uses make it a valuable choice for businesses.
4. Addition-Cure Silicone
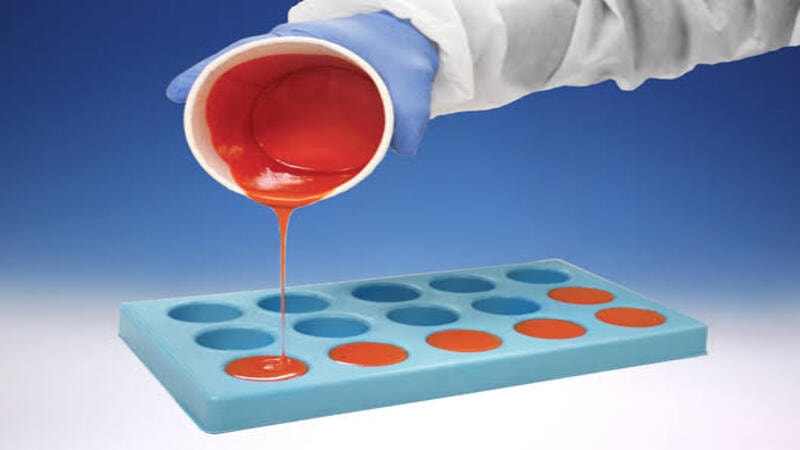
Addition-cure silicone rubber cures with a platinum catalyst in a fast chemical reaction. Curing is almost free from byproducts using modern techniques. Efficient methods reduce curing time and increase productivity.
Key Features
It has excellent consistency and superior chemical stability throughout. Formulations are engineered so that a clean process always occurs and no harmful releases go down the drain. High performance and quality are supported by innovative production across multiple batches.
Applications
It benefits medical devices greatly in terms of its purity and dependable performance. This silicone is used for food-grade products due to its safety and compliance with strict regulations. It is robust enough to use as electrical insulation and durable for silicone mold for gaskets.
Best Use Cases
Industries needing precise, stable materials choose this silicone for critical projects. Specialist sectors, including the medical and food industries, appreciate its outstanding performance.
Why It’s Important
Purity is vital for sensitive applications that demand high standards. Quality and reliability make this material a top choice for professionals. Ultimately, this versatile silicone ensures safety and meets the rigorous demands of professional industries.
5. Condensation-Cure Silicone Rubber
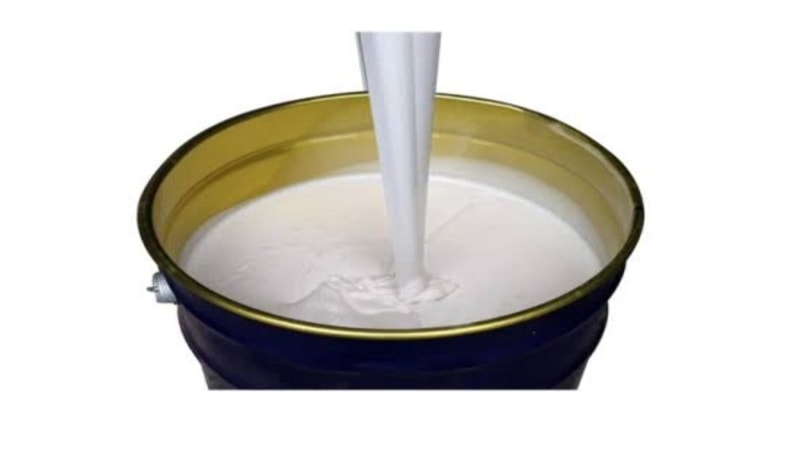
Condensation-cure silicone rubber cures through a chemical reaction that releases small molecules like alcohol or acid. At the beginning of the process, the rubber maintains its flexible state before becoming workable. The material transforms into a resilient protective substance after the completion of its curing process.
Key Features
The curing time of condensation-cure silicones exceeds the duration needed by addition-cure silicones. The delayed reaction period enables better installation adjustments to occur. The manufacturing industry chooses this material because it offers economic advantages. The special curing properties of this material enable it to function in diverse applications.
Applications
The silicone rubber finds regular use in manufacturing applications for creating industrial seals and gaskets. This material offers dependable electrical insulation as one of its main properties. The material finds occasional application in construction and manufacturing activities.
Best Use Cases
Primarily, it suits lower-cost applications. Commonly, it is selected when curing speed is not critical.
Why It’s Important
Ultimately, professionals value its reliability and affordability. Equally, businesses appreciate its industrial versatility. Certainly, ongoing innovation drives continued market interest.
6. Food-Grade Silicone Rubber
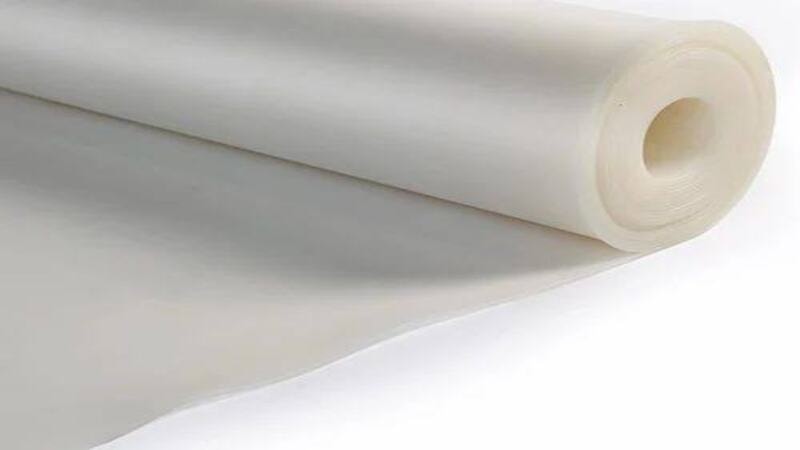
The versatile material known as food-grade silicone rubber serves as a safe contact material for food applications. The formulations undergo rigorous safety testing to fulfill all required standards. Manufacturers test the material to determine chemical composition, and its non-toxicity and confirm its adherence to industry regulations.
Key Features
The material offers two main advantages: Food and Drug Administration certification and immunity to chemical food reactions. The material exhibits innovative heat tolerance which allows it to function in high-temperature environments. The combination of several characteristics including odorless nature and enduring properties creates additional worth.
Applications
This silicone material finds application throughout different industries when making kitchenware and bakeware products. Multiple sectors apply this material in their production of baby-related food storage products too. Food processing equipment manufacturers utilize this silicone material for their operations.
Best Use Cases
The properties of this material provide great advantages to both cooking tools and baking molds. The product range for babies which includes pacifiers and teething rings makes ideal use of this material. The adaptability of this silicone material makes it attractive to retailers for normal household products.
Why It’s Important
Safety remains the top priority for food-related applications. Businesses trust food-grade silicone for its compliance and reliability. Professionals value its consistent performance in demanding environments.
7. Medical-grade silicone Rubber
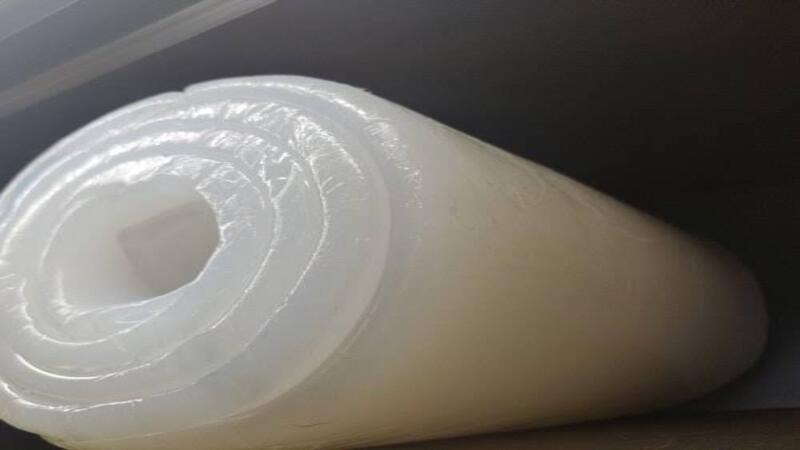
The medical-grade silicone rubber has been engineered to meet strict medical standards. It is chosen because of its biocompatibility and thus safety when it comes into contact with human tissue. Designed to guarantee reliability effectively.
Key Features
It supports sterilization and durability with innovative properties. Remarkable biocompatibility minimizes risk. Advanced non-toxic formulation withstands tough conditions. The use of critical medical devices for excellence consistently is fostered by unique performance.
Applications
In use in implants, catheters, and surgical instruments. They can be used in diagnostic devices and monitoring systems. Applied across hospitals and laboratories. Used in products with care where biocompatibility needs to be precise.
Best Use Cases
Preferred for intricate healthcare solutions, this material supports reliable performance. Selected for surgical implants and medical tubing. Valued in advanced research tools and specialized patient devices universally.
Why It’s Important
Essential for patient safety and regulatory compliance, this silicone rubber guarantees performance. It Prioritizes health with proven sterilization and durability.
The Common Forms of Silicone and Their Uses
Silicone comes in various each tailored for specific applications. Let’s look into those forms:
Silicone Emulsion
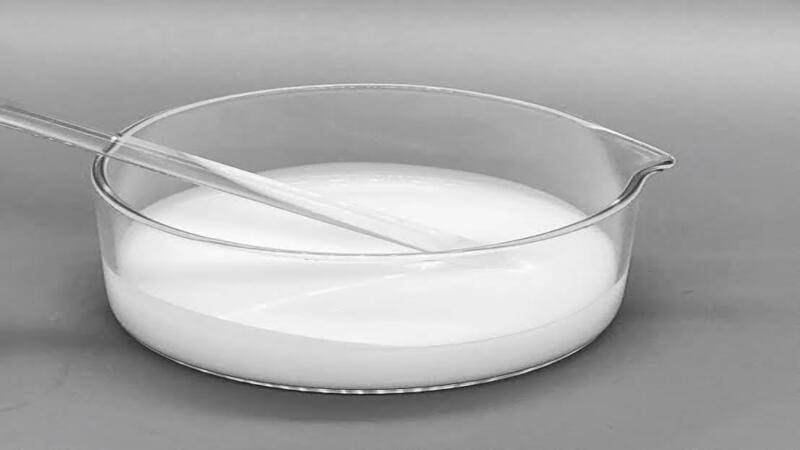
Silicone emulsion is a stable combination of water-based silicone molecules that functions effectively for lubrication release and surface protection. It spreads easily while maintaining a long-lasting effect with simple application methods. This material shows water-based properties alongside non-toxicity and biodegradability which makes it safe for various uses.
Businesses incorporate silicone emulsion into lubricants as well as release agents and cleaning products. The industry strongly favors this product because it offers durability and excellent spreadability features.
Silicone Oil
Silicone oil is made of polysiloxane chains which enable smooth movement between molecules to decrease friction. The substance exhibits low viscosity and maintains heat resistance while delivering exceptional lubricating properties. Hydraulic fluids and lubricants together with silicone-based products rely on silicone oils for their operation.
The material maintains its stability to deliver extended performance under all temperature conditions. Businesses choose silicone oil because it leads to operational efficiency decreased equipment wear and longer equipment lifespan.
Silicone Caulk
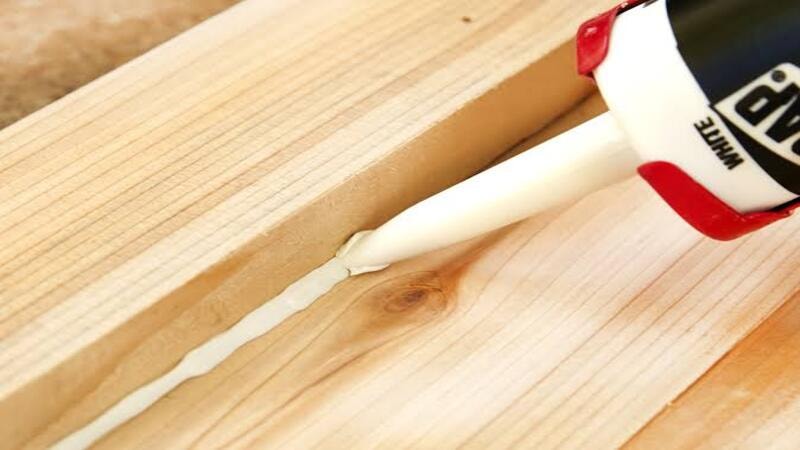
Silicone caulk is an RTV that cures at normal room temperature. It sticks tightly to surfaces while demonstrating moisture resistance together with long-term durability. Multiple industries use silicone caulk for gap-sealing purposes throughout construction projects and plumbing systems and window installations.
This material maintains flexibility which prevents it from breaking during movements. Businesses prefer it for long-lasting, waterproof seals in various applications.
Silicone Resin
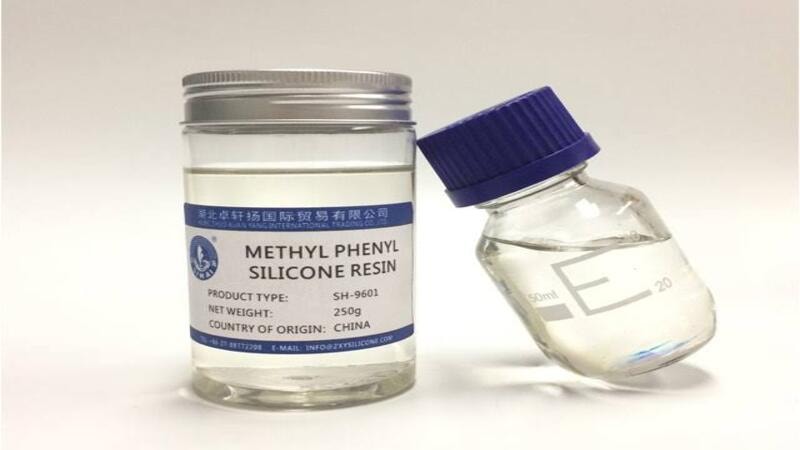
Silicone resins are thermosetting materials that result in powerful cross-linked systems after the curing process. The material demonstrates resistance to high temperatures, chemicals, and electrical currents. Industries use them in adhesives, coatings, and heat-resistant paints. Businesses in automotive, aerospace, and electronics rely on them for long-term performance and safety in demanding environments.
Silicone Grease
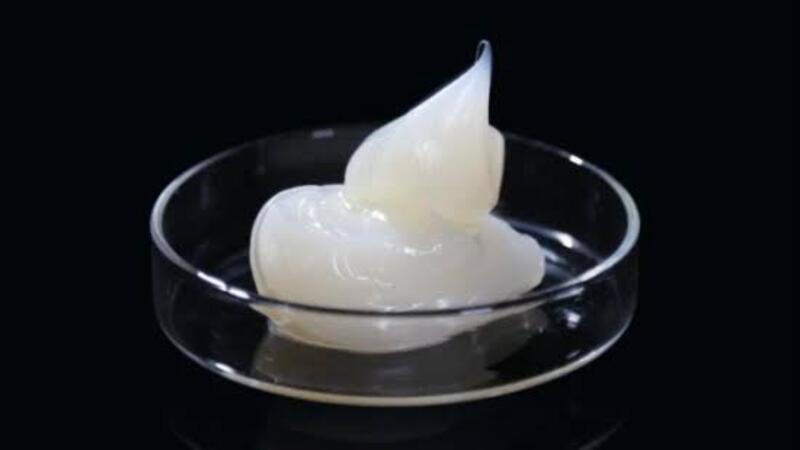
The combination of silicone oil with fillers produces silicone grease which functions as an effective heat-conducting lubricant resistant to moisture. The material demonstrates high durability because it retains stability under high temperatures while resisting water and providing electrical insulation.
The application of silicone grease extends to glass joint sealing electrical contact protection and waterproofing equipment. Tough conditions demand this material because of its proven reliable performance.
Silicone Gel
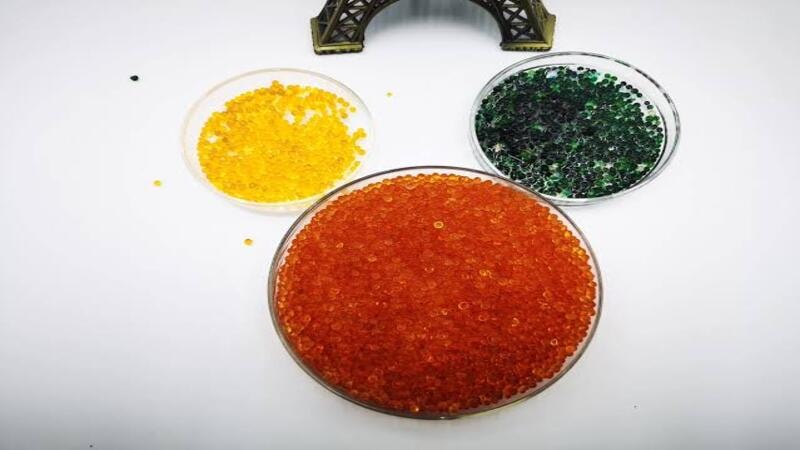
Two-part platinum-catalyzed liquid produces highly adhesive gel which becomes a soft and flexible material. This material demonstrates non-toxic properties while offering shock absorption and excellent surface adaptability.
Medical professionals utilize this gel to treat scars and provide wound care as well as use it to create cushions. Silicone rubber gel stands out as a preferred medical material because of its soft texture which supports safe medical applications while requiring skin-friendly performance.
Silicone Foam
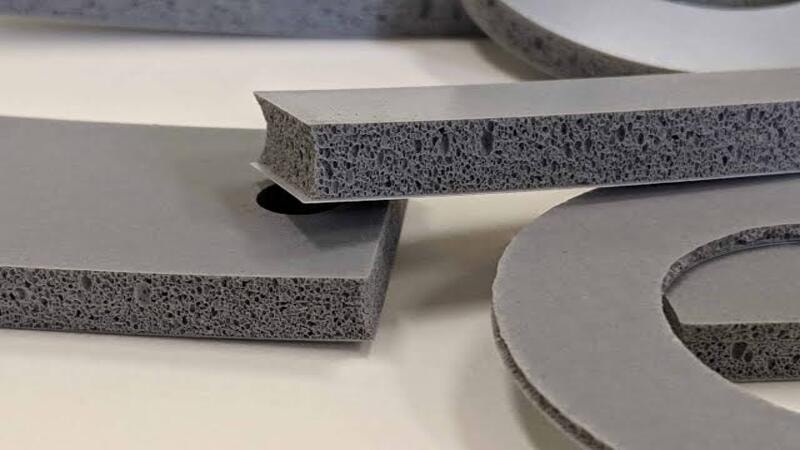
Silicone foam is made through the addition of outgassing agents to liquid silicone which creates lightweight and flexible foam material. It provides protection against weather elements and adapts to a wide range of application needs.
The manufacturing sector applies silicone foam to produce gaskets and spacers together with pipe insulation and other materials. The material stands out in construction packaging and insulation because it demonstrates excellent durability alongside versatility.
Solid Silicone Rubber
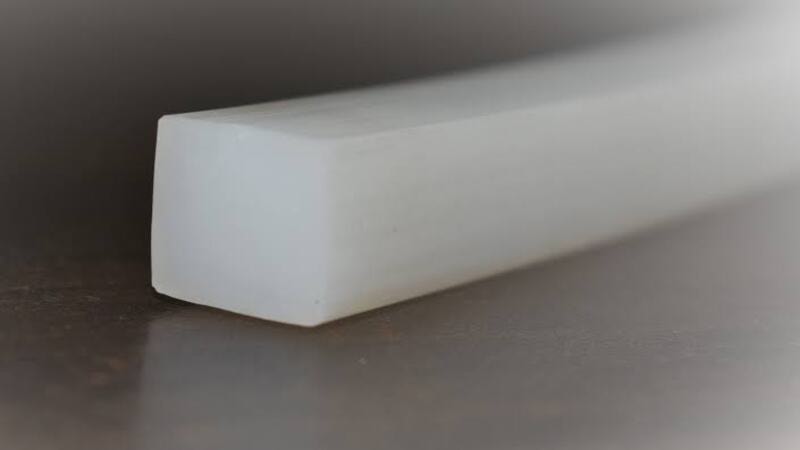
Solid silicone rubber is a high-consistency material that transforms into a durable rubber-like solid after the curing process. The material demonstrates outstanding tensile properties together with strong heat resistance and exceptional wear resistance.
The manufacturing sector implements solid silicone rubber to produce engine mounts in addition to seals and gaskets. The material excels in harsh environments, serving critical functions in automotive and aerospace industries that require durable and reliable components.
Classification of Silicone
Silicones are non-organic elastomeric polymers known for their flexibility and resilience. They withstand UV exposure and degradation exceptionally well, ensuring consistent strength across temperatures. These materials are non-toxic when used correctly.
Silicones can be tailored for various needs, including extra strength, thermal stability, and electrical conductivity. Businesses use silicones for a wide range of applications due to their adaptability and chemical resistance. Their versatility makes them suitable for industries requiring durable, stable materials in different environments.
Silicone Rubber Properties
A blend of silicon, oxygen, hydrogen, and carbon forms silicone rubber, a flexible elastomer made from silicone polymers. It blends rubber’s elasticity with impressive heat and chemical resistance. This material is transparent, but it can be easily pigmented to match various color needs, including skin tones.
Silicone rubber works well across a wide temperature range, from -60°C to +250°C. Its mechanical properties remain stable at room temperature, making it reliable for many industrial and commercial applications.
Advantages and Disadvantages of Silicone Rubber
Advantages of Silicone Rubber:
- It offers exceptional temperature resistance and flexibility.
- Silicone has a low compression set, maintaining its shape.
- Excellent weatherability and UV resistance ensure long-lasting performance.
- Chemical inertness makes it ideal for various industries.
- It has low electrical conductivity, providing safety in electrical applications.
Disadvantages of Silicone Rubber:
- Silicone has poor oil and tear resistance.
- Adhesion can be difficult in some applications.
- Processing silicone rubber can be challenging and complex.
Safety and Environmental Considerations
Silicone compounds are widely used but can impact the environment. Some, like cyclic siloxanes D4 and D5, pollute air and water. Studies show these chemicals harm test animals. Unlike other silicones, cyclic variants do not break down easily. During biodegradation in mammals, they form silanols, which may have further effects.
Businesses using silicone products must consider safer alternatives. Environmental regulations are tightening on cyclic siloxanes. Proper disposal and sustainable choices help reduce risks. Responsible sourcing ensures long-term safety and compliance.
Silicone Rubber in Industry
Silicone rubber is essential in construction for its strength and reliability. To seal gaps, joints, and crevices in structures, one-part silicone sealants and caulks offer a reliable solution. Many professionals use silicone membranes to restore industrial roofs. These membranes resist UV damage and maintain waterproof performance for decades.
What Goes Into Making Silicone Rubber?
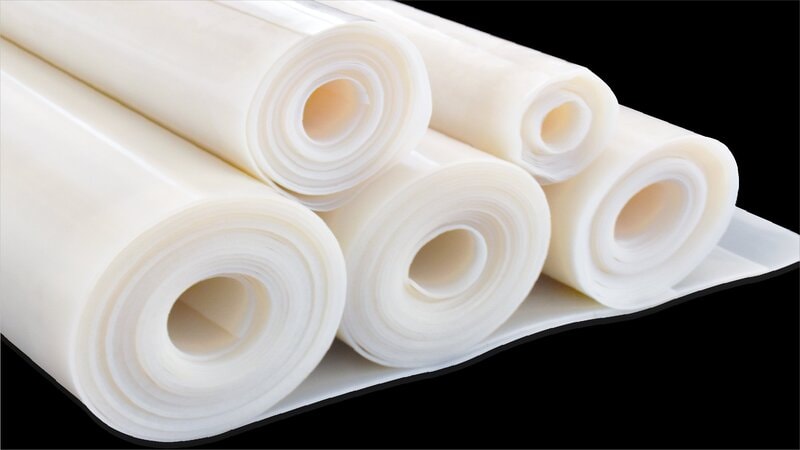
Silicone rubber is crafted through a detailed process. It starts with mixing raw silicone with necessary fillers and additives to achieve a consistent and well-balanced composition. Next, the material is shaped using extrusion, rolling, or molding techniques. After shaping, vulcanization takes place, where a curing agent cross-links the polymer chains for strength and flexibility.
Finally, post-treatment processes like heat stabilization or surface finishing enhance durability. This method ensures high-quality silicone rubber with material properties, widely used in industries like automotive, electronics, and healthcare.
Conclusion
Silicone rubber stands out for its versatility and high-performance qualities. Industries like automotive, aerospace, and healthcare depend on it for high-performance applications. Choosing the right type ensures better results, making it essential to understand its different properties and uses.
Partner with Hongju for a Greener Future – Connect Now!
At Hongju, we have led innovation since 1999. We prioritize quality and sustainability. Our silicone rubber products meet strict safety standards. Start your eco-friendly journey today. Contact us now to make a difference. Need an expert design guide? Click here!