Using the right material for seals can have a major impact on the performance of your machine or parts. But which material is best for you? Is synthetic rubber ideal, or does man-made work better? Knowing that is the tricky part.
All kinds of materials have their advantages and disadvantages. Let’s examine the different rubber gasket materials to see which better suits your intended application.
Factors Influencing Rubber Material Selection
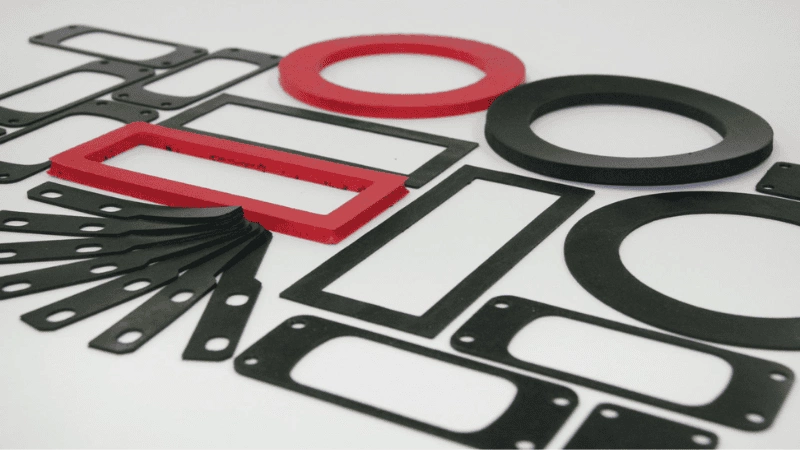
Rubber seal materials are very popular due to their multifunctionality. They can easily be molded, cut, or extruded as needed. Remember that choosing the right gasket material can determine your equipment’s life span, quality, and performance.
Poor quality or unfit rubber seals can break, peel off, and cause other issues. That’s why you need to do your homework before getting in touch with any supplier or rubber materials manufacturer.
So here are some factors you should consider when choosing the material.
- How much will the material or product get exposed to water, oil, and chemicals?
- What are the minimum and maximum operating temperatures of the application you require the seal materials?
- What is the extent of sun exposure to your equipment?
- Is a compression set required?
- What is the cost of the compound?
- Are the operating conditions low-pressure or high-pressure?
- Other environmental factors include UV exposure, etc.
All these aspects will help you narrow down your choice. We’ll explain further with each material below.
Take the First Step:
Requst for an Inquire
Quality Meets Affordability. Inquire Now for High-Quality Products at Low Volumes.
Common Rubber Materials for Seals
After you shortlist the factors most pertinent to your line of business, you’ll be better able to narrow down your options for rubber materials.
Here are some common types you’ll easily find in the markets today.
Nitrile Rubber (NBR)
Nitrile is the most economical and widely preferred sealing material, and It is used in the automotive, marine, aircraft, and military sectors. Gauge its popularity because its annual production is over 36 million metric tons.
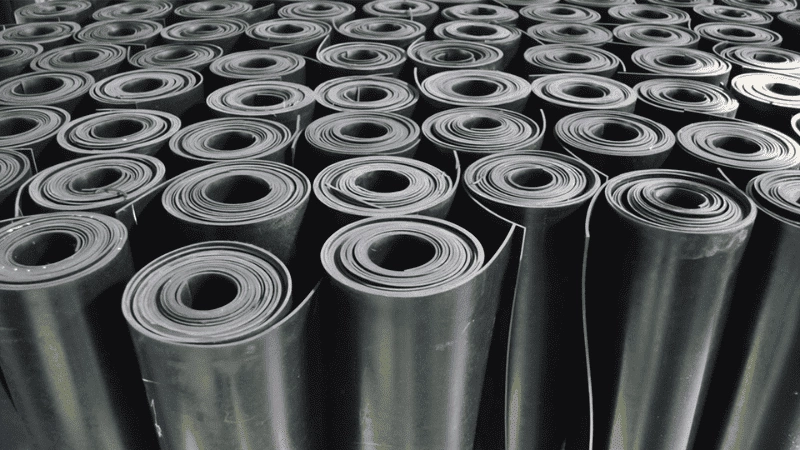
Based on its high resistance and durability, it is used in the automotive, engineering, and industrial sectors, usually in indoor applications. Nitrile-cut gaskets, sealants, o-rings, strips, sheets, etc., are the main products used industry-wide.
Here’s why it is more commonly used than the other types of gasket materials:
- It is resistant to oil, fuel, grease, water, and hydraulic fluid, so it is best for oil and gas applications.
- It has high tensile strength and abrasion resistance.
- It has a low compression set and works under the standard temperature range of -40 degrees Fahrenheit to 257 degrees Fahrenheit.
Also known as Buna-N and NBR, it is best suited for manufacturing rubber products exposed to fuel, oil, or other hydraulic fluids and chemicals.
Pros
- Exceptional Resistance: Nitrile is reliable and used in many industrial sectors. It does not swell or degrade, making it a long-lasting and reliable choice for manufacturing concerns.
- Durable: Nitrile is known for its long life and ability to withstand fuel, oil, and rough applications. It is widely used in conveyor belts and O-rings.
- High-Temperature Applications: It has excellent resistance to oil and fuel and operates well in the temperature range of -40 degrees Celsius to 120 degrees Celsius.
- Compression Set: Gaskets made from Nitrile material can maintain shape and other properties even after prolonged compression.
Cons
- UV Light Damage: Exposure to ultraviolet radiation and ozone can damage nitrile. The product may crack or degrade in the long run, so it’s unsuitable for outdoor applications.
- Not Cost-Effective: For products that do not require rubber resistance to oil and fuel, choosing more affordable economic options like silicone and EPDM is better.
Silicone Rubber
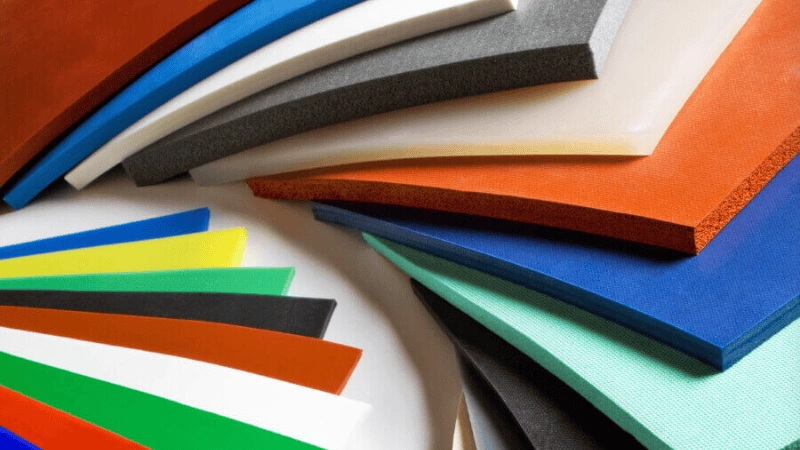
Silicone rubber, mainly used for making sealants, lubricants, and extrusions, is a synthetic polymer made from silicon.
Silicon is heated to 1800 degrees Celsius and treated with methyl chloride to manufacture this raw silicone compound.
You’ll find silicone rubber molded gaskets, die cuts, o-rings, extruded and molded seals, cut strips and sheets, etc., highly resistant to compression and high and low temperatures.
Pros
- Approved by FDA: FDA approval makes silicone rubber ideal for manufacturing products in the medical and food industry. It is non-toxic, biocompatible, and can be used in implants and other medical devices.
- Can Withstand High Heat: Silicone rubber’s ability to withstand high heat makes it an excellent choice for sealing autoclaves. It can withstand high temperatures up to 230 degrees Celsius.
- Flexible Below Freezing: Silicone is best for cold, cryogenic, and harsh environments.
- Resistant to Sun, Ozone, and Weather Conditions: It retains its physical properties and colors in outdoor environments over the long run.
Cons
- Poor Abrasion Resistance: Silicone can tear up when it comes in contact with a sharp object.
- Fuel and Oil Resistance: It is moderately resistant to fuel and oil. Consistent exposure to these under unfavorable circumstances can deteriorate the rubber.
Fluorocarbon Rubber (FKM)
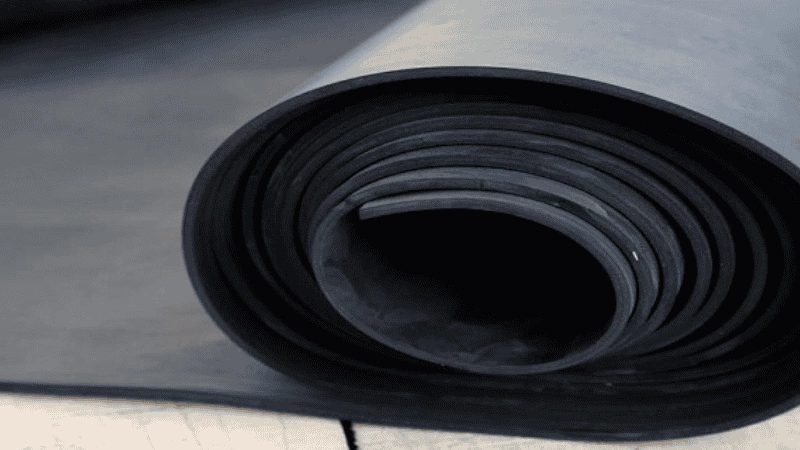
Although more expensive than the other options, Fluorocarbon Rubber or FKM is a high-performing rubber used in seals and o-rings.
The material offers deep resistance against ozone, climate conditions, oxidation, acidic solutions, and other hydrocarbons.
FKM is preferred for highly challenging and demanding industrial applications. It’s the most reliable and lasting material used in commercial-grade applications.
It is also very flexible at extremely low temperatures and is supplied as a sheet or extruded profile.
FKM was initially made for the aerospace industry due to its heat resistance and excellent performance in corrosive environments. Thus, it is the right seal material when temperatures rise to 400 to 600 degrees Fahrenheit.
Pros
- Hydrophobic: It can resist water and offers high resistance against oil and water-based liquids.
- Chemical Resistance: FKM is resistant to chemicals, fuel, oils, and other solvents.
- Low Gas Permeability: Low gas permeability restricts the passing of reactive gasses that may degrade or corrode the material’s structure.
- Good tensile strength: The material has strong tensile strength, so it keeps its shape and functions well under stressful conditions.
Cons
- Expensive: The material is more costly than the other compounds because of the cost of raw materials and the manufacturing process.
- Hard Material: Rubber is comparatively harder than the other materials, so it is not well suited for different applications.
Ethylene Propylene Diene Monomer (EPDM)
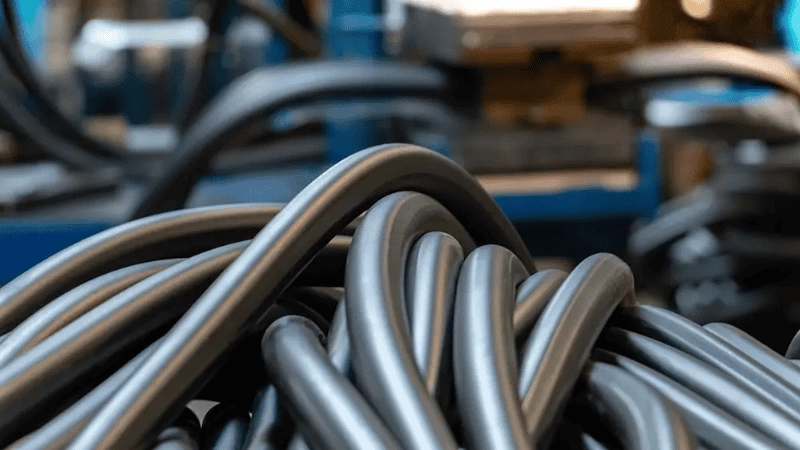
EPDM is the most popular man-made rubber material. The monomer is available in many variants in different densities and hardnesses.
Highly resistant to chemicals, weathering, and ozone, it is widely used across all industries. Being such a versatile material, it has high performance and is suitable for almost all applications, such as gaskets, trims, custom seals, and more.
It’s also a low-cost, mass-produced rubber compound and is best for outdoor applications.
EPDM is manufactured in solid form and extruded form like a gasket and cut-in sheets.
Pros
- Weathering: Because it can withstand exposure to different weather elements, it’s an ideal candidate for use in gaskets, trims, and seals.
- Differing Forms: EPDM can be molded in sponge or solid form, depending on the use, which enhances its application across the industry.
- Impermeable: The material resists water and other water-based compounds, increasing longevity.
Cons
- Low Oil Resistance: Rubber seals are unsuitable for petroleum-based oils and fuels. Constant exposure will cause the rubber to break down and swell.
- Not Suited for Extreme Temperatures: EPDM can only work well in temperature ranges of -40 to 120 degrees Celsius. It’s not ideal for lower freezing temperatures or extreme heat, such as in ovens and freezers.
Neoprene
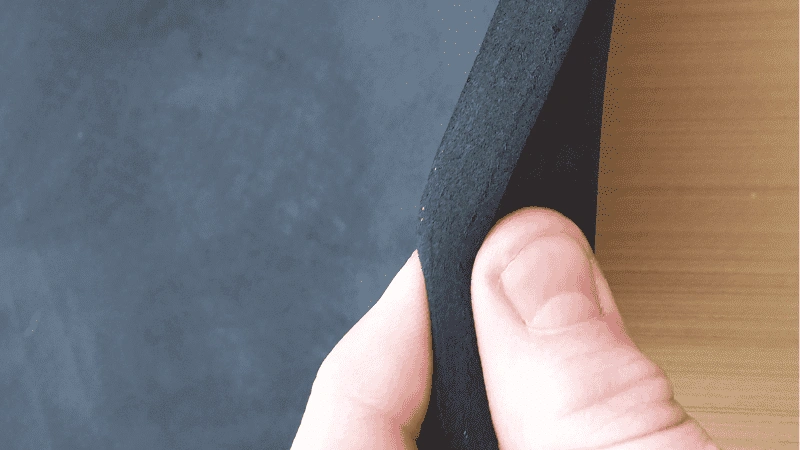
Polychloroprene or Neoprene is another man-made rubber that is useful for manufacturing industry-wide rubber products.
The material also shows high resistance to UV and weathering. It is very tough and abrasion-resistant and works well under extreme temperatures.
The compound is available as solid Neoprene and expanded in different densities.
Pros
- Weathering Properties: Neoprene is ideal for seals, trims, and outdoor applications. It is waterproof and highly resistant to direct sunlight, which makes it a good candidate for marine products and applications.
- Chemical Resistance: Prolonged exposure to chemicals does not degrade or affect Neoprene. It is highly resistant to splashes and oils.
- Resilient Material: Neoprene Rubber seals are also highly durable and abrasion-resistant. The material doesn’t stretch out or get damaged over time.
Cons
- Temperature Resistance: The material is not best suited for freezer cabinets or ovens. Unlike silicone and other materials, it cannot withstand extremely high and low temperatures.
- Chemical Resistance: It may degrade upon constant exposure to strong acids or ketones.
How to Choose the Right Rubber Seal Materials
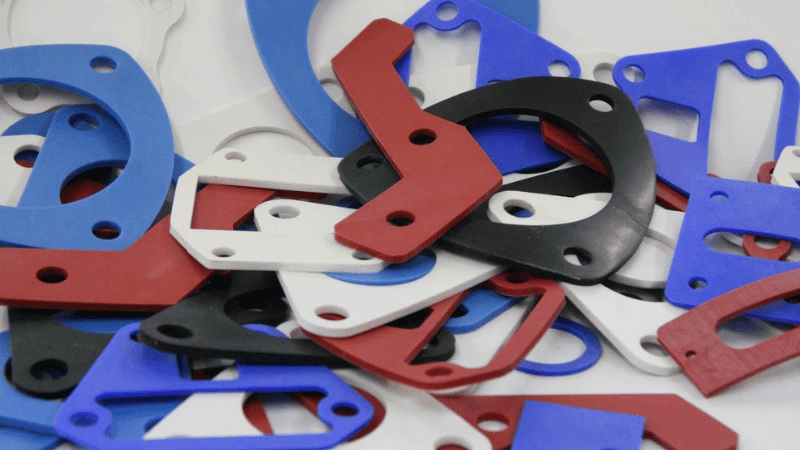
Choosing a suitable rubber material is not as easy as it looks. You need to look into factors like the type of seal you’re looking at, the material, exposure to chemicals, and the hardness required.
However, besides knowing your material, you need expertise and skills to decide which material is best for your applications. That’s why we have professional services like Hongju.
At Hongju, we provide a design guide to help you decide on the material of your products and equipment. Check here to learn more about Hongju and the services we provide.
Take the First Step:
Requst for an Inquire
Quality Meets Affordability. Inquire Now for High-Quality Products at Low Volumes.
Conclusion
The rubber seal industry has grown considerably over the years. With different equipment and heavy-to-light machines, the applicability of seals and gaskets is diverse.
That’s why knowing the right kind of seal products will help you choose the one that best matches your needs.
Why Go To Hongju for Your Rubber Material Seals Needs?
Choosing the wrong sealing material can cost you a lot in the long run. The seal may break, swell, or deteriorate, causing the entire equipment to suffer. That’s where Hongju can help. With over 24 years of experience, Hongju Silicone is the one-stop shop for all kinds of rubber and gasket solutions.
We provide reliable and professional services extending to all industrial sectors and ensure that we meet all our clients’ diverse sealing needs. Our experts work directly with you to assess your requirements and deliver customized solutions that meet your specifications and environmental conditions.
Contact us today to schedule a consultation and to get our complete catalog. We will elevate your product design, performance, and endurance at affordable rates.