The rubber material is quite prone to changes in temperature. However, an increase and decrease in temperature will affect the behavior of rubber in that hot temperatures might denature the rubber while cold temperature causes rigidity.
Temperature Ranges for Rubber Materials
At Hongju, each type of rubber is designed to withstand a specific temperature which, if wrongly chosen, can gradually degrade its material hence deteriorating performance and premature failures.
Specific rubber is required in high-temperature applications or extreme temperatures; below is a detailed table on temperature ranges for different rubber types.
ELASTOMER | LOWEST TEMPERATURE | HIGHEST TEMPERATURE | OTHER PROPERTIES AND ADAPTABILITY |
---|---|---|---|
SILICONE | Low-temperature limit of -60°F to -100°F | High temperatures of +400°F to +460°F | Low mechanical properties such as strength, easy tear, and break are suitable for UV, ozone, and weathering applications. |
CSM (CHLOROSULPHONATED POLYETHYLENE) | The low temperature of -30°F to -40°F | High temperature range of + 135°F to +150°F | 1. Also resistant to chemicals, water, and weathering. 2. They are non-combustible with the ability to self-extinguish. |
FLUOROCARBON - VITON (FKM) | Low-temperature limits of – 15°F to -20°F | High-temperature limits of +400°F to 440°F | 1. They exhibit high mechanical and excellent resistance to ozone, weather, oxygen, hydraulic fluids, and many solvent materials. 2. Can withstand a variety of corrosive and reactive chemicals |
NATRILE RUBBER (NBR) | Low-temperature range of -40°F | High-temperature limit of +275°F | 1. They have moderate resistance to ozone exposure and chemical reactions. 2. They are resilient to petro-chemical fluids such as vegetable oils and gasoline or grease. |
NEOPRENE OR POLYCHLOROPRENE (CR) | Low-temperature range from -30°F to -40°F | The high-temperature range is: +180°F to +200°F | 1. Very resistant to steam and water. 2. They can also combat oil, fuels, greases, and other solvents. |
NATURAL RUBBER / ISOPRENE (NR) | The lowest temperature of -20°F to -70°F | With a high-temperature range of +180°F to +210°F | 1. Very elastic with tensile strength for abrasion resistance. 2. Good with energy absorption emitted from the application and high chemical resistance. |
ETHYLENE PROPYLENE DIENE MONOMERS (EPDM) | Lows of -50°F to -75°F | High-temperature capabilities of +300°F to +340°F | 1. Its materials are generated from oil and natural gas and hence very good with oil resistance. 2. Resistance to weather, ozone exposure, water, and UV. |
Take the First Step:
Requst for an Inquire
Quality Meets Affordability. Inquire Now for High-Quality Products at Low Volumes.
Factors to Consider While Choosing the Right Rubber Material
Choosing the suitable material will always bring out the best performance and the longest efficient life functionality of an application, avoiding any issues that may arise during operation.
Everyone is looking to produce the best and most popular rubber properties, thus a broad scope to choose from and ensure maximum and efficient functionality. Before selecting rubber material or investing, one should consider some of the factors below.
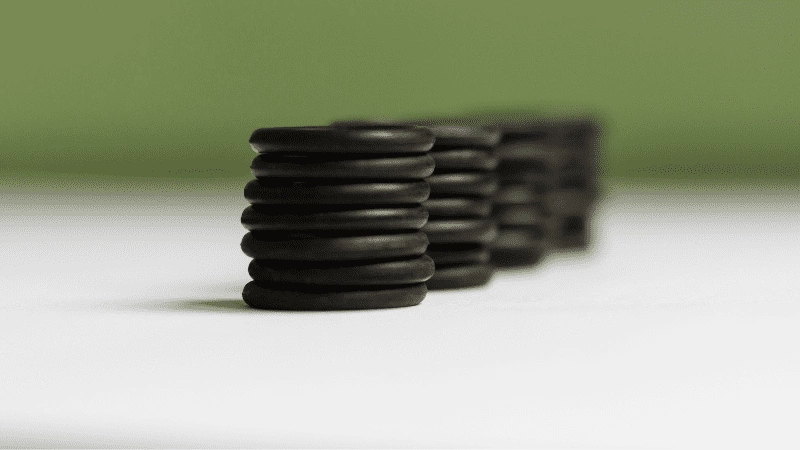
1. Temperature Range
When selecting a rubber product, the temperature range to which your rubber will be uncovered is always crucial. When a rubber’s temperature range exceeds in either direction, the rubber will denature and malfunction.
2. Thickness
The different application systems will always require a certain thickness of rubber. For instance, gaskets and seals always require thick materials to prevent leakage.
On the other hand, thin rubber may be required where application surfaces are required to slide past each other, like in a conveyor belt.
3. UV and Ozone Resistance
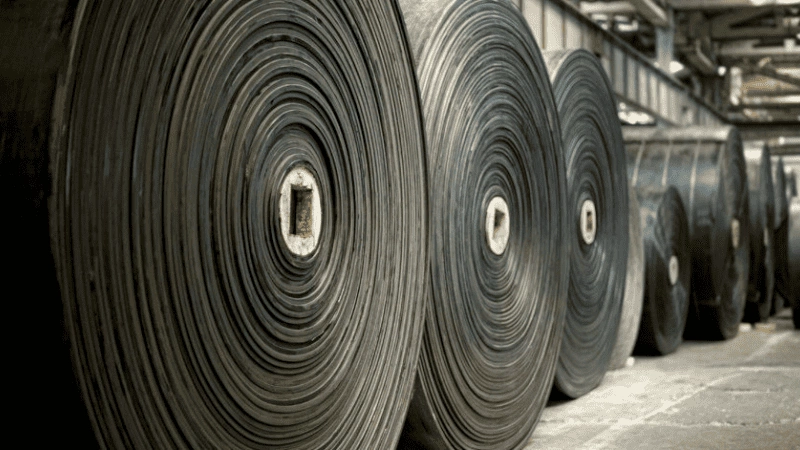
Most rubbers with a double bond to their polymer chain usually tend to break down and experience ozone cracking with stress corrosion.
These polymers don’t do well in environments with UV/ozone exposure. Viton, silicone, or EPDM rubbers are polymers that do well in such environments.
4. Abrasion Resistance
Abrasion is more of physical rubber properties or, instead, the ability of a polymer to resist mechanical strains such as rubbing, scrubbing, or erosion.
Mechanical resistance usually leads to material degradation hence lots of mechanical problems such as leakage due to space creation by erosion.
Applications that usually collide or slide past each other tend to exhibit their tenderness for abrasion effects on rubber. Natural rubber is very resilient to mechanical abrasion.
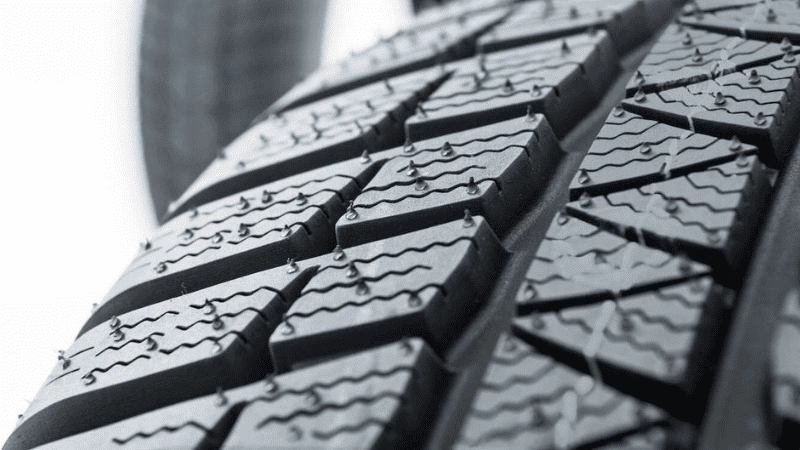
5. Oils and Chemicals Resilience
Nearly all rubbers are attacked or affected by chemical or acidic reactions. Only their endurances and the capability of rubber to withstand such conditions for a long time differ.
If a polymer in your intended application will be exposed to many acidic and chemical reactions, it’s best to always seek more help from an expert at Hongju. Viton rubber usually shows high chemical resistance to attacks.
Oil resistance is usually rarely considered, but under a required circumstance, Nitrile rubber is always the best in an oily environment.
6. Hardness
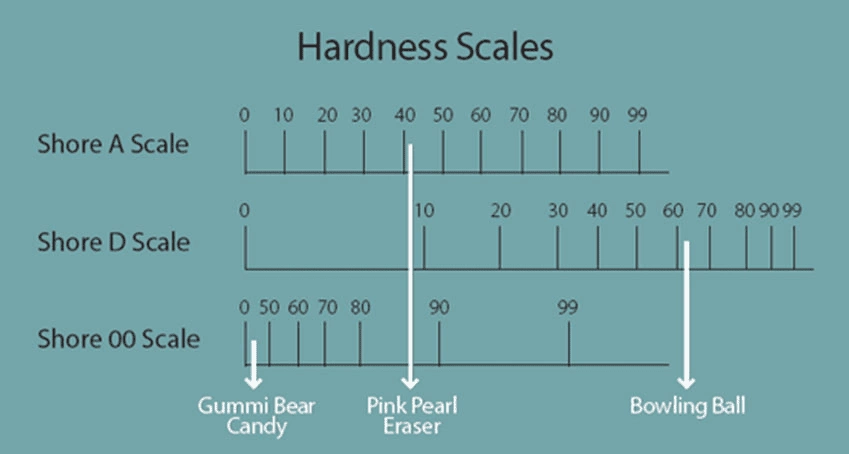
This is typical resistance to indentation measured by a Shore Durometer. Hardness usually affects the compression and pressure exhibited or exerted on an application.
Silicone rubber is malleable to produce different degrees of hardness, of which it achieves the highest of them all.
Natural rubber is not recommended where hard rubber is required. Hardness and abrasion resistance differ because abrasion corrodes, while hardness favors shape and insertion.
Take the First Step:
Requst for an Inquire
Quality Meets Affordability. Inquire Now for High-Quality Products at Low Volumes.
The Benefits of Using Rubber in Temperature-Sensitive Environments
Both synthetic and natural rubber exhibit a broad temperature range (low and high temperature) in that a slight temperature change will not affect the behavior, efficiency, or application setup.
Most polymers are exposed to a wide range of temperatures during production hence sustainability.
Precise and rapid changes in temperature in their application system will continually improve the structure of the materials, which provides optimum surface quality of a rubber product.
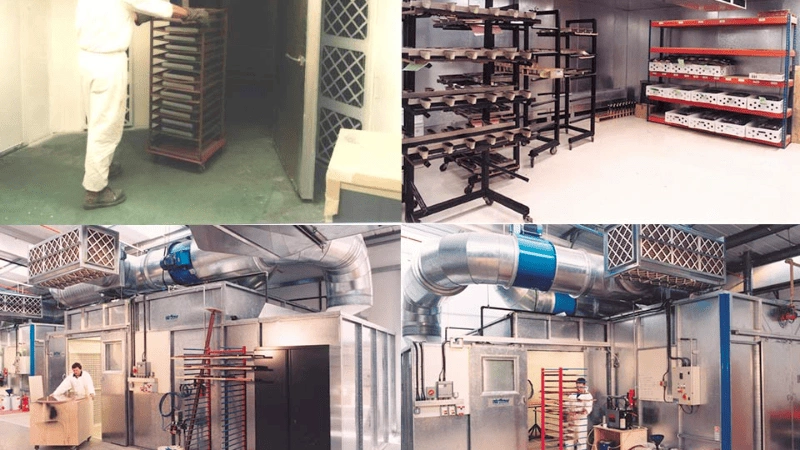
In a liquid high heat transfer application, rubber plays a significant role in the simultaneous removal and delivery of high temperature and deficiency in a system.
The high temperature will always increase rubber’s flexibility, thus intact cohesion with their application devices, which ensures durability and efficiency altogether.
Self-extinguishing synthetic rubber is always idle for temperature-sensitive environments since the chance of a fire outburst is minimal. Most polymers don’t easily combine with oxygen nor react with it, becoming less combustible.
Precautions to Take When Working With Rubber Materials
Rubber materials may resist many dangerous factors, making them inert and very docile in their position.
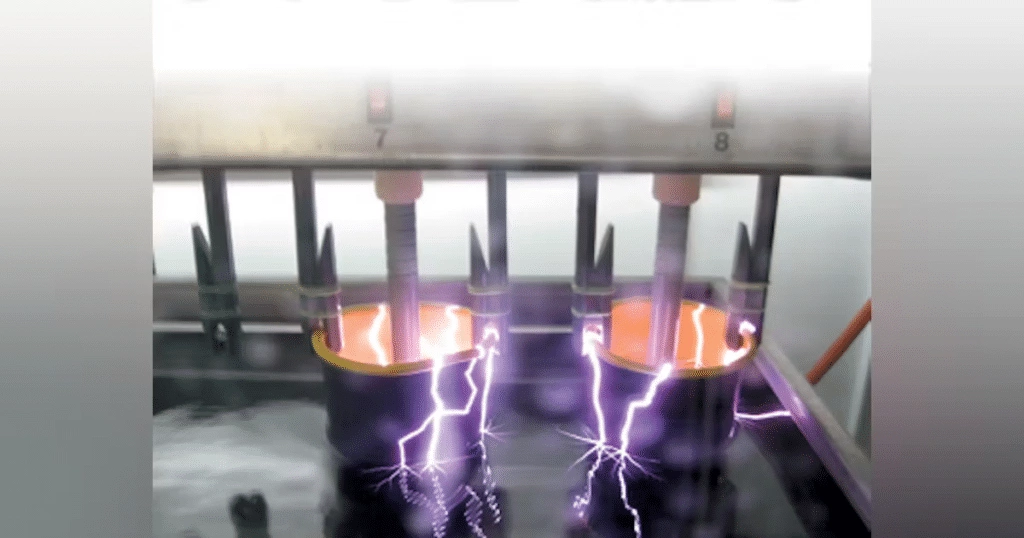
But with their excellent resistance or resilience comes dangerous output or contaminating their entire environments surrounding it, thus very harmful to humans.
One must always be cautious while handling rubber in that:
- Always wear a face mask to prevent inhalation of harmful substances reacting or emitting from rubber cloth or other material due to the workload exerted on it.
- Always wear hand gloves since a rubber may seem inert or rather cold, but in another sense, it is pretty hot for bare human hands.
- Getting suitable rubber for the job regarding the conditions the rubber will be subjected to is vital, and failure to do that may lead to unforeseen accidents.
- Popular Rubber materials are prone to malfunction; hence it’s cautious enough to always check the condition and state of the rubber before putting it to work.
- Always consult with an expert, especially during rubber installation, to prevent any miscalculation and improper installation, which may lead to accidents.
Tips for Maintaining Your Rubber Products Over Time
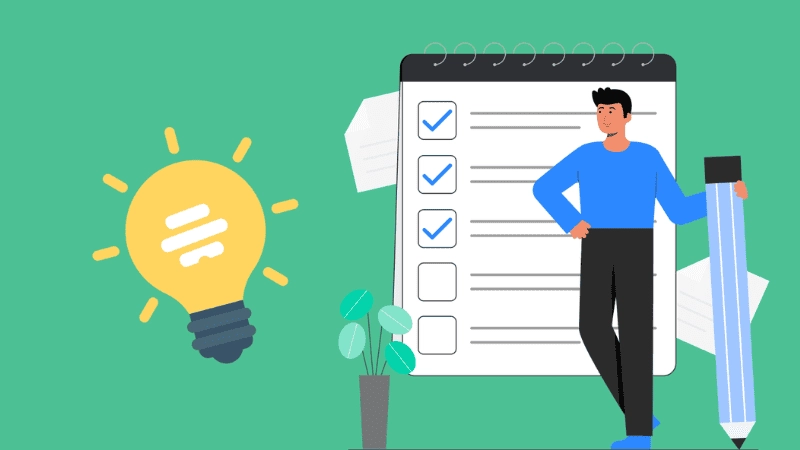
Most rubber products are very longevity and docile in appearance but prone to gradual degradation and tear.
Rubber may work efficiently during the day or at room temperature but creates a leakage during nights or cold hours, which may cause mechanical failure or accidents in the long run.
At Hongju, we give you the best tips for maintaining synthetic and natural rubber products and application devices for a sustainable future.
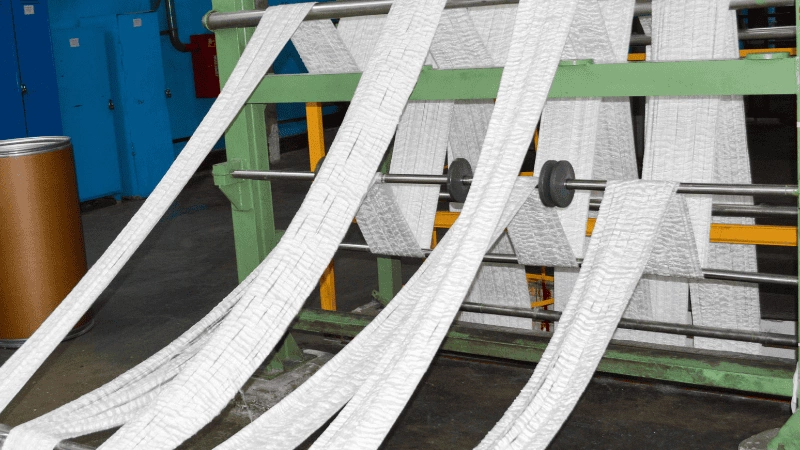
To withstand low-temperature or high-temperature environments, you must choose rubber materials accordingly with excellent resistance.
- Always ensure to check your rubber seals and gaskets regularly, especially ones that are deep installed in the system.
- Ensuring that you get the right product suitable to its duty and conditions subjected to is always wise and maintains your entire rubber ecosystem
- Research on new products available in the market will always come in handy if you want to achieve maximum output at all times.
- Maintaining the entire application system is always essential to ensure a normal workload is exerted on the rubber product to prevent explosions or leakage due to application malfunction.
Take the First Step:
Requst for an Inquire
Quality Meets Affordability. Inquire Now for High-Quality Products at Low Volumes.
Conclusion
Rubber products have different properties, and all behave differently when subjected to conditions that mainly identify the right rubber product to use.
Every day Hongju tries to find a new style of synthetic and natural rubber that can at least increase efficiency by a small inch. With this, the demand for quality rubber is always on the rise, making innovations in the rubber field very productive.
Get Quality Synthetic and Natural Rubber Material at Hongju
Quality speaks at Hongju for all your polymer needs and other rubber products you may need. Contact us today regarding any product inquiry or research. Our technical experts are always available for your assistance.