This guide will discuss whether you need silicone or neoprene rubber. We will compare both and evaluate their individual properties. You’ll make a more informed decision about which one to use.
What is Silicone?
Silicone is a highly inert synthetic oil-resistant elastomer, typically rubber-like, and has decent heat resistance.
It can resist extreme temperatures up to 300 degrees Celsius. It can also withstand extreme temperatures below -55 degrees Celsius.
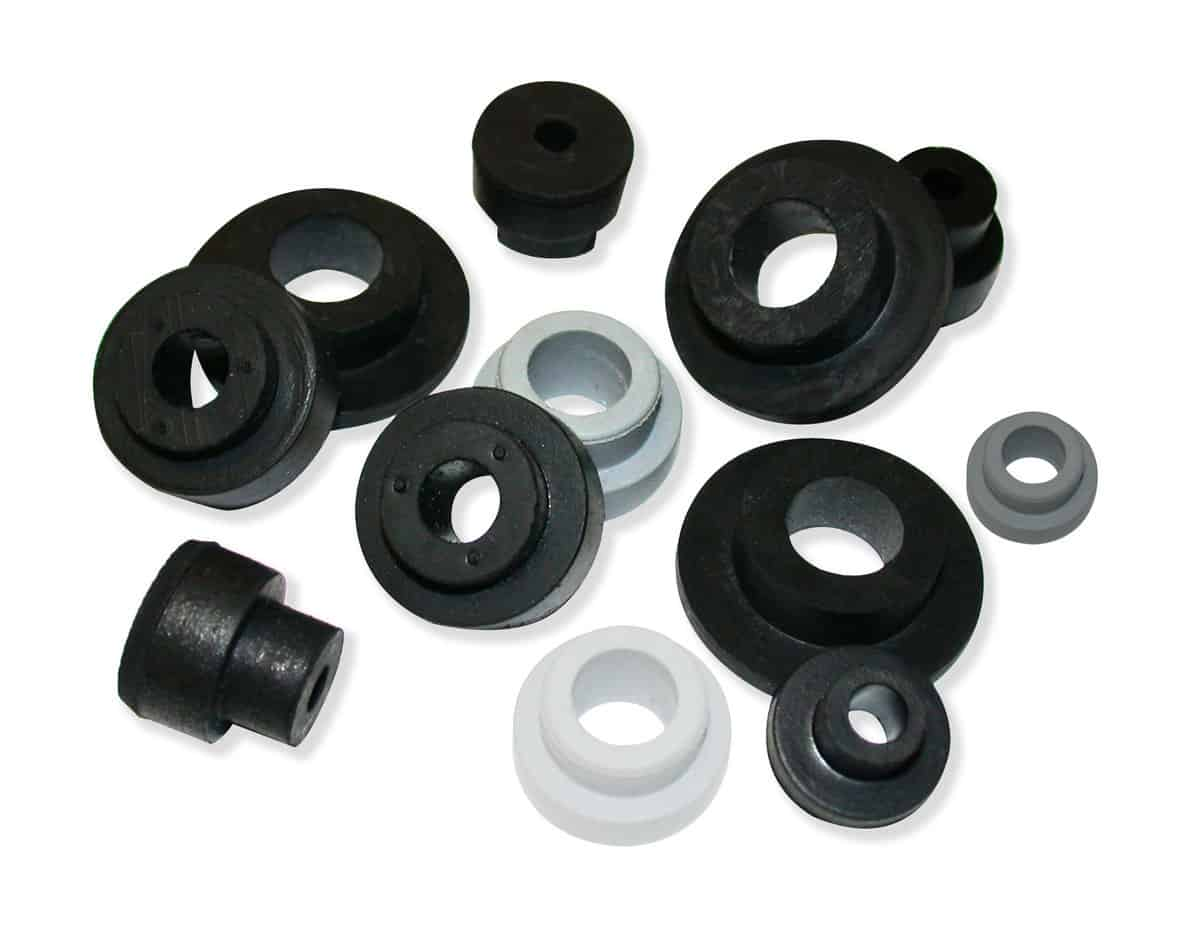
Its main properties include an excellent electrical insulator, thermal stability, and fire-resistant characteristics. Because it is a soft compressible material with a fair compression set, silicone is ideal for various sealing applications.
Note that silicone lacks chemical resistance, particularly oils. Also, silicone’s heat resistance might be a huge advantage, but its poor tear strength limits its application.
Finally, it would help to remember that silicone and silicon don’t mean the same thing. The latter is applied in solar cells and semiconductors.
What is Neoprene?
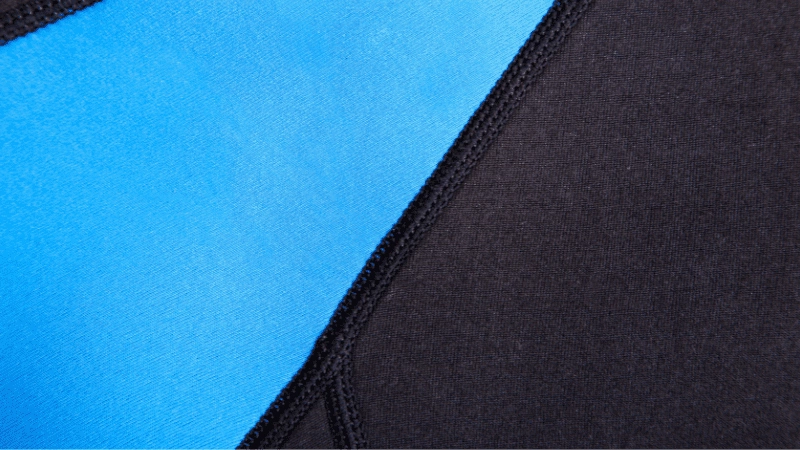
Neoprene is particularly an ideal gasoline-resistant material. It also has good resistance to sunlight, oxidation, and ozone. It has excellent air and water-tight sealing properties.
Its scope of use is broader because of its oil resistance. It is the first synthetic oil-resistant elastomer in the world.
Some places to use neoprene sponge rubber sheets include marine environments, shock or noise absorption, closure seals, weather strips, and construction and electronics industries.
Send your inquiry for prompt quotations!
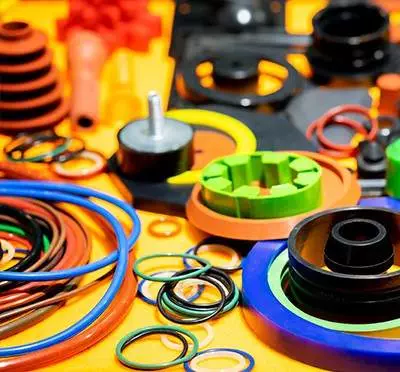
How is Neoprene Different From Silicone?
The significant difference between neoprene rubber and silicone is that the latter can withstand extreme temperatures but isn’t oil-resistant like the former.
While neoprene rubber is moisture-resistant, it can’t be used in applications requiring high-temperature resistance.
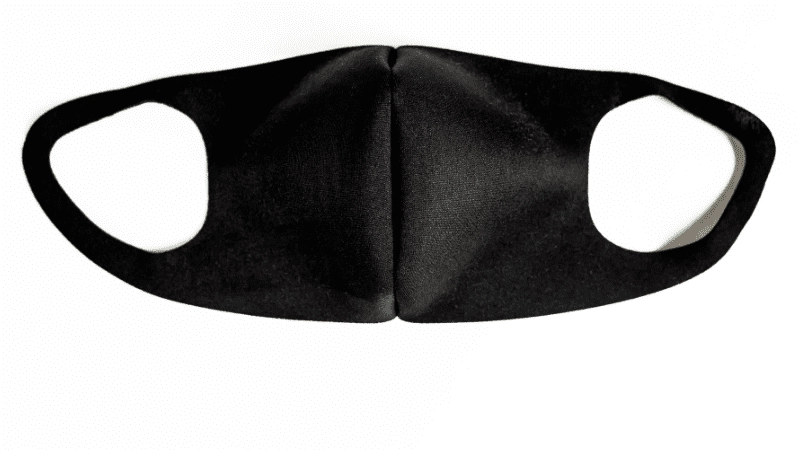
Neoprene and silicone have distinct advantages and disadvantages, which we will cover in the subsequent section of this guide.
But that’s even the reason you need to consult a professional in this field when deciding between the two for your industrial applications.
A few instances can utilize either neoprene or silicone. But that said, other instances only require one of the two. This is the point you need to weigh both silicone and neoprene based on the following factors:
- The manufacturing procedure.
- Durability.
- Temperature range and requirements.
- Resistance.
The Manufacturing Procedure
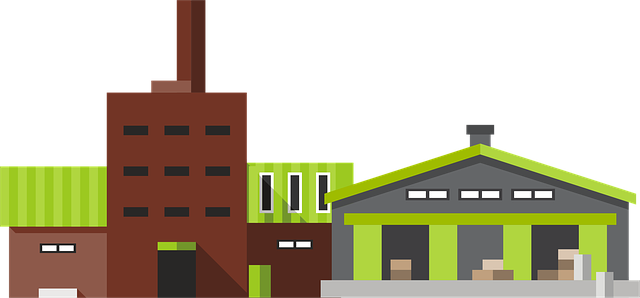
When choosing a material for a manufacturing procedure, there are specific properties to look at.
Both silicone and neoprene can be adjusted in plenty of ways to suit different needs in the manufacturing process. One can extrude, use injection molding, and die-cut silicone and neoprene.
The availability of silicone and neoprene in other densities is another massive advantage that they possess. This is particularly important for applications that need less noise and vibration. Hence, both silicone and neoprene can be in lightweight forms.
Durability
As for toughness and long lifespan, silicone and neoprene pass; they have a high tensile strength and are flexible.
Neoprene has a maximum elongation of 600% and a tensile strength of between 500 and 3,000 P.S.I. On the other hand, silicone has an ultimate extension of 700% and a tensile strength of between 200 and 1,500 P.S.I.
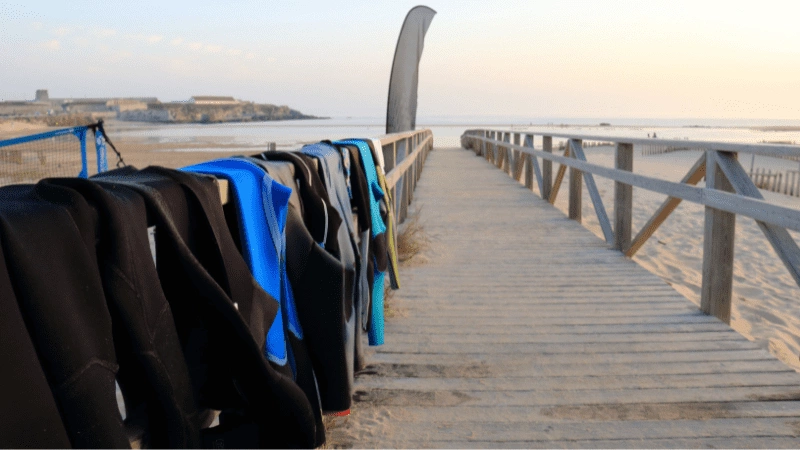
For rebound and compressible materials, neoprene sheeting comes on top of silicone. But this doesn’t mean that silicone performs dismally in these properties.
The tear and abrasion resistance splits silicone and neoprene about durability and toughness. Neoprene rubber is more tear-resistant and has excellent abrasion resistance compared to a silicone sponge sheet.
Therefore, it is right to claim that neoprene rubber has better resistance to damage caused by flexing and twisting.
Silicone has poor tear strength and abrasion resistance. Thus, silicone may not be ideal in applications involving a lot of rough contacts and tearing.
Temperature Range and Requirements
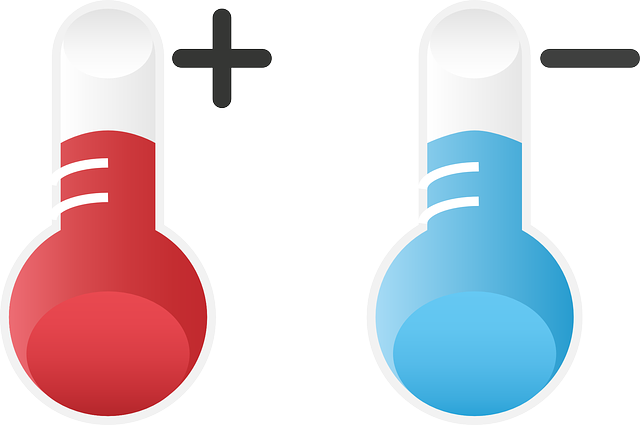
You could argue that silicone rubber isn’t so great with chemical resistance. Nonetheless, it performs exceptionally in withstanding extreme temperatures. This wide temperature range of resistance covers both hot and cold environmental factors.
Some silicone compounds can operate effortlessly in long-term high temperatures of even 392 degrees Fahrenheit. Its ability to withstand low and even higher temperatures makes silicone rubber an effective solution in dynamic applications.
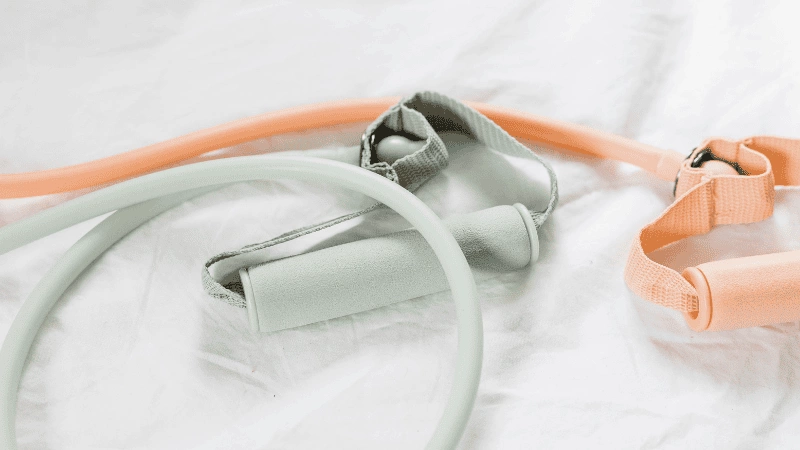
In addition to withstanding extreme temperatures, silicone rubber also exhibits fire-resistant characteristics. This makes it a perfect material for electronics industries, automotive applications, and aerospace industries.
It’s essential to keep in mind, though, that at high temperatures, silicone rubber becomes more rigid.
Neoprene rubber doesn’t possess the same resistance to different temperature range settings. It has a low-temperature range of between 10 and 50 degrees Fahrenheit.
It can not withstand extreme temperatures since its limit is 250 degrees Fahrenheit. As the temperature goes down, neoprene rubber becomes stiffer. The similarity here between neoprene and silicone is that either exhibits fire-resistant characteristics.
Resistance
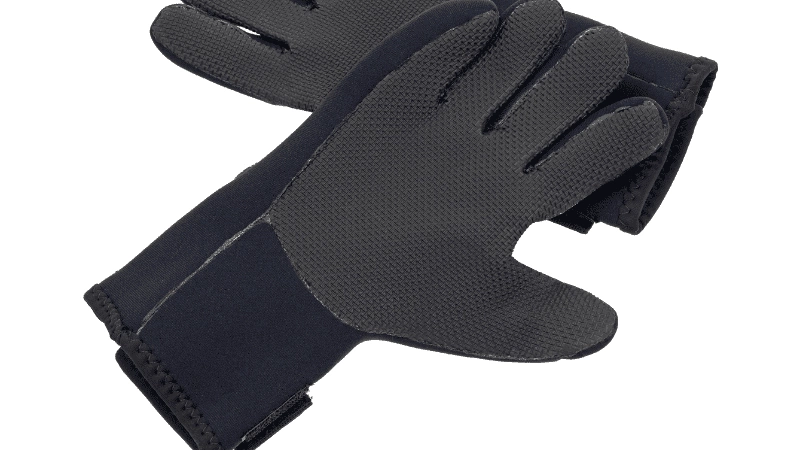
Environmental factors always dictate the correct material selection. Resistance, for instance, is a vital characteristic to look out for in different materials for industrial use.
Neoprene rubber came to the limelight as an oil-resistant alternative to natural rubber. Thus, it is an ideal material for particularly oils.
It is resistant to chemicals. Hence, it is suitable for greases, solvents, mineral acids, salt solutions, and methyl and ethyl alcohols.
Silicone rubber doesn’t perform as well as neoprene rubber when resisting oils and solvents. It can go as much as swelling and failing when used alongside petroleum products and oils. Neoprene rubber is, therefore, a preferred option here.
Weather resistance and aging are the only resistances that match neoprene and silicone. Both materials do well under intensive sunlight, which makes them an excellent pick for outdoor applications.
Send your inquiry for prompt quotations!
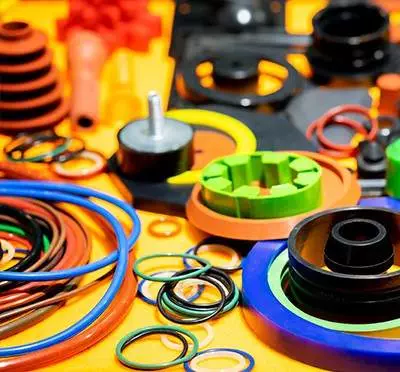
Pros and Cons of Each Material
Having looked at the above factors, we can come up with several pros and cons of silicone and neoprene. This will help you not to choose the wrong material for your applications. Let’s look at the pros and cons of each material independently.
Silicone
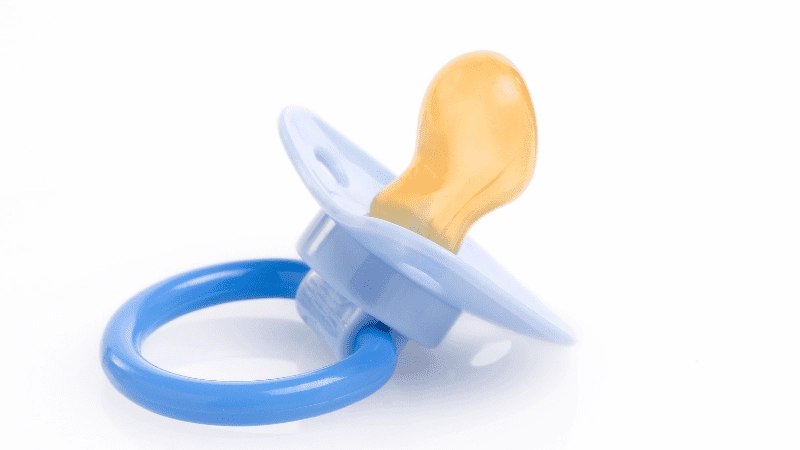
Pros
- It is non-reactive and stable.
- It can withstand a broader range of temperatures.
- Appropriate for hygienic applications and uses.
- It is a versatile rubber.
- Wide range of industrial applications, including construction and electronics industries.
- Durable.
- Thermal stability.
- Excellent electrical insulator.
- It is fire-resistant.
- Highly inert.
Cons
- Premium price tag or expensive compared to forms of synthetic rubber materials.
- Poor tear strength.
Neoprene
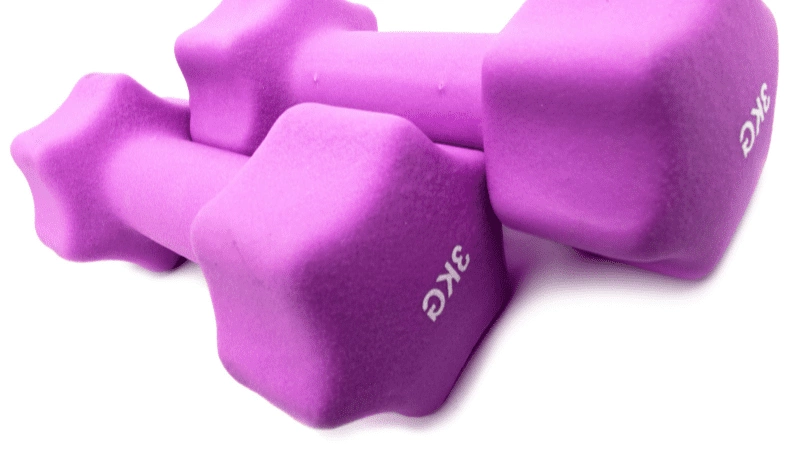
Pros
- It has water-tight sealing properties.
- Durable.
- Highly resistant to chemicals such as oils and petroleum products.
- It is a versatile rubber.
- Neoprene products have excellent resistance to weather, UV light, and ozone.
- Good in resisting moisture.
- Ideal for dynamic applications, including marine environments.
cons
- Not compatible with hydrocarbon fuels or ketones.
- Not resistant to strong acids or esters.
Send your inquiry for prompt quotations!
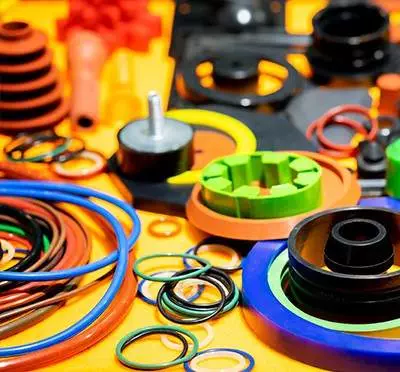
Examples of Projects that Would Rely on Silicone and Neoprene
Depending on the specific project, silicone or neoprene products will serve appropriately.
Here are some of the projects or applications that would require the physical properties of silicone:
- Aerospace.
- Automotive applications such as the case of rubber seals.
- In the creation of o-rings.
- Making silicone gaskets.
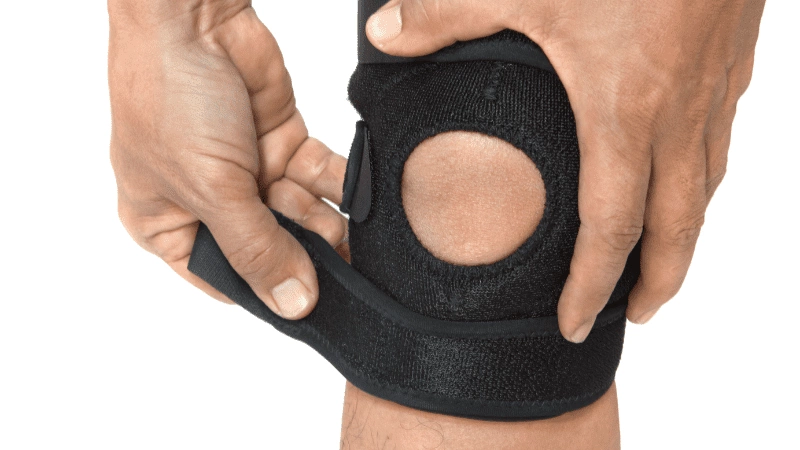
On the flip side, neoprene specializes in the following projects or applications:
- Marine environments.
- Making of reliable neoprene gaskets.
- Making closure seals.
- Creation of oil-resistant rubber seals.
- They create o rings.
- For weather strips.
- Construction and electronics industries.
Silicone vs. Neoprene – Which One is Better for You?
We have carefully analyzed the physical properties of silicone and neoprene. But now comes the tricky part of choosing between the two. The above factors can help decide on which semi-organic synthetic material to choose.
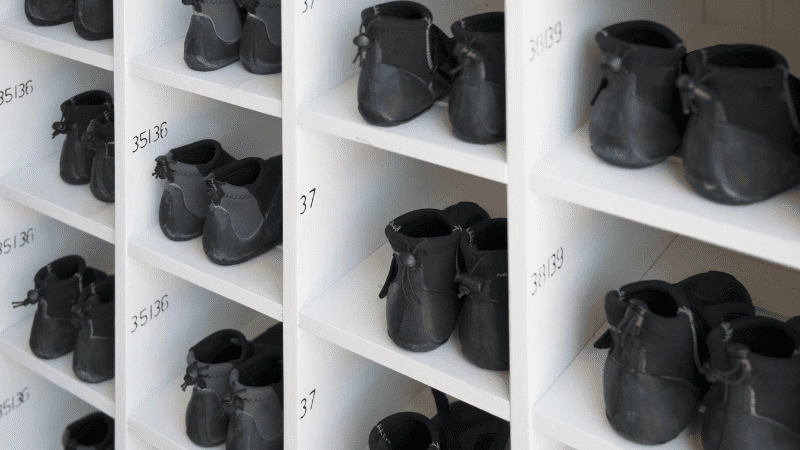
The final choice of suitable semi-organic synthetic material comes down to specific requirements for the project. Are you looking for rubber materials that can withstand high heat?
Or are you looking for synthetic rubber that can withstand chemicals such as oils? Are you looking for a compressible material with a good compression set? Is dry heat resistance a factor you’re considering? What about resisting moisture?
These are some of the factors to consider when making a decisive choice between silicone and neoprene. For instance, while silicone has good resistance to dry heat, neoprene specializes in withstanding chemicals, particularly oils.
Again, there are specific applications, such as brake fluids, where silicone and neoprene can be used. Fortunately, you don’t have to make this decision alone. We at Hongju have the right experience to share with you.
Send your inquiry for prompt quotations!
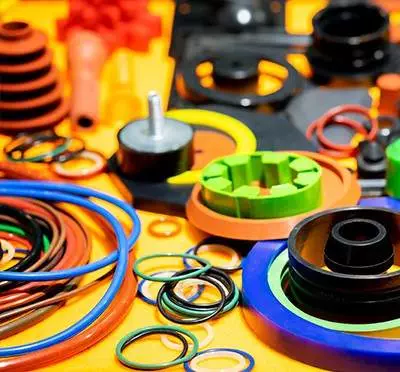
Conclusion
We hope this guide has helped you understand more about silicone and neoprene. Getting a partner who sources materials from a natural rubber tree or top-quality synthetic options is essential.
We know that you’re always searching for quality, which is why we pay a lot of attention to giving you just that.
Contact Hongju for Silicone and Neoprene Products
You will get a specialized experience here at Hongju. Our experience has led us to interact with different clients. This has helped us to understand that clientele needs are unique.
Our experts will help you to customize your neoprene and silicone products depending on your intended applications. Come and contact us quickly!