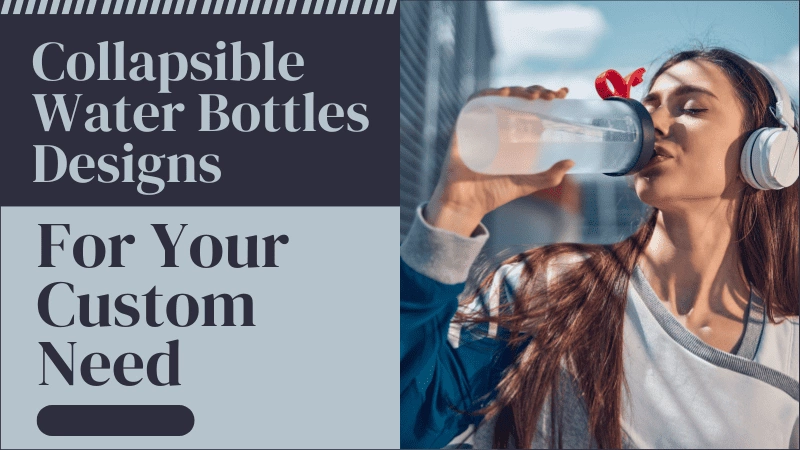
8 Best Collapsible Water Bottles Designs For Your Custom Need
Collapsible water bottles have become the calling card for anyone who’s all about that active, healthy lifestyle. Unlike regular, rigid bottles, collapsible bottles use designs and materials that deform easily. This makes them lighter and more compact, thus perfect for taking on the go.