This article offers a deep dive into what compression deflection is, how it’s measured, and its significance in design specifications.
We’ll compare it with a compression set to illustrate its importance in practical applications. Perfect for engineers, designers, and material experts, this piece aims to enhance your understanding and guide you in making informed material choices.
Let’s embark on a journey to demystify compression deflection and its pivotal role in your design toolbox.
Understanding Compression Deflection
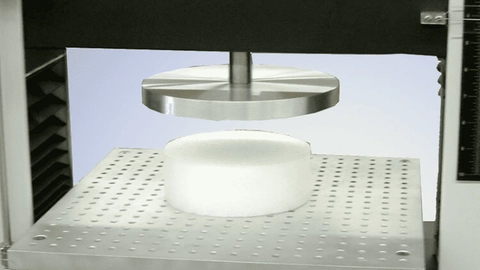
Compression deflection is a measure of a material’s resistance when subjected to compressive forces. It quantifies the force required to compress a material by a specified percentage of its thickness, indicating how a material will cope with the strain and maintain its shape when loaded.
This parameter is typically recorded in pounds per square inch (psi) or kilopascals (kPa), providing a standard to compare the firmness and flexibility across various materials.
Mechanical Perspective
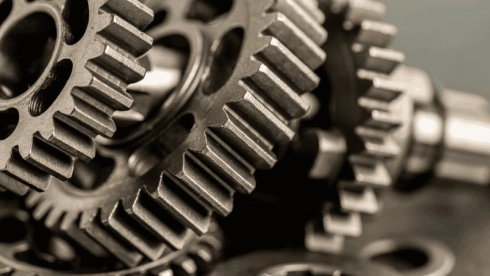
From a mechanical standpoint, compression deflection relates to how a material deforms under a compressive load. It considers the material’s modulus of elasticity—often referred to simply as ‘modulus’—which reflects the material’s stiffness or rigidity.
The higher the modulus, the less it will deform, and consequently, the higher the compression deflection value will be. Engineers use this as a baseline to predict how materials will perform in real-world applications.
Material Behavior Under Load
The behavior of materials under load can vary significantly. Elastomeric materials, like silicone and urethane, have different compression deflection characteristics compared to cellular materials, such as foams and sponges.
Elastomers tend to resist compression and bounce back more readily, while cellular materials may exhibit more deformation and less recovery. The actual response will depend on the material’s intrinsic properties, including its durometer (hardness), structure (whether it is solid or cellular), and composition.
Understanding these responses is paramount when selecting materials for gaskets, seals, and cushioning applications, where maintaining a seal or providing consistent support is critical.
Measurement of Compression Deflection
The measurement of compression deflection requires precise testing to ensure accurate and repeatable results. It involves standardized methods like those outlined in ASTM D1056, which specifies procedures for testing the compressive properties of flexible cellular materials (rubber or plastic foams).
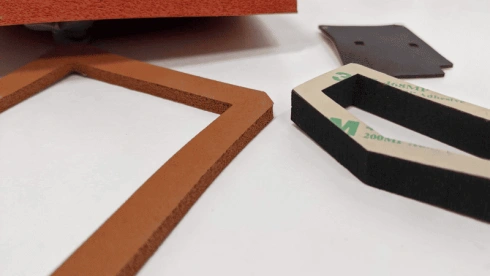
Factors Affecting Measurements
There are several factors to consider when measuring compression deflection to ensure the accuracy of the test:
- Sample Preparation: The dimensions and preparation of the sample can affect the results. It’s essential to adhere to the specifications of the testing standard.
- Temperature: Materials can behave differently at various temperatures. Tests are often conducted at room temperature, but other temperatures may be used to simulate operational environments.
- Rate of Loading: The speed at which the load is applied can influence the material’s response. The testing standard typically defines the rate to ensure consistency.
- Thickness: The original thickness of the material can impact the compression deflection value. Thicker samples may have different deflection values than thinner ones under the same force.
- Aging and Conditioning: The history of the material, including any aging or conditioning processes it has been through, can change its properties and thus the compression deflection.
By meticulously controlling these factors, manufacturers and designers can better understand the performance characteristics of materials and how they will function in real-world applications.
This understanding is critical when the material must meet specific functional and compliance requirements.
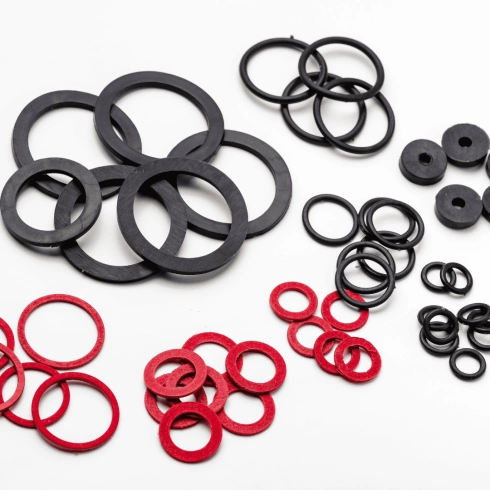
Send Your Inquiry Now!
Quality Meets Affordability. Inquire Now for High-Quality Products at Low Volumes.
The Role of Compression Deflection in Design
Compression deflection plays a crucial role in determining the functionality and durability of various products. It refers to the ability of a material to withstand pressure or compression without permanently deforming or losing its shape.
Let’s explore how compression deflection influences design choices and product performance.
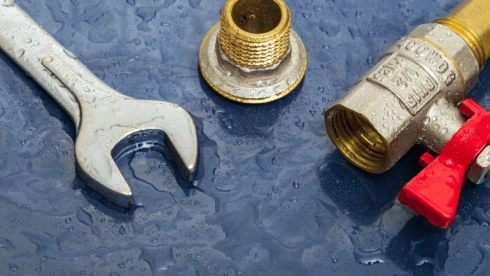
Influence on Product Functionality and Durability
Compression deflection is a vital consideration when designing products that require sealing, such as gaskets. Gaskets are used to create a tight seal between two surfaces, preventing leakage of fluids or gases.
The compression deflection properties of the gasket material directly impact its ability to maintain an effective seal under pressure.
When subjected to compressive forces, materials with higher compression deflection values can resist deformation better than those with lower values.
This ensures that the gasket maintains its integrity, even when compressed between two surfaces. As a result, it provides reliable sealing and enhances overall product functionality.
Selecting Materials Based on Compression Properties
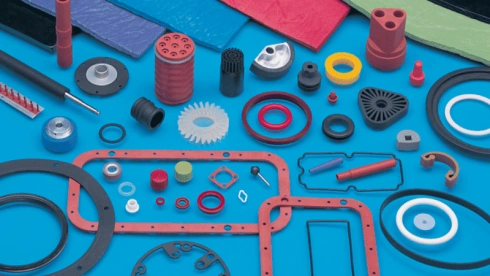
Designers must carefully select materials based on their desired compression deflection properties for specific applications. Different materials exhibit varying levels of resistance to compression, allowing designers to choose one that best suits their requirements.
Some factors to consider when selecting materials include the intended application, operating conditions (temperature, pressure), and desired level of compression resistance.
For example, if designing a gasket for high-pressure environments, materials with high compression deflection values would be preferable.
Critical Applications Requiring Compression Deflection
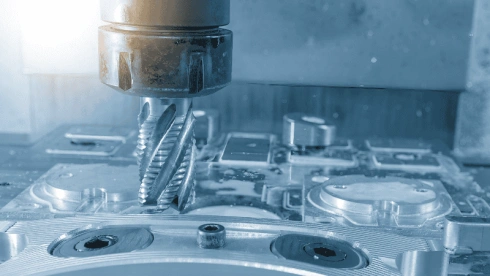
Compression deflection is critical in numerous design applications beyond gaskets. Here are some examples:
- Automotive industry: Sealing components like O-rings and engine gaskets rely on proper compression deflection for optimal performance.
- Aerospace industry: Aircraft seals and insulation materials must have excellent compression resistance due to extreme temperature variations.
- Medical devices: Sealing components in medical devices need reliable compression deflection properties for maintaining sterilization barriers.
When designing products that incorporate elastomeric components, understanding the distinction between compression deflection and compression set is crucial for ensuring long-term performance and reliability.
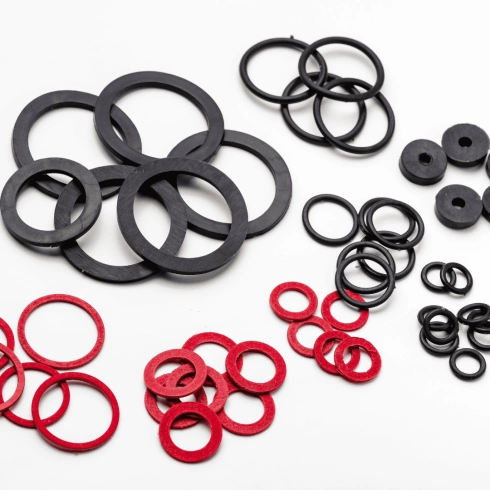
Send Your Inquiry Now!
Quality Meets Affordability. Inquire Now for High-Quality Products at Low Volumes.
Compression Set VS. Compression Deflection
Compression Deflection Defined: As previously described, compression deflection measures the force required to compress a material by a certain percentage of its thickness.
It gives an indication of the material’s stiffness and the load it can support before deforming.
Compression Set Explained: Compression set, on the other hand, is a measure of the permanent deformation of a material after it has been compressed for a specified time and then allowed to recover.
This is an important parameter when evaluating a material’s suitability for sealing applications, as it indicates the ability of a material to return to its original thickness and maintain an effective seal over its service life.
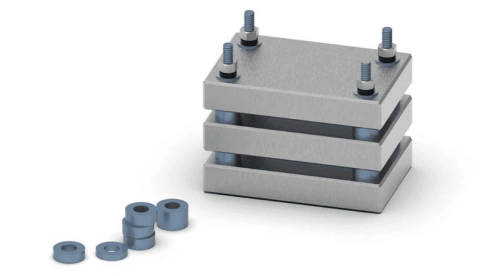
Key Differences
The measure of Elasticity vs. Permanent Deformation:
- Compression deflection is concerned with how a material temporarily deforms under a load and is a measure of its elasticity.
- The compression set measures the degree to which a material fails to return to its original shape (permanent deformation) once the load is removed.
Impact on Design:
- Products requiring a specific resistance to compression forces rely on the compression deflection value for design specifications.
- The compression set value is critical when the application requires the material to maintain a seal or specific shape over time, especially after being under compression.
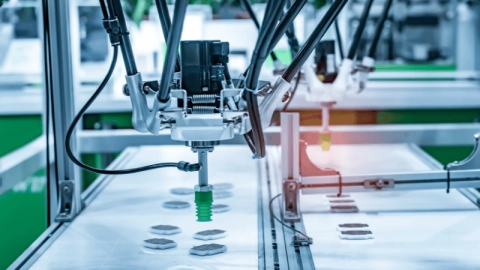
Testing Conditions:
- Compression deflection tests are performed by applying a force to a material and measuring the displacement.
- Compression set tests require the material to be compressed at a defined percentage of its thickness for a set time, often at elevated temperatures before being allowed to recover.
Performance Over Time:
- Compression deflection gives immediate feedback on material performance under load but does not indicate how the material will behave over an extended period or after repeated compressions.
- The compression set provides insight into the long-term durability of the material and its ability to perform consistently after repeated use.
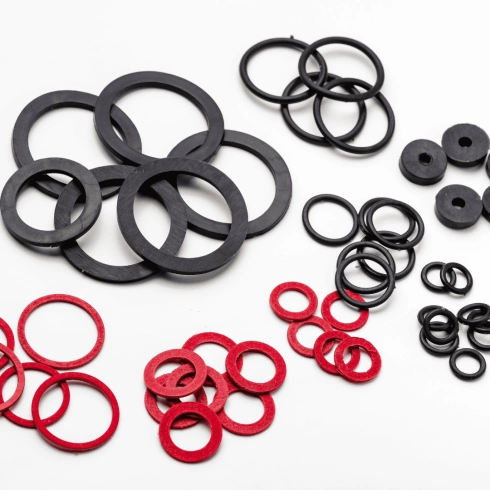
Send Your Inquiry Now!
Quality Meets Affordability. Inquire Now for High-Quality Products at Low Volumes.
Conclusion
Understanding the nuances of compression deflection and compression set is crucial in material selection for durability and performance.
While compression deflection assesses material stiffness and load-bearing capacity, compression set reveals its ability to retain shape and function over time.
Both are key to ensuring that products perform as expected throughout their lifecycle, making them essential considerations for designers and engineers in creating reliable and lasting applications.
Maximize Durability with Hongju Silicone’s Expertise
For durability under pressure, compression deflection is key. Hongju Silicone delivers expertly crafted materials designed for peak performance, ensuring your products withstand the rigors of use. Trust us to enhance your offerings with resilient silicone solutions. contact us now!