What is Compression Molding?
Compression molding compresses raw plastic into a heated mold with the final product’s shape. The combination of heat and pressure makes it possible for the plastic to form a new shape by filling out the space inside the mold.
Usually, the mold has two parts, the upper and lower half. The upper mold is movable, while the lower one is stationary. During production, the raw plastic is put on the heated lower mold. The equally heated upper mold is then put on top of the plastic, exerting enough pressure to get the plastic into the right form.
The mold stays together long enough to ensure that the heat and pressure will enable the plastic to maintain the integrity of the shape as it forms. This is the curing process.
Once everything cools, the upper mold lifts to reveal the new form of the plastic. This is when the new plastic product is removed from the mold.
Pros and Cons of Compression Molding
There are many reasons why you should use compression molding.
First of all, the process it follows makes it easier to apply color changeovers. It can also preserve the materials’ mechanical or chemical properties.
This method is also cost-efficient. The simple process allows it to create inexpensive plastic components with ease and high efficiency. This also allows it to develop products regardless of length, thickness, and design complexities.
Since the process also requires the use of material that exhibits a high level of strength, the final product has the same durability and resiliency.
Of course, this molding method isn’t perfect. There are drawbacks to using it. One of them is it’s not ideal for large productions. The final product may be less consistent – if the pressure on the mold varies even slightly.
And because the mold has two parts, there’s a chance that the final product will have an odd line in the middle.
Different Applications of Compression Molding
Compression molding can be optimal for creating durable plastic products. Most of the time, this method is excellent for appliance and automotive parts.
The typical applications include the following:
- Body armor
- Circuit breakers
- Clothing fasteners
- Electrical switchgear/components
- Plastic dinnerware
- Stove knobs
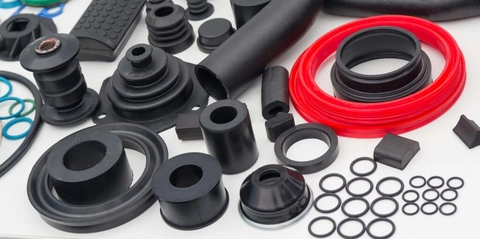
What is Injection Molding?
Injection molding is a process that involves injecting the raw material into the cavity of a mold. The raw material starts from a feeder hopper with a screw below it. This screw rotates and takes the material from the hopper into the mold. A heating process happens simultaneously as the screw injects the material into the mold. This makes the fabric soft enough to take the shape of the cavity.
The tool has various parts, including the feed hopper, injection unit, heater, hydraulic cylinders, clamping unit, etc.
This molding method makes it possible to create more complex and intricate designs. Since an injection process happens, producing a more consistent end product is more accessible. There’s more accuracy when it comes to meeting the design requirements.
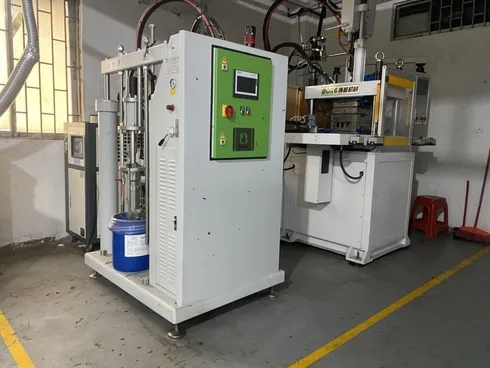
Pros and Cons of Injection Molding
Injection molding is perfect for products that require an intricate design. Not only that, but it’s also ideal if you want to produce a high volume. The simple process of injection makes it more cost-efficient for mass production purposes. The more product you produce, the more the cost per part can drop.
This is also the most versatile because creating a mold with different styles, shapes, and sizes is easy. If you want to customize mildew, the manufacturer must reshape the mold. You can have them add resins or other additives to create the design you want.
This very reliable molding process can result in a strong and durable product. This can even tolerate different types of materials.
While all these benefits are incredible, there are still some drawbacks. The cost of tools can be prohibitive. This is why it’s not ideal for low-volume production. You have to use it to create more products to maximize the cost of creating that one mold or tool.
Different Applications of Injection Molding
Thanks to the versatility of injection molding, it’s possible to use it in various applications. Whether it’s a small product or a very intricate design, it’s easier to accomplish using this molding method.
The different applications for injection molding include:
- Aerospace components
- Automotive parts
- Avionics products
- Cable assemblies
- Elements for windows and doors
- Dental and medical products
- Engineering prototypes
- Healthcare laboratory components
- Packaging for food and beverages
- Point of purchase (POP) display parts
How are Compression and Injection Molding Similar?
Even if the process of molding is different, there are similarities between compression and injection molding. Both use molding tools to shape the raw materials into the right design. They both use heat to help make the material flexible enough to take the shape of the design. They also use cooling methods to make the final product durable and sturdy.
But beyond that, here are other notable similarities.
Allows Customized Colors
Customizing the colors is easy for both compression and injection molding methods. You must blend the color you want into the raw plastic resin before feeding it into the mold.
This allows you to create an incredibly colorful, aesthetically pleasing product. Manufacturers usually have these ready colors to mix for you. This can be through dry pigment mixing, where plastic resins mix with dry pigment powder. This mixture happens in the hopper.
There’s also the option of solvent coloring. This is a mixture of pigment oil with solvent. You spray this over pellets with no color. This coating happens before the injection.
Has Low Labor Costs
Another similarity between compression molding and injection molding is the low labor cost. Since the process is very straightforward, very little manual intervention happens. The operator of the molds only needs a basic understanding of the process to get this done.
It’s done in automation, so there’s no need to get too much labor.
Cheaper Cost of Parts
Creating the rubber molding with the design of the product is one that changes every time. But for the rest of the tools, it remains the same. This is why the parts are very cost-efficient. Even if the molds use low-cost materials like steel, they can still be very effective in creating the right shape. Not to mention that you can reuse the molds, which usually last a long time.
What makes Compression and Injection Molding Different?
There are several considerations when it comes to differentiating the two molding methods. The main difference is in the process that they both follow. In compression molding, the top half of the mold compresses the raw material into the lower half of the mold to create the right shape. In injection molding, a screw injects the raw material into the mold cavity to create the end product.
Beyond this, there are other differences to consider so you’ll know what to choose between the two.
Precision
The die for injection molding uses durable materials with high strength and hardening capabilities. That means there’s a lower chance of deformity in the final product.
This isn’t true for compression molding. The pressure of the upper mold can affect the shape and final design of the product.
Model Complexity
Complex models are more applicable to the injection molding method. It’s easier to manipulate the mold and make it as intricate as possible. This also allows you to test how the design will look – and make changes when necessary.
Compression molding is better for simpler designs without a lot of intricacies.
Lead Time
Compression molding takes longer to complete. This is why you must ensure you give it enough time to produce the number of products as promised.
Injection molding can be faster – this method allows time to test prototypes and make revisions when needed.
Compression Molding and Injection Molding: How to Choose?
Choosing between compression molding and injection molding will depend on the product’s application and the ideal completion time.
For some, injection molding has the advantage over compression molding because it allows intricate designs and the creation of prototypes. However, compression molding still has its benefits. The straightforward process can be ideal for some production requirements.
Make sure you talk to your manufacturer and give them the complete details of what you want to produce. That way, they can give you the options available to get the best result.
Buy Custom Molded Silicone Rubber Products from Hongju
As one of China’s leading custom silicone rubber products manufacturers, Hongju is dedicated to providing value to our customers. Our main products include custom silicone rubber keypads, rubber O-rings, gaskets and seals, rubber feet, etc.
Check out our services:
- Silicone Rubber Compression Molding
- Liquid Silicone Rubber (LSR) Injection Molding
- Silicone Rubber Die Cutting
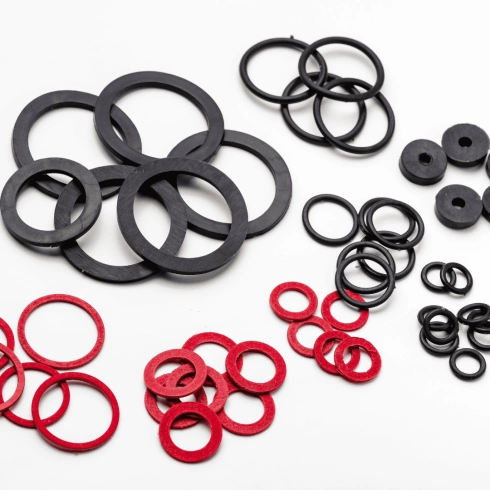
Send Your Inquiry Now!
Quality Meets Affordability. Inquire Now for High-Quality Products at Low Volumes.