What is Rubber Compression Molding Process?
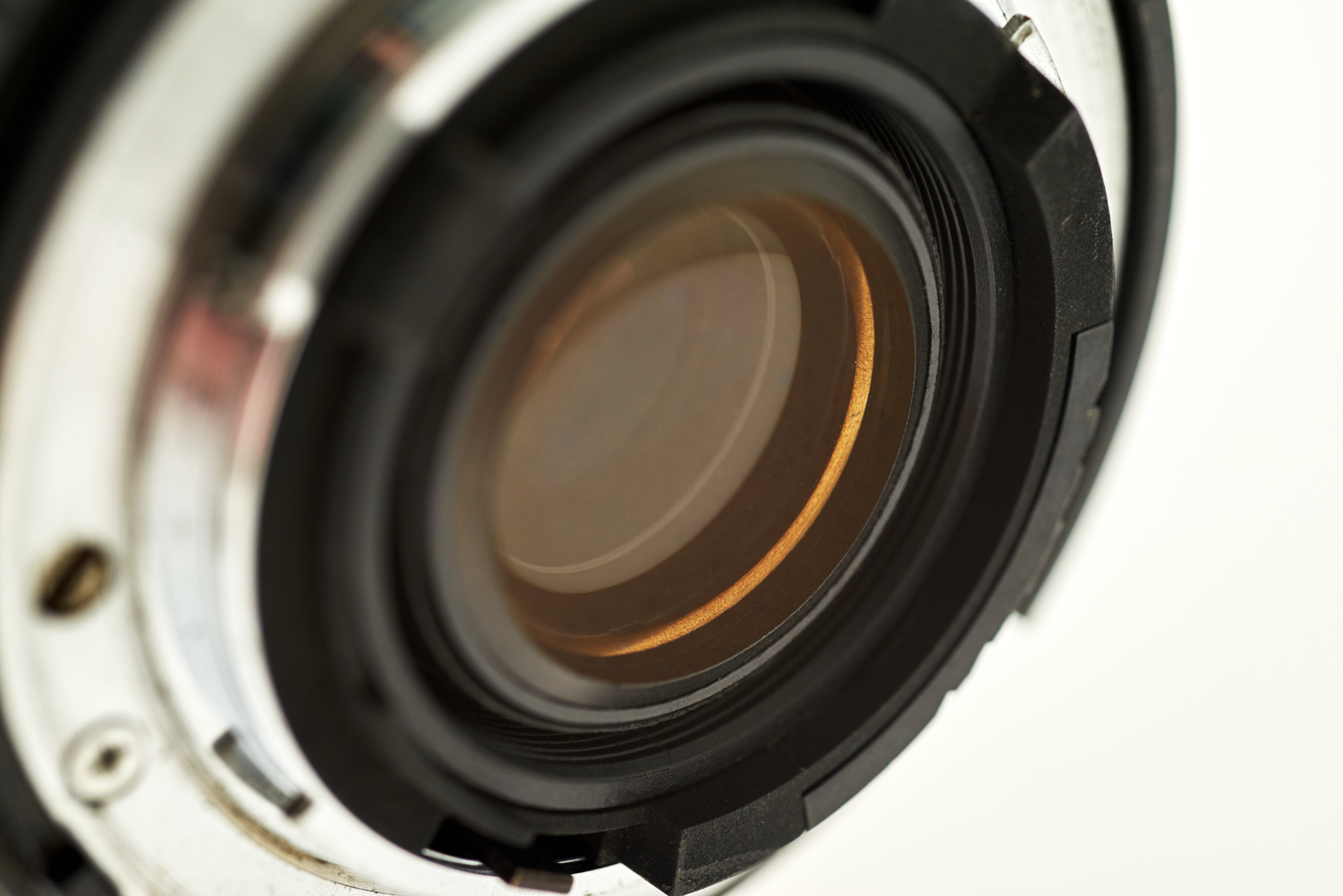
Rubber compression molding makes rubber parts by pushing raw rubber pre-forms into a sturdy mold by applying high pressure. Heat is applied once the raw rubber is inside the mold cavity until the rubber cures into the final shape.
Compression molding is a relatively low-cost and quick means of producing large parts. It is a famous rubber molding process used for low to medium-volume productions.
What is a Pre Formed Material?
A Pre-form is an uncured rubber material that is rough cut to match the shape of the final product. The pre-shaping of the material reduces the total force required for compression molding and helps with mold filling.
Without pre-forms, you would need to apply a ridiculous amount of force to push the uncured rubber into the corners and edges of the mold cavities.
What is Curing?
Curing transforms soft, flexible rubber into tough, rigid rubber by applying heat. The specific time and heat required depend on the rubber material used. Various compounds can help accelerate the curing process and even increase rubber rigidity.
Vulcanization is a particular type of rubber curing process that utilizes sulfur to strengthen rubber’s molecular structure further. Learn about what vulcanized rubber is used for.
Why is Curing Necessary for Compression Molding?
Compression molding applies a strong compressive force to the raw, uncured rubber into the mold cavity. Since the rubber is uncured, it is easier to push into the shape of the mold. However, due to the elastic properties of rubber, it will return to its original shape once the force is removed. Curing accomplishes two tasks: strengthening the uncured rubber and helping set the shape.
4 Benefits of Rubber Compression Molding
The benefits of compression molding are all relative to other rubber molding methods. Following are four key benefits compression molding has over transfer and injection molding.
1. Quicker Production Runs
Compression molding is the faster rubber molding process due to its simplicity. It requires minimal setup, and the pre-formed materials reduce the duration of the compression phase. Compression-molded rubber parts can typically be produced within a week of ordering, not including shipping time.
But it should be noted that this is a standard rubber molding process, and compression molds take the same time to construct as any other mold.
2. Compatible with a Wide Varia ety of Rubber Materials
Since the process uses a solid compressive force, it can push even the most complex rubber materials into the mold cavity. The compatibility with a diverse set of materials makes compression the ideal process for custom rubber molding.
The following are three rubber materials commonly used for rubber compression molding.
- Nitrile – Softest material
- Silicone Rubber – Soft to medium material hardness.
- FKM or Viton – Hard and resilient synthetic rubber.
3. Minimal Material Waste
Rubber compression molding yields less material waste than transfer and injection molding. The difference in the amount of waste material is relatively small but stacks up over time.
4. Cost-Effective Rubber Molding Process
Compression molding can be very cost-effective when used correctly. As the process is simple and requires very little setup time, manufacturers can quickly produce samples, prototypes, and small-volume custom rubber parts.
Compression molding is most effective when dealing with small-scale orders.
Rubber Compression Molding Process
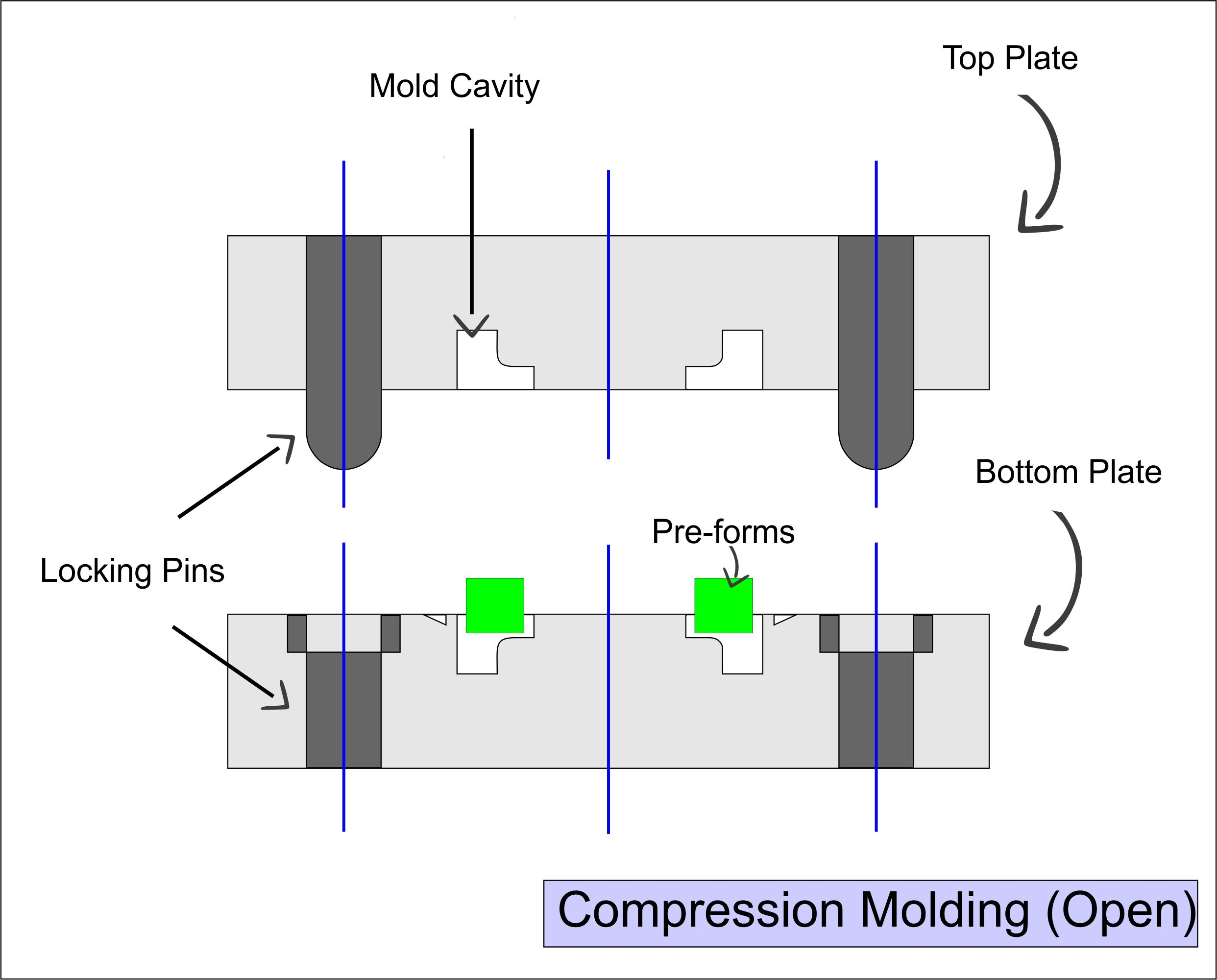
Following are the main steps involved in any custom rubber compression molding process.
Step 1
All molding processes start with a standard two-part metal mold. The molding material depends on the estimated temperature and pressure inside the cavity.
Step 2
Once the mold is finalized, a pre-form is cut down to match the rough shape of the mold. The pre-formed material doesn’t need to be precise, just close enough to the final shape. Optionally you can preheat the molds while you shape the pre-forms. Preheating helps more complex materials melt more consistently.
Step 3
Next, the pre-form is placed in the center of the compression mold’s bottom half (plate). If the pre-from is misaligned, it could lead to poor mold fill.
Step 4
Close the mold and secure the two mold plates using latches or locking pins.
Step 5
Now step back and slowly apply the compressive force to the top of the mold. The excess rubber material will leak into the overflow grooves as the rubber is pressed into the mold.
Step 6
Heat is applied to the mold at a constant rate for even curing. Curing is a complex process, and curing time varies based on material choice and additives, but a standard cure time is around 5 minutes.
Step 7
Unlatch the mold and eject the rubber part from the cavity. The rubber parts will be hot and need to be cooled off.
Step 8
Trim the excess material off of the final part. This includes cutting off the sprues, sports, rubber overflow, and occasional flash.
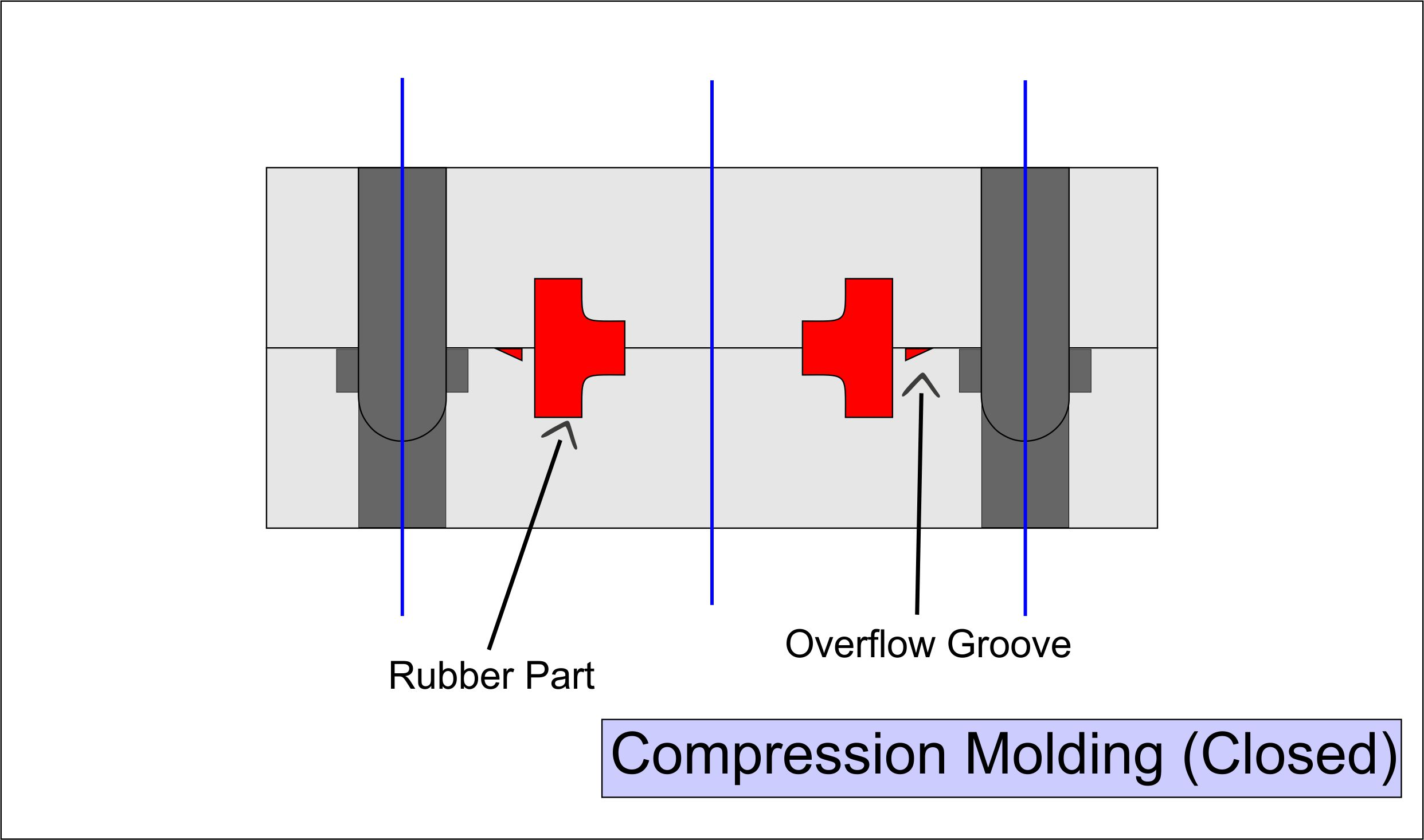
Compression Molding vs. Transfer Molding vs. Injection Molding
Rubber molding is a relatively simple process that has very few customization options. So the three rubber molding processes differentiate themselves from one another based on application and production volume.
Rubber Transfer Molding
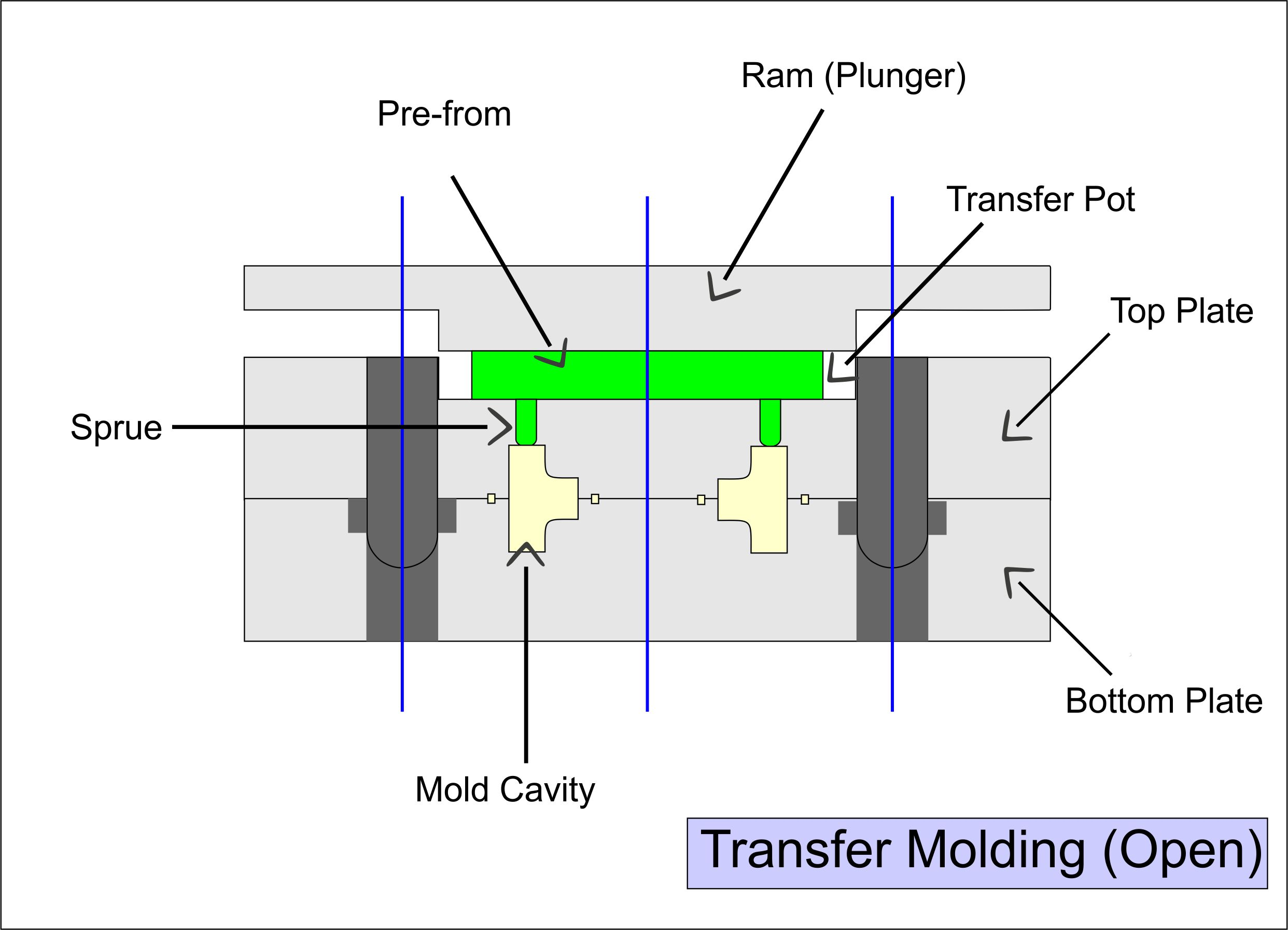
Transfer molding uses an additional container called a runner (or transfer pot) that houses the uncured rubber before it is pushed into the mold cavities. The runner helps the rubber flow consistently into several molds attached to it. Transfer molding is only compatible with softer raw materials like nitrile and silicone rubber.
Transfer molding results in better dimensional accuracy and can simultaneously fill six or more mold cavities during a single run.
However, transfer molding is incompatible with more complex raw rubber materials, producing more waste from leftover rubber (flash pads).
Rubber Injection Molding
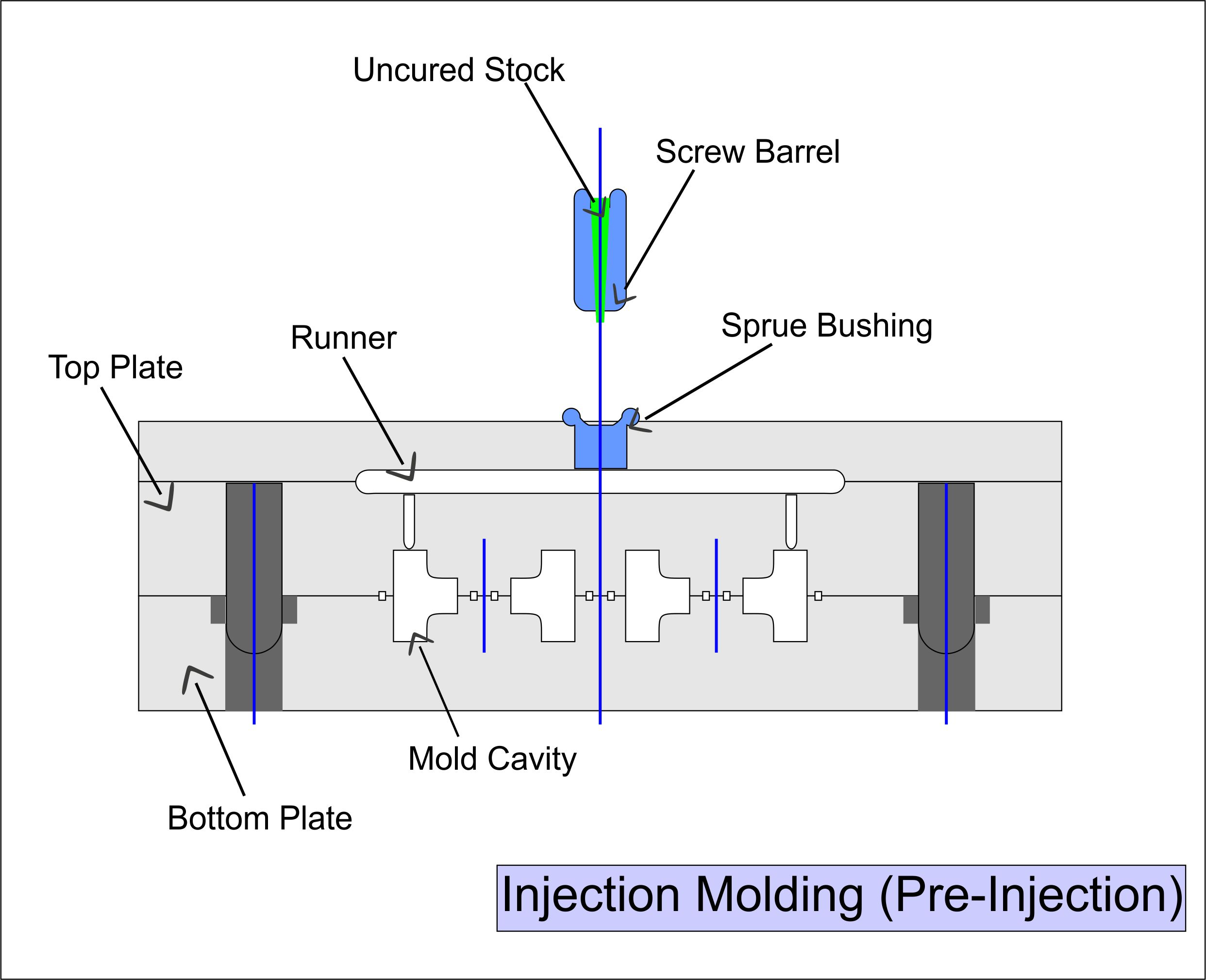
Rubber injection molding pre-heats the uncured rubber into a molten state. The liquid rubber can quickly be injected into a mold cavity with less force. Injection molds need to be stronger here to deal with a sudden and quick injection of molten rubber. Injection molding is commonly done with liquid silicone rubber.
Rubber injection molding is much faster regarding large-volume productions, but compression molding takes the lead in low-volume runs.
Common Products Made with Rubber Compression Molding
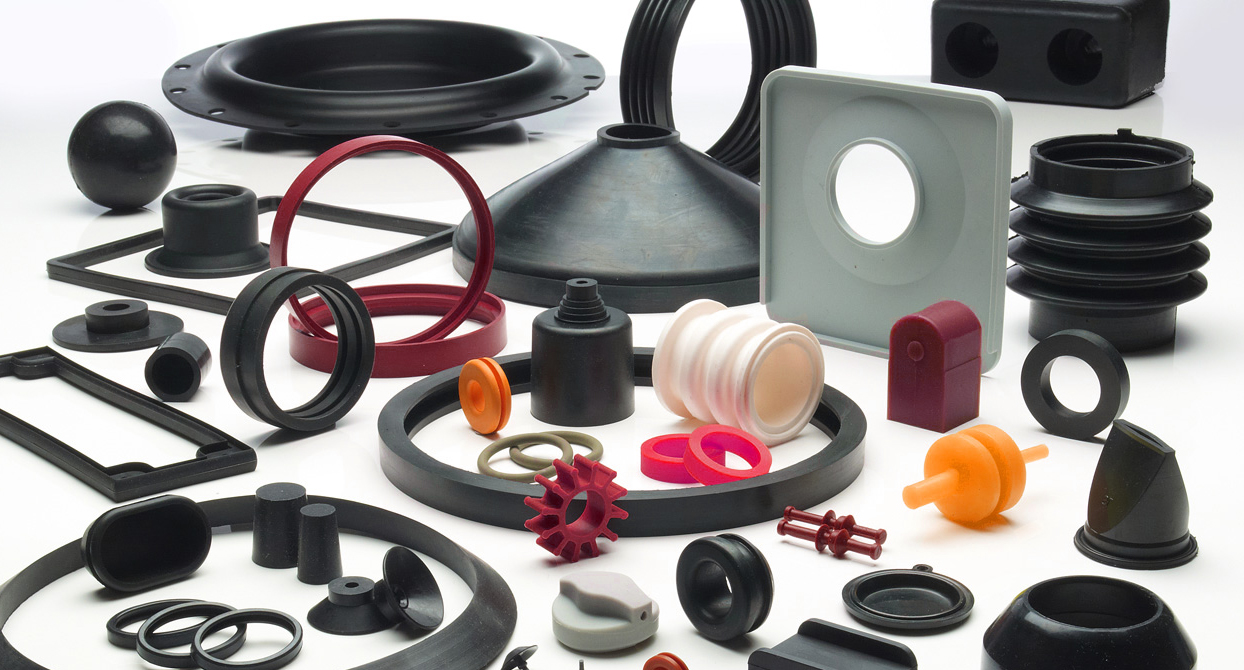
Compression molding can make nearly any type of small to medium-sized rubber part. But it is commonly used to create custom rubber parts for specialized applications.
Following are a few industries that utilize compression-molded rubber parts.
Applications of Rubber Compression Molding | ||
---|---|---|
Industry | Application | Rubber Material |
Chemical | Adhesives Seals for Chemical Containers Gaskets, etc. | Nitrile (NBR) |
Automotive | Engine Seals Cable Sleeving O-rings Gaskets, etc. | Viton (FMK) Silicone Rubber |
Oil & Gasoline | Pipes Hoses Seals Container Lid, etc. | Viton (FMK) Hydration (ECO) Rubber |
Aerospace | Vibration Dampeners Air tights Seals Low-Temp Gaskets O-rings, etc. | Viton (FMK) Fluorosilicone (FVMQ) Rubber |
Heavy Machinery | Sound & Vibration Dampeners Shock Absorbers Seals, etc. | Natural Rubber Styrene Butadiene (SBR) Butyl (IIR) |
Medical Equipment | Rubber Seals Tubing Containers, etc. | Medical Grade Silicone |
Domestic Appliances | Rubber Feet Seals Electrical Sleeving, etc. | Natural Rubber Low-Cost Synthetic Rubbers |
Maintaining a Rubber Compression Molding Machine
A standard rubber compression molding machine requires very little maintenance work. Most of it revolves around greasing lead screws, cleaning residual rubber leftovers, and regular cleaning.
Additionally, a well-maintained compression molding machine should have its thermal sensors checked frequently. Erroneous temperature readings can lead to overheating, which results in burnt rubber in the mold cavity.
Neglecting maintenance won’t break your rubber compression molding machine, but it will result in more and more defects. Rubber molding defects can range from little air bubbles to massive geometry damage.
Why is the Best Material for Compression Molding?
The material choice for rubber compression molding comes down to applying the final part. A stricter material like EPDM is ideal for high-performance applications that frequently experience harsh environments and surface damage. Use silicone rubber for everything else.
Silicone Compression Molding
Silicone is a soft-touch rubber material that has exceptional temperature resistance. It can also withstand environmental effects like ozone, water, UV light, etc. Silicone is safe from all the risk factors a specific rubber product will experience. To top it off, silicone is considerably cheaper than other synthetic rubber.
Silicone compression molding is commonly seen in toys, kitchen appliances, and medical equipment.
EPDM Compression Molding
Ethylene Propylene or EPDM Rubber is a tough synthetic rubber best suited to outdoor applications. Unlike silicone, it lacks resistance to extreme temperatures but compensates for it with its excellent abrasion resistance.
You will typically see EPDM compression molding for vehicle seals and non-slip pads.
Conclusion
In summary, the rubber compression molding process is an efficient and cost-effective way to manufacture rubber products. However, it’s crucial to work with a reputable manufacturer with the latest technologies, experienced personnel, and a commitment to quality and customer satisfaction.
Choose Hongju for Your Rubber Compression Molding Needs
Hongju is an industry leader in custom rubber molding solutions. We offer high-quality and high-precision rubber compression molding, injection molding, and die-cutting services. We understand that businesses rely on quick turnaround times to stay successful. This is why Hongju offers rapid prototyping services to help with those deadlines.