In this article, we will examine what compression molding is, the important features of the molds used, the types of compatible materials, and the process’ pros and cons. We’ll also examine compression molding’s many use cases and how it compares to other molding processes. Read on as we explore one of the oldest molding processes in active use.
What is Compression Molding?
Compression molding is a production process that uses a two-sided heated mold, top and bottom, to compress a moldable material into a shape or form determined by the mold. Both heat and pressure are important aspects of the compression molding process.
Heat helps the material used for compression molding to melt or cure, depending on the type of material used. Pressure forces the softened material to flow evenly into the mold cavities.
As suggested by its name, compressive forces are key to this molding method. The tonnage of presses used can go as high as 2500 tons. Compression molding is an excellent manufacturing method for high-volume production.
The Compression Molding Process
The compression molding process has a few variations depending on the type of material you are working with. However, the main process can be broken down into six basic steps.
Step 1: Preparing the Machine for Molding
There are different types of compression molding equipment, but each will have to be prepared in some way before a production cycle starts. This can include actions like:
- Cleaning the mold
- Spraying a release agent
- Turning on the heat and preheating the mold
- Placing inserts, etc.
These actions are essential, and missing a step could result in a defective or damaged part.
Step 2: Measuring and Loading the Feed Material
The amount of plastic material used in compression molding must be precisely measured. This helps to ensure consistency between products. Too much material in the mold can result in several issues, including:
- Excessive amounts of flash that must be cut off
- Demolding challenges
- Damaged molds
- Low-dimensional accuracy
On the other hand, too little material can result in a part that lacks the right density, has poor surface quality, or even has missing sections of material.

When the correct amount of material is measured, it is placed in the cavity of the mold. The molding material may be preheated before being placed in the mold. This can help to reduce the cycle time.
Step 3: Closing the Mold/ Compressing the Material
Once the material is in place, the mold is closed to apply the compression that forces the material into every part of the mold cavity. Heat may be applied to the mold at this stage as well to soften the material or to aid in the curing of thermoset materials.
The closing of the mold takes place at a predetermined speed for faster cycle times. The speed also can’t be too high as the material can become displaced from inside the mold cavity.
Step 4: Curing or Cooling
After the mold is closed, the material is held in place for a certain amount of time, typically 1 – 5 minutes. For a thermoset plastic, the material will be undergoing curing during this period. Curing is the process where crosslinking takes place in the polymer resulting in a solid part with specific properties.
In the case of thermoplastics, the formed part within the mold is cooled during this period until it is hard enough to be removed without being damaged.
Step 5: Demolding
During this step, the mold is opened and the solid part is removed from the mold. Ejection pins and other mechanical systems can assist with this. In some cases, demolding can be done by hand.
Some parts have a more complicated demolding process than others. For example, for a part molded with the help of inserts, the inserts have to be removed at some point during the demolding stage.
Step 6: Post-Processing
After a part has been removed from the mold, it may need to undergo a few more steps before it is considered ready. Cutting away excess material or flash is a common procedure at this stage. Other parts may need heat treatment to reduce internal stresses or cleaning.
Take the First Step:
Requst for an Inquire
Quality Meets Affordability. Inquire Now for High-Quality Products at Low Volumes.
Mold Design in Compression Molding
Success in compression molding starts with designing the right mold for your part. The mechanics of compression molding place certain limitations on the features a part can have. It’s important to be aware of these limits to ensure the part designed can be manufactured.
Choose an Achievable Level of Complexity
Compression molding machines can be used to mold parts with complex designs, but these make the process more challenging.
A complex design can add several steps to the process. Such designs can also make it harder for the material to flow and reach every part of the mold. Extra steps mean longer production cycles and higher cost, while poor material flow can lead to defects in the part.
The mold designer should have the experience to come up with a design that creates complex parts without significantly reducing the manufacturability of the final part.
Make Part Ejection Easy
Ease of part ejection should be considered when designing a part because parts that are difficult to eject may face the following issues:
- Long cycle times
- Poor surface finish
- Breaking during ejection
Two factors that make it easier to eject parts are using draft angles in the design of the mold, and avoiding undercuts.
Choose an Appropriate Wall Thickness
Both thick and thin walls can pose a problem to molded parts. Thick walls are prone to the formation of internal voids. This is caused by the outer sections of the walls cooling much faster than the inner sections.
Thin walls lack the strength to resist the deforming forces induced by changes in temperature. They are more likely to warp or distort in some way as a part is cooling.
These challenges mean that the mold design must choose an optimal wall thickness based on the structural needs of the part and the flow of the material. Ribs are often used to attain strong parts without thick wall sections.
Consider the Material
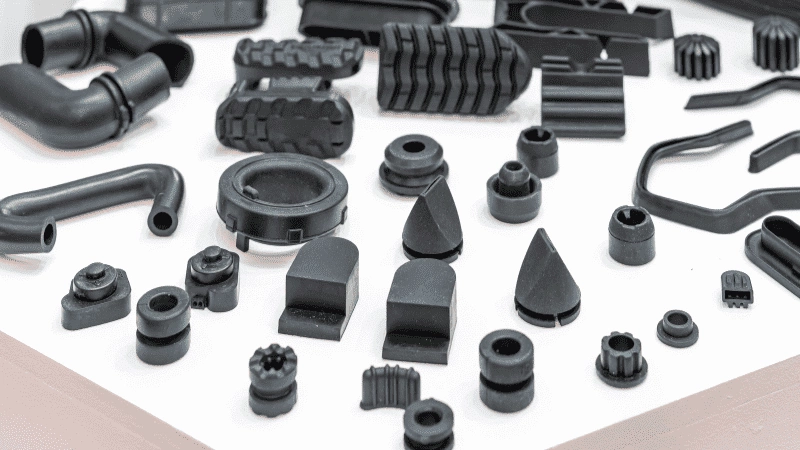
Different materials behave differently during the compression molding process. Some materials will not flow as easily as others. Others will heat or cool at a slower or faster rate. Some materials can also expand or shrink during some stages of the process.
The mold design must take into account such facts to avoid making defective parts or parts with incorrect dimensions.
Design to Last
Compression molding is classified as a high-volume manufacturing method. This means that the mold used should last a long time and be used for many parts.
To ensure this is the case, the mold should be designed in a way that minimizes the damaging effects of high temperatures and pressures.
Parts of the mold that can be more easily damaged should be designed to be easy to repair. This will reduce the downtime in case these parts need to be replaced or repaired.
Take the First Step:
Requst for an Inquire
Quality Meets Affordability. Inquire Now for High-Quality Products at Low Volumes.
Materials for Compression Molding
Compression molding is one of the few manufacturing processes that can work with both thermosets and thermoplastics. This greatly expands the range of products that can be manufactured using this process. Some common materials used now include silicone, epoxy, and HDPE.
Silicone
Silicone is an amazing elastomeric material that is replacing natural rubber in many applications. It has better temperature resistance and performs very well as an insulator. It is also more durable than rubber and can be used in both medical and food-grade applications.
Silicone is great for compression molding because it flows easily, allowing it to fill the forms of the mold well. Silicone is commonly used to produce gaskets, seals, and parts of medical equipment.
PU
PU, also known as polyurethane, is used to make parts that have high impact strength, abrasion resistance, and toughness. Depending on the formulation, a PU part could have many different physical qualities.
This thermoset flows easily and, with compression molding, can be used to make wheels, seals, rollers, etc.
HDPE
High-density polyethylene is a thermoplastic that melts easily and flows well in a molten state. It can be used for compression molding of fairly complex parts. This material has very good dimensional stability and impact resistance.
Compression molding is used for the manufacture of HDPE parts for industrial and automotive applications.
Epoxy
Cured epoxy parts are very strong and durable. They can be used for electrical insulation and even aerospace components. In an uncured state, the resin flows easily and fills mold cavities well.
Epoxy parts can withstand high temperatures and have excellent dimensional stability.
PTFE
Polytetrafluoroethylene exhibits excellent non-stick properties and is also highly resistant to chemicals. PTFE is a good material for compression molding because it flows easily. Bearings, gaskets, and parts for electrical insulation can all be molded using PTFE.
Take the First Step:
Requst for an Inquire
Quality Meets Affordability. Inquire Now for High-Quality Products at Low Volumes.
Comparison With Other Molding Processes
Compression molding and injection molding are frequently compared because both processes use molds. Although there is a significant degree of overlap, these two manufacturing methods are significantly different and usually serve different manufacturing needs.
Open Vs Closed Mold
Compression molding uses an open mold design. The material is placed into the exposed mold cavity before the top part of the mold closes on top of it.
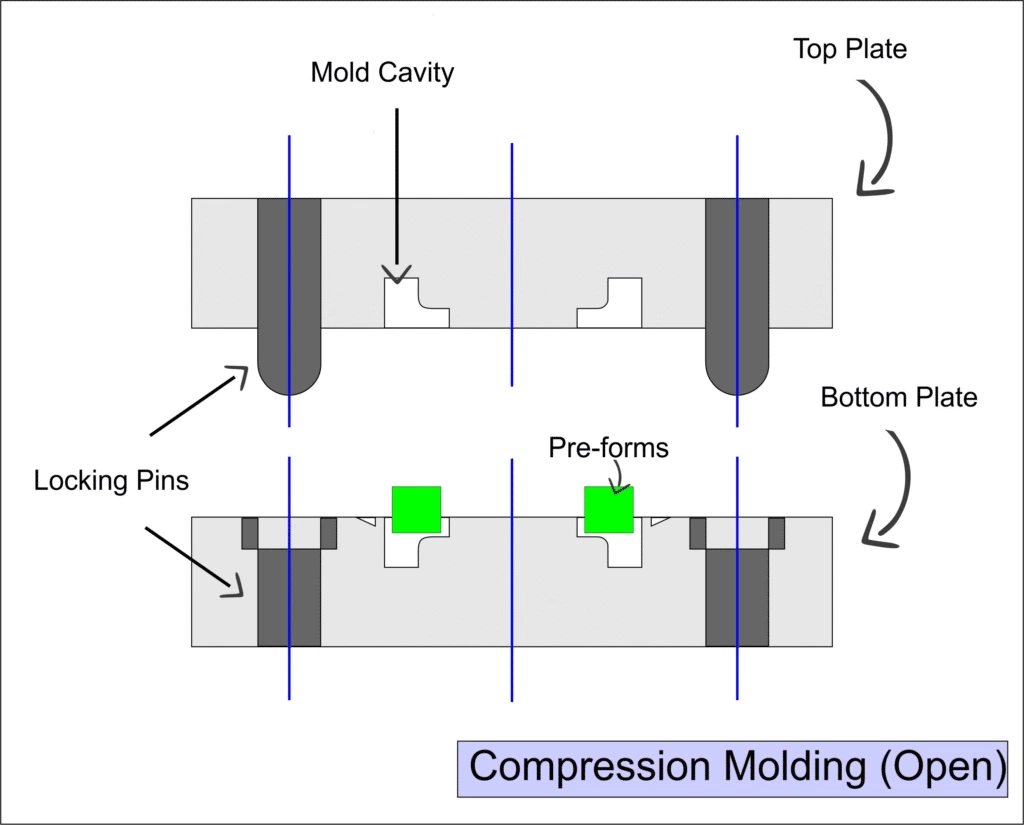
On the other hand, injection molding uses a closed mold design. The material is injected into a mold that is already closed. There are passageways for the introduction of material or venting.
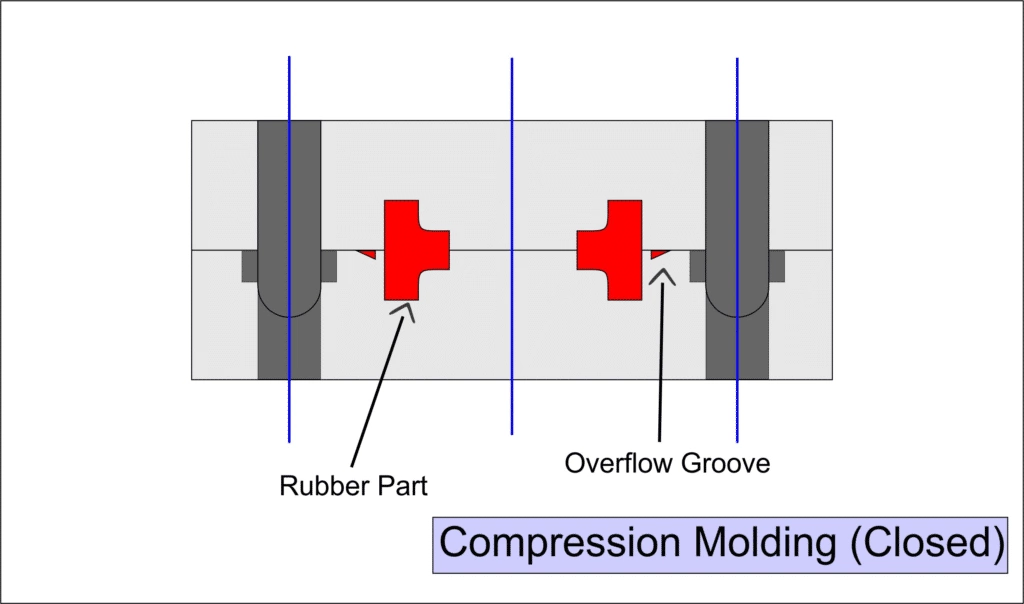
Part Design
The open nature of the molds used for compression molding makes it a good process for making large parts with non-complicated geometries e.g. panels. Parts such as car bumpers can be easily made using this process.
The closed nature of injection molding molds makes it an excellent process for the production of parts with more complicated designs. The materials are introduced into the mold at a high pressure that enables it to flow into complex forms.
Setup Cost
Setting up an injection molding operation tends to be more expensive than setting up for compression molding. The tooling costs are quite high because they have to be able to handle the high pressures of the injection molding process and tightly control the process parameters.
The tooling for compression molding doesn’t cost as much, and this makes it a better choice when the production volume is lower.
Cycle Times
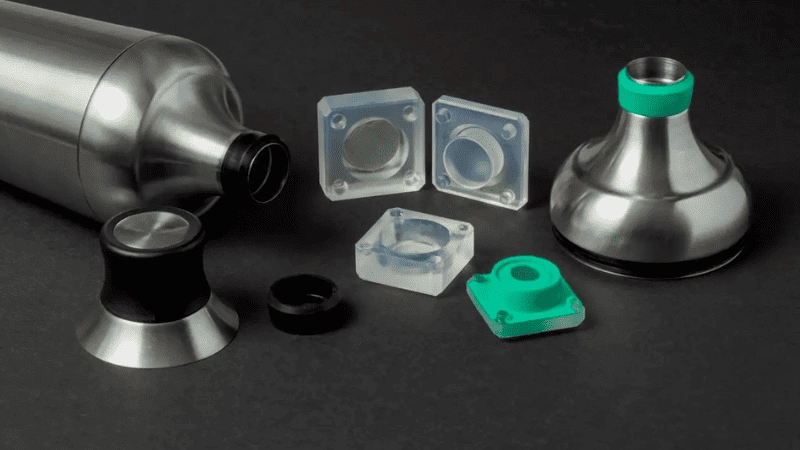
Compression molding cycles can range between one and six minutes. Some injection molding cycles on the other hand can be as low as two seconds.
There are cases where the production times for injection molding are over a minute long, but it is generally a faster process and is an excellent choice for mass production.
This difference in cycle times comes from the fact that injection molding processes are usually fully automated, while compression molding can be manual, with parts needing time to cure before being ejected. Loading of materials and ejection of parts may also be manually done in compression molding.
Level of Precision
The injection molding process is a much more precise process compared to compression molding. The molds used for injection molding are made from very strong materials. They are less likely to develop defects that affect the shapes and dimensions of parts.
The level of precision is high enough that injection-molded parts may not need any post-processing.
Material Options
Although injection molding works well with many materials, a special case with compression molding is that it can use bulk molding compound or sheet molding compound. These materials contain chopped fibers and can be used to manufacture composite parts.
Injection molding cannot make use of such materials and is not suitable for making parts made up of composite materials.
Take the First Step:
Requst for an Inquire
Quality Meets Affordability. Inquire Now for High-Quality Products at Low Volumes.
Advantages and Drawbacks of Compression Molding
Compression molding has survived for more than a century. This is because it has advantages that include:
- Lower tooling cost: The equipment associated with compression molding, such as hydraulic presses, is not as complicated as the equipment used for injection molding. This makes it less costly to start a compression molding operation.
- Better for low-volume production: The lower cost of compression molding tooling makes it better for low production volumes. This is because fewer products are needed to break even.
- Great for large items: The main limiting factors in terms of size and weight of parts made using compression molding are the tonnage and size of the press. Therefore, compression molding is commonly used to manufacture larger parts compared to injection molding and other processes.
- Inserts are possible: Insert molding is the molding of one material over another. This is possible with compression molding if the right methods and tooling are used.
- Strong parts: Compression molding produces dense parts that are quite robust, thanks to the large compressive forces it uses.
- Material compatibility: Compression molding is compatible with many different types of material, including fiber-impregnated composites.
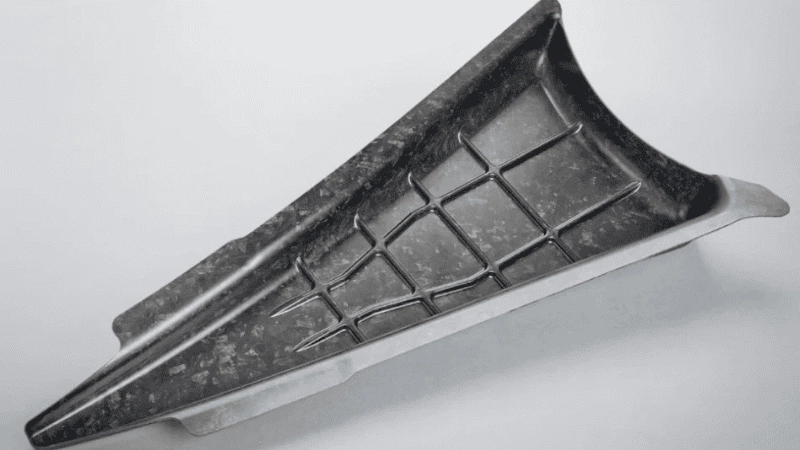
This manufacturing method is not always suitable for some products. The disadvantages of compression molding include:
- Part complexity: The level of complexity that can be achieved using compression molding is not poor, but it cannot compete with injection molding and some other processes.
- Production times: The production times for compression molding are longer than those for injection molding.
- Post-processing: Without the right measures, flash can be a significant problem in compression molding. This excess material has to be trimmed away, and this extra step can be expensive.
The Applications of Compression Molding
Compression molding can be used to make a wide range of parts from thermoplastic and thermosetting polymers. Some examples of these are:
- Electrical parts: Sockets, faceplates, switches, and other electrical components can be made using compression molding.
- Electronic devices: Parts of keypads, game controllers, etc., can be made using this technique.
- Automotive parts: Large panels and other parts of vehicles can be made using compression molding.
- Medical device parts: Respirator masks and other medical devices are made using compression molding.
Take the First Step:
Requst for an Inquire
Quality Meets Affordability. Inquire Now for High-Quality Products at Low Volumes.
Conclusion
Compression molding doesn’t have the sophistication of injection molding, but it remains the best method for making certain types of products.
This manufacturing process is simple, and the materials are even manually loaded into the mold. Despite its simplicity, it produces products that have very high strength and good surface finish, and it can even manage some complex geometries.
Compression molding now works with many thermosetting and thermoplastic materials, and its products are used across many industries.
Talk To Hongju’s Compression Molding Experts Today
Compression molding is a versatile manufacturing process that you can use to manufacture products that include o-rings, keypads, rubber feet, and more. It’s an excellent choice if you need a low-to-medium volume product.
To get the most out of compression molding, you’ll need a team that has experience making high-quality products using this process. That is what you’ll get when you reach out to the team at Hongju.