These different types of molding processes involve different techniques. Two of the more commonly used techniques are compression molding and injection molding.
But which one of these manufacturing processes is better suited for your needs? Read our detailed comparison of compression molding vs. Injection molding to find out the best technique for your needs.
What Is Compression Molding?
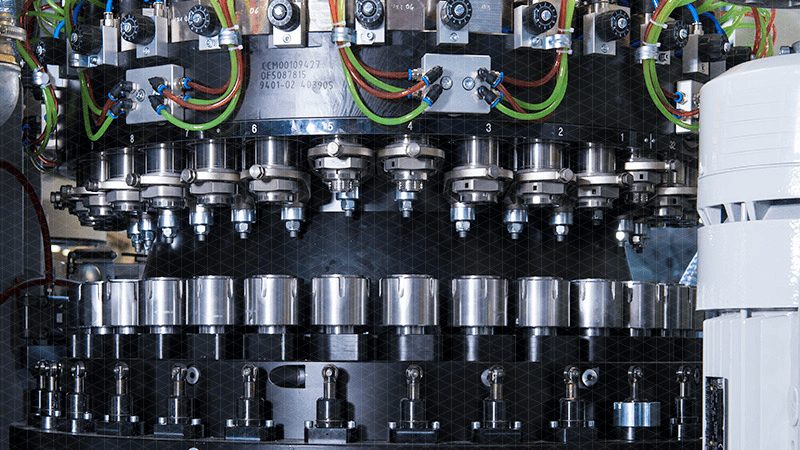
As the name indicates, in compression molding the materials are compressed to attain the desired shape. During this process, the raw materials placed in the mold cavity are heated. Specially designed plugs are then inserted into the melted plastic from the top.
The plugs seal the cavity and apply high pressure to the material. Under high temperatures and high pressure, the raw material starts to cure in the mold cavity and a new product or component is created.
Advantages of Compression Molding
- Provides an excellent surface finish
- Requires short time to set up lead time length is short
- Wastage is minimal and prototyping is easier
- Sizes of the products can have a wide range- but it is best suited for parts that have a large cross-section
- Perfect for parts that require long cure time and need to be manufactured in smaller quantities
- Materials that are stiff and have high durometer can be processed
- The cost of tools and equipment is low. The tooling is simple and less expensive as compared to the injection molding.
- Although this technique has a longer cycle time, it uses a low-pressure mold and thus different types of cavities can be produced without the high cost of tooling.
Disadvantages of Compression Molding
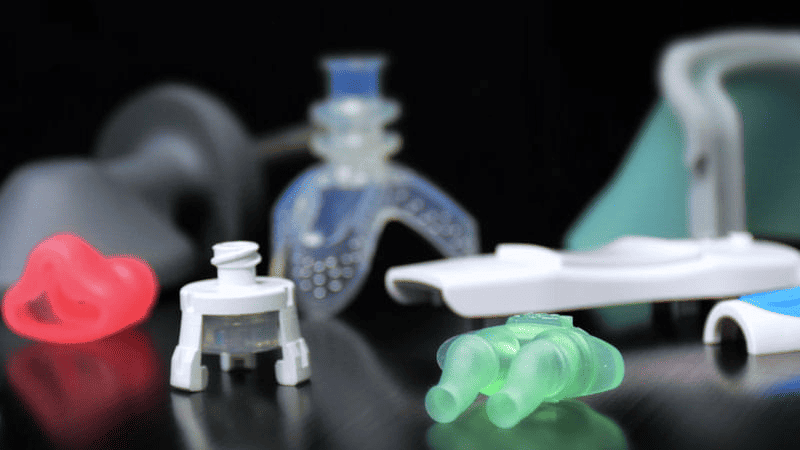
- The tolerance level is intermediate so, the parts produced are not very consistent
- Deflashing may also be required. A flash is when the resin escapes between two parts. This extra resin must be trimmed manually which considerably slows down the production. In addition, it is not possible to grind the excess which results in more wastage.
- To remove flash manual labor is required which increases the human capital investment.
- The cure times are longer. The time required to repeat the cycle is from 1-6 minutes which is much slower than injection molding. So, it is not suitable for high-volume production.
- The technique is not suited for complicated parts. It is best suited for parts with simpler design
- Contamination is common in the case of colored plastics and silicone
Applications of Compression Molding
- Automotive industry: The compression molding process is used in the production of automotive parts such as panels for tractors, cars and other vehicles. It’s also used for dashboards, center consoles, door panels
- Computer and related devices: It’s used for gaming consoles, controllers, and keypads.
- Kitchenware: It’s involved in the production of storage containers, bottle caps and other small plastic consumer products.
- Medical and dental devices: Syringe stoppers, respirator masks and models for medical studies are made using compression molding.
- Electrical devices: Electrical insulators, and outer covering of household appliances such as refrigerators and washing machines are also made using compression molding. Sockets, faceplates, switches and metering devices are a few other examples.
- Sports: Equipment such as skateboards, protective gear, and snowboards are made using this technique.
Inquire Now for Fast Quotations!
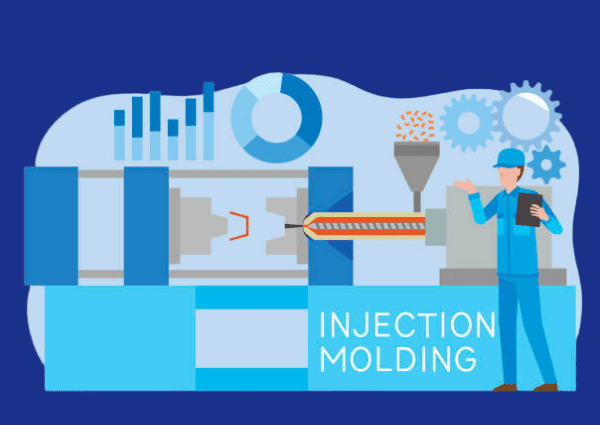
What Is Injection Molding?
Injection molding manufacturing technique can be used for the mass production of products from a variety of different materials having different mechanical properties such as glass, metal, polymers and elastomers. In contrast to compression molding, the materials in injection molding are injected into a closed mold cavity which results in the production of identical items every time.
With injection molding large volumes of products can be manufactured that are consistent in their final shape. First, a mold is created with steel or aluminum. The mold is made up of two parts, the cavity and the core. These two parts are brought together by high pressure from the machines.
Silicone or plastic is then melted and injected into the mold. The mold can then be tempered or cooled to the desired temperature.
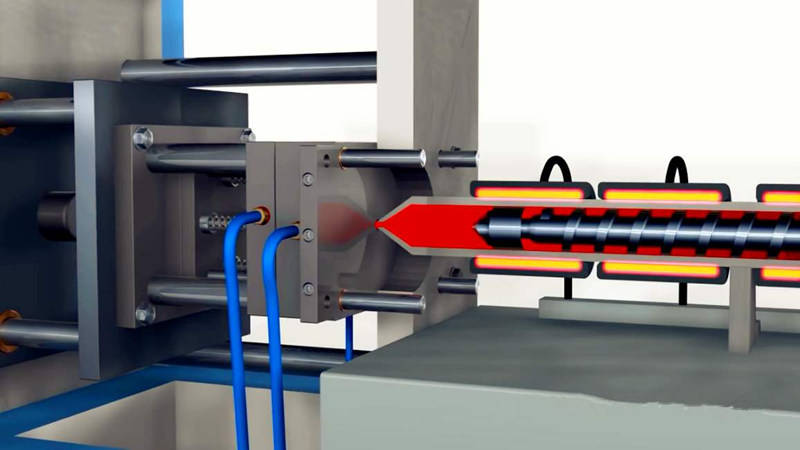
Advantages of Injection Molding
- High production efficiency: once the mold has been developed the process becomes very fast. The cycle time can be as short as 10 seconds.
- If the production volumes are high the cost per part is considerably small. For medium production volumes, the cost per part is also small if aluminum molds are used. Thus, this method is more cost-effective.
- High-volume production of identical parts is possible.
- A wide range of materials can be used for the injection molding process from thermoplastic materials to liquid silicone.
- There is little to no wastage because no flash is created. The unused material can be recycled easily which makes it cost effective.
- It is possible to achieve detailed complex shapes with proper mold design. The molten plastic is injected into the heated mold with high pressure which presses the material against the mold thus allowing it to form into intricate shapes and designs.
- Almost no secondary operations are required after producing parts. No edges are to be removed meaning less waste and the products usually have good finish post-production.
Disadvantages of Injection Molding
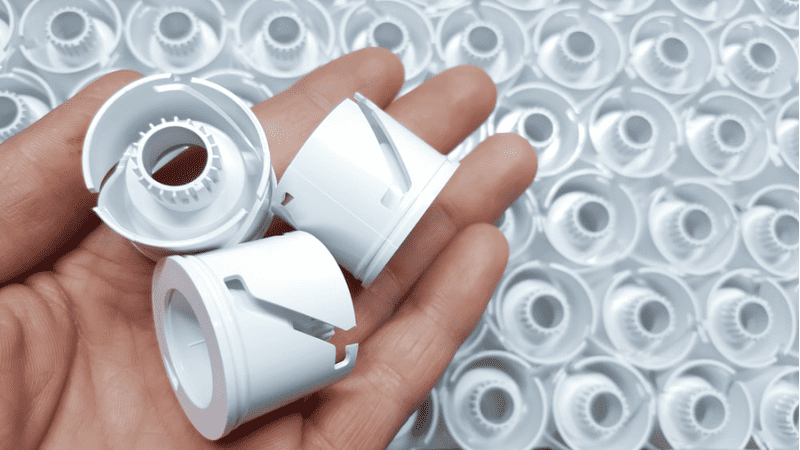
The initial cost is very high in the case of stainless steel mold for the production of large volumes of parts. The design and manufacturing of injection mold can also take a long time. If the production volume is low the cost per part would increase. In this case, it would be better to consider aluminum molds.
To produce stainless steel mold the initial lead time is long. It can take up to 12 weeks to manufacture the steel mold cavities.
There are also some design constraints that must be considered while designing the molds. Such as the placement of ejectors, gates and cooling lines, avoiding defects like sharp edges and controlling the thickness of the walls to make the production process smooth.
Applications of Injection Molding
Injection molding has a number of applications ranging from consumer toys to components of airplanes.
- Construction: Injection molds are used to make small hand tools, fasteners, and other accessories.
- Food industry: Containers for food and beverages, over caps, components of conveyor systems, and filtering and dispensing devices are made using the plastic injection molding method.
- Medical industry: Surgical products, dental X-ray components, testing kits, closures and stoppers are also produced via the same process.
- Electronics: It is used to make switches, circuit board closures, battery enclosures, components of desktops and laptops
- Automotive and Aerospace industry: It’s used to make panels, enclosures, housings, and chassis components.
Inquire Now for Fast Quotations!
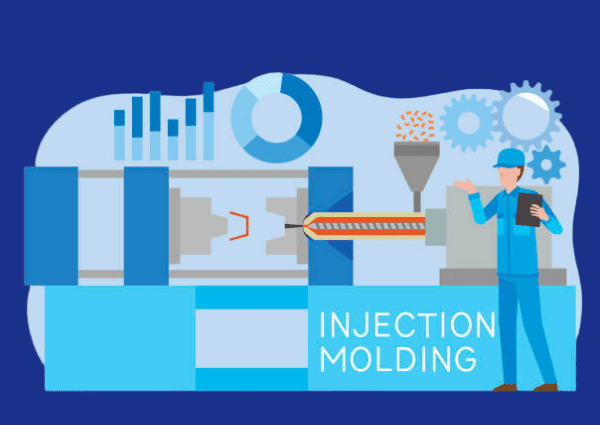
Compression Molding vs. Injection Molding: What’s the Difference?
Plastic and other related raw materials can be molded through many different processes. While comparing compression molding vs. injection molding you should understand which method is suitable to your particular needs. Which method is more efficient and which one can be used for a wide range of designs and prototypes?
Both injection molding and compression molding make use of heat and pressure to attain the desired shape of the plastic raw materials. However, there are some key differences that can help you choose the best option. Read further to find out.
Differences in the Process Mechanics
Compression molding is a relatively simple process that requires few components such as the raw polymer, heated mold and the plug. The process proceeds as follows.
- First, the raw plastic material is compressed and heated.
- The heated material is then placed in an open die with a specific cross-section. In this step, the focus is on the lower half of the material.
- To attain the final shape the upper plug is pressed into the plastic material. This ensures even distribution of the material in the mold cavity.
Injection molding on the other hand requires a larger number of components including injection units, feed hoppers, heaters, hydraulic cylinders, clamping units and others. Here is how it is done:
- First, the raw materials such as nylon, polypropylene, polystyrene or acrylic are converted into small resins or pellets which are then fed into the hopper.
- The raw materials are then consistently heated and transferred into the mold to attain the desired shape
- The other part of the mold is then secured by the clamping unit. The final product is cooled before being released from the die.
Material Utilization
In injection molding, rigid thermoplastics can be used along with thermoplastic elastomers and urethanes. Compression molding often makes use of flexible materials such as silicone and rubber. Compression can also be applied to BMC (Bulk moulding compound) and SMC (Sheet moulding compound) to produce rigid components.
The injection molding process does not result in any flash and thus no wastage of the material takes place. If there is some leftover material it can be melted and used again. Compression molding does have flash around the products which cannot be used again. Thus, some of the material gets wasted in each cycle. Injection molding is, therefore, more efficient in terms of material utilization.
Cycle Time
In terms of processing speed, the injection molding process is significantly faster than the compression molding. The injection molding cycle time is only a few seconds as compared to a few minutes cycle time of the compression molding. This is mainly due to the curing time required for the compression molded components before their removal from the molds.
Mold Complexity
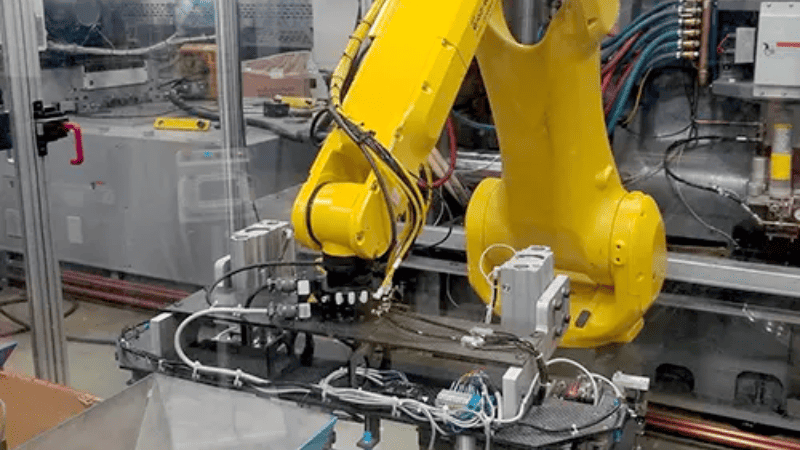
If you are interested in more complicated designs with high precision then injection molding is your best option. Injection molding provides the ease of experimenting with different design ideas more conveniently. Moreover, injection molding also allows you to test a product in the actual setting before the manufacturing actually starts.
This is why injection molding is used to make intricate designs and is used in the manufacturing of headphones, plastic containers, protective gear and other plastic and silicone products.
Compression molding mainly focuses on simpler parts because of less sophisticated procedures and components of the technique. Parts such as electrical housing, bottle caps and round inserts are formed through compression mold which explains their simpler designs.
Cost Comparison
The cost for both injection and compression molding varies with the type of material used, the product requirements, and other factors. In general compression molding costs less as compared to injection molding but the per-part prices are higher due to longer cycle time and post-production processing. Thus, compression molding is better for less complex parts and low production volumes.
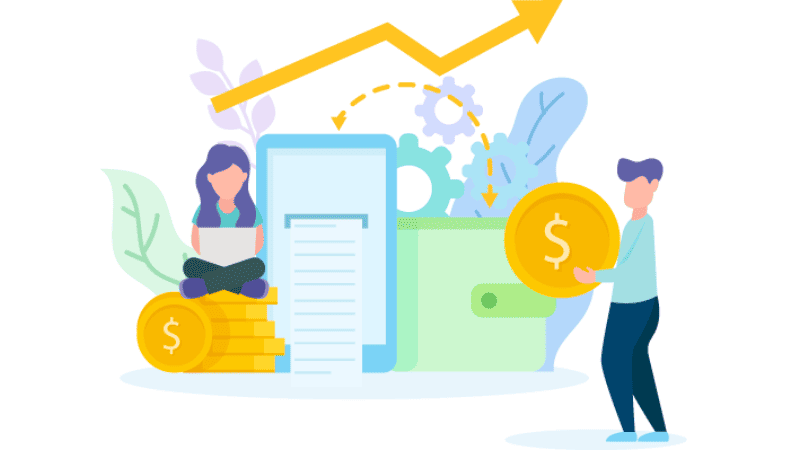
The initial cost of injection molding is high due to the larger investments required for tool designing and building. But once the molds have been formed they can be maintained easily and help in the production of large volumes of products. The post-production processing is also reduced which cuts the labor cost. Thus for the production of complex parts in higher volumes, the injection molding procedure is the path to choose.
Compression Molding vs. Injection Molding: Which Is Better for You?
It is a long-standing debate as to which type of molding process must be used. Each molding process has its own pros and cons. If you are interested in making large volumes of complex products with low cost and better visual appearance then injection molding is the best option.
Injection molded products are also durable and it is easier to change their sizes. Many different varieties of materials can be used in injection molding technique, multiple layers can be created and mass production is also possible with high consistency. All these benefits make injection molding an amazing manufacturing solution.
On the other hand compression molding must be opted in case the parts being formed are bigger in size, simpler in shape and need to be produced in smaller volumes because the process is time-consuming.
At Hongju Silicone, we specialize in both compression and injection molding and offer a variety of products. Our step-by-step design guide can help you get the best tips on product design and molding techniques that can be used.
Inquire Now for Fast Quotations!
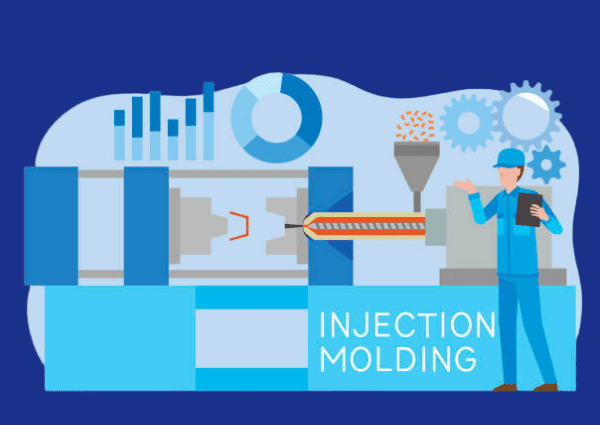
Conclusion
As said before there cannot be a definite answer to which molding process is the most efficient. It all depends on the type of outcome you want, the production requirement and the complexity of the design.
Choosing the right methods depends on your understanding of the process and the ability to assess which process meets your needs best.
Discover the Perfect Solution for Your Business with Hongju
Still confused about the best option for your needs? Visit our webpage to find more information on molding and our products. Or want to solve a specific molding problem? Contact our team of experts now and we will be happy to assist you with the best solutions.