Liquid silicone rubber (LSR) is different from solid silicone rubber. LSR is a liquid material that undergoes high pressures and temperatures to manufacture finished parts. As a result, this elastomer has a faster curing time and higher precision than solid silicone rubber.
Furthermore, LSR manufactures products with intricate designs and fine details due to its flexibility. This article explores Liquid silicone rubber, its types, and industries where it is applicable.
What Is Liquid Silicone Rubber?
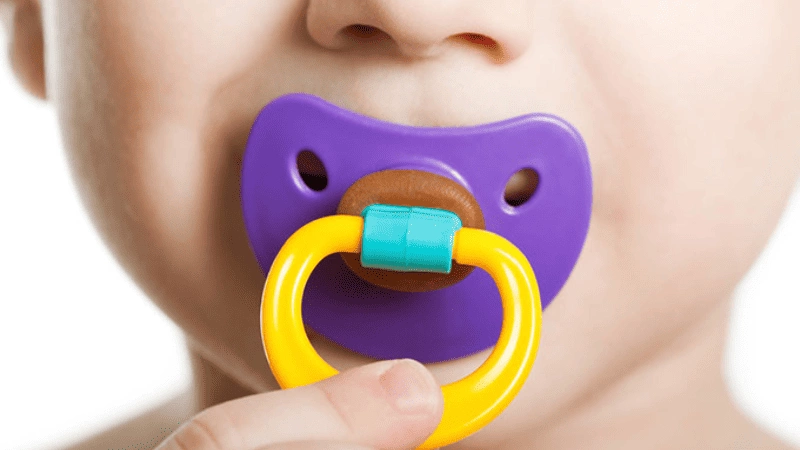
LSR (Liquid Silicone Rubber) is made of siloxane (Si–O–Si), which gives it great resistance to heat and chemicals. It’s cured with platinum-based catalysts, creating stronger, clearer, and cleaner products compared to older methods. This process results in a material with excellent strength, clarity, and no leftover residue.
Liquid silicone rubber (LSR) is not just silicone rubber in liquid form. Instead, it is formed by curing the long polysiloxane backbones using platinum and peroxide in silicone rubber. These catalysts form crosslinks that reinforce the tensile and tear strength of the elastomer.
As a result, LSR consists of short polymer chains with low molecular weight. In addition, this type of silicone rubber has better flow properties.
LSR is processed through liquid injection molding. First, the liquid raw material is mixed in equal parts from two separate components. It is then injected into a hot mold through a cold runner system.
Due to the design flexibility, LSR injection molding is suitable for manufacturing products with complex geometries in large quantities.
What Are the Different Types of Liquid Silicone Rubber?
1. High Consistency Rubber (HCR)
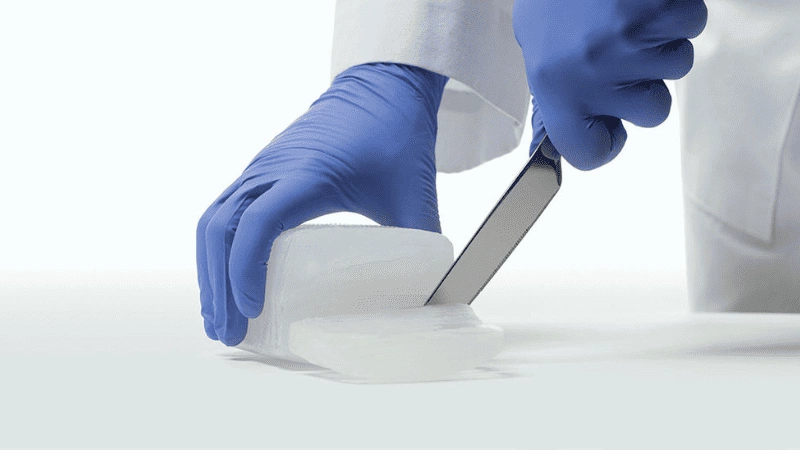
High-consistency rubber LSR is also known as high-temperature vulcanizing or heat-cured rubber. This elastomer has long polymer chains with high molecular weight. This type of rubber is manufactured in batches at high temperatures.
The key properties of HCR include its excellent electrical properties, thermal resistance, and weather resistance.
In addition, HCR insulators have excellent mechanical properties, making them suitable for power transmission systems.
2. Liquid Injection Molding (LIM)
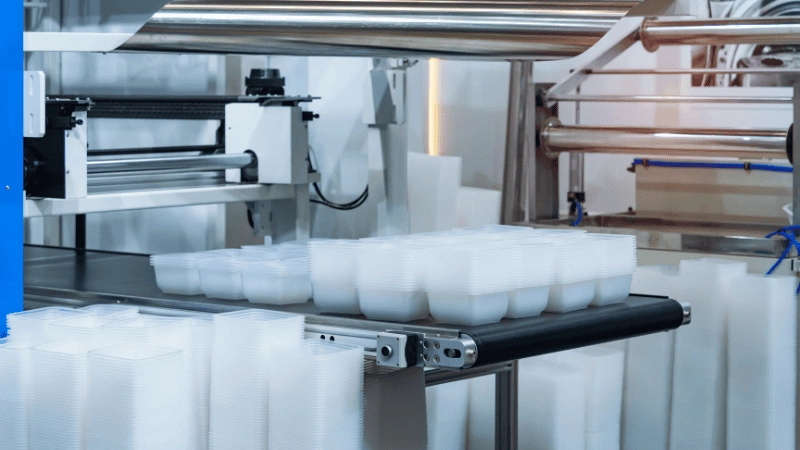
Liquid injection molding LSR is manufactured using the liquid injection molding process. The process creates high-quality rubber products with complex and intricate designs.
Furthermore, LIM LSR is biocompatible, consistent, and precise. The design flexibility of this elastomer makes it ideal for producing parts of several shapes and sizes.
3. Room Temperature Vulcanizing (RTV)
Room temperature vulcanizing LSR is a type of LSR that cures at room temperature without requiring additional heat. Usually, during the manufacture of RTV LSR, a platinum catalyst is used to harden the rubber.
Consequently, RTV LSR is suitable for applications that do not require heat. The properties of this LSR include a low compression set, chemical resistance, electrical insulation, and high thermal stability.
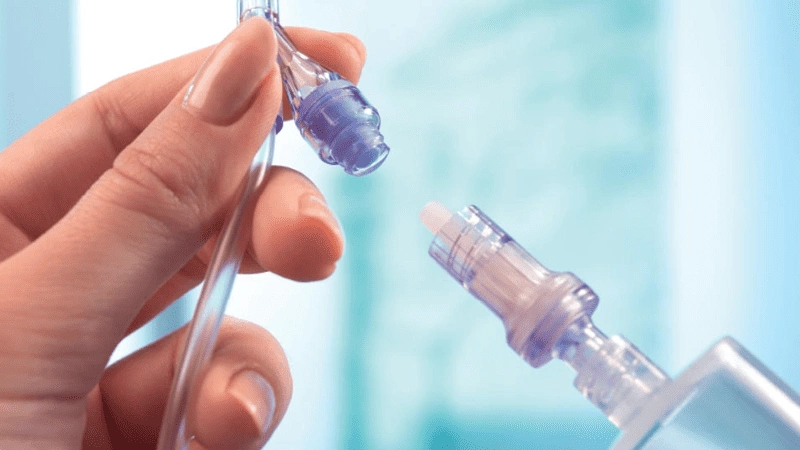
4. Fluorosilicone Rubber (FSR)
The molecular structure of fluorosilicone LSR contains fluorine. Fluorine reinforces the properties of LSR, improving its chemical, fuel, and oil resistance.
Furthermore, this type of LSR can withstand high temperatures and possesses excellent physical properties like flexibility and high tear strength.
Because fluorosilicone LSR can withstand high and low temperatures, it is used in sealing and gasket applications with extreme operating conditions.
5. Self-Bonding LSR
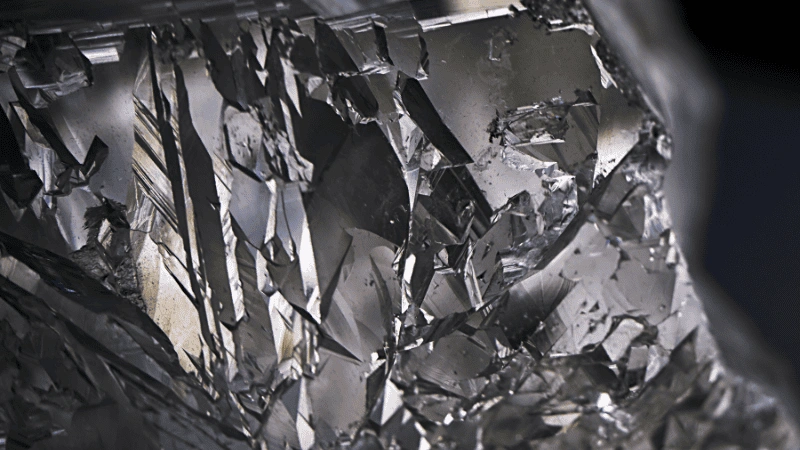
Self-bonding LSR can adhere to other substrates without needing a bonding agent. This type of LSR contains a reactive silicone resin that improves adhesion to several substrates, including glass, metals, and plastic.
Furthermore, this type of LSR cures quickly and possesses good flexibility and chemical resistance. Self-bonding LSR is especially suitable for over-molding applications and applications that need to bond two different materials, including silicone rubber.
6. Medical Grade LSR
The manufacturing process for medical-grade LSR follows stringent rules to ensure it is suitable for medical applications. This type of LSR is biocompatible, non-toxic, and sterile.
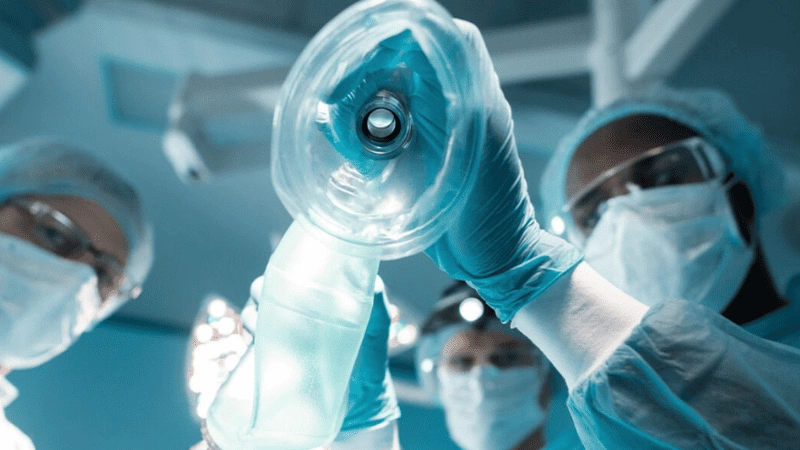
What Are the Advantages of Liquid Silicone Rubber?
- Biocompatibility
LSR is biocompatible and inert. This elastomer does not react with body fluids or cause allergic reactions. In addition to its biocompatibility, LSR can be sterilized without changing its physical or chemical properties.
This elastomer is used in the medical industry to manufacture several medical devices, including implants, respiratory, orthodontic, and orthopedic devices. These devices improve quality of life, comforting patients and reducing the risk of allergic reactions.
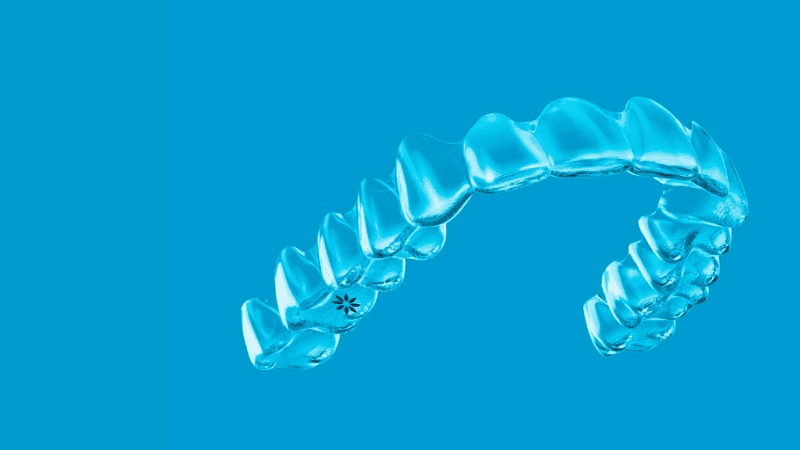
- Design Flexibility
LSR is flexible and can be molded into different complex shapes and sizes. This elastomer has a low viscosity and high precision.
Therefore, it fills molds to create intricate designs with consistent quality. The design flexibility of LSR is often utilized in the medical, consumer products, and automotive industries.
- Physical Properties and Chemical Resistance
Liquid silicone rubber offers superior tear strength (up to 35 kN/m), tensile strength (up to 12 MPa), and elongation at break (>300%). Its inert molecular structure resists chemical attack, water absorption, and microbial growth.
Unlike many thermoplastics or organic elastomers, LSR maintains elasticity across a wide temperature range from –60°C to +230°C.
What Are the Common Applications of Liquid Silicone Rubber?
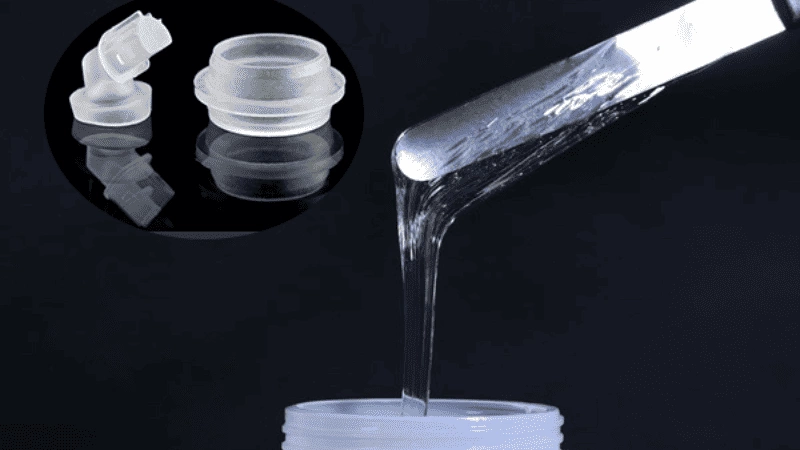
As discussed earlier, the properties of LSR make it ideal for various applications. Different industries that use this elastomer include;
Automotive
Automotive seals and gaskets are manufactured from LSR. This elastomer is also used to manufacture vibration-damping components and connectors.
Ideal for under-the-hood seals, sensor housings, and wire harness grommets due to its UV, heat, and vibration resistance.
Aerospace
LSR is used to manufacture tubings, seals, and gaskets for aerospace applications.
Electronics
Electronic components like seals, connectors, and keypads are manufactured from LSR materials. Insulating keypads, waterproof gaskets, and over-molded connectors in harsh environments.
Consumer goods
LSR is used in the consumer goods industry to manufacture kitchen utensils, sports gear, and baby products. Earbuds, baby pacifiers, shower nozzles—thanks to softness, biocompatibility, and FDA-compliance.
Healthcare
Surgical instruments, catheters, masks, infusion pumps, medical tubing, and syringes are some LSR medical devices manufactured from liquid silicone rubber.
Used in respirator masks, catheters, infusion pumps, and surgical valves due to its sterility, hypoallergenic nature, and ability to be sterilized via autoclave, gamma, or ETO.
How to Manufacture Liquid Silicone Rubber Products?
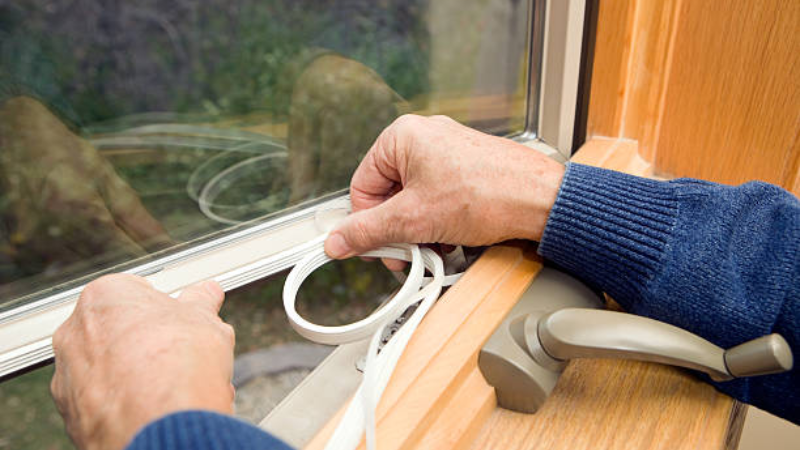
Liquid silicone rubbers are flexible and can be molded into different products using several processes. The common methods of manufacturing LSR include injection, compression, and transfer molding.
Injection Molding
The injection molding process injects mixed LSR into a mold cavity. This molding is usually in the shape of the desired product. Once the elastomer fills the mold, it begins to cure and solidify.
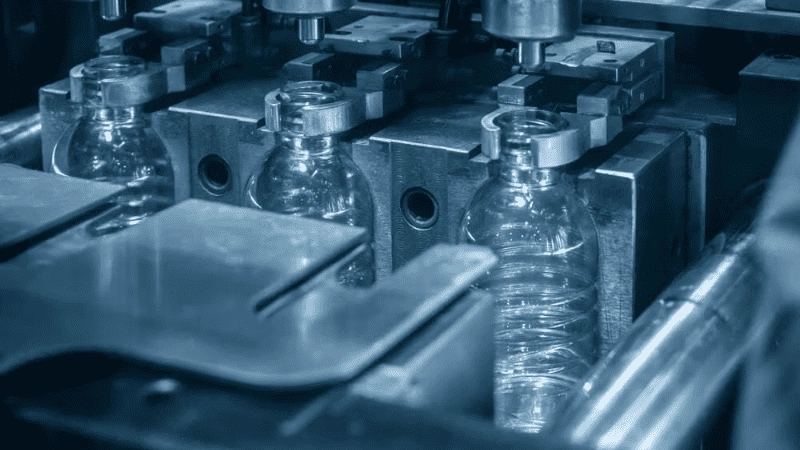
Liquid Injection Molding (LIM) is the most efficient way to mass-produce precision LSR components. The process uses a closed-loop system to meter, mix, and inject two-part LSR materials into preheated molds. Compared to compression or transfer molding, LIM offers:
– Shorter cycle times (as low as 20 seconds)
– Minimal waste (<2%)
– Flashless molds for clean parting lines
– Fully automated robotic demolding and in-line post-processing (trimming, marking)
Compression Molding
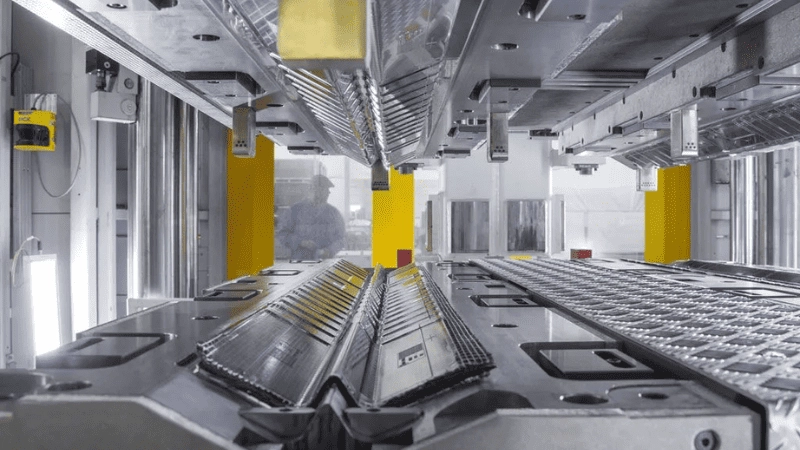
In compression molding, the LSR mixture is not injected into a mold. Instead, it is performed before being placed in a mold cavity.
After closing the mold cavity, the material undergoes high pressure and temperature applied by a hydraulic press.
This process then cures and solidifies the material. After solidification and cooling, the finished rubber product is removed.
Unlike injection molding, compression molding has a low upfront cost. The process also produces minimal waste, and the finished products have high tensile strength. However, compression molding has longer lead times than injection molding, and the process is less precise.
Transfer Molding
In the transfer molding process, LSR is mixed with pigments and curing agents before it is heated. The material is then loaded in a transfer pot and placed in a press.
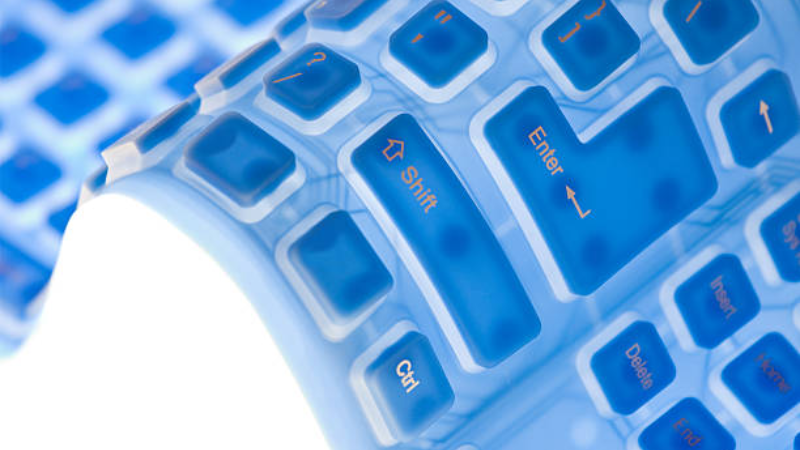
After applying pressure to the transfer pot, a sprue forces the LSR material into the mold cavity. The mold is then heated to cure and solidify the elastomer. After curing, the final products are removed.
Transfer molding is suitable for manufacturing complex shapes of high strength. In addition, the process has high precision and consistent quality.
However, the downside of transfer molding is that it is only suitable for small production runs and has a high initial investment.
The table below summarizes the differences between injection molding, compression molding, and transfer molding
Method | Advantages | Disadvantages |
---|---|---|
Injection Molding | High production rates | Complex and expensive machinery |
Precise control over material flow | Limited material options | |
Minimal waste | ||
Compression Molding | High volume production | Lower dimensional accuracy |
Efficient use of material | Longer processing time | |
Low energy consumption | Limited material options | |
Transfer Molding | High volume production | Complex and expensive machinery |
Precise control over material flow | Limited material options | |
Minimal waste | Long lead times |
Conclusiom
Liquid silicone rubber is versatile and used for manufacturing several products across several industries.
Due to its excellent properties, the material is suitable for medical, automotive, food, and consumer goods applications. Because there are different types of LSR, choosing one that suits your application and molding process is best.
Contact Hongju for Your Rubber Needs!
With over two decades of experience, Hongju delivers precision-engineered liquid silicone rubber solutions tailored to your needs.
Whether you’re designing a medical-grade implant or an automotive seal, we have the expertise, technology, and ISO-certified processes to make it happen. Contact us today to start your next LSR project.