In this guide, we’ll uncover why material traceability is an absolute must in this industry and how it directly impacts the end user. Strap in as we dive into the less-explored territories of the automotive world, enriching your perspective and bolstering your manufacturing strategies.
What is a Gasket and Why is it Essential in the Automotive Industry?
Gaskets are an integral part of the automotive industry, playing a crucial role in ensuring proper sealing and preventing leaks. Without gaskets, vehicles would experience numerous performance issues and potential safety hazards.
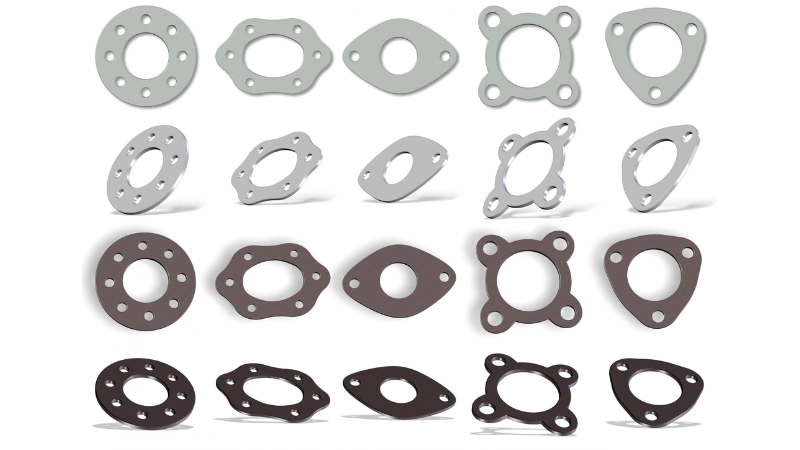
Definition and Purpose of Gaskets
A gasket can be defined as a mechanical seal that fills the irregularities between two surfaces, typically made from materials like rubber, silicone, metal, or composite materials. Its purpose is to create a reliable barrier against leaks by filling gaps caused by imperfect mating surfaces. The primary function of gaskets is to provide a secure connection between different parts of an engine or other automotive systems.
Role of Gaskets in the Automotive Industry
Automobile gaskets are pivotal in the overall functioning and safety of a vehicle, fulfilling several vital roles:
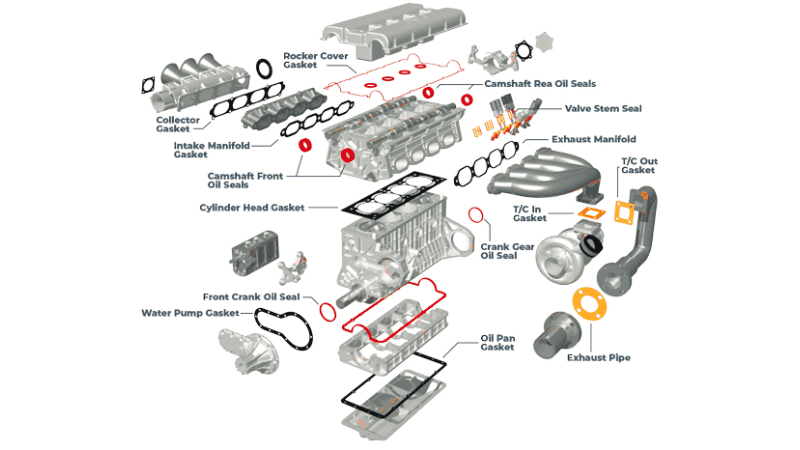
Preventing Leaks and Ensuring Proper Sealing
At its core, the primary role of a gasket in any vehicle is to maintain a robust and secure seal, preventing the escape of fluids and the entry of contaminants. They effectively mitigate the chances of oil, fuel, and coolant leaks, which if unchecked can result in significant engine damage and a subsequent decrease in the overall performance of the vehicle.
Impact of Faulty Gaskets on Vehicle Performance
On the flip side, a faulty or compromised gasket can drastically impact the performance and safety of a vehicle. A failed gasket can lead to leakage of essential fluids, overheating of the engine, or even catastrophic engine failure. This not only increases maintenance costs and decreases the lifespan of the vehicle but also poses significant safety risks for the driver and passengers.
Reducing Noise and Vibration
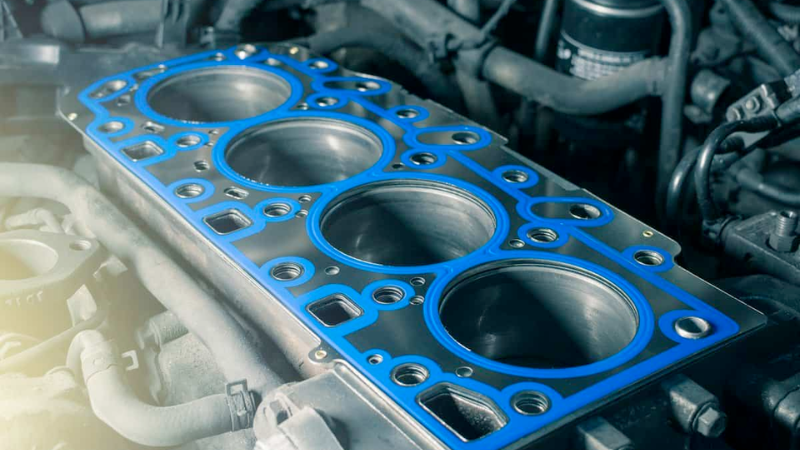
Gaskets also serve a role that might not be immediately obvious but is crucial to the overall experience of the vehicle. By providing an effective seal, gaskets help reduce noise and vibration within the vehicle’s components. This ensures a smoother, quieter ride and less wear and tear on the parts of the vehicle, thus enhancing the driving experience while extending the vehicle’s lifespan.
Given the critical role that gaskets play in the automotive industry, it becomes evident that ensuring the reliability and performance of these components is of utmost importance. This leads to the relevance of traceability in gasket materials.
Definition and Significance of Gasket Material Traceability
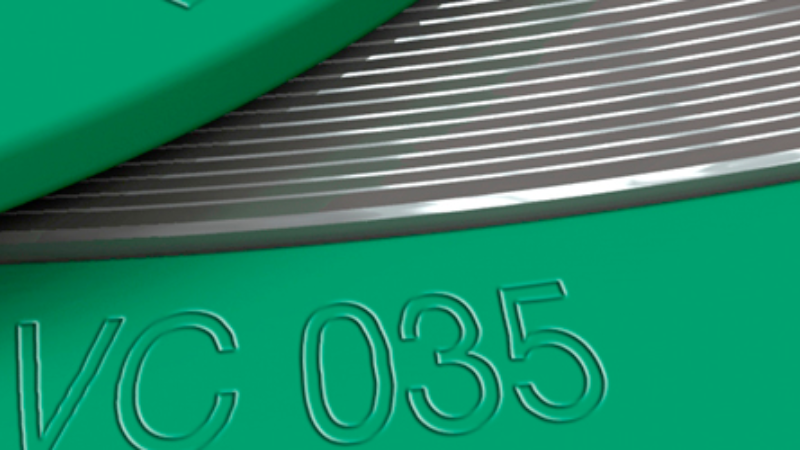
In the production of automotive gaskets, the concept of traceability is a vital one. To provide a clearer understanding of this concept, let’s delve into its definition and its fundamental importance in the automotive industry.
What is Gasket Material Traceability?
In the world of manufacturing, particularly in sectors like the automotive industry that require high standards of quality control, traceability is an indispensable concept. When we talk about gasket material traceability, we refer to the ability to track the journey of a gasket’s material from its source through the manufacturing process, to its installation, and even its disposal. Just as the gaskets provide a form of physical reinforcement, traceability provides a virtual form of material reinforcement.
It involves keeping a record of every batch of material used, the date of manufacture, the machines used, the operators involved, and any testing and quality control data. In this way, a gasket material traceability program guarantees that an informed engineer always has access to an updated source file of all the gasket materials and manufacturing chains used in the production process.
Why is Gasket Material Traceability Important for the Automobile Industry?
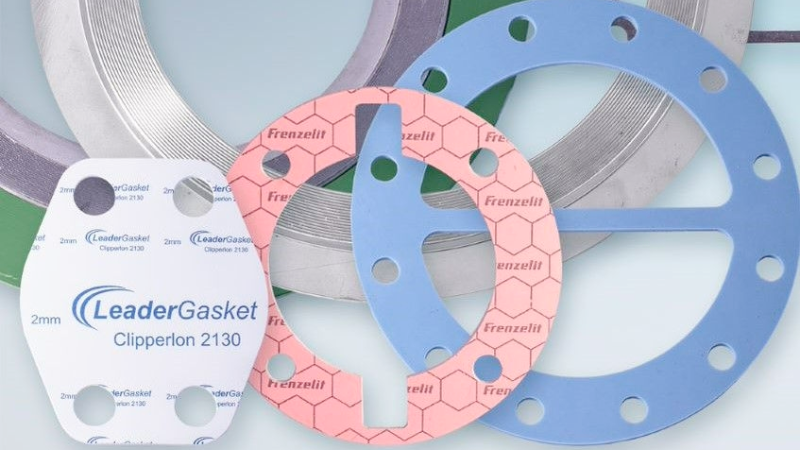
- Quality Assurance and Control: With traceability, manufacturers can identify when and where a gasket was produced. If any quality issues arise, it’s easier to zero in on the source of the problem. It could be a faulty batch of material, a machine error, or a human mistake. Once identified, the manufacturer can address the issue promptly, preventing further faulty production and potentially saving significant costs and time.
- Regulatory Compliance: For the automotive industry, adhering to various regulatory standards is a must. Having clear traceability helps demonstrate compliance with these standards, showing that the materials used meet the necessary specifications and that all processes were carried out correctly.
- Consumer Safety and Recall Efficiency: In the case of a recall, knowing exactly which vehicles received the faulty gaskets can allow for a targeted recall, limiting disruption and minimizing the impact on consumers and the manufacturer.
- Improved Reputation: Traceability can boost a brand’s reputation for quality and reliability. It demonstrates a manufacturer’s commitment to quality control and regulatory compliance, fostering trust with customers.
Given these benefits, it’s clear that gasket material traceability is not just a good-to-have, but a necessary aspect in the automotive manufacturing industry.
Reasons for the Necessity of Gasket Material Traceability in the Automotive Industry
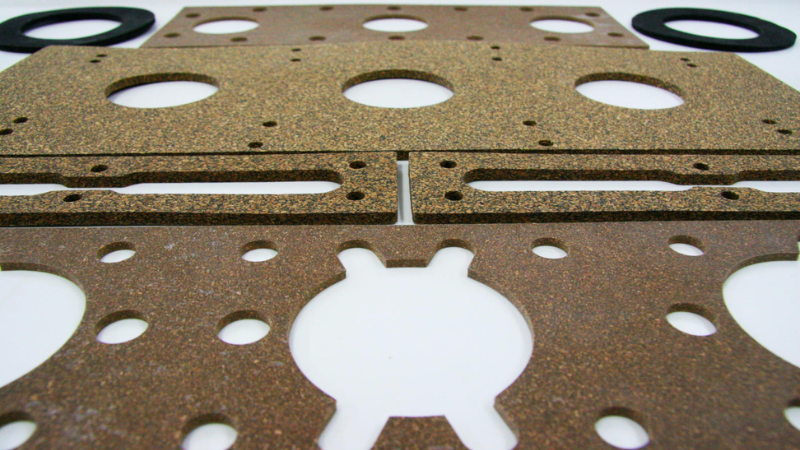
Automobile manufacturers understand the critical importance of ensuring the safety and reliability of their vehicles. One area that requires careful attention is the traceability of gasket materials used in automotive assembly. This article explores the reasons why gasket material traceability is necessary in the automotive industry.
Preventing counterfeit or substandard gaskets from entering the supply chain
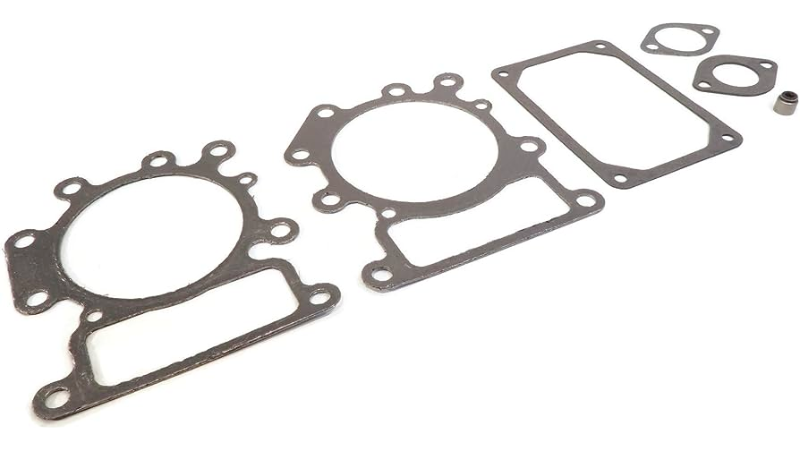
Counterfeit or substandard gaskets can have disastrous consequences for both automobile manufacturers and consumers. These inferior products may not meet the required specifications, leading to potential leaks, engine failures, or even accidents. By implementing robust traceability systems, automobile manufacturers can effectively prevent counterfeit or substandard gaskets from entering their supply chains.
Traceability enables manufacturers to track every step of a gasket’s journey, from its origin to its final destination on a vehicle assembly line. By verifying authenticity and quality at each stage, any suspicious or non-compliant products can be identified and removed before they cause harm. This ensures that only genuine and reliable gaskets are used in vehicle production.
Tracing back defective products to their source for quality control purposes
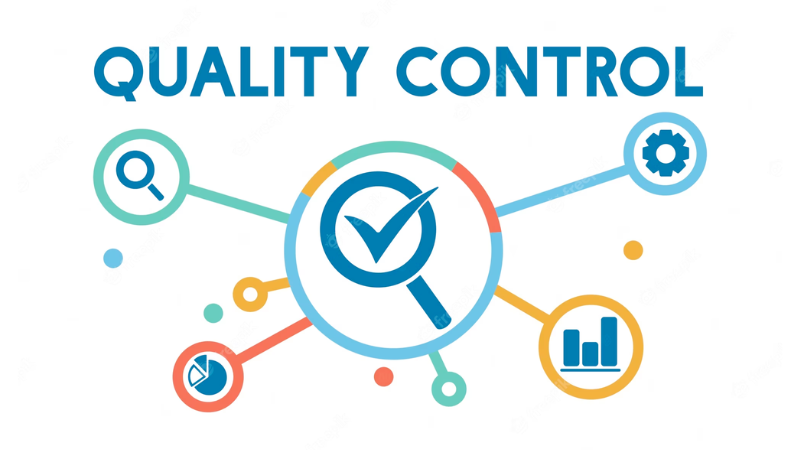
In an industry where product quality is paramount, it is essential to identify and rectify any defects promptly. Gasket material traceability plays a crucial role in this aspect by allowing manufacturers to trace back defective products to their source.
By accurately tracking each component’s origin and manufacturing process, automobile manufacturers can quickly identify which supplier or production batch is responsible for producing faulty gaskets. This information enables them to take immediate corrective actions such as halting production from specific sources, conducting thorough inspections, or implementing stricter quality control measures.
Meeting regulatory requirements for safety and environmental standards

The automotive industry operates within stringent regulatory frameworks aimed at ensuring safety and environmental responsibility. Compliance with these regulations is not only a legal obligation but also vital for maintaining brand reputation and customer trust.
Gasket product and material traceability is instrumental in meeting these regulatory requirements. By maintaining comprehensive records of gasket materials, their sources, and compliance certifications, automobile manufacturers can demonstrate due diligence and adherence to safety and environmental standards. This information is invaluable during audits or inspections by regulatory bodies.
Benefits of Traceable Gasket Materials in the Automotive Industry
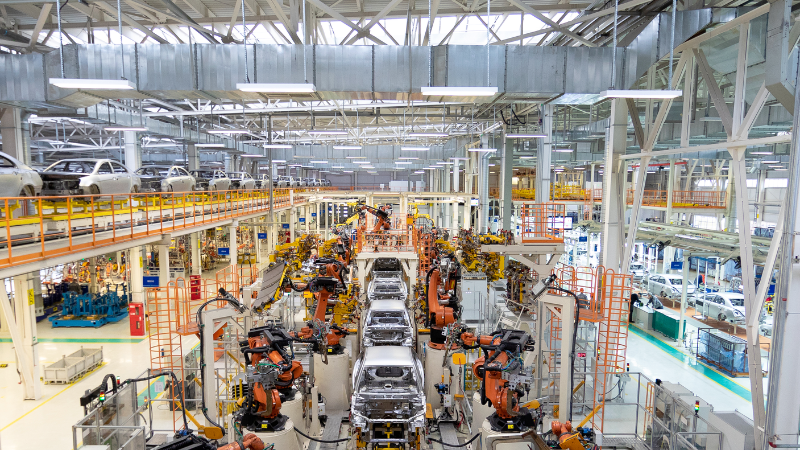
Implementing traceability for gasket materials in the automotive industry yields numerous benefits that span across the entirety of the supply chain. Not only does it allow for a more robust and reliable quality control process, but it also improves safety measures, compliance with regulatory standards, and the overall efficiency of the manufacturing process. Let’s delve deeper into these advantages:
- Enhanced Quality Control: Traceability provides a comprehensive overview of the production process of each gasket. This enables manufacturers to effectively track and monitor the quality of their products, facilitating swift detection and rectification of any anomalies that may occur during the manufacturing processes.
- Improved Safety Measures: Risks increase because the sandwiching layer between two components is suddenly sensed as a weak link. This is why a properly stamped traceability code is important to guarantee safe function. With traceability, if a safety issue arises, manufacturers can quickly identify the exact batch of gaskets, helping to mitigate potential risks effectively and promptly. This means fewer errors, less waste, and most importantly, safer vehicles on the road.
- Compliance with Regulatory Standards: The automotive industry is regulated by several stringent standards. Traceable gasket materials allow manufacturers to demonstrate adherence to these standards, such as ISO/TS 16949, thereby ensuring that their operations are compliant and up to par with the industry’s quality expectations.
- Efficient Recall Processes: In the event of a product recall, traceability can expedite the identification of vehicles equipped with faulty gaskets, thereby minimizing the impact on customers and reducing costs associated with the recall process.
- Boosted Customer Confidence: Traceability acts as a testament to a manufacturer’s commitment to quality, safety, and transparency. It boosts customer confidence and trust in the brand, potentially leading to improved customer loyalty and a stronger market position.
In summary, the benefits of traceable gasket materials in the automotive manufacturing industry are multifaceted and substantial. Incorporating traceability into the manufacturing process is a strategic decision that can significantly enhance the performance, safety, and overall value of automotive products.
Case Studies of Companies That Have Benefited from Traceable Gasket Materials
Traceable gasket materials have proven to be a game-changer for automotive manufacturers, leading to improved operational efficiency, cost savings, and increased customer satisfaction. Let’s take a closer look at some success stories that highlight the benefits of using traceable gaskets.
Case Study 1: Ford Motor Company
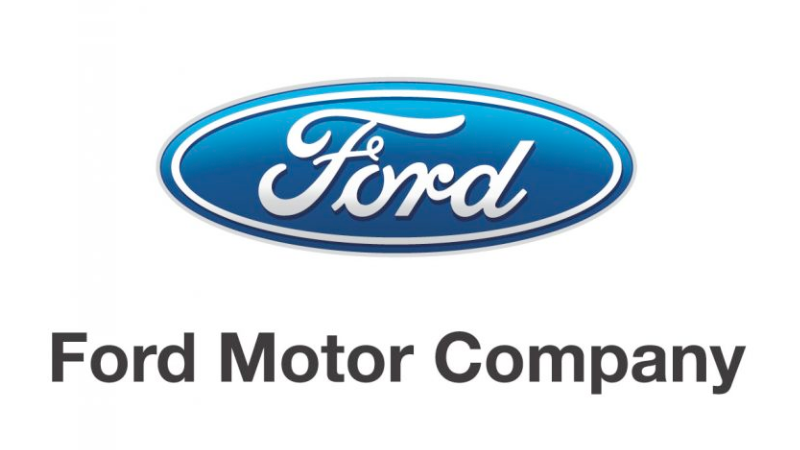
Ford Motor Company, one of the pioneers in the automotive industry, implemented a traceability system for their gasket materials. They quickly recognized the benefits as it led to a significant reduction in their warranty costs. When a series of leaks were reported in a particular vehicle model, Ford was able to swiftly trace the faulty gaskets back to a particular batch of material from a specific supplier. This allowed them to quickly isolate and resolve the issue without impacting the entire line of production.
Case Study 2: BMW Group
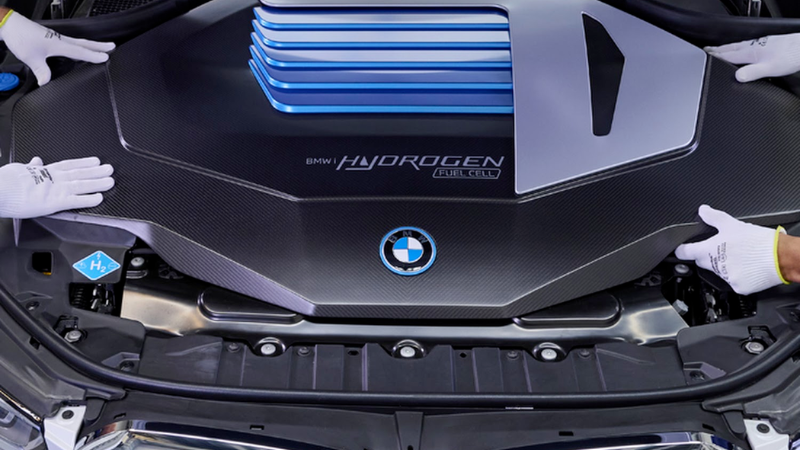
BMW Group adopted a traceability strategy for its gasket materials as part of its commitment to quality and safety. During a random quality check, they identified a minor inconsistency in the composition of a batch of gaskets. Through traceability, BMW was able to pinpoint the exact cars fitted with the gaskets from the concerned batch, making it possible for them to proactively reach out to the customers and perform necessary replacements, thereby preventing any potential failures on the road.
These case studies demonstrate how the traceability of gasket materials can significantly enhance a company’s ability to maintain quality, safety, and customer satisfaction, further solidifying its importance in the automotive industry.
Ensuring Quality: Gasket Edge Quality Assurance
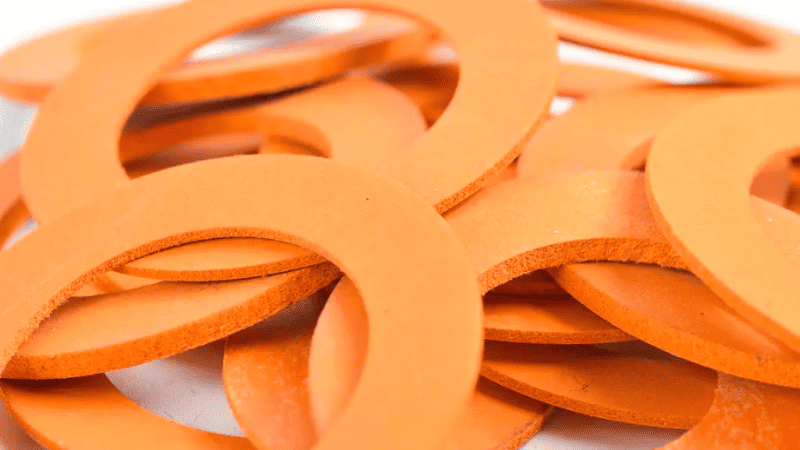
Gasket Edge Quality Assurance is a crucial part of the manufacturing process for gaskets. It encompasses procedures that ensure the gaskets are manufactured precisely according to the required specifications. In the automotive industry, even the minutest deviation can cause issues like leaks, loss of pressure, and overall performance degradation.
Several parameters determine the edge quality of gaskets. These include the smoothness of the edges, the absence of burrs or frayed edges, and the consistency in the cut quality across the entire length of the gasket.
- Cut Precision: The edges of the gasket should align precisely with the design. Any slight variations can lead to leaks, compromising the functionality of the vehicle system.
- Material Integrity: The material of the gasket should not be compromised during the cutting process. There should be no cracks or tears at the edges, which could affect the performance of the seal.
- Dimensional Accuracy: The gasket should adhere strictly to the specified dimensions in its design. This includes the thickness of the gasket, which plays a significant role in the effectiveness of the seal.
To ensure gasket edge quality, manufacturers must implement strict quality control processes and use advanced manufacturing techniques. This includes using high-quality cutting tools and machinery, regular inspections and audits, and traceability to ensure the highest standards of quality are maintained consistently.
Testing and Certifying Gasket and Seal Materials

Testing and certification of gasket and seal materials are fundamental aspects of the manufacturing process, ensuring the quality, durability, and effectiveness of the final product. Let’s look at some key areas of this process:
- Material Testing: This involves assessing the physical properties of the gasket material, such as tensile strength, elongation, compression set, hardness, and tear resistance. These tests are necessary to ensure the material can withstand the operating conditions of the vehicle, including temperature fluctuations, pressure changes, and exposure to various fluids.
- Chemical Resistance Testing: Since automotive gaskets are often exposed to oils, fuels, and other chemicals, it’s crucial to test their resistance to these substances. This can be achieved through immersion tests, where the gasket material is submerged in a specific fluid and then inspected for any changes in its physical properties.
- Thermal Testing: Automotive gaskets must resist high temperatures, especially those found in the engine compartment. Therefore, materials are often subjected to high-temperature environments to assess their ability to maintain their physical properties and performance levels.
- Certification: Once a gasket material passes all required tests, it can be certified as fit-for-purpose. In the automotive industry, important certifications include ISO/TS 16949 (Quality Management System for Automotive Industry), ASTM (American Society for Testing and Materials) standards, and FDA (Food and Drug Administration) for materials used in food-related applications. Certifications act as a guarantee of quality, ensuring customers they’re buying a product that’s been rigorously tested and approved.
Investing in certified, high-quality gasket materials not only ensures vehicle performance and longevity but also reduces the risk of costly recalls and repairs. It’s an essential part of maintaining a brand’s reputation for quality and reliability.
Conclusion
In conclusion, the traceability of gasket materials in the automotive industry is not just an option—it’s an essential aspect of quality control, risk management, and regulatory compliance.
With the rising demand for superior and reliable vehicles, manufacturers must prioritize traceability to ensure product integrity, enhance customer satisfaction, and foster their competitive edge.
Embark on Your Traceability Journey with Hongju Silicone
The experts at Hongju Silicone have partnered with diverse industries to implement advanced tracking systems and solutions, paving the way for high-quality products and refined processes.
Should you require more insights on how our team could aid you in developing a robust traceability program, please do not hesitate to get in touch.