Rubber Materials: Chemical Industry
The chemical industry uses a wide range of rubber materials for their properties and features. The most common examples include EPDM, Neoprene, Silicone, etc. Let’s look at some of the best ones for this industry:
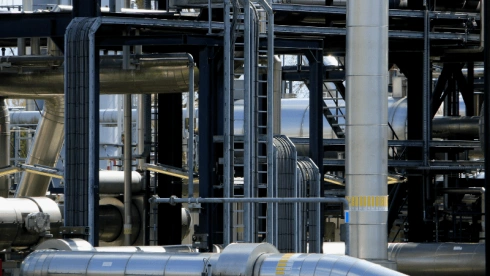
- Neoprene Rubber: neoprene has excellent resistance to oils, chemicals, and fuels, which all play a vital role in the chemical industry. Hence, the most common nitrile rubber molding products used in this industry are seals and gaskets.
- Nitrile Rubber: this rubber material also offers commendable mechanical properties for the chemical industry. These include resistance to oils and fuels, just like neoprene. However, nitrile also withstands high-temperature conditions and regular wear and tear. Hence, chemists often use nitrile O-rings, hoses, and seals.
- EPDM Rubber: famous for its outdoor performance and weather resistance, EPDM is a solid choice for outdoor applications in the chemical industry. Another reason why EPDM stands out includes resistance to ozone. Thus, EPDM seals, gaskets, and hoses are common in outdoor chemical lab applications and experiments.
- Silicone Rubber: Silicone performs exceptionally well in harsh weather conditions like any other synthetic rubber. Hence, chemical applications that involve UV light, high temperatures, and chemicals use silicone-molded rubber products.
- Natural Rubber: we all know natural rubber does not perform as well as other synthetic rubber materials. But then, why does the chemical industry use natural rubber? Natural rubber offers incredible flexibility and elasticity, making it ideal for applications requiring flexible custom-molded rubber products.
Rubber Molding Techniques
Manufacturers mold rubber using different molding techniques. But why? Because each molding method comes with its pros and cons. Let’s have a different look at each and see how the industry benefits from them:
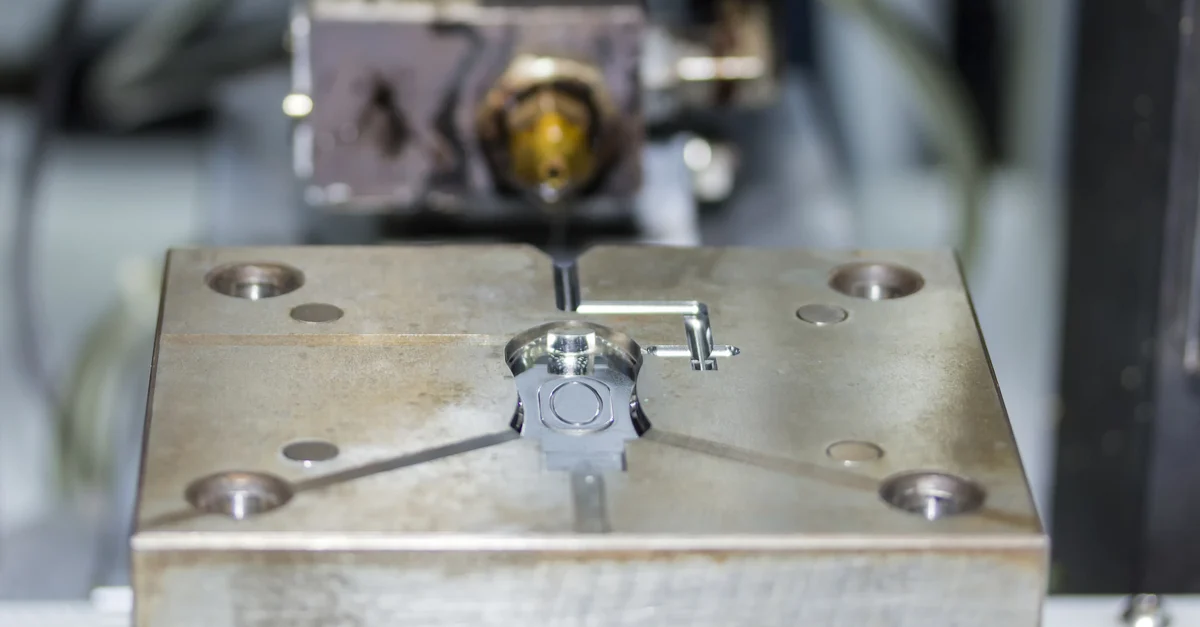
Compression Rubber Molding
Manufacturers take a heated mold for compression molding and fill it with uncured rubber. Upon applying pressure, the mold turns the uncured rubber into the desired shape. Hence, given the simplicity of the process, manufacturers use it for the high-volume production of custom-molded rubber parts.
Transfer Rubber Molding
Transfer molding and compression molding are pretty similar. The only difference lies when the uncured rubber is transferred from the heated mold to a controlled cool area. This helps dry out the complex rubber molding parts entirely and precisely to the desired shape.
Die Cutting
Die cutting is a manufacturing process that uses a die (a specialized tool) to cut, shape, or form rubber material into a desired shape. The dice, typically made of steel, has a shape carved into its surface that corresponds to the desired shape of the final product. Hence, manufacturers put the rubber molding material on top of the die, and then a press applies pressure to the die to cut.
Injection Rubber Molding
Injection rubber molding is most commonly used to produce identical rubber molded parts. That too in bulk quantities. Moreover, this rubber molding technique also allows for high volume production of complex custom-molded rubber components.
The Benefit of Using Molded Rubber Parts for Chemical
Using custom-molded rubber components in the chemical industry has several benefits. Some of the key advantages include the following:
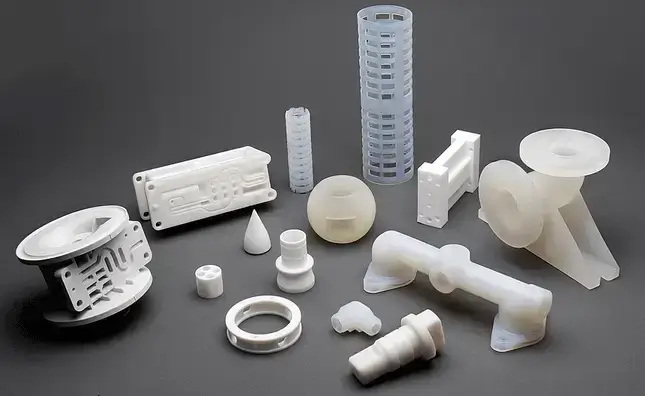
- Chemical resistance: Molded rubber parts have high resistance to various chemicals. Hence, they are ideal for use in environments where chemical exposure is a concern.
- Extreme temperature tolerance: Molded rubber parts can withstand extreme temperatures, making them suitable for high-heat or low-temperature environments.
- Flexibility: Rubber is a naturally flexible material. Moreover, molded and vulcanized rubber parts retain their properties, making them ideal for flexible applications.
- Leak protection: Molded rubber parts can be designed to seal against leaks. Hence, many chemical applications use them for experiments, packaging, and other elements where leak prevention is vital.
- Durability: Rubber, especially synthetic rubber, has incredible durability performance. This makes it ideal for long-term applications where you must rely on molded rubber parts to keep things together. Moreover, it also withstands harsh abrasions and environments pretty well. If you ask to what extent, it depends on the rubber molding material.
- Cost-effective: rubber generally does not cost a lot. The custom rubber molding process is also cost-effective when manufacturers produce rubber parts in bulk. Hence, the low cost of rubber proves beneficial for the chemical industry.
Common Molded Rubber Products for Chemical
The chemical industry uses a variety of rubber-molded products. The most prominent examples include the following:
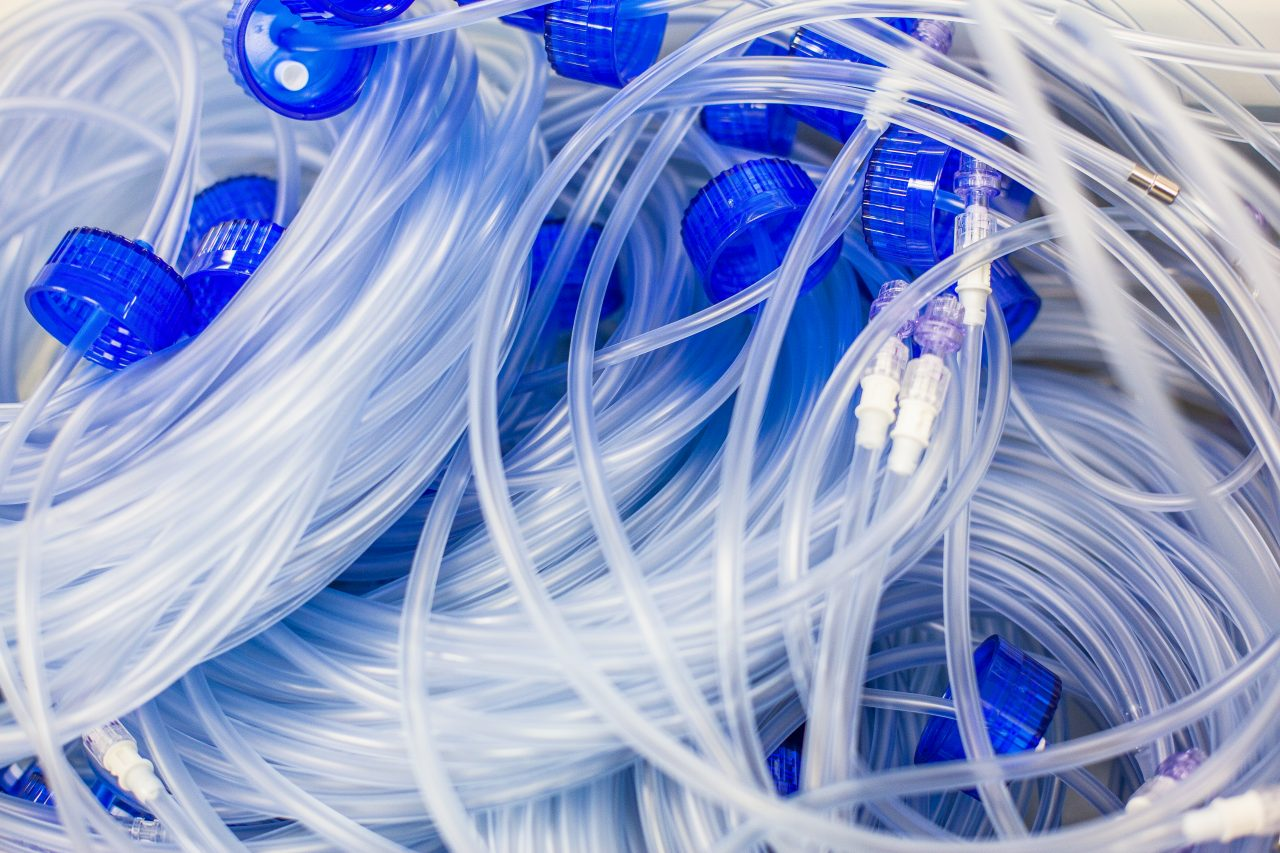
- Gaskets and Seals: These molded rubber parts help create a tight seal between two surfaces. This tight seal, in turn, prevents leaks and protects against chemical exposure.
- Hoses: Rubber hoses help transfer chemicals and liquids between different areas and chemical equipment. They achieve this by preventing any damage to the nearby equipment.
- O-rings: These small, circular, molded rubber parts help create lid seals and other seals needed in chemical laboratories. O-rings are the most common type of molded rubber products used in this industry for industrial and regular applications.
- Diaphragms: this rubber molded part has a specific design that allows you to control the flow in valves and pumps. Hence, many petroleum and chemical companies use rubber diaphragms to regulate the flows in these systems.
- Bellows: These accordion-shaped molded rubber parts absorb movement and vibration in pipes and other equipment. Hence, they successfully protect against leaks and damage.
- Rollers and Wheels: rubber rollers and wheels are incredible for protecting against wear and tear and improving traction. Hence, the chemical industry uses them readily for safety purposes in chemical plants.
- Lining and Coatings: as the name suggests, rubber linings and coatings help keep equipment from chemical exposure. Moreover, they also help minimize wear and tear over time.
How to Choose The Right Molded Rubber Part for Your Need?
Choosing the right molded rubber part for your specific need requires considering several factors. Let’s look at the most important ones:
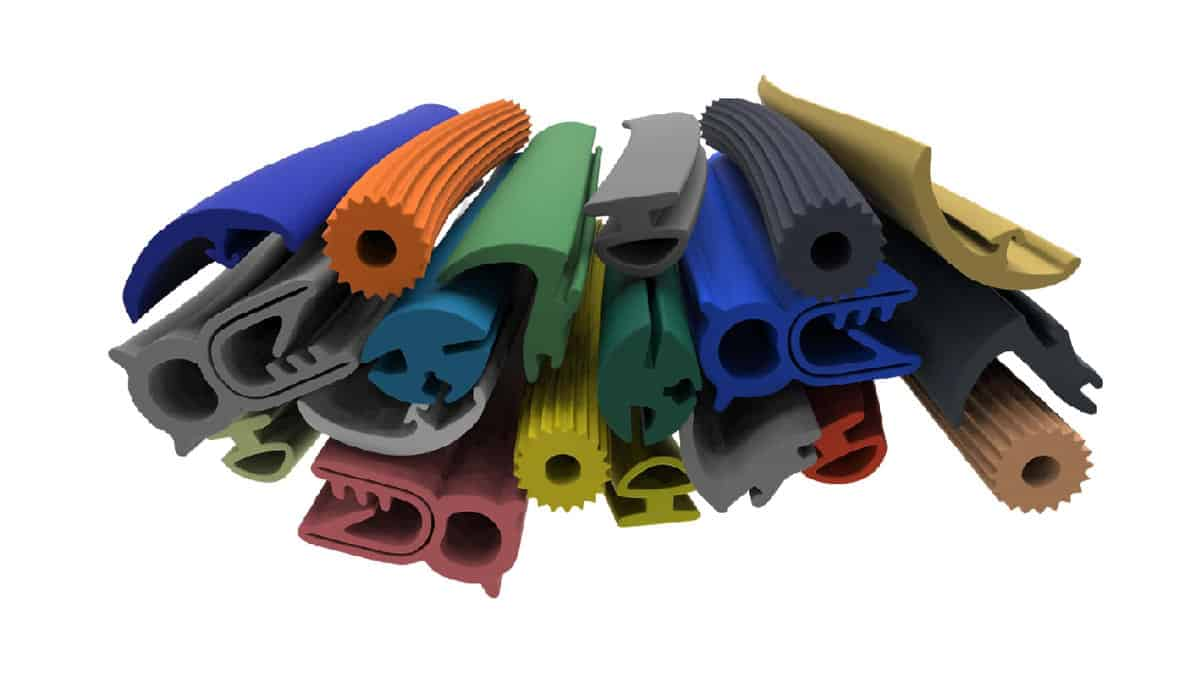
Chemical Resistance
Consider the specific chemicals the part will come in contact with. Based on that, choose a rubber material resistant to those chemicals.
Temperature Tolerance
Different rubber materials can withstand varying temperature ranges. Make sure you know the specific temperature range of your application. Once you know, you can find the right molded rubber part.
Flexibility
Consider if the part needs high flexibility or elasticity. This also varies from application to application; hence, you can choose from various rubber materials and components. Similarly, if the application requires a stiff fabric, you must select a material with opposite properties.
Durability
You also must consider the amount of wear and tear the part will experience. Based on the information, you can decide on the rubber material, size, and quality.
Cost
Definitely one of the most critical factors, as you can’t go beyond your budget. Hence, look for cheaper alternatives if you have a low budget. Otherwise, look for reliable manufacturers who offer good quality for a lesser price.
Quality
Choose a reputable, experienced manufacturer that uses high-quality rubber molding processes and raw materials.
Size and Shape
Consider the size and shape of the part. Once you know what you want, you can choose a manufacturer capable of producing the specific size and shape required.
Faqs About Chemical Molded Rubber Parts
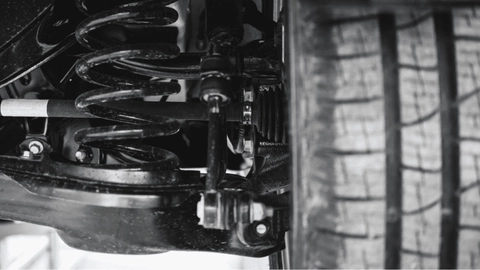
How are rubber parts molded?
Rubber parts are molded using custom rubber molding techniques. Most manufacturers use multiple techniques to achieve a variety of products with varying shapes, sizes, precisions, and properties. The most common styles include injection rubber molding, compression rubber molding, and transfer rubber molding.
What is molded rubber for chemicals?
Molded rubber for chemicals includes all molded rubber parts specifically designed for use in the chemical industries. These rubber parts provide protection and have a long life which helps avoid mechanical failures.
What are some common molded rubber parts for chemicals?
The chemical industry uses rubber seals, gaskets, hoses, bellows, and O-rings. Manufacturers offer them a variety of rubber materials based on customer needs and demands.
How do I mold my rubber parts?
It is not advisable to mold your rubber parts since it’s a professional process. Hence, one should always rely on a reliable manufacturer with the experience, industrial equipment, and expertise to mold rubber into different parts.
Conclusion
The rubber industry has evolved exponentially over the years. The progress has dramatically benefitted the chemical industry. So much so that today rubber is the most prominent material found in chemical equipment. Hence, the market has great demand for these products.
Looking for A Reliable Manufacturer That Offers Quality Rubber Molded Parts for Chemicals?
Look no further! Hongju has the capabilities, capacity, and experience to offer you great deals on rubber products. We have an open-door policy for all sorts of customers and order quantities. You can also ask for a prototype by contacting our design team directly for custom rubber molding services.