Different prototyping methods are used in the rubber industry, but selecting the right one requires carefully balancing the client’s needs with what different processes can achieve.
To demonstrate how great rubber prototypes are made, we’ll be explaining how this process is conducted at Hongju Silicone. We’ll examine the different prototyping methods, our in-house approach to rubber prototyping, and why our solutions will be right for you.
What is Rubber Prototyping?
Rubber prototyping is the process of creating early samples of products that will be made from rubber materials. This includes products that are to be made using both natural rubber and synthetic elastomers such as neoprene, SBR, and silicone rubber.
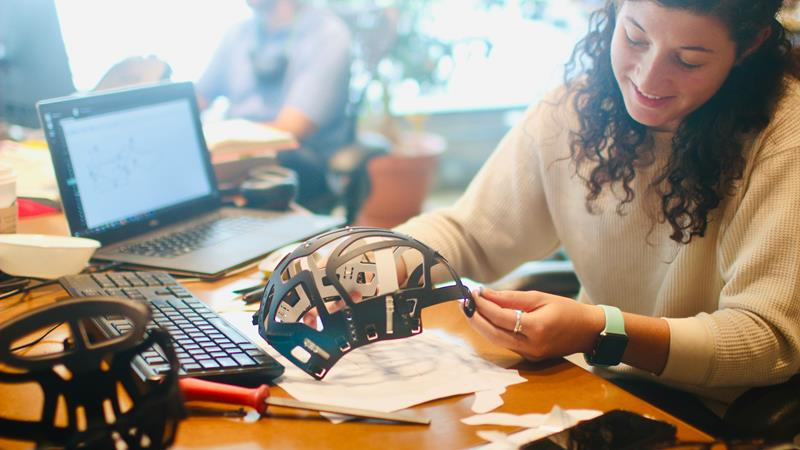
Prototyping can be done to demonstrate a concept or confirm the look and feel of the final product. It can also involve creating a functional part that can demonstrate the working of the finished product and be subjected to physical testing.
The physical properties of rubber such as softness and elasticity make it harder to machine, especially when accurate detail is required. As a result, creating a prototype of a rubber part can be difficult.
Inquire About Our Silicone and Plastic Products!
Four Common Rubber Prototyping Methods
Four common prototyping methods are used for natural rubber and other elastomers. These are:
- 3D Printing
- Injection Molding
- Stereolithography
- CNC milling
3D Printing
3D printing forms parts by depositing layers of material on top of each other to create the final 3D shape. It is an additive manufacturing process.
Modern 3D printing works with many materials including plastics (thermoplastics and thermosets), metals, and some elastomers. 3D printing flexible materials like elastomers, can be challenging without the right printing technology and technical expertise.
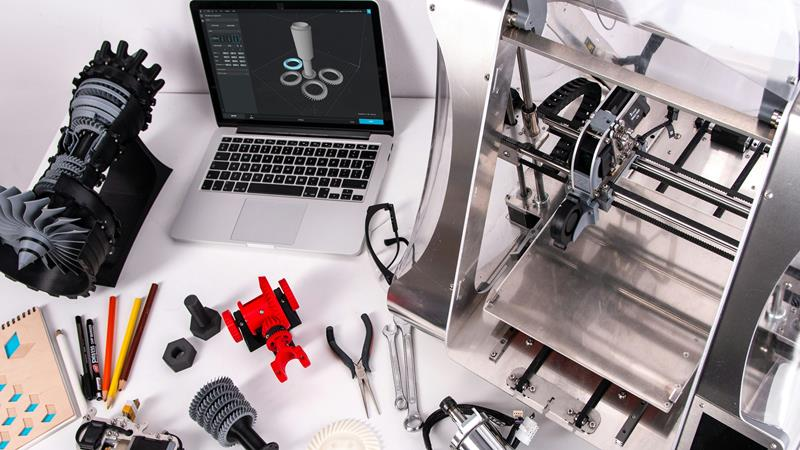
3D printing of prototypes has several advantages including:
- The ability to produce complex geometries that can’t be achieved using other prototyping methods.
- If the CAD design is ready, the lead times for producing 3D-printed prototypes are negligible.
- Compared to other prototypes, the cost of 3D-printed prototypes is very low.
This prototyping method also has significant disadvantages that make it unsuitable for some rubber prototypes. These include:
- Poor surface quality due to the presence of layer lines.
- Sanding and other forms of post-processing may be required to produce acceptable prototypes.
- Parts may have artifacts left by supports.
- 3D printed prototypes are often unsuitable for testing strength and other properties.
Injection Molding
Injection molding is a manufacturing process commonly used for the large-scale production of plastic and rubber products. The parts are formed by injecting a liquid or molten material into a closed mold.
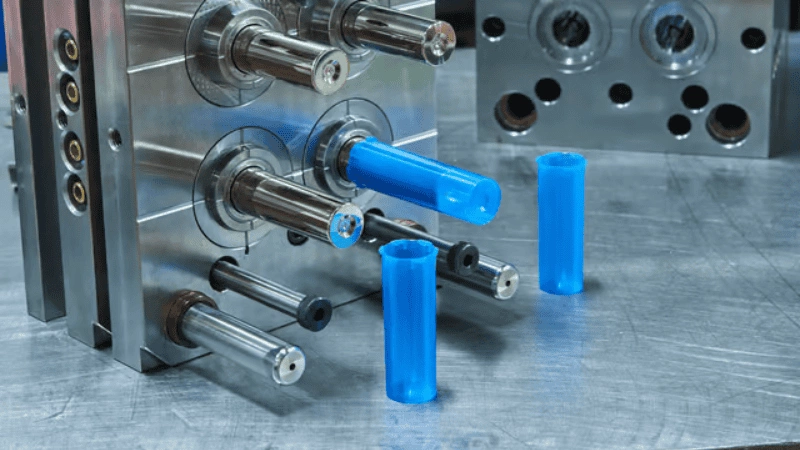
Prototype Injection molding uses mold materials that are cheaper and easier to machine such as aluminum and ‘soft’ steels.
Due to its high costs, prototype injection molding should be reserved for the latter stages of product development when injection-molded prototypes may be necessary to produce accurate parts that can be tested and to test the manufacturability of the final design.
Advantages of injection molding for prototypes include:
- It can achieve the exact geometry of the final part.
- It can be used for parts with complex designs.
- Product properties such as strength can be accurately tested.
- It can be used to test the production process and improve the manufacturability of injection-molded products.
The main disadvantages of injection molding prototypes are:
- Mold creation is very expensive compared to 3D printing.
- Lead times are very long due to the time needed to prepare molds.
- Not suitable for testing multiple iterations of the same product.
Stereolithography.
Stereolithography is another additive manufacturing process. It uses light to selectively cure a resin. The resin is cured in successive layers to form the three-dimensional part.
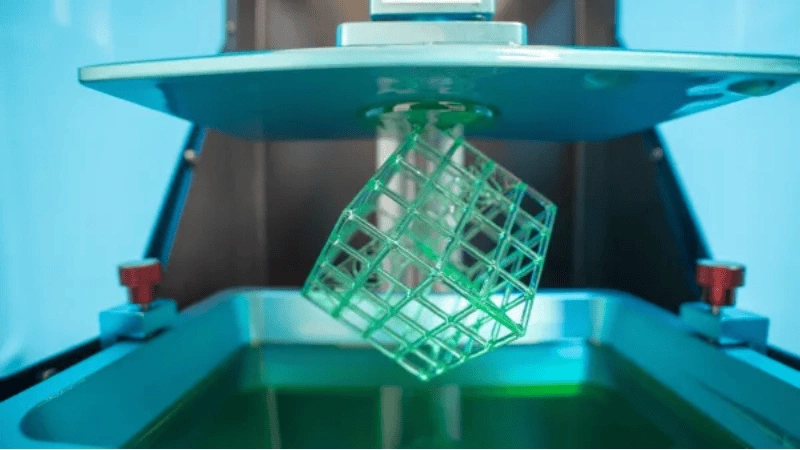
Stereolithography has a higher resolution than filament 3D printing resulting in thinner layers and higher product accuracy.
The advantages of stereolithography are:
- It has negligible lead times.
- For prototyping and low-volume production, it is inexpensive.
- It can produce parts with complex geometries at a higher detail than filament 3D printing.
The disadvantages of stereolithography for prototyping are:
- The parts produced can’t undergo accurate mechanical testing.
- Supports may leave artifacts on the products.
- Layer lines may be visible on some prototypes.
CNC Milling
In this prototyping method, the final part is cut or curved from a block of rubber material. The prototypes made are of high quality but are relatively simple in shape. Prototypes with hollow parts and complex shapes are not suited to this method.
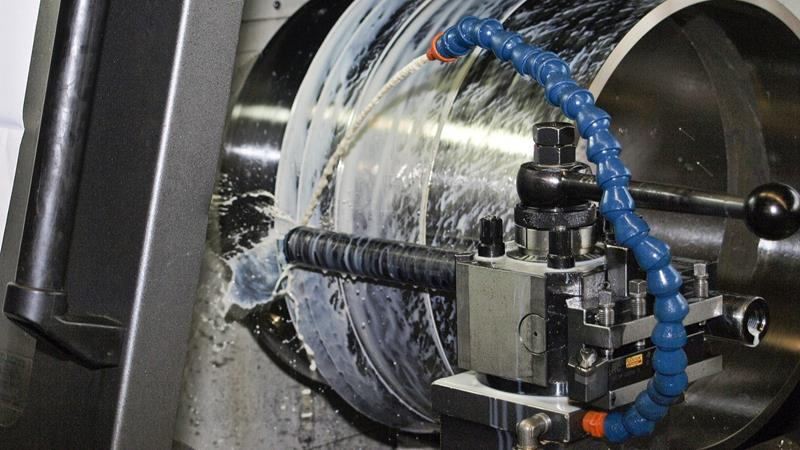
The advantages of CNC milling of prototypes are:
- Creates high-quality products
- The process has a lower lead time than injection molding
The disadvantages of CNC milling of prototypes are:
- It can’t be used to produce very complex parts and may still be challenging for prototyping parts with low to mid levels of complexity.
- The intended material must have a minimum level of hardness to be milled.
Inquire About Our Silicone and Plastic Products!
Hongju’s Rubber Prototyping Process
At Hongju Silicone, clients are treated to a comprehensive five-step process to ensure their prototyping objectives are met. These steps are described below.
1. Initial Consultation
This is usually the first meeting between the client and the team of experts at Hongju. This is a high-level meeting where the issues discussed include the overall project requirements, the design specifications of the final product, and the objectives the prototype must meet.
2. Design and Engineering
In this step, the prototype is designed using CAD software. If the client already has a CAD design, it can be analyzed and optimized to ensure it is ready for prototyping. Different prototyping methods will have different design standards.
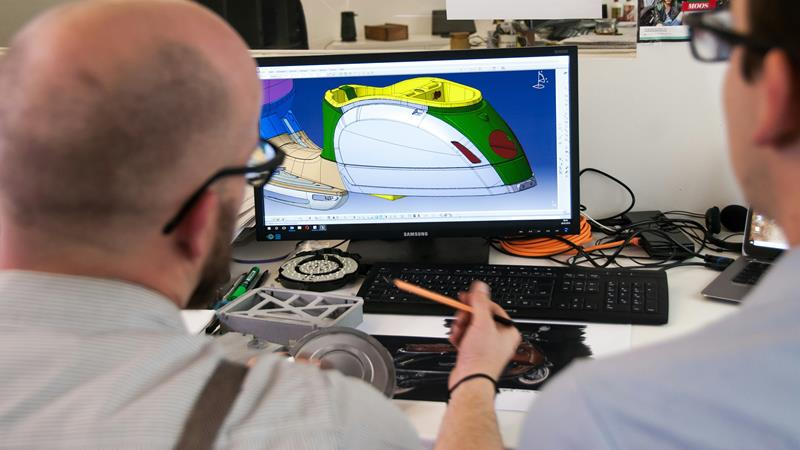
The experience of the engineering team at Hongju is important at this stage to ensure the design is compatible with the prototyping method.
3. Selection of Prototyping Method
This step goes hand in hand with the engineering and design phase. Depending on the objectives set out in the initial consultation, a suitable prototyping method is selected.
Selection of one method or another may require modifying the design to ensure excellent quality and a short production time. At Hongju Silicone, the available prototyping methods include:
- 3D printing: This method is great for producing multiple quick iterations of the same product. It is ideal for early prototypes and can advise basic design decisions.
- CNC machining: For compatible materials, prototypes can also be CNC machined to attain precision parts.
- Molding: This method is used for parts with complex geometries that also need to undergo testing of physical properties and thermal characteristics.
4. Material Selection
Hongju Silicone’s clients also receive guidance on choosing the best rubber material for their products. The team’s experts can advise on material specifications, e.g., which materials will perform well in certain operating conditions/environments and which will achieve the desired product function.
5. Quality Assurance
Quality assurance is a key consideration throughout the prototyping process at Hongju Silicone, and even after the completion of the prototype.
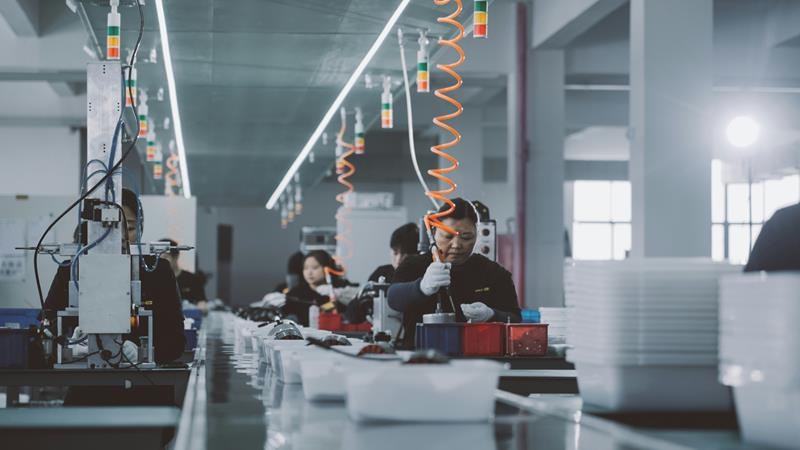
Strict quality control measures are implemented at every step to produce prototypes that are consistent with the client’s specifications. Open lines of communication are also maintained between the team and the client to ensure the final prototype meets their needs.
Benefits of Choosing Hongju Silicone for Rubber Prototyping
Working with Hongju Silicone will significantly boost your rubber prototyping efforts. The benefits you’ll enjoy while working with this company include:
- Expertise and experience: Hongju has been in the rubber manufacturing industry for over 23 years. The expertise and experience of the team there are unmatched and will be valuable in material selection, prototyping method selection, and making design and engineering decisions.
- State-of-the-art Facilities: Hongju Silicone’s facilities are state-of-the-art and prototyping is done with the latest machines and equipment to produce high-quality results.
- Customization and flexibility: Prototyping at Hongju is flexible and clients can get custom prototypes to suit different needs cost-effectively.
- Short lead times: CNC machined prototypes can be ready in as little as 3 days.
Inquire About Our Silicone and Plastic Products!
Conclusion
Rubber prototyping will take you one step closer to getting your product to market, but working with the right prototyping team is important. Different prototyping methods are available and not all will meet your needs or budget.
Hongju Silicone uses a prototyping process that takes advantage of their team’s experience while ensuring their clients’ expectations are considered. This company’s clients enjoy many benefits including short lead times and different customization options for prototypes.
Explore Modern Rubber Prototyping With Hongju Silicone
Are you interested in manufacturing prototypes for your rubber product? Hongju Silicone has the solutions you need. We offer diverse prototyping solutions for different materials and product types and our skilled team is equipped with years of experience in cost-effective rubber prototyping.
Contact us today and find out how we will amplify your prototyping efforts.