Prepare yourself and be prepared to uncover the ways in which becoming skilled in these methods can completely transform the way you produce goods!
What are Rubber Molding Techniques?
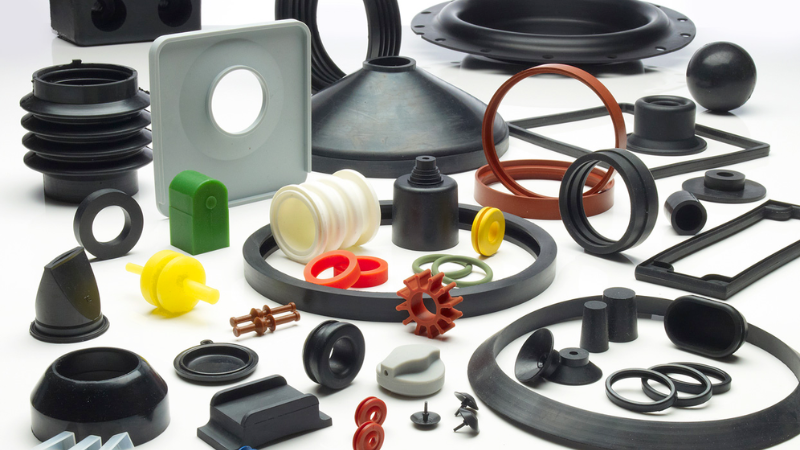
Rubber molding involves transferring, compressing, or injecting natural rubber material into a metal mold, transforming flexible, naturally-derived elastic polymers into functional products.
Under the watchful eye of skilled technicians and engineers, this process applies pressure and heat at approximately 140-160 degrees Celsius, resulting in a customized product with unique metal bonding.
The various rubber molding techniques are categorized based on specific variations of molded rubber components, required product specifications, and the final manufacturing process.
Types of Rubber Molding Techniques
Rubber molding techniques are essential in the manufacturing industry for producing a wide range of rubber parts. These rubber compression molding techniques allow manufacturers to create products with different shapes, sizes, and complexities.
Compression Molding
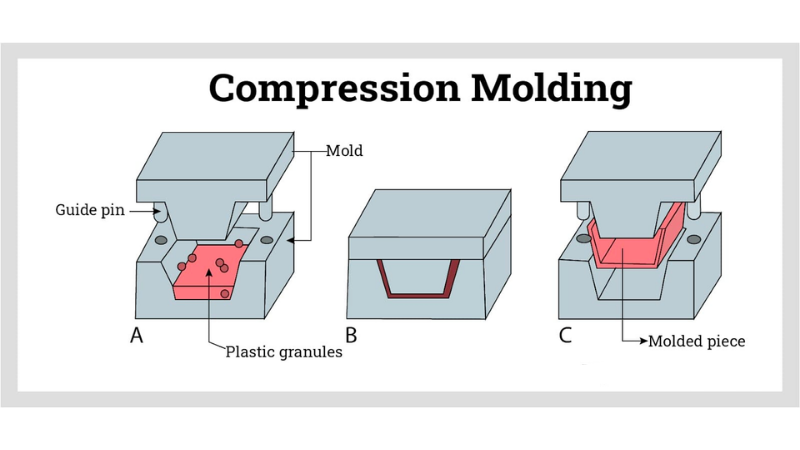
Compression molding is a widely used technique for producing large quantities of simple rubber parts. The process involves placing a pre-measured amount of uncured rubber material into a heated mold cavity. The mold is then closed, and pressure is applied to compress the rubber. This pressure helps shape the raw material according to the design of the mold.
One advantage of compression molding is its ability to handle high-volume production efficiently. It also allows for cost-effective manufacturing since it does not require complex machinery or extensive setup time. Compression molding can produce durable and long-lasting rubber parts suitable for various applications such as rubber gaskets, seals, and O-rings.
Transfer Molding
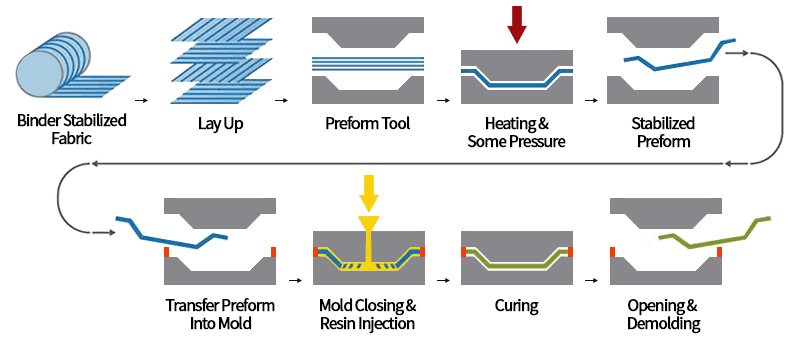
Transfer molding is often preferred for more intricate designs and better control over material distribution. This technique combines elements of both compression and injection molding processes. It involves heating a measured amount of uncured rubber in a separate chamber called a pot before transferring it into the mold cavity.
Transfer molding offers several advantages over other techniques. Firstly, it enables manufacturers to create complex shapes with fine details that may be challenging to achieve using the compression molding process alone. Secondly, this method allows for precise control over material flow and distribution within the mold cavity.
Moreover, the transfer molding process also provides shorter cycle times compared to compression molding since it utilizes additional heat sources during the curing process. This results in faster production rates while maintaining consistent quality across multiple parts.
Injection Molding
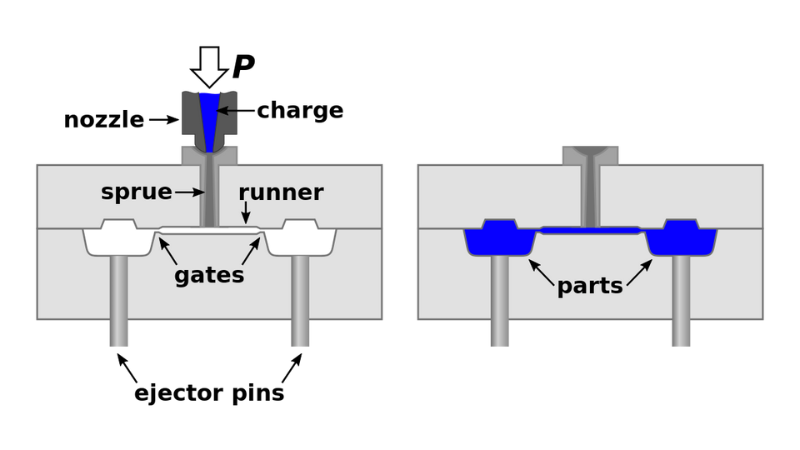
Injection molding stands out as one of the most advanced rubber molding techniques available today due to its high precision, consistency, and rapid production capabilities. It involves injecting molten rubber material into a closed mold under high pressure.
The process begins with heating the raw rubber material until it becomes fluid. Then, the molten rubber is injected into the mold cavity through a nozzle. Once inside the mold, the material cools and solidifies, taking on the shape of the mold.
Injection molding offers exceptional precision and repeatability, making it ideal for producing intricate and complex rubber parts with tight tolerances. This technique also allows for efficient production rates, making it suitable for large-scale manufacturing.
Common Materials Used in Rubber Molding Techniques
Rubber molding techniques utilize a variety of materials to create high-quality rubber products, rubber components, and parts. From natural rubber to synthetic options, each material offers unique properties suited for specific applications. Let’s explore some common materials used in rubber molding techniques.
Natural Rubber
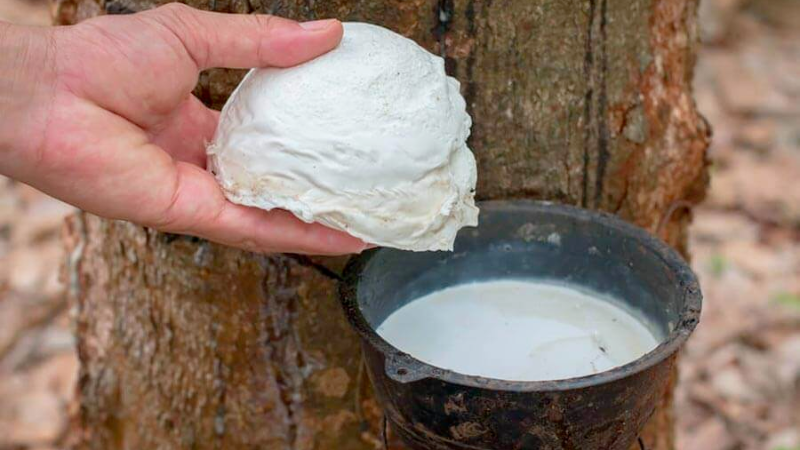
Derived from latex, natural rubber is a popular choice due to its exceptional elasticity and tear resistance. It provides excellent flexibility and resilience, making it ideal for various applications that require durability and stretchability. Natural rubber compounds are commonly used in automotive parts like tires, seals, gaskets, and hoses.
Synthetic Rubbers
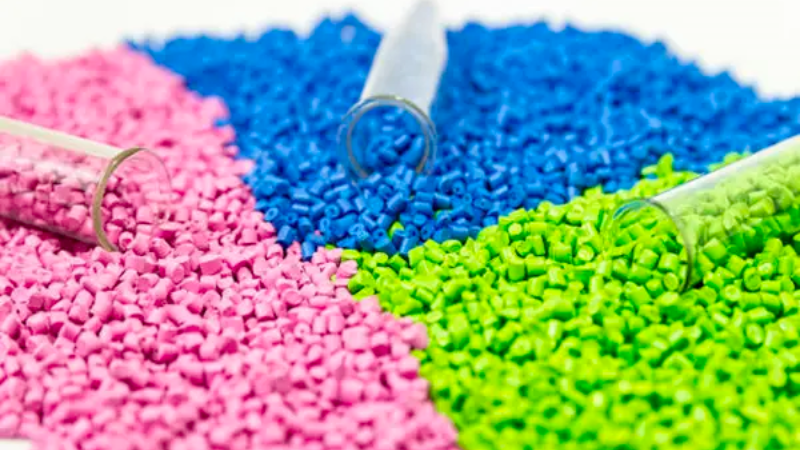
Synthetic rubbers offer specific properties that make them suitable for diverse applications. Some commonly used synthetic rubbers include:
- Styrene Butadiene Rubber (SBR): SBR combines the advantages of styrene and butadiene polymers. It exhibits good abrasion resistance and stability over a wide temperature range. SBR is commonly utilized in conveyor belts, shoe soles, adhesives, and other industrial products.
- Ethylene Propylene Diene Monomer (EPDM): EPDM possesses excellent weather resistance, making it ideal for outdoor applications such as roofing membranes and automotive weatherstripping. Its resistance to UV radiation and extreme temperatures ensures long-lasting performance.
- Nitrile Rubber: Known for its oil resistance, nitrile rubber is widely used in industries where contact with petroleum-based fluids or chemicals is common. This material finds application in fuel hoses, gaskets for oil seals, O-rings, gloves, and more.
Thermoplastic Elastomers (TPE)
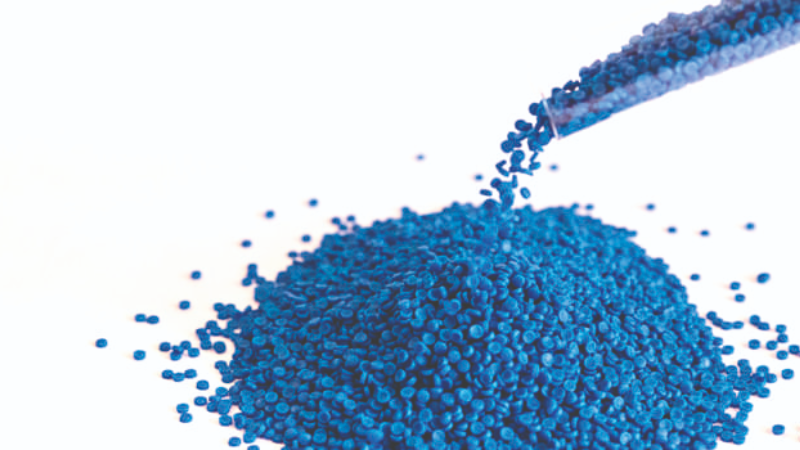
Thermoplastic elastomers combine the advantages of plastic and rubber materials. They can be easily melted down multiple times without undergoing degradation or losing their physical properties like elasticity or flexibility. TPEs are highly versatile and find use in various industries such as consumer goods manufacturing, automotive, and medical equipment production.
In addition to the materials mentioned above, there are other specialized rubber materials available for specific applications:
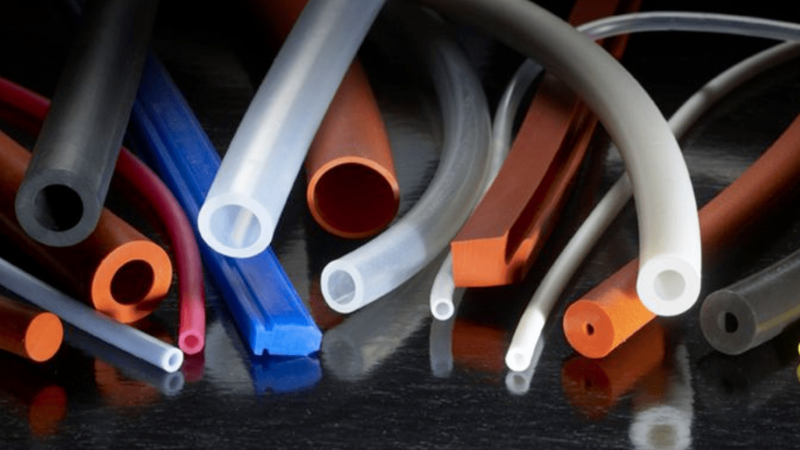
- Silicone Rubber: Known for its high temperature resistance, silicone rubber is commonly used in electrical insulation, cooking utensils, medical devices, and automotive components.
- Neoprene Rubber: Neoprene exhibits excellent resistance to chemicals and weathering. It finds application in wetsuits, industrial hoses, gaskets, and orthopedic braces.
- Uncured Rubber: This refers to raw rubber that has not undergone the vulcanization process. It is often used in prototyping or custom applications where specific properties need to be tested before finalizing the rubber compound.
How to Choose the Correct Rubber Moulding Technique?
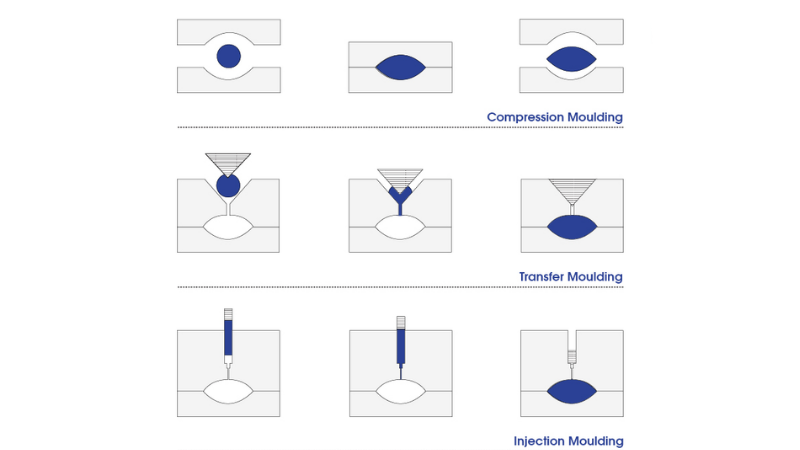
Choosing the correct used rubber injection molding technique is crucial for the success of any project. There are several factors that need to be considered in order to make an informed decision.
Let’s take a closer look at these factors and how they can help you choose the right technique for your needs.
- Product Design and Complexity: Assess the design complexity of the desired rubber product. For intricate and detailed shapes, injection molding or injection-compression molding may be more suitable. Compression molding is better for simpler shapes, while extrusion molding is ideal for products with a consistent cross-section.
- Material Properties: Different rubber materials exhibit varying characteristics, such as hardness, elasticity, and chemical resistance. Ensure that the chosen molding technique is compatible with the specific rubber material required for the product.
- Production Volume: The anticipated production volume plays a significant role in selecting the molding technique. Injection molding is preferred for high-volume production due to its efficiency, while compression molding is suitable for lower quantities and custom orders.
- Tolerance and Precision: Consider the level of precision required for the product. Injection molding generally offers higher precision and tighter tolerances compared to other techniques.
- Cost and Budget: Evaluate the budget and cost implications associated with each molding technique. Complex techniques like injection molding may require higher initial tooling costs but can be more cost-effective in large-scale production.
- Lead Time: Assess the time constraints for production. Some techniques, like compression molding, may have shorter lead times compared to others, making them suitable for quick turnaround projects.
- Environmental and Safety Regulations: Consider any environmental or safety regulations that may apply to the chosen molding technique, especially if specific rubber materials or processes are subject to compliance requirements.
- Expertise and Equipment: Evaluate the capabilities and expertise of the manufacturing facility. Ensure that they have the necessary machinery and skilled personnel to execute the chosen molding technique effectively.
By carefully considering these factors, you can make an informed decision and select the most appropriate rubber molding technique that aligns with the product’s requirements, budget, and production volume, ultimately leading to successful and efficient manufacturing processes.
How Can You Ensure that Your Rubber Molding Project is Successful?
Ensuring the success of a rubber molding project involves careful planning, effective communication, and attention to detail throughout the entire process. Here are some key steps to help guarantee a successful outcome:
Properly Design Your Mold
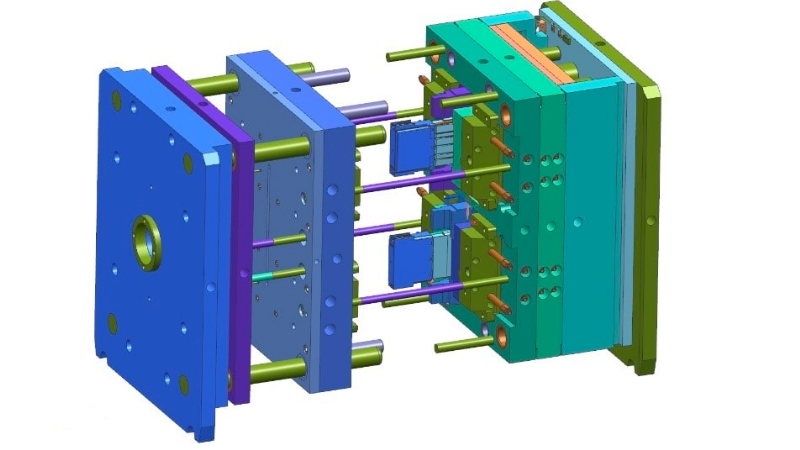
The mold design is a critical aspect of rubber molding projects. It is essential to work closely with experienced rubber injection molding designers who understand the intricacies of rubber materials and molding processes.
The mold design should consider factors such as parting lines, draft angles, gate placement, and venting to ensure proper filling and complete replication of rubber molded parts with the desired shapes and dimensions. Accurate mold design minimizes the risk of defects and ensures the final product meets the required specifications
Use High-quality Molds
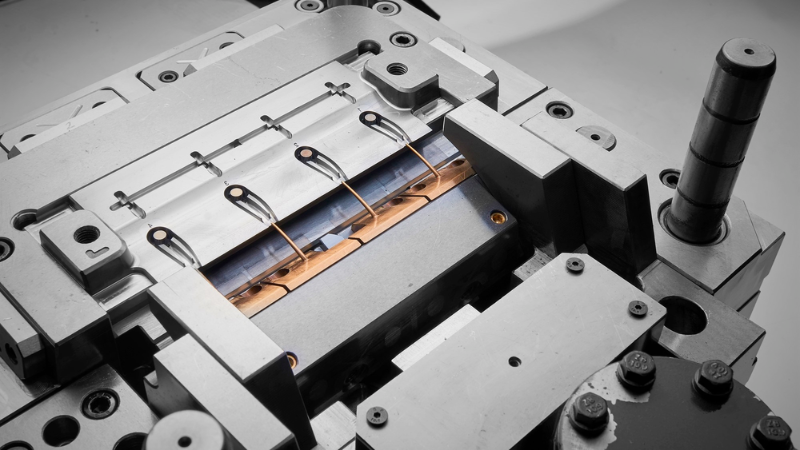
Investing in high-quality molds is essential for the success of rubber molding projects. Durable materials, such as high-grade steel or aluminum, should be used to construct the molds to withstand the rigors of production runs and repeated use. Low-quality or poorly maintained molds can lead to premature wear, resulting in inconsistencies, defects, and increased downtime.
Regular maintenance and inspection of molds are necessary to identify and address any issues promptly, ensuring the longevity of the molds and the overall success of the project.
Implement Strict Quality Control Measures
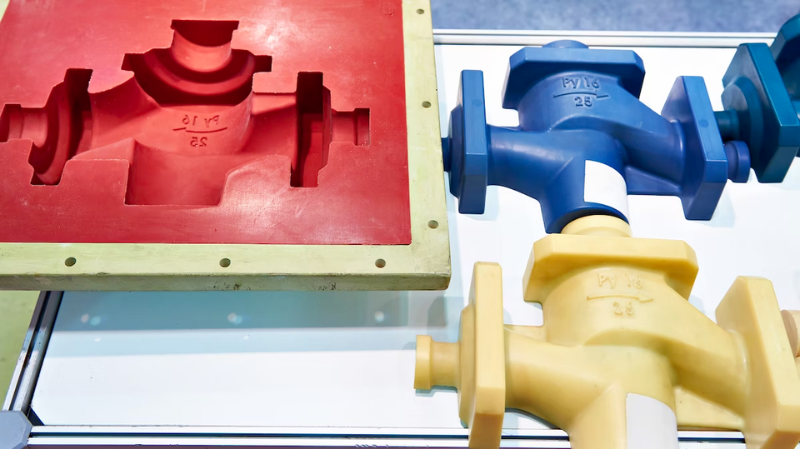
Quality control is a crucial aspect of rubber molding projects to ensure the products meet the required standards. Implementing a robust quality management system involves conducting regular inspections, dimensional checks, and performance testing of the rubber molded in products.
In-process inspections at different stages of production can help identify potential issues early on, allowing for immediate corrective actions. Consistent monitoring of product quality ensures that the final output adheres to the desired specifications and meets customer expectations.
Potential Problems Associated with Rubber Molding Projects
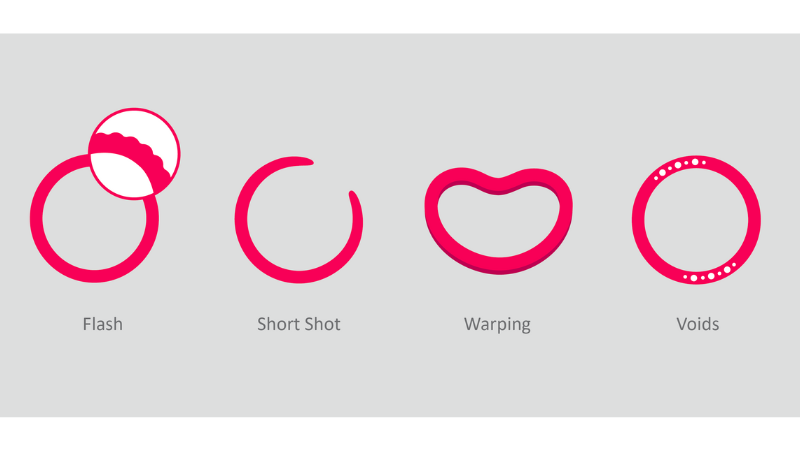
Rubber molding projects, like any manufacturing process, can encounter several potential problems that may impact the final product quality and overall project success. Some common issues associated with rubber molding projects include:
- Flash or Burr Formation: Excess material can seep out of the mold cavity during the molding process, leading to flashes or burrs on the finished product. This can result from improper mold design, inadequate clamping force, or inconsistent molding parameters.
- Voids or Air Traps: Air pockets or voids can form within the rubber part during the molding process, leading to weak spots or reduced functionality. Proper venting and degassing techniques are essential to minimize this issue.
- Warping or Distortion: Uneven cooling or improper material distribution can cause warping or distortion in the final product. Proper cooling and mold design can help mitigate this problem.
- Inadequate Cure: Insufficient curing of the rubber material can result in under-cured parts, leading to reduced mechanical properties and performance issues. Accurate control of temperature and curing time is critical to achieve a proper cure.
- Material Contamination: Contaminants, such as foreign particles or leftover material from previous runs, can cause defects in the molded parts. Proper cleaning and maintenance of equipment are necessary to prevent material contamination.
- Mold Damage or Wear: Over time, molds can experience wear and tear, leading to defects or inconsistencies in the molded parts. Regular maintenance and replacement of worn molds are essential to avoid production issues.
- Poor Surface Finish: Mold surface imperfections or improper release agents can result in a rough or inconsistent surface finish on the molded parts.
To address these potential problems, it is essential to have skilled technicians and engineers overseeing the rubber molding process, implementing rigorous quality control measures, and regularly inspecting the molds and equipment. A proactive approach to identifying and resolving issues as they arise can help ensure smoother rubber molding projects with consistent, high-quality results.
Tips for Getting the Best Results from Rubber Molding Techniques
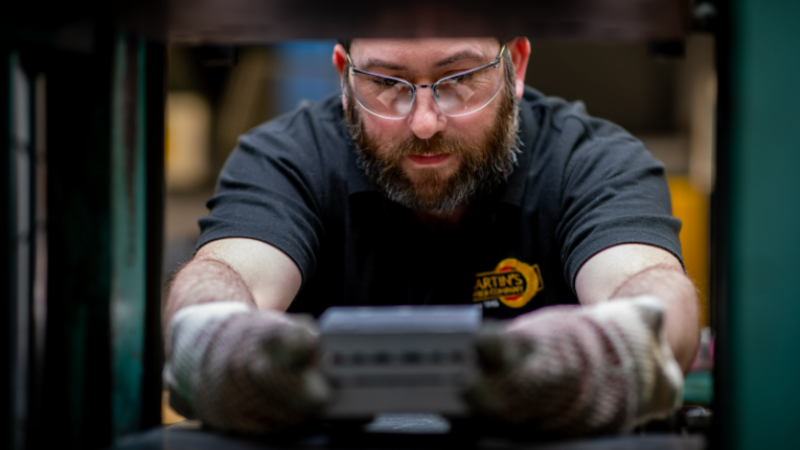
When molding rubber, it’s crucial to avoid sharp edges as they are undesirable. An experienced technician should round them off to ease the design and construction of the custom molded rubber part, speeding up the rubber molding process.
Additionally, the material specifications are vital, depending on the industry and application. Using substandard rubber can compromise the overall quality of the custom part, leading to defects in the final product. Prioritizing these tips ensures a smoother custom rubber part molding process and delivers high-quality results.
Conclusion
This article thoroughly examined the Rubber manufacturing industry and the rubber molding techniques used in its custom products manufacturing process. It has become a guide to rubber molding techniques and how we can improve the custom-molded rubber end product through Industry tested methods.
Why go to Hongju for your Rubber Molding needs?
Hongju Silicone is an innovative custom-molded rubber products manufacturer in China. We provide high-quality custom rubber molding products for our customers in different industries.
Our main rubber molding products include conductive silicone keypads, rubber grommets, furniture rubber feet, gaskets, O-rings, etc. To glimpse our diverse and high-grade product range, visit our products page.
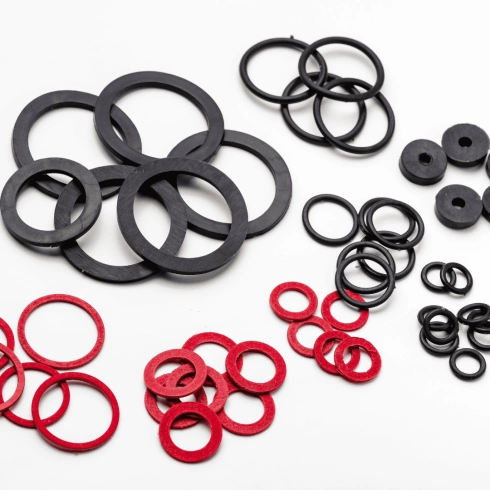
Send Your Inquiry Now!
Quality Meets Affordability. Inquire Now for High-Quality Products at Low Volumes.