In this blog, we have explained the types of plastic molding to help you select the perfect fit for your product. We will briefly discuss the technologies, applications, and impacts of molding on the environment to help you make the selection easier.
What Is the Plastic Molding?
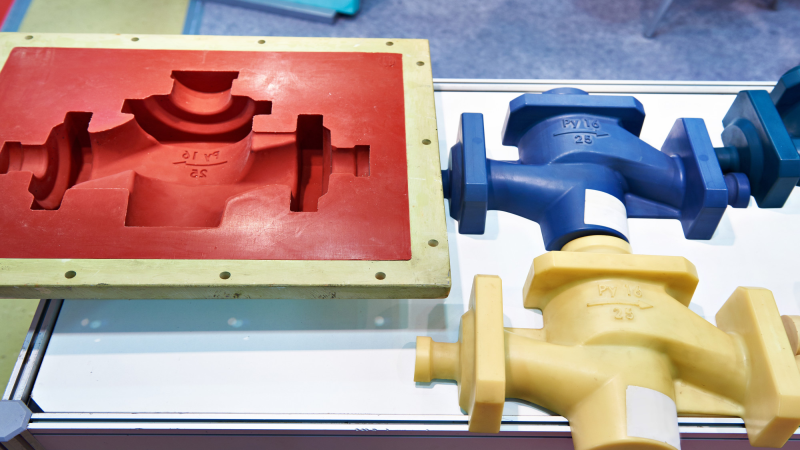
Plastic molding is the process of manufacturing plastic products by shaping a pliable material or liquid resin in a solid frame known as a mold or matrix. It involves polymers like low-density polyethylene or polypropylene placed in a hollow mold to yield the final product.
These molds have a complex pattern to use in the production of products with different shapes, features, and functions. The applications of molding are not limited; in fact, they stretch to different industries and in a wide range of products.
Each manufacturing process requires different heat and pressure levels for the final product’s desired form.
5 Technologies for Molding Plastic
Plastic molding processes are critical to converting plastic into new objects for diverse industries and purposes. However, there is no one-size-fits-all technology for the plastic injection molding industry. There are 5 different methods for transforming plastic with some less common methods like extrusion molding for the production of plastic components.
All these methods have distinctive benefits and unique applications. So, it is necessary to choose according to your product requirements. The following are the commonly used plastic molding technologies:
Injection Molding
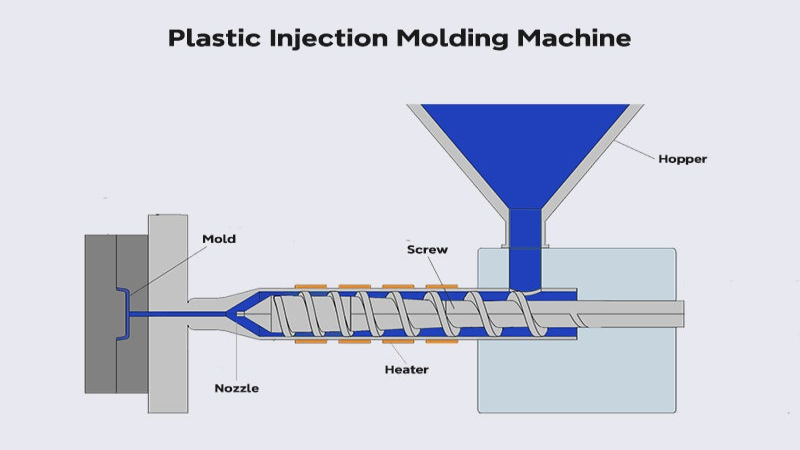
Plastic injection molding produces highly complex parts at a fast speed with excellent accuracy. This plastic injection molding technique covers the manufacturing of a large number of high-quality complex products. The process involves several crucial steps to ensure the quality.
It is different from the other plastic molding techniques as it is a thin-walled molding with a low cost per part. This typical injection molding process involves pouring plastic resin/thermoplastic or liquid silicone injection into a customized heated mold of a plastic injection molding machine. The molten plastic eventually begins to form and takes its shape with subsequent cooling.
The plastic solidifies after cooling and takes the desired shape. After that, ejection pins or plates of the injection molding machine release the finished product. It has various types including gas-assisted injection molding which helps in manufacturing plastic parts. The injection molding process produces products with three-dimensional shapes, unlike extrusion molding which produces two-dimensional structures.
Blow Molding
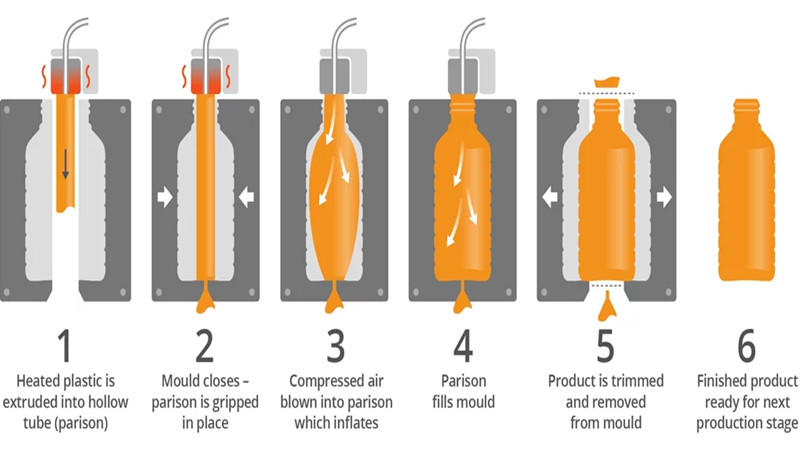
Blow molding is one of the most commonly used techniques for producing hollow objects, such as storage containers and bottles with thin walls and automotive parts like fuel tanks. It consists of a heating process and ranks second for low cost per part among molding technologies. In this process, molding starts with using heated plastic in a hollow tube that expands to get the desired shape of the final product.
It involves heating the raw plastic and then injecting air into it. After that, the molten plastic resins start to blow into the shape of the hollow mold cavity with the help of inert gas in the machine. Finally, it takes the desired shape upon cooling according to the mold used.
Blow molding is a fast and cost-effective process. In addition, manufacturers produce many lightweight and hollow plastic products using this technology. The manufacturing process of injection molding and blow molding is the same as both use liquid resin. It differs from injection molding in that it involves molten plastic material and a tube-like part.
Rotational Molding
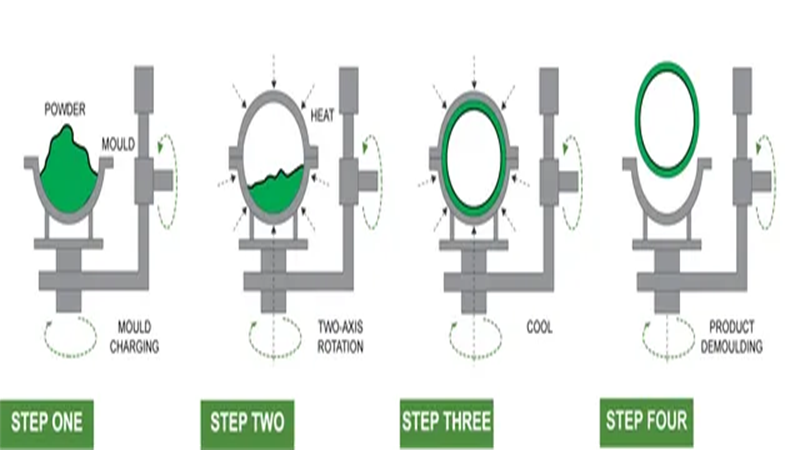
Rotational or roto-molding is unique among plastic molding techniques for producing one-piece plastic parts. This technique involves injecting molten plastic resins into the mold cavity and then rotating at high speed. Later, after cooling, the heated plastic converts into the desired shape. There are various benefits and applications of this type of plastic manufacturing process.
Rotational molding is less expensive than injection molding. The best thing is that rotational molding reduces material wastage, and you can use excess material. It reduces the costs involved in maintaining the pressure but at the expense of the production speed.
Compression Molding
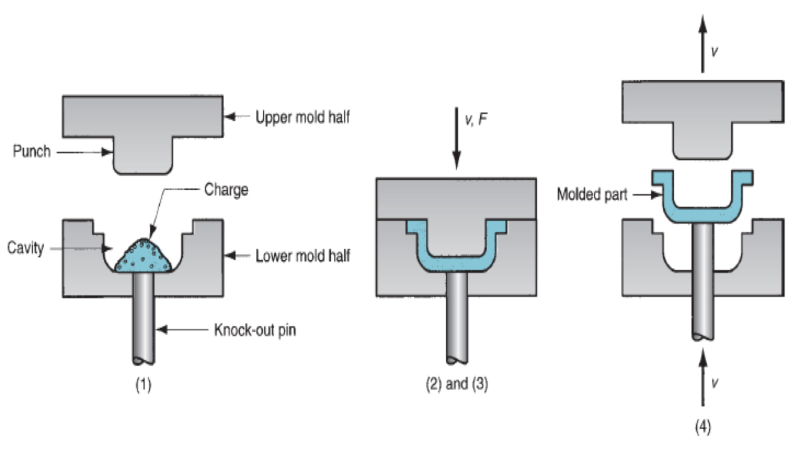
Compression molding is highly cost-effective, with low tooling costs for plastic components as compared to the other traditional methods of molding plastic. It is a commonly used molding type with specific applications in various fields like aerospace and automotive. However, it’s more beneficial for manufacturing plastic parts of thick walls with good heat resistance.
The compression molding process involves pouring the raw melted plastic resin into a heated mold and then compressing it to a certain extent under the right heat and compressed air. Thus, cooling the molten plastic material and cutting the excessive material gives it the desired shape.
When comparing compression molding vs injection molding processes, they look the same. But there is a huge difference. Injection molding involves pouring the raw material into the mold. However, compression molding involves compressing the molds around the raw material.
Thermoforming
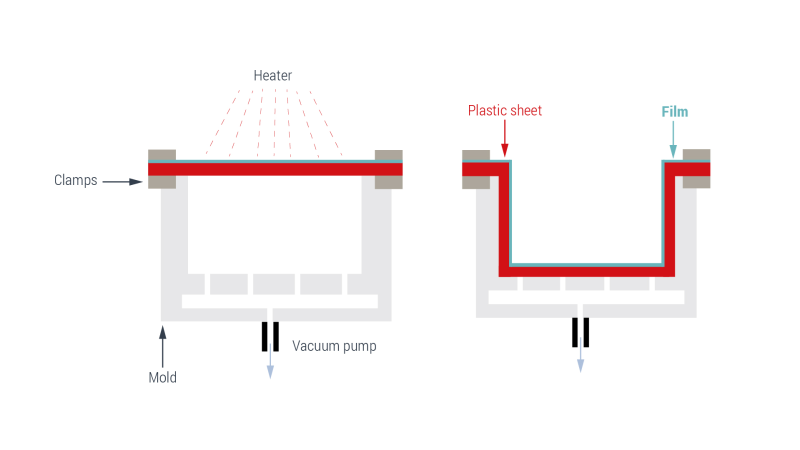
Thermoforming is another cost-effective and widely used technique for plastic injection molding. In this method, manufacturers use a pre-existing plastic sheet to transform it into various shapes under high heat and pressure.
After production, excess material is removed from the final product to give it the desired form. Thermoforming is a highly reliable and durable technique for mass production of products. It plays a pivotal role in shaping the world around us with its balance of speed, cost-effectiveness, and material versatility.
Take the First Step:
Requst for an Inquire
Quality Meets Affordability. Inquire Now for High-Quality Products at Low Volumes.
Applications of Different Types of Plastic Molding Techniques
Each plastic injection molding technique provides a dynamic toolbox for converting plastics into various versatile forms. In addition, each type has its unique capability and limitations, which makes them specialized for specific industries and products. Following are some of the applications of each type of plastic injection molding in which it excels:
Compression Molding
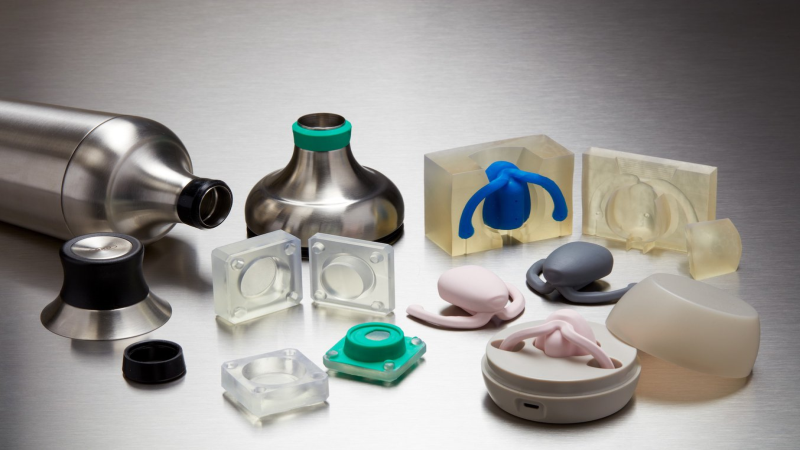
- It is suitable for simpler and cost-effective products of plastic molding as compared to the other types.
- This type of molding usually forms different electrical products and plastic parts, such as circuit breakers, switchgear, etc.
- It produces automotive components (gaskets, interior trims, bushings, etc), as well as certain household appliances like door handles, knobs, etc.
- The aerospace and sports goods industries also use it to produce many high-quality parts, for which compression molding is the best choice.
Blow Molding
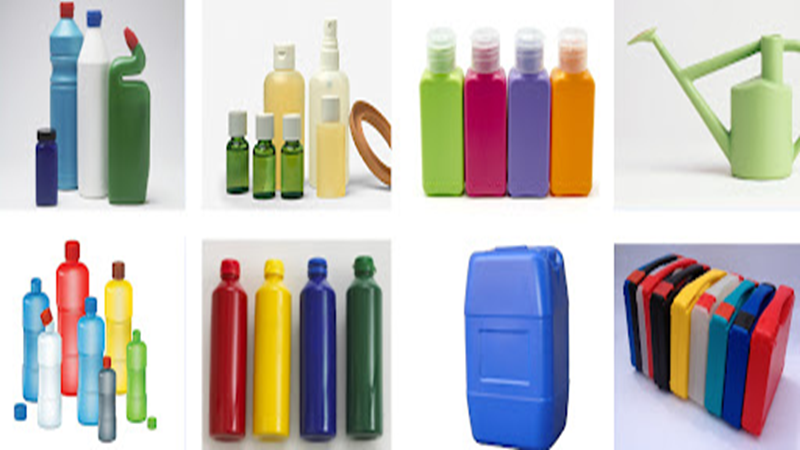
- Blow molding is the right choice for making hollow toys like balls, toy cars, etc.
- The technology is highly effective for medical devices like oxygen masks and nebulizers due to its lightweight nature and low cost per part.
- It is responsible for manufacturing all types of beverage bottles and most automotive fuel tanks due to its hollow and durable nature.
- Many industries prefer this technology for making large containers for storing certain chemicals and other liquids.
- Manufacturers produce plastic drums and containers used in households and industries using blow molding.
- This process also manufactures kitchen utensils like jugs and oil containers.
Injection Molding
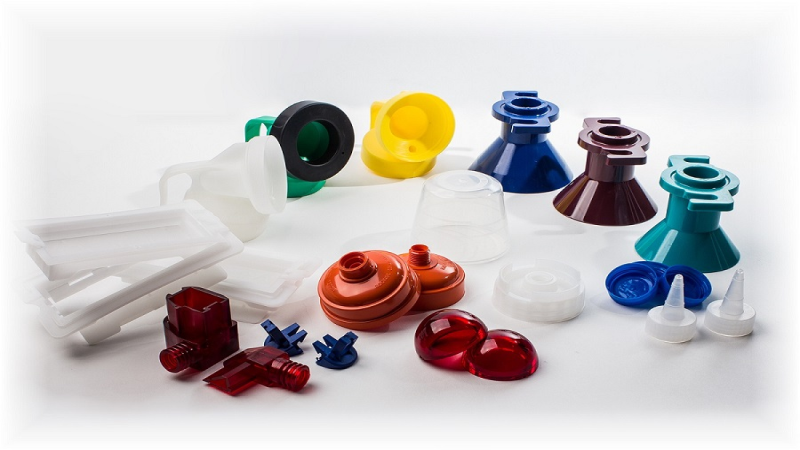
- Medical equipment, especially disposable ones, including syringes, are the result of injection molding.
- Producing toys and game pieces using the injection molding technique is industry standard.
- Plastic injection molding produces packaging materials like food containers and beverages.
- This plastic injection molding technology also manufactures many daily-use electronics. The list starts from smartphones and goes on to the laptops.
- A few automotive parts, like vehicle dashboards and engine parts, are also injection-molded parts manufactured by using injection molding technology.
Rotational Molding
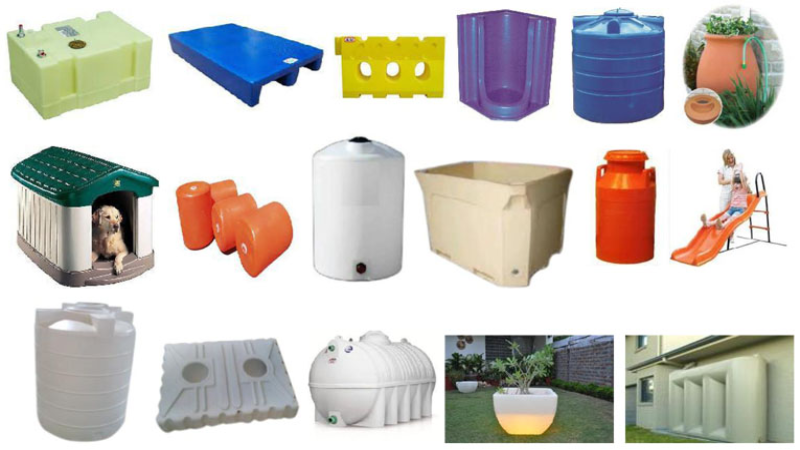
- Furniture like chairs, tables, etc., are mostly manufactured using rotational molding for durability and waterproofing quality.
- Certain playground equipment, e.g., swings, ladders, slides, and seamless kayaks and canoes, are also formulated by roto-molding.
- Big-sized storage containers of water, chemicals, and sometimes waste material, as well as crates and pallets, are also the result of rotational molding.
- Rotational molding produces medical equipment like prosthetics, waste containers, and medical cases.
Thermoforming Molding
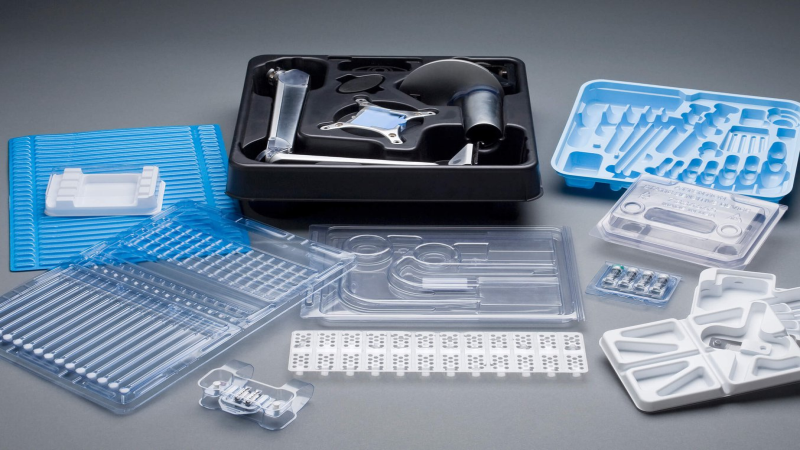
- Disposable medical instruments, blisters, and clamshell packings for foods and electronics are the results of thermoforming.
- Plastic signs used in outdoor and indoor displays, door liners, and many other intricate parts come through the process of thermoforming.
- Thermoforming checks prototypes for testing and verifying different kinds of designs before further processing them for molding.
- This technique is responsible for manufacturing fitness equipment. They include cable weight machines, treadmills, and other equipment.
- Manufacturers use thermoforming to make aircraft components like luggage racks, seat backs, tray tables, and armrests. Some other examples of pliable material include paneling and bulkhead components.
Take the First Step:
Requst for an Inquire
Quality Meets Affordability. Inquire Now for High-Quality Products at Low Volumes.
Environmental Impacts of Plastic Molding
In addition to the numerous and vast benefits of plastic injection molding, these techniques possess some limitations, too. These limitations mostly impact our environment and surroundings in several ways.
Material
The environmental impacts of plastic include pollution and greenhouse emissions. Plastic manufacturing can result in elevated levels of sulfur dioxide, volatile organic compounds (VOCs), and certain other harmful gasses entering the atmosphere upon heating and melting plastics, which causes a huge impact on the air quality index.
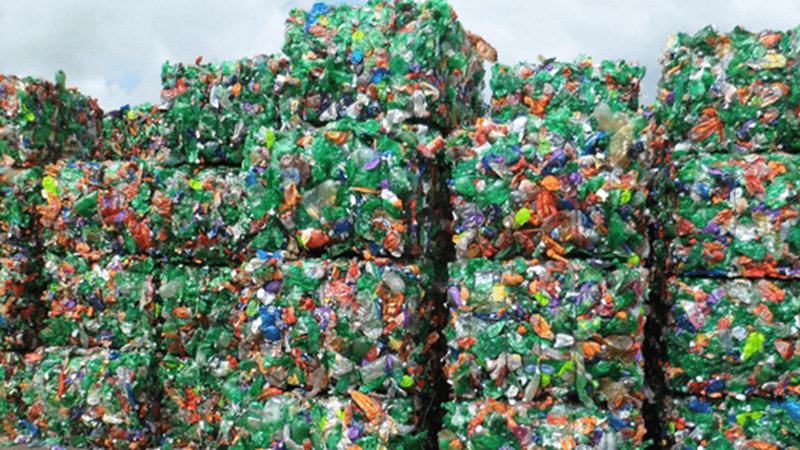
Pollution
The degradation of plastics produces tiny microplastics which can pollute the water of oceans and soil too and can cause harm to many ecosystems and disrupt food chains. Excess plastics or material wastes left after production are not recycled properly, and huge landfills remain as waste materials. Only 16% of plastic goes into making new products, showing how it contributes to pollution.
Energy
Melting the plastic for injection molding requires a lot of energy. The main source of this energy primarily comes from fossil fuels. Their burning can result in pollution and greenhouse gas emissions. In general, the heat produced during this process can also cause global warming. To address this concern, Hongju utilizes energy-efficient machines that carefully manage energy use during molding.
Selection Considerations of Plastic Molding Technology
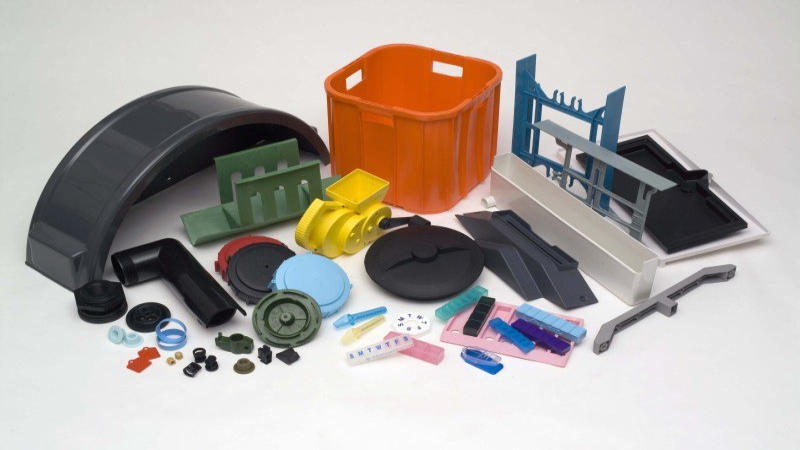
Choosing the right type of plastic molding technology depends upon various factors, including the required shape, production volume, and material properties. Each molding technology offers unique products. So, which plastic molding technology is right for your product?
Injection molding is incredibly useful for intricate parts as it’s a molding technique for complex products with uniform wall thickness, and blow molding is suitable for hollow structures. In addition, extrusion molding is suitable for producing metal products such as metal injection molding.
Similarly, roto molding is best for large one-piece structures, compression molding for for low—to medium-volume manufacturing processes, and thermoforming for simpler shapes and mass production of plastics.
So, to select the right plastic molding technology, first analyze your needs and research the strengths and qualities of each type of method to choose the perfect fit for your products.
Take the First Step:
Requst for an Inquire
Quality Meets Affordability. Inquire Now for High-Quality Products at Low Volumes.
Conclusion
Plastic molding technology is commonly used to produce a vast variety of plastic products. There are many types of plastic molding processes, each with its unique durability and quality. Each type of molding technology is suitable for specific applications. Like thermoforming for pre-existing plastic sheets and rotational molding for huge, one-piece hollow parts.
The considerations for selecting a molding technique include material qualities, production volume, molding machines, and product shape. So, you can choose the best option for your product while investigating and analyzing the qualities and advantages of each kind of molding technique.
Seek Help from Experts at Hongju to Select the Right Plastic Molding Technology
If you are still confused about selecting the right type of plastic molding technique for your product, ask the experts at Hongju Silicone. We can provide professional consultancy to help you choose the best molding process for your products. Here at Hongju, we manufacture all types of plastic with our advanced molding machines which are of high-end quality and efficiency.