This article explores the differences between these two outstanding materials. It explores the properties and characteristics of each and highlights their differences. It also explores common applications of EPDM and Viton and how you can choose between them.
What is EPDM Rubber?
EPDM is a synthetic rubber primarily made of ethylene, propylene, and some diene comonomer. Commonly used dienes include dicyclopentadiene or DCPD, ethylidene norbornene or ENB, and vinyl norbornene or VNB.
EPDM rubber can be crosslinked or vulcanized using sulfur or peroxides. This results in rubbers with different qualities. The name EPDM is an acronym that stands for ethylene propylene diene monomer.
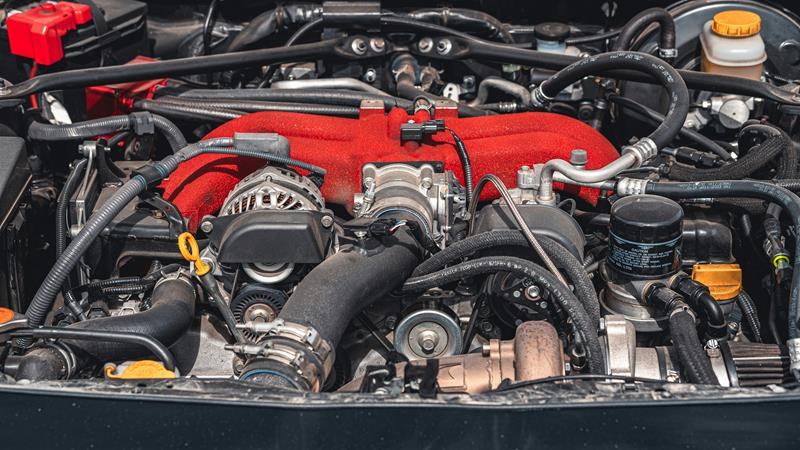
EPDM rubber is commonly used for radiator and heater hoses, electrical insulation, freezer room seals, window and door seals in the automotive industry, and tubing for solar panel heat collectors.
Properties of EPDM Rubber
EPDM rubbers can have a density as low as 0.90g/cm³ or even greater than 2.0g/cm³. This will be an important factor to consider when comparing it to Viton. This material is not transparent and its shore hardness can range between 30 and 90.
The tensile strength of EPDM is 17 MPa or approximately 2500 PSI.
This versatile synthetic rubber has good temperature tolerances for many applications and can be formulated to operate in temperatures as high as 150°C(302°F).
However, EPDM shines in low-temperature applications. It can maintain its elasticity in temperatures as low as -40°C(-40°F).
Characteristics of EPDM
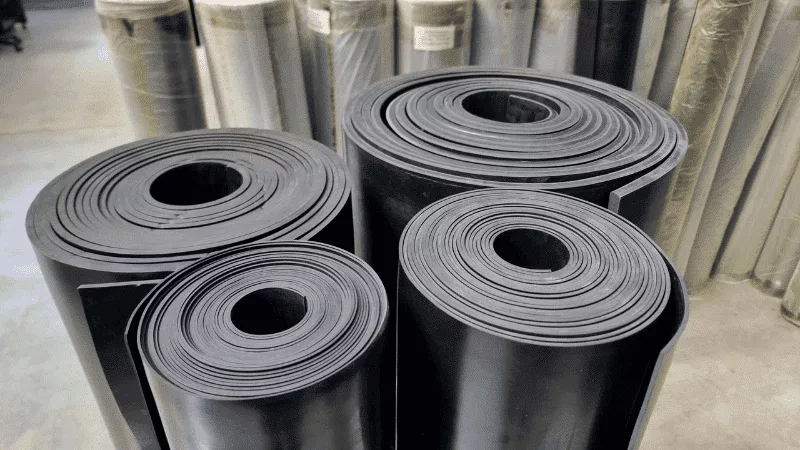
When you’re considering EPDM for any application, some of the characteristics of the materials you should know are:
- Excellent impermeability
- It’s a good electrical insulator
- Poor flame resistance without blockers
- Extreme durability plus low-maintenance needs
- Exceptional moisture resistance including hot water and steam.
- High resistance to hydraulic fluids, alkalis, silicone oils, and ketones.
- Poor resistance to fuels, mineral oils, solvents, and aromatic hydrocarbons.
- It has a higher resistance to heat, light, and ozone compared to SBR, neoprene, and natural rubber.
The presence of these characteristics depends on how the specific EPDM material has been compounded.
Types of EPDM
EPDM can be made in different ways depending on the desired characteristics. As a result, there are different types of EPDM rubbers, including peroxide-cured EPDM, sulphur-cured EPDM, solid EPDM, and expanded foam EPDM.
Peroxide-cured EPDM or EPDM PC has superior steam and temperature resistance compared to sulfur-cured EPDM. The peroxide-curing process gives the rubber greater thermal and chemical stability.
On the other hand, sulfur-cured EPDM or EPDM SC has superior tear and tensile strength. It also allows the use of more types of fillers.
Solid EPDM is denser, less permeable to liquids, and more durable than foam EPDM. Foam EPDM offers more cushioning and is better as a seal in certain applications.
Inquire About Our Silicone and Plastic Products!
What is Viton Rubber?
Viton rubber is a fluoroelastomer, i.e., a synthetic rubber made using fluorocarbons. It’s also been called fluoro-rubber or fluorine rubber. Viton is not the actual name of this elastomer but a brand name currently owned by The Chemours Company.
Viton rubber is an FKM (Fluorine Kautschuk Material) originally developed by DuPont in the 50s for aerospace applications. Today, FKMs are manufactured all over the world but are still referred to as Viton rubber.
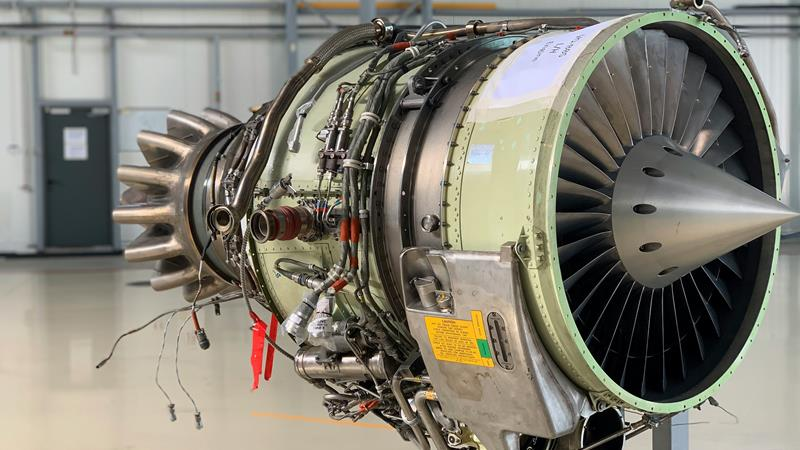
There are at least five varieties of FKMs today with different formulations, but they all have vinylidene fluoride. FKMs are used in applications with frequent exposure to oxygenated automotive fuels, and applications where high temperature tolerance is critical.
Properties of Viton Rubber
Viton rubber rubber has a density of over 1.8g/cm³. This makes it significantly denser than most rubbers, including common formulations of EPDM. Just like EPDM, Viton rubber is not transparent. It can have a shore hardness of between 50 and 95.
This rubber’s tensile strength can be as high as 20.7 MPa, depending on its formulation.
Viton can be used at temperatures as low as -20°C(-4°F). However, this material made a name for itself due to its unbeatable high-temperature performance. Viton rubber is rated for operations at temperatures as high as 260°C or 500°F.
Characteristics of Viton Rubber
Common characteristics of Viton rubber and other FKMs include:
- Highly durable
- Stain resistant
- Comfortable to wear
- Can withstand skin oils
- Good flame resistance
- Exceptional resistance to heat
- High impermeability to organic solvents
- Poor resistance to ketones, amines, ethers, and aldehydes
- Exceptional resistance to many chemicals, including fuels, mineral acids, and mineral oil-based lubricants
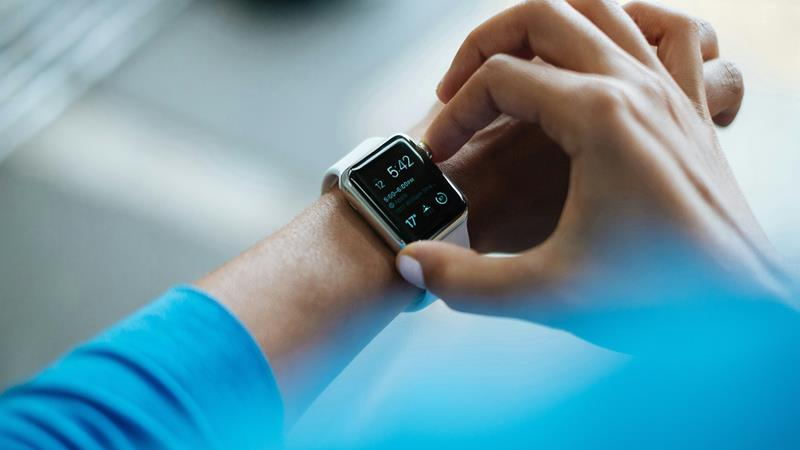
Both the chemical and physical properties of Viton rubber will vary depending on the type and the specific formulation.
Types of Viton Rubber
There are five main types of Viton rubber: Type-1, Type-2, Type-3, Type-4, and Type-5. Although all these types contain vinylidene fluoride or VDF, they can contain many other chemicals and also have different amounts of fluorine.
Type-1 FKMs are good all-rounders, but type-2 FKMs offer better heat and chemical resistance, although flexibility at low temperatures suffers. Type-3 FKMs have better low-temperature flexibility and type-4s have a higher base resistance.
Finally, type-5 FKMs have a higher base resistance and withstand hydrogen sulfide better at higher temperatures.
Inquire About Our Silicone and Plastic Products!
Viton Vs EPDM
The table below compares EPDM and Viton rubbers. These comparisons are for common or standard formulations and exceptions may exist.
Property | EPDM Rubber | Viton Rubber |
---|
Choosing Between EPDM and Viton for Sealing Applications
Viton and EPDM are two of the most commonly used rubber materials for manufacturing gaskets and O-rings. However, they are not always suited to the same applications.
When Should You Use EPDM O-Rings or Gaskets
EPDM seals such as o-rings and gaskets are the better choice when very high temperatures and chemical resistances are not critical. This includes applications with exposure to hot and cold water, steam, and specific chemicals e.g. ketones.
Although Viton rubber could be used for some of these applications, the added cost would be unnecessary.
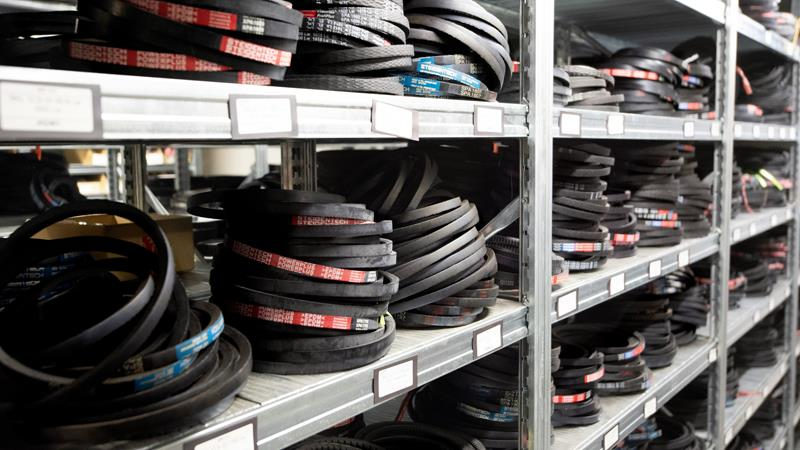
EPDM is also a better choice in applications where very low temperatures will be the norm.
When Should You Use Viton O-Rings or Gaskets
Viton is the material of choice for o-rings or gaskets that will be operating at temperatures above 150°C. It should also be considered where very high chemical resistance is required. Viton seals are also good for applications where exposure to fuels and mineral oils is expected.
Due to the specific nature of chemical resistance, you should confirm that Viton is resistant to the actual chemicals it will be exposed to in your application.
Inquire About Our Silicone and Plastic Products!
FAQs
1. Is Viton or EPDM Better?
Both materials have good mechanical properties and other advantages, but neither is better in every application. EPDM is unmatched in low-temperature applications and holds up well against diluted acids, sodium hydroxide solutions, and other chemicals.
Viton takes the crown in high-temperature applications and also resists corrosion by many harsh chemicals that would degrade EPDM.
Ultimately, the material will be better determined by the specific application. EPDM’s lower cost will give it an edge if all other factors are equal.
2. How Long Does EPDM Last?
In some applications, EPDM can last as long as 50 years. EPDM stands up well to sunlight, rain, and other weather conditions and is suitable for outdoor use. It also has additional properties that improve its durability such as low permeability.
3. What are the limitations of Viton?
Viton can be degraded by chemicals such as acetone, acetic acid, amines, ethyl acetate, and methyl ethyl ketone. Viton’s effective operating temperature range is -20°C to 260°C. Below -20°C it loses its flexibility.
Although it has a high-temperature resistance, it can release toxic hydrogen fluoride at extremely high temperatures or in a fire. Viton can also be harder than other elastomers, making it unsuitable for some applications.
Inquire About Our Silicone and Plastic Products!
Conclusion
EPDM and Viton are good examples of the marvels of synthetic rubber. Both materials have excellent properties that make them indispensable in many applications and different qualities can be improved by using specific formulations.
EPDM is an excellent material for very low-temperature applications and outdoor use. Viton is very well suited to high operating temperatures. Neither material is inherently superior and the better choice should only be dictated by the application.
Why Choose Hongju Silicone For Your EPDM and Viton Rubber Seals?
Hongju Silicone has been in the rubber manufacturing business for over 23 years. We have worked with many elastomers, including EPDM, Viton, SBR, and Nitrile rubbers.
Our experts can advise you on the best material for your needs, and you can take advantage of our expertise in injection and compression molding to get high-quality seals. Contact us today so we can help you navigate the challenges of choosing the right material.