Did you know that pumps, valves, and other fluid systems create pressure between fluids and gases to generate movement? Diaphragm rubber is the main component that flexibly manages this pressure.
It controls movement and acts as a barrier between the two layers. Read on to learn what rubber diaphragms are, where they’re used, and how to choose the right diaphragm seal.
Understanding Rubber Diaphragms: Function and Importance
Most rubber diaphragms are used for sealing. The strength of a diaphragm is the ability to stretch, compress, and return to form. It is flexible, reliable, and chemical resistant. It can withstand extreme pressure, vacuum, or corrosive environments.
Diaphragms are used in valves, pumps, and regulators to control flow and pressure. They maintain isolation between the two chambers. So, a liquid, a gas, or gases or liquids do not mix. This prevents leakage and contamination.
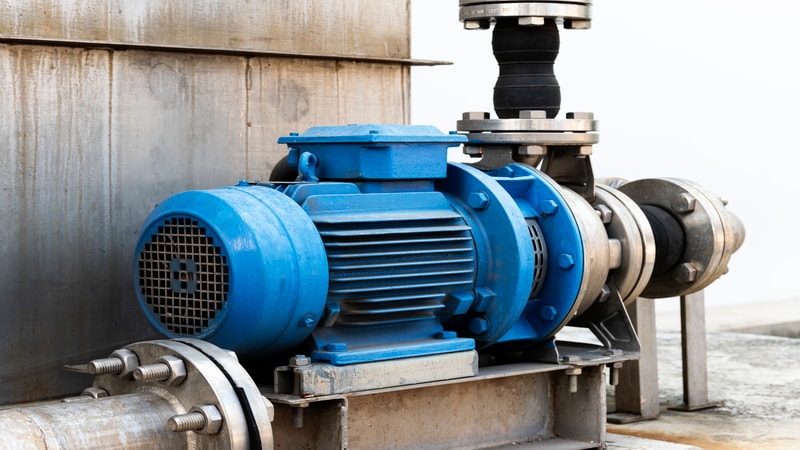
Various industries rely on rubber diaphragm seals:
- Oil & gas (natural gas valves, separators)
- Food processing (sanitary pumps, regulators)
- Medical (blood analyzers, infusion devices)
- Automotive (fuel pressure regulators, braking systems)
- Water treatment (metering pumps, backflow preventers)
Common Applications of Rubber Diaphragms
It is used where controlled pressure gauges and fluid isolation are required. Commonly, they are applied in:
- Diaphragm Pumps: It is used to move liquids without contamination. It is ideal for chemicals and food-grade fluids.
- Regulators and Meters: They maintain precise pressure and measurement. Also, control the flow of gas or liquid in regulators and meters.
- Accumulator Tanks: Diaphragms separate the fluid and gas in hydraulic and pneumatic systems.
- Natural Gas Valves: In valves, it isolates combustible gases and adjusts flow rates.
- Water Well Systems: Diaphragm seals are used in water well systems and air-over-water pressure tanks. It maintains consistent water pressure.
Static vs. Dynamic Uses:
Diaphragms serve as seals and separators in various applications. A static diaphragm seal is a component. It is applied with minimal or no movement required, such as separating water and air in tanks. Dynamic diaphragms flex under repeated pressure and movement.
Rubber Diaphragm Materials: Choosing the Right One
Diaphragm seals are made from various materials. The temperature limit shows how much a diaphragm resists heat. To choose the right diaphragm material, consider chemical compatibility and pressure demands. Some commonly used options:
1. EPDM Diaphragms
Best for: Water, steam, and UV-exposed systems.
Temperature Range: -60°F to 275°F (-51°C to 135°C)
EPDM diaphragms offer excellent resistance to ozone, UV, and weather. They remain flexible and chemically stable in outdoor and long-term settings. Ideal for water, steam, and WRAS-approved systems.
2. Nitrile (NBR) Diaphragms
Best For: Automotive, industries, and defense systems.
Temperature Range: -30°F to +220°F (-34°C to +104°C)
Nitrile diaphragms are durable, chemical, and oil-resistant. It is used in automotive and industrial environments that involve lubricants and hydrocarbons.
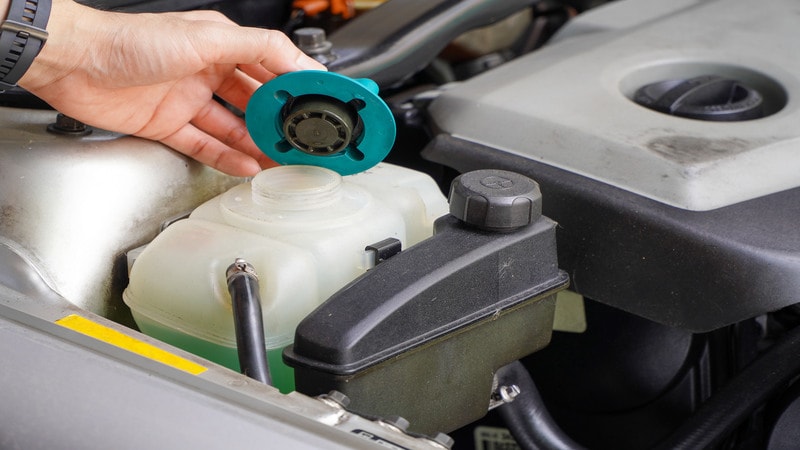
3. Silicone Diaphragms
Best For: Food, medical, and high-temperature applications.
Temperature Range: High -85°F to 450°F(-65°C to 232°C)
Silicone diaphragms are highly flexible. It can resist extreme heat, UV, and chemicals. It is commonly used in food processing, medical devices, and pharmaceutical systems.
4. Neoprene Diaphragms
Best For: Actuators, pumps, shock mounts, and industrial equipment.
Temperature Range: -20°F to 200°F (-29°C to 93°C)
Neoprene is a versatile, all-purpose material. It withstands UV, ozone, oil, fuel, and heat. It is ideal for outdoor and demanding industrial applications.
5. Natural Rubber Diaphragms
Best For: Abrasion-heavy, non-oil applications.
Temperature Range: -40°F to 180°F (-40°C to 82°C)
Natural rubber has high elasticity and tensile strength. It can resist abrasion, light, and high pressure. It is used widely in pumps, meters, valves, and accumulators.
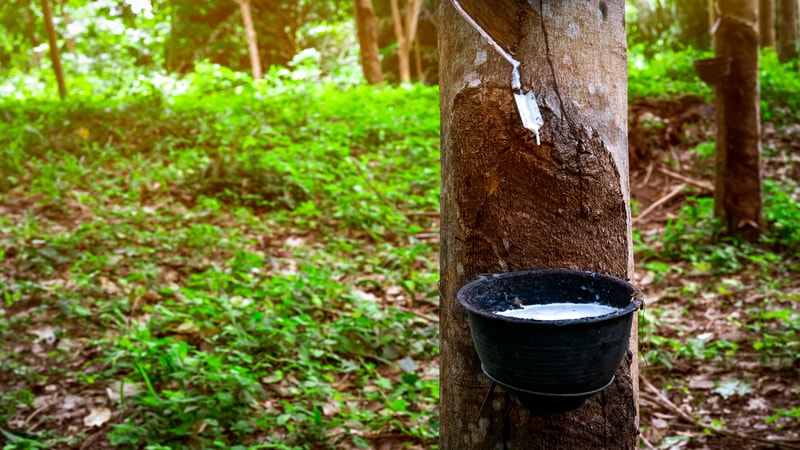
Fabric Reinforced vs. Homogeneous Rubber Diaphragms
Rubber diaphragms are of two types: homogeneous or fabric-reinforced diaphragms. Homogeneous diaphragms are made of rubber. It is suitable for pumps, valves, actuators, and other applications. Ideal for low-pressure and intricate molding.
Fabric-reinforced diaphragms are made by combining rubber with woven reinforcements like nylon, cotton, or Kevlar. Polyester fabric can give cost-effective reinforcement. Reinforced fabric adds durability to the diaphragm structure. It is ideal to use in high-pressure or long-life applications such as compressors and gas regulators.
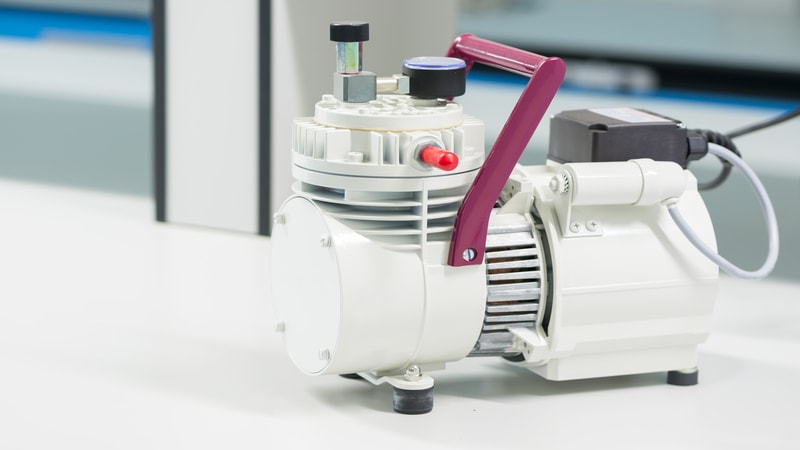
How Rubber Diaphragms Are Manufactured
Rubber diaphragms are produced through a series of precise steps. The process depends on the diaphragm’s shape, size, and application.
- Material Selection: The material, such as rubber, silicone, or EPDM, is chosen. The material selection is based on performance needs like temperature resistance, flexibility, and chemical exposure.
- Molding Process: Most diaphragm seals are circular. After cutting the material, it is placed into a heated mold. In compression or transfer molding, the material is shaped under pressure. It forms thin, complex profiles. Precision is critical, especially when placing reinforcement fabrics.
- Curing and Finishing: When molded, the diaphragm undergoes curing. This process enhances strength and elasticity. Quality checks are followed for uniform thickness, smooth edges, and no surface defects.
Thin diaphragms manufacturing need strict control over temperature, pressure, and timing. It helps to avoid defects and get optimal performance in high-pressure applications.
Understanding Durometer in Diaphragms
The durometer measures the hardness of rubber in diaphragms. This measurement evaluates the rubber’s durability. It also shows its flexibility and sealing ability. The durometer range for diaphragms is typically 50–70 Shore A. It is the balance of flexibility and burst resistance.
Extra soft diaphragms can deform under load. Too hard cracka or fail to seal under pressure.
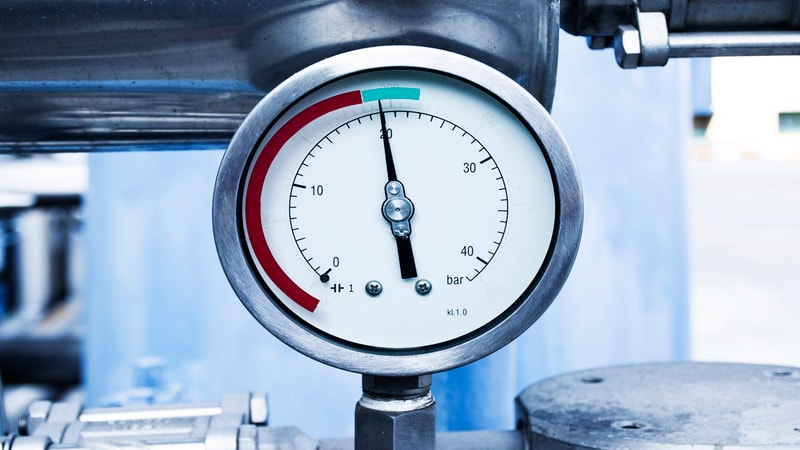
Rubber Diaphragms vs. Gaskets vs. Seals
Rubber diaphragms, gaskets, and seals are closely related to each other. All three provide sealing, but their roles are different. Rubber diaphragms are flexible seals that work as a barrier. It can bear pressure, high temperatures, and resist chemicals.
Gaskets are flat, static seals. It is used between flanges or stationary components. Seal is a broader category. It includes diaphragms, gaskets, and components that prevent leakage.
How to Choose the Right Diaphragm for Your Application
There are so many factors to consider for selecting the right diaphragm. So that it can perform well, consider this quick checklist:
- Required pressure range
- Media compatibility (fluids, gases, chemicals)
- Flexibility or motion requirements
- Temperature tolerance
- Environmental exposure (UV, ozone, food grade, etc.)
- Need for fabric reinforcement
For complex requirements, custom rubber molding offers the best performance match.
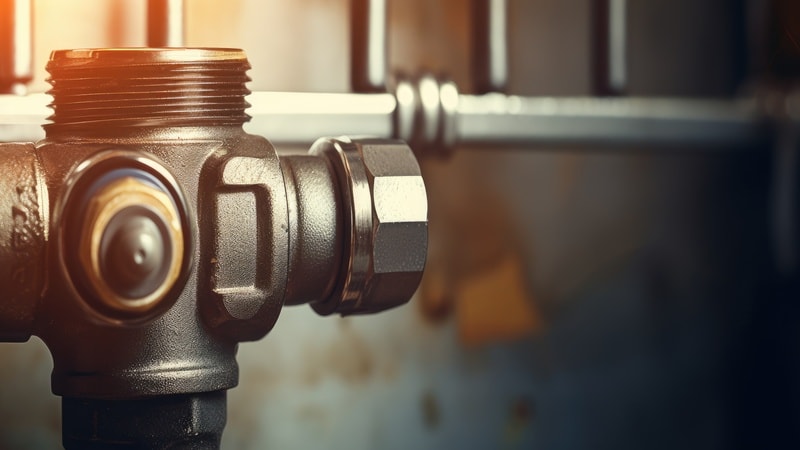
Conclusion
Rubber diaphragms are flexible and durable mechanical components. They adapt to a wide range of pressures and chemicals and can be customized for nearly any system.
If you are engineering or manufacturing diaphragm seals for performance, consider diaphragm material, reinforcement, and molding methods early in the process.
Need a Custom Rubber Diaphragm? Let’s Talk
With over 20 years of experience, Hongju is a market leader in manufacturing precision-engineered rubber diaphragms and silicone seals across various industries. We provide seals that are high-temperature resistant, flexible, and durable.
Ready to start a custom project or need technical guidance? Contact us now for a consultation or prototype quote.
FAQs About Rubber Diaphragms
Q1: Can rubber diaphragms handle high pressure?
Yes, rubber diaphragms can handle high pressure up to 150 PSI or more if reinforced properly.
Q2: Is EPDM better than Nitrile?
It depends on their application. EPDM is weather, UV, and ozone resistant, ideal for outdoor use. Nitrile has superior oil and chemical resistance and is used in automobiles and various industries.
Q3: Can diaphragms be square or custom-shaped?
Yes, custom diaphragm seals can be made in non-standard shapes for specialized designs.
Q4: How long do rubber diaphragms last?
Diaphragm rubbers usually last 5 to 10 years. The life cycle depends on media exposure and maintenance practice.
Q5: Can rubber diaphragms be used with food or medical devices?
Yes, especially silicone diaphragms, which are FDA and ISO-compliant.