What are O-rings?
An O-ring seal works specifically to safeguard equipment and ensure it works correctly. They come in various forms and sizes and differ in the type of materials they are made of. O-rings are generally crafted through extrusion or molding, a mechanical seal in a torus shape.
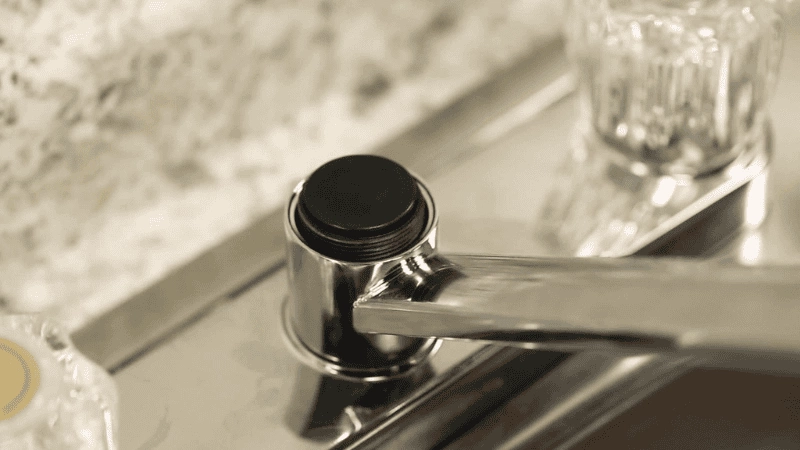
While O-rings differ in several aspects, they serve the same purpose- to seal and ensure that no liquid, gas, or air can get through two surfaces.
O-rings are usually specified by their inner diameter, outer diameter, and cross-sectional width. O-rings are generally fitted into grooves and built tough enough to withstand pressure. This resistance is intended to keep liquid or air from infiltrating or escaping the joining.
There is a risk of some oil, liquid, air, or other substances permeating through the area where the two edges intersect whenever the two surfaces or pieces of machines are joined. The O-ring design considers quality, quantity, cost, application temperature, sealing pressure, chemical compatibility, movement, action, lubrication, and other requirements.
Liquid, air, and other substances infiltrating the joint can impair the machine’s work, affecting the pressure inside a pipe.
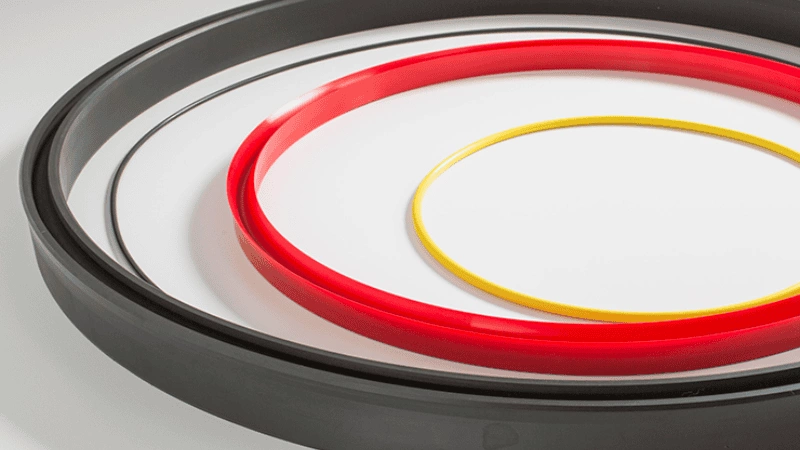
Hence, a correctly fitted ring is used for round two-piece joining to ensure proper sealing. The seal ensures that nothing escapes the connection and nothing infiltrates, obstructing an unreliable seal. With their natural propensity to return to their original shape when pressure is exerted over the cross-section, O-rings have proven to be very reliable and strong.
It’s worth noting that joints can be the most vulnerable area in the machinery pipe. For this reason, it’s crucial to safeguard them with a premium O-ring seal built from a substance suitable to the application.
Inquire About Our Silicone and Plastic Products!
O-Ring Materials and Types
You can select from several O-ring types and ring material options.
Picking up the most excellent O-ring seal in any given scenario will remarkably help you meet the particular operating temperature required and the most low-cost material alternative at that performance point.
Here are the different materials and types of O-rings materials to choose from:
Ethylene Propylene Rubber (EPR)
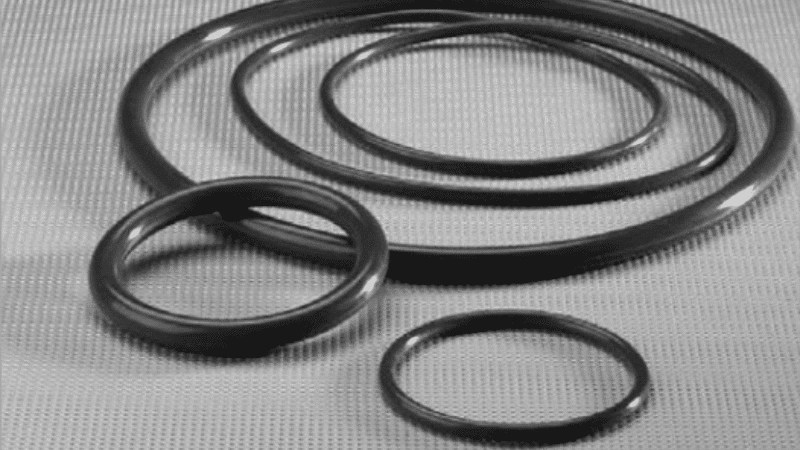
Used for: Skydrol and other hydraulic fluids, including water, brake fluids, steam, alcohol, and silicone oils
Note: Skydrol comes with a toxic odor and corrosive properties that could cause damage to equipment, and it can also irritate your skin.
Wide temperature range: between -65 ° F and 300° F
Ideal for: Aerospace industries (i.e., the United Aircraft Corp) that utilize EPR O-rings in hydraulic pumps
Caution: EPR is not recommended for various applications due to wear and tear issues.
Neoprene
Used for:
- Sealing refrigerants in air conditioners and refrigeration units
- Mild acid resistance ester lubricants and petroleum oils
Temperature range: between -65 ° F and 300 ° F.
Ideal for: refrigeration units of air conditioning systems
Caution:
Finished neoprene products are generally compounded with lead-based agents, making them potentially toxic to human health.
Neoprene doesn’t have 100% resistance to oxygen and petroleum lubricants.
Some people are allergic to Neoprene.
Nitrile Rubber O-rings (Buna-N)

Used for:
- General-purpose seals, for instance, water, petroleum oils, and other hydraulic fluids
- Resistant to abrasive and tears treatment
Temperature range: between -65 ° F and 300 ° F
Ideal for: Applications with limited resistance and low-temperature requirements
Caution:
Buna-N rubber O-rings can have issues with halogenated hydrocarbons, phosphate ester hydraulic fluid, automotive brake fluid, nitro, and Ketones.
Nitrile o-rings are weather-resistant and ozone-resistant; however, this resistance isn’t inerrant but can be backed up by compounding.
Silicone O-rings
Used for: high-temperature fuel injection ports
Temperature range: between -120 ° F and 450 ° F
Note: This type of O-rings material has been revealed to resist -175 ° F during short periods of exposure.
Caution: Silicone rubber O-rings show low tensile strength, abrasion, and tear resistance. Low abrasion resistance implies that silicone is ideal for static applications. Hence, it works best with petroleum fluids, steam, and water.
Ethylene Propylene (EPDM)
Used for:
- Applications with exposure to hot water, ozone, and stream
- ·Exposure to sunlight, ketones, aircraft, and automotive brake fluids,
- Weathering, alcohol, and plumbing applications
- Some bases and acids
Temperature range: between -65 ° F to 300 ° F
Ideal for:
- Drinking water
- Medical and pharmaceutical applications
- Life science industry
- Manufacturing food and beverages
Caution: EPDM rubber o-rings are not applicable to use with fuels and petroleum oils.
PTFE
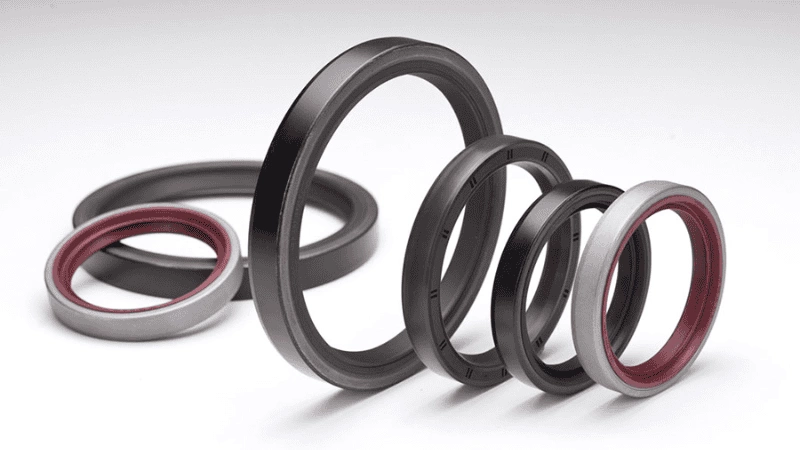
Used for:
- Pure PTFE O-rings are challenging to apply; nonetheless, PTFE-embedded O-rings manage surface wear excellently.
- Can withstand abrasion and corrosion
Note: PTFE exhibits low absorption, chemical inertness, and non-permeable properties.
Temperature range: between -100 ° F and 500 ° F.
Ideal for: paint guns and automotive steering devices
Caution: PTFE rubber O-rings are well-fitted for static applications because they are rigid to apply.
Fluorosilicone
Used for:
- applications with some chlorinated and petroleum-based solvents
- scenarios with exposure to dry heat and jet fuel
Temperature range: between -90 ° F to 350 ° F
Ideal for: automotive, aerospace, and chemical industries
Avoid/Caution: Ammonia, Ketones such as MEK, some acids, Phosphate esters, aircraft, and automotive brake fluids
Fluorocarbon O-rings (Viton)
Used for:
- Handling several different applications, including a wide range of sealing jobs that involve relative motion (or involve movements)
- Some halogenated hydrocarbons, such as carbon tetrachloride
- Acids, petroleum oils, gases, and silicone fluids
Ideal for: appliances, automotive, and chemical processing industries
Caution: Not suitable for hot hydraulic acids, phosphate ester hydraulic fluids, ethers with low molecular weight, amines, and Skydrol
FFKM
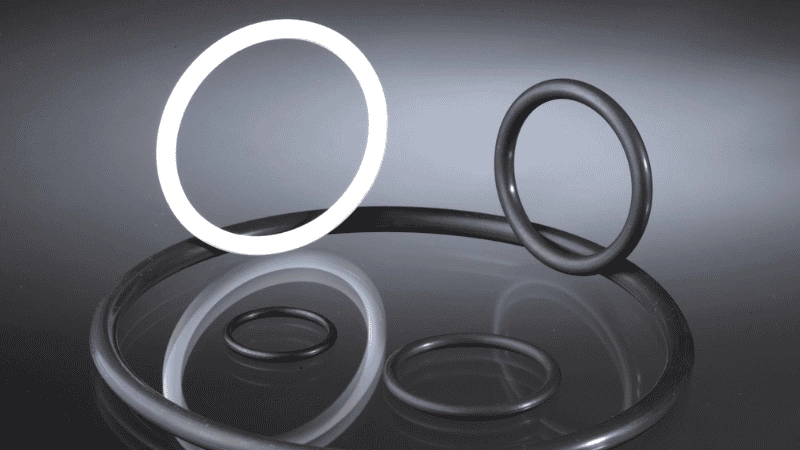
Used for:
- Environments/scenarios with a high cost of downtime or maintenance
- Where low outgassing is needed
- Where high-temperature resistance is required
Temperature range: between 5 ° F to 625 ° F
Ideal for: manufacturing food and beverages, Life Sciences, gas, and oil
Caution: Not recommended for halogenated freons/fluids, gaseous alkali metals, or molten metals
Polyurethane O-rings
Used for: general toughness and extrusion and abrasion resistance
Temperature ranges: between -65 ° F and 212 ° F.
Ideal for:
- Firearms
- Hydraulic cylinders
- Pneumatic tools
- Hydraulic fittings
- Valves
Caution: Not suitable for applications calling for excellent heat resistance and compression
Inquire About Our Silicone and Plastic Products!
What is the difference between a seal and an O-ring?
A gasket or seal is a flat piece commonly used to create a tight seal between two flat surfaces, for instance, a bolted joint. Gaskets usually come in circles; however, they are also available in various shapes.
On the other hand, an O-ring comes in a round and ring-shaped form, typically fitted in a groove to secure a solid seal between two joints.

Seals and O-rings are crafted with flexible materials, but metals and incredibly sturdy elastic polymers are also utilized for manufacturing gaskets.
Seals may be layered with special coatings to suit a wide range of applications, while you can customize an O-ring’s thickness to make it suitable for specific purposes.
What are O-rings used for?
You use O-rings to provide a reliable seal between two pieces of joints to obstruct the unwanted escape of liquids, gases, air, and other substances.
Since O-rings can keep gasses, air, and liquid from entering freely, you can quickly locate them in mechanical components and processes.
In particular, you can find them in environments with high temperatures and pressure. Surprisingly, you can also find O-rings in the following:
High-pressure environments
They are typically used in environments prone to high pressure, where a rubber or paper gasket or a regular cork is more susceptible to breakdown.
Chiefly, high-temperature O-ring seals are specially built to resist extreme heat while at the same time ensuring a dependable seal between two components.
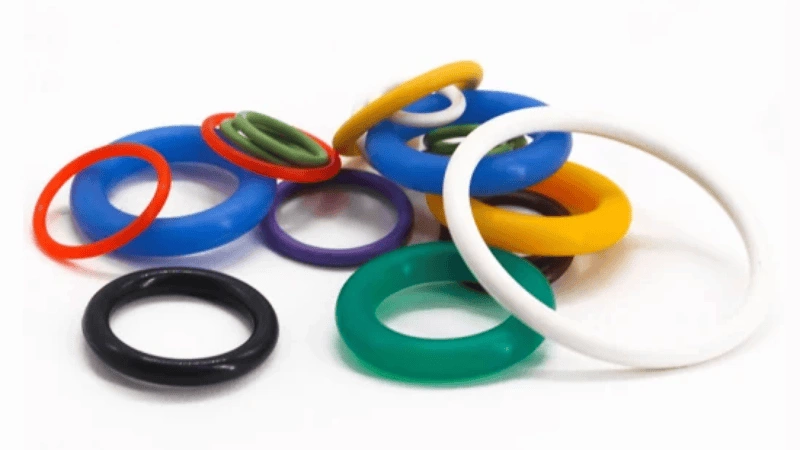
O-rings are in demand in environments and industries such as chemical processing, gas, oil refineries, or other areas where a high-temperature seal is needed, such as aerospace engineering and turbo engines.
Pneumatic, Static, Hydraulic, and Dynamic Components
They’re also used with pneumatic, static, and dynamic applications and hydraulic components, making them unrivaled in providing an effective solution to various engineering problems.
Plumbing O-ring Seals
Plumbing O-ring options are prevalent, given the range of gauges, sizes, and materials for pipework and ducting purposes. In addition, O-rings help secure solid waterproof seals surrounding faucets and other fittings.
Picking the most excellent O-ring for the job largely relies on determining the suitable shape and size for a specific purpose.
Scuba Gear
O-rings are also used in scuba gears, serving as a life-saving component of breathing apparatus.
If you notice, divers check the O-ring in the neck of their air tank before diving.
This approach is crucial since you can determine if it can provide a tight seal and transport air to the regulators.
Food Grade O-ring Seals
These seals have been made to more rigorous standards of material composition than common seals. Such O-ring material has been asserted as “food safe” in preparing and producing dining products, refreshments, meals, etc.
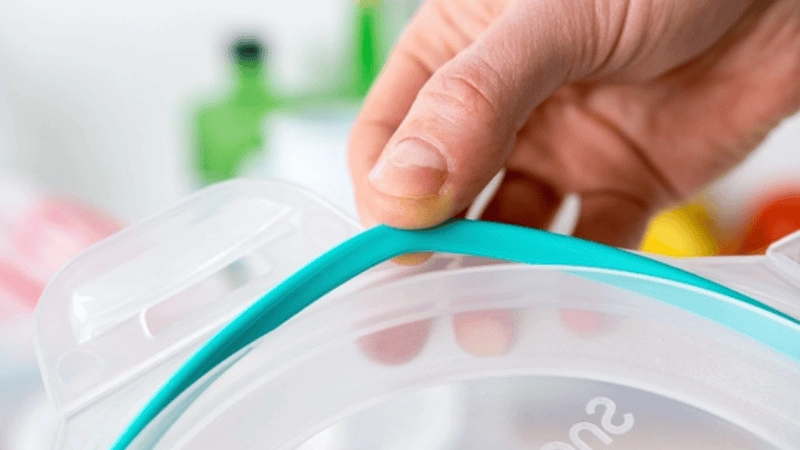
Did you know that without the help of O-rings, it’s impossible to transfer the beer from the container to the tap or to carbonate it to create refreshing and sparkling refreshment?
Yes, that’s right; O-rings play a vital role in our leisure and relaxation when drinking beer.
Aerospace O-rings
These O-rings feature superior chemical resistance, making them adept at operating within an extensive range of pressures and temperatures, enabling the aircraft’s powertrain to work sleekly, efficiently, and neatly.
Aerospace O-rings are commonly utilized for valve cover seals, fuel system O-rings, and fuel cap gaskets.
Paintballing Activities
Are you into paintballing hobbies? If so, you probably know that paintball guns utilize compressed air to blast batches of paint at unprepared opponents.
You use O-rings throughout the gun to ensure that the air is tightly sealed and can secure a strong shot.
O-ring Seals for Engines
O-ring seals used for engines, particularly turbo or high-performance ones, are incredibly durable in material build and design.
The O-ring design should be sturdy enough to withstand rigorous chemical compatibility requirements, high pressure, and extreme temperature.
Dental Implants
Do you have dental implants? Dental professionals must keep the liquid out of the implant to protect their patients from infection or pain.
To make this possible, they use a biomedical ring or silicone that creates a secure seal and keeps the new tooth safe.
Inquire About Our Silicone and Plastic Products!
Conclusion
O-rings are versatile sealing devices used to prevent the leakage of liquids and gases. They are typically made of rubber and are designed to be seated in a groove and compressed during assembly between two or more parts, creating a seal at the interface.
O-rings are used in various applications, including automotive, aerospace, and hydraulic systems, due to their cost-effectiveness, simplicity, and reliable sealing capabilities. Their effectiveness depends on maintaining the correct size, material, and operational conditions to withstand the specific pressures and temperatures of their application environment.
Get the Seal of Quality with Hongju O-Rings
Ensure the integrity of your machinery with Hongju‘s high-quality O-rings. Trusted in various industries, our O-rings provide superior sealing solutions that stand up to any challenge. Shop now and experience the reliability that only Hongju can deliver. Upgrade your equipment today with Hongju O-rings!