In this blog, you will learn about the differences between TPE and silicone, their properties, and their respective applications. We will also give you tips on how to choose the right TPE or silicone product for your needs. So, let’s start!
What is Thermoplastic Elastomer (TPE)?
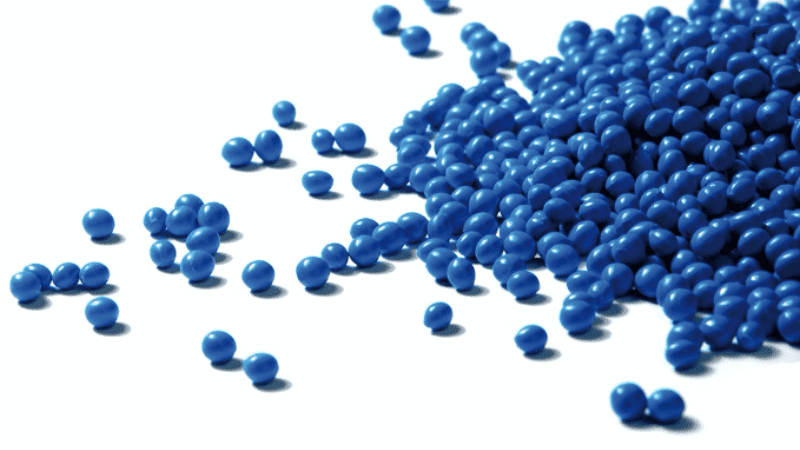
Thermoplastic Elastomers (TPE), also known as Thermoplastic Rubber (TPR), belong to a unique category of copolymers or a blend of polymers. This mix usually involves plastic and rubber, combining to offer characteristics similar to both.
TPEs are unique because they can be heated and cooled multiple times. When they are heated, they become soft and easy to shape. Then, once they cool down, they harden again. This special feature comes from their mixed makeup (of plastic and rubber as we just said above), which allows TPEs to be used in many different ways.
What is Silicone?
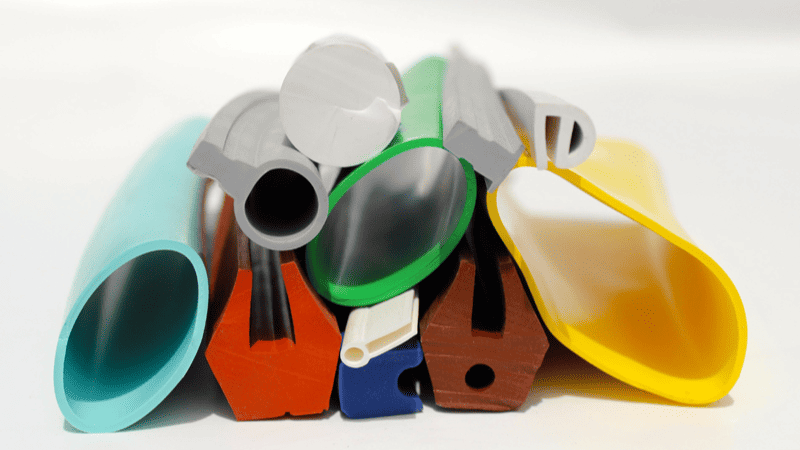
Silicone, or polysiloxane, is a flexible, durable polymer made of siloxane. Siloxane is a chain of alternating silicon and oxygen atoms, often combined with carbon and hydrogen. Unlike conventional polymers, silicone’s structure gives it a unique set of properties.
Generally found in either fluid form as colorless oils or solidified as rubber-like materials, silicones stand out due to their versatility. This versatility allows silicones to be used in a wide range of applications. Some common uses of silicone include adhesives, sealants, lubricants, insulation, and medical devices.
Send your inquiry for prompt quotations!
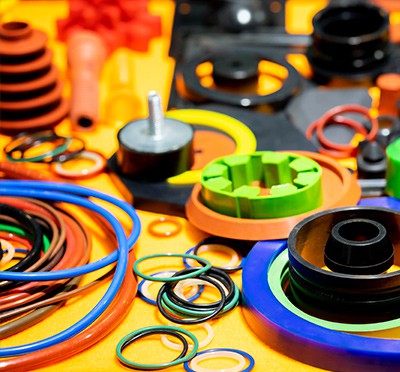
Property Differences: TPE VS. Silicone
Several key differences between TPE and silicone affect their properties and applications. Let’s look at each of them in detail to understand the key differences.
Temperature Resistance
Silicone exhibits exceptional heat resistance and does not possess a definitive melting point as silicone injection molding requires higher temperatures. This characteristic makes silicone rubber remarkably durable across both high and low-temperature extremes. Remarkably, silicone rubber maintains its properties indefinitely at temperatures up to 150°C.
It continues to perform efficiently even at 200°C for durations extending beyond 10,000 hours, with certain silicone products capable of withstanding short-term exposure to temperatures as high as 350°C. This exceptional thermal stability lends silicone its widespread application in environments requiring resistance to severe temperature fluctuations without degradation.
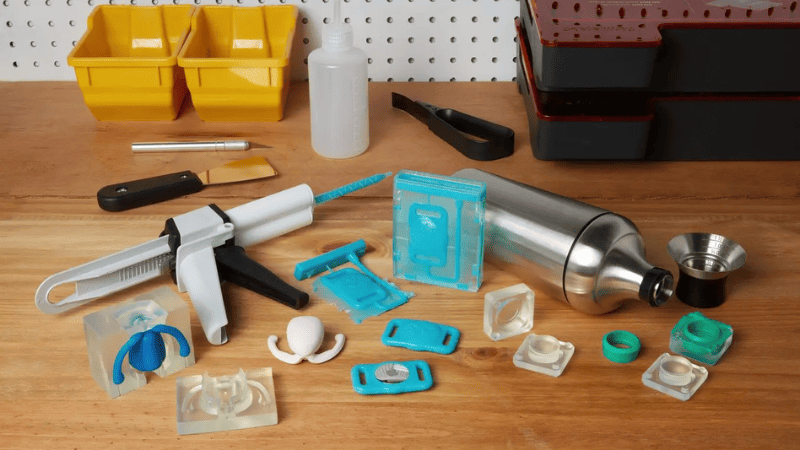
The thermoplastic Elastomer material also demonstrates a broad but limited temperature resistance range, spanning from -30°C to +150°C. This range indicates that TPEs can ensure material stability and retain their thermal properties across various temperatures, making them versatile for numerous applications.
However, note that TPEs have a defined melting point, typically between 260°C and 320°C. This means that, unlike silicone, TPE materials can be melted down and reprocessed through heating and cooling cycles.
While TPEs can handle both cold and warm temperatures pretty well, they can start to change shape if they get too hot, specifically above their melting point. This behavior sets them apart from silicone, which can withstand much higher temperatures without losing its shape or properties.
Chemical Resistance
Silicone stands out for its solid resistance against water, oxidation, ozone, and a vast spectrum of chemicals. However, its resistance shakes when faced with steam, hydrocarbon fuels, alkalis, acids, and aromatic hydrocarbons. This particular resistance profile makes silicone an ideal candidate for environments that demand high chemical stability, such as in the manufacturing of medical equipment, cooking utensils, and insulation materials.

On the other hand, TPE shows commendable resistance to water, oils, greases, and some solvents, though it falters against strong acids, bases, or oxidizing agents. TPE isn’t quite as tough against chemicals as silicone is, but it still does a pretty good job. This makes TPE good for making things like car parts, stuff we use every day, and sports gear. In these cases, the items don’t run into super strong chemicals that often.
Biocompatibility
Another key difference between the two materials is biocompatibility. Biocompatibility is the ability of a material to perform with an appropriate host response in a specific application. It indicates how suitable a material is for use inside the human body.
Silicone is widely used in the prosthetic and medical industry due to its excellent biocompatibility. This means that it does not cause adverse reactions when placed inside the body, making it safe for prolonged contact. TPEs, on the other hand, are not as biocompatible as silicone and are mostly used in non-medical applications.
Barrier Properties
Barrier properties are the ability of a material to prevent the passage of gases or liquids. Here, TPEs do an awesome job. This is super important for medical stuff, like when you need disposable gloves that keep out germs and other nasty things. People who are allergic to latex can use these gloves without any issues. In the world of drinks, especially for beer lovers, TPEs are used inside the caps of bottles to make sure the beer stays fresh and doesn’t lose its taste by letting oxygen sneak in.
Silicone, though, actually lets air pass through it. This might sound like a downside, but it is super useful for stuff like bandages that cover wounds or contact lenses that need to let your eyes breathe. And, if you mix in a material called polytetrafluoroethylene with liquid silicone rubber, you will get even better at keeping stuff out or in, whichever you need.
Recyclability
Recycling, of course, is a vital consideration in the selection of materials for various applications. Silicone presents a challenge in this regard. Due to its solid nature, breaking down the chemical bonds of silicone requires high temperatures and special catalysts. As a result, it is considered less environmentally friendly and more expensive to dispose of or recycle.
If we look at TPE, it stands out for its recyclability. It can be melted down and reshaped multiple times, all while retaining its quality. This attribute not only makes TPE more environmentally friendly but also offers an economical advantage by facilitating reuse.
Send your inquiry for prompt quotations!
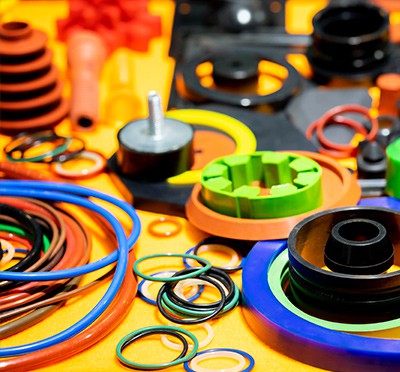
Applications of Silicone and TPE in Industries
Both silicone and TPE have unique material properties that make them suitable for various applications across different industries. Some of the common uses of these materials are discussed below:
Silicone Applications
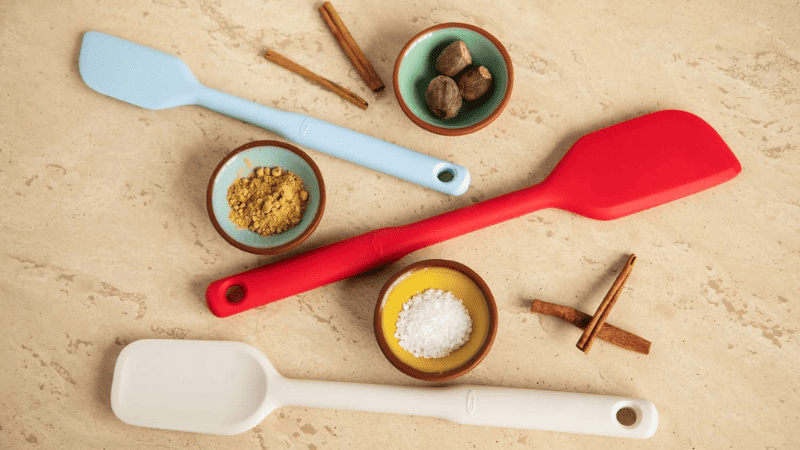
Some of the most common applications of silicone are:
- Electronics and Computing: Extensively used in manufacturing keypads, keyboards, and copier rollers thanks to its protective and insulating capabilities. It is also used in the production of computer parts, mobile devices, and home entertainment systems.
- Lighting Technology: Significant role in advancing LED lighting technology. Its high thermal stability, combined with excellent dielectric properties, makes it a preferred material for various electrical transmission applications.
- Solar Energy Devices: Enhances the efficiency, durability, and performance of solar panels and photovoltaic devices. Its unique ability to withstand prolonged sun exposure makes it an ideal choice for solar technology.
- Kitchenware: Silicone bakeware and cookware are favored for their flexibility, non-stick surface, and ease of cleaning. These products can go from the freezer to the oven or microwave and then to the dishwasher without impacting the food’s flavor or quality.
- Construction and Exterior Coatings: Silicone-enriched paints ensure the exterior surfaces of buildings or bridges remain flexible enough to withstand freeze-and-thaw cycles without succumbing to cracks. Additionally, highway and road coatings become more resistant to salt spray and acid rain, reducing rust.
- Personal Care Products: In the world of personal care, silicone enhances the feel of products like deodorants by minimizing white residue. It also contributes to the lasting effect and vibrant appearance of cosmetics, shampoos, and conditioners.
TPE Applications
TPE’s most common applications include:
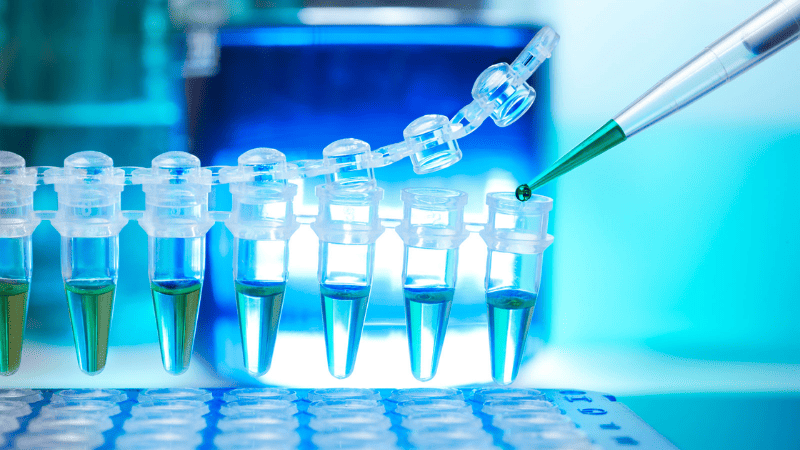
- Automotive: Used in components such as weather seals, shock dust boots, bumpers, and various parts both inside and outside the car, including trims, instrument panels, air ducts, and drive belts.
- Construction: Features in extruded seals for doors and windows, with applications in simple or co-molded hydraulic seals, glazing seals, and pipe seals.
- Consumer Goods: Found in magnetic seals for refrigerators, power tool handles, remote control covers, mobile phone covers, push-button panels, etc.
- Medical: Integral to the production of breathing tubes, syringe seals and tips, ventilation masks, bags, seals, valves, and catheters.
- Electronics: Utilized for the sheaths of condensers, plugs and loose sockets, specialty cables, and components in mobile phones.
- Footwear & Sporting Goods: Essential for the manufacture of items used in diving and skiing, along with other sports goods and shoe soles.
It is worth mentioning that both silicone and TPE can be used to make sex dolls, if you want to know more, please click here.
Send your inquiry for prompt quotations!
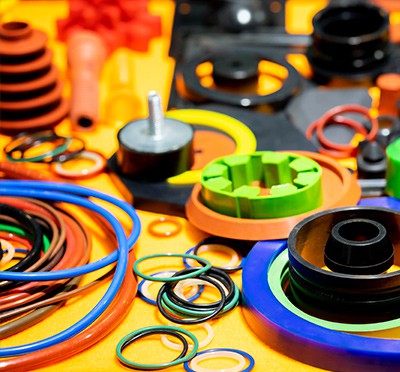
Are TPE And Silicone Safe To Use?
Safety comes first in all aspects of life, and the same applies to using materials. Silicone, widely acknowledged as chemically stable, is considered safe and likely non-toxic by experts. This assurance has led to its extensive use in the medical field, particularly for cosmetic and surgical implants aimed at enhancing body contours.
Similarly, TPE stands out for its hypoallergenic nature, making it an unlikely candidate to trigger allergic reactions. Furthermore, TPE is recognized for being free from potentially harmful substances such as phthalates, latex, and BPA, reinforcing its safety profile for widespread use in consumer products.
So, both TPE and silicone offer a safe choice for use in various industries.
Tips to Choose the Right Material
After going through the detailed comparison of silicone and TPE, it is up to you whether to go for the chemical stability of silicone or the recyclability of TPE. Here is a quick guide to help you make a decision that you will not regret later:
Choosing Silicone
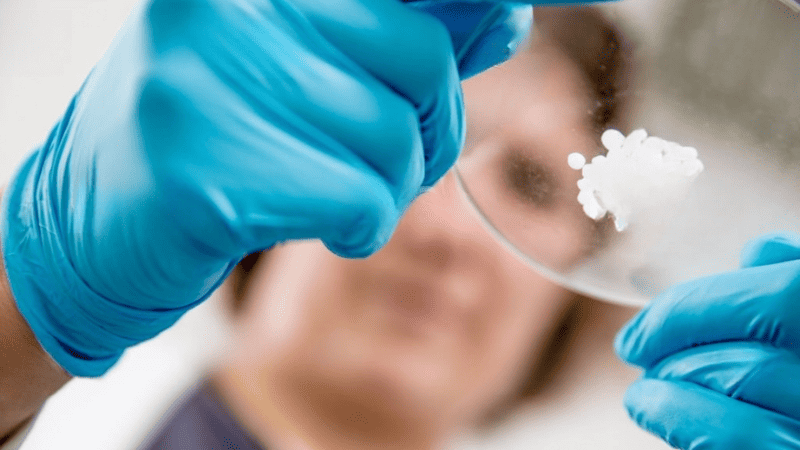
If you opt for silicone as your material of choice, you have to understand that not all silicones are created equal. Different applications require specific types of silicone, each with its unique set of properties such as flexibility, durability, and resistance to various conditions.
When selecting the right silicone for your needs, consider the desired chemical, mechanical, and physical properties necessary for the product’s intended use. For example, Liquid silicone rubber parts can be used to replace glass in applications where safety is a concern. This careful consideration ensures that you choose a silicone material that is perfectly suited to meet your project’s requirements and offers the best performance and durability.
Choosing TPE
Similarly, in the case of TPE, selecting the appropriate material involves carefully analyzing its intended application. Initially, consider the material currently in use and identify areas where improvements might be necessary, or if there’s a particular price point to achieve. Outline any specific functional or performance requirements the TPE must meet.
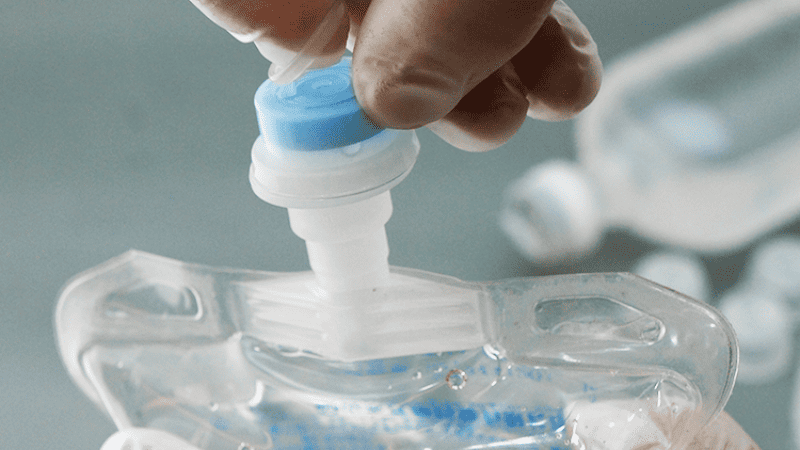
Understanding the manufacturing process—whether through injection molding, extrusion, or blow molding—is vital since TPE formulations vary significantly based on their processing. If the TPE is intended for over-molding or co-extrusion onto another material, choose a type that ensures strong adhesion, as compatibility varies across different substrates.
With this quick guide, we believe you can now choose the suitable material for your specific needs. Both TPE and silicone offer unique properties that make them valuable in their respective applications. Just remember to consider your project’s requirements and conduct thorough research before making a decision.
Send your inquiry for prompt quotations!
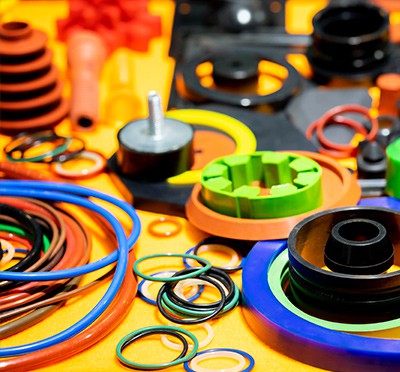
Conclusion
The debate between TPE and silicone has no clear winner as both materials offer distinct advantages in different applications. While TPE is prized for its recyclability and versatility, silicone stands out for its chemical stability and durability.
In the end, choosing between TPE and silicone comes down to understanding the specific needs of your project and selecting the material that best meets those requirements. Just one last thing: Both are great and safe options!
Get Premium Quality Silicone Products by Hongju
Experience the perfect blend of safety and sustainability with Hongju‘s eco-friendly silicone products. Whether you need Silicone Rubber Keypads or Silicone Swim Caps, choose us for superior quality and peace of mind. We have been in the market since 1999, providing custom silicone solutions to various industries worldwide. Learn more About Us and make the eco-conscious choice today!