Consequently, this article explores the properties of different rubber elastomers, their specific applications, and factors to consider before choosing them.
What is a Rubber Elastomer?
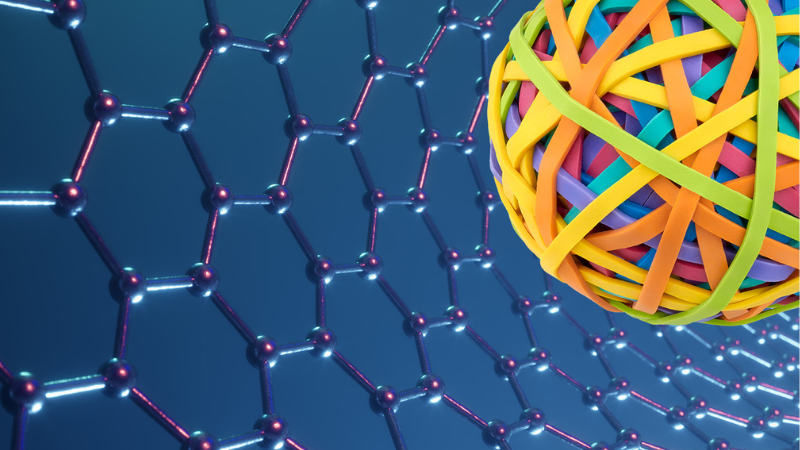
A rubber elastomer is any material that possesses the properties of rubber, including abrasion resistance, resilience, strength, and high-temperature resistance. Usually, the words rubber and elastomers are often used interchangeably.
Elastomers are elastic polymers with properties that make them suitable for various industrial and mechanical applications. As a result, these materials are often synthesized to meet specific needs. On the other hand, rubber is used to describe natural rubber. Natural rubber is an organic compound naturally found in nature from rubber trees.
Unlike elastomers, natural rubber is not a category of materials with elastomeric properties. Instead, it is a specific compound.
What are Rubber Elastomer Properties?
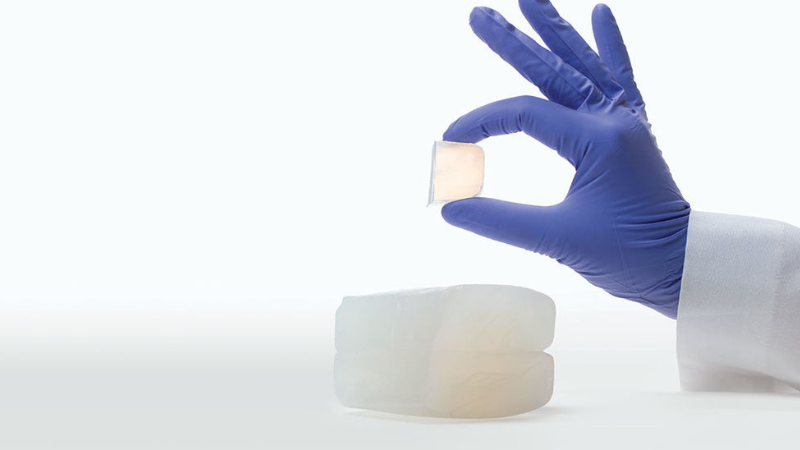
There are several properties of elastomers that make them suitable for specific applications. These properties include;
- Water resistance
- Abrasion resistance
- Chemical resistance
- Gas permeability
- Compression set
- Electrical properties
- Weathering resistance
- Oil resistance
- Heat resistance
- Flame resistance
- Low-temperature resistance
Water Resistance
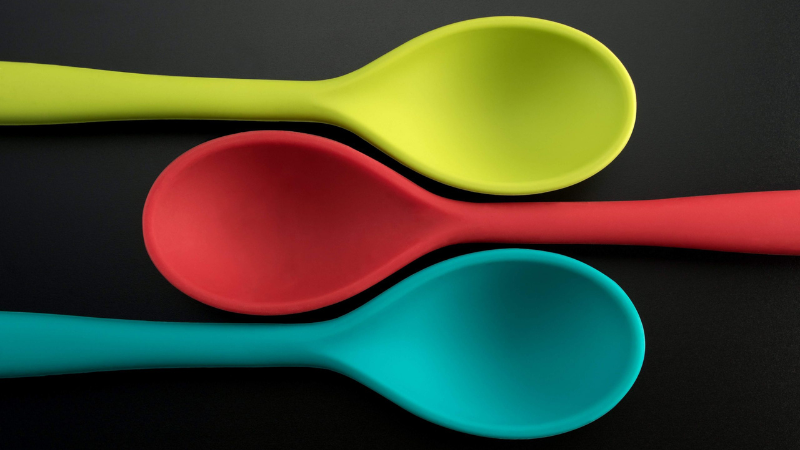
The water resistance of an elastomer is the ability of that elastomer to withstand the effects of water immersion. A water-resistant elastomer has excellent stability upon immersion for the long term. Usually, water-resistant elastomers are used in several applications, including sealants, paints, and tubings.
Abrasion Resistance
The abrasion resistance of an elastomer is the ability of that elastomer to withstand consistent harsh conditions, including scraping, rubbing, or scratching. An abrasion-resistant rubber can withstand wear and tear in high-friction mechanical applications. Abrasion-resistant rubber helps make rubber grommets, tires, gaskets, seals, and o-rings.
Chemical Resistance
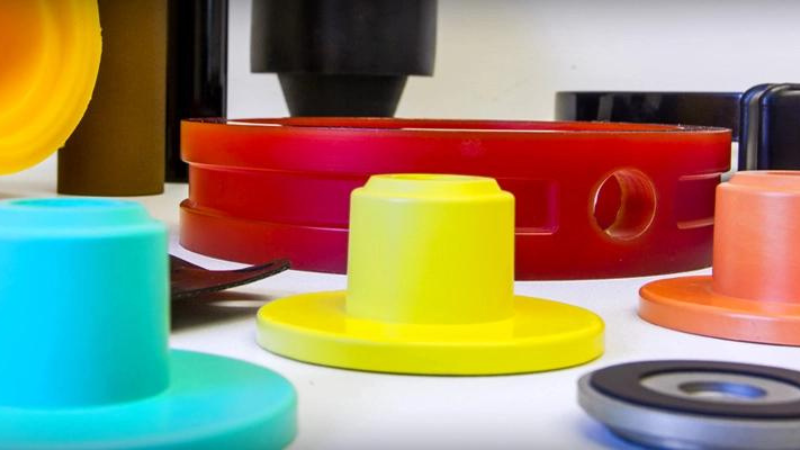
Chemical-resistant elastomers can withstand attack from chemicals for a specific period. Usually, these elastomers do not degrade or degenerate upon exposure to certain chemicals.
However, it is essential to note that elastomers have varying degrees of resistance to various chemicals. For instance, some elastomers can withstand mineral acids but, at the same time, are not resistant to phosphate esters.
Gas Permeability
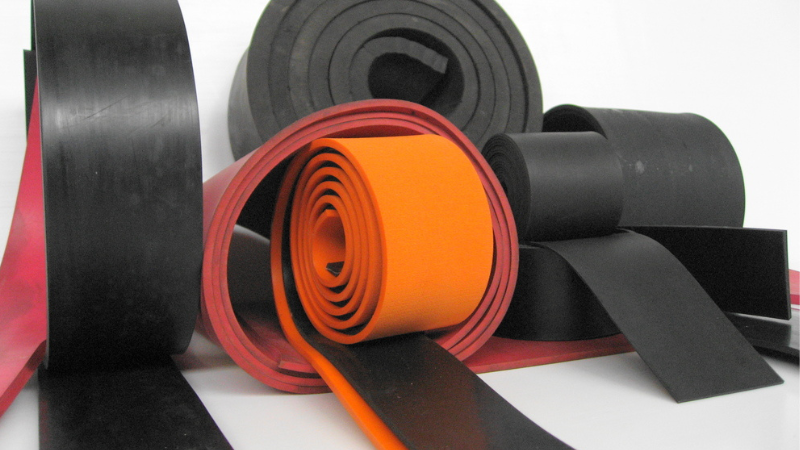
Gas permeation is the rate tiny gas molecules pass through an elastomer. Elastomers with low gas permeability are more resistant to gas permeation. Applications like vacuum sealing and inner tubings need elastomers that can withstand gas permeation.
Compression Set
A compression set is the amount of permanent deformation in an elastomer after exposure to a force for a specified time. This property is often expressed as a percentage. For example, a zero compression set means an elastomer returns to its initial size after removing the force. In contrast, a 100% compression set means the elastic material remains deformed and does not recover after removing the power.
Elastomers with low compression sets are ideal for dynamic sealing applications due to constant exposure to varying levels of force.
Electrical Properties
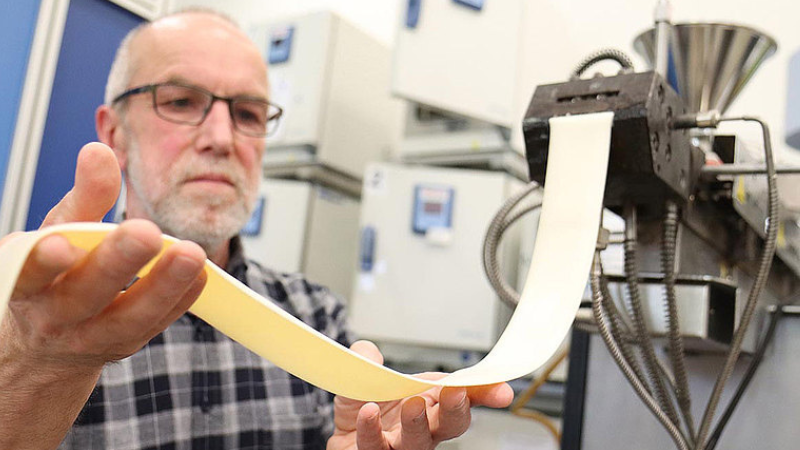
Elastomers are known to be insulators, preventing the free flow of electrons. Rubber materials with excellent electrical properties can work at high temperatures and under wet conditions without losing their form or shape. Electrical insulating rubbers are usually used in making cable connectors and insulators.
Weathering Resistance
An elastomer’s weather resistance is its ability to retain its form on prolonged use in outdoor applications. However, not all elastomers are weather-resistant due to ozone and UV exposure.
Oil Resistance
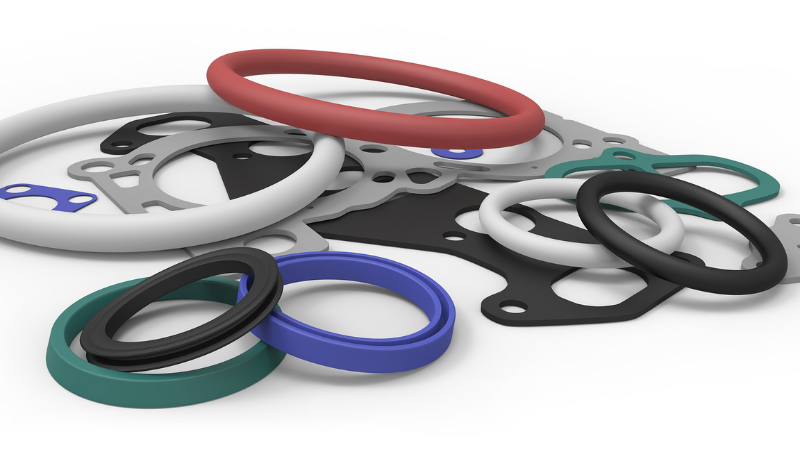
Oil attacks rubber and weakens it. Oil-resistant elastomers can withstand hydrocarbon fluids and mineral and vegetable oils without deforming. Rubber materials with good oil resistance are suitable for automotive fuel applications.
Heat Resistance
The heat resistance of rubber materials is the ability of that material to retain its shape and form upon exposure to extreme temperatures for a prolonged period. Not all elastomers are heat resistant. Some elastomers are more resistant to higher temperatures than others.
Flame Resistance
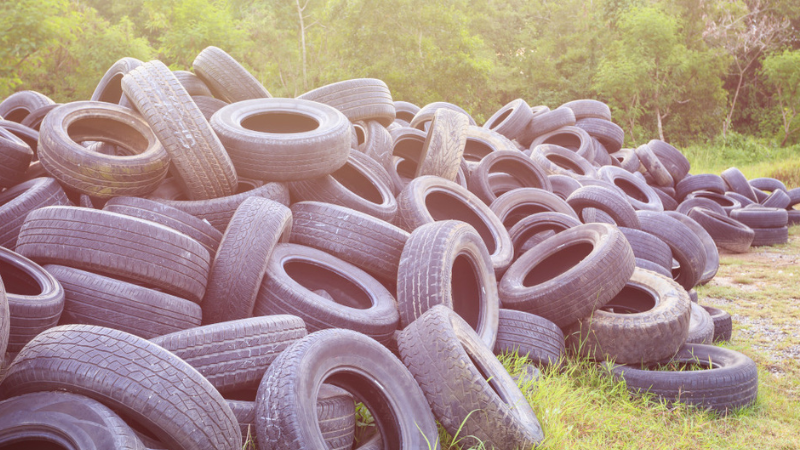
Very few elastomers are flame resistant or non-flammable. Flame-retardant synthetic elastomers can withstand fire while retaining their form. Elastomers with poor flame resistance undergo irreversible chemical changes.
It is important to note that not all high-temperature-resistant elastomers are flame retardants. Nevertheless, many elastomers can be compounded to have fire-resistant properties.
Low-Temperature Resistance
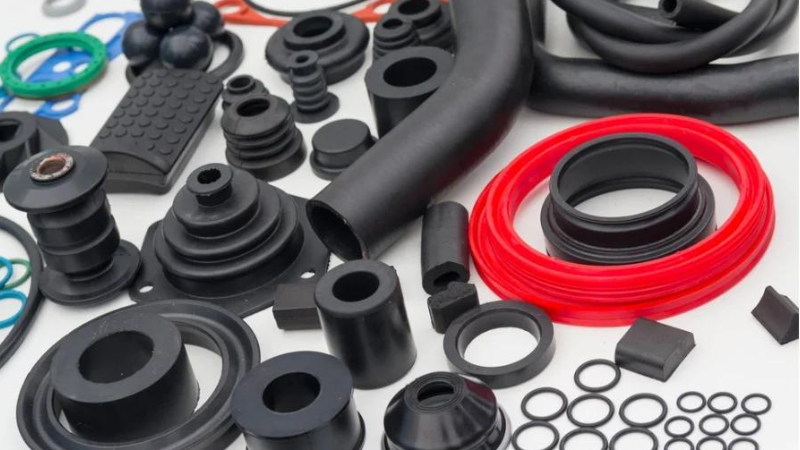
Besides working in high-heat applications, several low-temperature applications require elastomers with low-temperature flexibility. Unfortunately, some elastomers lose their flexibility at low temperatures and cannot respond to force. As a result, these rubber materials stiffen and become very hard and brittle.
What are the Different Types of Rubber Elastomers?
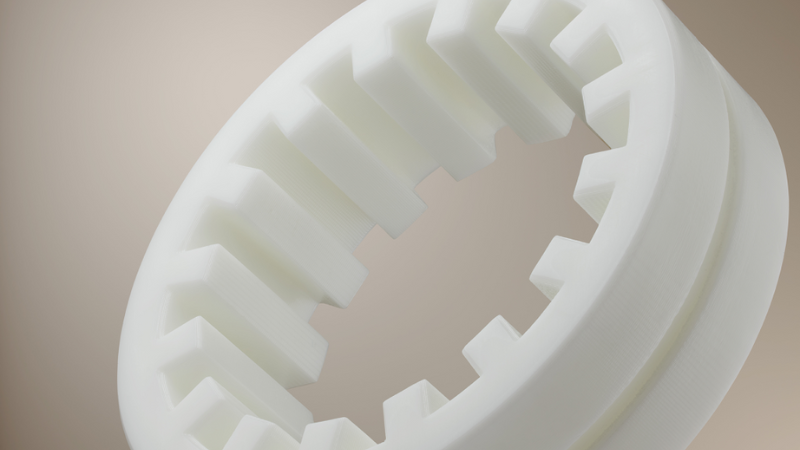
There are several synthetic rubber materials. This section summarizes the properties of some of these elastomers. It is important to note that this list is not exhaustive. Other significant rubber materials include styrene butadiene rubber (SBR) and hydrogenated nitrile rubber.
1. Vulcanized Rubber Elastomer
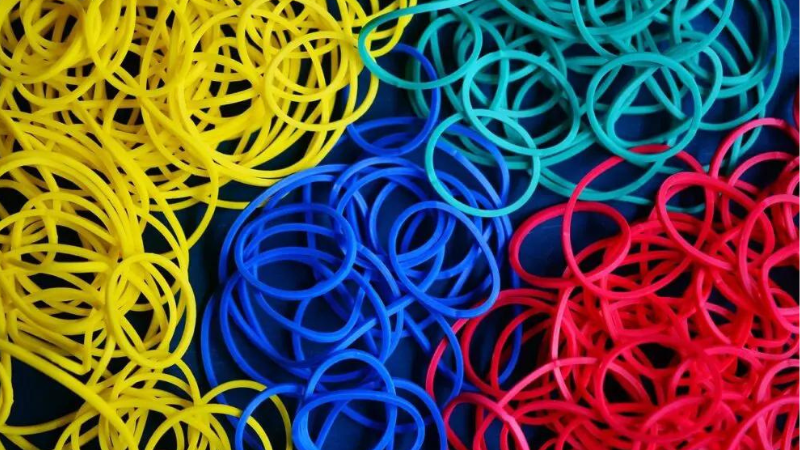
Vulcanization strengthens natural rubber through the addition of heat and sulfur. Unlike natural rubber, vulcanized rubber is more elastic and can withstand higher pressure and stress.
The properties of vulcanized rubber include excellent resilience, tear resistance, low water absorption, chemical resistance, and excellent tensile strength. Furthermore, this type of elastomer has increased electrical insulation and good resistance to abrasion.
2. Butyl Rubber Elastomer
Butyl rubber is synthetic. This elastomer is made from a combination of isoprene and isobutylene. Furthermore, the elastomer is known for its low gas permeability and biocompatibility.
Other properties of butyl rubber include its chemical, ozone, and abrasion resistance. It also has excellent electrical insulation properties. Unfortunately, butyl rubber has poor fuel resistance
3. Nitrile rubber Elastomer

Nitrile elastomers are oil-resistant synthetic rubbers. This elastomer possesses chemical and physical properties that make it widely used in the seal industry. Properties of nitrile rubber include its excellent resistance to water, fuels, and petroleum-based oils.
Furthermore, this synthetic rubber can withstand hydraulic fluids, alcohol, and silicone greases. Other properties of nitrile rubber include its good abrasion resistance, high tensile strength, and low compression set.
4. Neoprene Rubber Elastomer
Neoprene is a multi-purpose elastomer with waterproof and chemical-resistant properties. In addition, this rubber material has properties that make it resistant to degradation, burning, and corrosion.
Furthermore, this rubber is biocompatible and sometimes used as a latex substitute. Other properties of neoprene rubber include its good water, oxygen, flame, and ozone resistance.
5. Silicone Rubber Elastomer
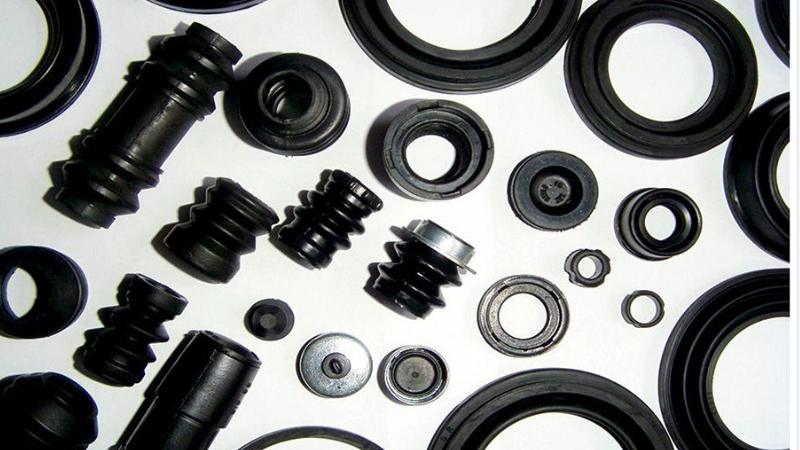
Silicone is a versatile rubber material used in several applications because of its stability in elevated temperatures. It is also known for its low-temperature properties.
Furthermore, this elastomer has characteristic chemical and physical properties that make it suitable for water, steam, or fuel applications. It also has excellent chemical stability, and it is biocompatible. Thus, it is used widely in medical and food-grade applications.
6. EPDM Rubber Elastomer
EPDM is short for ethylene propylene diene monomer. This synthetic elastomer has excellent properties, making it an alternative to silicone rubber. In addition, this elastomer is an even more cost-effective option. Properties of EPDM include heat and weather resistance. This elastomer is also an excellent electrical insulator.
What are the Applications for Each Type of Rubber Elastomer?
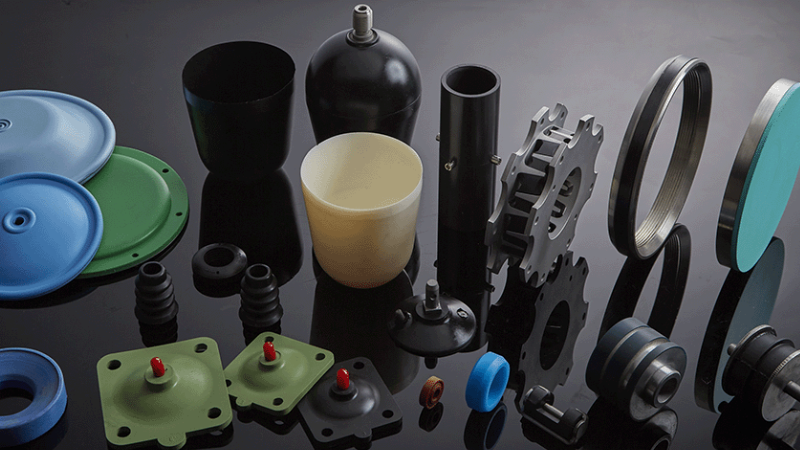
Each rubber elastomer has unique properties, making it suitable for several industrial applications. This table shows the application of different rubber elastomers.
Rubber Elastomer | Applications |
Vulcanized rubber | This elastomer has excellent resilience, making it suitable for the manufacture of vehicle tires, rubber hoses, toys, o-rings, rubber grommets, and gaskets |
Butyl rubber | This elastomer is used to produce inner tubes and air-filled balls used in sports. As a liquid, this elastomer is used as a cleanser for fuel injectors and to manufacture products for cleaning oil spills |
Nitrile rubber | This elastomer is used in the automotive industry to produce gaskets, o-rings, hoses, and seals. It is also used to manufacture heavy-duty protective gloves and molded goods, including floor mats and footwear |
Neoprene rubber | This elastomer is used in corrosion-resistant coatings, adhesives, and belts. It also manufactures gaskets, masks, fire doors, and equipment. Furthermore, household goods like dishwashing gloves are made from this rubber |
Silicone rubber | This elastomer is used in medical and food-grade applications because it is biocompatible and hypoallergenic. It is used to produce surgical gloves, masks, and medical implants. This elastomer is also used to produce cooking utensils, food storage containers, and cosmetics applicators |
EPDM | This rubber is used in outdoor applications as hoses and door seals. It is also used as a sealant in automotive applications and as a roofing and waterproofing sealant |
How do You Choose the Right Type of Rubber Elastomer for Your Application?
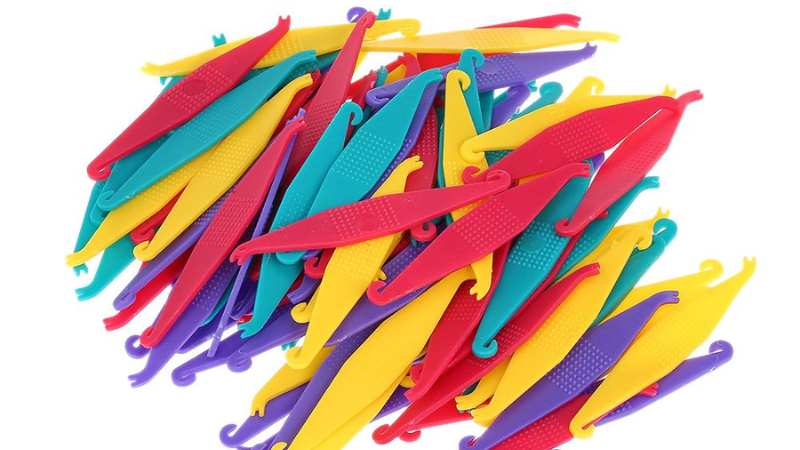
There is no one right type of elastomer for all applications. The controlling conditions of your application determine the best elastomer for your needs. Before choosing a suitable rubber material for your application, consider the following factors;
Temperature
An application’s temperature is an essential operating condition and a significant factor in your choice of rubber elastomers. Therefore, the best elastomer for your project should have a temperature range that fits the project’s temperature range.
Type of Application
Is your application static or dynamic? Not all elastomers are suitable for active or fixed applications. For instance, silicone is more suited to stationary applications, while nitrile rubber is better for dynamic sealing applications. Therefore, it is best to consider the type of application before choosing a suitable rubber material.
Exposure
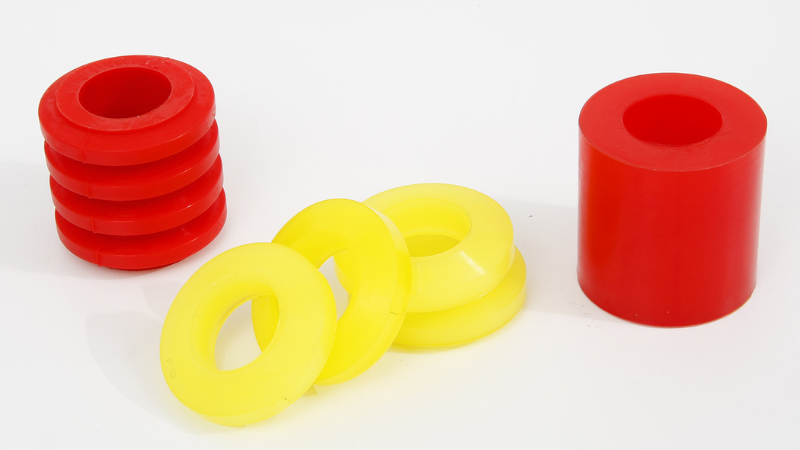
What conditions are you exposing your rubber material to? Is it mineral acids, water, or weather? How long is the exposure? The best rubber elastomer for your application should withstand long-term operating conditions.
Industry Standards
Every industry has its standard for elastomers. For instance, the standards in the food industry differ from those in the automotive industry. Therefore, when choosing an elastomer, consider the industry standards and choose a befitting material.
Availability
The availability of your elastomer significantly affects your project. Production time, cost of supplies, and equipment all depend on the availability of your raw materials. Therefore, it is best to consider an elastomer’s availability before choosing it for your application.
What are Some Common Problems with Rubber Elastomers?
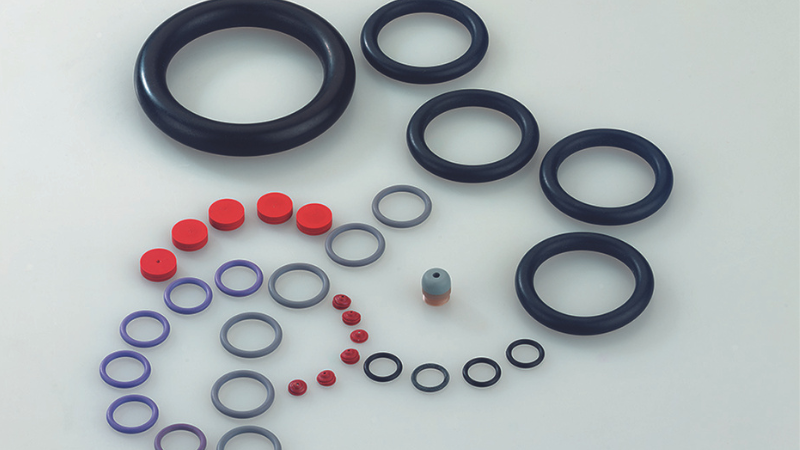
There is no generally common problem with all rubber elastomers because they all possess different properties. Nevertheless, individually, these rubber materials have their shortcomings. The table below shows the common problems with rubber elastomers.
Rubber Elastomer | Common Problems |
Vulcanized rubber | The vulcanization process in itself is costly and hazardous. In addition, this rubber is unrecyclable |
Butyl rubber | This elastomer is costly and difficult to process. It also has poor resistance to petroleum oils. In addition, the elastomer cannot withstand wide temperature ranges |
Nitrile rubber | This elastomer has poor resistance to UV, ozone, and weather exposure. In addition, it is not suitable for steam applications because of its poor heat resistance |
Neoprene rubber | The most significant disadvantage of this elastomer is its cost. It has poor oil resistance. In addition, this rubber material does not perform well in strong oxidizing acids, ketones, and esters. |
Silicone rubber | This elastomer is costly and bulky. In addition, it has poor tear strength. Nevertheless, this tear strength can be improved by the use of additives |
EPDM rubber | This rubber is inert, making it challenging to adhere to. It also has poor chemical resistance to non-polar solvents and most oils. Furthermore, this elastomer has poor fuel resistance. |
Conclusion
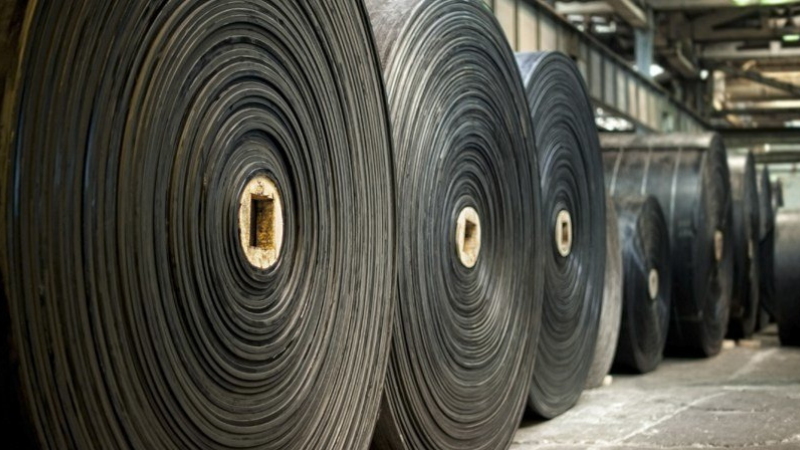
Elastomers have characteristic properties, including water resistance, oil resistance, UV resistance, electrical insulation, and compression set. These properties determine if a rubber material will be suitable for your application.
Therefore, before choosing a rubber material for your application, you must consider the elastomer’s properties and operating conditions. The best elastomers are the ones that suit your application perfectly without any deformations.
Get Quality Rubber Products at Hongju
You don’t have to look any further for quality rubber products. Hongju Silicone is ready to deliver products that meet your specifications when you need them. The company is a leading rubber manufacturer with excellent results when it comes to customizations. In addition, there is top-notch customer service, always ready to answer your questions, ensuring you get the best service.
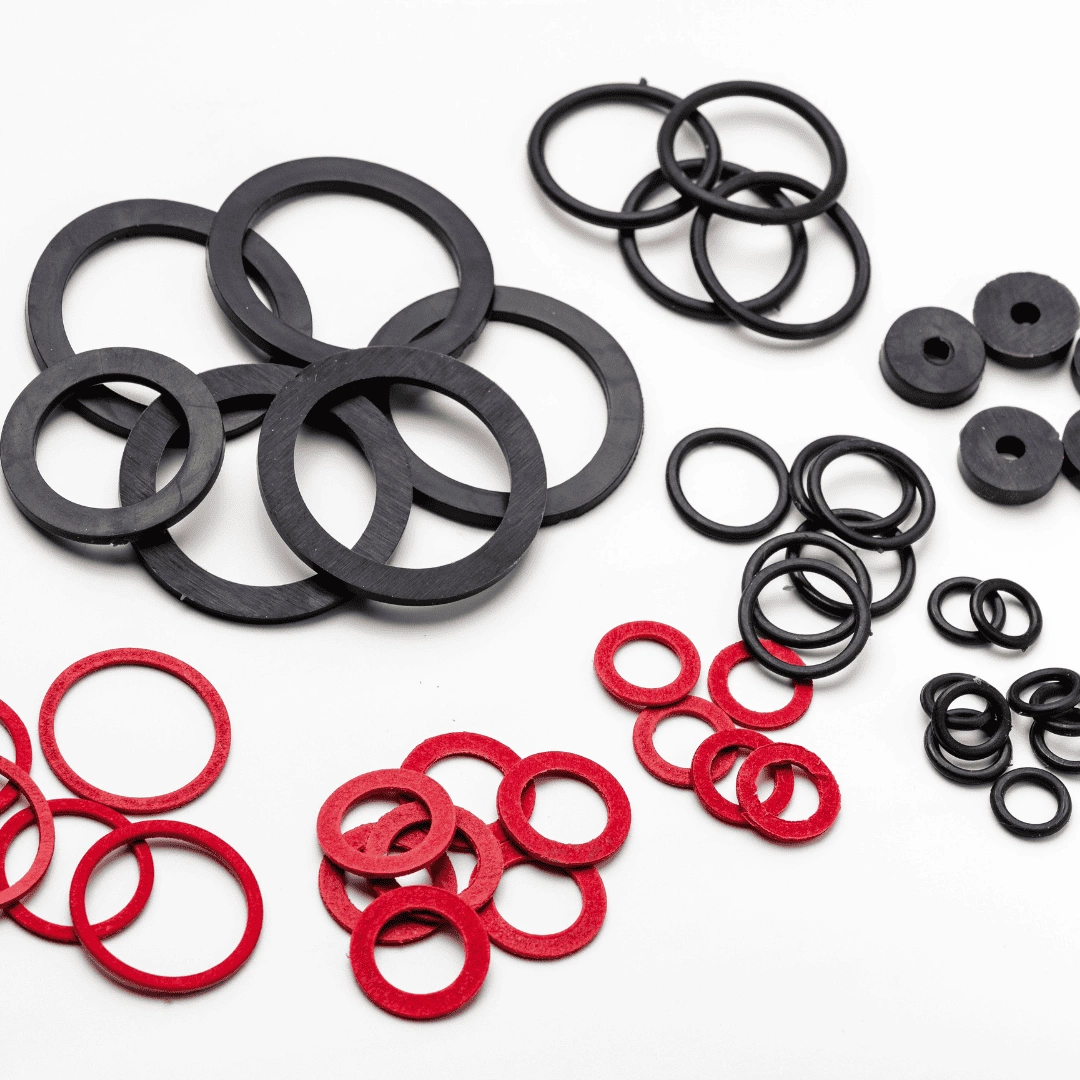
Send Your Inquiry Now!
Quality Meets Affordability. Inquire Now for High-Quality Products at Low Volumes.