In this article, we explore why quality control matters in plastic injection molding and we also discuss six approaches you can use to implement it effectively. Read on to learn how quality control makes it easier to get it right the first time.
Why is Quality Control Important?
Quality control refers to the process that a company or business implements to ensure its products or services meet or exceed a standard. This standard can be set by the company itself, its customers, or an independent body.
For an injection molded part, quality control ensures that it will perform its job as expected and allows the manufacturer or seller to make corrections if deviations from the standards are recorded.
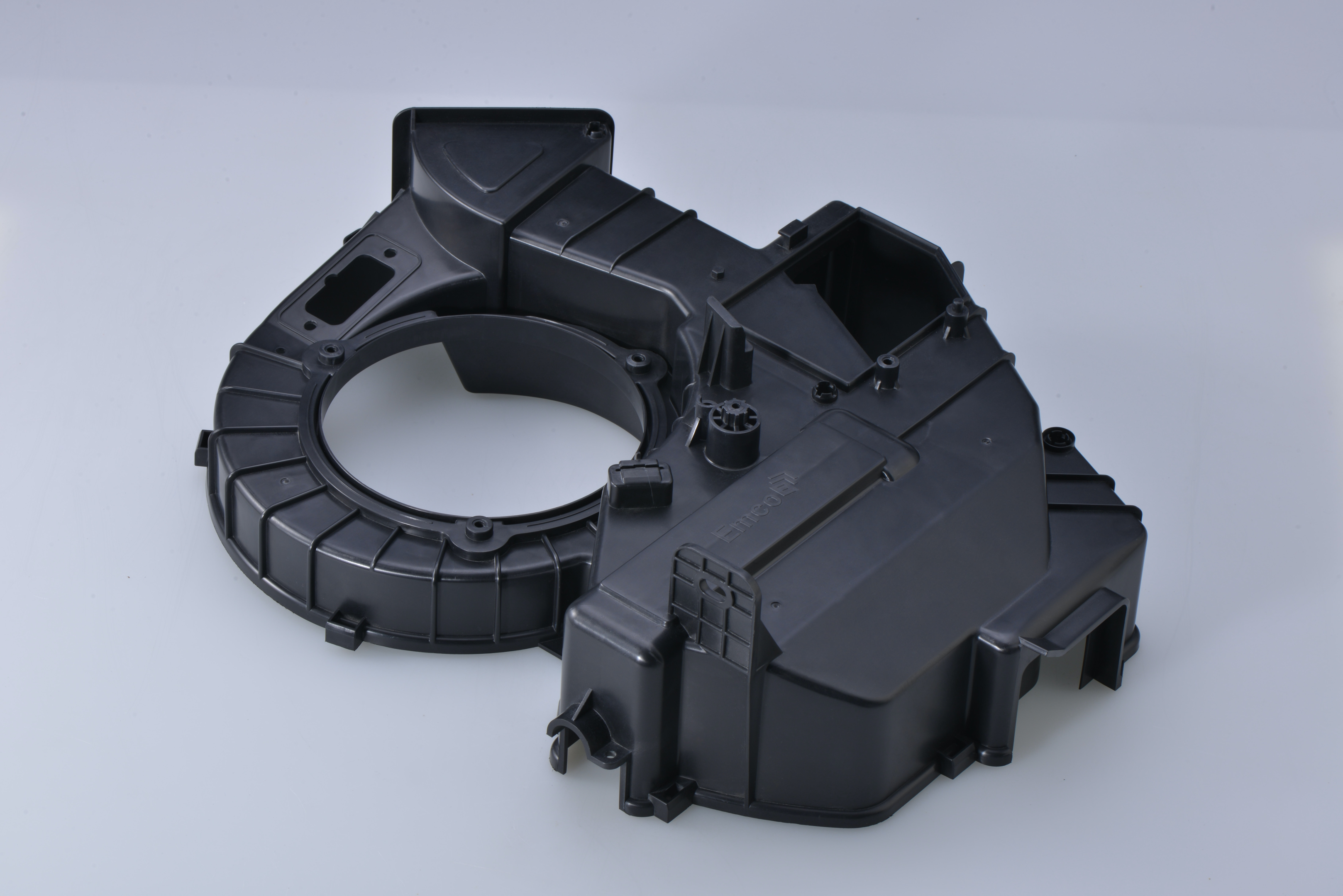
Specific reasons why manufacturers should implement quality control measures include:
- Reducing the number of defective products: Defects mean having to rework, recall, or dispose of finished products. All these options can be costly but they can be avoided if the defective parts or the cause of the defects are noted early.
- Reducing manufacturing costs: In a production process like injection molding, deviations can lead to waste, higher production costs, and lower process/equipment efficiency. Measures as simple as monitoring process parameters can identify these inefficiencies early.
- Compliance: A company may be subjected to heavy fines and other penalties if it fails to meet standards set by a regulatory body.
- Customer satisfaction: Satisfied customers are more likely to remain loyal to your business. Quality control can ensure customers get products that meet or exceed their expectations.
- Staying ahead of the competition: The problem of substandard products is, unfortunately, common. Good quality control can give you a competitive edge when other manufacturers are disappointing customers.
- Continuous improvement: Being able to offer your customers a better product today than you did yesterday can keep your business going for a long time. Quality control coupled with data analysis can help you identify areas where processes can be improved or costs cut.
- Quality is a brand: For companies that consistently deliver high-quality products, this becomes part of their brand image. This consistency requires excellent quality control but the benefit is that it can attract new customers and justify price increases depending on market conditions.
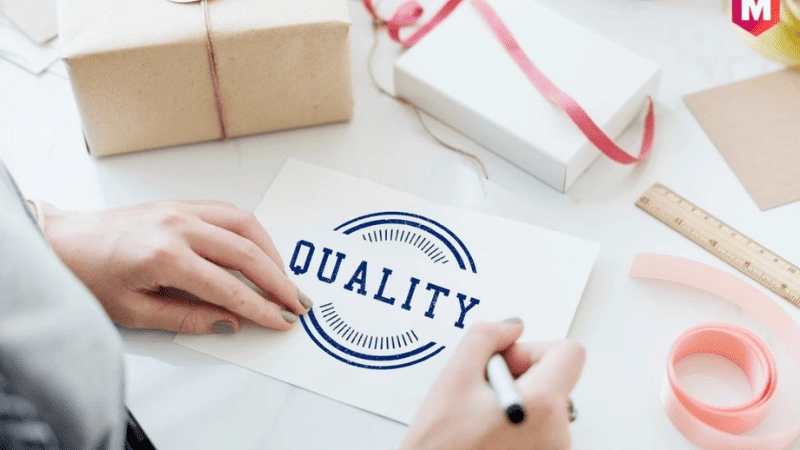
In injection molding, effective quality control involves multiple steps and calls on the skills and expertise of different people and groups in different departments.
Send your inquiry for prompt quotations!
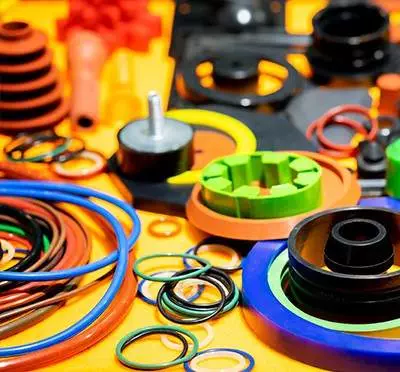
Here are 6 ways to control the quality of injection molding:
Communication and Collaboration
Good communication and collaboration may seem basic, but they are the backbone of good quality control in injection molding. It ensures that expectations and challenges are communicated between different parties and that everyone works towards the same goals.
Pre-Production Communication and Collaboration
Proper communication is important in the initial stages of injection molding because it helps to establish:
- The needs of the customer
- The specifications of the item(s) to be molded
- The standards that are to be used to determine if a product is acceptable
Additionally, the manufacturer also needs to properly communicate their capabilities and limitations. Not every manufacturer will have injection molding machines that can produce the parts that you want.
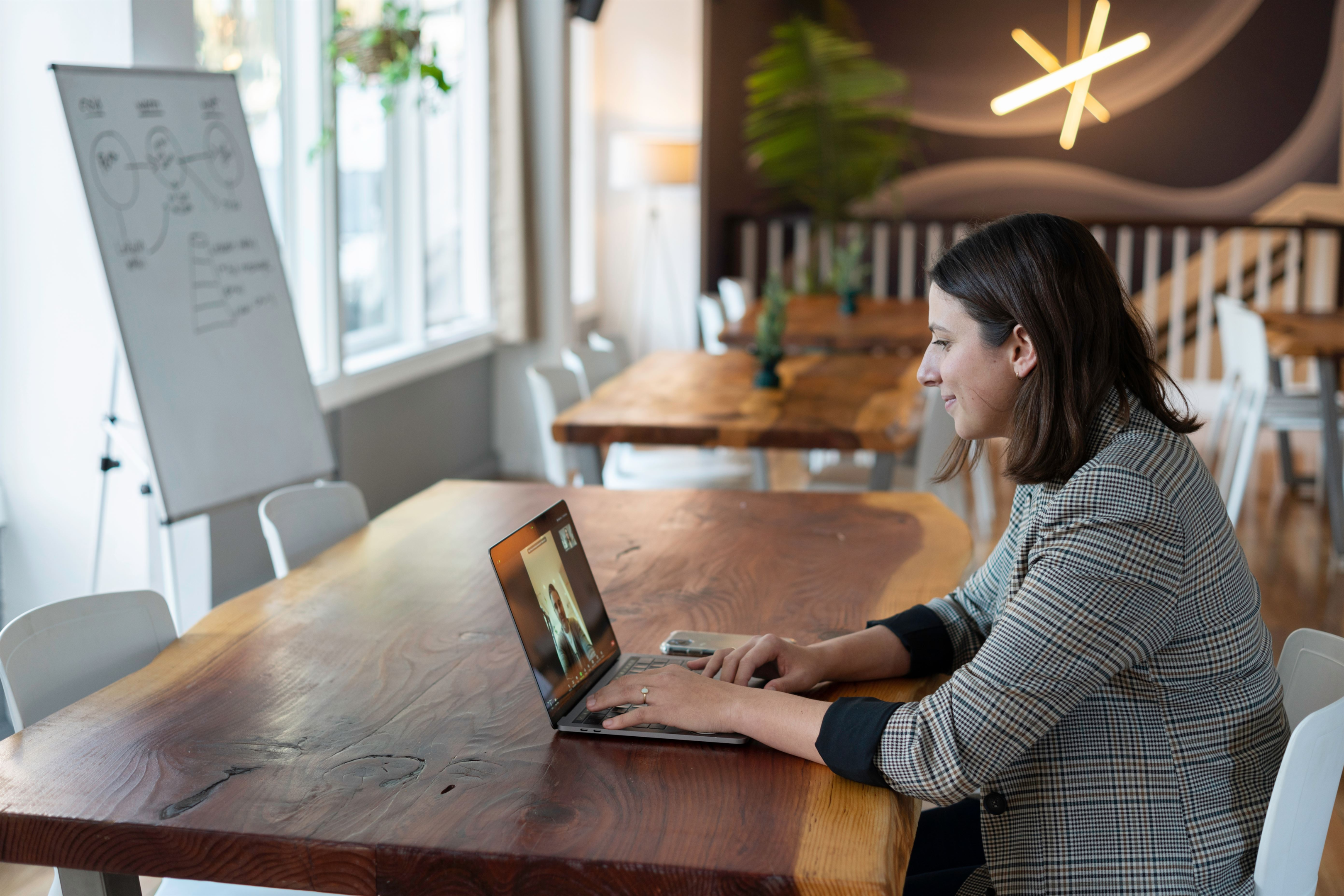
This early communication helps both parties to know if their collaboration is a good fit. This helps to avoid costly disappointments down the road.
In-Production Communication
Communication and collaboration are also important for quality control once manufacturing has kicked off. Certain issues will not become evident until the process has started. It’s also possible that the result may not be what the client assumed it would be.
There could also be issues with the design that make the product harder to produce than expected, or the manufacturer’s equipment may not be able to achieve the accuracy or precision needed for some specific detail.
Having open lines of communication ensures the existence of such challenges are communicated promptly. The client and manufacturer can work collaboratively to identify viable solutions early before thousands of parts have been made.
Post-Production Communication
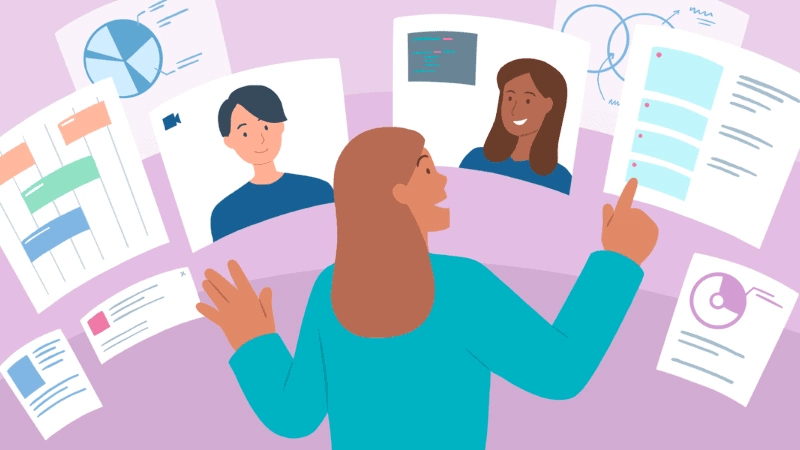
Communication at the end of the project also helps with quality control for future projects. A successful part may have multiple production runs, or the client may need a similar product in the future.
Getting feedback from the client allows the manufacturer to know what they can improve on. The manufacturer can also use the opportunity to communicate their ideas on how they can produce parts more efficiently in the future based on their experience with this project.
There are many accepted forms of communication today including:
- Phone calls
- Instant messages
- emails
- Traditional mail
- Voice messages
- Video calls, etc.
Regardless of the method of communication, the issues discussed must be documented or followed up with written communication. This ensures there is a record of what was discussed and when it was discussed.
Send your inquiry for prompt quotations!
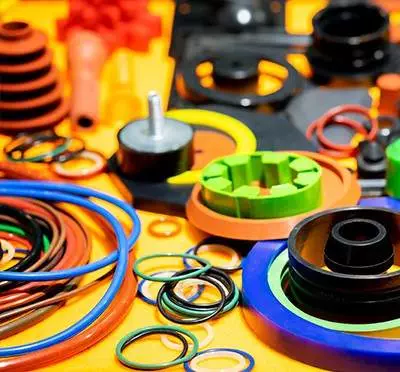
Design with Manufacturing in Mind
Redesigning a product after manufacturing has started is a costly process. This might happen if the initial part design is incompatible with the production process.
The best way to avoid this is to design the part with the manufacturing process, i.e., injection molding, in mind. An injection molding design analysis during the design stage can help with this. It can identify which parts or features are likely to yield poor results or make the injection molding process inefficient.
When you design parts for injection molding, some of the corrections that can be made to improve manufacturability include:
- Optimizing wall thickness
- Choosing the best locations for gates
- Choosing the best locations for ejector pins
- Introducing drafts in features that need them
In-Process Inspection and Controls
Inspecting samples at the end of a production run can ensure the next batch is better, but inspecting the products and the process parameters during the production cycle can stop a bad batch from being manufactured.
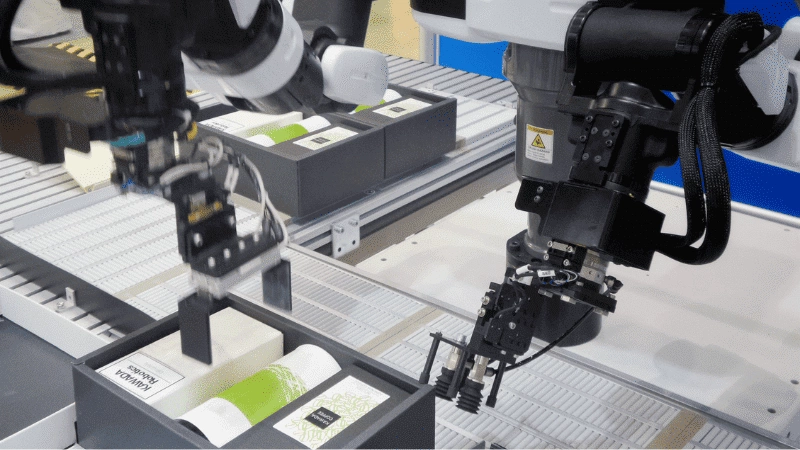
In-process inspection can be achieved by identifying critical features that must meet standards such as:
- Flatness
- Parallelism
- Color
- Straightness, etc.
There is state-of-the-art equipment that can be used to check these and other features automatically with no human intervention. Many inspection methods add very little time to the plastic injection molding cycle.
If some feature isn’t up to standard, in-process controls can be used to make adjustments to change this, or the production run can be stopped until the cause of the problem is identified.
Implement Inspection Methods
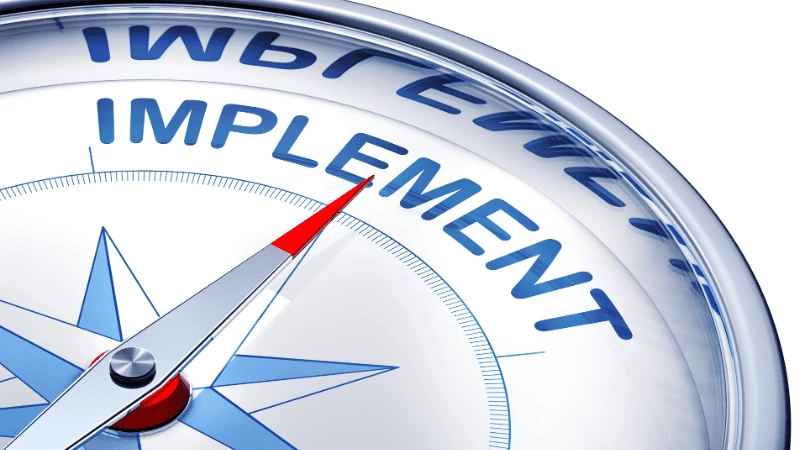
Having inspection methods and implementing them are not the same thing. A manufacturer may have a long list of inspection methods that they can use for an injection molded part but this doesn’t mean they will always use them.
Inspection of a part during production can be more expensive and result in a slightly longer cycle time. Additionally, it may turn out that implementing a specific inspection method is more challenging than initially thought due to process dynamics or product features.
It is, however, important to remember that the benefits of implementing inspection methods far outweigh the benefits of skirting them. The time and costs saved by not implementing inspection methods might be significantly less than the losses suffered if customers are unhappy with the product or if more products fail the standards test at the end of production.
In this regard, it’s also important to know what inspection methods can be realistically implemented and communicate this to the client, rather than overpromising.
Send your inquiry for prompt quotations!
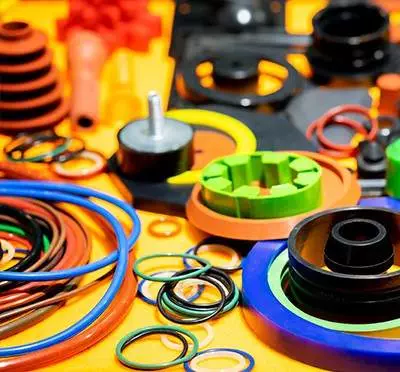
Address Specific Manufacturing Problems
Even with a good part and tooling design, the manufacturing process doesn’t always go according to plan. Certain issues are harder to predict and they may cause molding defects. These issues include:
- Incorrect injection pressure and speed
- Inconsistent material flow within the mold
- Temperature differences throughout the mold
- Poor flow of material through gates
- Insufficient venting of gases
- Incorrect use of mold release agents
- Insufficient cooling times, etc.

Process monitoring systems can let you know if some of these issues exist. However, you can also tell by looking for sink marks and other defects in the earliest molded parts.
Some of the common defects that will let you know there is a manufacturing problem to be addressed include:
- Cracking of molded parts
- Underfilled molds, i.e. short shots
- Excess sticking of parts in the mold cavity
- Flush or overflow of material
- Warping, etc.
It can be challenging to identify which exact manufacturing problem gives rise to an issue in the product.
For example, the warping of parts can be due to different rates of cooling in the molded part, excessive injection pressure, inconsistencies in the mold temperature, or incorrect material choice. Luckily, there are handy guides that can tell you which specific issues are likely to cause some defects.
Manufacturing problems may not always result in parts not meeting the set standards, but they can make it harder and more expensive. They can cause a lot of waste and slow down the cycle times.
Continuous Improvement
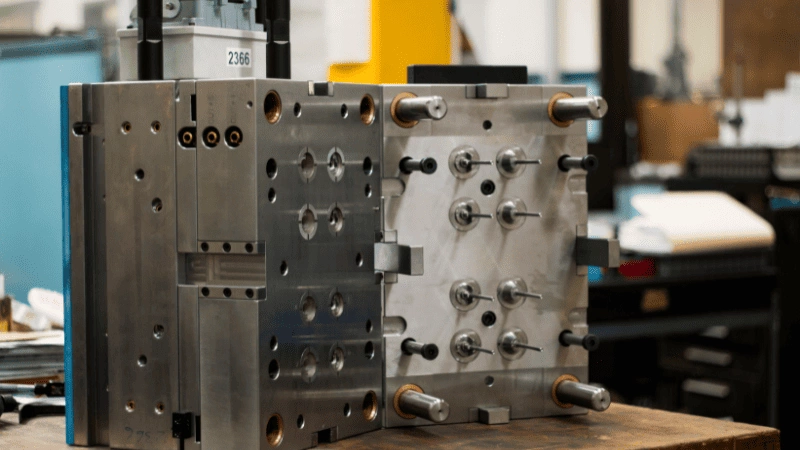
One of the best ways of ensuring quality control is maintained in injection molding is to make continuous improvements a culture.
It is common for manufacturers to implement quality control measures that make their products just good enough. Unfortunately, standards and consumer expectations change especially when the competition can make similar injection molded parts at a lower cost or higher quality.
Continuous improvement enables you to stay ahead of the competition and it can be achieved in a few ways.
Reviewing and Refining Existing Processes
The best place to start improvement is where you currently are. When you’ve had quality control measures in place for a while, you’ll have a good idea of what measures have prevented the most defects and which ones can be considered redundant or inadequate.
Reviewing your existing system will tell you how the entire quality control process itself can be made more efficient so you can guarantee the same or better quality while using fewer machines, tools, or personnel.
Adapting New Technologies
The use of new technology can allow you to improve the speed and accuracy of your quality control system for injection molding.
Equipment used for in-process inspection, for example, has been improving. It is now possible to check parameters such as wall thickness, shapes, flatness, and colors of manufactured parts much faster and with greater accuracy thanks to new technologies.
The rapid rise of machine learning and AI is also improving the speed and accuracy of manufacturing processes. Computer vision makes it easier to quickly inspect parts for defects and can also be used to measure surface characteristics.
Learning from Past Mistakes and Client Feedback
Another easy way to know which improvements you need to make is by examining areas or situations where mistakes were made or getting feedback from clients who used your injection molded parts.
By examining past mistakes, you can improve your quality control system to ensure the same mistakes won’t happen again in the future. Feedback from clients, even after successful part production, can give the manufacturer good ideas on what can be improved about their existing processes.
Send your inquiry for prompt quotations!
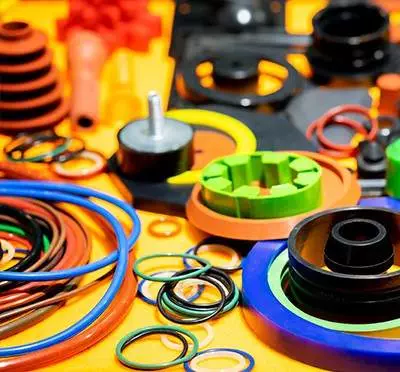
Conclusion
The expectations of both consumers and industry regulators make quality control a necessity for any injection molding company that wishes to remain competitive and avoid penalties.
Some may view quality control as an unnecessary and expensive hassle, but when properly implemented, these measures can prevent you from running into more expensive roadblocks.
There are many different ways to approach quality control ranging from communication and proper design to in-process inspections and a culture of continuous improvement.
How Does Hongju Approach Quality Control for Your Products?
When you need injection molding services, it’s important to know how your company of choice will handle quality control. This will ensure that you’ll spend less time shipping back defective products and allow you to focus on delivering what your customers need. The injection molding experts at Hongju can discuss their quality control methods with you and let you know how they enable them to deliver better products with fewer defects.