A keypad-based machine interface works best when each key is clearly labeled. Therefore, the labels should be easy to read, accurate, and resistant to moisture or scratches. Below are the top 3 methods for labeling molded rubber keypads.
Screen Printing
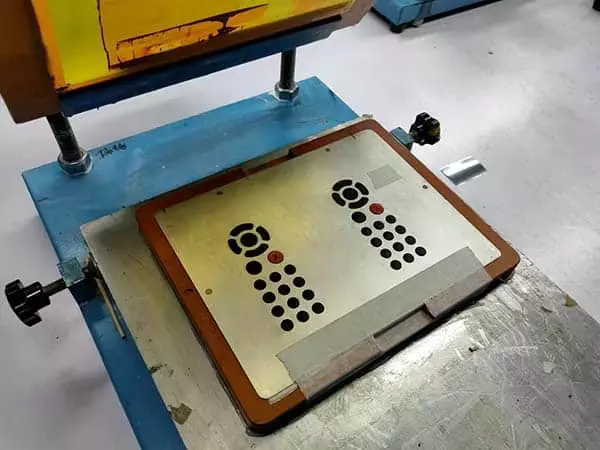
Screen printing, or serigraphy, is one of the world’s oldest technologies for silk-screening letters and images. It is an excellent method for printing letters and graphics on consumer and industrial products.
Screen printing of rubber keypads is cost-effective compared to other methods, making it one of the most popular options for labeling silicone rubber keypads.
A screen mesh or fabric is tightly stretched onto a rectangular or square frame. The screen mesh may be polyester, cotton, organdy, nylon, or silk. A stencil is used only to expose keytops and block the rest of the rubber keypad. The stencil design depends on the layout of the silicone rubber keypad.
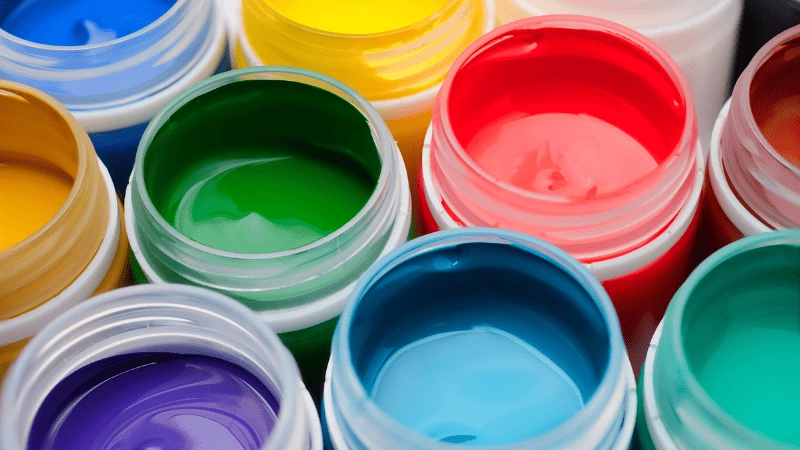
A squeegee is used to push and spread the ink through the silicone rubber keypad when ink is deposited onto the screen and the frame assembly.
Silicone-based ink delivers long-lasting results when labeling keys on silicone custom rubber keypads. However, non-silicone-based ink can also be used for silk screening. However, the quality of the print may not be good enough for high-traffic silicone rubber keypads. The letters may fade and peel depending on the actuation force of each key.
The manufacturer can use an epoxy coating to prevent the labeling from fading to protect the silk-screened keys. An epoxy coating gives the keys a glossy appearance and a hard plastic feel.
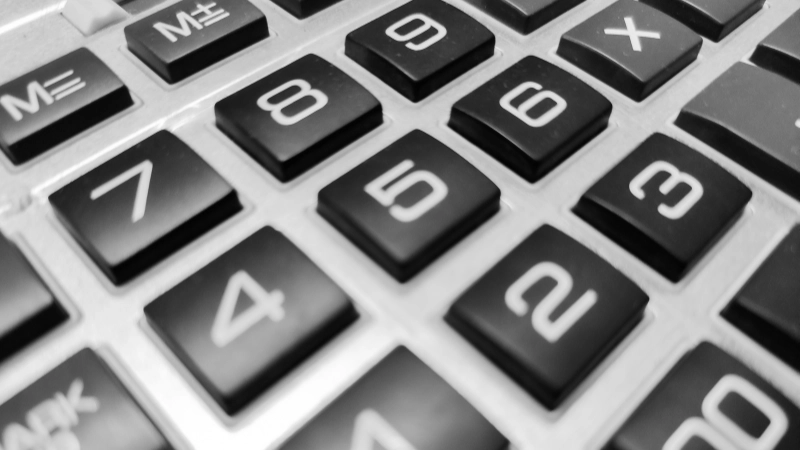
Here’s a quick overview of the main pros and cons of screen printing for rubber keypad labeling:
Pros | Cons |
Suitable for industrial and consumer products | Non-silicone-based ink may fade quickly |
It can be used on membrane switches | Multicolor printing may be labor-intensive and time-consuming |
Suitable for both silicone and non-silicone-based inks | |
Produces an excellent printing effect on silicone keypads | |
An excellent method for printing remote controls |
Laser Marking
The popularity of laser marking and laser cutting is increasing in manufacturing elastomeric keypads.
Laser marking, also called laser etching, is a unique process of labeling silicone rubber keypads using a high-powered laser. This method works by generating contrast in materials to convey information. It is the ideal method to use for backlit rubber keypads.
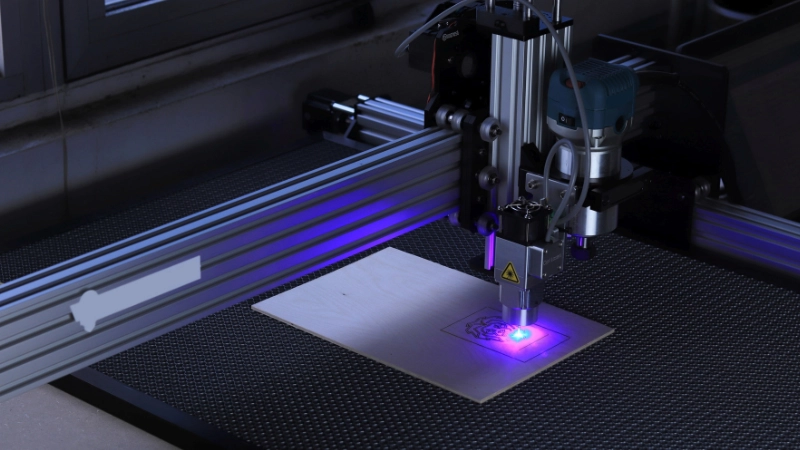
Usually, most custom rubber keypads are labeled using screen printing because it is cost-effective and easy for mass production. Laser marking is a newer and more advanced labeling technique that can be used in industries ranging from keypads to food equipment.
This labeling method is easiest to use on custom keypads with backlighting features. Unlike silk screening, laser marking takes place entirely without contact. While the exact labeling process varies from manufacturer to manufacturer, the technology removes the black coating on the upper layer of a rubber keypad.
A rubber keypad manufacturer can use two laser marking techniques for labeling: galvanometer and flatbed lasers.
In the first method, direct writing is done by steering a laser beam with galvanometer-driven mirrors. This technique continuously marks vector-style characters and texts very fast.
The marking is usually smooth and relatively quick. On the other hand, flatbed lasers use a lens equipped with a fixed mirror to effectively direct the beam on the keytop of a rubber keypad.
Silk screening may be cheaper. However, the simplicity of manufacturing laser-etched rubber keypads, the speed of application, and the permanence of the texts and characters have opened up a considerable appetite within the industry.
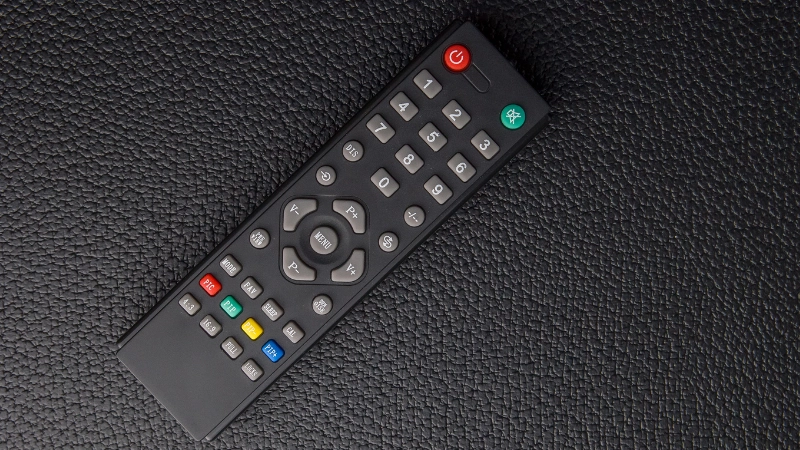
Pros | Cons |
Flexible in text and character design and application | Involves high investment costs |
Non-contact technology means no clamping | Thermal load is exerted on the rubber keypads |
Laser-etched rubber keypads are aesthetically appealing. | Requires a skilled operator for practical application |
The texts and characters don’t fade easily | |
It can be used to mark a membrane switch. |
Plastic Caps
Another trending method for labeling a custom rubber keypad is plastic caps. Rubber keypads labeled using this method are called Plastic + Silicone Rubber Keypads or P+R Keypads. This is one of the most expensive labeling solutions in manufacturing silicone rubber data input devices with backlighting effects.
A silicone rubber keypad with plastic caps offers several advantages, including superior aesthetic effects, improved oil, dust-proof surface, and increased wear resistance. The plastic caps are attached to the rubber keys using elastomeric sealing.
The most popular materials used in the production of plastic caps are PBT and ABS. PBT is generally preferred over ABS because it produces stiffer and more durable caps. A manufacturer of rubber keypads usually produces plastic caps through injection molding.
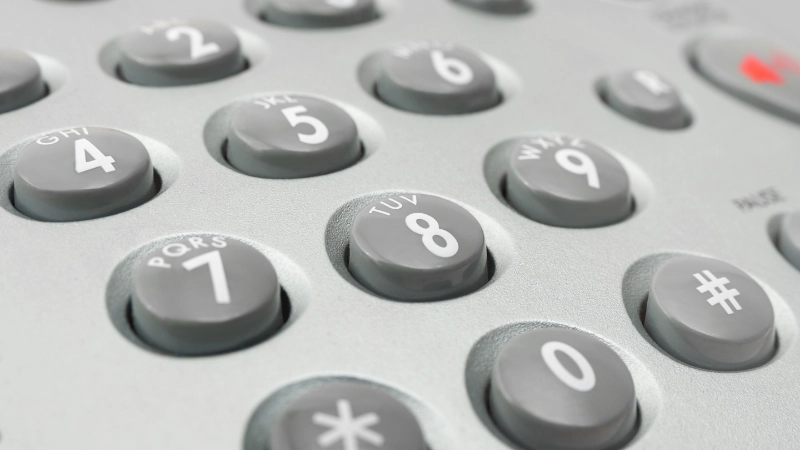
Once the plastic caps have been produced through injection molding, they can be laser-etched or silk-screened. The caps are then assembled on the silicone keypad with glue.
Pros | Cons |
Allows for pleasing aesthetic and backlighting effects | High tooling costs for injection molding, positioning toolings, and die-cutting tooling |
P+R keypads have an incredibly long lifespan, making them great for high-traffic applications | Not the most economical option for low-quantity P+R keypad production |
Produce a highly versatile and user-friendly interface | Processing and assembling the plastic caps may need a lot of labor |
Plastic caps can be labeled with different methods, allowing for superior customization |
Take the First Step:
Requst for an Inquire
Quality Meets Affordability. Inquire Now for High-Quality Products at Low Volumes.
Tips on Choosing the Proper Labeling Method for Your Keypads
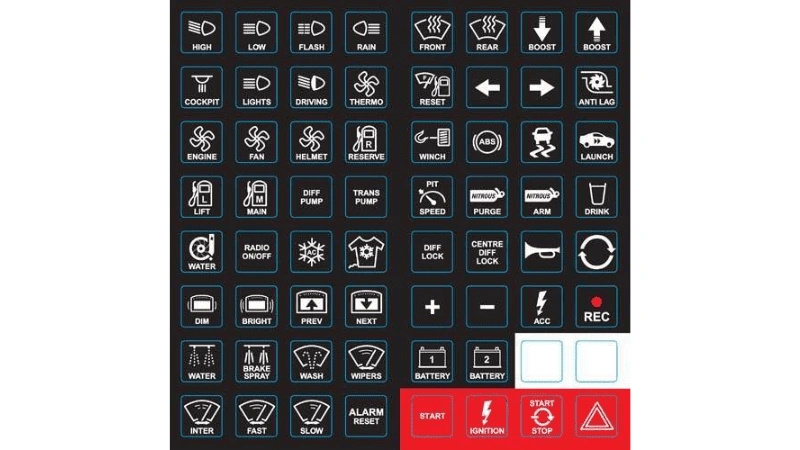
As you have seen, all the popular rubber keypad labeling options have certain downsides. This means you’ve got to consider a few things when selecting a labeling method. Here are a few tips to help with the selection:
Cost-Effectiveness & Labor
A keypad-based human-machine interface must have accurate labeling to properly operate a computer or electronic device. However, the manufacturer must also consider the costs of the labeling process. This can include the cost of materials, the cost of tools, and labor costs.
The most economical method that is used by most industries is silk screening. However, a manufacturer with a higher budget could consider the more advanced options for better quality and durability.
Keypad Design & Aesthetics
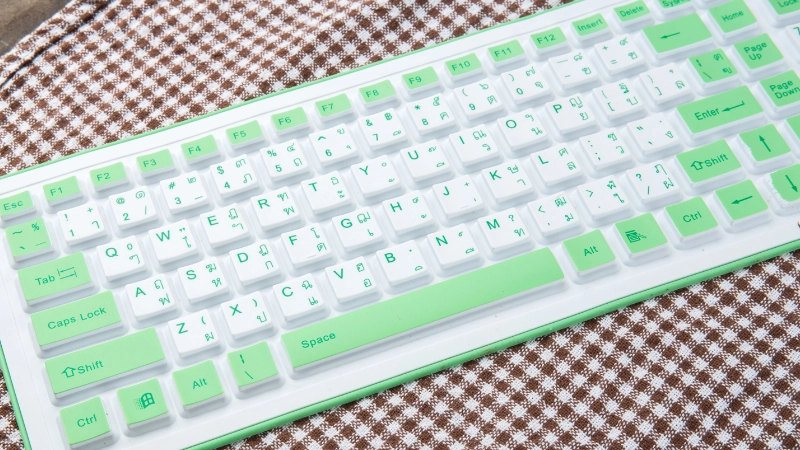
The keypad’s design also matters, including membrane switches and metal domes.
Membrane keypads have an electrical contact on the underside that connects with the board when a key is pressed. A membrane keypad uses a metal dome to provide a tactile feel. The ideal labeling option for this keypad design would be silk screening.
On the other hand, metal dome keypads have a metal dome and two circuits. Metal domes have an excellent snap ratio when pressed for better tactility. All the labeling methods above would be ideal for a metal dome design.
Some industrial or consumer applications may call for backlighting. In this case, laser marking would be the most preferred labeling technique. However, laser marking can be integrated with silk screening to introduce back-lighting effects into silicone keypads.
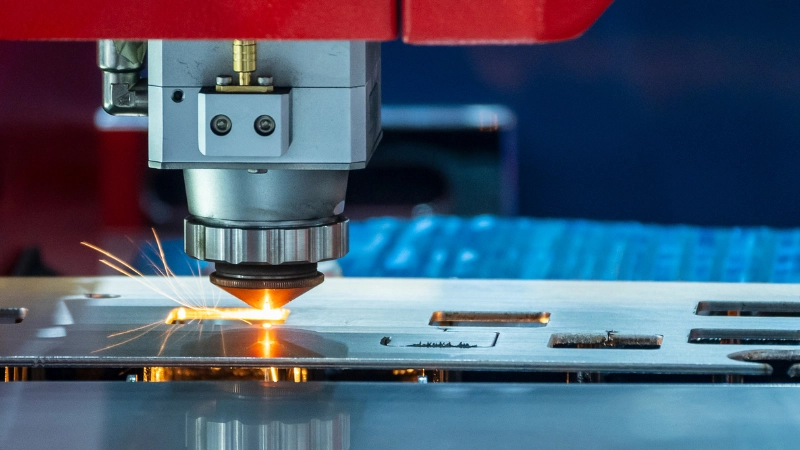
For customization of colors and aesthetics, a manufacturer can consider plastic caps. But silk screening can still be used with color customization.
The Durability of the Labeling Method
As we mentioned earlier, the importance of keypad labeling is to identify the function of each key. So, choose a method that will be a good fit for the application.
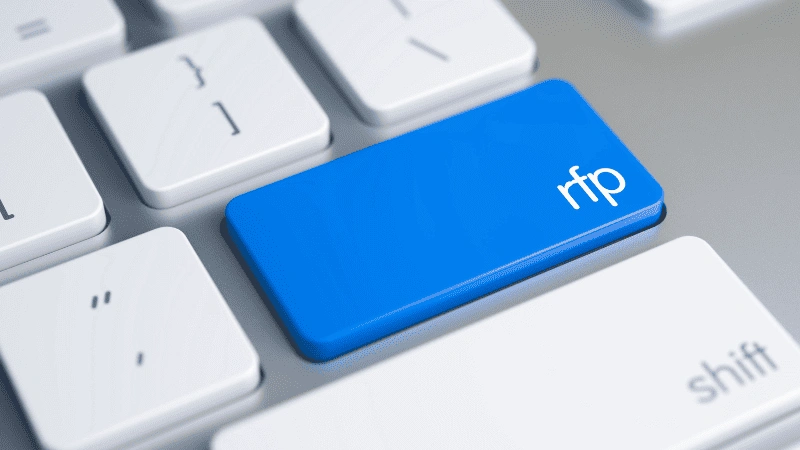
Silk screening or silk screen printing is the cheapest, but it is usually criticized for its low durability. Silk-screened keys are known to be susceptible to scratching.
Therefore, this labeling method may not be the most convenient option for high-traffic applications. Laser-etched keys, however, don’t fade quickly and can withstand repeated use.
Plastic caps are also ideal for high-traffic applications, but it depends on the labeling method used on the lids.
For medical applications, the labeling method needs to have good chemical resistance. This is so because medical settings usually use chemicals to clean surfaces. Some labeling solutions can be covered with epoxy coating to make them chemical-resistant.
The following table provides a clear comparison of the three keypad printing methods across different dimensions:
Method | Cost | Durability | Aesthetic Appeal | Backlighting |
Screen Printing | Low | Low to Medium | High | Not suitable |
Laser Marking | High (Initial Investment) | Very High | Medium to High | Excellent |
Plastic Caps | Very High | Very High | Excellent | Excellent |
Take the First Step:
Requst for an Inquire
Quality Meets Affordability. Inquire Now for High-Quality Products at Low Volumes.
Conclusion
Durable, clear labeling ensures keypad longevity and user efficiency. The top 3 methods are screen printing, laser etching, and plastic caps. They can balance cost, aesthetics, and resilience for industrial, medical, or high-traffic applications. Choose wisely based on your specific needs to enhance functionality and value.
Get Durable Silicone Keypads from Hongju: Precision-Built for Your Exact Needs!
With more than 20 years of design and production experience, Hongju Silicone delivers high-performance keypads with superior tactile response, environmental resistance, and extended lifespan. Our expertise ensures your design achieves a perfect balance between durability and value, optimizing your cost-efficiency.
Contact us now to get a free design consultation and quote!
FAQs
Q1: Which labeling method is the most cost-effective?
Screen printing is the most cost-effective method and is widely used for mass production to save more cost.
Q2: Which method offers the highest durability for high-traffic applications?
Both laser marking and plastic caps are ideal for high-traffic applications. Laser-etched legends do not fade quickly and can withstand repeated use, while plastic caps also have an incredibly long lifespan.
Q3: Can I combine different labeling methods?
Yes, a hybrid approach is possible. For example, some manufacturers use a combination of screen printing and laser etching to achieve both colorful designs and backlighting effects.
Q4: How long will your prototyping take?
Hongju Silicone‘s prototyping can be ready within 3-5 work days with CNC machining.
Q5: What’s your MOQ?
We can produce flexible quantities of keypads according to your needs.