Delving into the unique characteristics of liquid, solid, and room-temperature vulcanized silicone rubbers, we highlight their mechanical properties, resistance to extreme temperatures, and electrical insulation capabilities.
We explore the versatility of silicone rubbers in injection molding and their applications, highlighting the importance of choosing the appropriate type for optimal performance.
So, let’s dive into the world of silicone rubbers, uncovering the nuances that make each type distinct and invaluable in their respective fields.
What is Silicone?
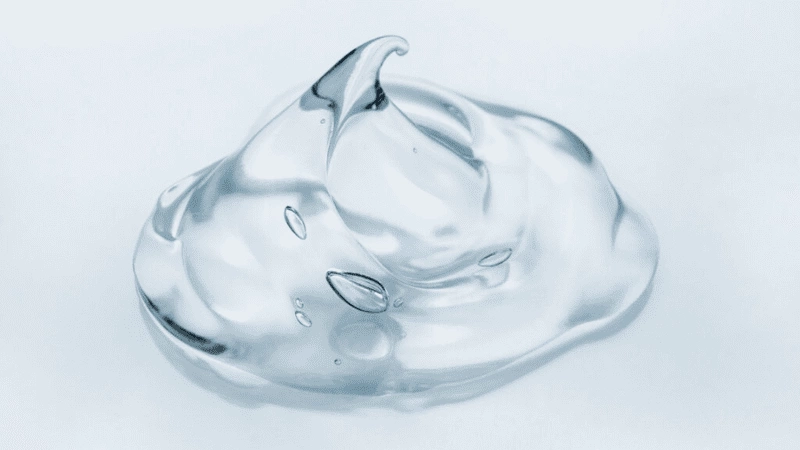
Silicone, a versatile material derived from inorganic silicon, stands out for its unique combination of chemical and physical properties.
This synthetic elastomer is celebrated for its heat resistance, excellent electrical insulation properties, and durability across a wide temperature range, making it indispensable in various applications, from medical devices to automotive seals.
Send your inquiry for prompt quotations!
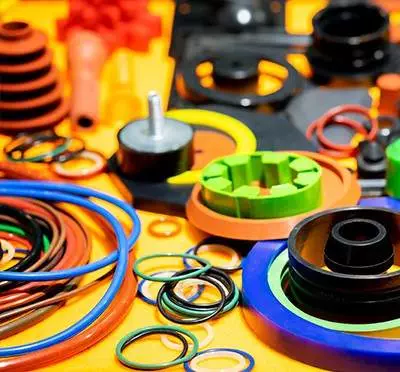
4 Types of Silicone and Their Distinctions
There is a spectrum of types of silicone rubber, each designed for specific uses and functionalities.
The distinctions among these different types of silicone rubber hinge on their mechanical properties, curing processes, and molecular structure, which make silicone rubbers so adaptable.
Type 1: Liquid Silicone Rubber
Liquid Silicone Rubber (LSR) is a high-purity thermoset elastomer that boasts a range of beneficial properties due to its unique molecular structure.
This versatile material is distinguished by its ease of processing through liquid injection molding, making it a preferred choice for a multitude of applications.
Properties:
- Temperature Resistance: Liquid silicone rubber maintains its integrity in extreme temperatures, from very low to high temperatures, showcasing remarkable heat resistance and stability.
- Mechanical Properties: It exhibits excellent mechanical properties, including flexibility and elasticity, due to its long polymer chains and elastomeric nature.
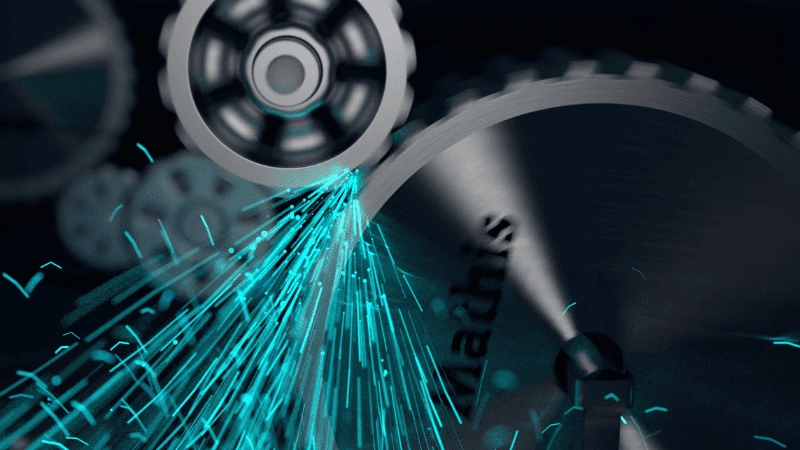
- Electrical barrier: With its inherent electrical insulation properties, LSR is ideal for electronic applications requiring dielectric strength.
- Chemical Resistance: Resistant to a variety of chemicals, oils, and water, LSR’s chemically resistant nature makes it suitable for harsh environments.
- Biocompatibility: Often used in medical devices, Liquid silicone rubber is biocompatible, making it safe for applications involving human contact.
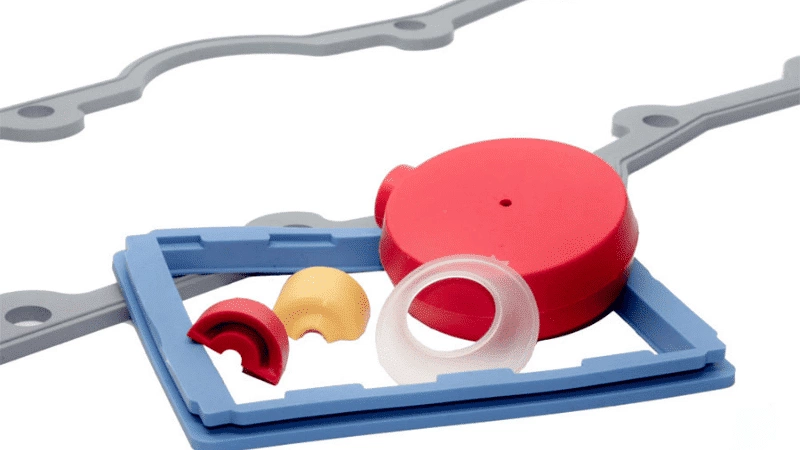
Applications:
- Medical Devices: Due to its biocompatibility and sterilizability, LSR is extensively used in medical applications, from surgical tools to implants.
- Automotive Components: Its durability and resistance to temperature fluctuations make it ideal for automotive seals, gaskets, and hoses.
- Consumer Goods: LSR’s flexibility and safety are leveraged in consumer products such as silicone rubber band bracelets, kitchenware, and waterproof watches.
- Electronics: Its excellent electrical insulation properties make it suitable for insulating wires, seals, and protective cases.
Liquid silicone rubber’s role in modern manufacturing and product design is highlighted by its adaptability and performance across a wide temperature range, resilience in challenging environments, and compliance with stringent safety and hygiene regulations, particularly in medical and food-grade applications.
This makes LSR a foundational material in the development of products designed for durability, safety, and high performance.
Type 2: High Consistency or Solid Silicone Rubber
High-consistency silicone rubber (HCR), commonly known as solid silicone rubber, is a high molecular weight silicone material that embodies the robustness of traditional organic rubbers with the advanced properties of silicone.
This high-performance elastomer undergoes a high-temperature vulcanized process, making it indispensable in applications exposed to high temperatures and demanding environments.
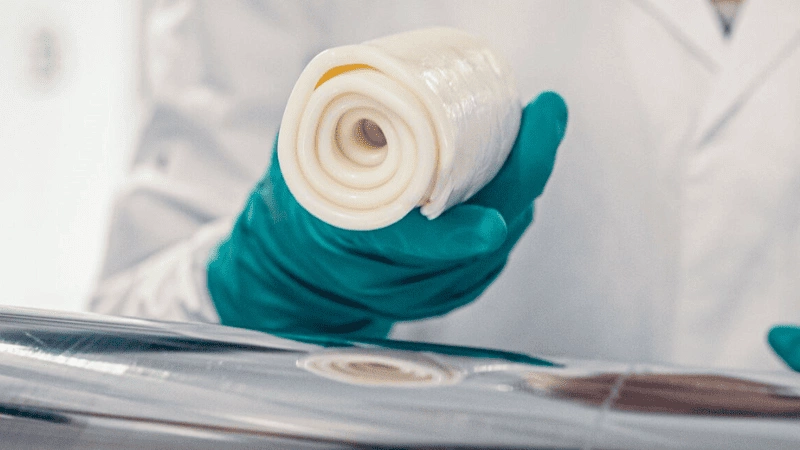
Properties:
- Heat Resistance: HCR’s heat resistance is exceptional, thanks to its high-temperature vulcanization, allowing it to maintain integrity under extreme temperatures.
- Mechanical Durability: The physical and mechanical properties of HCR, characterized by its long polymer chains and high molecular weight, offer superior tensile strength and longevity.
- Chemical Stability: Solid silicone rubber is inherently chemically resistant and weather resistant, benefiting from the pure silicone rubber matrix that includes methyl and vinyl groups, alongside silicone oil and silicone grease, enhancing its utility in harsh conditions.
- Versatility and Adaptability: The versatility of HCR is underscored by its ability to be compounded with various additives, such as more silicone oil and silicone grease, to tailor its properties for specific applications, from increased elasticity to enhanced chemical resistance.
Applications:
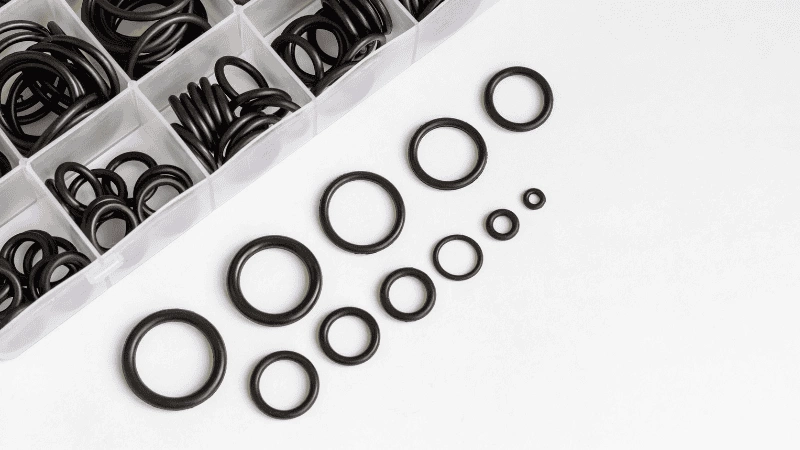
- Sealing and Gasket Solutions: In the automotive and aerospace sectors, HCR’s high-temperature resistance and mechanical strength make it ideal for gaskets, seals, and hoses.
- Consumer Products: The safety, durability, and heat resistance of solid silicone rubber are leveraged in consumer goods like kitchenware and silicone rubber band bracelets, ensuring both functionality and consumer safety.
- Medical Devices: The biocompatibility and sterilization compatibility of HCR make it a preferred material for medical applications, including tubing and various silicone rubber products used in healthcare settings.
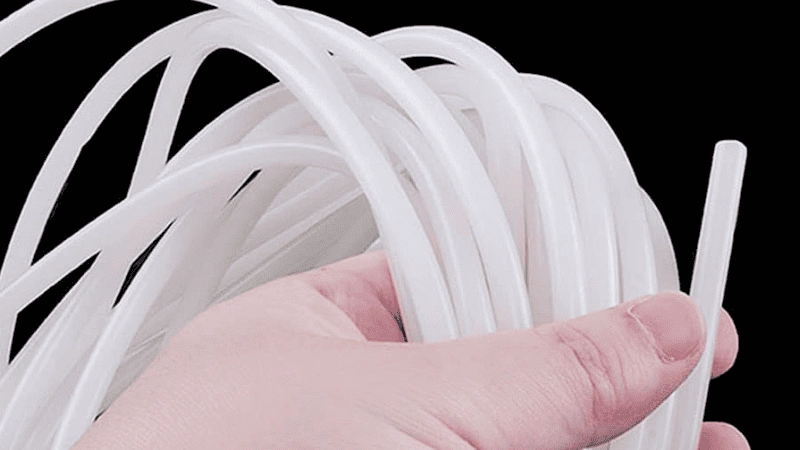
Solid silicone rubber’s contribution to industries requiring materials that withstand high temperatures and harsh conditions is significant.
HCR’s combination of high-temperature vulcanized properties, along with its mechanical durability and chemical stability, makes it a material of choice for a wide range of applications.
The capacity to reuse silicone rubber products and the recyclability of silicone rubbers highlight HCR’s alignment with environmental sustainability efforts.
Furthermore, the inclusion of silicone oil and silicone grease in HCR formulations enhances its performance, making it a versatile and indispensable material in the manufacturing of durable, high-quality silicone rubber products.
Type 3: Room Temperature Vulcanized (RTV) Silicone
Room Temperature Vulcanized (RTV) silicone is a type of silicone rubber that cures at room temperature, making it highly versatile for a wide range of applications.
Unlike high-temperature vulcanized silicone rubbers, RTV silicone does not require heat to initiate the curing process, allowing it to be used in situations where heating is impractical.
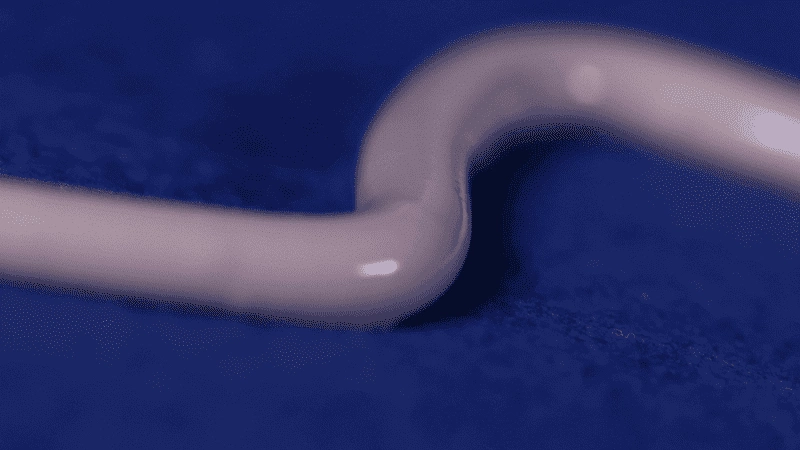
Properties:
- Ease of Use: RTV silicone can be applied and cured at room temperature, offering convenience and efficiency in sealing and molding applications.
- Flexibility and Durability: Once cured, RTV silicone exhibits excellent flexibility and durability, withstanding various environmental conditions without degradation.
- Chemical Resistance: This type of silicone rubber is chemically resistant to many substances, making it ideal for applications requiring long-term exposure to harsh chemicals.
- Thermal Stability: RTV silicone maintains its physical properties across a wide range of temperatures, from low temperatures to moderately high temperatures, ensuring reliability in diverse environments.
Applications:
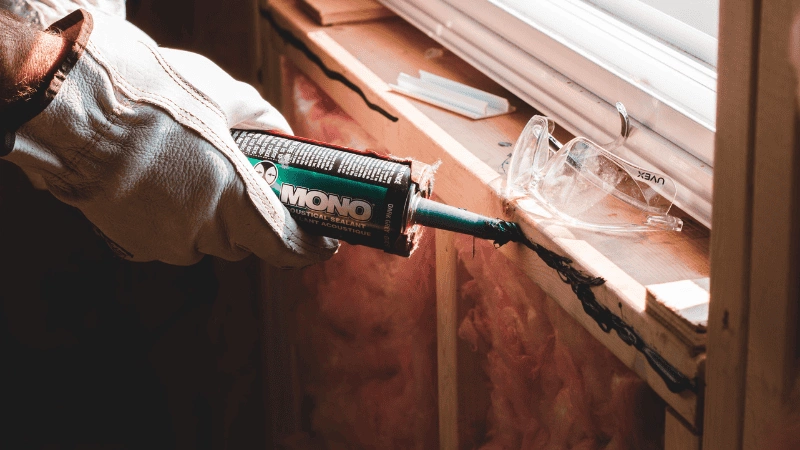
- Sealants and Adhesives: RTV silicone is widely used as a sealant and adhesive in construction, automotive, and electronics for its strong bonding capabilities and weather-resistant properties.
- Molding and Casting: Its ease of use and detailed reproduction make RTV silicone a preferred material for molds and casts in the arts, crafts, and prototyping industries.
- Gaskets and Insulation: In electronics and automotive applications, RTV silicone serves as an effective gasket material and insulator, thanks to its thermal stability and electrical insulation properties.
RTV silicone’s adaptability and ease of use make it a staple in both industrial and creative fields. Its ability to cure without additional heat sources simplifies processes where controlled heating is not feasible, broadening the scope of projects and applications.

The environmental resilience and robust physical properties of RTV silicone, combined with its straightforward application, underscore its utility as a solid silicone rubber for a multitude of sealing, bonding, and molding tasks.
Utilizing silicone oil and silicone grease, RTV silicone can be modified to enhance certain properties, such as elasticity or lubrication, further extending its application range.
The recyclability and potential for reusing silicone rubber products contribute to the environmental sustainability of RTV silicone, aligning with green manufacturing practices and waste reduction efforts.
Whether used in its pure form or modified with additives like methyl silicone rubber or platinum-cured silicone, RTV silicone remains an essential material in industries ranging from automotive to electronics, offering high performance and reliability.
Type 4: Fluorosilicone
Fluorosilicone combines the desirable characteristics of basic silicone rubbers with enhanced chemical resistance, attributable to fluorine integration into its molecular structure.
This makes it a standout in applications demanding resistance to aggressive chemicals, oils, and solvents.
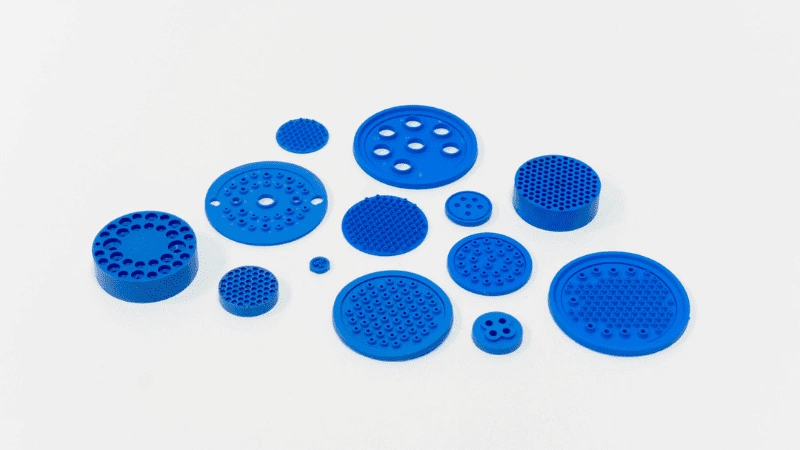
Properties:
- Chemical Resistance: Exceptional against harsh chemicals, oil resistant.
- Temperature Stability: Maintains properties across extreme temperatures.
- Durability: Robust molecular structure with relatively long polymer chains.
- Versatility: Usable in both liquid and solid silicone rubber forms for diverse silicone rubber products.
Applications:
- Aerospace and Automotive: Ideal for seals and gaskets due to oil resistance.
- Industrial Sealing: Used in chemical processing for its chemical resistance.
- Electronics: Serves as protective coatings, leveraging excellent resistance.
Fluorosilicone’s advanced resistance, combined with the inherent benefits of silicone rubbers, makes it invaluable in challenging environments. Its recyclability and status as uncontaminated silicone rubber align with sustainable practices, ensuring its role in high-performance elastomer applications.
With the use of platinum catalysts and peroxide cure systems in production, fluorosilicone ensures the creation of high-quality, durable silicone rubber products.
Send your inquiry for prompt quotations!
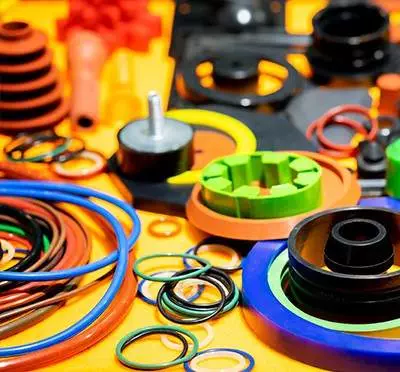
Comparison of 4 Types of Silicone
To grasp the distinct capabilities of each silicone variant, it’s essential to compare them side by side.
Below is a comparative analysis of Liquid Silicone Rubber (LSR), High Consistency Rubber (HCR), Room Temperature Vulcanized (RTV) Silicone, and Fluorosilicone, highlighting their properties and applications:
Feature | LSR | HCR | RTV | Fluorosilicone |
---|---|---|---|---|
Cure System | Platinum catalyzed cure system | Peroxide/Platinum catalyzed | Condensation cure system | Platinum catalyzed cure system |
Consistency | Liquid, heat curable elastomer | Solid, heat cured elastomer | Varies, room temperature vulcanization | Solid or liquid, heat curable elastomer |
Temperature Resistance | High temperatures | High temperatures | Moderate to high temperatures | High temperatures |
Chemical Resistance | Good, with excellent resistance | Good, with excellent resistance | Good, with excellent resistance | Excellent, with excellent resistance |
Primary Applications | Sealing applications, silicone products | Sealing applications, silicone products | Sealing applications, silicone products | Sealing applications, silicone products |
Mechanical Properties | Flexible, with relatively long polymer chains | Durable, with relatively long polymer chains | Flexible, varies with formulation | Durable, with relatively long polymer chains |
Raw Materials | Silicone polymers, methyl groups | Silicone polymers, methyl groups | Silicone polymers, methyl groups | Silicone polymers, methyl and phenyl groups |
This comparison reveals that each type of silicone is uniquely suited to specific needs based on its properties and potential applications.
LSR and HCR are both capable of high-temperature resistance and utilize platinum or peroxide cure systems, differing mainly in their physical state—LSR being liquid and HCR solid.
RTV silicone’s ability to cure at room temperature offers versatility in applications where heat curing is impractical.
Fluorosilicone distinguishes itself with superior chemical resistance, which makes it ideal for environments with exposure to harsh chemicals.
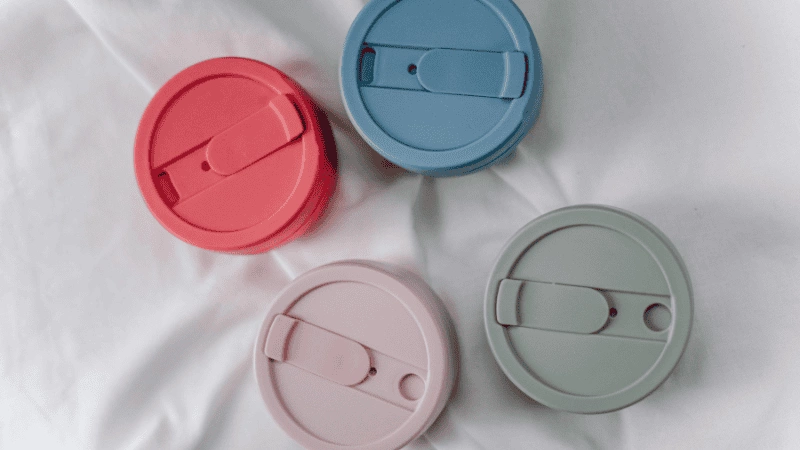
Selecting the appropriate silicone type hinges on the application’s specific demands, such as mechanical strength, flexibility, chemical resistance, or curing requirements.
The broad range of silicone products, from organic rubber-like materials to heat-cured elastomers and their sealing applications, demonstrates the material’s versatility.
The excellent resistance and use of platinum and peroxide cure systems across these types of silicone emphasize their integral role as raw materials in diverse manufacturing and design contexts, from natural rubber to advanced silicone sealants.
Choosing the Right Silicone
Selecting the right types of silicone for your project involves understanding the specific needs of your application and the properties of different silicone polymers.
Consider factors like temperature exposure, chemical resistance, and mechanical demands.
For example, if you need a durable, weather-resistant seal, a silicone sealant with a platinum catalyst might be ideal.
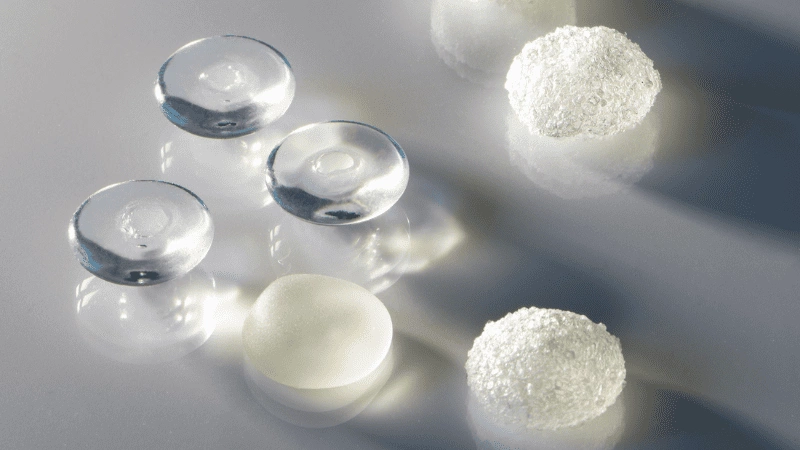
For applications requiring high flexibility and stretch, such as in medical devices, a heat-curable elastomer with long methyl groups, typical of natural rubber, could be more suitable.
Consulting with experts in silicone polymers can provide valuable insights, especially when considering the complexities of silicone materials, from their uncured form to the final rubber-like material.
Experts can guide you on whether a platinum-catalyzed cure system or a peroxide cure system is best for your application, taking into account the silicone’s chemical element composition and its behavior as a raw material.
Remember, the right silicone choice hinges on its compatibility with the organic groups involved in your project, ensuring optimal performance and durability.
Send your inquiry for prompt quotations!
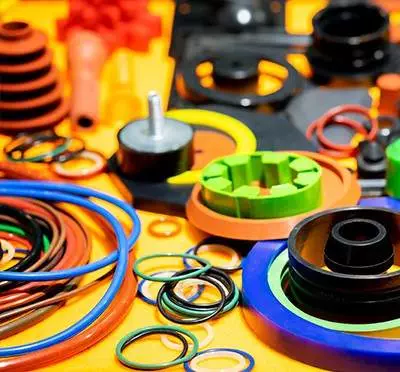
Conclusion
In conclusion, knowing the different types of silicone available Silicone Rubber (LSR), High Consistency Silicone Rubber (HCR), Room temperature vulcanization (RTV) silica gel, and fluoro silicone is crucial for making informed decisions in various industries.
Whether it’s choosing between silicone sealants for construction, heat-cured elastomers for automotive parts, or silicone polymers for medical devices, understanding the unique properties and applications of each silicone type is key.
Remember, the right types of silicone, be it an organic rubber variant or a specialized polymer, can significantly impact the performance and longevity of your products.
Discover the Perfect Solution for Your Business with Hongju
Are you ready to leverage the diverse applications and benefits of silicone for your upcoming endeavors? Consult with the experts at Hongju to navigate the complexities of silicone selection, ensuring your products achieve the highest standards of quality and performance.
Take the next step towards innovation. Access our comprehensive design guide. Visit our website for an extensive product catalog and more insightful blog posts.
contact us today and elvate your projects with Hongju’s advanced silicone solutions.