This article will shed light on why silicone seals have gained widespread acceptance in the food industry.
What are Silicone Rubber Seals?
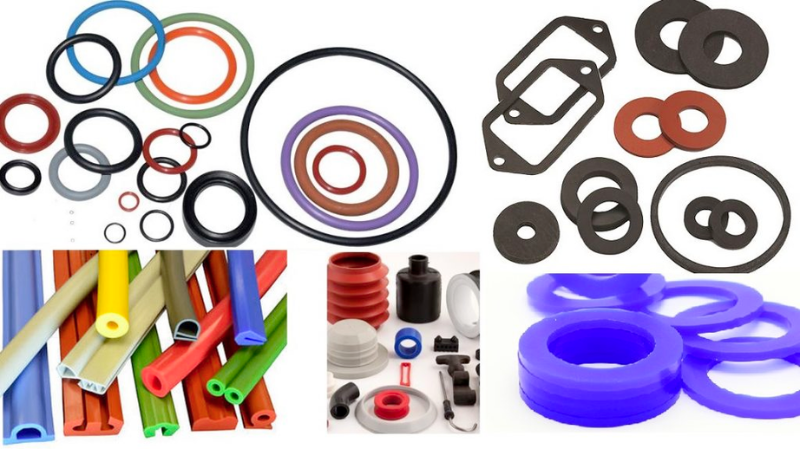
Before we delve into the application of silicone seals in the food industry, let’s explore the most basic knowledge of silicone seals.
Definition
Silicone rubber seals are devices that prevent the escape or entry of fluids (gas or liquid) between two mating surfaces. Silicone rubber is ideal for providing a watertight seal. They provide a barrier to stop leakage and serve as a buffer to dampen vibrations, making them essential in numerous industrial applications.
Properties
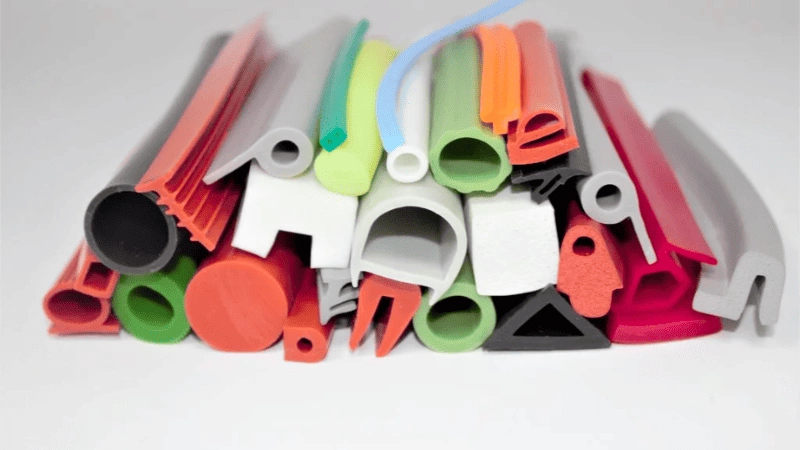
What makes silicone rubber seals stand out from others are their unique properties:
- Temperature Resistance: They have an impressive temperature resistance, capable of withstanding extreme temperatures, both low and high, ranging from -55°C to 232°C. This makes them perfect for use in food service equipment, where they may be subjected to various temperatures.
- Flexibility: Silicone rubber seals remain flexible even in extreme temperatures, thereby ensuring effective sealing under different conditions.
- Durability: These seals exhibit excellent resistance to ozone, UV light, and aging, ensuring a long lifespan and less frequent replacement.
- Chemical Resistance: They are resistant to many chemicals, oils, and water, making them suitable for food service equipment that might come into contact with various substances.
- Food-Grade Quality: Most importantly, for the food industry, silicone rubber is FDA approved. It is non-toxic and does not impact the taste or odor of food, making silicone seals ideal for food-related applications.
Now that we know what silicone rubber seals are and their inherent properties, let’s delve into why they are particularly useful in food service equipment.
What are the Benefits of Silicone Rubber Seals?
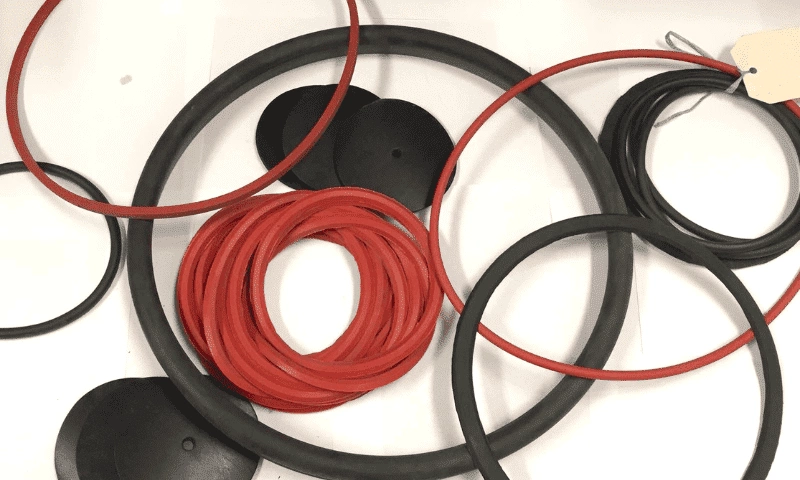
Silicone rubber gaskets are ideal for use in the food processing industry due to properties including the following;
Food-Grade
Silicone makes great FDA-approved gaskets and other various types of food-grade seals because it has a low compression set along with superior levels of flexibility and elongation. In the case of silicone rubber seals, FDA accreditation is critical because these seals come into direct contact with food or beverage products. For example, in a brewing machine, silicone seals ensure that the flavor of the beverages is not altered due to contact with the seal.
High-Temperature Resistance
Food service equipment work with high and low temperatures varying from cold to boiling. Silicone can withstand temperatures between -100 °C and 250 °C. Therefore, the material is suitable for high-heat applications. Food-grade silicone retains its integrity and shape, does not deform, and stays elastic in low and high temperatures.
Non-toxic and Environmentally Friendly
Food processing requires non-toxic materials to preserve human health. Silicone products meet FDA requirements and are suitable in the food, medical, and pharmaceutical industries because of their non-toxic properties.
Furthermore, the material is chemically stable and safe for contact with food and beverage. In addition, silicone is more recyclable and environmentally friendly than plastic.
Variety of Colors and Styles
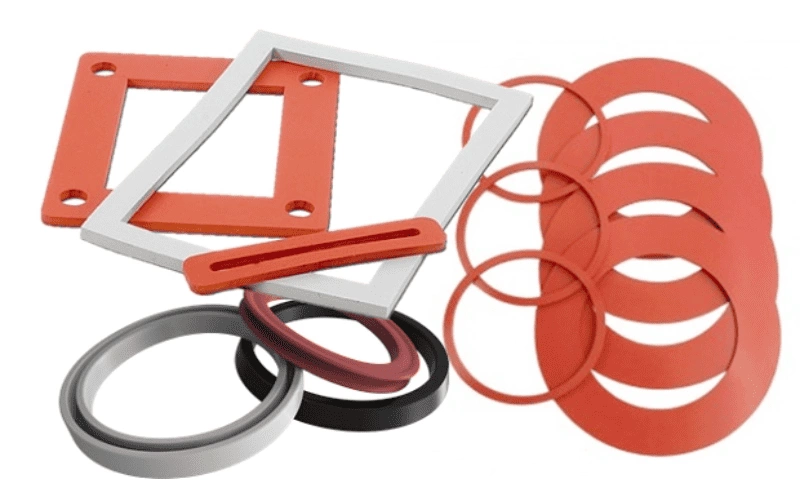
Silicone seals can be customized to match the aesthetic of your equipment or color-coded for different functions. For example, a red silicone seal could be used for hot applications, while a blue one could be used for cold.
Prevent Leaks and Contamination
Silicone is a waterproof sealant that prevents leaks in equipment. Furthermore, food-grade silicone prevents contamination due to its resistance to moisture, liquids, and chemicals.
It is important to note that silicone gaskets are unsuitable for petroleum-based chemicals. You can use fluorosilicone gaskets instead in these applications.
Flame Retardant
In the event of a fire, silicone doesn’t catch fire easily and when it does, it doesn’t produce harmful fumes. This adds an extra layer of safety in environments where open flames are a common occurrence, such as in commercial kitchens.
Resistant to Compression Set
Silicone works well under pressure. The material returns to its original thickness after exposure to compression sets over extended periods. Some food service equipment applies high pressure to ensure food safety.
Consequently, silicone is ideal for these processes since the material remains flexible and does not deform under high pressure.
Highly Durable
Silicone rubber is more durable and weather resistant than other materials. The material can withstand extreme weather conditions, including ozone-resistant and UV resistant. Furthermore, because of its durability, silicone is highly economical.
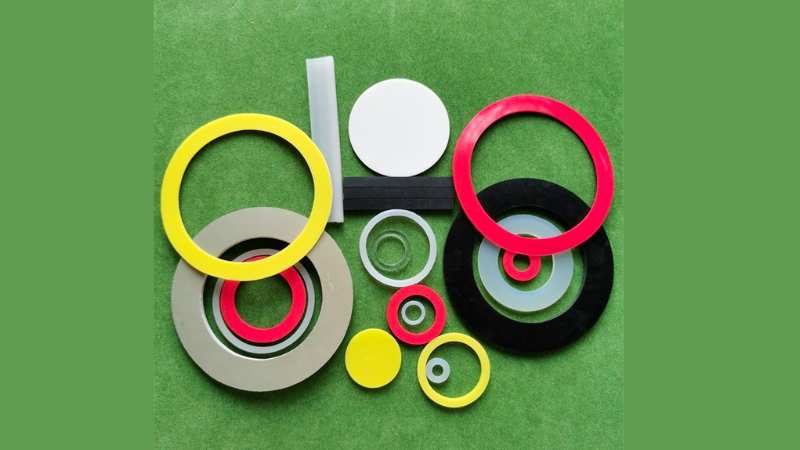
You can use the material in your food service equipment for a long time without showing wear. Furthermore, food-grade silicone does not require a lot of maintenance after installation.
Excellent Insulators
The food processing industry, especially dairy, requires insulation materials to prevent heat loss or gain. Silicone provides good electrical insulation by providing electromagnetic interference (EMI) shielding for electrical components. Consequently, this material is suitable for meat processing, oven and refrigeration, and food packaging.
The Role of Silicone Gasket in Ensuring Quality and Compliance in the Food and Beverage Industry
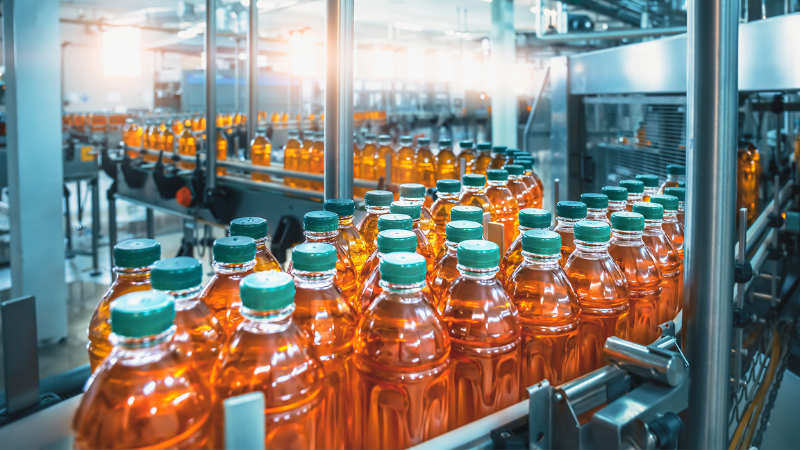
Silicone gasket plays a crucial role in maintaining food safety standards and ensuring compliance within the gasket industry. These FDA-approved silicone rubber gaskets not only help prevent cross-contamination between different food products but also contribute to maintaining product integrity throughout the supply chain.
Silicone seals help maintain consistent quality standards by preventing cross-contamination between different food products.
In the fast-paced world of food service, preventing cross-contamination is paramount to ensure consumer safety. Silicone gaskets act as a barrier, effectively sealing off different compartments or sections within equipment such as refrigerators, ovens, and blenders. This prevents any potential transfer of flavors, odors, or harmful bacteria from one food item to another.
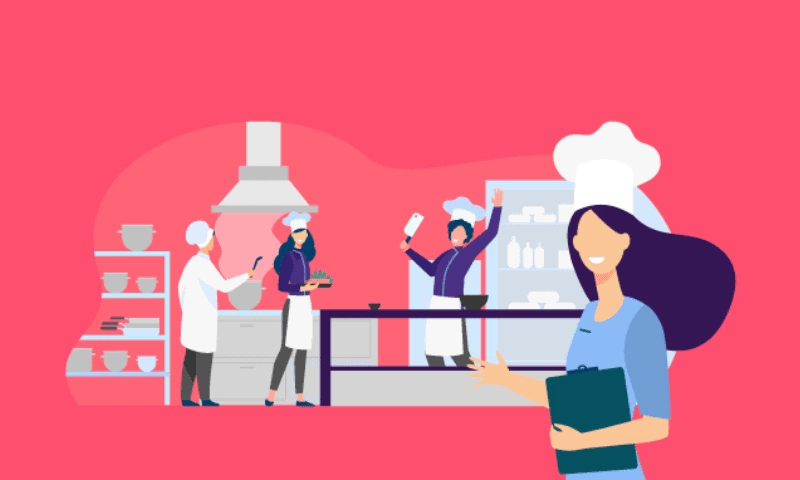
Imagine a busy kitchen where various ingredients are being prepared simultaneously. Without proper sealing provided by silicone gaskets, there would be a high risk of flavor contamination. For instance, pungent spices used in one dish could easily permeate into neighboring containers if not for the reliable barrier created by these seals.
Compliance with industry regulations is facilitated through the use of FDA-approved silicone rubber gaskets.
The food and beverage industry is subject to strict regulations to ensure consumer safety and prevent health hazards. Silicone seals are designed with compliance in mind, meeting the rigorous requirements set forth by regulatory bodies such as the FDA.
By utilizing FDA-approved silicone rubber gaskets, manufacturers can confidently meet these standards while avoiding potential legal consequences or reputational damage caused by non-compliance. These seals undergo thorough testing to ensure they are free from harmful substances that could leach into food products.
By ensuring proper sealing, silicone seals contribute to maintaining product integrity throughout the supply chain.
From production facilities to transportation and storage units, maintaining product integrity is crucial for businesses operating in the food and beverage industry. Silicone seals provide an effective solution for achieving and preserving this integrity.
During transportation, for example, silicone gaskets help create a tight seal in containers and packaging, preventing any leakage or contamination that could compromise the quality of the products. This ensures that consumers receive goods in optimal condition, free from any external contaminants.
Moreover, when used in equipment such as industrial mixers or blenders, silicone seals prevent leaks that could lead to product loss or equipment damage. This not only helps businesses save costs but also ensures consistent production and avoids unnecessary disruptions.
Conclusion
The use of silicone seals in food service equipment offers a wealth of benefits. From their superior temperature resistance, non-toxic composition, and environmental friendliness, to their excellent insulating properties, durability, and variety, silicone seals ensure safe and efficient operations. This comprehensive set of advantages makes silicone seals an indisputable choice for food service applications.
Searching for the Perfect Silicone Seals? Hongju Has Got You Covered!
If you’re in the market for silicone seals that meet all the required standards for food service equipment, look no further than Hongju Silicone. Our seals are not only FDA-approved, but also stand out for their superior resilience, non-toxicity, temperature resistance, and colorful variety. At Hongju, we’ve got your silicone seal needs covered!
Take the First Step:
Requst for an Inquire
Quality Meets Affordability. Inquire Now for High-Quality Products at Low Volumes.