What is a Silicone Rubber keypad?
An elastomeric keypad or a silicone rubber keypad is a particular type of input device with a webbing made of compression-molded silicone rubber. A silicone rubber keypad is built around a printed circuit board. Silicone keyboards are an essential component in many applications.
Silicone rubber is a rubber-like material containing silicon, oxygen, hydrogen, and carbon. Silicone keyboards use integrated carbon pills to trigger a switching function and create a tactile feel. This unique keypad material is also flexible and easy to customize.
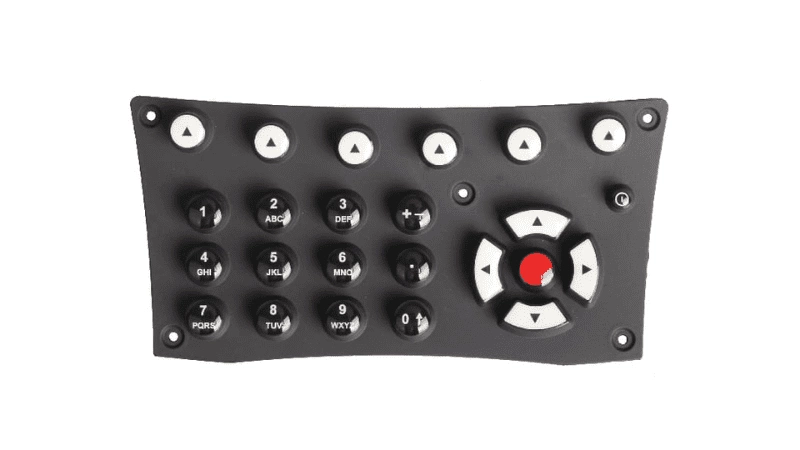
Silicone Rubber Keypads Properties
Custom silicone rubber keypads demonstrate outstanding compression molding properties. They feature a unique combination of mechanical and chemical properties that regular rubber cannot match.
The reason for choosing silicone rubber keypads is their ability to resist environmental degradation. They are generally non-reactive and resistant to extreme environments and temperatures. At extreme temperatures, silicone keypads’ mechanical properties (tear strength, elongation, and tensile strength) are far superior to those of conventional rubber keypads.
Because a silicone keypad is a natural light diffuser, you can easily backlight it using LEDs. Silicone rubber keypads are also waterproof, so they will not allow accidental spills to spoil the circuit board.
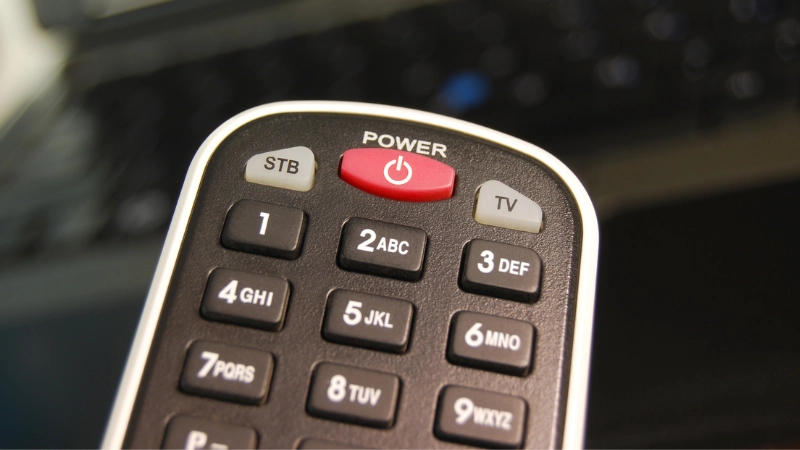
How Are Silicone Rubber Keypads Made?
Step 1:Making the Tool
Elastomeric keypad designs require a two-plate mold tool consisting of a silicone compression molding tool (top half) and a molded keypad (bottom half). EDM or CNC milling machines can be used to make mold tools. The molding tool is pre-heated for the best results.
Silicone rubber keypads can be uniquely engineered to have positive feedback when you press the keypad. The keypad needs around 0.060 inches of travel to achieve the ideal tactile feel.
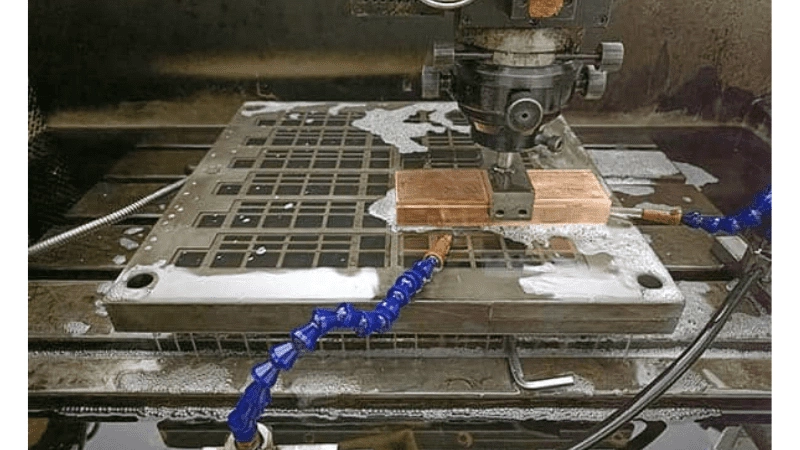
The keys on the keypad have different actuation forces. A cone-shaped key, for example, can have an actuation force of 20 to 250 grams, whereas a flat-shaped key can have an actuation force of 20 to 100 grams.
The silicone rubber keypads obtained from molding should have at least 30 grams of minimum return force. This will ensure there are no sticking keys on the silicone keypad.
Step 2: Choose the Ideal Form of Silicone Rubber
We use two forms of silicone material to make silicone rubber keypads, gum stock and liquid.
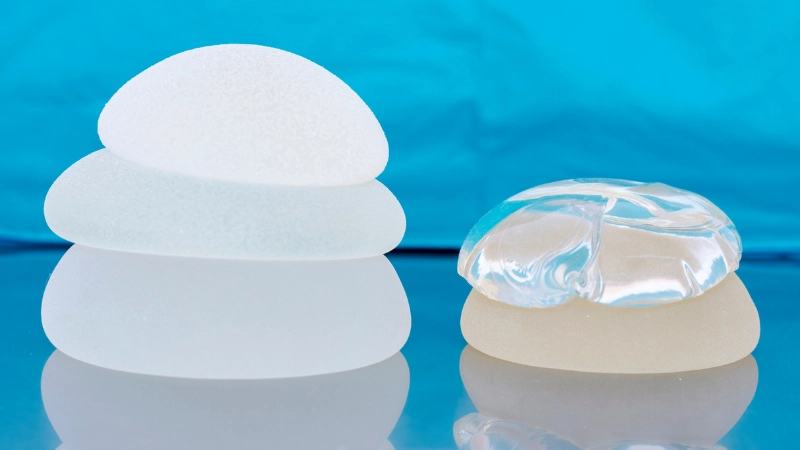
Liquid silicone rubber is composed of platinum-cured silicone with a remarkable ability to resist high temperatures. Liquid silicone rubber has a similar consistency to that of petroleum jelly. Creating custom features using a liquid silicone rubber injection molding process is usually less expensive and easier.
Gum stock silicone rubber, on the other hand, is a high-consistency rubber that looks and feels like dough or thick putty. The solid silicone rubber is prepared in large sets. The components are usually mixed at high temperatures before adding a peroxide catalyst.
The cross-linking process is usually interrupted to create gum-stock silicone rubber. The mildly cross-linked silicone is then rolled out into sheets.
Step 3: Silicone Preform Preparation
Compression molding of silicone rubber is one of the most effective methods for making industrial electronic products.
It is the primary method we will be using in this demonstration. But first, we must prepare the silicone preforms (what we put into the tool).
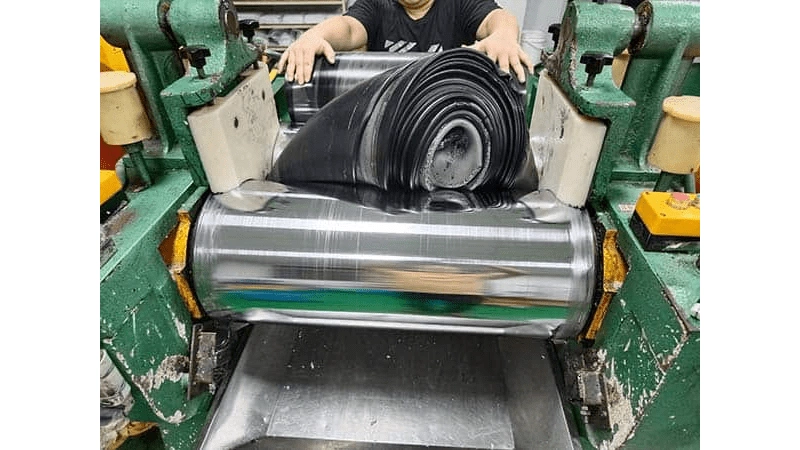
Before vulcanizing, silicone rubber looks more like a pliable Play-Doh. Color is usually added to the mold to match our client’s specific requirements or personal preferences. Each molded part contains a precise amount of silicone.
We carefully weigh and cut the silicone into preforms. Then we place the cut pieces in the tooling cavity, ensuring that the correct amount fills each cavity.
Step 4: Loading Silicone Preforms into the Mold
Once we’ve got the right mold design for the elastomeric keypads, we will load the silicone rubber material into the mold tool. We assemble and insert silicone rubber preforms into the compression molding press. Then we press the clamp to a set pressure to create high-quality rubber keypad parts.
The silicone must have the right shape that appropriately matches the mold’s cavity. This will ensure the hole is filled with enough raw material without creating extra flash. The extra flash refers to the overflow material that remains attached to the parts from around the edge of the molded rubber keypad.
Pressure, heat, and time will transform the silicone preforms into the configuration of the keypad mold at the bottom. The combination of pressure and heat forces the silicone rubber to flow and fill the mold cavity, forming the rubber keypad.
Step 5: Curing and Removing the Keypad from the Tool
Typically, molded silicone rubber keypads take approximately 5 minutes to cure at 180°C. We must maintain the optimum heat and pressure until the rubber is cured.
Then we remove the silicone keypad from the mold tool after curing. The removal or ejection process requires a pair of gloves and a compressed air hose. The gloves are necessary since the silicone rubber keypads in the mold tool are very hot. The compressed air hose helps lift the silicone keypads from the tool.
Step 6: Screen Printing the Silicone Keypads
The next important step is to specify the function of each key on the silicone rubber keypads. There are four popular methods for printing silicone rubber keypads: screen printing, silicone ink, laser marking, and label plate engraving.
However, we use screen printing to guarantee superior quality control. It is also one of the most cost-effective methods ideals for mass production. Two things are required for screen printing: screen print color and a hollowed mesh.
Letters that will appear on the keytops are hollowed out in a mesh. The keypad is placed into a screen nest, exposing only the keytops. The screen nest will ensure the silicone rubber keypad is stationary during this manufacturing process step.
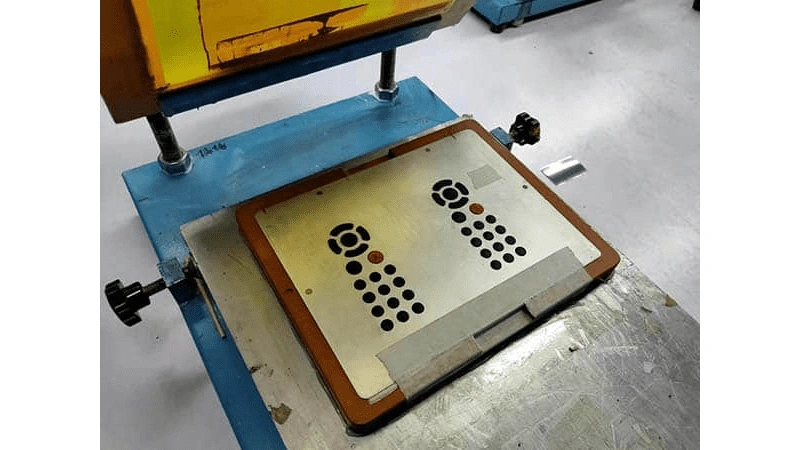
Then we position the hollowed mesh on top of the key tops. Only the hollowed parts of the mesh will contact the paint. Each essential top will receive ink evenly. The screen printing pass is used to apply the paint to the exposed parts of the keypad.
Step 7: Laser Etching
After curing, we use laser etching to expose the final color on the silicone rubber keypads. Unlike screen printing, we do laser etching with tighter tolerance to ensure detailed keypad nomenclature.
Step 8: Creating Tactile Response with the Switch
Two ways exist to create a contact or tactile response with the switch in silicone keypads. They include a conductive carbon pill or a rubber switch.
We make each carbon pill the same way we make silicone keypads. We mix a conductive material (carbon) with silicone. When a rubber button is pressed, the carbon particles come in contact with the switch on the board, allowing electricity to flow. The user’s resistance when pressing a rubber button creates a tactile response.
We mold the conductive pills into the keypad by inserting molding.
In contrast, rubber switches don’t produce webbing returns. Instead, they have a metal dome under the keys. The metal dome creates contact with the circuit to produce tactile feedback.
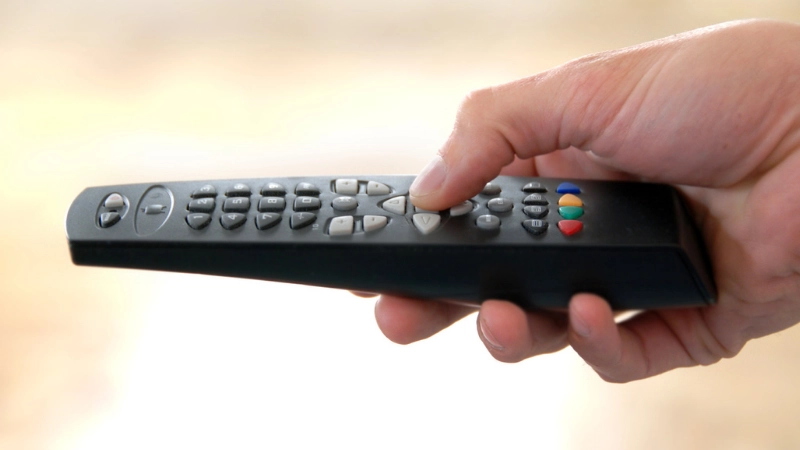
When a key is pressed, the concave design of the metal dome makes contact with the PCB to complete the loop. When current flows, the membrane switch will function normally. We attach the metal dome membrane switches to the keypads.
Step 9: Testing and Quality Control
Next, we test the silicone rubber keypads for quality control. First, we do a silicone button lifetime test to determine the durability of the rubber keypads. We do this by continuously beating the keys from the top.
Second, we do an alcohol abrasion test to ensure the text and graphics aren’t rubbed off. We do this by continuously rubbing the entire surface of the keypads with alcohol. Lastly, we do an actuation force test to ensure the keypads have the ideal tactility.
Conclusion
The manufacturing process for silicone rubber keypads involves casting, molding, trimming, printing, assembly and so on. By understanding the manufacturing process, businesses can achieve consistent results and reduce the risk of defects, ensuring high-quality silicone rubber keypads for customers.
Custom Silicone Keypads: Precision-Engineered to Your Exact Specifications
For over 20 years, Hongju Silicone has partnered with global clients to deliver high-performance silicone rubber keypads, which combine tactile precision, durability, and perfect functional integration. Our expertise in compression molding and precision die-cutting ensures your designs come to life with consistency and reliability.
Let’s bring your design to life! Contact us today for a free, no-obligation project evaluation!
Take the First Step:
Requst for an Inquire
Quality Meets Affordability. Inquire Now for High-Quality Products at Low Volumes.