Silicone rubber extrusion can truly change your product’s appearance, functionality, and strength. Therefore, here we have discussed important aspects of the silicone rubber and extrusion process to help you understand its importance and applications. Read on now!
What is Silicone Rubber
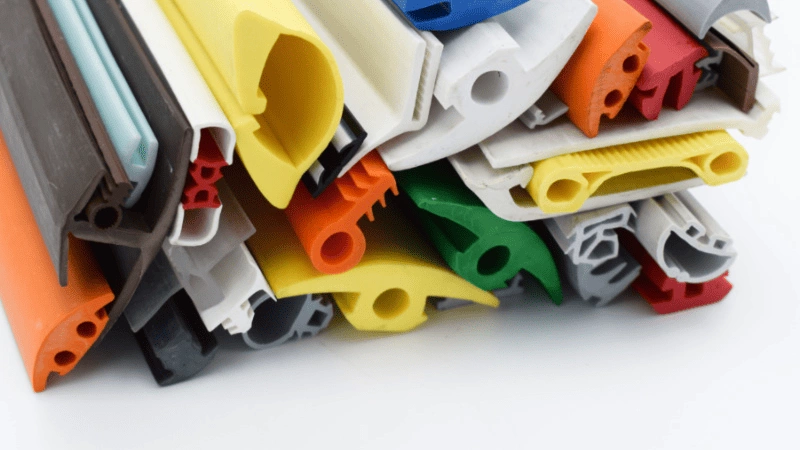
Silicone, also known as polysiloxane, is considered a rubber compound. It is a human-made elastomer, which has properties of both rubber and plastic. Silicone is usually used to make hard solids, liquids, and rubbery products, but as elastomers are indicated as rubbers, silicone is also usually described as rubber.
Some people also confuse silicone with silicon, but they are different materials. Silicone is a polymer, while silicon is an element. Silicone rubber has many properties and applications.
What are the Properties of Silicone Rubber
The high bond energy and strong Si-O chemical structure give Si Elastomers unique properties. Some of the silicone rubber properties that make it perfect to use are:
- Excellent resistance to attack by ozone, oxygen, and sunlight
- Wide service temperature range: thermal oxidative stability and thermal resistance
- Excellent non-adhesive and non-stick
- Readily resistant to particle and electromagnetic radiation (alpha, UV, gamma, and beta rays)
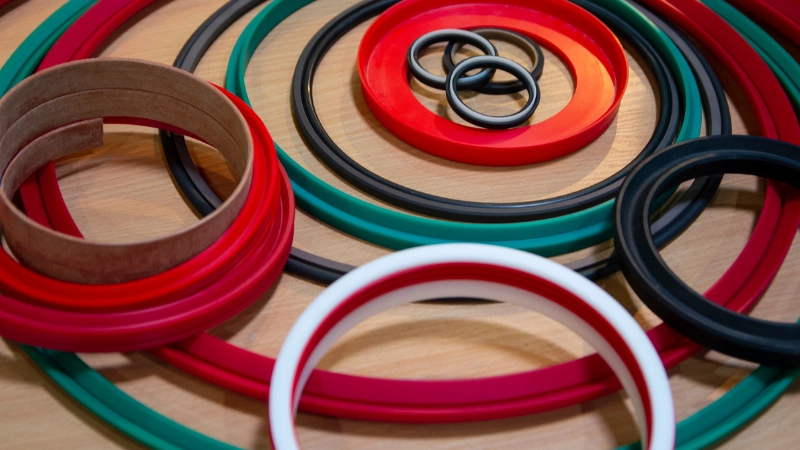
- Works great at low temperatures because of their lower glass transition temperature
- Chemical resistance
- Excellent insulation properties
- High bio-compatibility
- Optical transparency
- Mechanical properties
Industrial Applications of Silicone Rubber
Due to the amazing properties of silicone rubber compound, it is widely used in different industries such as automotive, aerospace, medical, food processing, construction, E&E, and others. Here are some common applications of silicone in industries.
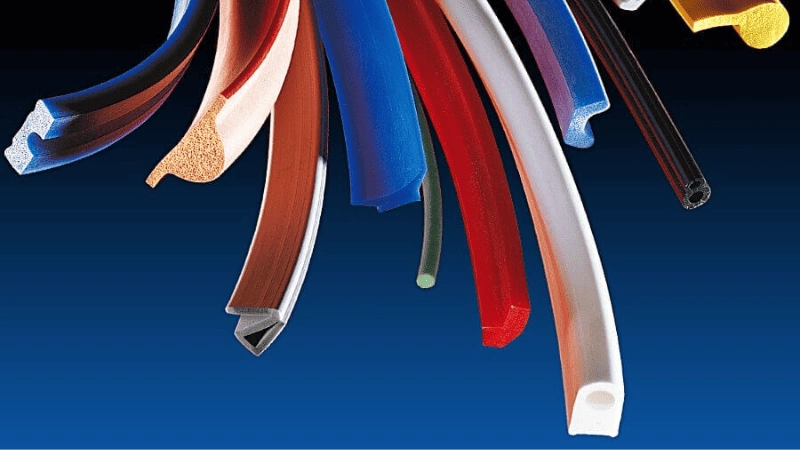
Electronics
Electronics applications require some of the highest quality silicone rubber for sealant, insulating tape, housings, lubricants, varnish, and keyboards. High-thickness rubber is also injection molded into arrestors and insulators.
Construction
This industry uses silicone rubber for sealants, adhesives, and coatings because of its ability to bond to metals and weathering properties.
Aerospace
Silicone rubber is commonly used in tooling materials, spacesuit fabrics, gaskets, seals, and other aircraft maintenance and manufacturing products.
Medical
Silicone rubber has been commonly used for deformers, tubing, and adhesives.
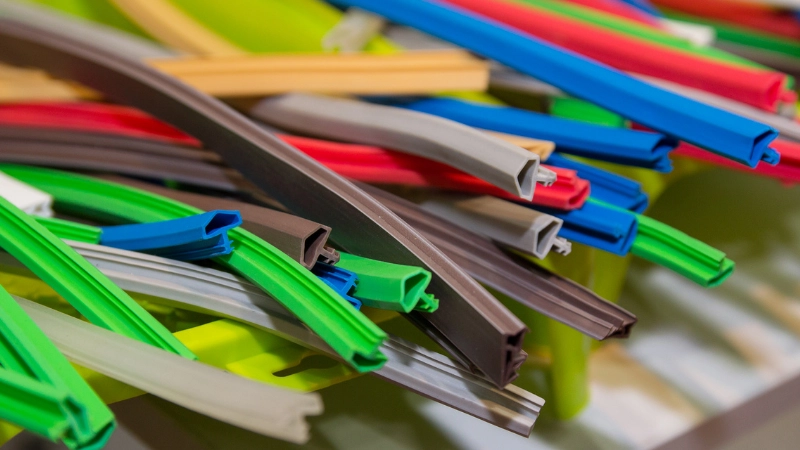
Automotive
This industry uses silicone for weather and vibration-resistant parts, varnishes, and coatings.
Consumer goods
Silicone rubber is used as anti-stick bakeware, utensils, food containers, jewelry, and toys. You can even find silicone rubber band bracelets. Besides that, silicone is also used as an ingredient in cosmetics, deodorant, laundry soap, and shampoo.
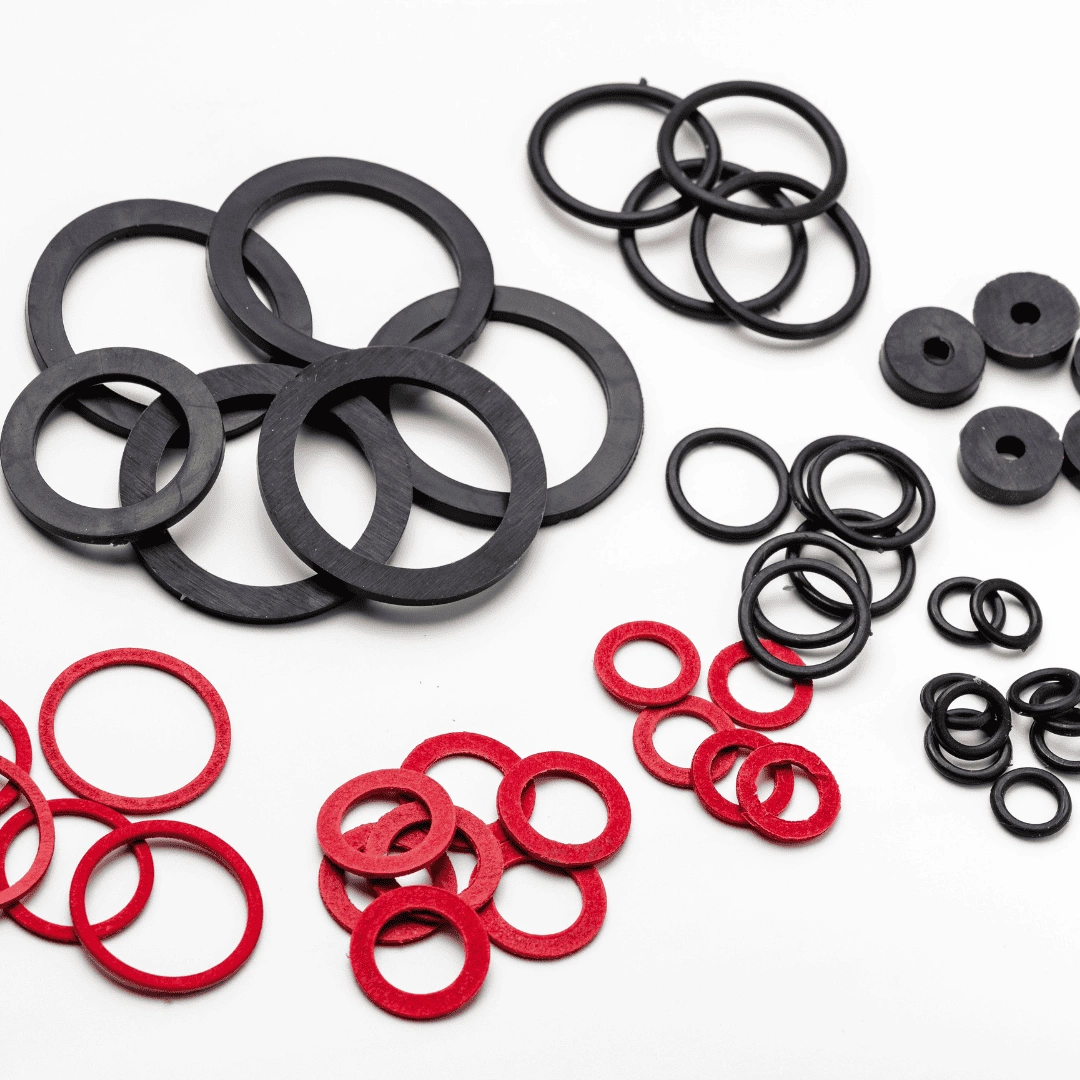
Send Your Inquiry Now!
Quality Meets Affordability. Inquire Now for High-Quality Products at Low Volumes.
Natural Rubber vs. Other Synthetic Rubbers
Tensile Strength
The tensile strength of natural rubber is higher than synthetic rubber. This is why breaking or tearing natural rubber with stretching is difficult, making it the best material for several important applications. While synthetic rubber has lower tensile strength, they are still difficult to break.
Tear Resistance
Tear resistance of rubber refers to the optimal force required to tear a test specimen in a direction normal to the direction of the stress. Natural rubber has higher tear resistance than synthetic rubber.
However, the silicone rubber compound is one of the best man-made rubbers that ensures maximum strength, making it the ideal option for producing different compounds.
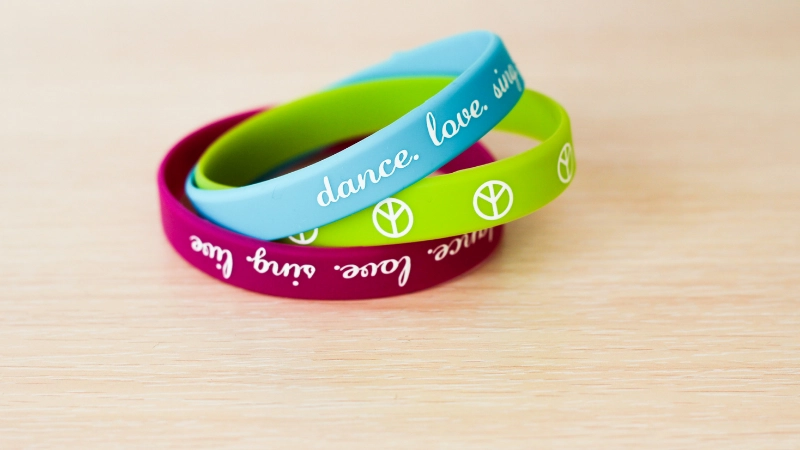
Chemical Resistance
Silicone rubber is resistant to chemicals, preventing it from easily getting damaged or impacting the product’s composition. They resist oxidizing chemicals or moderate, concentrated sodium hydroxide and ozone. Natural rubbers have poor resistance to oils, ozone, atmospheric oxygen, and several hydrocarbon solvents.
Importance of Silicone Rubber Extrusions
Silicone extrusion is a process in which silicone rubber is forced through a hardened steel die. The extruder head keeps the die in place, and the die provides the required shape of the silicone rubber.
The silicone extrusion process helps manufacturers provide appropriate raw materials in terms of colors and shapes to companies for their production lines.
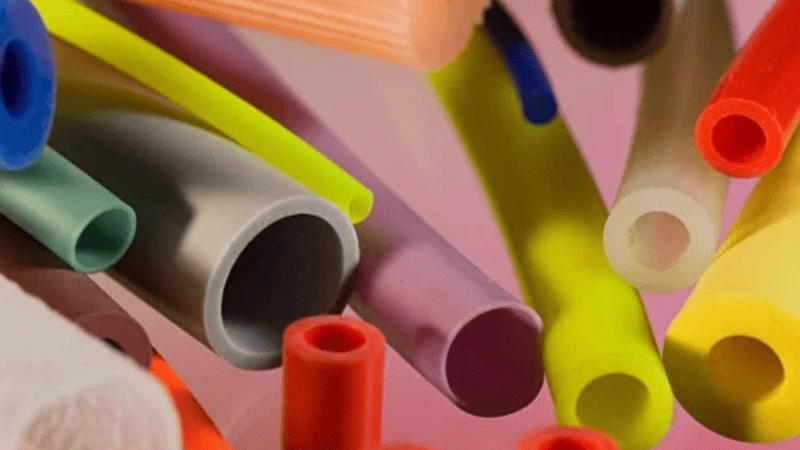
The process offers several options, such as cords, continuous strips, and others at the desired thickness. This way, manufacturers can easily produce products by treating the silicone rubber compound achieved by the extrusion process.
The compound you receive after the process will offer you the following features, making it ideal for making different products.
- Transparency and translucency
- Flexibility
- Chemical resistance
- High-temperature resistance
- High elastic and resilience memory
- Processability
- Biocompatibility
- Conductive
- Flame resistance grade
- Excellent mechanical properties
- Processibility
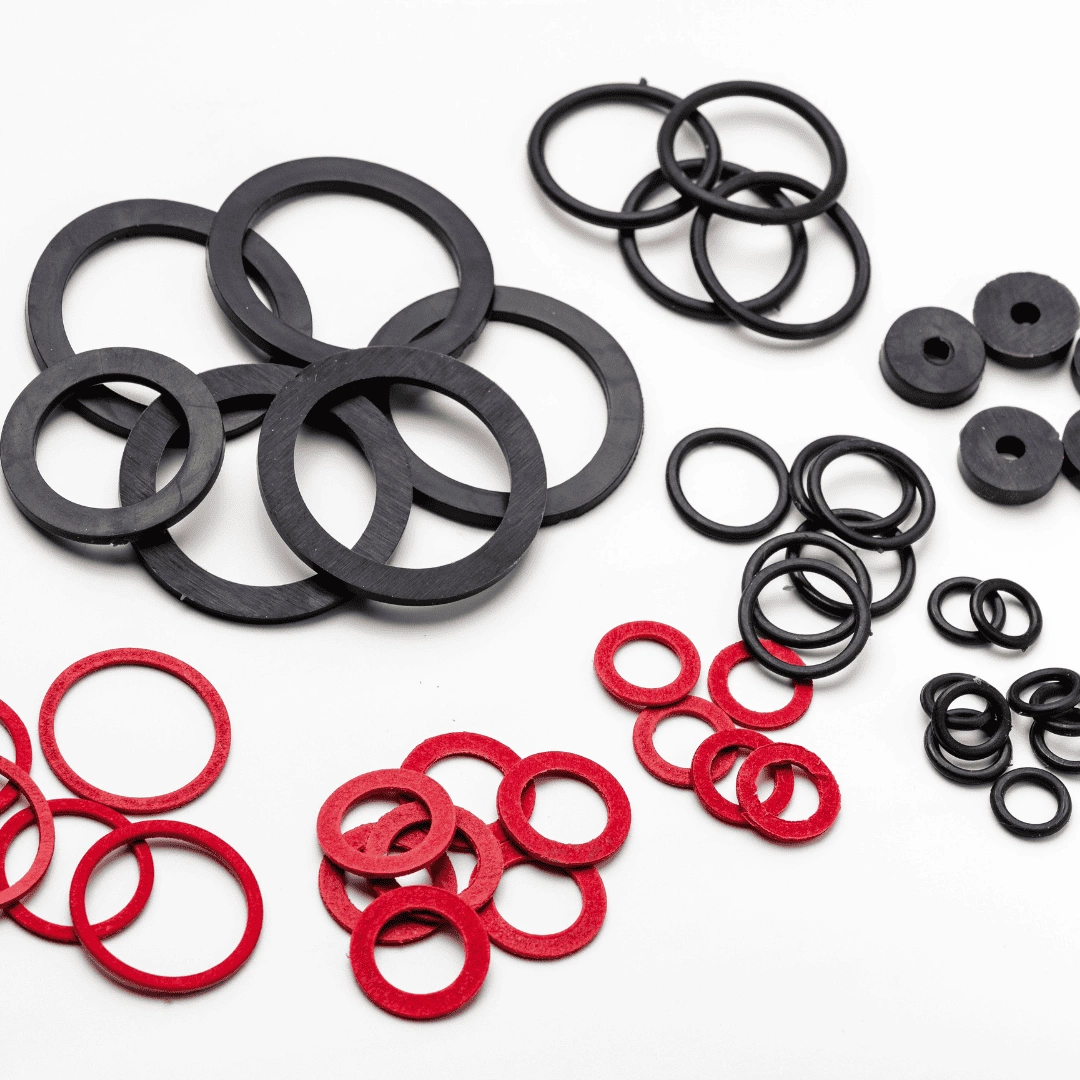
Send Your Inquiry Now!
Quality Meets Affordability. Inquire Now for High-Quality Products at Low Volumes.
Extrusion Process of Silicone Rubber Compound
What is Extrusion
It is a process used to create products of a fixed cross-sectional profile by forcing material through a die of the required cross-section. The manufacturer uses a plunger or piston to apply compressive force on the materials.
Benefits of Extrusion
The extrusion process has several benefits that might help industries improve their products. Here are some benefits of opting for the extrusion process.
- Flexibility of operation
- Low cost per part
- Continuous operation
- Different types of raw materials can be used
- High production volume
- Surface finish results are good
- Good compounding or mixing
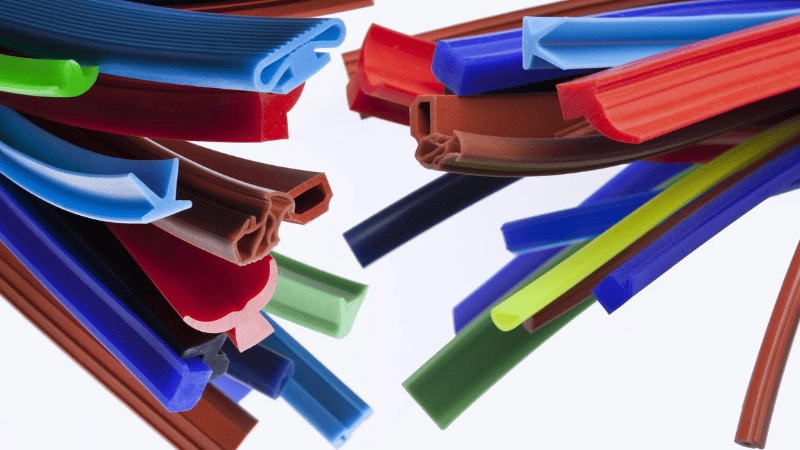
Extruder Types
Screw extruder
A screw extruder is a pump used for manufacturing machines to pump molten plastic. This is the most commonly used extrusion machinery in the modified polymer and plastic processing industry.
Screw extruders can be divided into twin-screw extruders and single-screw extruders. Also, the function and structure of the twin-screw extruders are very similar to single-screw extruders, but there are many differences in their working principle.
- Forced delivery: In twin screws, both screws rotate in opposite directions at the meshing part. One screw pushes the material out of the gap, and the other screw pulls the material into the meshing gap. The element is forcibly pushed out toward the head along the screw.
- Mixing and homogenization: These machines have a small gap at the meshing point, and the machine’s speed is relatively faster than the single screw extruders.
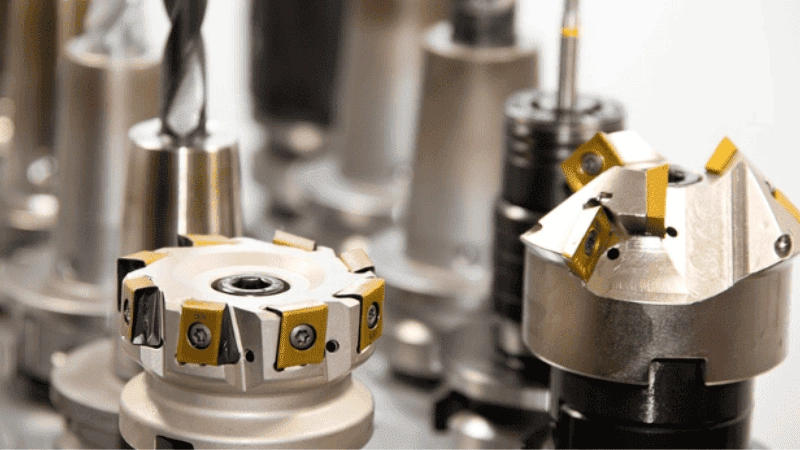
- Self-cleaning: Since twin screws have high speed in the meshing area, they can easily scrape off any element adhering to the screw. This benefit helps to reduce the risk of material deterioration and degradation.
- Feeding method: The twin screws require quantities and uniform feeding. They also assume metered starvation that helps them to feed at a controlled rate below full capacity.
- Exhaust: With the help of starvation feeding, a lead screw is used at the leading end, where the materials are pushed out so that the screw can move in a zero-pressure state. This allows the extrusion section to maintain consistent pressure.
Extruder head
The extrusion head is the processing part of the machine that shapes the extrudate, i.e., the tool that determines properties, shape, dimensions, and structures of the mutual position and extrudate of the elements during the extrusion process.
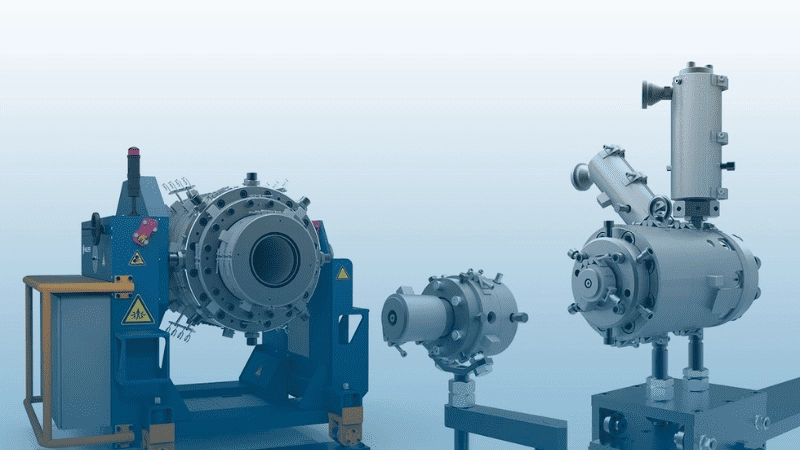
This tool has an open-forming cavity, i.e., an extrusion die. It ensures the proper chemical and physical processes in the polymer during the production of the materials through the flow channels.
The extrusion head is adjusted to the plasticizing part of the extruder. Larger extrusion heads are adjusted using bolt-pin connections that are firmly fixed with the bolt connections.
Furthermore, there are different extrusion heads, such as spiral, longitudinal, transverse, and singular. The spiral extrusion heads can be made as transverse and longitudinal extruder heads.
The extruder heads allow you to obtain foam or solid polymer material. The extrusion heads for the solid polymer are different in design to give your required state of silicone rubber.
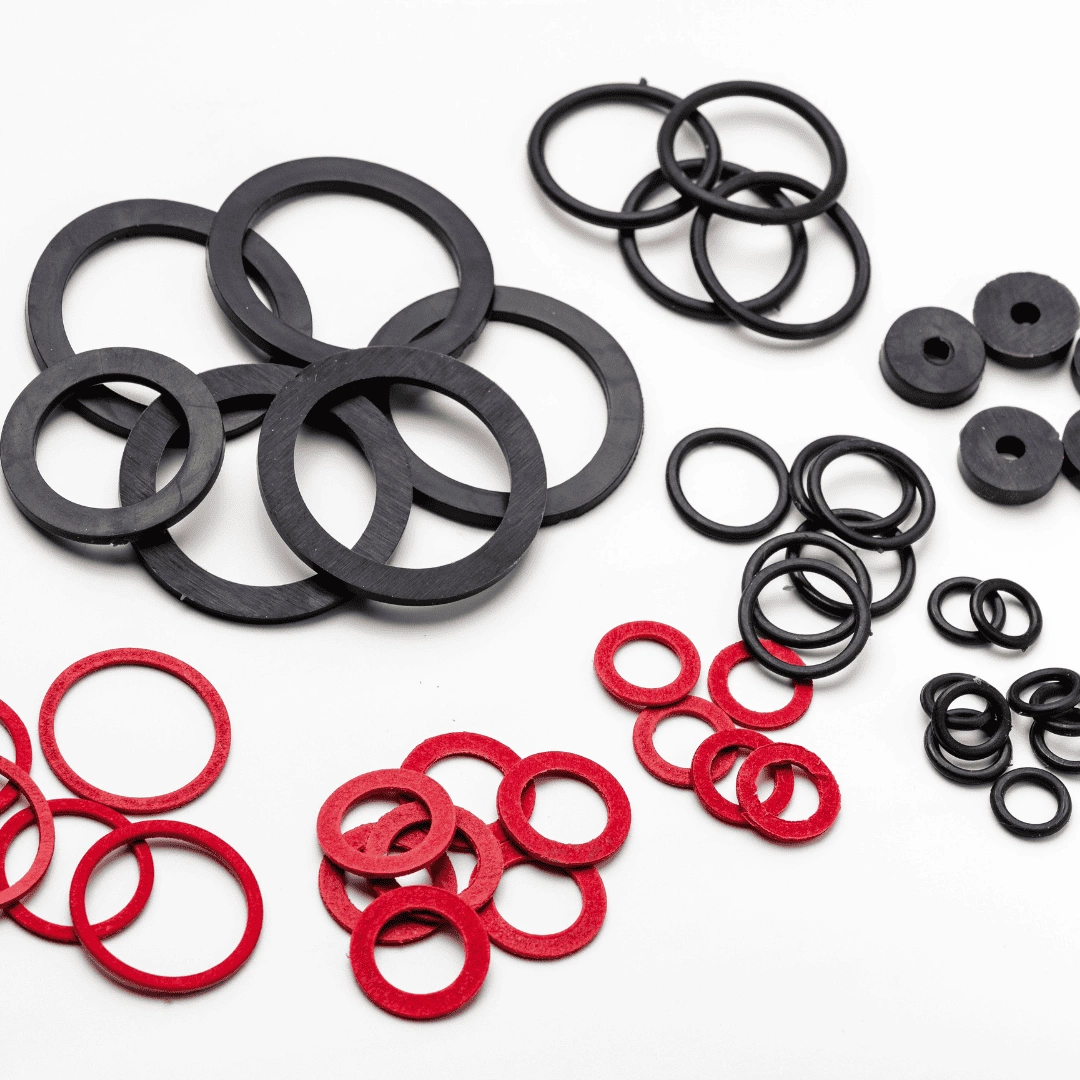
Send Your Inquiry Now!
Quality Meets Affordability. Inquire Now for High-Quality Products at Low Volumes.
Silicone Extrusions in Diverse Industries
Here we have discussed the industry’s most common use of silicone extrusions.
Industrial applications
Silicone rubber extrusion is used effectively in many branches of production and industry. It can be found in almost every type of industrial and oil lubricant, among others in lubricants and engine oils for engines and gears.
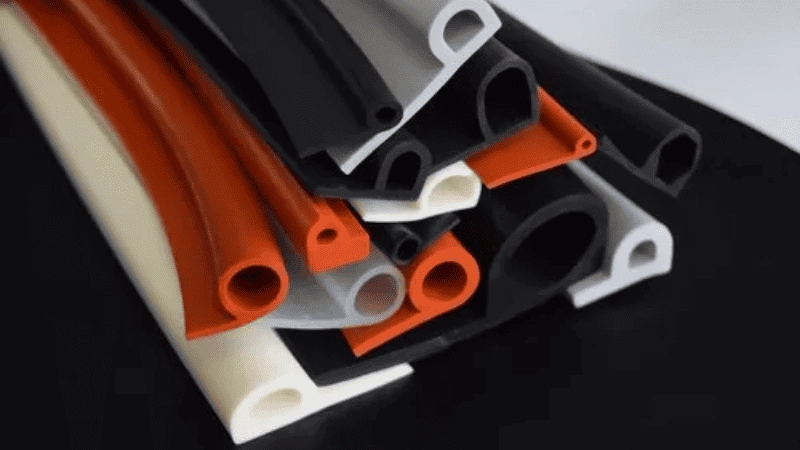
Also, silicone extrusions are used for seals, rubber bumpers, keyboards, keypads, and copier rollers. Extruded silicone sheets are common silicone extrusions used for parapet wall connections, aluminum window seals, metal-to-metal joinery, EIFS joints, etc.
Medical Industry
Some of the common uses of silicone rubber extrusions are in the medical industry. It produces medical components like compression bars, balloon catheters, feeding, hearing aids and ear plugs, test chambers and infusion sleeves, and others.
High-consistent silicone rubbers are also extruded to make a variety of profiles and tubing. Extruded silicone rubber is considered the best element to incorporate in medical devices because they are thermal stability and glass-transition temperatures.
Optimal Extrusion Process
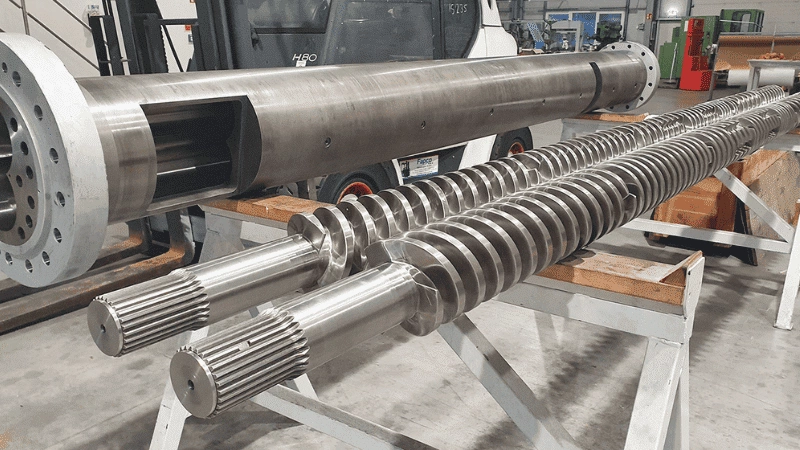
Several things need to be in place to achieve efficient extrusion. You need professional people running and managing the operation for a stable, high-quality process. The equipment needs to be in good condition, an excellent preventive maintenance program should be used, and the best equipment required to get good, efficient results.
The extrusion process is not about doing one thing right but doing everything right to get the results. Here are a few of the most important things that can greatly impact the outcomes of the extrusion process.
Avoid High Temperatures
The deformation energy is transformed into heat during the extrusion process, increasing the extrudate’s temperature. As a result, it affects the mechanical and microstructure properties. The increased rate in temperature in the deformation process greatly impacts the temperature of the extrudate.
You need to maintain the temperature to get your desired results and avoid causing product errors. The experts control the deformation energy so that lower heat is produced, which can impact the process.
Use Cured Silicone
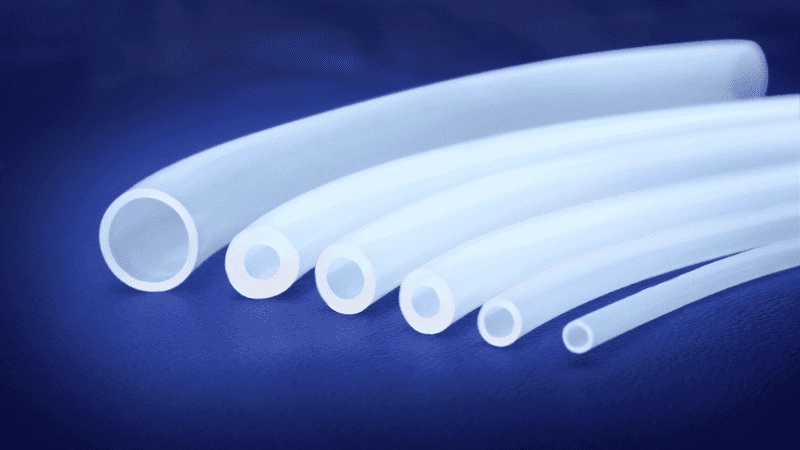
Cured silicone material has great mechanical properties, significantly improving extruded silicone functionality. It helps you get an outcome that is highly tear-resistant and has a stable application process. These materials also have low fire resistance and thermal conductivity, making them easy to use for extreme temperatures.
Advancements and Innovation in the Rubber Industry
Silicone rubber is helping companies make incredible advancements in their work and making innovation possible in different industries. Several rubber industry trends are impacting consumer and industrial product manufacturing worldwide.
Some of the popular trends include the rising popularity of electric vehicles (EVs), growing demand for synthetic rubber, consumer demand for sustainable rubber materials and products, and ongoing supply chain disruptions.
The rubber market is also expected to grow at a CAGR of more than 5% from 2024 to 2030. Also, the industry is expected to be driven by important rubber uses in some important industries like medicine, aerospace, defense, agriculture, and others.
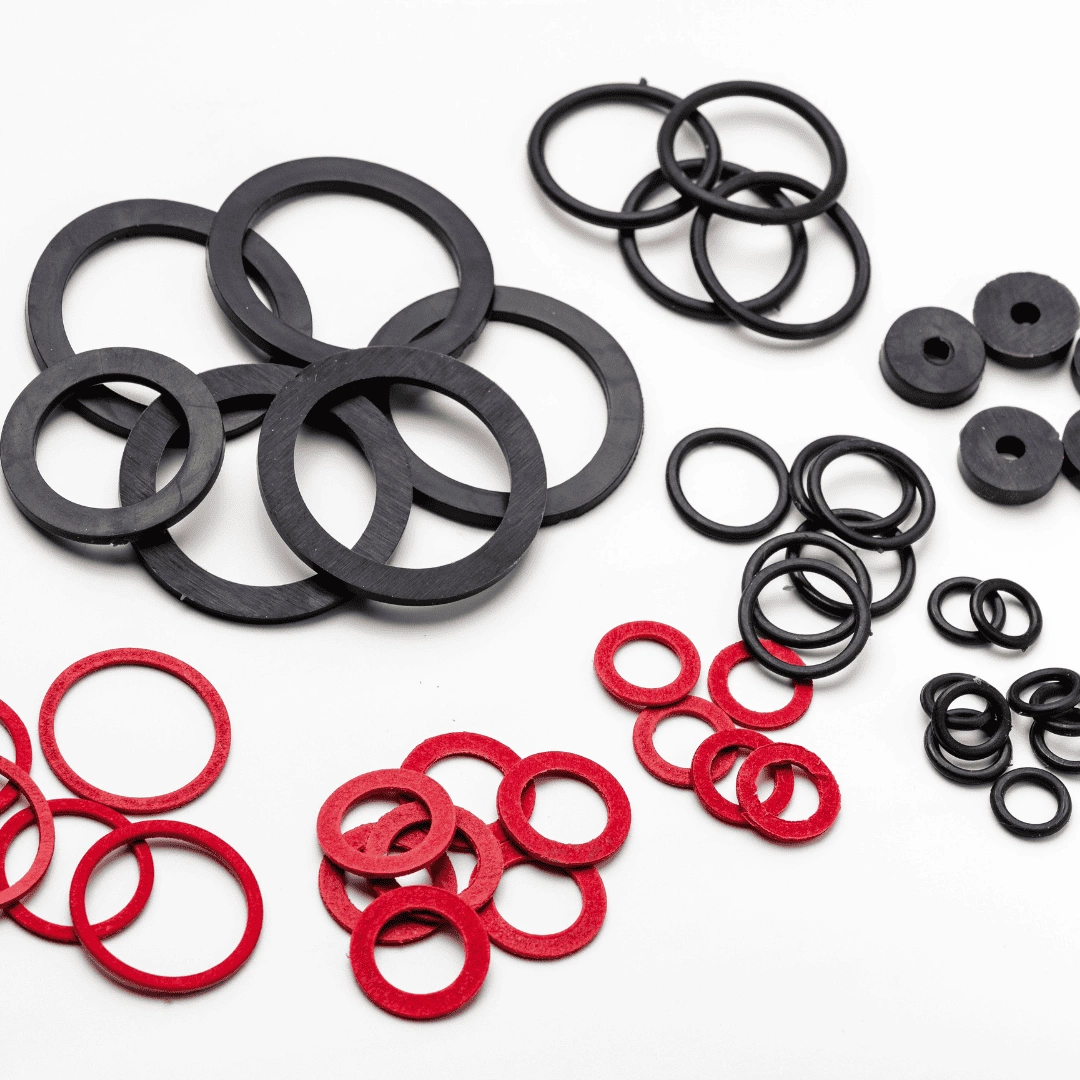
Send Your Inquiry Now!
Quality Meets Affordability. Inquire Now for High-Quality Products at Low Volumes.
Conclusion
Silicone rubber is an important type of rubber that works best for different applications. It can be used to produce different materials and to fix several things together. The silicone rubber can be achieved through the extrusion process. It helps you get different shapes, colors, and sizes of the silicone.
Transform Your Products with Silicone Rubber: Boost Performance & Durability!
Elevate your products with high-performance silicone rubber extensions now, enhancing durability, functionality, and user experience with Hongju’s custom-formulated solutions. Perfect for seals, gaskets, o-rings, and other silicone products, our silicone rubber offers superior temperature resistance, flexibility, and longevity.
Contact us today for superior-quality, promising, flexible, and durable silicone rubber now!