So, let’s dive into the world of measuring o-rings size and discover how this seemingly small task can make a big difference in your applications.
What is an O-Ring?
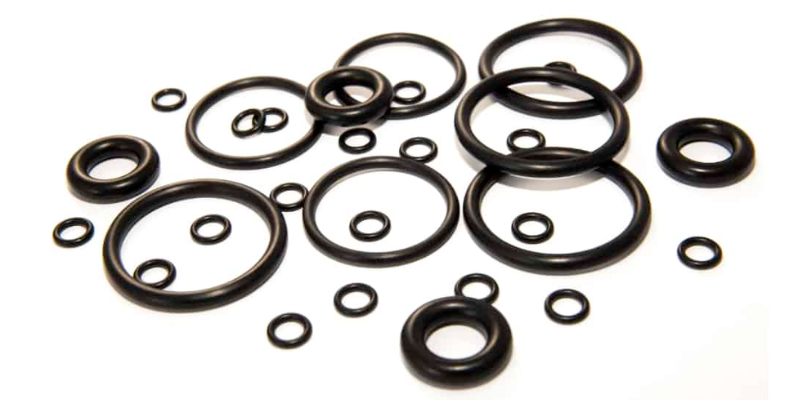
An O-ring, also known as a mechanical gasket, is a circular sealing device made from elastomers. These flexible rings are designed to fit into grooves and create a tight seal between two mating surfaces. O-rings play a crucial role in various industries due to their ability to prevent leakage and contamination.
Manufacturers utilize different materials to produce o-rings based on the specific requirements of each application. Some common materials include:
- Nitrile rubber: Ideal for applications that require resistance against oil, fuel, and water.
- Silicone rubber: Suitable for high-temperature environments and offers excellent flexibility.
- Viton (fluorocarbon): Resistant to extreme temperatures, chemicals, and fuels.
- EPDM (ethylene propylene diene monomer): Known for its superior resistance to weathering and ozone.
These materials provide the necessary properties such as durability, flexibility, chemical resistance, and temperature tolerance required for diverse industrial applications.
Why is it Important to Measure O-Ring Dimensions?
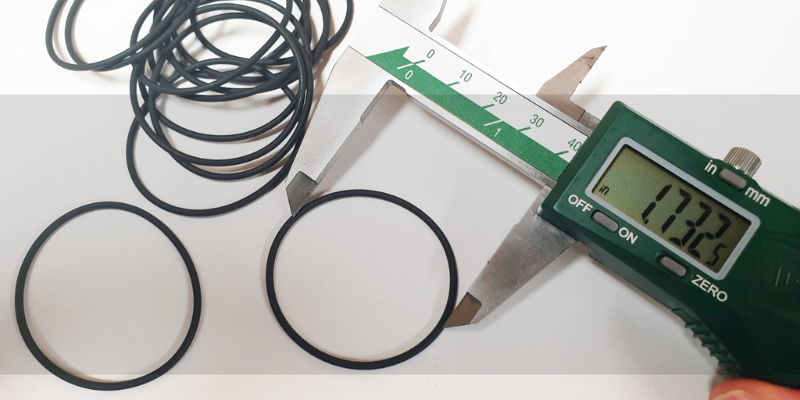
Measuring O-ring dimensions is important for several reasons:
- Ensuring proper fit: The correct O-ring dimensions are crucial for the proper functioning of the system. If the O-ring is too small or too large, it may not provide a proper seal, leading to fluid leakage or the failure of the system.
- Maintaining performance and avoiding damage: A properly sized O-ring will ensure that components within a system work as intended and are not damaged. A too-short or too-large O-ring can cause binding and excessive stress on the components, leading to damage and failure.
- Avoiding costly repairs: Incorrectly sized O-rings can lead to costly repairs, maintenance and downtime of the system. An improper fit can cause leaks or damage to the components, leading to costly repairs and downtime.
- Ensuring safety: Properly sized O-rings help to ensure the safety of the system. For example, in a hydraulic system, an incorrectly sized O-ring can lead to leaks and damage to the system, which can result in injury or damage to equipment and surrounding areas.
- Maintaining quality: Correctly sized O-rings help to maintain the quality of the product and the efficiency of the system. Inaccurate O-ring measurements can lead to decreased product quality and reduced system efficiency.
Quick and Efficient Methods for Measuring Rubber O-Rings
There are several quick and efficient methods that can be used. These methods ensure accurate measurements without wasting valuable time. Let’s explore some of these techniques:
Use of calipers or micrometers
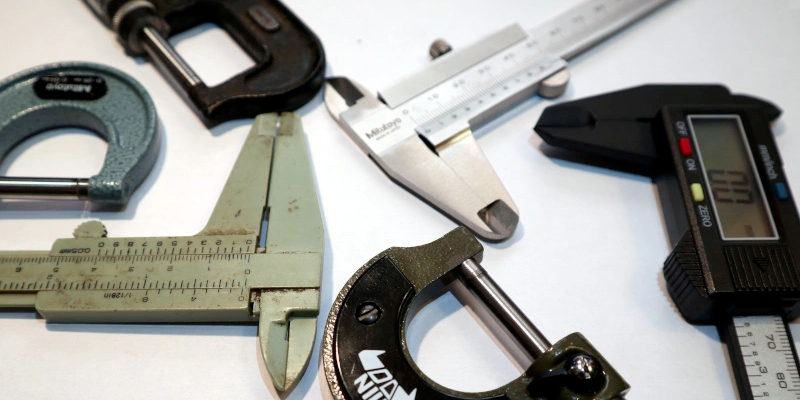
Calipers and micrometers are handy tools for measuring the dimensions of rubber O-rings. By using these instruments, you can easily determine the inner and outer diameters of the metric o ring, as well as the thickness of the O-ring. Simply place the O-ring between the jaws of the calipers or micrometer and take your measurements.
Visual inspection techniques
In addition to using measuring tools, visual inspection is crucial in determining any irregularities or damage present on the rubber O-rings. Carefully examine the surface for signs of cracks, tears, or deformities that could affect its performance. It is essential to identify any issues before proceeding with installation or use.
Non-destructive methods
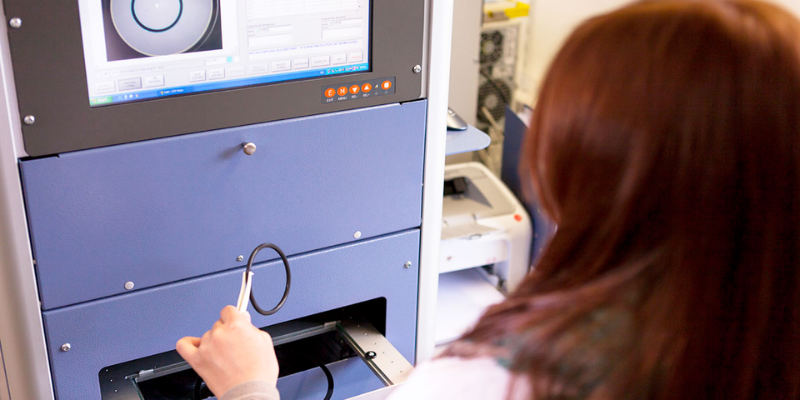
Optical measurement systems provide non-destructive ways to measure o-ring dimensions accurately. These systems utilize advanced technology like lasers and cameras to capture precise measurements of standard o-ring sizes without causing any harm to the o-ring itself. By employing optical measurement systems, you can obtain accurate results quickly and efficiently.
By incorporating these quick and efficient methods into your o-ring measurement process, you can save time while ensuring accuracy.
How to Measure O-Rings?
You must take two vital measurements to ensure you get the right size O-ring. These include the inside diameter, which we will refer to as ID. The other one is to measure the cross section which we will refer to as (CS). Read the following steps carefully for accurate measurements of both the ID and CS:
Step One: Inside Diameter (ID)
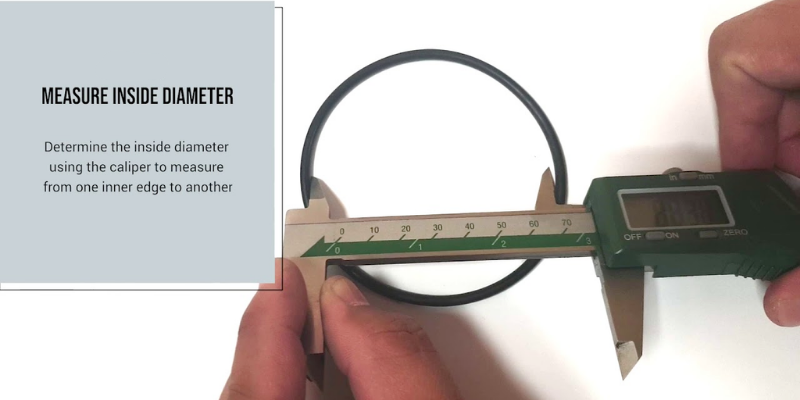
Place it on a flat surface to measure the O-ring’s inside diameter. Now you can use a variety of tools for measurement. However, in this example, we will use calipers. Use the calipers to touch it from one outer corner to one inner edge. Once you have it sturdy inside the O-ring, lock it and read the measurement.
You can also measure the outside diameter if you want. Follow the same technique. However, use the caliper hands to touch the opposites of the outer edge this time. The measurements can be measured in inches or millimeters, depending on the tool and your preference. Remember, the outside diameter isn’t necessary, but the inner diameter is.
Step Two: Cross-Section (CS)
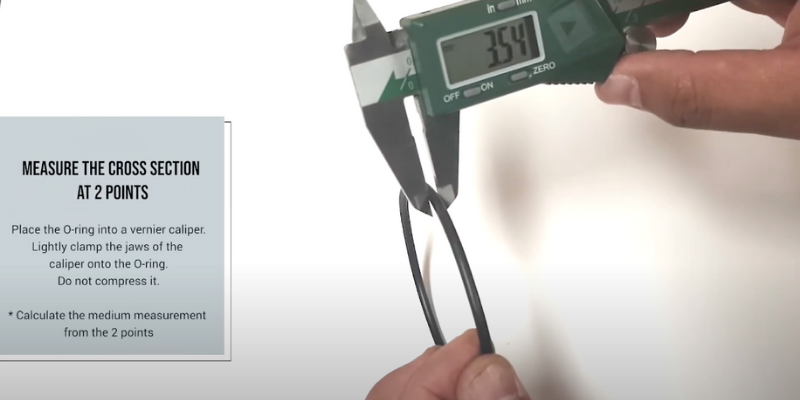
The cross-section of your O-ring is referred to as the thickness or width of the seal. You will need to get your hands on a vernier caliper. Make sure you place the O-ring in the caliper delicately. Ensure the O-ring does not compress when placed inside one outer corner of the caliper.
Now, please measure the width of the O-ring and record it somewhere. If you want a ruler to measure to be sure, repeat the measure three-four times and take the average. You must be wondering what the use of this measurement is. The CS allows you to measure the compression resistance of the O-ring, abrasion resistance, and volume swell.
Step Three: Making Use of the Measurements
Use the ID and CS to formulate the exact size O-ring required for specific applications. Most standard O-rings are referenced by their measurements ID and CS.
Common Mistakes People Make When Measuring O-Rings
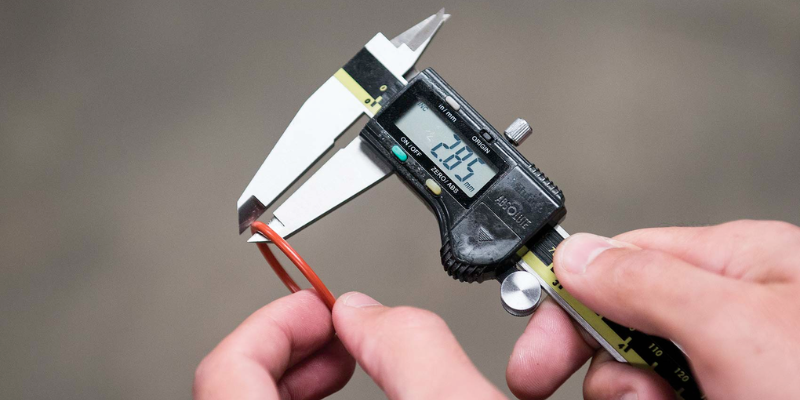
Many people are not familiar with the measurements of O-rings, which is surprising considering their importance. It is essential to raise awareness about the significance of accurately measuring O-ring size. However, there are common errors that people tend to make when measuring O-rings. These include:
Improper tool usage or technique
Using the wrong tools or employing incorrect techniques can lead to inaccurate measurements of o-rings. It is crucial to ensure that the measuring instruments are appropriate for the task at hand and are used correctly. Some common mistakes include:
- Using a worn-out caliper or gauge, which may provide inconsistent readings
- Applying excessive force while measuring, results in distorted dimensions
- Failing to hold the measuring instrument perpendicular to the o-ring surface, leads to skewed measurements
Neglecting to account for compression set or tolerances
One must consider factors such as compression set and tolerances when measuring o-rings. Ignoring these aspects can result in misleading measurements and affect the overall performance of the replacement o ring and the seal. Here are some important points to remember:
- Compression set: Failure to account for the amount of compression an o-ring has undergone can lead to inaccurate measurements. This parameter affects its sealing capabilities.
- Tolerances: O-rings come with specified tolerance ranges, which determine acceptable variations in their dimensions. Neglecting these tolerances during measurement can result in incorrect assessments.
Failing to consider temperature variations
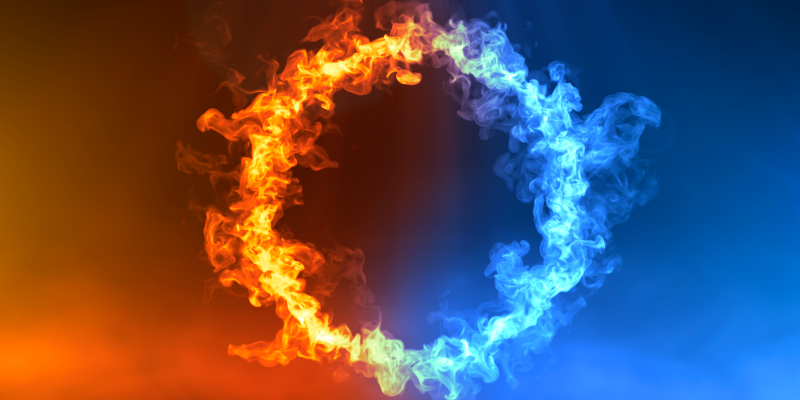
Temperature fluctuations play a significant role in altering o-ring dimensions, making it essential to consider this factor when measuring them. Temperature changes can cause expansion or contraction, affecting both o ring size chart, and shape. Here’s what you need to know:
- Expansion: Higher temperatures cause o-rings to expand, increasing their dimensions.
- Contraction: Conversely, lower temperatures lead to contraction, reducing their size.
- Thermal cycling: Repeated exposure of o-rings to varying temperatures can cause dimensional changes over time.
By avoiding these common mistakes when measuring o-ring dimensions, you can ensure accurate results and maintain optimal performance for your sealing applications.
Factors that Affect O-Ring Sizing
There are several factors that can affect O-ring sizing, including:
- Operating temperature and pressure: The operating temperature and pressure of the system can affect the size of the O-ring. In general, as the temperature and pressure of the system increase, the size of the O-ring also increases to maintain proper sealing.
- Material of construction: The material of construction of the O-ring can affect the size as well. Different materials have different properties, and they require different sizes to ensure proper sealing.
- Environmental conditions: The environmental conditions of a system, such as temperature, pressure, and chemicals, can also affect the size of the O-ring. Different environments may require different sizes to maintain proper sealing.
- Design and application: The design and application of the system can also affect the size of the O-ring. For example, if the system has a specific size or shape constraint, the O-ring will need to be sized accordingly.
- Performance requirements: The performance requirements of the system are an important factor in determining the size of the O-ring. For example, if the system requires precise sealing, the O-ring will need to be made with tighter tolerances, while if the system requires a loose seal, the O-ring will need to be made with looser tolerances.
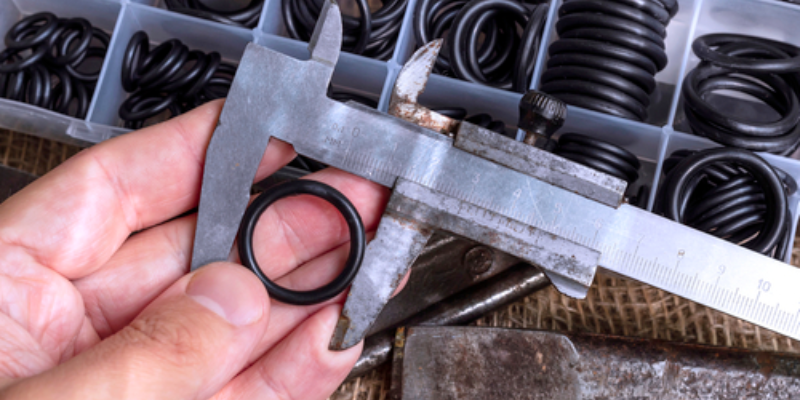
Considering these factors when measuring o-ring dimensions is vital for ensuring optimal performance and reliability. it is essential to take into account all pertinent factors, such as operating temperature and pressure, the material of construction, environment, design and application, and performance requirements.
Remember that each application may have unique requirements sizing o rings for, so consulting with experts or referring to industry standards can further enhance your understanding of o-ring sizing considerations.
Conclusion
In conclusion, accurately measuring the dimensions of o-rings is crucial for the correct size and ensure proper fit and functionality in various applications.
By following these guidelines and implementing best practices for measuring o-rings accurately, you can avoid costly errors and improve overall efficiency in your projects or manufacturing processes.
Get Top-Of-The-Line Products From Hongju
At Hongju Silicone, we manufacture state-of-the-art O-rings. Our wide range includes O-rings of all sizes for various applications. If you have taken your O-ring measurements, send us the dimensions. We will deliver exactly what you ask for. With Hongju, you can achieve business success in no time!
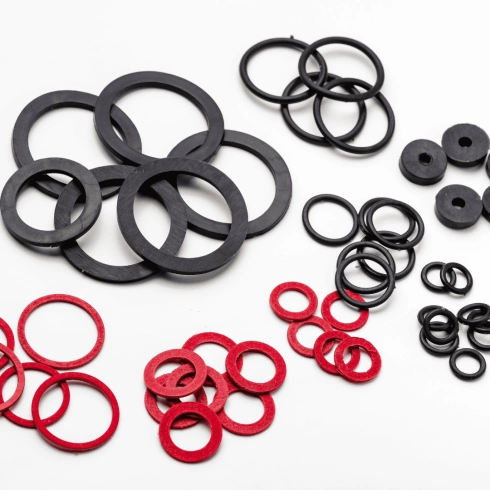
Send Your Inquiry Now!
Quality Meets Affordability. Inquire Now for High-Quality Products at Low Volumes.