It might sound trivial to an outsider, but incorporating the right draft angle can be the difference between a high-quality injection molded part and a defective one. This article delves into the significance of draft angles in the injection molding process and offers insights to ensure a high-quality production process.
Draft Angle Basics
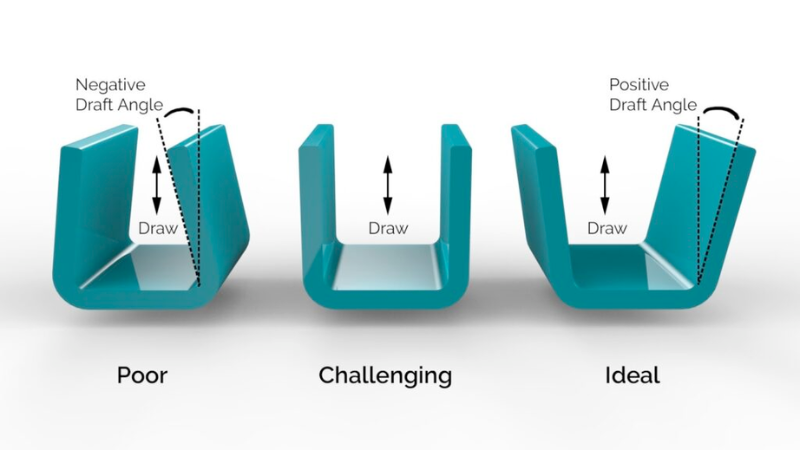
At the heart of the injection molding process lies an elemental design consideration known as the draft angle. For those new to the field, the draft angle might appear as a mere slant or inclination on a part’s vertical surface, but its implications run deep in the world of injection molding.
- Definition
The draft angle, often just referred to as ‘draft’, is the degree of incline given to the vertical walls or surfaces of injection molded parts. Expressed in degrees, this angle ensures that the wider part of the molded product is at the base, allowing for easier ejection from the mold.
- Purpose
The primary purpose of the draft angle is to facilitate the smooth ejection of a part from the mold. Without it, the part can stick or drag against the mold, leading to defects and potential damage both to the part and the mold.
- Ejection & Surface Integrity
A well-integrated draft angle ensures that there’s minimal friction between the part’s vertical surfaces and the mold during ejection. This not only aids in preserving the part’s surface finish but also prevents scuffs, drag marks, or distortions that can compromise the final product’s aesthetics and function.
- Mold Health
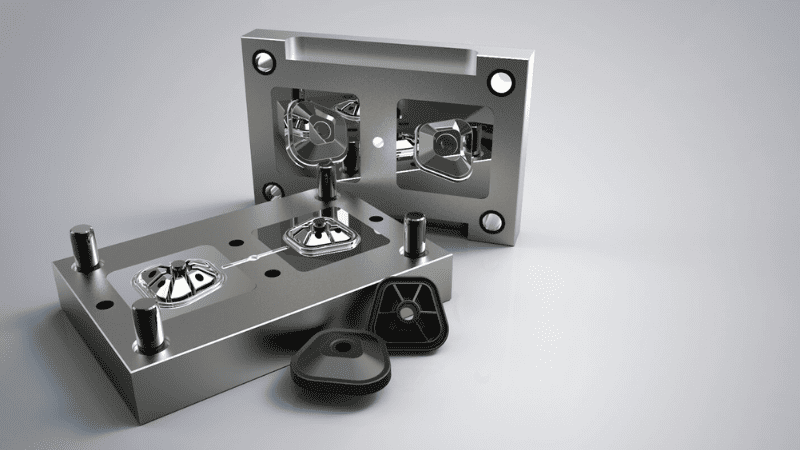
Continually molding and ejecting parts without an adequate draft angle can exert undue stress on one metal mold component, leading to quicker wear and tear. A well-calculated draft, on the other hand, can extend the mold’s operational lifespan, saving time and costs in the long run.
- Design Precision
Beyond the functional benefits, draft angles also play a crucial role in design accuracy. They help in retaining the intended dimensions and geometric accuracy of a part, especially when dealing with complex shapes or intricate designs.
- Aesthetic Appeal
When incorporated thoughtfully, draft angles can also enhance the visual appeal of the injection molded part. They can provide a sleek and ergonomic finish, making the product not just functional but also aesthetically pleasing.
In the grand scheme of plastic injection molding, draft angles are not merely optional—they’re indispensable. They stand as a testament to the intricate balance of art and science in the realm of molding, ensuring that every part ejected from a mold is of optimal quality and durability.
Inquire About Our Silicone and Plastic Products!
Factors Influencing Draft Angle Selection
Several factors come into play when determining the appropriate draft angle for injection molded parts. These factors include part geometry, material properties, surface finish, wall thickness, depth of draw, mold complexity, and tooling limitations. Let’s delve deeper into each of these influences:
- Part Geometry
The shape and design of the part being molded greatly impact the selection of draft angles for injection. Parts with complex geometries or intricate features may require larger draft angles to ensure easy ejection from the mold. On the other hand, parts with simpler designs or straight walls may allow for smaller draft angles. The goal is to strike a balance between ensuring proper ejection during the injection molding process and minimizing any negative impact on the final part’s aesthetics or functionality.
- Material Properties
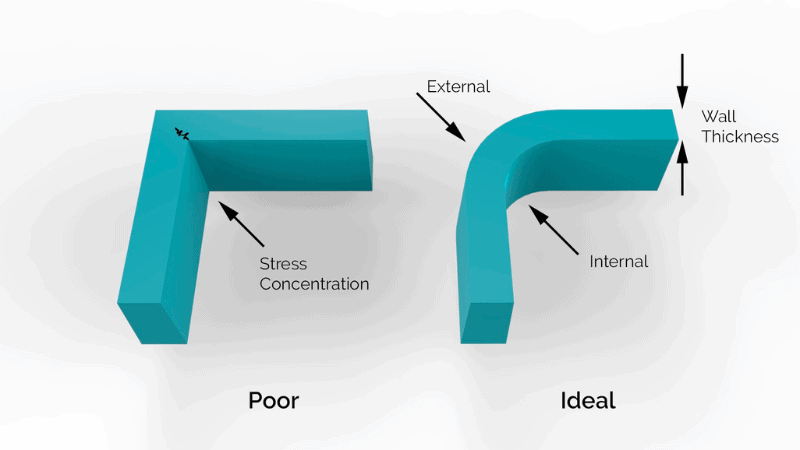
Different materials exhibit varying levels of shrinkage during the cooling process in injection molding. Materials with higher shrinkage rates may necessitate larger draft angles to compensate for potential dimensional changes upon solidification. Conversely, materials with lower shrinkage rates might allow for smaller draft angle injection molding requirements. It is crucial to consider these material properties when selecting appropriate draft angles to achieve accurate and consistent part dimensions.
- Surface Finish
The desired surface finish of the final molded part can also influence the choice of draft angle. Parts requiring a high-quality production process finish often demand larger draft angles to prevent cosmetic defects like scratches or marks caused by friction during ejection. However, parts that will undergo secondary processes like painting or coating can tolerate smaller draft angles since any imperfections will be concealed by subsequent treatments.
- Wall Thickness and Depth of Draw
The wall thickness plays a significant role in determining the required draft angle for successful mold release in the injection molding mold design. Thicker walls generally require larger draft angles due to increased resistance during ejection. Parts with deeper draws (where features extend further into the cavity depth of the mold) may necessitate larger draft angles to accommodate smooth removal from the tooling without damage or distortion.
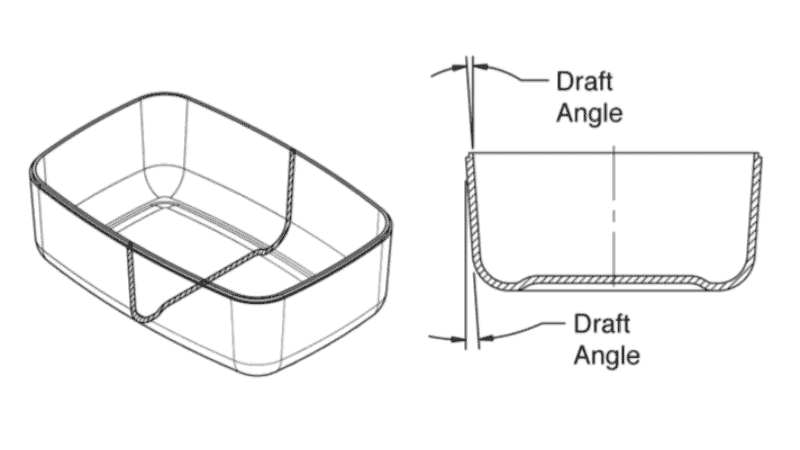
- Mold Complexity and Tooling Limitations
The complexity of the mold design and any limitations imposed by the tooling can also impact draft angle selection in the molding process. More intricate molds with undercuts or complex geometries may demand larger draft angles to facilitate proper ejection. Similarly, certain tooling constraints, such as limited space or restricted movement, might dictate the need for specific draft angles to ensure smooth operation during the injection molding process.
Inquire About Our Silicone and Plastic Products!
General Draft Angle Recommendations
In the realm of injection molding, draft angles serve a crucial role in ensuring the seamless ejection of parts from their molds. While specifics can vary based on material, geometry, and surface finish, industry data and insights suggest the following guidelines:
- Standard Draft Angle: Research from leading injection molding companies supports a 1-2 degree draft angle as optimal for basic, non-complex designs using common plastics. This angle typically ensures an effective balance between easy part ejection and design integrity.
- Textured Surfaces: Industry standards dictate that for parts with a textured finish, an additional 1-3 degrees on top of the basic draft angle is recommended. So, for a light texture, a total draft of 2-3 degrees, and for a heavy texture, 3-5 degrees can be necessary.
- Deep Features: Based on material flow studies, deeper cavities or recessed features benefit from more pronounced draft angles. For recesses deeper than 2 inches, a draft angle of up to 5 degrees might be essential.
- Thin Walls: For parts with wall thicknesses less than 0.04 inches, data suggests a draft angle between 0.5 to 1 degree, as this helps prevent warping caused by differential cooling rates.
- Tall Vertical Features: Industry guidelines recommend adding an incremental 1 degree of draft for every inch in height for tall vertical features, reducing potential friction during part ejection.
- Fine Details: When handling intricate details or engravings, data from successful injection moldings indicates a draft angle of 1.5 to 2.5 degrees. However, consulting with injection molding specialists remains crucial for these nuanced features.
- High Production Runs: For molds expected to produce over 100,000 parts, leaning towards the higher end of the recommended draft angle range can prolong mold life. Historical data has shown a reduction in wear and tool damage with slightly increased draft in high-production scenarios.
While these recommendations are rooted in industry standards and empirical data, it’s paramount to remember that each project has its own unique demands. By combining these guidelines with project-specific insights and expert consultations, one can achieve optimal results in the injection molding process.
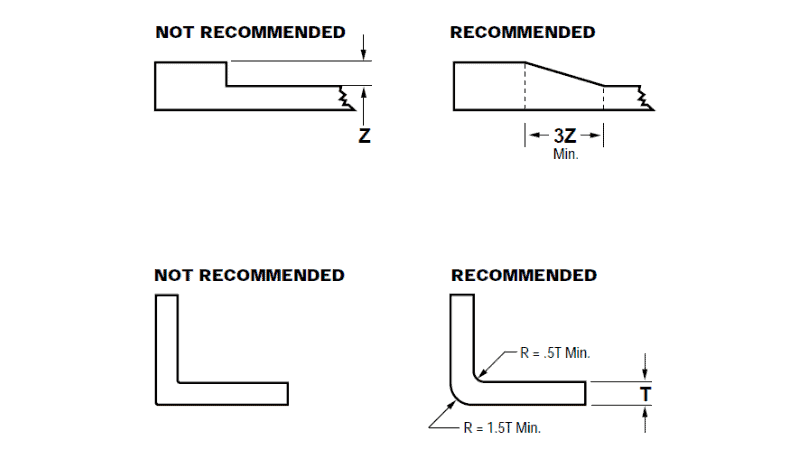
Common Pitfalls and How to Avoid Them
Inadequate Draft Angle
- Pitfall: One of the most prevalent issues in injection molding is not incorporating sufficient draft, leading to parts sticking to the mold. This not only damages the part but also strains the mold.
- Avoidance: Always ensure an adequate draft angle based on the material and design specifics. Consulting with injection molding specialists can provide guidance on the minimum draft angle necessary for a particular part.
Overemphasis on Aesthetics
- Pitfall: While aesthetics are crucial, prioritizing them over functionality can lead to designs that are difficult to eject from the mold.
- Avoidance: Balance aesthetic requirements with practical injection molding design considerations. If a certain aesthetic is essential, consider secondary operations post-molding.
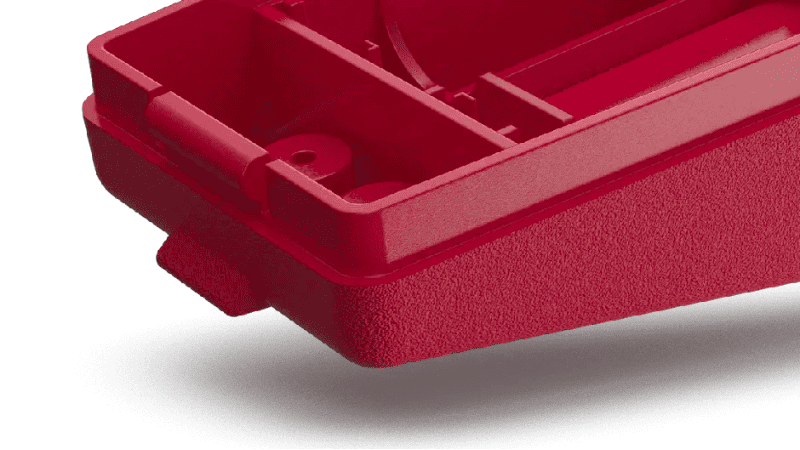
Ignoring Material Shrinkage
- Pitfall: Every material has a specific shrinkage rate in the injection molding process. Not accounting for this can lead to distorted parts.
- Avoidance: Understand the material’s properties, especially its shrinkage rate. Adjust the draft angles accordingly to compensate for this inherent material behavior.
Zero or Negative Drafts without Justification
- Pitfall: While sometimes necessary for specific features, unjustified use of zero or negative drafts can pose ejection problems.
- Avoidance: Only utilize zero draft mold or negative draft angles when absolutely necessary, and ensure that the mold design and injection molding process can support them without complications.
By being aware of these pitfalls and implementing the suggested precautions, you can navigate the challenges of draft angle injection molding and ensure a smoother, high-quality production process.
Inquire About Our Silicone and Plastic Products!
Draft Angles for Specific Features
When talking about draft angles in plastic injection molding, it’s important to know how different parts work with these angles. Each feature needs its own draft angle to make sure the mold can release the part without causing any harm. Here’s more about it:
Ribs
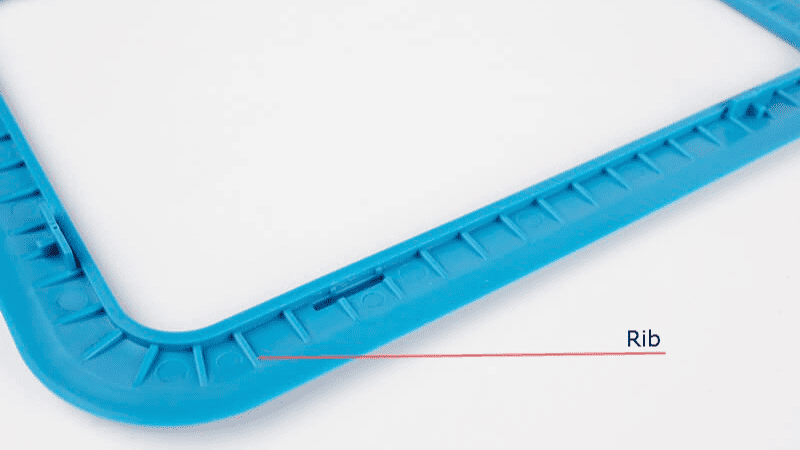
When designing ribs for injection molding, it is crucial to consider the draft angles. Ribs are thin, elongated features that provide additional strength and support to a part. To ensure easy removal from the mold cavity, ribs should have a minimum 1° per side taper. This slight angle allows the rib to release smoothly without getting stuck in the mold.
However, there may be cases where achieving sufficient rib taper becomes challenging due to design constraints. In such situations, increasing the rib thickness can help compensate for the lack of taper. By adjusting the thickness, you can maintain proper functionality while still ensuring easy ejection from the mold.
Pros:
- Facilitates smooth release of ribs from the mold cavity.
- Increases ease of manufacturing and reduces production issues.
Cons:
- Increased rib thickness may affect overall part design and aesthetics.
- May require adjustments in other areas of the part geometry to accommodate thicker ribs.
Holes
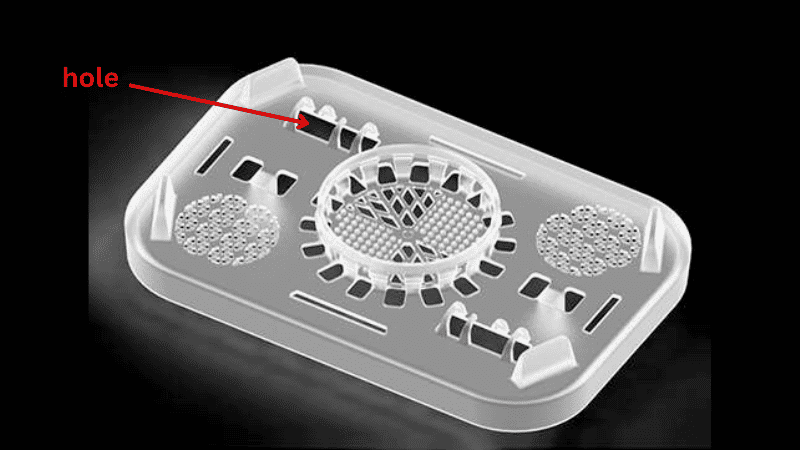
The treatment of holes in injection molding depends on their shape and geometry. Cylindrical holes generally do not require any additional draft angle since they have a uniform diameter throughout. However, non-cylindrical holes, such as those with tapered or irregular shapes, may necessitate adding draft angles to facilitate ejection from the mold.
Including draft angles on non-cylindrical holes allows for easier removal by providing a gradual release during demolding. These angles reduce friction between the part and mold surfaces, preventing damage or distortion when extracting the part from the tooling.
Pros:
- Enhances ease of part removal from molds with non-cylindrical holes.
- Minimizes potential damage or distortion during the demolding process.
Cons:
- Adding draft angles to complex geometries may increase manufacturing costs.
- Requires careful consideration during product design to avoid compromising functionality or aesthetics.
Threads
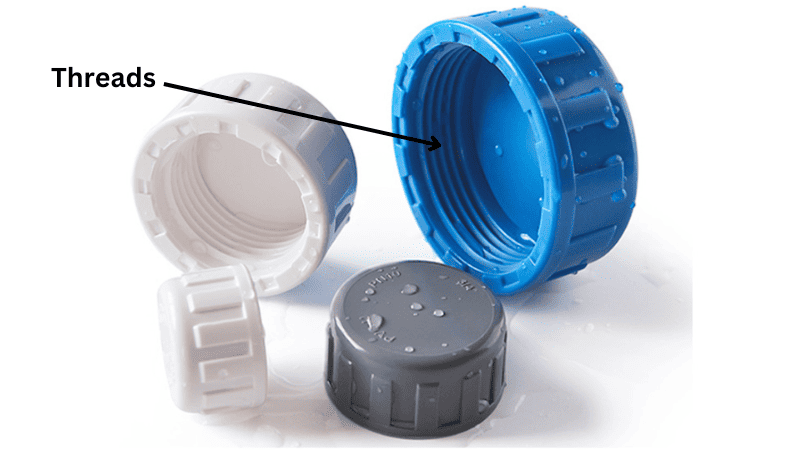
Threads are commonly found in plastic parts used for fastening or joining components. When designing parts with external threads, it is recommended to incorporate a draft angle of 1° to 3°. This slight taper allows for smooth release from the mold, preventing any potential sticking or binding issues.
On the other hand, internal threads may not always require draft angles if the mold can be designed with collapsible cores. Collapsible cores are specialized features that enable the creation of internal threads without the need for additional draft angles. These cores collapse during ejection, allowing for easy removal of the threaded part.
Pros:
- Ensures smooth release and functionality of parts with external threads.
- Eliminates the need for draft angles on internal threads when using collapsible cores.
Cons:
- Incorporating draft angles on external threads may slightly alter their dimensions.
- Designing molds with collapsible cores can increase manufacturing complexity and costs.
Best Practices for Draft Angles in Plastic Injection Molding
Ensuring a successful plastic injection molding process requires a meticulous approach, especially when it comes to designing draft angles. Their importance cannot be overstated, given their influence on both mold release actions and the overall performance of injection molded parts.
1. Consultation is Key
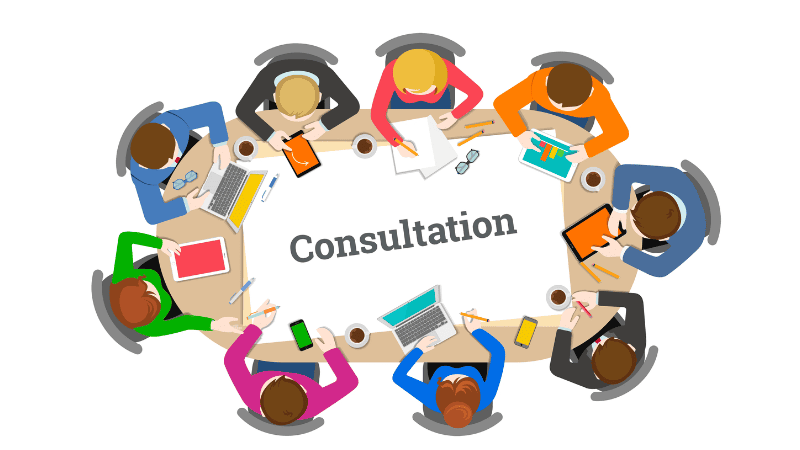
Leverage the wisdom of experienced mold designers. With their vast expertise, these specialists offer invaluable insights, guiding you to draft angle injection molding practices that yield premium plastic parts. Their familiarity with various design challenges helps in recommending precise draft angles tailored to specific mold designs.
Inquire About Our Silicone and Plastic Products!
2. The Value of Prototyping
Before plunging into large-scale manufacturing, test the waters with prototyping. This phase is your proving ground, enabling the validation of selected draft angles. It’s also your safeguard, revealing any hitches that might emerge during the full-blown injection molding process.
Through iterative prototyping, you can refine those draft angles, inching closer to that perfect mold. While at it, keenly observe part ejection dynamics, scrutinize the quality of the surface finish, ensure dimensional fidelity, and assess the overall functionality of the part. Such diligent evaluation aids in preemptive corrections, ensuring the final output aligns seamlessly with your stipulations.
3. Harnessing Digital Forethought
Modern problems require modern solutions. Enter computer simulations, your window to foresee how the molten plastic navigates the mold cavity. These digital previews are adept at spotlighting regions where the current draft might falter during part ejection.
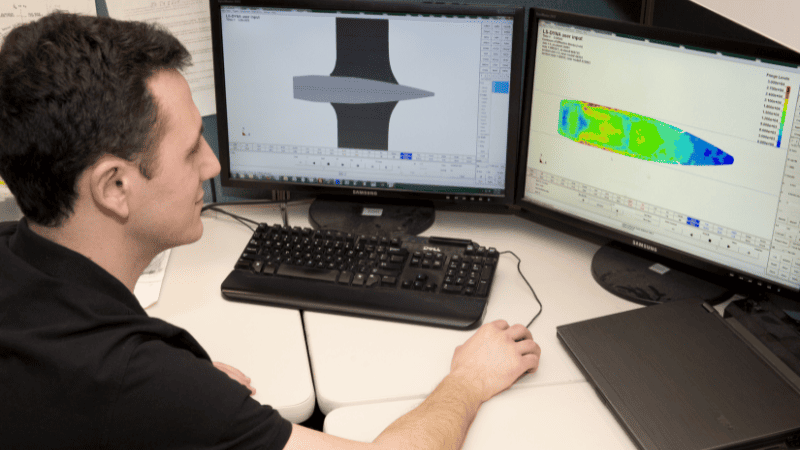
By integrating these simulations early in your design process, you can pinpoint potential snags, be it undercuts or friction zones, that could disrupt the smooth release from the mold. Amending these in the virtual realm translates to tangible gains in the real world—accelerating design timelines, curtailing prototyping expenses, and diminishing the prospect of hiccups during the actual molding process.
Conclusion
Draft angles are pivotal in the injection molding process, influencing part ejection and overall product quality. They cater to the nuances of different features and designs, ensuring smooth manufacturing outcomes. By grasping their significance and adhering to best practices, designers can achieve optimal results. Collaborating with injection molding specialists and employing advanced simulations can further streamline production, ensuring efficiency and excellence.
Unlock the Full Potential of Injection Molding with Hongju!
Navigating the intricacies of draft angles can be daunting, but you don’t have to go it alone. At Hongju, our injection molding specialists bring unparalleled expertise to every project. Dive deep into the world of precision molding with us and ensure that each part you produce stands out in quality and functionality.