This article explores the similarities, differences, and applications of injection and compression molding. Kindly read further to make an informed choice.
What is Injection Molding?
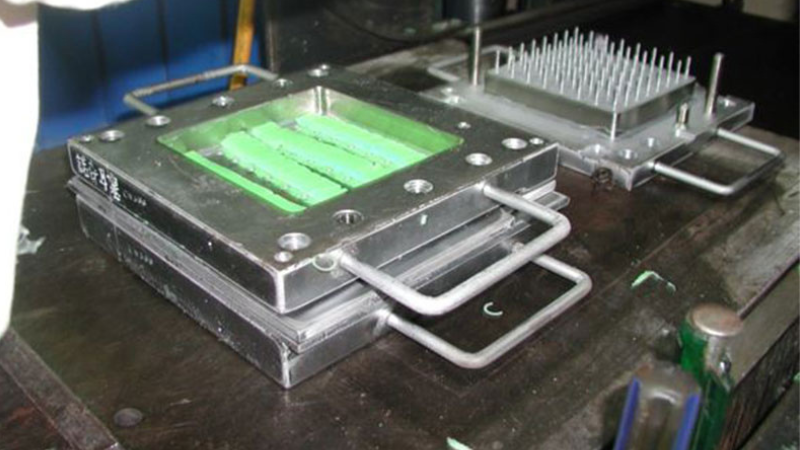
Injection molding is a process that injects molten plastic into a heated mold cavity to form desired parts at high pressures. A screw pulls the raw material into a hopper before it is heated into liquid form and injected into the mold cavity.
The manufactured parts are then allowed to cure before the pins eject them. As a result, the injection molding process is precise, efficient, and suitable for mass-producing complex parts with intricate designs.
Furthermore, the injection molding machine has several parts, including the feed hopper, hydraulic cylinders, injection and clamping units, and heaters. This machine produces a more consistent and accurate product that meets your requirements.
Advantages of Injection Molding
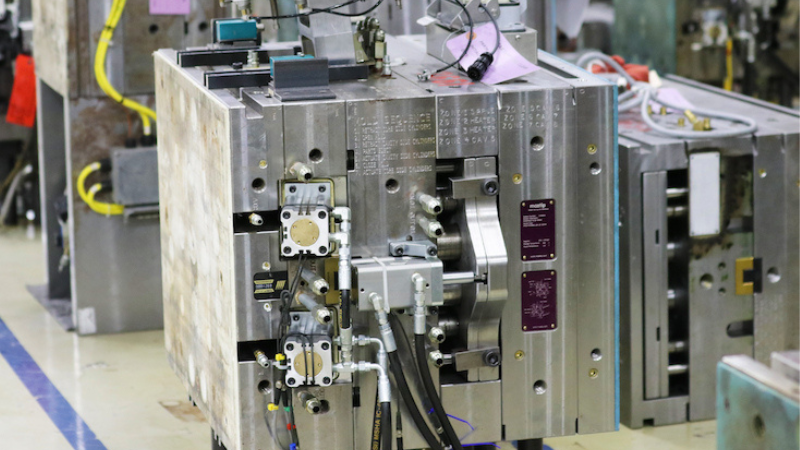
- Rapid cycle times, which results in high volume output and lower production cost
- Excellent precision, especially for complex and intricate parts
- Strong and durable parts
- Tolerates a wide range of raw materials
Disadvantages of Injection Molding
- High cost of mold designs
- Not suited for manufacturing large parts
- Producing a small number of molded products can be quite costly
Applications of Injection Molding
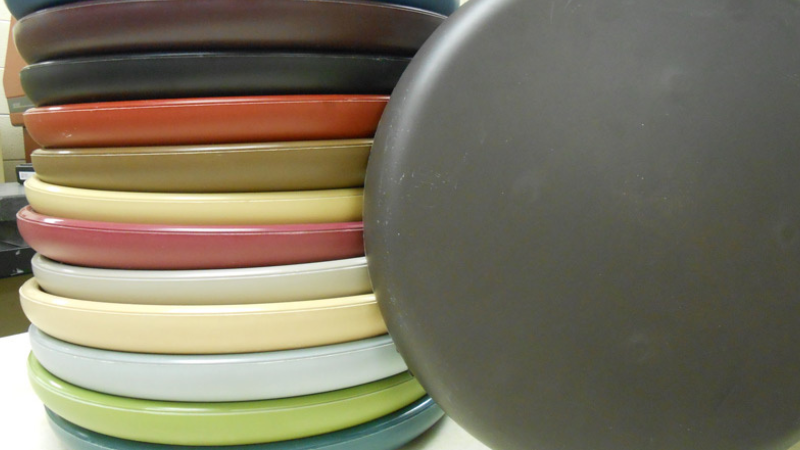
Injection molding can accommodate many materials and is suitable for producing complex parts. Consequently, this molding process is versatile and applicable in manufacturing;
- Automotive products like dashboard components, dials, and switches
- Computer and consumer electronics
- Window and door components
- Engineering prototypes
- Kitchenware
- Plastic bottles
- Packaging for food and beverages
- Cable assemblies
- Medical and dental devices that are resistant to bacteria and corrosion
What is Compression Molding?
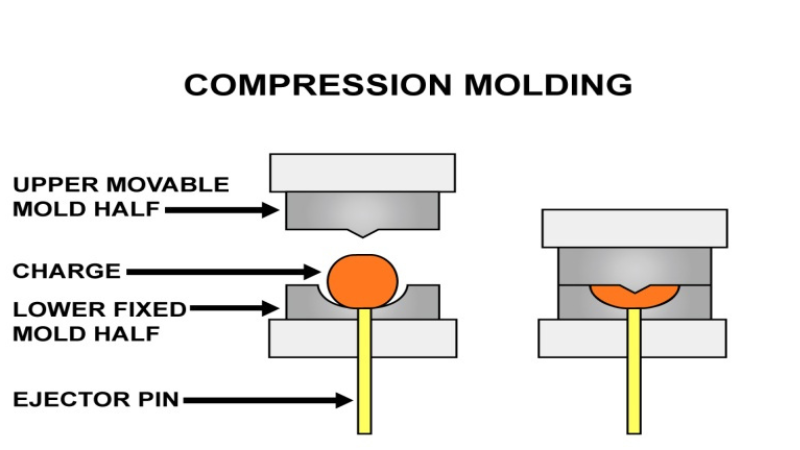
Unlike injection molding, compression molding heats and compresses a plastic material into its desired shape in the same mold. A compression molding machine has two parts – the upper and lower compression molds. While the lower half is stationary, the upper half is movable.
During the process, the lower mold is preheated before placing the plastic. After closing the mold, it presses the melted plastic and cures it. You can then remove your final product once it is cooled.
Advantages of Compression Molding
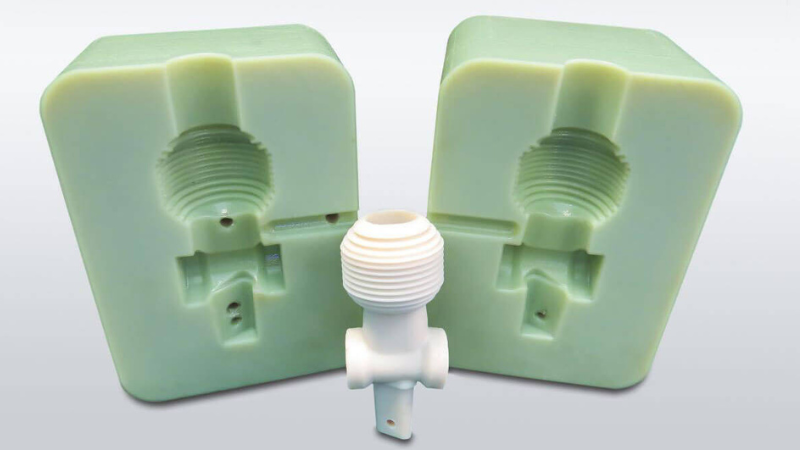
- The process is suitable for small production, which results in lower cost
- Compression molding is excellent for manufacturing products if varying thicknesses and lengths
- The process produces minimal waste
- The end products are sturdy and resilient
- The compression molding process preserves your raw material’s chemical and mechanical properties.
Disadvantages of Compression Molding
- Slower production time
- The process cannot produce complex parts
- The end products are not as consistent compared to injection molding
- Compression molding is not ideal for large-volume productions
- The end products may need extra processing to remove the overflow
- The final product may likely have an odd line in its middle because the mold has two parts
Applications of Compression Molding
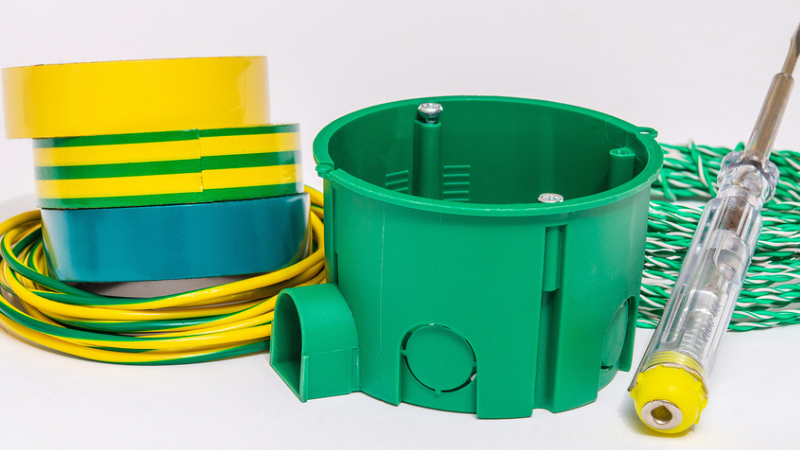
Compression molding is suitable for producing durable and robust parts. This process is therefore applicable in;
- Automotive parts
- Electronic components
- Circuit breakers
- Clothing fasteners
- Plastic dinnerware
- Body armor
Common Traits Between Compression Molding and Injection Molding
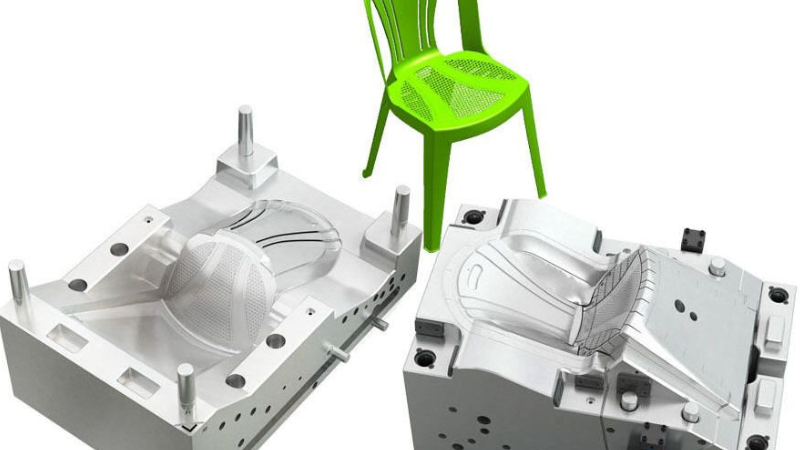
Although compression molding and injection molding have significant differences, they are alike in some ways. The table below summarizes the common traits between compression and injection molding.
Material | The two processes use plastic as raw material |
Custom color | You can create custom-colored plastic resins with both processes |
Conditions | Although they use different mechanisms, injection, and compression molding processes use heat and pressure to create end products. |
Differences Between Compression Molding and Injection Molding
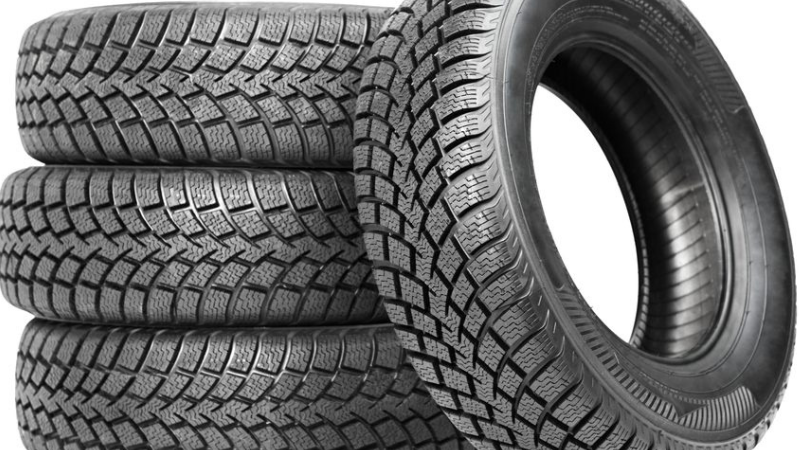
Compression molding | Injection molding | |
Material | The process uses flexible elastomers, thermosets, and sheet molding compound (SMC) | Rigid thermoplastics, urethanes, and elastomers are the standard raw materials in this process. |
Product size | The final products are usually large and have varying thicknesses | The process is suitable for smaller products with tight tolerances |
Production time | The compression molding process is slow and results in a longer cycle time | The process is faster |
Production capacity | Low-volume production | High-volume production |
Process | A straightforward process with fewer components. The process only needs a raw material, a heated mold, and an upper plug. | More components are needed in the process |
Precision | Not as precise. There is a need for post-processing to remove overflow on final products. | Precise. The process creates end products of consistent shapes |
Model complexity | The process creates simple products with less-sophisticated components | The process is suitable for manufacturing complex designs |
Injection Moulding VS. Compression Moulding: Which is Better for You
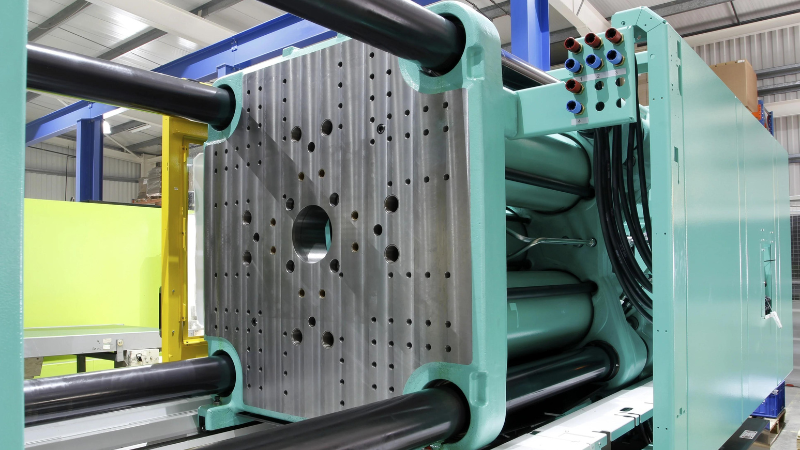
The choice of a suitable rubber molding process depends on your application, the cycle time, and product complexity.
If you want to manufacture products for complex parts quickly, injection molding is ideal. And if your application requires simple products, compression molding may be excellent.
Nevertheless, before choosing a suitable molding process, you can discuss the details of your application with your manufacturer.
FAQs about Injection Moulding and Compression Moulding
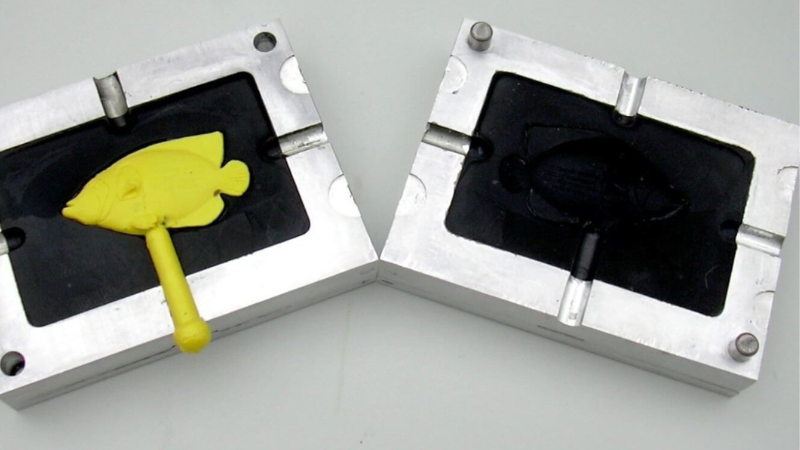
Why is Injection Molding Preferred?
Injection molding is the preferred manufacturing process because it allows the high-volume production of complex parts. The process is also highly efficient and is compatible with a wide range of plastic and thermoplastic material. Furthermore, there is minimal waste and a faster cycle time, which saves you money.
What Can Plastics Go through Compression Molding?
Thermoplastics and thermosets are raw materials that can go through compression molding. These plastics are flexible and can be easily molded into desired parts. Furthermore, sheet molding compound (SMC) and bulk molding compound (BMC) can also be compression molded.
BMC and SMC are reinforced resin mixtures suitable for producing parts with excellent tensile and flexural strength.
What are the Main Parts of the Injection Mold?
The main parts of an injection molding machine are the base, hopper, clamping unit, and barrel. Although these are the main parts, the device has other smaller parts, like the ejector pins, injection unit, and split mold, for a smooth-running process.
What are the Alternatives to Injection Molding?
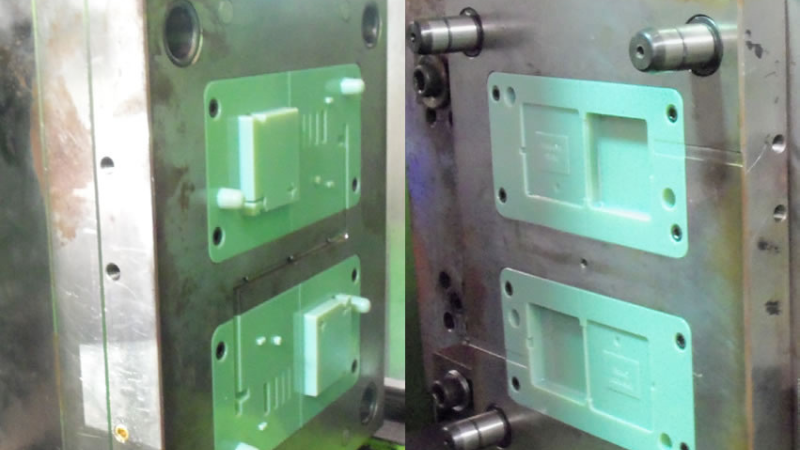
There are several alternatives to injection molding for producing high-quality parts. These alternatives include 3D printing, blow molding, extrusion, thermoforming, and rotational molding.
- 3D printing
3D printing creates parts by printing layer upon layer of material, while injection molding uses a mold to create a desired part out of molten material. Although both methods are ideal for creating complex designs, injection molding has minimal wastage and is suitable for high-volume production.
3D printing, on the other hand, has a slower cycle time but a faster setup.
- Blow molding
Blow molding is a high-volume production molding process. Although this process is suitable for most thermoplastics, it is used explicitly in molding hollow products like bottles and beakers. In contrast, injection molding is used to mold solid parts.
- Extrusion
Extrusion is a comparatively new plastic molding process. Both extrusion and injection molding inject molten material through a machine to mass-produce parts. However, unlike injection molding, extrusion is only suitable for creating two-dimensional products. In addition, extruded products are not as strong are injection-molded details.
- Thermoforming
Thermoforming and injection molding are repeatable processes that produce high-quality parts from thermoplastic materials. The difference between these two methods is that thermoforming molds a heated flat sheet of plastic using suction and pressure, while injection molding injects molten plastic into a mold.
- Rotational molding
Injection molding and rotational molding use preheated plastic injected into a mold. The difference, however, is that rotational molding rotates the mold on two axes in an over to create a uniform coating of the molten plastic.
What is an Alternative to Injection Molding and Compression Molding?
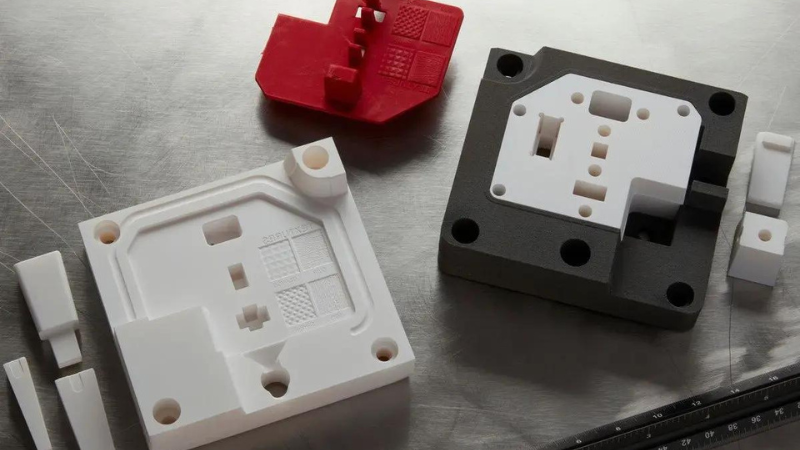
Transfer molding is similar to both injection and compression molding. However, the process combines the characteristics of both methods to produce high-quality consumer products with better design flexibility. Transfer molding involves pressure forcing the raw material into an enclosed mold.
Compared to compression molding, transfer molding uses an enclosed mold. And compared to injection molding, the process uses higher pressures.
Conclusion
Injection molding and compression molding are plastic manufacturing processes that produce different results. Although similar, these processes differ significantly. Nevertheless, you must consider your application and the cost before choosing one.
Generally, injection molding has a higher upfront cost compared to compression molding. However, injection molding is cost-effective in the long run due to high-volume production, shorter cycle time, and the production of complex parts.
Hongju – Your One-Stop Custom-Molded Rubber Products Manufacturer
Hongju is a leading manufacturer in the rubber industry. We offer custom-molded products at fast turnaround times and competitive prices. Our process is simple, effective, and dedicated to providing value to our customers.
We also have efficient compression and injection molding capabilities – we create swimming caps, rubber grommets, o-rings, and gaskets from silicone and other elastomers.
Contact us today for your rubber molding needs.