Recognizing these common injection molding defects, discerning their origins, and identifying solutions are pivotal for producing high-caliber molded components. In this discourse, we’ll explore some pressing issues inherent in plastic injection molding and elucidate their potential remedies.
We hope these tips help you tackle your own challenges. Now, let’s dive deeper.
Defect 1: Cracking
Cracking stands out as a prevalent issue in the realm of injection molding. It manifests as visible lines or fissures, either on the surface or within the body of the injection molded parts. This blemish not only affects the appearance of the product but also raises concerns about its durability and effectiveness.
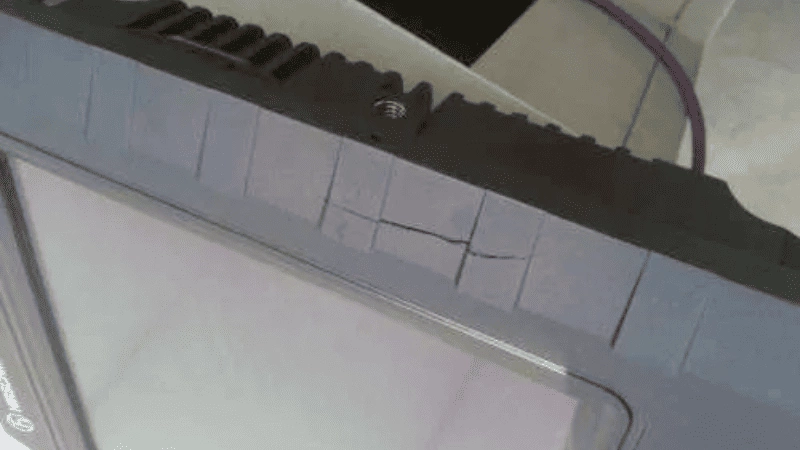
Causes of Cracking in Injection Molded Parts
Cracking can originate from various aspects of the injection molding process:
- Injection Speed and Pressure: A rapid injection speed or excessive injection pressure might result in the molten plastic material setting prematurely, paving the way for cracks.
- Material Flow: An inconsistent flow of molten plastic material due to blockages or impediments can induce internal stresses, leading to cracks.
- Mold Temperature Imbalances: Disparities in mold temperature can cause differential cooling rates, which in turn can instigate cracks.
- Non-Uniform Wall Thickness: Uneven wall thickness can introduce stress variations in the component, making some areas more susceptible to cracking.
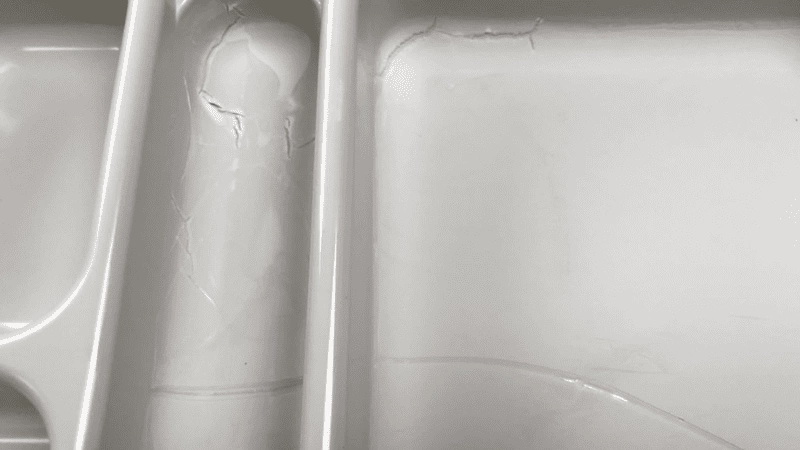
Impact of Cracking on Structural Integrity and Functionality
The repercussions of cracks in injection molded components can be detrimental:
- Compromised Strength: The presence of cracks means the part has inherent weak points, potentially reducing its overall strength and life span.
- Functional Failures: For components that must retain fluids or other substances, cracks could lead to leaks or total part failure.
- Aesthetic Shortcomings: Cracks mar the surface appearance, potentially reducing the commercial appeal and perceived value of the product.
Techniques to Prevent Cracking
To combat the occurrence of cracks in the injection molding process, manufacturers can adopt several strategies:
- Material Selection: Opting for materials with superior mechanical properties and inherent flexibility can deter crack formation.
- Optimizing Mold Design: A well-thought-out mold design, with uniform wall thickness and smooth transitions, can distribute stress evenly and avert cracks.
- Regulating Mold Temperature: Achieving and maintaining a consistent mold temperature is pivotal in ensuring even cooling and solidification, thereby eliminating conditions conducive to cracking.
- Calibrated Injection Parameters: Setting the right balance in injection speed and pressure can help ensure a seamless flow and settling of the molten plastic, preventing premature hardening that can lead to cracks.
Defect 2: Underfilling
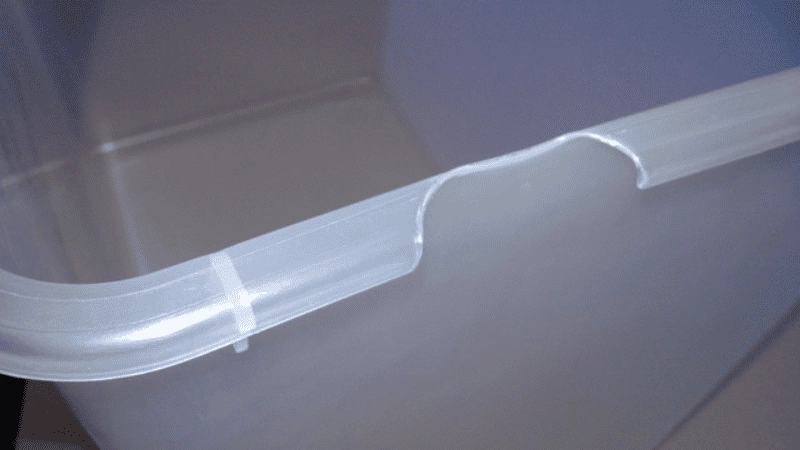
Underfilling, often recognized in the industry as “short shots,” occurs when a molded part doesn’t completely fill with molten plastic material, resulting in parts that are partially formed or missing certain features.
This defect not only diminishes the aesthetic appeal of the part but can also affect its functionality, depending on the severity and location of the underfill.
Causes of Underfilling in Injection Molded Parts
Underfilling can arise from several issues in the injection molding process:
- Insufficient Injection Speed or Pressure: If the injection speed and pressure are too low, the molten plastic may not reach all sections of the mold before solidifying.
- Material Viscosity: High viscosity of the plastic material can impede its flow, preventing it from filling intricate mold features.
- Blocked or Inadequate Gates: Gates guide the molten plastic into the mold cavity. Any obstruction or suboptimal size can limit the flow, leading to underfilling.
- Improper Mold Temperature: Too low a mold temperature can cause the molten material to solidify prematurely, preventing complete cavity filling.
- Inadequate Venting: Entrapped air or gases can block the material flow, leading to pockets of underfill.
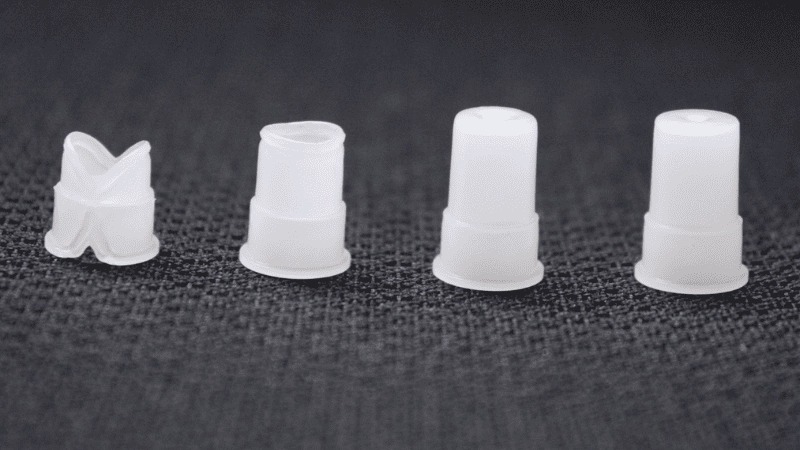
Impact of Underfilling on Structural Integrity and Functionality
The implications of underfilling are far-reaching:
- Structural Weakness: Incomplete parts may lack necessary support structures, reducing their strength and stability.
- Functional Inadequacy: Underfilled parts might not perform as intended, especially if critical features or sections are missing.
- Cosmetic Flaws: Underfilled areas are easily detectable and mar the visual quality of the finished product.
Inquire About Our Silicone and Plastic Products!
Techniques to Prevent Underfilling
Addressing underfilling requires a combination of design refinement and process optimization:
- Enhancing Injection Parameters: Adjusting the injection speed and pressure to ensure complete, rapid mold filling can mitigate underfilling risks.
- Mold Design Reevaluation: Redesigning or optimizing gate locations, sizes, and types can facilitate smoother material flow and more complete filling.
- Material Selection: Choosing a plastic material with suitable flow characteristics for the mold’s intricacies can reduce the chances of underfilling.
- Vent Placement: Strategically placing vents can help release trapped air or gases, ensuring uninterrupted flow of the molten plastic into the mold cavity.
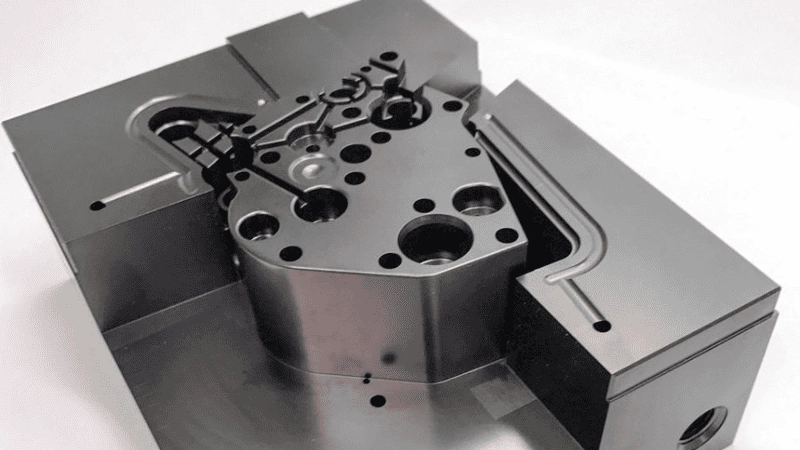
Defect 3: Sticky Mold
Sticky mold, commonly termed “sticking” or “adhesion,” refers to a scenario where the injection molded part adheres too strongly to the mold walls, causing difficulty in ejection.
This phenomenon not only disrupts the manufacturing process, making it less efficient, but also risks damaging the molded component or the mold itself.
Causes of Sticky Mold in Injection Molded Parts
Several factors within the injection molding process can lead to the sticky mold issue:
Inquire About Our Silicone and Plastic Products!
- Inadequate Mold Release Agents: Failing to apply, or uneven application of, mold release agents can cause the molten plastic to adhere more strongly to the mold surface.
- High Mold Temperature: If the mold temperature is excessively high, the plastic may not solidify adequately, leading to increased tackiness and adherence to the mold.
- Improper Cooling Time: Insufficient cooling can leave the plastic in a semi-molten state, increasing its stickiness.
- Rough Mold Surface: Surface imperfections or roughness on the mold walls can increase friction, leading to stronger adherence to the plastic material.
- Inadequate Ejection Mechanism: Weak or uneven ejection forces can fail to overcome the adhesive force between the part and the mold.
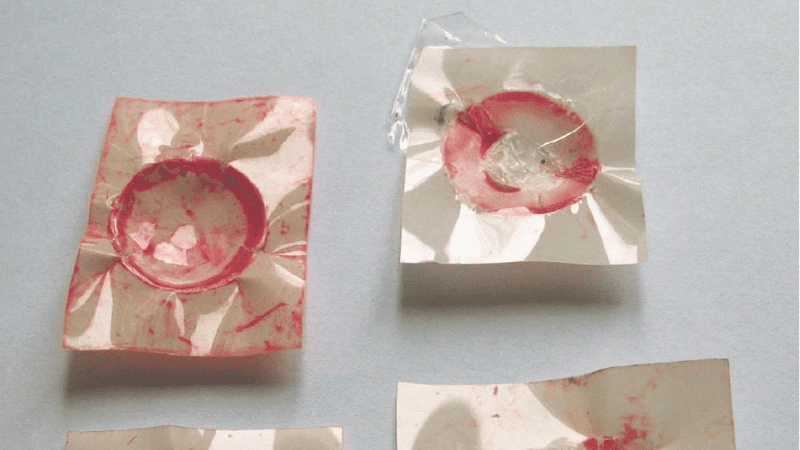
Impact of Sticky Mold on Structural Integrity and Functionality
The repercussions of sticky mold can be detrimental:
- Damaged Parts: Difficulty in ejection might lead to deformed, stretched, or even broken components.
- Extended Cycle Time: Increased time and effort to remove the part from the mold slows down the entire production process.
- Mold Wear: Persistent sticking can cause wear or damage to the mold over time, especially if forceful methods are employed for part removal.
Techniques to Prevent Sticky Mold
Addressing sticky mold necessitates both mold care and process adjustments:
- Utilize Effective Mold Release Agents: Regular and even application of high-quality mold release agents can greatly reduce the chances of sticking.
- Optimize Mold Temperature: Regulating the mold temperature to be within recommended ranges for the specific plastic material in use can ensure better solidification and easier release.
Inquire About Our Silicone and Plastic Products!
- Refine Ejection Mechanism: Ensuring that the ejection pins or plates apply uniform and adequate force can facilitate smooth part release.
- Mold Surface Treatment: Polishing or treating the mold surface to reduce roughness can minimize the friction between the molten plastic and mold walls, reducing sticking.
- Adjust Cooling Time: Properly calibrated cooling times based on material and part thickness ensure that the part is solid enough for ejection without adhering too strongly to the mold.
Defect 4: Shrinkage Pit
Shrinkage pits, commonly referred to as “sink marks,” are depressions or dimples that appear on the surface or sometimes internally within injection molded parts.
They arise from differential cooling rates in varying thickness areas of the part. These defects can severely impact the aesthetic appeal, structural integrity, and function of molded components.
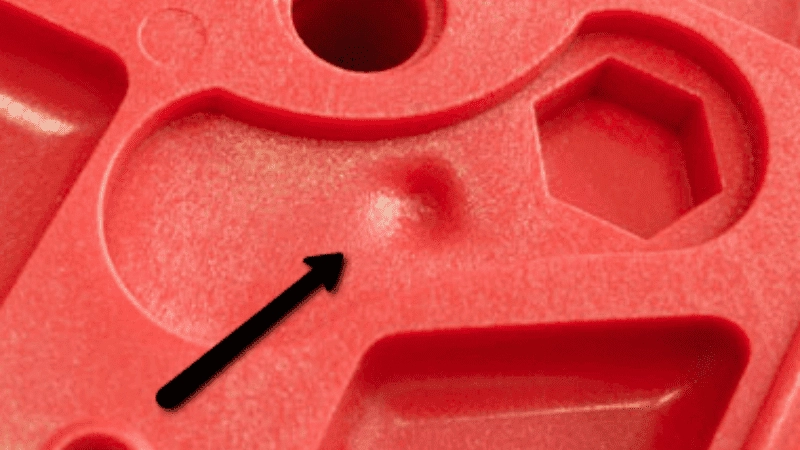
Causes of Shrinkage Pits in Injection Molded Parts
The emergence of shrinkage pits can be attributed to multiple factors in the injection molding process:
- Differential Cooling Rates: Thick sections of a part cool more slowly than thinner areas, leading to volume contraction, which results in pits.
- Insufficient Packing Pressure: If the molten plastic isn’t adequately packed into the mold cavity, it can leave spaces that manifest as pits once the part cools and solidifies.
- Inadequate Venting: Poor venting can trap air or volatile substances in the mold, causing depressions as the plastic contracts.
- Material Choice: Some plastic materials are more prone to shrinkage than others, depending on their molecular structure and cooling characteristics.
- High Mold Temperature: An elevated mold temperature can cause the plastic to remain in a semi-molten state longer, increasing the chance of shrinkage as it cools.
Inquire About Our Silicone and Plastic Products!
Impact of Shrinkage Pits on Structural Integrity and Functionality
The effects of shrinkage pits can be multifaceted:
- Aesthetic Compromise: Pits and depressions can mar the visual appeal of a product, especially for consumer-facing components.
- Structural Weakness: Shrinkage pits can act as stress concentrators, making the part more susceptible to cracks or breaks under load.
- Functional Impairment: For parts with precise functional requirements, pits can cause misalignment, improper fits, or other functional failures.
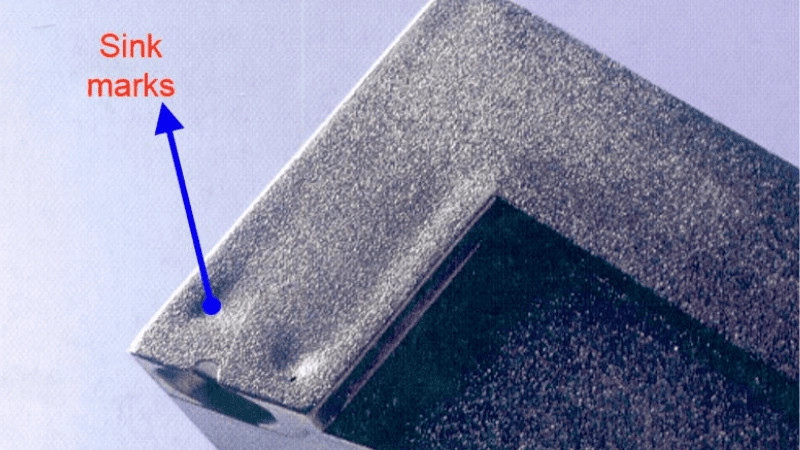
Techniques to Prevent Shrinkage Pits
To mitigate the occurrence of shrinkage pits, certain strategies and best practices can be implemented:
- Mold Design Optimization: Ensure uniform wall thickness in part design to promote even cooling. Using ribs or gussets can help maintain strength without creating thick sections.
- Adjust Packing Pressure: Modulating the injection pressure, especially during the packing phase, can ensure that the mold cavity fills, reducing the chances of volume deficits leading to pits.
- Venting Improvement: Adequate and strategically placed vents can help eliminate trapped air or volatiles, preventing pit formation.
- Material Selection: Choose plastic materials with low inherent shrinkage rates or those known for uniform cooling characteristics.
- Regulate Mold Temperature: Maintaining a consistent and optimal mold temperature ensures that the molten plastic solidifies uniformly, reducing the risk of shrinkage pits.
Inquire About Our Silicone and Plastic Products!
Defect 5: Overflow Edge
Overflow edge, also known as “flash,” is an unwanted excess of material that extends beyond the intended boundaries of an injection-molded part. This thin layer of plastic forms in the spaces between mold parts or along ejector pin locations and can mar the appearance and function of the final product.
Causes of Overflow Edge in Injection Molded Parts
Several factors can give rise to the overflow edge in the injection molding process:
- Excessive Injection Pressure: When the injection pressure is too high, molten plastic can be forced into unintended areas, leading to flash.
- Inaccurate Mold Clamping: If the two halves of the mold aren’t clamped together securely or uniformly, spaces may emerge, allowing the plastic to seep through.
- Worn or Damaged Molds: Over time and use, molds can undergo wear or damage, causing gaps where molten material can escape.
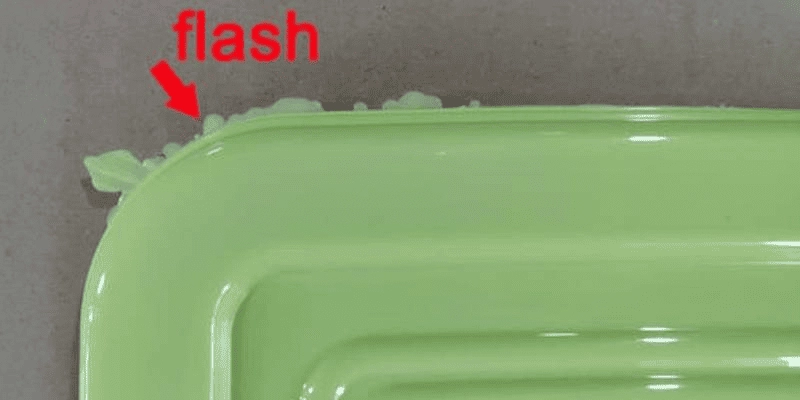
- Elongated Injection Time: Injecting the molten plastic for too long can lead to overfilling the mold cavity, causing flash.
- Inadequate Mold Design: Molds without proper venting or with poorly designed ejector pins can cause overflow edge issues.
Impact of Overflow Edge on Structural Integrity and Functionality
The presence of an overflow edge can have several implications:
- Aesthetic Concerns: Flash can detract from the visual quality of the product, making it look unfinished or flawed.
- Additional Labor and Cost: Removing the overflow edge post-production can add to the manufacturing time and costs.
- Functional Impediments: Excess material at seams or joints can prevent proper assembly or operation of parts or systems.
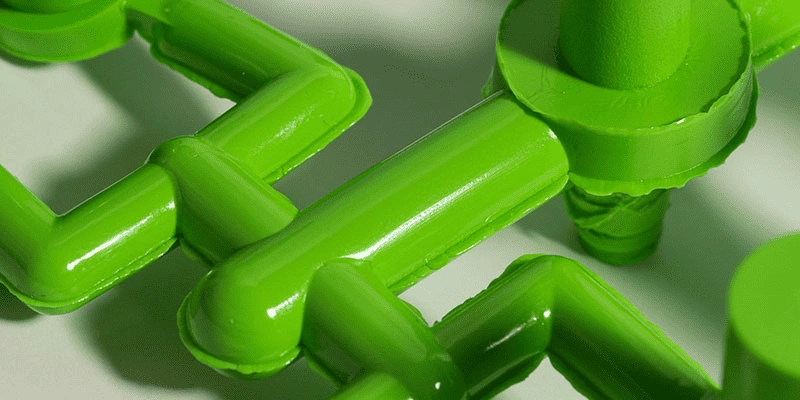
Techniques to Prevent Overflow Edge
To curtail the incidence of overflow edge, consider implementing these solutions:
- Refined Injection Parameters: Adjusting the injection speed and pressure can help in achieving a balanced fill, preventing overflows.
- Mold Maintenance: Regularly inspecting and maintaining molds to address wear and damage can prevent the formation of gaps and flashes.
- Optimized Clamping Mechanism: Ensuring that the mold halves are clamped securely and uniformly will prevent the escape of molten material.
- Improved Mold Design: A well-designed mold with appropriate venting, gate placements, and ejector pin design can minimize the risk of overflow edge.
- Post-molding Operations: Investing in automated trimming or deburring systems can effectively remove flash, ensuring consistent part quality.
Defect 6: Warpage and Deformation
Warpage and deformation are distortions that occur in an injection-molded part, causing it to deviate from its intended shape or design. These defects are especially concerning as they can impact both the aesthetic and functional aspects of the final product.
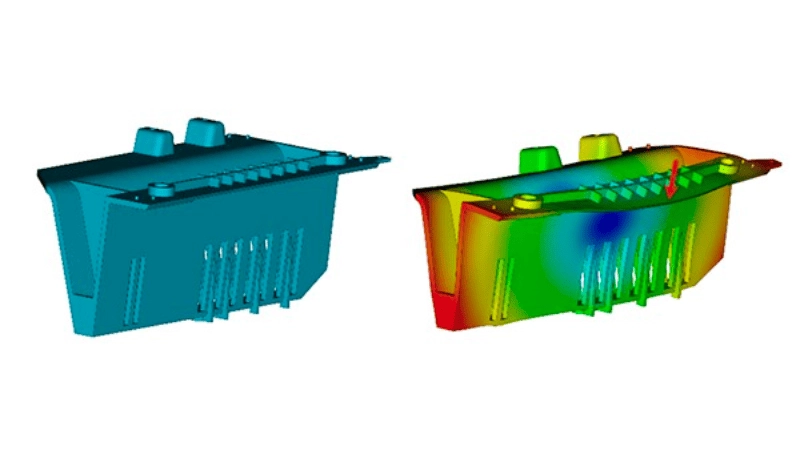
Causes of Warpage and Deformation in Injection Molded Parts
Warpage and deformation can arise due to a multitude of reasons:
- Differential Cooling Rates: Uneven cooling within different sections of a molded part can lead to warpage. Parts that cool faster shrink more rapidly, causing distortions.
- Inconsistent Wall Thickness: Variations in wall thickness can cause uneven shrinkage. Thicker sections will cool and shrink at a different rate from thinner sections.
- Excessive Injection Speed or Pressure: Too much pressure or speed can introduce internal stresses into the part, which manifest as warpage once the part cools.
- Inadequate Material Selection: Some materials have inherently higher shrinkage rates or less dimensional stability than others.
- Mold Temperature Discrepancies: If mold temperatures are not maintained uniformly or optimized for the specific plastic material, it can lead to uneven cooling and subsequent warping.
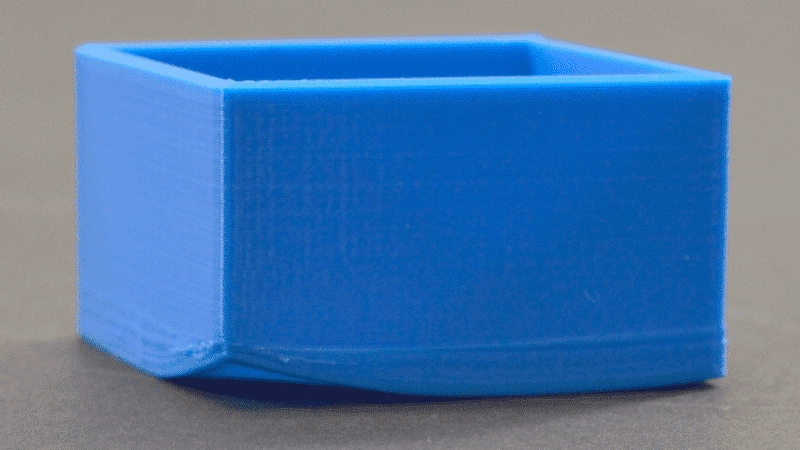
Impact of Warpage and Deformation on Structural Integrity and Functionality
The repercussions of warpage and deformation are manifold:
- Fitment Issues: Deformed parts may not fit or assemble correctly with other components, leading to functional challenges.
- Strength Reduction: Warped parts can have compromised structural integrity and may not bear loads or stresses as intended.
- Visual Imperfections: Deformations can be visually unappealing and may result in increased product rejects or returns.
Techniques to Prevent Warpage and Deformation
Addressing warpage and deformation necessitates a multi-faceted approach:
- Uniform Wall Thickness: Designing parts with consistent wall thickness can promote even cooling and reduce the risk of warpage.
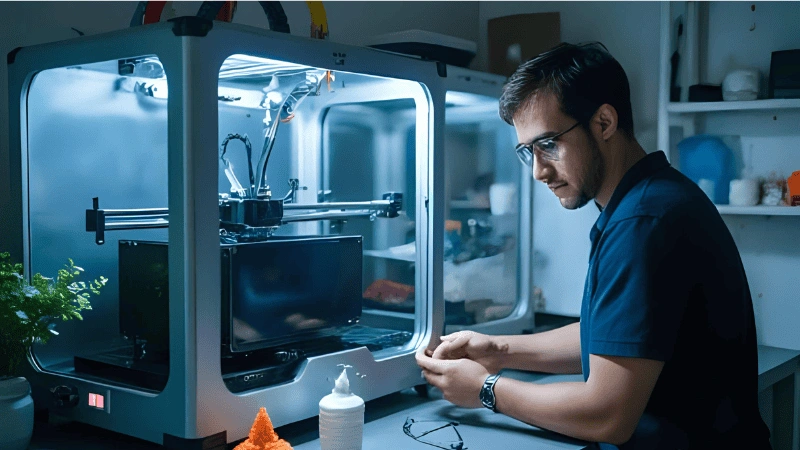
- Mold Temperature Control: Utilizing cooling channels and maintaining a consistent mold temperature will ensure that the part cools uniformly.
- Material Considerations: Opt for materials known for dimensional stability and understand their specific molding requirements.
- Optimized Injection Parameters: Fine-tuning the injection speed, pressure, and hold time can help minimize internal stresses and promote even filling and cooling.
- Post-mold Treatment: In some cases, post-mold treatments, like annealing or conditioning, can be employed to relieve internal stresses and correct minor warpages.
Inquire About Our Silicone and Plastic Products!
Conclusion
Injection molding is a complex yet vital manufacturing process, pivotal for producing high-quality plastic components across numerous industries. Understanding the common defects, from cracking to warpage and deformation, is imperative for any manufacturer aiming to maintain product integrity and satisfy customer requirements.
By recognizing these defects, delving into their causes, and implementing robust monitoring and preventative measures, businesses can ensure a consistent, efficient, and cost-effective production process.
Why Choose Hongju for Your Injection Molding Manufacturing Needs?
Hongju stands out in the realm of injection molding, offering unparalleled expertise and a track record of excellence. With state-of-the-art machinery, seasoned specialists, and a dedication to precision, Hongju guarantees top-tier molded components.
Contact us now and get the right solution for your needs, and improve your business. Choosing Hongju means prioritizing quality, reliability, and industry-leading solutions for all your molding challenges.