By delving into the mechanics behind the structure of an injection mold, we can explore how it influences every aspect of production. So get ready to discover what lies beneath the surface of this essential manufacturing process!
What is an Injection Mold?
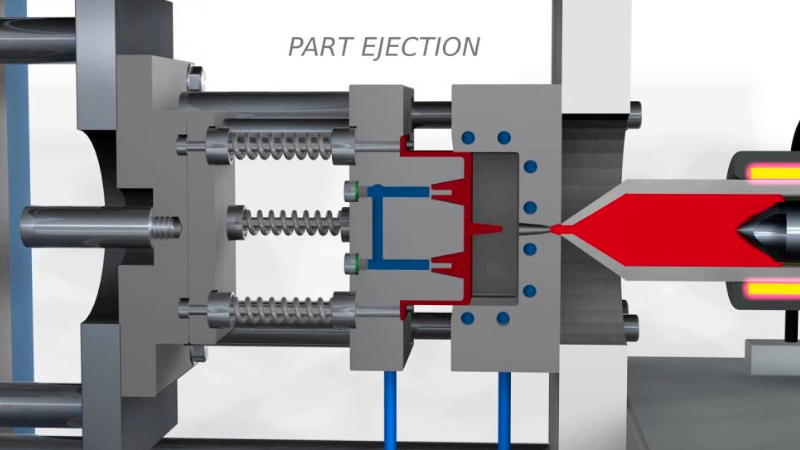
An injection mold refers to a steel or aluminum tool that consists of two main parts: the front mold and the movable mold. These molds are designed with precision to create cavities that match the desired shape of the final product. The front of the plastic injection mold contains an opening called the sprue, which allows for injecting molten plastic and rubber into the cavity.
The purpose of an injection mold is to provide a controlled environment for shaping plastic and rubber materials using high pressure. It ensures that each molded part maintains its intended dimensions and characteristics consistently. By employing precision engineering techniques, such as computer-aided design (CAD), manufacturers can create intricate designs with utmost accuracy.
Exploring the Components of an Injection Mold
Injection molding is a popular way to make plastic parts. The mold used in this process is important for making good quality products. Let’s delve into the main components of an injection mold and understand their significance in the plastic molding process.
Overview of the Main Components
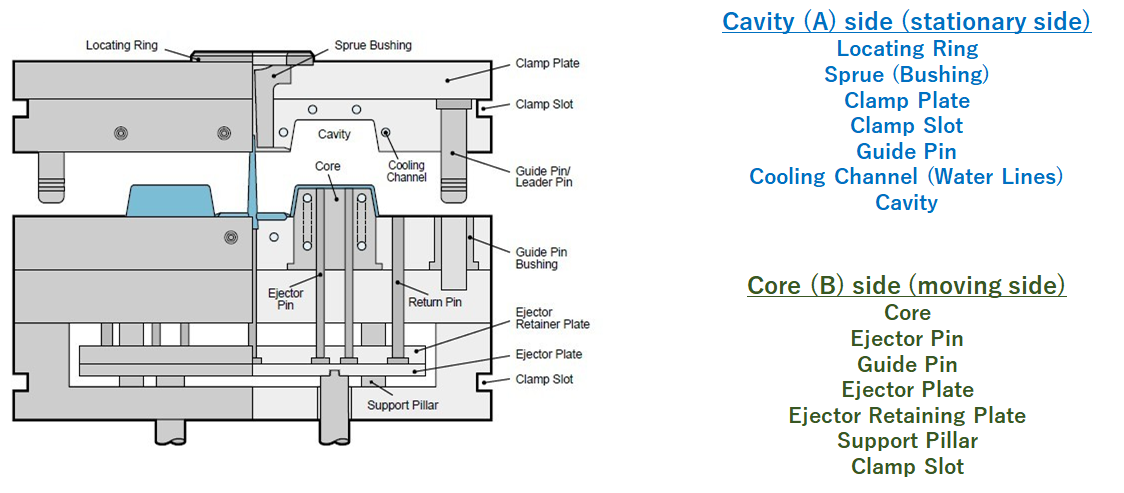
- Cavity: The cavity is responsible for shaping and forming the final plastic part. It is designed to match the desired shape and size of the product being manufactured. The molten plastic material fills the cavity, taking its form and solidifying it into a finished product.
- Core: The core complements the cavity by providing internal features to the molded part. It creates hollow spaces or additional details that cannot be achieved solely with the cavity. Together, the cavity and core define every aspect of the plastic part, ensuring accuracy and precision.
- Runner System: The runner system acts as a channel through which molten plastic flows from the injection machine into the mold cavities. It consists of various components such as nozzles, sprue bushings, and runners that facilitate the proper distribution of plastic material within the mold.
- Cooling System: Effective cooling is essential for maintaining dimensional stability and minimizing cycle time during injection molding. The cooling system comprises channels or passages strategically placed throughout the mold to circulate coolant (usually water) and extract heat from both cavities and cores.
Importance of Each Component in the Molding Process
- The cavity determines how each molded part will look, feel, and function.
- The core enables complex designs by adding internal features like holes or threads.
- The runner system ensures a consistent flow of molten plastic into all cavities.
- The cooling system controls temperature to prevent defects like warping or shrinkage.
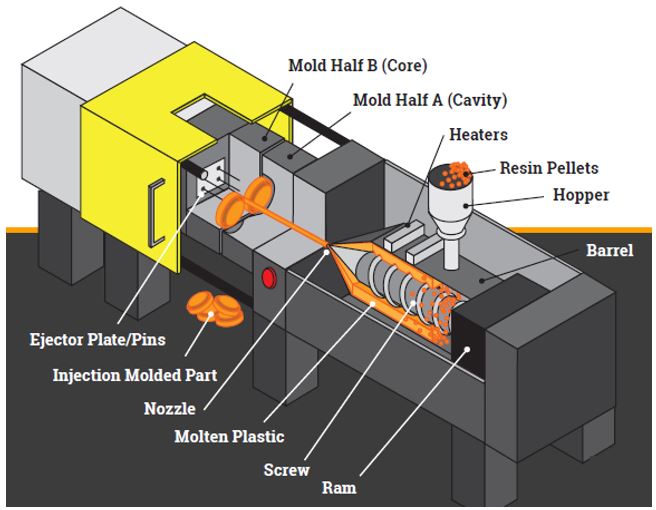
The interplay between these components directly impacts product quality, cycle time, cost-efficiency, and overall productivity.
Materials commonly used for different components
- Mold Base: Typically made of steel or aluminum, the mold base provides a sturdy foundation for all other components. Steel offers superior durability and longevity, while aluminum molds are lighter and more cost-effective.
- Cavity and Core: These components are often made from hardened tool steels such as H13 or P20. These materials exhibit high wear resistance, toughness, and heat conductivity required for withstanding the molding process.
- Runner System: The runner system can be constructed using various materials depending on specific requirements. Common choices include stainless steel or hardened tool steels like D2 or S7.
- Cooling System: Copper alloys are frequently used in cooling channels due to their excellent thermal conductivity properties. Copper beryllium alloys (CuBe) are particularly popular for their high heat transfer capabilities.
How Does the Injection Molding Process Work?
The injection molding process is a crucial manufacturing process that allows for the efficient production of various plastic products. Understanding the structure of a plastic injection molding part and how this process works can provide valuable insights into its functionality and applications.
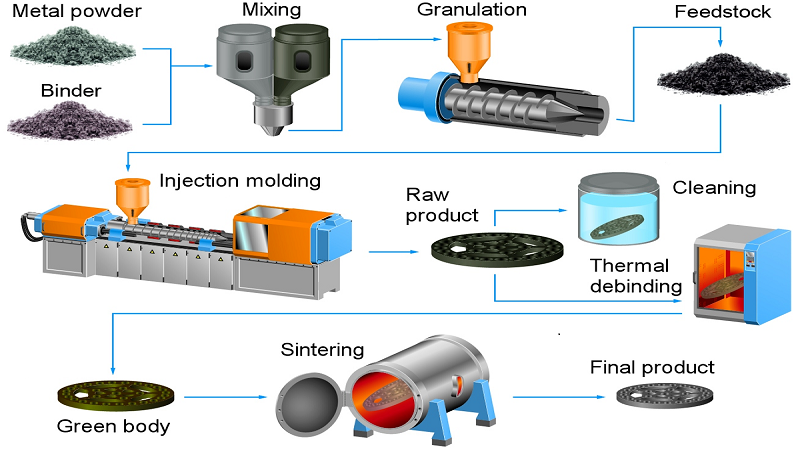
Step-by-step overview from material preparation to finished product:
Material Preparation:
- The injection molding process begins with the preparation of the raw material, usually in the form of small pellets or granules.
- These materials are typically thermoplastics, which can be melted and cooled multiple times without undergoing significant chemical changes.
- The chosen thermoplastic is carefully selected based on factors such as strength, durability, flexibility, and cost.
Melting:
- Once the material is prepared, it is fed into a hopper located on top of the molding machine.
- From there, it enters a heated barrel where it undergoes a controlled melting process.
- The temperature within the barrel is precisely regulated to ensure optimal fluidity without causing degradation to the molten plastic.
Injecting:
- After achieving the desired molten state, a screw mechanism pushes the molten plastic through a nozzle and into a mold cavity.
- The mold cavity has been designed to impart specific shapes and features onto the final product.
- Injection pressure helps fill every detail of the cavity accurately while maintaining consistent quality.
Cooling:
- Once injected into the mold cavity, rapid cooling begins to solidify the molten plastic within seconds.
- Cooling channels integrated within the mold help facilitate this process by circulating coolants like water or oil around critical areas of high heat transfer.
- Proper cooling ensures dimensional stability and minimizes internal stresses in the final product.
Ejection:
- After sufficient cooling time has elapsed, an ejection system activates to remove the solidified part from inside the mold cavity.
- The ejection system, often consisting of pins or ejector plates, pushes the product out using a core extraction mechanism.
- Care must be taken to avoid damage to the product during this stage.
During the injection molding process, each step plays a vital role in ensuring the production of high-quality products. From material preparation to finished product ejection, precision and control are crucial for achieving consistent results.
The Three Stages of the Injection Molding Process
The injection molding process consists of three crucial stages: filling, packing, and cooling. Each stage plays a significant role in ensuring the successful creation of a high-quality product. Let’s delve into the description and importance of each stage, the factors that affect their duration, and the role played by pressure control throughout the molding cycle.
Filling Stage
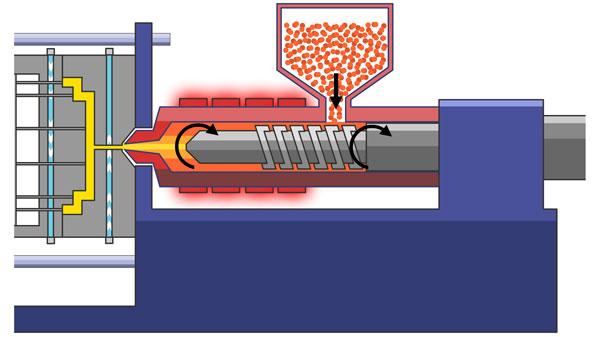
During the filling stage, the molten material is injected into the mold cavity. This is where the magic begins. The melted plastic or other materials are carefully pushed into every nook and cranny of the multi-cavity of the mold to form the desired shape. It is essential to ensure proper filling to avoid defects such as voids or short shots.
The duration of this stage can be influenced by several factors. Firstly, material properties play a vital role. Different materials have varying viscosities and flow characteristics, affecting how quickly they fill up the mold cavity. Secondly, part complexity also impacts filling time. Intricate designs with numerous details may require more time to complete filling.
Pressure control during this stage is crucial to achieve optimal results. Maintaining consistent pressure helps ensure uniform distribution of the melt within the mold cavity, preventing any potential defects.
Packing Stage
Once the mold cavity is filled with molten material, we move on to the packing stage. Here, additional pressure is applied to compress and pack more melt into any remaining gaps within the mold cavity.
Similar to the filling stage, material properties and part complexity influence how long this stage lasts. Materials with a higher viscosity may require more packing time to eliminate any potential voids or sink marks on the final product’s surface.
Pressure control remains critical during this phase as well. Properly controlled pressure ensures that all areas of the mold are adequately filled, minimizing defects like warping or dimensional inconsistencies.
Cooling Stage
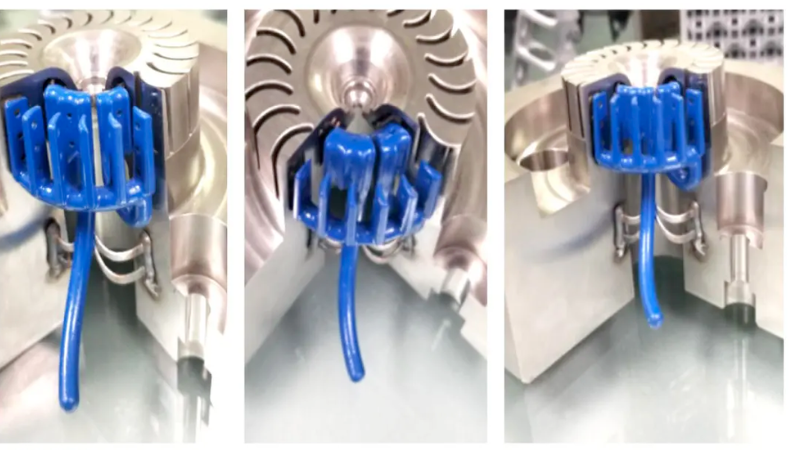
After completing both the filling and packing stages successfully comes one last vital step – cooling down! During the cooling stage, the mold is left undisturbed, allowing the molten material to solidify and the mold halves to take its final shape.
The duration of this stage primarily depends on the material used and part thickness. Thicker sections take longer to cool down compared to thinner ones. Machine settings such as coolant temperature can also influence the cooling time.
Effective pressure control during this stage helps maintain dimensional stability. By carefully controlling pressure, we can prevent any deformations or shrinkage that may occur as the material cools and solidifies.
Major Types and Systems of Injection Molds
Injection molds are essential tools used in the manufacturing process of plastic products. They determine the structure and quality of the final product. Understanding the major types and systems of injection molds is crucial for selecting the appropriate mold type/system based on specific production requirements.
Various Types of Injection Molds
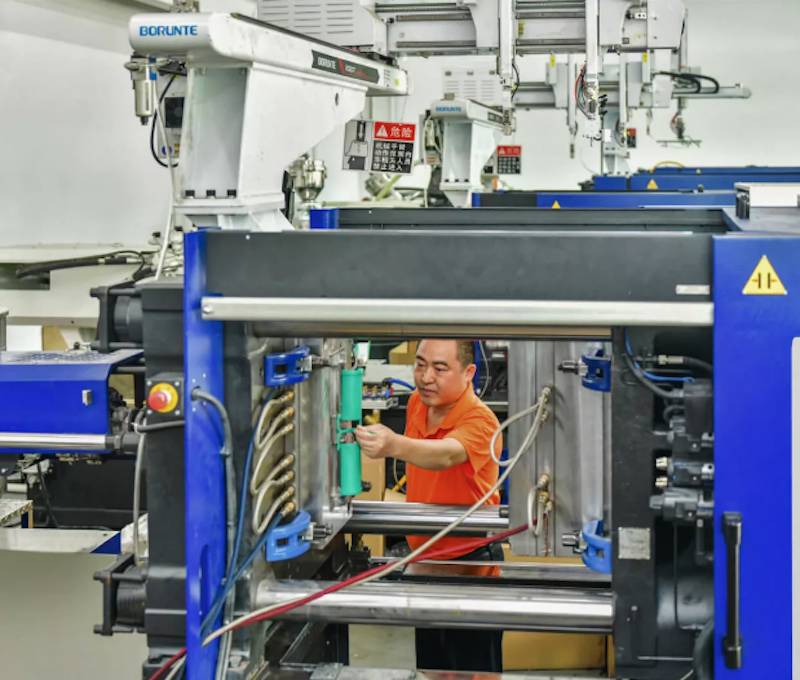
Injection molding is a widely used manufacturing process, especially in the production of parts from plastic materials. Different types of injection molds are available to meet the variety of needs in this field. Here are some of the major types and systems:
- Two-Plate Mold: This is the simplest type of injection mold. It consists of one parting plane and the mold splits into two halves at this plane. One half is connected to the movable platen and the other to the fixed platen.
- Three-Plate Mold: A more complex system, the three-plate mold has two parting planes and splits into three sections when opened. It allows more flexibility in the design of the runner system and gating locations.
- Hot Runner Mold: In this system, the runner system is kept hot and plastic remains molten in the runner system, allowing for faster cycle times and reducing material waste. However, these molds are more expensive and require a more advanced machine to control the temperature in the runner system.
- Insert Mold: Insert molding is a process where a preformed part—often metal—is loaded into a mold, where it is then overmolded with a thermoplastic resin to create a final component.
- Overmold: Overmolding involves a process where a single part is created using two or more different materials in combination, usually first creating a hard plastic part, then overmolding it with a softer material.
Comparison of Different Types of Injection Mold
Here’s a comparative table to illustrate the differences among various types of injection molds:
Injection Mold Type | Advantages | Disadvantages |
---|---|---|
Two-Plate Mold | Simple and less expensive, with fewer moving parts leading to less maintenance | Limited in complexity, a single parting line may restrict design |
Three-Plate Mold | Greater flexibility in runner system design and gating locations | More complex and costly, slower operation due to additional movements |
Hot Runner Mold | Faster cycle times reduce material waste, ideal for larger production volumes | Higher initial cost requires advanced machines to control temperature, possible material limitations |
Insert Mold | Allows for a combination of materials, can integrate both plastic and non-plastic components | Requires careful handling of insert parts, possible issues with insert shifting or sinking |
Overmold | Allows for a combination of materials, and can create complex parts with varied textures | Can be costly due to the need for multiple molds, and requires careful material compatibility check |
The Benefits of Using an Injection Mold
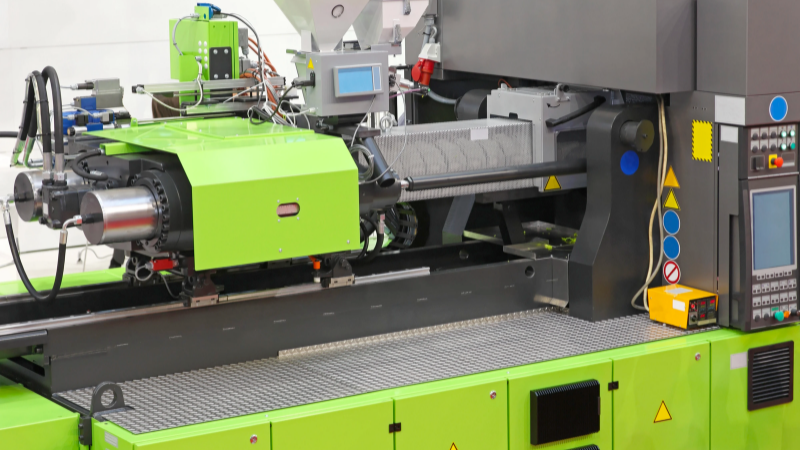
Injection molding is a versatile manufacturing process with a host of benefits, especially when producing plastic parts in high volumes. Here are several key advantages:
- Efficiency: Injection molding is an incredibly efficient process. Once the initial costs have been paid and the mold has been produced, you can create a large number of parts at a minimal cost. This is ideal for high-volume production runs.
- High Accuracy: Injection molds are precision-machined, which allows for high levels of accuracy and consistency from part to part. This is particularly beneficial in industries where precision is paramount, such as in the medical, automotive, and aerospace sectors.
- Complex Part Design: The high pressure used in injection molding allows for the production of complex and intricate plastic parts. This opens up a wide range of design possibilities that may not be achievable with other manufacturing processes.
- Material and Color Flexibility: A wide variety of materials can be used with injection molds, from various types of plastics to different types of rubber, all with varying colors and finishes.
- Enhanced Strength: Through the use of fillers in injection molds, the strength of the manufactured parts can be enhanced. This is crucial in sectors where component strength is a significant factor.
While injection molding has its advantages, it’s also crucial to consider the initial investment for injection molding cycle part design and manufacturing, which can be high, especially for complex parts. Therefore, it’s most cost-effective when producing high volumes of parts.
Downsides of Injection Molding
While injection molding is an effective and widely used manufacturing technique, it does come with its set of challenges. Here are a few of the downsides:
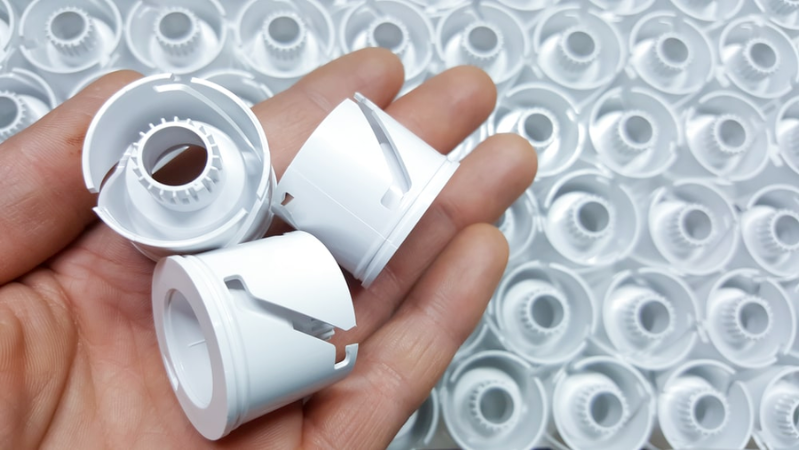
High Initial Costs
The initial investment for injection molding can be quite high, especially when creating custom molds. This cost is spread over many units in high volume runs, making the process more cost-effective. However, for small runs, the cost per unit can be higher.
Design Restrictions
Although injection molding is suitable for complex designs, there are still certain design restrictions. For example, the design of injection molded parts must allow for the part to be ejected from the mold. Design changes can also be costly once the mold has been manufactured.
Long Lead Times
Developing a mold for a conventional injection molding process can take a significant amount of time, especially for complex parts. This can slow down the product’s time-to-market.
Material Limitations
Not all materials can be used in injection molding. Certain materials can degrade or cannot withstand the high temperatures involved in the mold core process.
Despite these downsides, with proper planning and design, many of these challenges can be mitigated. It’s also important to work with experienced manufacturers who can guide the process and help optimize designs for the injection molding process.
Is Injection Molding a Good Choice for My Goal?
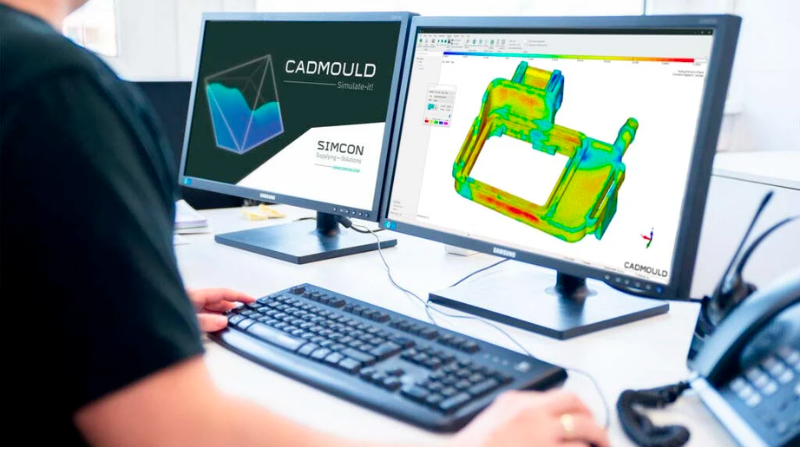
Deciding whether injection molding is the right choice for your specific project or goal requires careful consideration of several factors. Let’s explore these factors to help you make an informed decision.
- Production Volume: Injection molding is ideal for high-volume production runs. If your goal involves manufacturing large quantities of identical parts, then injection molding can offer significant cost savings and efficiency compared to other manufacturing processes.
- Complexity of Design: Injection molding excels at producing intricate and complex designs with precision. If your project requires intricate details, tight tolerances, or complex geometries, then injection molding can deliver the desired results consistently.
- Material Selection: Injection molding supports a wide range of materials, including various plastics, metals, and elastomers. Consider the properties required for your part or product and ensure that the chosen material is compatible with the injection molding process.
- Cost Considerations: While injection molds may have higher upfront costs compared to other manufacturing methods, they are more cost-effective in the long run for high-volume production due to reduced labor costs and faster cycle times.
- Lead Time: If time is a critical factor for your project, it’s important to evaluate the lead time associated with injection molding. While initial mold fabrication may take longer than other processes, once the mold is ready, production cycles are significantly faster.
Alternatives to injection molding based on specific requirements
While injection molding is a versatile manufacturing method, it may not always be the most suitable choice for every project. Depending on your specific requirements, you might consider alternative options:
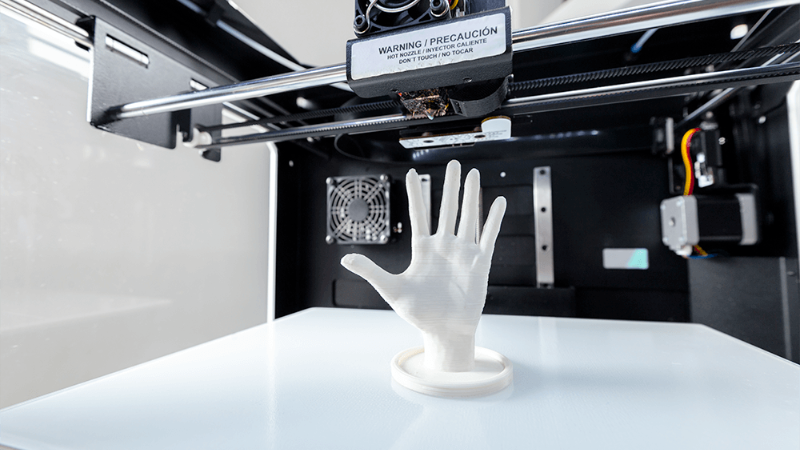
- 3D Printing: If you require rapid prototyping or have low-volume production needs, 3D printing can offer flexibility and quick turnaround times.
- CNC Machining: For smaller production runs or parts that require high precision but don’t justify the cost of an injection mold, CNC machining can provide excellent results.
- Thermoforming: When producing large parts with shallow depths or irregular shapes, thermoforming offers a cost-effective solution.
Conclusion
Injection molding is a dependable manufacturing process with a broad range of applications. Nonetheless, the success of the production process hinges on the quality and design of the injection molding equipment employed.
The construction of an injection mold tool from the ground up is an intricate process that necessitates substantial technical knowledge and meticulous oversight.
Why go to Hongju for your Injection molding needs?
At Hongju, we combine superior technical expertise and advanced machinery to deliver high-quality injection molding services. By choosing Hongju, you’re partnering with a reliable provider committed to making your vision a reality with cost-effective, high-volume production.
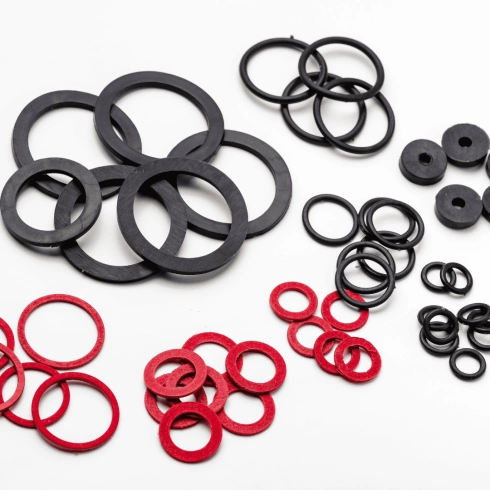
Send Your Inquiry Now!
Quality Meets Affordability. Inquire Now for High-Quality Products at Low Volumes.