Why do many industries choose silicone for their products? The answer lies in its remarkable properties. Silicone is both strong and flexible, allowing it to perform well under stress. It can endure high and low temperatures without degrading.
Additionally, its resistance to water and chemicals makes it suitable for various uses. These benefits make silicone a preferred material in numerous applications.
Types of Silicone Materials
Silicone materials are versatile polymers renowned for their adaptability across various industries. There are four primary types of silicone materials:
RTV Silicones
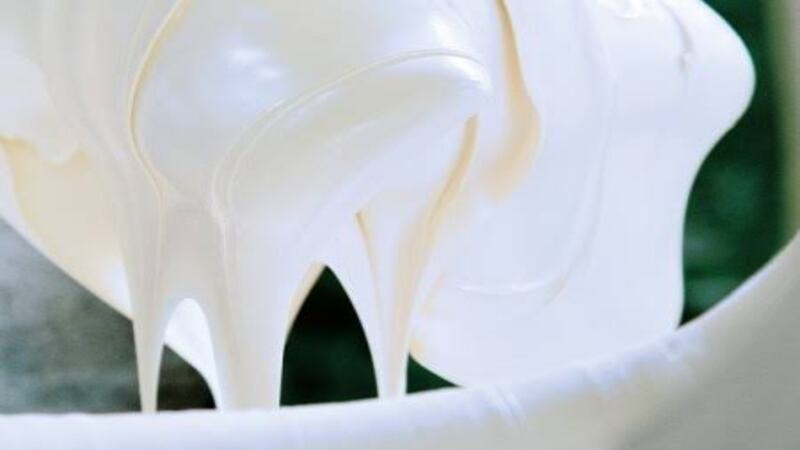
The silicones with room temperature vulcanization cure at ambient temperatures, eliminating the need for heat. Available in one-component (RTV-1) and two-component (RTV-2) formulations, they are prized for their ease of use and excellent adhesion.
RTV silicones are commonly employed as sealants, adhesives, and coatings in industries ranging from automotive to electronics.
Liquid Silicone Rubber
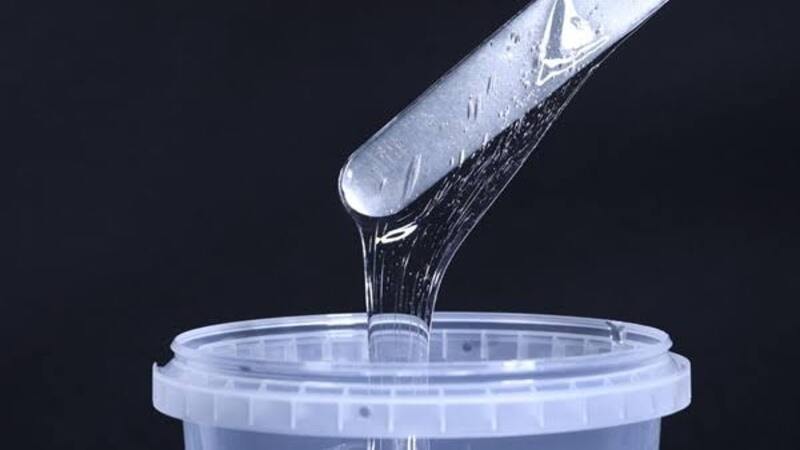
LSR is a two-part, platinum-cured elastomer known for its low viscosity and high purity. It maintains mechanical properties over a wide temperature range, from -50°C to 250°C, and offers excellent optical clarity and durability in harsh environments.
LSR is ideal for applications such as high-power LED lighting, electronics, and automotive lighting.
High-Consistency Rubber

Also known as solid silicone rubber, HCR consists of high molecular weight polymers with relatively long chains. It is available in an uncured form and requires traditional rubber processing techniques.
HCR is suitable for applications requiring durable and flexible materials, such as automotive engine components and consumer household products.
Fluorosilicone
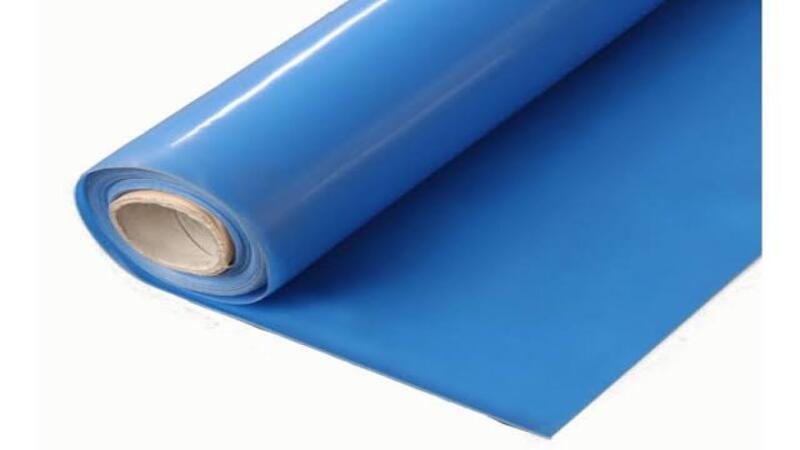
These modified silicones incorporate trifluoropropyl groups into their polymer structure, enhancing resistance to fuels, oils, and solvents.
While maintaining the inherent flexibility and thermal stability of standard silicones, fluorosilicones are particularly valuable in aerospace and automotive sectors, among other properties where exposure to harsh chemicals is common.
Each Silicone material possesses unique properties suited to specific applications. Their versatility allows for customization to meet precise requirements, making them indispensable across various industries.
Industrial Applications of Silicone
Silicone is a material with a number of unique properties that have made it a versatile material for use in many industries.
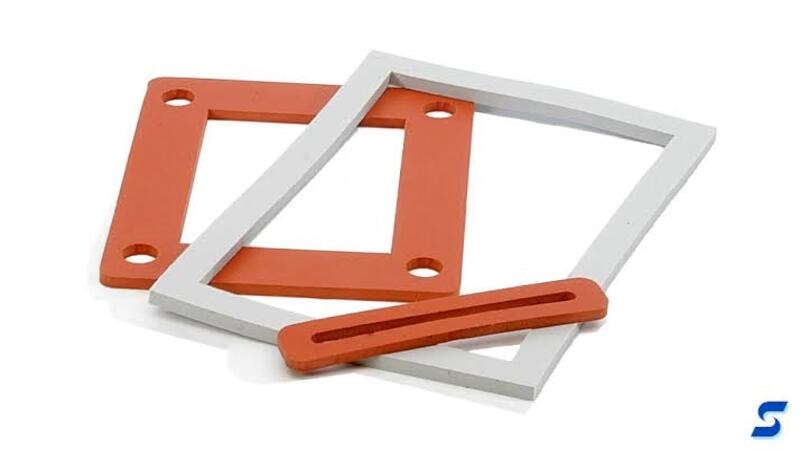
Seals, gaskets, and hoses are made using silicone in the Automotive Industry. They can withstand high temperatures and wear and are thus perfect for car engines and other parts.
In electronics, silicone is an adhesive and insulator. It keeps moisture and dust away from delicate parts so that devices can work for a long.
Silicone is also used in sealants and adhesives in construction and building. Its flexibility and durability make it useful to seal gaps in windows, doors, and other structures to keep buildings weatherproof.
Medical-grade silicone is safe for the body and is used in the healthcare and medical industry. It is nontoxic and does not cause allergic reactions, and the benefits of silicone are used in implants to protect wires, tubing, and wound dressings.
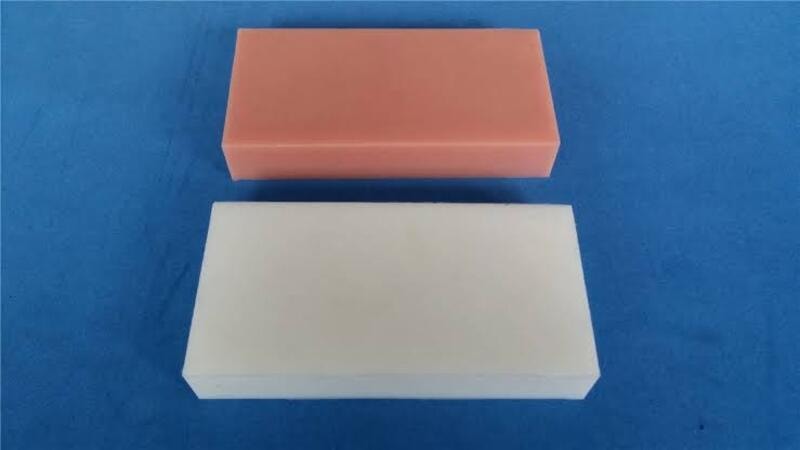
Silicone can be found in kitchens, baking mats, molds, and storage containers for Food and Beverage. It is non-stick, easy to clean, and can take high temperatures without breaking down.
Silicone is used in the aerospace industry for sealing and insulation. It is also good in extreme temperatures and pressures, and the silicon is thus suitable for aircraft components manufacturing.
Silicone is used in solar energy as it seals solar panels and provides electrical insulation. It helps solar panels to last longer or work better.
Why Silicone Rubber Is Ideal for Industrial Use
It is for this reason that silicone rubber is ideal for industrial use.
Resistance to Extreme Conditions
Silicone rubber has heat resistance and a wide temperature range of operation from room temperature of -100°C to +300°C and continues to be flexible and perform. It is UV radiation and ozone-resistant and is reliable in harsh environments.
Durability and Longevity
Silicone rubber has good retention of shape and flexibility over time, better than many other elastomers. It is a durable material in the sense that it is resistant to wear and tear and will remain resistant for long-term applications.
Chemical Resistance
Silicone rubber remains nonreactive in oils, fuels, and many other chemicals in industrial settings, providing stability and safety in many applications in everyday life.
Advantages of Using Silicone Rubber in Industrial Applications
Industries rely on silicone rubber for its heat resistance, chemical stability, and long-lasting performance. Here is how industries benefit from silicone rubber.
High-Performance in Extreme Environments
Silicone rubber is excellent in high-heat, high-pressure, and chemically aggressive environments. It has excellent mechanical and physical properties from -60°C to 260°C and is used in industries such as aerospace, automotive manufacturing, and construction.
Customization and Versatility
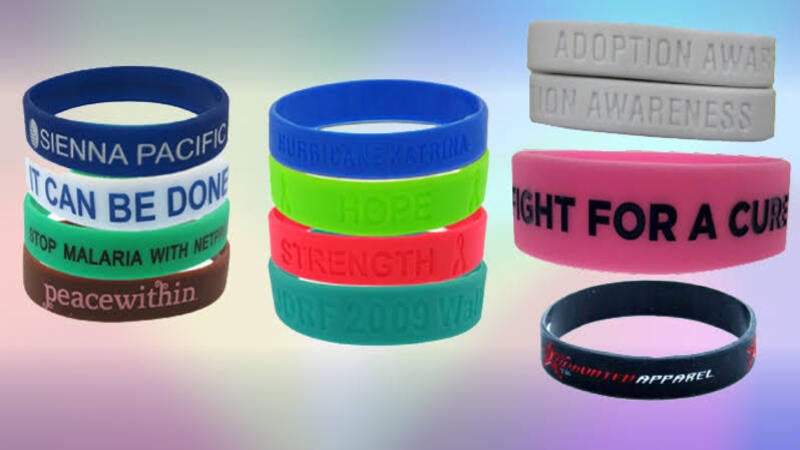
Silicone rubber can be molded and shaped as needed to fit a particular industry need. Formulations and hardness are offered, from which tailored solutions for gaskets, seals, and O-rings, or for protecting critical pump components against metal contaminants, can be provided.
Long-Term Cost Efficiency
Silicone rubber is more durable and thus reduces maintenance costs and the need for frequent replacements. The longevity of silicone means that it yields a better return on investment for businesses.
Challenges and Limitations of Silicone Rubber in Industrial Use
Cost Considerations
Silicone rubber has a higher initial cost compared to other elastomers like rubber or thermoplastics. However, its durability and long lifespan often make it more cost-effective in the long run.
The material’s resistance to extreme temperatures, chemicals, and wear can reduce maintenance and replacement costs. For industries that prioritize performance and reliability, the upfront investment in silicone rubber can be justified by its lower overall lifecycle costs.
Processing and Handling
Silicone rubber can be challenging to mold and process, particularly in complex shapes. The curing process requires precise control of temperature and pressure, making it more difficult to handle than other elastomers. This can increase production time and costs in certain industrial applications.
Liquid Silicone Rubber (LSR): A Versatile Material
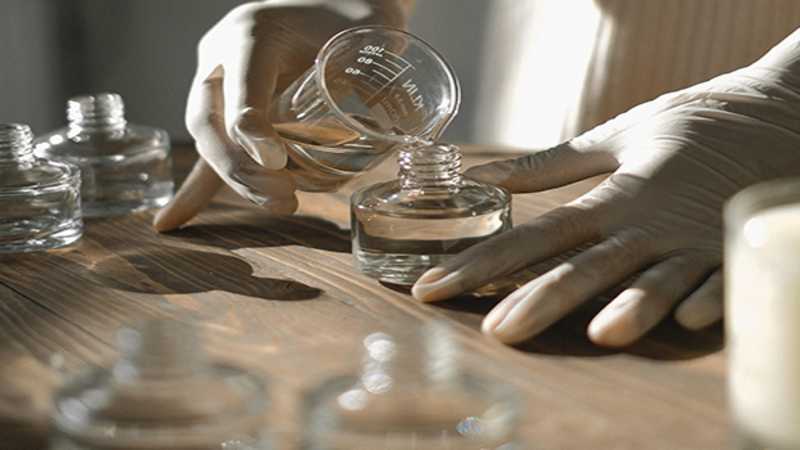
Liquid Silicone Rubber (LSR) is a two-part, platinum cure elastomer with excellent fluidity and is used for injection molding and casting. This property enables the production of parts with intricate and complex shapes. LSR is also biocompatible and durable enough to be used for medical devices like catheters and asthma inhalers.
Together with its resistance to extreme temperatures and chemicals, this makes it suitable for many microelectronics applications. Moreover, LSR is safe in medical environments because it can be sterilized through methods such as steam autoclaving and gamma radiation.
Silicone Oil: Industrial Application
It is a clear, odorless liquid with a high viscosity index and excellent thermal stability. It is a versatile lubricant serving in industrial settings as a lubricant that helps drastically minimize friction and wear in machinery.
Being chemically inert and having low surface tension, it is well suited for use in hydraulic fluids, assuring smooth working of equipment.
Silicone oil also has excellent electrical insulating properties, which are used in transformers and capacitors to improve the safety and efficiency of electrical systems.
Silicone oil is also used in personal care products such as hair conditioners and cosmetics, for its smooth texture and moisture retention.
Silicone Curing Systems
Silicone curing systems, such as condensation, platinum, peroxide, and UV curing, each offer unique benefits and limitations tailored to specific applications. Condensation curing uses tin-based catalysts and atmospheric moisture, releasing byproducts like alcohol and acetic acid.
Post-curing may be necessary to eliminate residues. Platinum curing employs platinum-based catalysts, resulting in cleaner processes without VOC emissions, making it ideal for medical and food-grade applications.
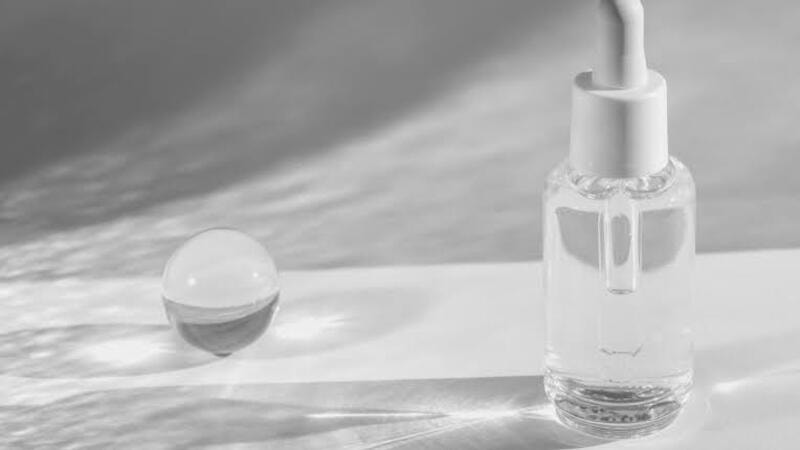
Peroxide curing uses organic peroxide catalysts, requiring lower curing temperatures but potentially leaving residues that necessitate post-curing.
UV curing employs ultraviolet light to initiate silicon crosslinking, enabling rapid silicon processing and precise control over curing time, suitable for electronics and medical devices.
Each system can be customized to meet specific requirements, balancing factors like heat, silicon purity, processing conditions, and application suitability.
Customization and Fabrication of Silicone
Silicone is a very versatile material that can be tailored to your requirements. It can be fabricated by injection molding, casting, and extrusion. Pump-nozzle extrusion systems can be used to 3D print silicone tubing as well.
The processes involved in product development and manufacturing using injection molding of liquid silicone include first injecting molten liquid silicone into a mold, which creates complex, high-precision components.
Low-volume production casting is pouring liquid silicone into a mold and allowing it to cure. Silicone is forced through a die to make continuous profiles (seals, gaskets), while extrusion and 3D printing with pump-nozzle extrusion systems are quick prototyping and customization.
Electrical Insulation and Microbial Resistance
Silicone serves as an exceptional electrical insulator because it demonstrates strong dielectric properties and minimal electrical conductivity. The material is superb for electrical insulation needs because of its reliable performance characteristics.
The insulating material maintains its performance capabilities across all environments since it operates effectively from -100°C to 300°C. The low chemical reactivity of silicone, together with its low toxicity, makes it appropriate for use in sensitive applications.
Silicone demonstrates two important features by being resistant to microbial development, which enables its use in medical devices and food processing applications.
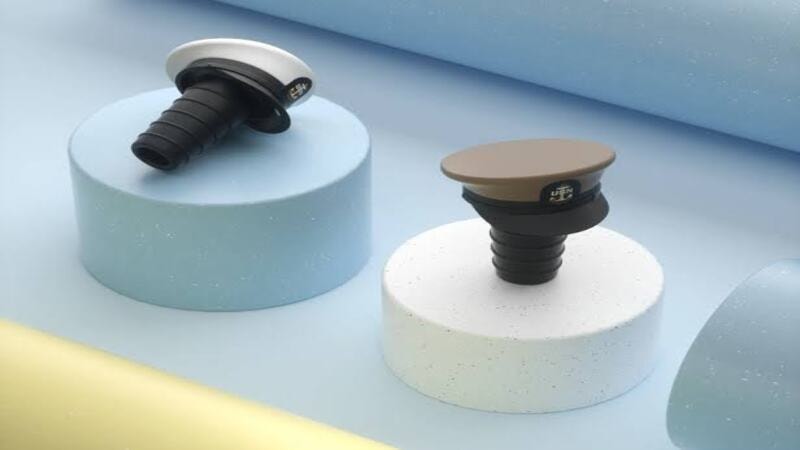
Silicone maintains safe exposure to human bodies because it demonstrates both biocompatibility and hypoallergenic properties. Silicone exists in multiple formulations, which enable manufacturers to fulfill different industry requirements.
Human Health and Silicone
The extensive use of silicone is used extensively in medical applications because it maintains both excellent compatibility with biological systems and resistance to microbial growth. When human tissues come into contact with silicone, it exhibits an inert behavior, which leads to minimal unwanted side effects.
The application of silicone in hair and skin care enables better product texture while improving operational effectiveness. The chemical substance demonstrates non-toxic properties, which drives manufacturers to use it in many forms in their product formulations.
Choosing the Right Silicone for Your Industrial Needs
Selecting the appropriate silicone material for industrial applications requires careful consideration of several key factors. Temperature range is crucial; silicone can withstand extreme temperatures, typically from -100°C to 300°C, making it suitable for high-heat environments.
Flexibility is another important aspect; silicone’s inherent flexibility allows it to maintain performance under dynamic conditions. Environmental resistance is also vital; silicone offers excellent resistance to UV radiation, ozone, and various chemicals, ensuring durability in harsh conditions.
For specific industrial needs, custom silicone solutions are available. Manufacturers can tailor silicone formulations to meet precise requirements, such as enhancing chemical resistance or achieving specific hardness levels.
Custom-cut silicone products, like gaskets and seals, can be produced to exact specifications, ensuring optimal performance in specialized applications.
Future Trends in Silicone Rubber Applications
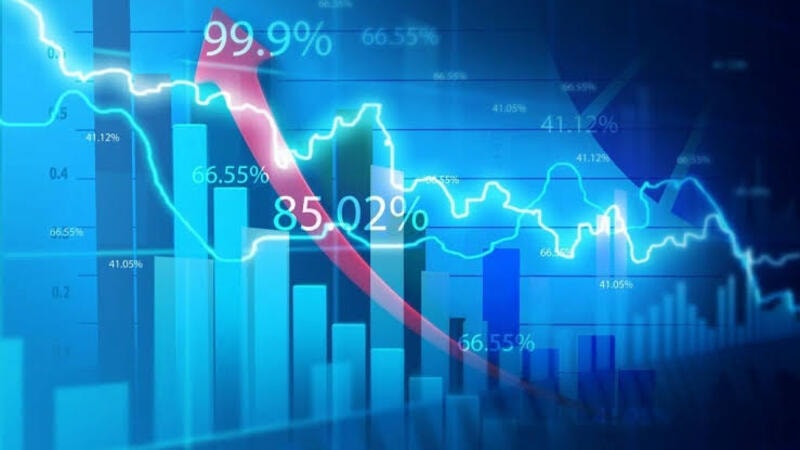
Silicone rubber is set to play a bigger role in future technologies, thanks to enhanced properties and innovative applications. From eco-friendly alternatives to high-temperature resistance, its potential is expanding rapidly.
Advancements in Material Technology
Silicone rubber production innovations have resulted in new advanced silicon industrial materials that display improved characteristics.
Silicone rubber has become applicable to automotive applications, consumer electronics, and industrial machinery due to recent manufacturing improvements in silicon compounds. The global automotive market is expected to expand at a CAGR of 5.62% from 2024 to 2031.
Growth in Green and Sustainable Solutions
The silicone industry boosts sustainability through its development of environmentally friendly silicone products that can be recycled. Silicone research now follows a sustainable direction because manufacturers seek eco-friendly industrial materials.
Conclusion
Silicone’s exceptional thermal stability, flexibility, and resistance to extreme temperatures make it indispensable across various industries.
Its applications span construction, automotive, aerospace, and medical devices, underscoring its versatility and reliability. These properties ensure that silicone continues to meet the demanding requirements of modern industrial applications.
Make the Smart Choice for Sustainability – Connect with Hongju!
For over two decades, Hongju has delivered innovative silicone rubber solutions. Our commitment to safety and sustainability drives everything we do. Experience eco-friendly excellence with products designed for a better future. Get in touch today!