What is EPDM Rubber?
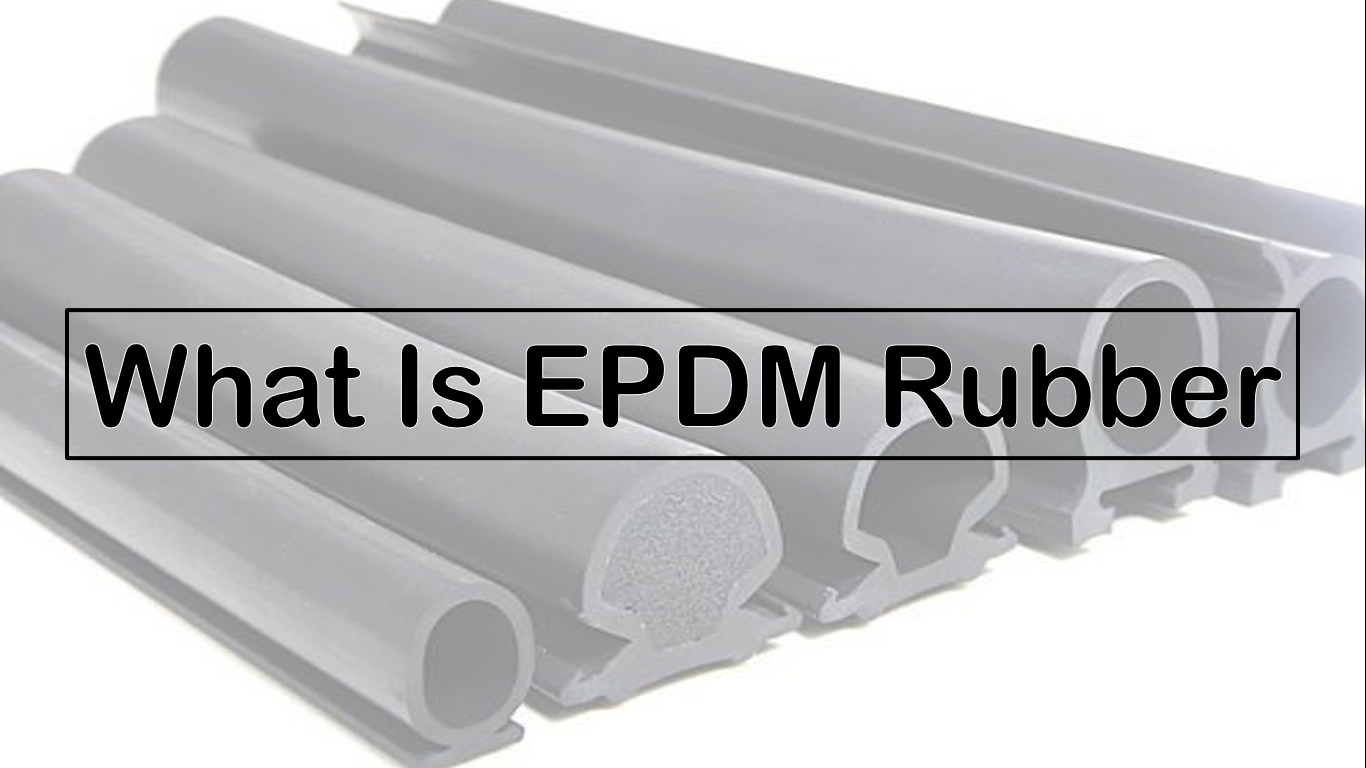
Ethylene Propylene Diene Monomer, in short, EPDM, is a kind of synthetic rubber. It is made from the chemical components that are given in the name. EPDM has a variety of industrial applications.
The most common industries where EPDM is used are construction and automobile. In these industries, seals are primarily made of EPDM because this synthetic rubber has excellent resistance to UV rays and Ozone.
This material exhibits exceptional elastic properties not only at average temperatures but also at low temperatures. Moreover, this material is highly resistant to abrasion and tearing due to its superior mechanical properties.
What is Silicone Rubber?
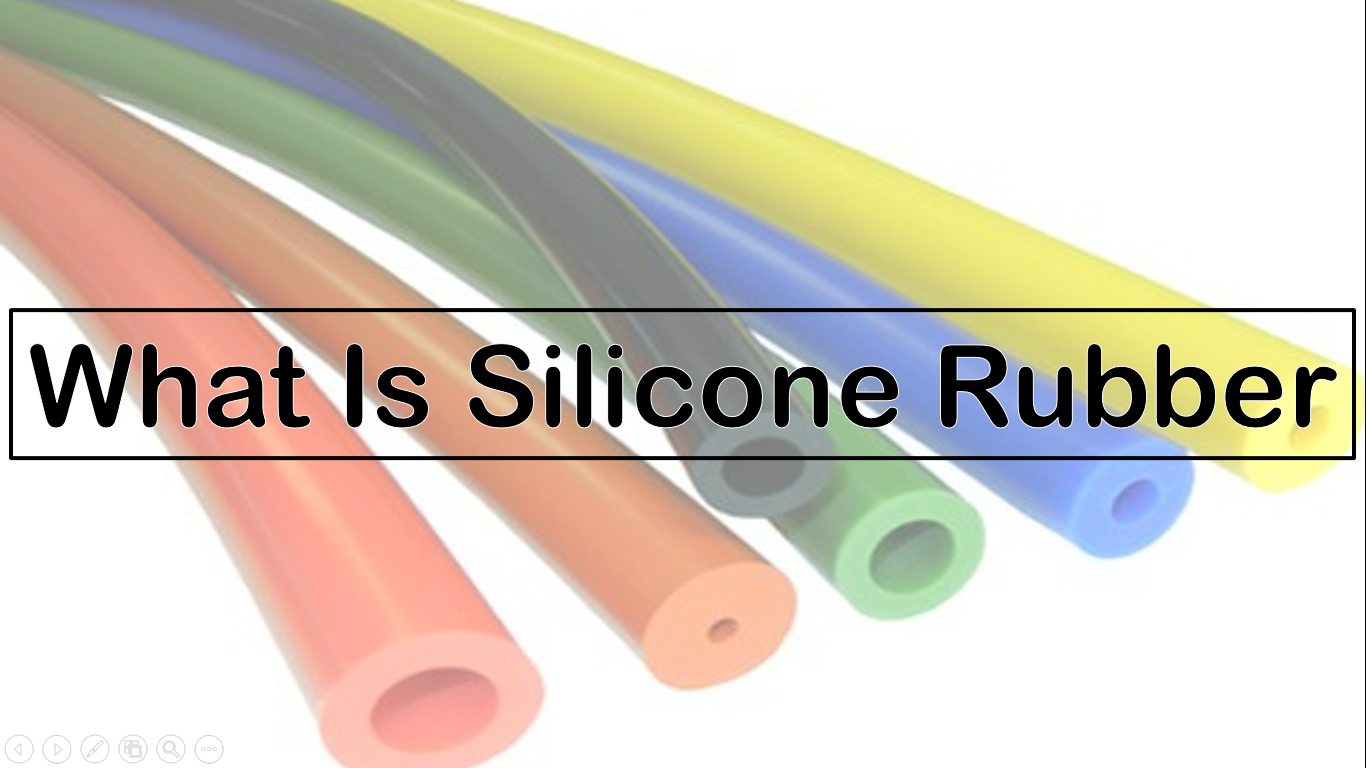
Silicone rubber is a type of inorganic polymer primarily comprising hydrogen, carbon, oxygen, and silicone itself. Silicone, again, is made up of a substance called Siloxane, where Silicon is an essential constituent.
Silicone rubber has a wide range of applications in several industries, including food and beverage, automobile, aerospace, etc.
There are countless advantages of silicone rubber in industries, but one of the most important ones is its usability in higher temperatures. This material can keep its properties stable even at 230°C temperature.
Silicone rubber is an excellent sterile elastomer. Therefore, it is used to manufacture seals, dairy tubing, gaskets, etc. Moreover, drinks machines have vending tubes where this inorganic polymer is used vastly.
Technical Comparison between EPDM and Silicone Rubber
In general, silicone rubber has a longer lifespan than EPDM rubber. However, this doesn’t mean EPDM is useless or silicone rubber is always better. There are specific differences between these two materials.
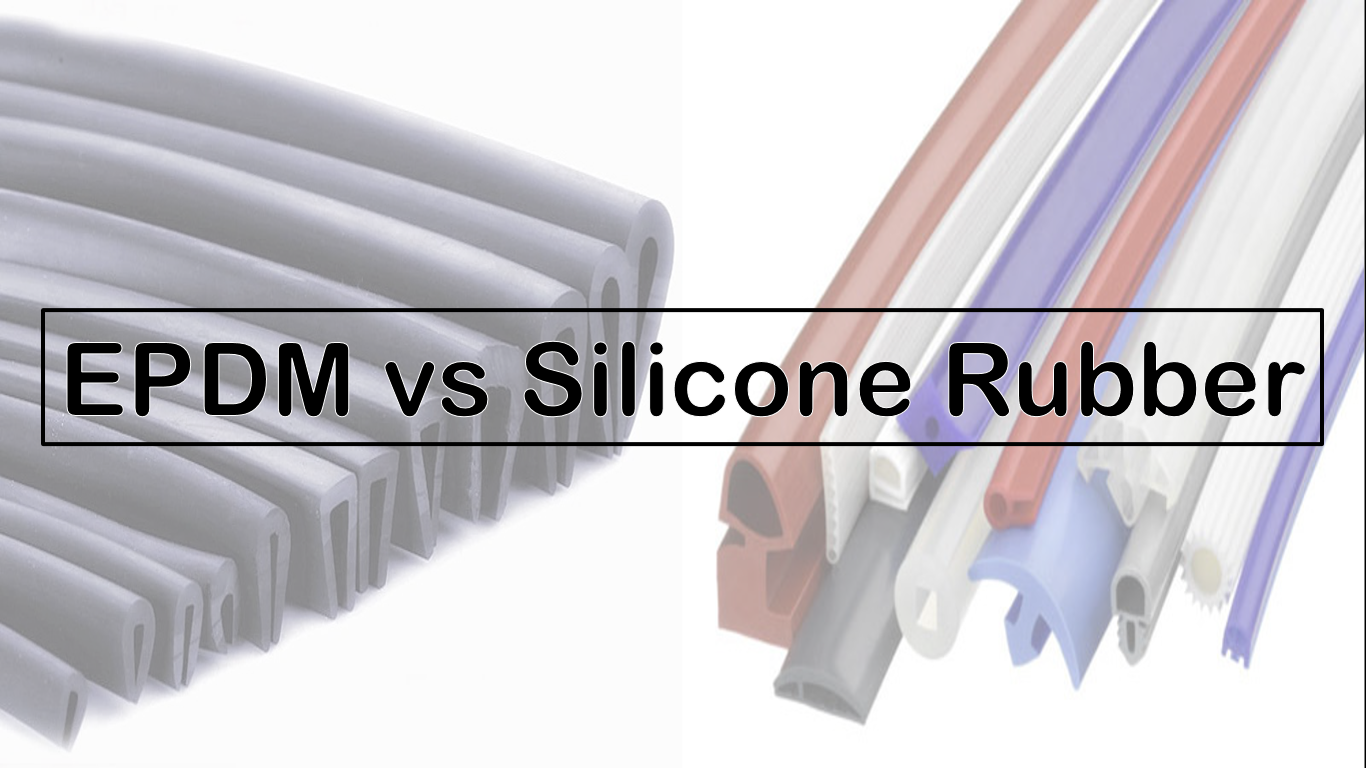
The below segment shows the comparison between EPDM and silicone rubber based on different aspects:
Temperature Resistance
There are tons of applications where temperature varies a lot. In such cases, it is vital to choose the correct rubber. Because choosing the wrong type of rubber may cause severe damage to the components used in a particular application.
For example, if the rubber component cannot withstand high temperatures, then the element may deform or melt. This can lead the piece to become brittle, which is not good. This is why it is essential to focus on temperature resistance.
In the case of silicone rubber, it can withstand about 230°C temperature, whereas EPDM can withstand about 130°C. When subjected to temperatures above 130°C, EPDM would lose its properties. Therefore, silicone is better for high temperatures applications.
Oil Resistance
Both EPDM and silicone are capable of handling oil. This means both have good oil resistance. But if compared thoroughly, one should know that silicone has better oil resistivity than EPDM.
There are many applications where a component must be in contact with oil for a long time. In this case, the part can be made with formulated silicone for better oil resistivity. EPDM can not be composed like this.
Tear Strength
Tear strength or tear resistance of material means the value of the load or force it can withstand before breaking or tearing. Directly speaking, EPDM (Ethylene Propylene Diene Monomer) has high tear resistance. But the tear resistance of silicone is lower than EPDM.
This means components made of EPDM can withstand more force or load than silicone components. But this doesn’t make silicone any weaker. Silicone has greater flexibility than EPDM.
With correct formulation, silicone-made components can have very high strength near EPDM. But overall, tear resistance is higher for EPDM compared to silicone.
Elongation
The elongation of a material indicates its stretchiness. A long material can be contracted or expanded without tearing or breaking. Silicone has a better extension than EPDM rubber.
When it comes to stretchiness, silicone is stretchier than EPDM. Silicone elongation can reach up to 800%, which is far better than EPMD. For this reason, silicone rubbers are used to make vacuum membranes.
On top of that, silicone’s elongation properties stay stable even at -60°C temperature. This is why silicone is suitable for harsh weather conditions. As silicone can remain stable over a considerable range of temperatures, it has better weather resistance than EPDM.
Environmental Resistance
Silicone Rubbers are not only used as internal components but also have outdoor applications. For this reason, it is crucial to justify the resistance of rubber against weathering. So, both silicone and EPDM rubber has environmental factors to consider.
Some rubbers cannot withstand UV light or the effect of Ozone. But silicone rubber and EPDM are not like that. These rubbers are equally capable of withstanding the effects of UV and Ozone.
So, regarding environmental resistance, both silicone and EPDM have equally outstanding properties. For this reason, these materials are used to make components outside.
Silicone vs. EPDM Rubber: Which One is Better for Gasket?
Gaskets are not a very expensive component, but it is mounted on many elements, which are pretty costly. If the suitable material is not chosen for a gasket, it may fail and damage the component it is mounted on.
Regarding EPDM vs. silicone for choosing gasket material, there are specific properties to consider. The gasket material should be changed or selected based on the application, weather conditions, or other factors.
As silicone can withstand extreme temperatures, it is suitable for gaskets used in high-temperature applications. Silicone can also be used in cold temperatures. But when it comes to extreme pressure, it will be better to use EPDM instead of silicone.
Applications of EPDM
There are lots of applications of EPDM in different industries. For example:
- It is used to make gaskets that are used in the automobile industry. It is also used to make window seals and door seals.
- EPDM reduces or eliminates unwanted vibration movement in the consumer appliance industry.
- In the enclosure industry, EPDM seals are used to isolate vibrations. It also provides a slight advantage in preventing contamination.
- EPDM has excellent liquid and water resistance, used in masking industries to prevent paints from reaching unwanted areas.
- Seals and gaskets used in the military industry and HVAC systems are made of highly durable EPMD rubber.
Applications of Silicone Rubber
Silicone is a highly versatile material suitable for various applications, including electrical applications (i.e., electrical insulation). The applications of silicone rubber are discussed below:
- As silicone provides better resistance, it is suitable for smoke sealing, shock protection, and vibration prevention in HVAC systems.
- Silicone can resist fungal growth, which is perfect for the medical industry. This material can work in varying degrees, so it is used in ultracold storage containers in the medical sector.
- In the food industry, silicone is used in food machinery, food containers, and in other sectors because it is a part of aromatic hydrocarbons.
- The water resistance property of silicone makes it suitable for cable industries where the cables are covered with this material. It is also used for the manufacturing of O-rings.